Welcome to Tire Tech, Bikerumor’s mostly-weekly series on bicycle tires. Like our Suspension Tech and AASQ series, we take your questions about tires, whether it’s road, cyclocross, fat, plus, gravel, or mountain bike, and get answers from the brands and people behind them.
In our previous Tire Tech installment, we peeled back the rubber to get a better understanding of tire casings. This week we once again solicited help from Tim Krueger of Terrene Tires to walk us through the different types of flat-prevention reinforcements hiding beneath the tread.
Although every tire is susceptible to a cut, puncture, or pinch, not all require the same level of protection. A tire built for ripping down an enduro course needs more brawn than one made for fast XC racing. In order to provide each tire with the appropriate degree of reinforcements, tire developers use a variety of materials strategically placed within the carcass. Knowing how those technologies work can help you select the ideal tire for your individual needs.
When evaluating protective features consumers are forced to wade through a quagmire of marketing buzzwords and trade names. Some refer to specific materials. Others denote proprietary designs incorporating a combination of technologies. As an example, Aramid is a specific type of synthetic thread. Terrene offers reinforced tires badged as Tough tires, which are built with the brand’s TekShield reinforcements. Although it sounds like a singular technology, it is a multi-faceted approach to tire defense using several materials—including Aramid. According to Krueger, their approach involves choosing the right casing, integrating the necessary anti-flat barriers, then applying the best inserts and rubber laminates to achieve the desired toughness.
The end goal for Terrene, and all tire manufacturers, is to place the reinforcements where they are needed without compromising the tire’s performance any more than necessary.
Super fibers and fabrics
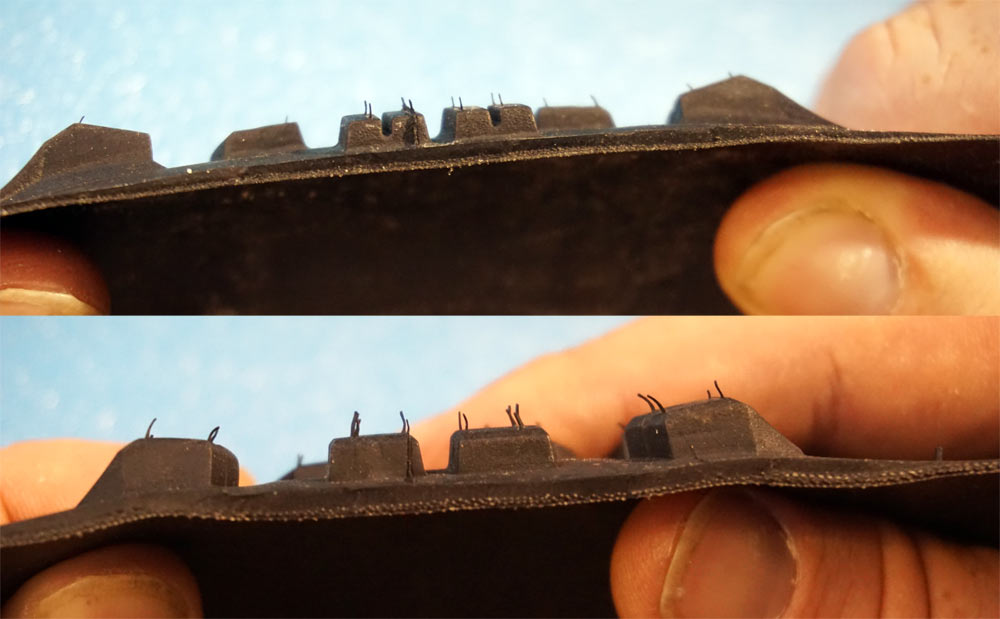
Tire science wouldn’t be where it is today without high-tech filaments like Kevlar, Aramid, Vectran, Dyneema, Teijinconex, and Toray. Most of them are similar in application even if chemically different. They have all been described as synthetic spider silk. Known for their exceptional tensile strength, they are spun into lightweight and cut-resistant threads. That, in turn, is woven into a tough and flexible fabric. In some cases Aramid, Kevlar, and Vectran are blended with nylon or polyester to produce a protective fabric with specific characteristics.
As we covered in the tire casing overview, fiber diameter and thread count (tpi) determine the characteristics of the fabric. The more densely packed the Kevlar or Aramid fibers, the more durable the fabric is. More costly as well. For this reason, manufacturers use different types of reinforced fabrics in different applications to achieve their design objectives.
Layering and placement of reinforcements
Once designers select a protective layer they have to decide where to place it on the casing. Materials designed to guard against punctures from thorns, needles, and other sharp objects are usually placed beneath the tread surface and not along the sidewall where small holes are less common. Fabrics with superior cut resistance are typically placed under the tread cap and/or sidewall. How these layers are combined all depends on the unique threats the tire needs to defend against.
