Nestled away in the Pentland Hills just outside of Edinburgh, Scotland, Five Land Bikes are quietly making a name for themselves as quality steel bike frame builders. Stepping up the volume, Matt and Callum are now fabricating for Cotic and Swarf. If you’re thinking of buying bikes from either of these brands, it is highly likely it, or at least one of its two triangles, originated right here. I took a trip up to the workshop for an educational experience and an inside look at the set-up.
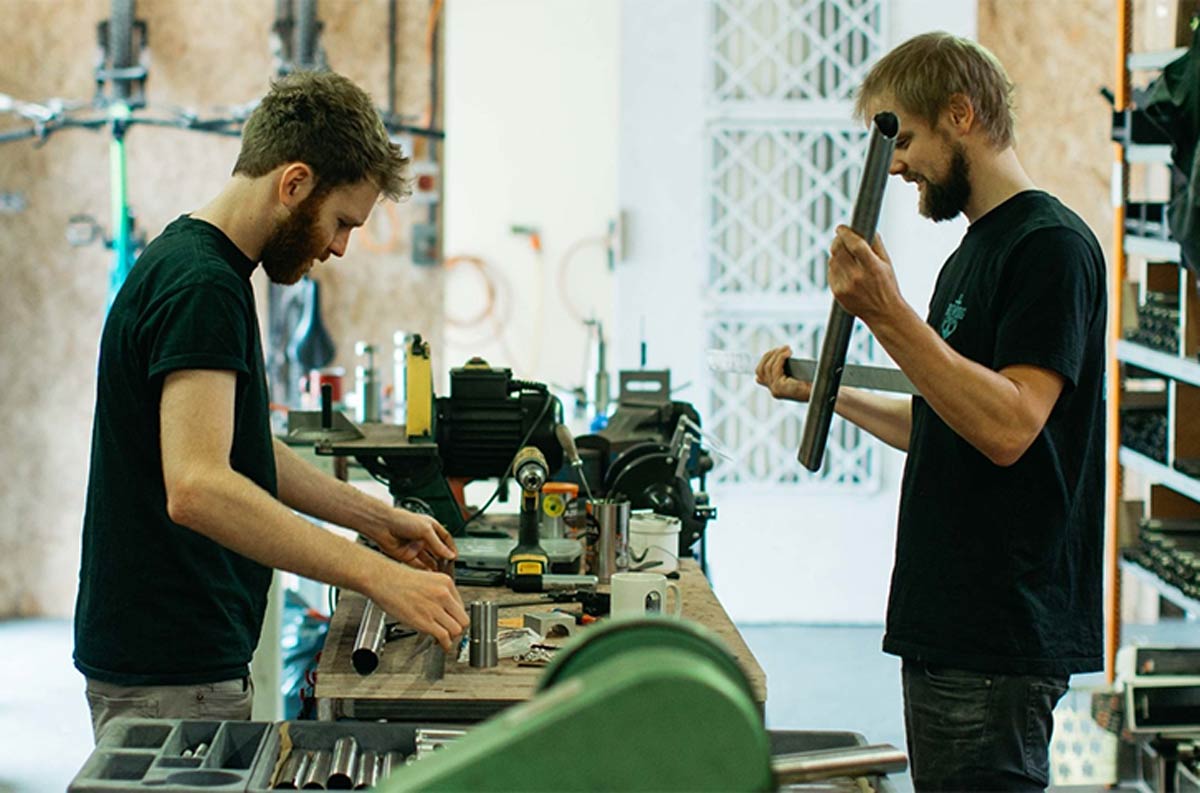
Matt and Callum met at Robert Gordon University in Aberdeen where they both studied Product Design. Matt went straight to work for Shand, the boutique gravel bike fabricators based in Livingston, Edinburgh, where he specialised in welding for 4 and a half years. After travelling in Australia for some time, Callum made the jump back to Scotland just as Shand were expanding the team, and took on a role in the workshop in fabrication; cutting tubes, brazing, welding, the lot.
With the experience of gravel bike fabrication behind them, the pair took the leap to go out on their own with Five Land Bikes, originally named Fisher and Stitt (their surnames). They set up in an old farm on the edge of the Pentland hills, just outside of medieval Edinburgh, and got to work on the not insignificant task of renovating an old shed (with ferns growing out of the walls).
