Like most truly great products, the Hope Bike line was born from the brand’s desire to build a bike that they wanted to ride. For years and years it was always a dream of founders Ian Weatherill and the late Simon Sharp that they would one day ride bikes of their own, made in their own factory. Hope jokes about the fact that if you put a price on the development beforehand, it never would have happened – the investment has been astronomical. But then again, Hope has never been about doing something the easy way. For Hope, it has to be made in house, and it has to pass very high standards. That’s how it’s been for the past 30 years, and it seems like that won’t change in the foreseeable future.
After years of designs never making it past Design Engineer Guillaume Leon’s desk, five years ago things started happening. After assembling a small team of carbon experts, the first HB.160 sprang from the mold in 2016. It ended up launching in the summer of 2017 with sales starting later that year, but before it hit the trails Guillaume was already hard at work on the next model.
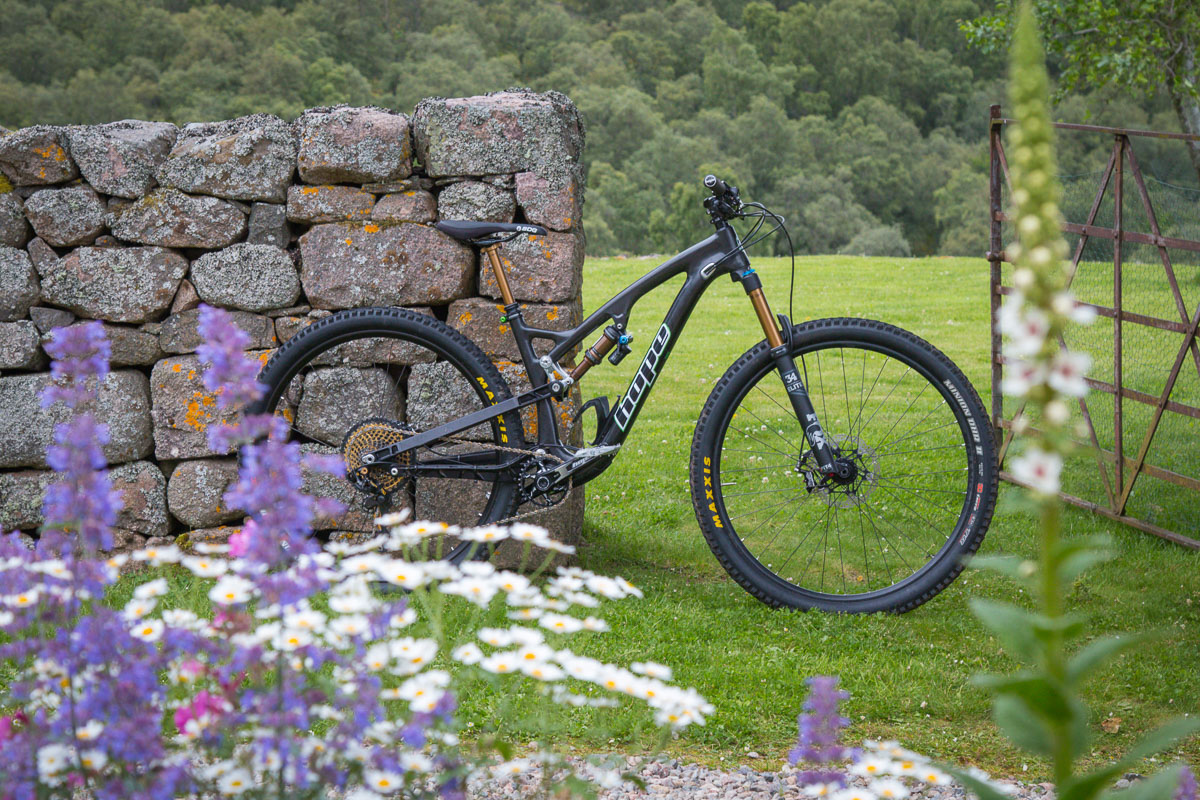
At the time of the HB.160, mountain bike development was changing quite rapidly and while there was a chance that the bike would be outdated quickly due to changing trends, it served as a huge learning experience. Happy with the suspension design, Hope really wanted to make a short travel 29er with improved geometry – something they saw as the perfect all-rounder. The result is the new HB.130, a 130mm travel 29er meant to pair with a 140mm travel fork.
