The latest piece of performance bicycle jewelry from Industry Nine has nothing to do with your wheels. Instead, I9 is living up to the new “Industry Nine Componentry” name with an all new stem. Starting with the shortest, and likely stiffest options, the A35 is the first stem from I9 and it originates from the same Asheville, NC facility that has been turning out their hubs, spokes, and axles for years.
One of the benefits of owning your own manufacturing facility is that with the right equipment and engineering & testing brain power, you can pretty much create whatever you want. The design of the A35 started out in the hands of I9 designer and engineer Jeremy Hume, who worked directly with the highly skilled machinists at Turnamics Inc. next door to figure out how to turn solid billets of aluminum into finished stems. As a refresher, Turnamics is the machining business owed by the same family, of which Industry Nine was their ninth business venture.
Once the design and manufacturing was in place, Jeremy devised a testing rig based on the Syntace method which is known for going past the typical industry standards. Initially, the strength of the Industry Nine A35 proved to be too much for the test rig, and the solid steel steerer tube snapped off the block where it was welded together. From there, Jeremy created a new steerer tube assembly that was one solid piece of steel.
Now the test rig was holding up to the pressure, and it allowed I9 to see just how far their stems would go. While running up to 600Ft-lbs of torque in various phases, Industry Nine’s stems were lasting past 50k cycles, only to have the bolts finally break as the weak link. Compare that to their competition which they claim to have tested only to 30k cycles because the bolts end up loosening or breaking long before they reach 50k cycles.
Industry Nine attributes that strength to the use of 7075 aluminum which is a better material to begin with, which is then 100% CNC machined from a solid billet – which is where the A35 gets its name, from the A-axis of their 5-axis machining centers. The result is a beautiful little stem that is designed, machined, anodized, and assembled, all within their Asheville, NC facility.
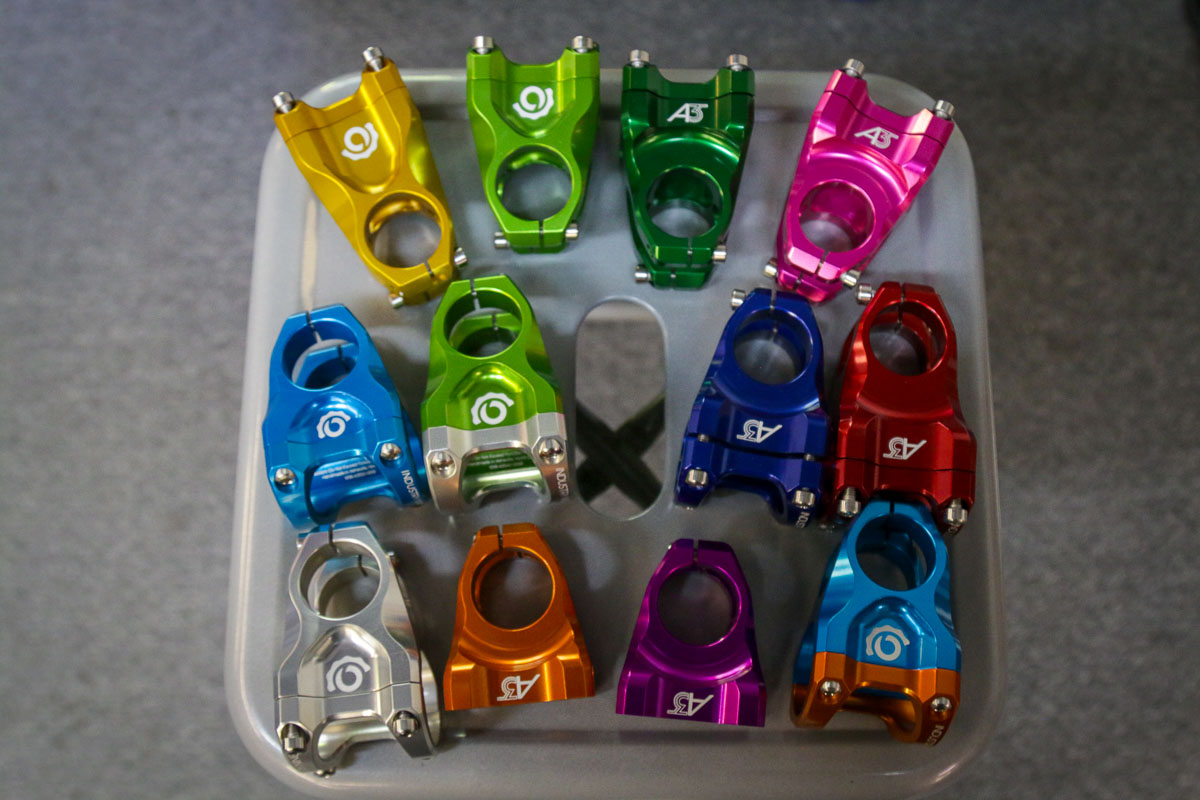
Like their colorful hubs and spokes, the A35 stems will be available in 11 different anodized colors with the option to mix and match bodies and face plates. They’ll also be available in 32, 40, 50, or 60mm lengths, all with 35mm bar clamps and their own unique degrees of rise. Pricing is set at $125 for a solid color stem, or $140 for the mix and match combo.

First Impressions
We were lucky enough to get our hands on an early sample, and can confirm that they are as nice as they look. Shown above is the 40mm version.
On the scale, the stem comes in at 135g – exactly as claimed.
That includes the precision stainless bolts included with the stem.
Installation went as smoothly as you’d expect with a super premium stem. The stem oozes precision from how well it fits onto the steerer and bar, to how smoothly the bolts turn when you’re torquing things down (7-9Nm at the steerer, and 5-7Nm at the bar).
Considering it’s just barely more expensive than a Thomson Elite 35mm X4 stem in a solid color, we won’t blame you if you buy this on looks alone – especially if you have matching hubs. Available now.