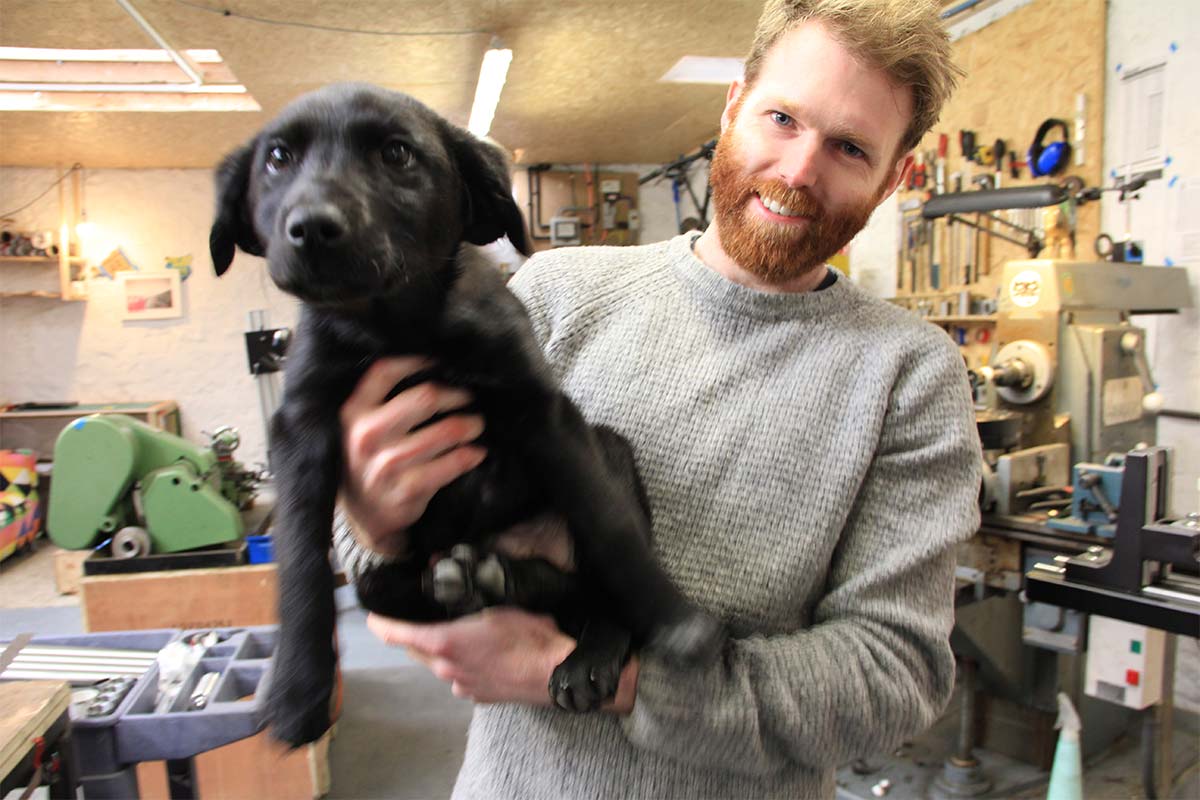
12 months down the line, Fisher and Stitt are now Five Land Bikes, fabrication is in full swing, they’re inundated with build requests, and they even have a workshop mascot to boot – meet 14 week-old Labrador Collie cross, Scout. Can I take him home with me?
It’s been a steep learning curve for the pair; running a business for the first time and learning how to fabricate full suspension bikes. Everything they worked on at Shand was gravel, save for an original Cotic longshot prototype.