A woven material won’t really stop a puncture, which is why you can stab through a Kevlar vest. But they’re hard to tear, so they work well to keep your sidewall together. Here, you’ll find Kevlar, Aramid and even advanced nylons.
A solid layer, however, does stop punctures. Usually this is a synthetic rubber with additives to add friction properties so a penetrating object can’t work its way through. Krueger says these can be 1-3mm thick, depending on what the manufacturer thinks is necessary. City and touring tires are on the thicker end of this. Terrene’s Honali touring tire has a ~2.5mm layer.
And they’re not just for mountain bike tires. According to Krueger, tires used on pavement and gravel may suffer fewer sidewall cuts, but are more likely to see nails and glass. So puncture reinforcements are best placed beneath the tread cap. But enduro riders pushing hard through rock gardens are more likely to damage a sidewall, so they get more layers there.
Butyl Inserts and Apex Layers
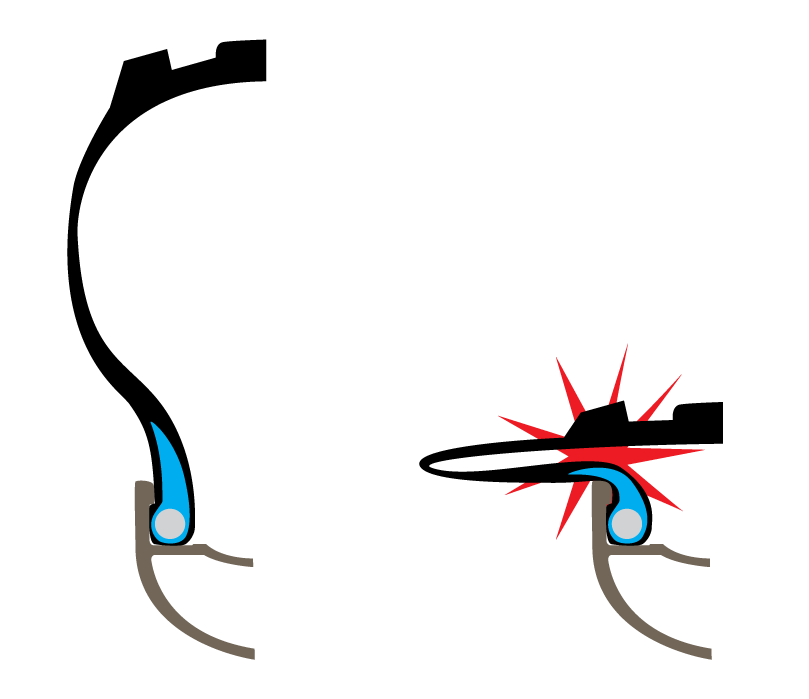
There are other methods used to reinforce a tire beyond space-age fibers and fabrics. Apex layers (aka butyl inserts) are types of reinforcements used widely in automotive, motorcycle, and bicycle tires. Some brands simply call them an Apex layer or Apex protection, others may use “Anti-Snake Bite” or other terminology.
An apex layer is an extra facet of butyl rubber encasing the bead and extending up the sidewall. Different brands use different heights, thicknesses and types of material. Even different tire models from the same brand may vary the apex’s shape, size and thickness. So, even though they may be called the same thing, one tire’s apex layer is not necessarily the same as another’s.
But they all aim to do similar things, and mainly provide two distinct benefits. The first is to give the sidewall additional support. For tires ridden in extreme applications like downhill and enduro racing, it lends the tire more rigidity in hard turns. That extra support is also beneficial for heavy bikes—think e-bikes. By adjusting the thickness of the rubber, designers can fine-tune sidewall stiffness.
The extra rubber also absorbs impact to lessen the potential for cuts and tears -think “snakebite” punctures- to the lower sidewall, which are all but impossible for sealant to fix. Even for riders still using tubes, the apex layer can reduce the pinching forces of the sidewall on the inner tube, potentially saving your ride. It can also save your rim from damaging impacts.
Putting it all together
With the tools on the table, tire developers pick and choose which components they want to laminate to the casing…and where…to achieve the desired durability without adding excess weight, complexity or cost. Although few companies measure rolling resistance of mountain bike tires in a laboratory setting, it’s well understood that compounding layers eventually degrades efficiency. How much? Without numbers to work with that is up for debate. But one thing is universally understood – a flat tire is much slower than an inflated tire.
This Episode is presented by Terrene Tires. At Terrene, we put riding at the center of the experience. We understand what matters most—be it an afternoon on your favorite stretch of singletrack, a long day on an unending dirt road, or a worldwide tour. We took what we have learned through decades in the bicycle industry to bring you tires that are designed to ride how you do. From the very beginning of the process until the tread hits the dirt, we bring together our experience in product development and a passion for riding to create tires that are ready to ride for people that live to.
Pumped on this? Got a question you want answered? Email us. Want your brand or product featured? We can do that, too.