Back as winter was setting in we had the chance to travel to northern Italy to visit the headquarters of Vittoria-partner Directa Plus, who have developed some of the most advanced graphene manufacturing and applications to hit the cycling industry. We have seen a lot of hype on this new material that promises to revolutionize everything from helmets, to wheels, to tires, and even clothing textiles. But to be honest we had been (and to some degree continue to be) a bit skeptical. A lot of the talk about graphene is filled with hyperbole and such thick marketing-speak, that it is hard to accept claims of bigger, faster, stronger, and at the same time lighter.
So we were definitely more interested in not just claims of improvements, but the actual behind-the-scenes science that should back up the claims. So we sat down with both the Vittoria product development team and the Directa Plus scientists who developed their own proprietary graphene solutions for cycling, dubbed Graphene+. Then in the meantime, for the couple of months it took to get Directa Plus and Vittoria to agree to let us publish some unique details of their protected patented processes, we’ve been riding tires with the new tech to see how they perform in the real world. Join us after the jump as I try to both explain and illustrate how Graphene+ might really have the potential to revolutionize the tire market, both on and off the road…
Graphene
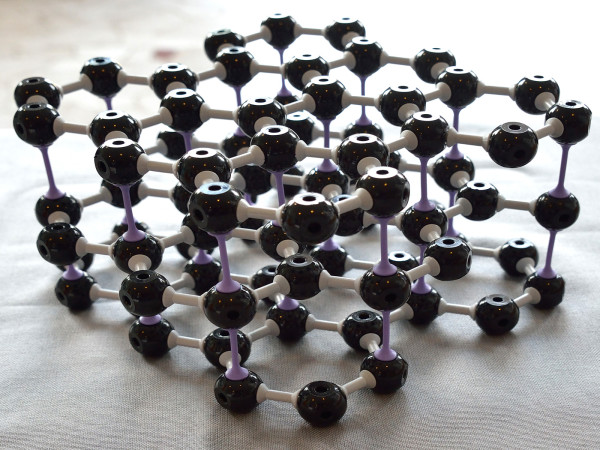
The first thing to know about graphene is that it is essentially just carbon atoms grouped together at a very small-scale, as in a material from just one atom thick. The Graphene+ (G+) version we’re talking about here mostly that Vittoria is using though isn’t a single atom layer, but tiny disks of graphene that are then evenly mixed in with some other materials to improve their function or performance. The continuous single layer concept is actually quite problematic, as a single layer on the outside of a material it would be subject to wear, while putting it in the middle of a composite material it would act as a barrier and be difficult to transfer loads across.
Relying heavily on the physical properties of materials for the bulk of their products Vittoria sees material research as the future of their sector of the bike industry. And they see the development of graphene as similar to the modern development of commercial plastics.
While all of this graphene is being put into Vittoria wheels and tires now, the development of the process and its applications comes from the company Directa Plus, of which Vittoria is a part owner. What that also means is that all the patented tech we’ll get into here is exclusive to Vittoria. So while it may get applied to the products of other companies in other industries, for the cycling wheel market Graphene+ isn’t likely to show up in any of Vittoria’s competitor’s product lines. That doesn’t mean that some variation of elemental graphene won’t continue to show up in other products, but from what we’ve seen it’s not very easy to actually create the material at a useful scale, and even harder to combine it with other materials to actually produce performance benefits without causing other problems.
Graphene Production
Directa Plus produces all of the Graphene+ that Vittoria uses in their Lomazzo, Italy research and development facility. To do that, they start with raw graphite and superheat it to about 10,000°C (a temperature beyond that of the surface of the sun) with some type of plasma system to create the graphene. This is more than 3x the temperature that causes the graphite to sublimate (jump straight from a solid to a gas) and when they cool it down a completely new crystalline graphene structure is formed that super-expands the carbon leaving a fluffy, incredibly light black material that Directa Plus has also applied to absorb contaminants in the case of oils spills.
The process of breaking down the material to such a nano-scale is done entirely with heat not chemicals, so the physical change is totally clean, with no adverse environmental impact. This also makes it easier for Directa Plus who have their R&D lab right next to the clean-room production line and their offices in the next building in the historical industrial tech park on the edge of Lomazzo.
The first step of the process of turning graphite to Graphene+ also greatly expands the material. It’s then through a series of further steps (which Directa Plus didn’t want to reveal) that the material is further refined and brought back down to a higher density and more uniform and controlled physical shape, which enables its application in composite materials.