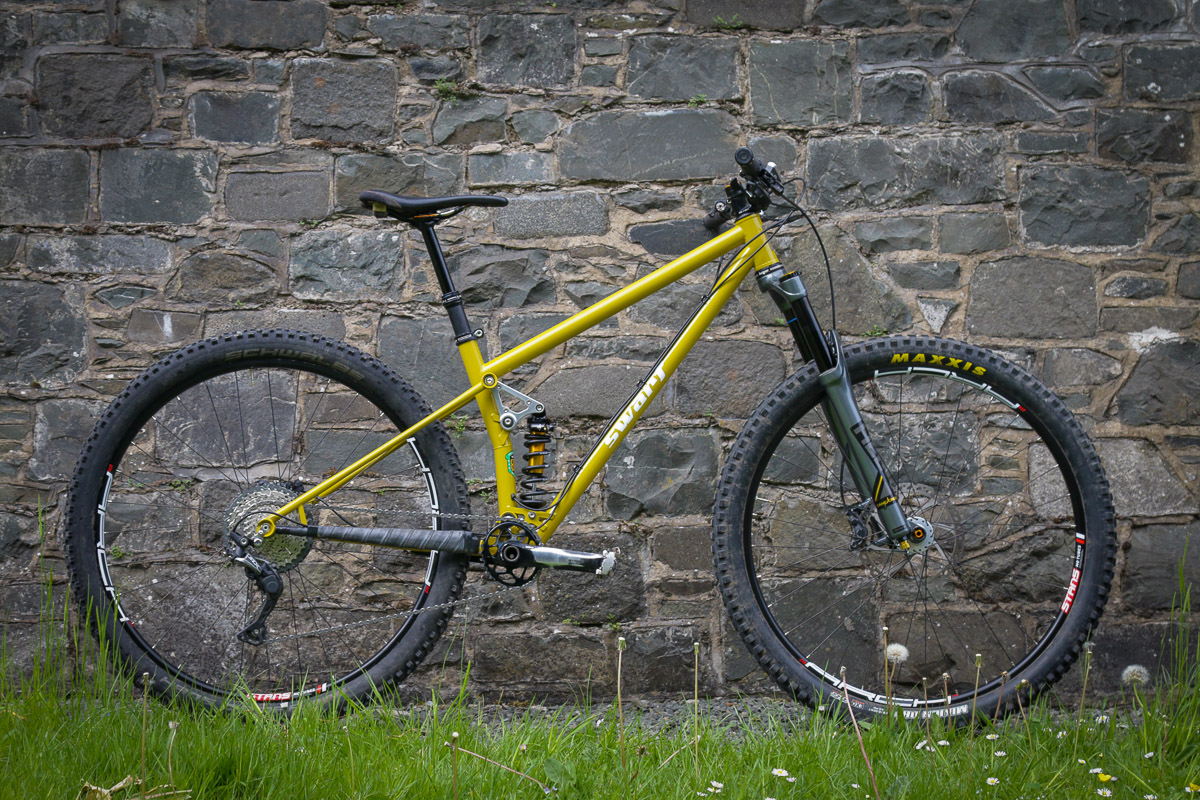
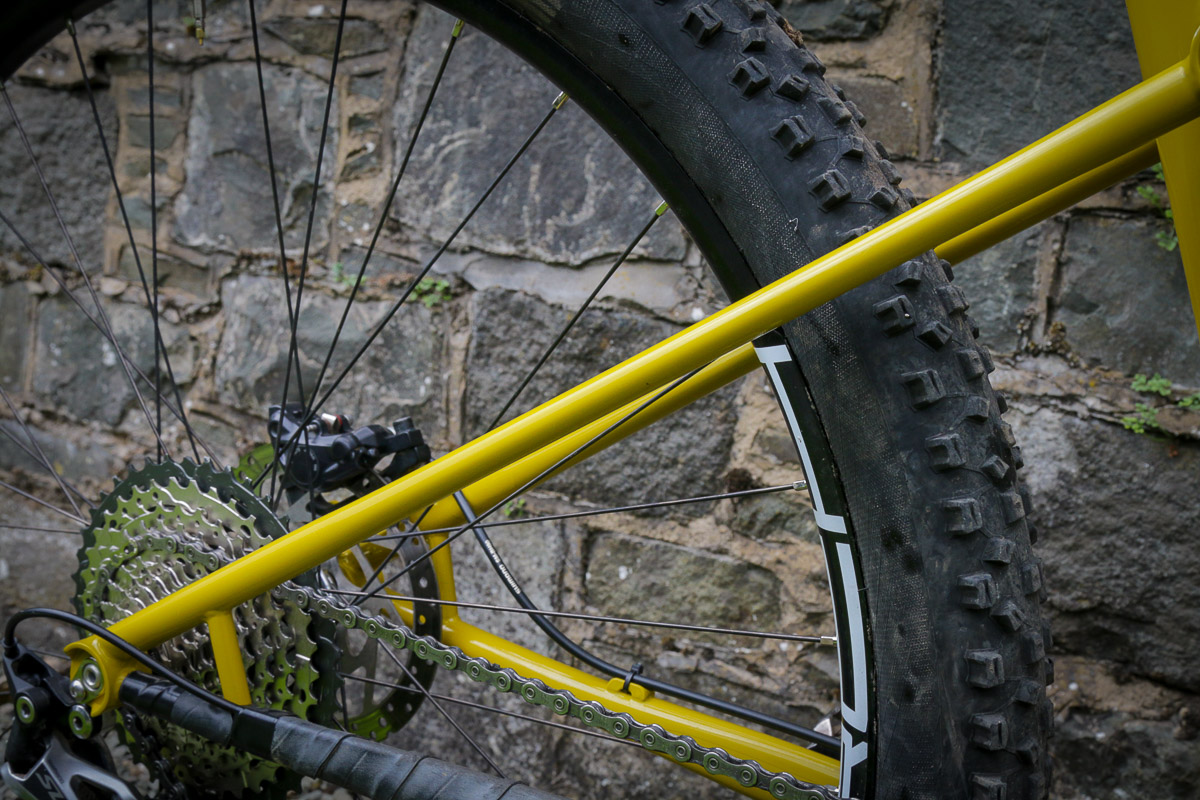
Five Land Bikes have significant collaborations with two brands; Cotic, a UK brand based in the Peak District, and Swarf, a Scottish brand owned by ex-aerospace engineer Adrian Bedford, based in the Tweed Valley.
For Swarf, Five Land Bikes fabricate the swing arm. The collaboration between these two businesses is allowing Swarf to grow without the need for a larger workshop or the huge investment in additional tooling and machinery.
