Maybe it’s fitting that the first rider to win the Tour de France on a carbon bike also has his hand in what’s being called the future of carbon fiber. On the surface, it might be difficult to grasp just what is going on in Oak Ridge, Tennessee, but it’s bigger than just bikes. What initially started with Greg LeMond’s search for a better way to produce carbon fiber bike frames domestically has turned into a potential game changer for the construction of anything that moves.
While LeMond’s name is on the building, Greg is just one part of a world class team with some of the best and brightest minds in the world of composites. The story may continue with LeMond Composites, but it started with the Oak Ridge National Laboratory and their Carbon Fiber Technology Facility which was started by Connie Jackon, now President of LeMond Composites. After pioneering a new carbon fiber production technique with drastically reduced costs, the technology was licensed to LeMond Composites for commercial development.
What does that mean for the future? During the presentation at the opening celebration, Greg said that this won’t just usher in a new line of LeMond bikes, but this technology “will change the world…”
How will a new process to create carbon fiber change the world? According to LeMond and the staff at the ORNL it all starts with the “Holy Grail of carbon fiber.” Apparently, that was the term given to the theoretical carbon that could be produced at $5 per pound in 1989. If someone was able to produce a carbon fiber this affordable, it would have drastic implications on many manufacturing and transportation sectors as it would allow anything that moves to be made lighter, more efficient, and more affordably. At least once over the course of the night it was mentioned that at that price, carbon fiber would be cheaper than aluminum.
When LeMond Composites talks about creating a new low cost carbon, they aren’t talking about assembling bikes from carbon sheets – they’re talking about actually making the individual carbon strands that go into that carbon fiber. According to Edward Western, a carbon fiber consultant who has been engineering carbon for as long as it’s been used in bikes, at least half the cost of carbon fiber comes from the raw material itself. In order to reach the Holy Grail, they would have to find a way to start with a cheaper raw material.
That’s exactly what the ORNL team, led by Connie Jackson, did. Using the pilot line shown above, the team was able to demonstrate commercial viability of the new technique that turns raw fibers into strands of lower cost carbon fiber. The fibers are stretched and pulled through ovens that oxidize the acrylic fibers turning the martial into carbon – the higher the heat, the stiffer the carbon (higher modulus). Of course, describing it that simply doesn’t do the process justice, but ORNL and LeMond were keeping the actual details of the process close to their chest which is why we weren’t allowed to take pictures of the actual machinery. As you can imagine if the Grail carbon fiber, as it’s being called, turns out to be as big of a revolution as they expect, you don’t want to be giving away your secrets.
Once that fiber is created, it can then be used in any of the ways carbon fiber is currently used. That includes carbon filament, woven fabrics, chopped and injection molded, and more. Not only does cheaper carbon fiber stand to revolutionize the transportation industry with lighter vehicles, the process of making Grail fiber also uses less energy compared to conventional carbon production improving the “green” potential even more – the future might even hold a way to make carbon fiber strands out of recycled material. The Grail fiber also provides improved bonding between the fiber and resins which causes it to perform better than it theoretically should. Really, the only draw back of the Grail carbon is that it probably won’t qualify as aerospace grade. That will mean it won’t be used to build planes or rockets, but it could finally make things like carbon fiber shipping containers a reality.
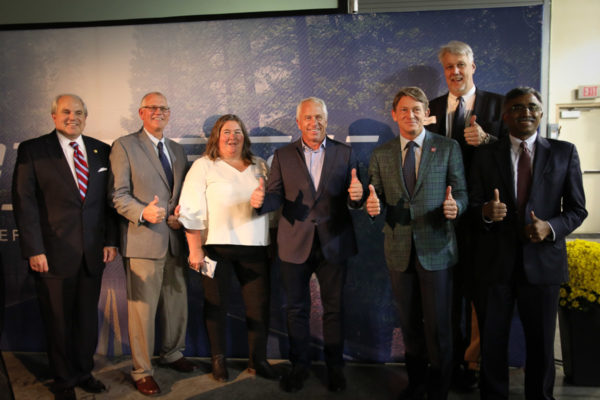
Located right next to the ORNL Carbon Fiber Technology Facility is the new LeMond Composites headquarters. This building will serve as LeMond’s head offices but the actual carbon fiber production facility is yet to be built. LeMond plans to construct the factory in close proximity to their headquarters and will keep all of the production in Oak Ridge, TN which will bring 242 new high paying jobs and a massive amount of business to the area. LeMond Composites is still securing funding but with interest from major automotive manufacturers, not to mention other bike companies, it seems like it’s all but a sure thing that this will indeed be the future of carbon fiber.
No timeline was given as to the arrival of new bikes, but we were told that prototypes are in the works and that LeMond Composites will be holding a job fair in 2017 to staff the facility.