The end result here is what they call Graphene+ nano platelets, which range in thickness from about 1 to 10 atoms thick (0.35-4nm) and lateral dimension between 500-10,000nm. (Just for frame of reference since this nano-scale is pretty hard to grasp, that means the nano platelet could be 1/1,000,000th of a millimeter thick and 1/1,000th of a millimeter in diameter. That would make it just 3 carbon atoms thick, and 3000 atoms across.)
As alluded to above, getting the carbon down to a single atom width isn’t actually the end goal. Creating a graphene mono-layer is not really desirable (for cycling). While it can be incredibly strong itself, the monolayer is exceptionally slippery. It effectively acts as a barrier between materials on either side of it. Exposing it directly on the outside of a product would make the extremely thin layer susceptible to wear, and embedding it inside of a composite would make it almost impossible to bond to on either side.
Graphene in Wheels & Tires
So what Directa Plus and Vittoria did was figure out a way to uniformly and consistently distribute their nano platelets in a composite matrix. For carbon fiber applications, like their use in wheels and other components, Vittoria is able to evenly mix the Graphene+ nano platelets directly into the resin before impregnating the fibers. In doing so, they increase the thermal character of the resin. Graphene actually makes the resin thermally conductive which allows the carbon to conduct heat as well. Now typically composite resins do not conduct heat, which is what makes standard carbon wheels have such a heat buildup problem as a result of braking.
In addition, Vittoria claims that the nano tech makes the resin stronger leading to a stronger composite and wheel. That let them develop a tubeless clincher bead that they were confident could handle significantly higher pressures (much higher than the 8bar/116psi minimum standard they were working with) even if heat build-up were still a concern. That also lets them use at times one less layer of carbon fibers in the layup, while producing the same strength, so again they can reduce weight. The end result is a complete rim that Vittoria says is stiffer and more durable, while shedding a bit of weight from their previous wheelsets.
Inside of tires the Graphene+ is even a little easier to see how it performs. The Graphene nano platelets get aligned in the rubber, and move as the wheel rolls.
Vittoria didn’t want to elaborate as to how they align the platelets with the direction of travel (perpendicular to the radius of the wheel), but it seems to have something to do with the pressure as the rubber is extruded, compressed, and the tread pattern is rolled in. The important aspect is that the parallel alignment of the nano platelets that you can see a bit of in the SEM image (above at right) allows them to act together.
Under low stress, just rolling along, the platelets stay parallel to the road surface and that slippery single layer graphene bond actually reduces rolling resistance. Then under braking the rubber of the tire starts to deform, the front edge of the platelets turn down in the rubber matrix, and you end up with more edge grip. That is said to also improve cornering grip, as the same thing happens as the side edges of the platelets turn down with the flexing of the base rubber.
Then past the point of rubber deformation, the platelets are said to snap the rubber back to shape more quickly leading to even lower rolling resistance.
The Graphene+ tech can then be applied to varying degrees in both trail and road tires. Vittoria mixes in different amounts of platelets into multi compound tires for improved structure and grip where needed, while using harder faster rolling rubbers where they can.
On the mountain tires that means the orange & light blue compounds in the 4C tire can offer more support, while the harder red with G+ and softer blue with G+ can deliver a very fast rolling tire that has still long-wearing but grippy shoulder knobs. On the 4C road tires you end up with a similar solution that gets a fast rolling grey center, more sticky cyan shoulders, and super grippy purple edges, supported by the underlying stiff and fast red rubber that will never touch the road.
The end result is said to be better control of the performance character of each type of rubber in a multi-compound tire, without as much of the wearing downsides of the softer, more grippy rubber that is usually required to maximize performance.
Vittoria claims the top-level race tires end up being 3x longer lasting. The Graphene+ embedded rubber become stronger so effectively harder, which means it wears slowly but still reacts in braking. So far our use of the Corsa Speed tubeless clincher seems to back that up. With a bit under 1000km on the tires so far, they really do look almost new from a wear perspective. We’ve actually been trying to test their durability on some rough surfaces, so they do have a number of tiny cuts, but so far it hasn’t resulted on a flat out on the road. As for the Mezcal mountain tires, we’ve only put a hundred or two kilometers on them so far, and they seem to grip well and still look as new. We’ll spend a lot more time on both tires, as well as probably the new cross tires and even possibly the new Classics-ready wide tubulars when they are available, and will report back on their long-term durability and performance.
Vittoria claims that now with G+ added to the rubber, the tires are now “intelligent”, becoming effectively harder or softer depending on rider needs. It is an interesting idea, and we are curious to see how the claims stand up to the test of time.