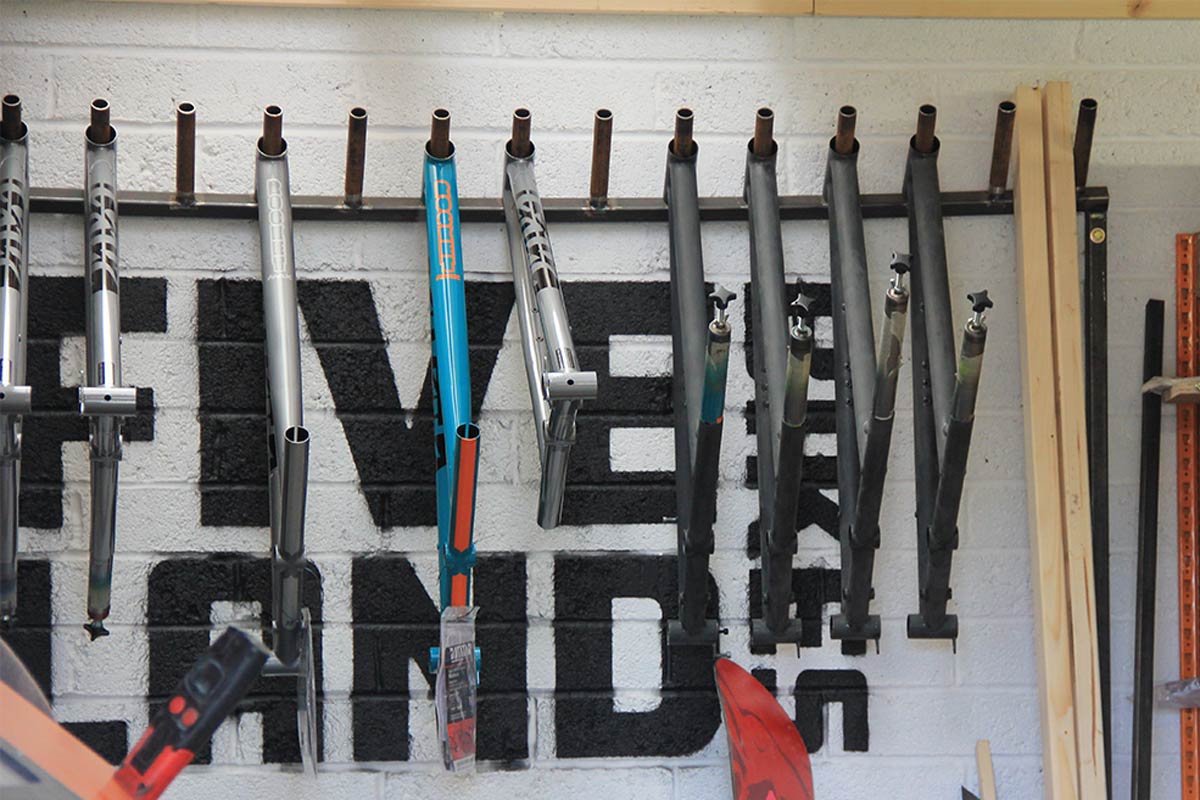
For Cotic, Five Land Bikes have a bigger operation underway. If you bought the Cotic Rocket MAX long shot that was launched in October 2018, this is where it came into being. Matt and Callum receive tubing straight from Reynolds, including the Cotic-specific ovalform custom-butted top tube, and they fabricate and paint the front triangles on site.
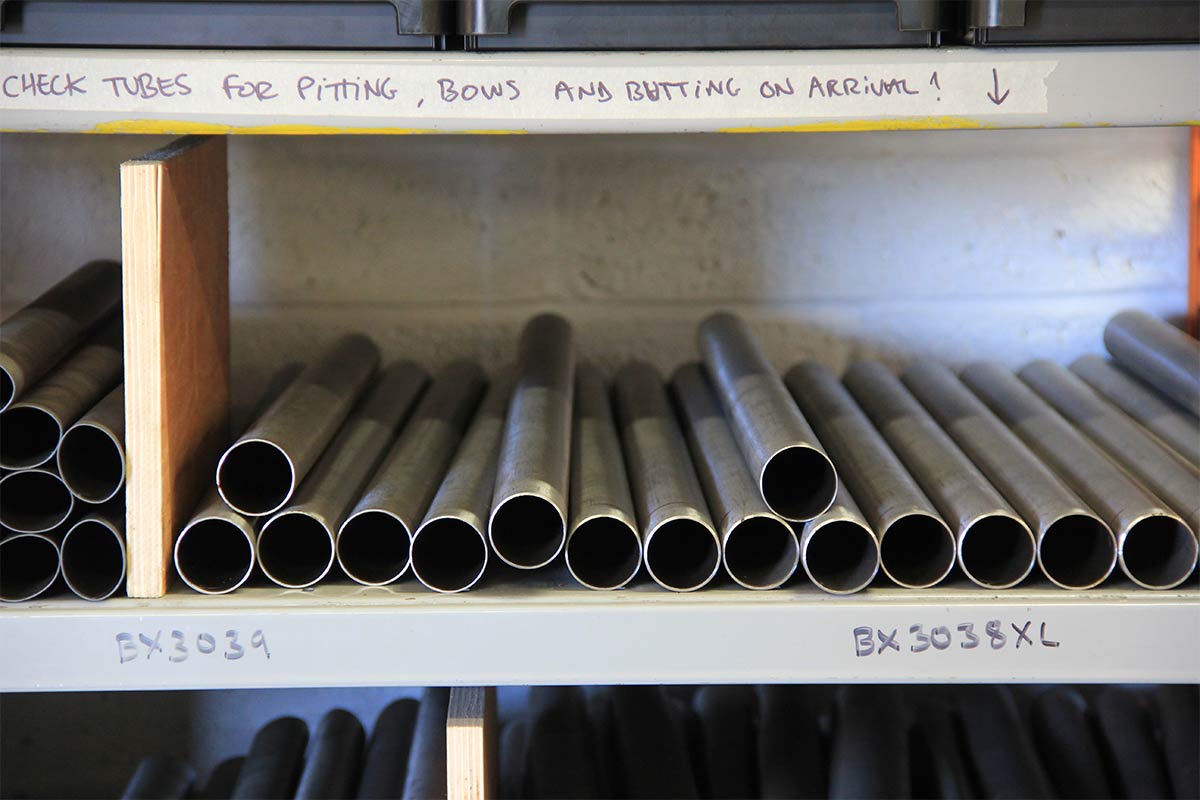
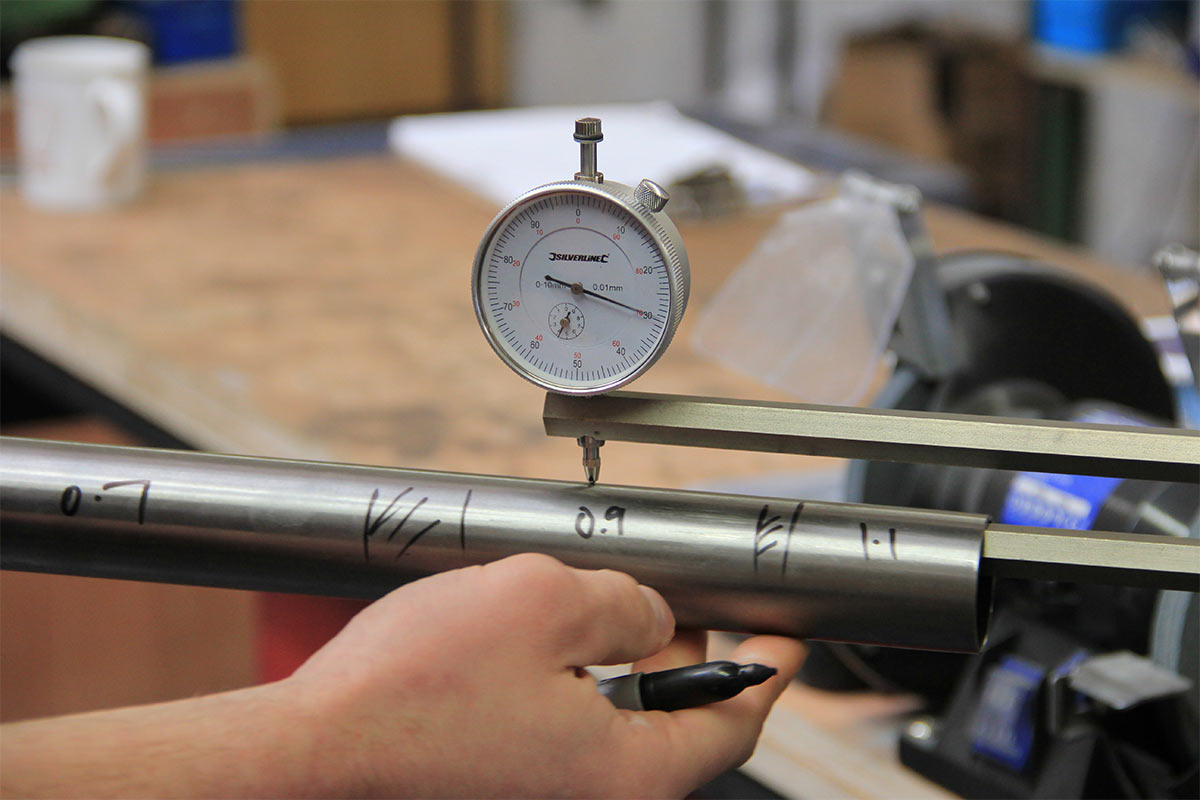
The process begins with thorough quality checking of tube thicknesses, including checking the accuracy of the butting profiles, and checking for bows and pitting in the steel.
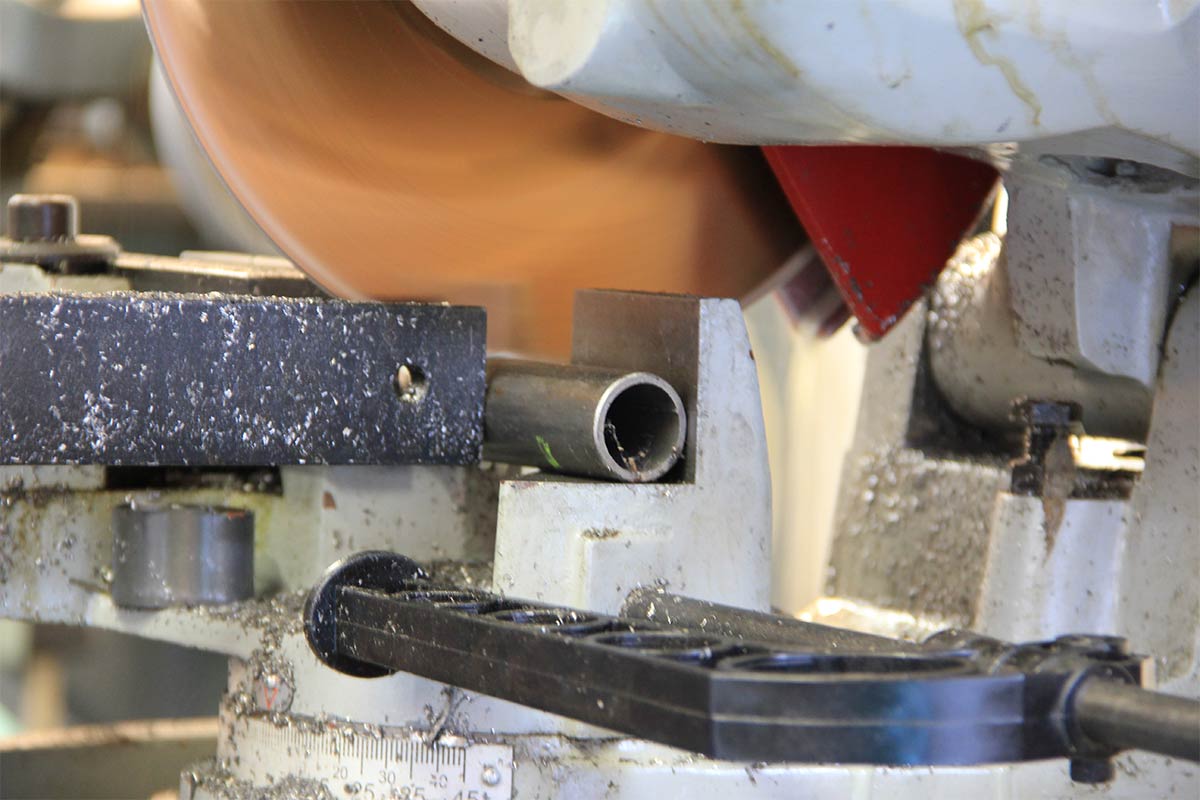
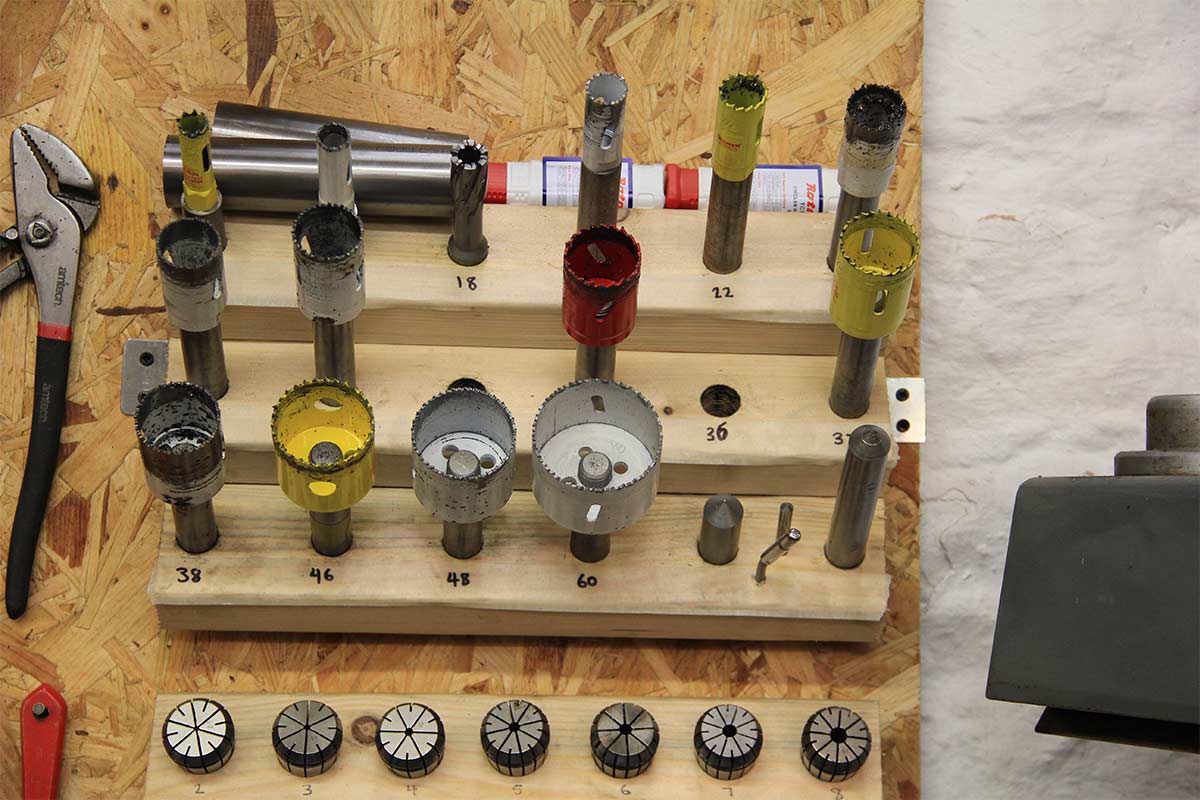
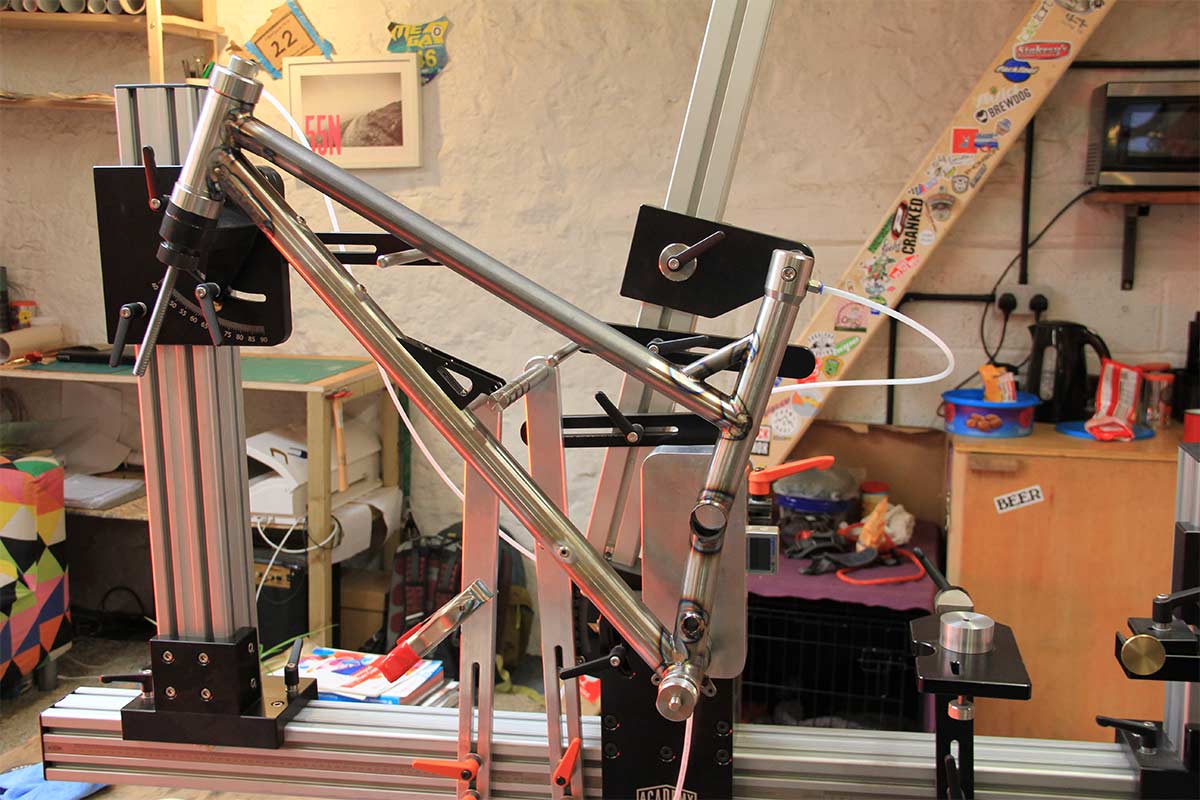
