If you were offered a brand new pair of carbon crank arms for $100, would you feel a bit skeptical? One thing riders never want to do is save a few bucks (or grams) on a part they don’t fully trust to perform. However, manufacturers constantly struggle to find cheaper, yet effective means of producing products. It’s hard to imagine they would invest in new ideas if they weren’t confident about the outcome…
A company called Carbon.Bike is currently raising eyebrows by combining the low manufacturing cost of forging with the weight savings of carbon fiber. They have created some very inexpensive forged carbon cranks, spiders and stems, and all the carbon bits are American-made in Raleigh, North Carolina. Their components are pretty darn light too, as a 170mm crank with a spider or chainring weighs in at just over 500g.
Potential customers will simply have to debate the advantages versus the unknowns – Do you trust a new company with a new manufacturing process? Is their experience in other industries enough to assume their bike parts will hold up? Does the low price tag scare you off, or tempt you to buy and try? Forge ahead for the details on Carbon.Bike’s cranks and stems…
Carbon.Bike’s components are made of a solid forged ‘structural composite’ which uses chopped carbon fiber reinforced with a Vinyl Ester resin molding compound. The creators claim their cranks share the same strength as forged aluminum arms but offer a much lighter weight. To describe the process in short form, advanced resins are used to bond the carbon fiber together in a high temperature and pressure mold. In about 8 minutes, a part is molded and ready for finishing.
The term ‘Forged Composites’ is a trademark of Carbon.Bike’s co-developers, and apparently they have products already being used in defense projects and elite car manufacturing. Their Indiegogo page makes no mention of how much testing has been done on their cycling components.
All threaded inserts for the carbon components are made from stainless steel, and threaded BB cups and axles are made from hard anodized aluminum.
Crank Arms:
The crank arms come in a wide range of lengths and are adaptable to almost any bike by selecting the correct chainring/spider, bottom bracket and spindle options. There are four options for different spindles, each built with the appropriate Q-factor for the application- Road, Road Disc/MTB Narrow, Boost/MTB Wide, and Fat Bike (coming soon). Carbon.Bike’s spindles fit any chainrings or BB’s compatible with Sram GXP.
Crank arms are available in the following lengths: 140, 142.5, 145, 147.5,150, 152.5, 155, 157.5, 160, 162.5, 165, 167.5, 170, 172.5, 175, and 177.5mm. Crank weights (includes arms, 156 Q Axle, preload ring and spacers, paint and screws) range from 365g for the shortest 140mm option up to 435g for 170mm and 445g for 175mm.
The cranks can be purchased with an armoured black finish or with painted stripes in ten different colors. Firearm paint is used as a finish as opposed to clear gelcoat, as it is much stronger and lighter.
Chainrings/Spiders:
If you’re running a 1x drivetrain, you might want to add a front ring. The chainrings are made of hard-anodized aluminum, and the sizes/weights are as follows: 30t /67g, 32t /70g, 34t /78g, 36t /85g.
For double ring road or MTB 2x or 3x setups, you’ll have to add a spider. The spiders are made from forged carbon with stainless steel eyelets. With paint, the Road Double 110 BCD weighs in at 65g, and the MTB 104 BCD at 69g.
Stems:
Carbon.Bike is also producing MTB stems with their forged carbon process. The company says stems are an ‘ideal product for forged carbon manufacturing’ and apparently they can produce one in mere minutes. 40, 50 and 60mm lengths are available, all with the option for 31.8 or 35mm clamps. The stem weights, including paint and screws, are as follows- 40mm/110g, 50mm/130g, 60mm/150g (weights are listed the same for either clamp size).
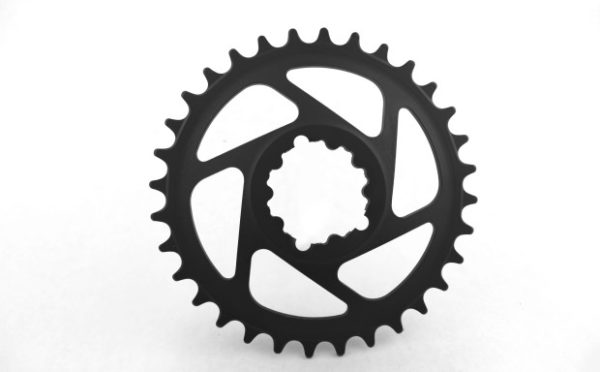
As a ‘Launch Special’ customers can buy any size of crank arms with your choice of the three available spindle options (Fat Bike currently excepted) for just $99 USD. Fat Bikers will have to buck up $129 for the arms with a longer spindle.
A single front ring can be added to the arms for $35. Alternately, you can add a 110 BCD road spider with a ti bolt kit for $39, or the 104/64 MTB spider for the same price. Also, for an additional $19-29 you can slap some painted accents on the crank arms. The company is also offering a selection of bottom brackets and BB tools. Stems can be purchased in any length and clamp diameter for $89, and come with titanium bolts. Paint can be added for $19.
Carbon.Bike says they will work with buyers to ensure they get the right fit for their bike before the product is shipped out. If this campaign is successful, estimated product delivery is for May 2016. Furthermore, the company has plans for several other components including forks, rims, cassettes, seat posts, bars, and eventually frames. Their Indiegogo campaign currently suggests skepticism might be outweighing interest, but if you want to learn more about forged carbon components check it out here.