Next, tubes are cut to size and a hole saw is used for mitering the tube ends at an angle for a flush join between adjacent tubes. Cut tubes are hooked up to the jig (adapted for Cotic bikes), and tacked together with a filler rod before the tig weld process begins. It is difficult to know what temperature is reached by the arc of the welder as it is attached to the foot pedal which means it varies a lot. Tig welding is a fusion process whereby the base metal (tubing) is melted and joined together with the addition of filler rod to add material and strength. Each joint is welded in a specific sequence for reproducibility and to ensure it stays as straight as possible.
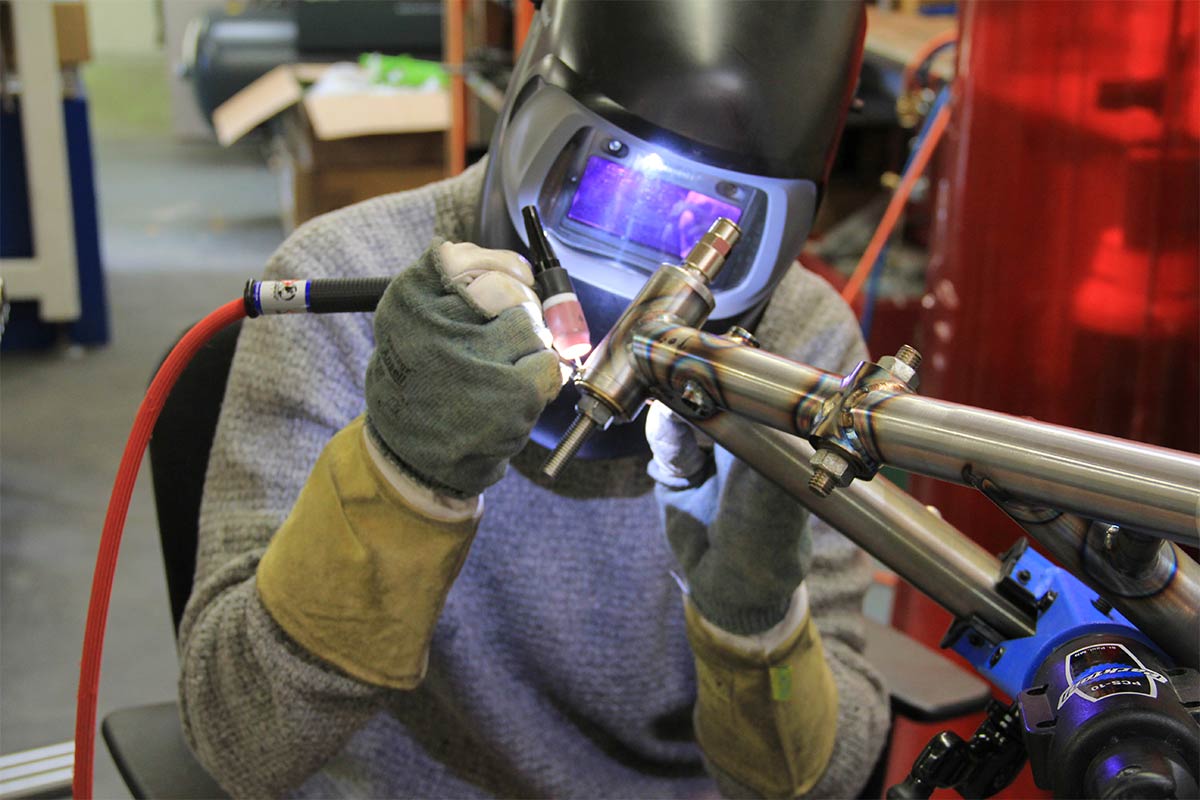
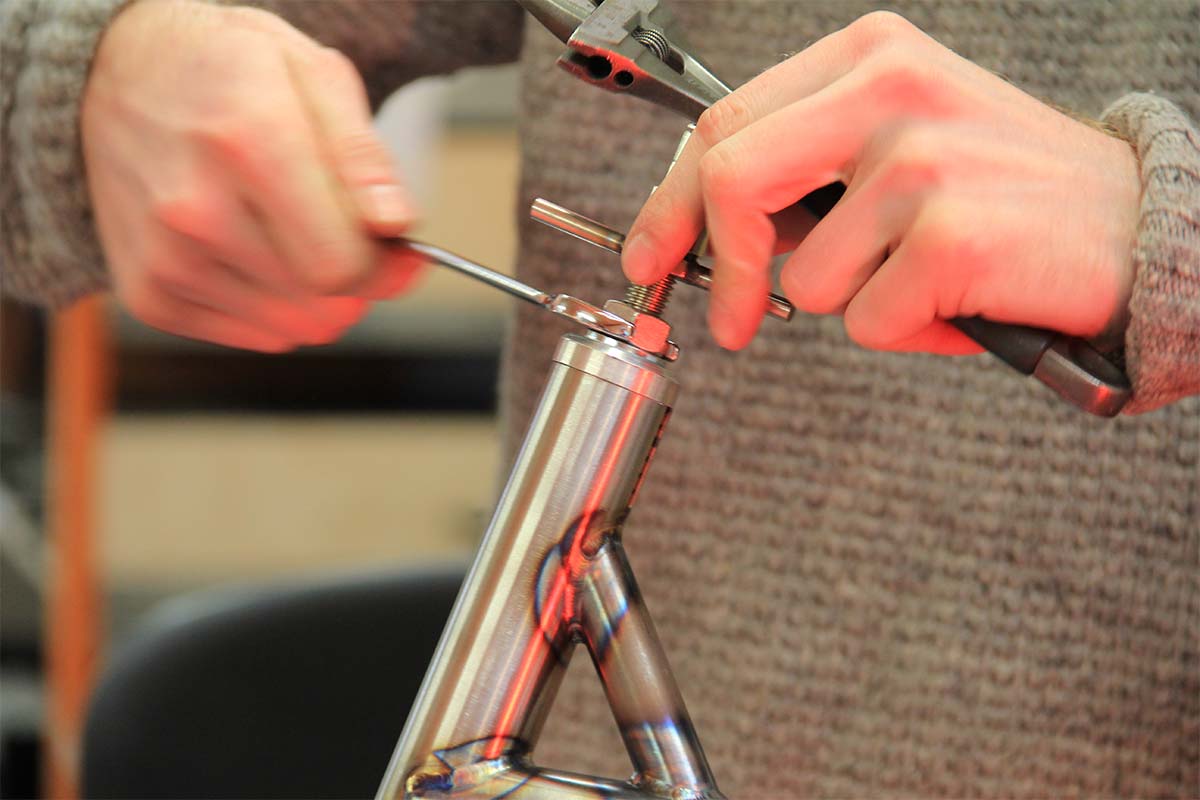
To prevent oxidation of the steel during the weld process which can cause brittleness, inert Argon gas flows out of the weld torch onto the weld surface to push away the oxygen-containing room air. Matt and Callum have designed and produced their own heat sinks in house. These brass contraptions insert into the tubes and expand inside them so they are flush to the inside surface of the tube. During the weld process the heat sink absorbs some of the heat energy to prevent distortion of the tube. This makes reaming and facing after welding much easier, and it can also improve the quality of the weld by reducing the size of the heat-affected zone. Matt and Callum also use these heat sinks to seal off tubes, purging them of air by flowing Argon through the tubes – this is particularly important when welding stainless steel or titanium.
Aluminium shock mounts are bolted to the downtube with tight-as-you-like 0.1 mm precision. These tight tolerances are important to ensure the bike’s geometry sits just as intended by Cotic’s frame designers.
Five Land Bikes also paint the Cotic frames in house. The paint contains isocyanates so Matt and Callum wear an air-fed mask and gloves to protect themselves from these aerosolized nasties. A make-shift oven then bakes the paint on at 65 degrees celsius to help cure it to a hard durable finish.
Also kicking around in the workshop was this Klunker Matt made while still working at Shand. Matt put this together at the Hack Bike Derby put on by the Bicycle Academy in 2016.
It would be rude if I signed off without a goodbye from this wee man. Every bicycle frame workshop should have a mascot! It is clear that Five Land Bikes prioritise quality frame building over everything else. They created this business to do what they love doing most, building bikes. It is no surprise to hear that they “can’t make enough” and that they are completely inundated with requests for builds and prototyping. Though they have no immediate plans to build a Five Land Bikes own brand frame, they’re pretty sure it will happen at some point in an organic fashion. What they do know is that it will be a bike that they like to ride, and if others like riding it too, well that’ll just be an added bonus.