As it happens, the geometry ended up changing three times during development but that’s something you can do when you make your own molds. Most carbon fiber frame molds are made from steel because aluminum molds are more costly and less durable in the long run. But when you have the ability to make them yourself, the cost is more attainable and the ability to quickly change small details is priceless for a small manufacturer.
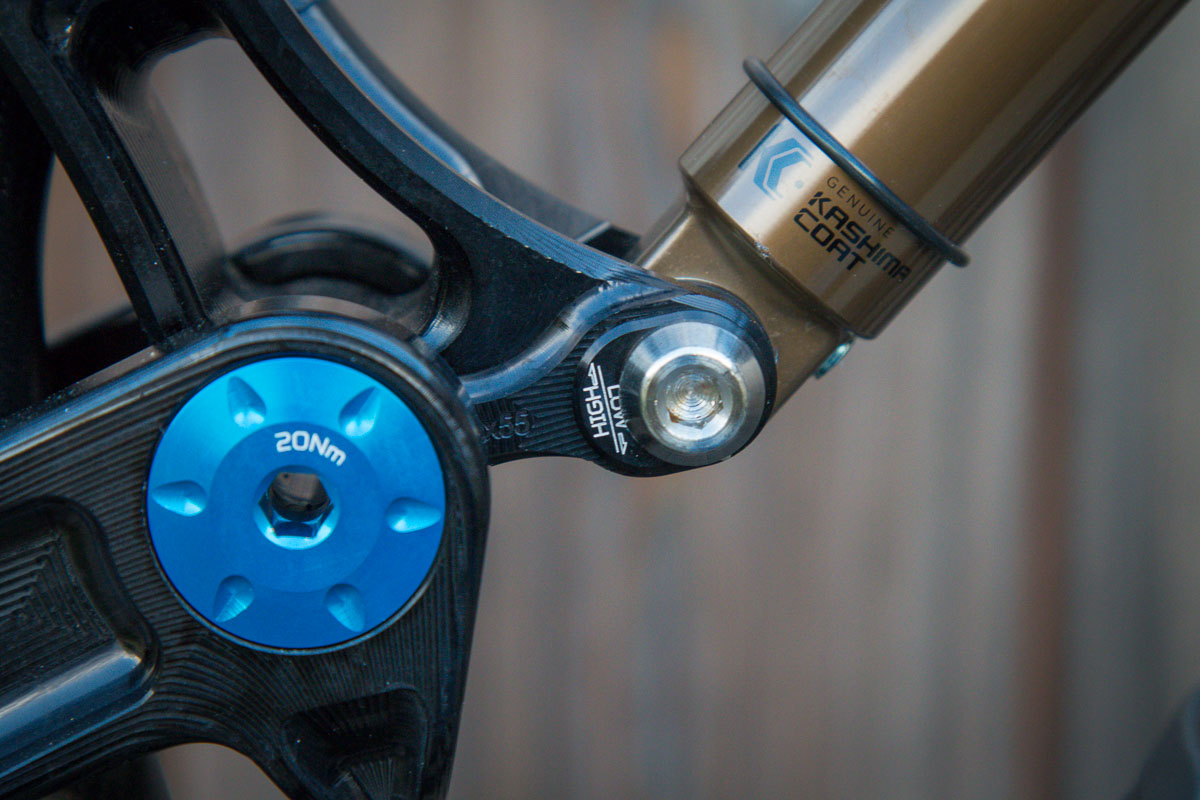
Adjustable Geometry
Those changes in geometry led them to a bike with a slacker head tube angle, steeper seat tube angles, and longer reach numbers along industry trends. They also added a flip chip which changes the head tube angle from 66.5 to 66° and drops the bottom bracket by 6mm. Comparatively, the geometry of the HB.160 is fairly conservative. Hope says that hasn’t stopped the bikes from selling though, they’re about to sell their 300th bike. That may not sound like much, but it’s a handmade frame that takes a full day to manufacture each one.
Meticulous Carbon Tech
All of that carbon is meticulously laid by hand. Hope actually gave us a look at the care that goes into laying up each frame which is something that not many manufacturers provide. It’s a lot more labor intensive than you might think – the pieces are sticky and have to be positioned perfectly. It’s also done in a way that results in a near perfect finish straight from the mold.
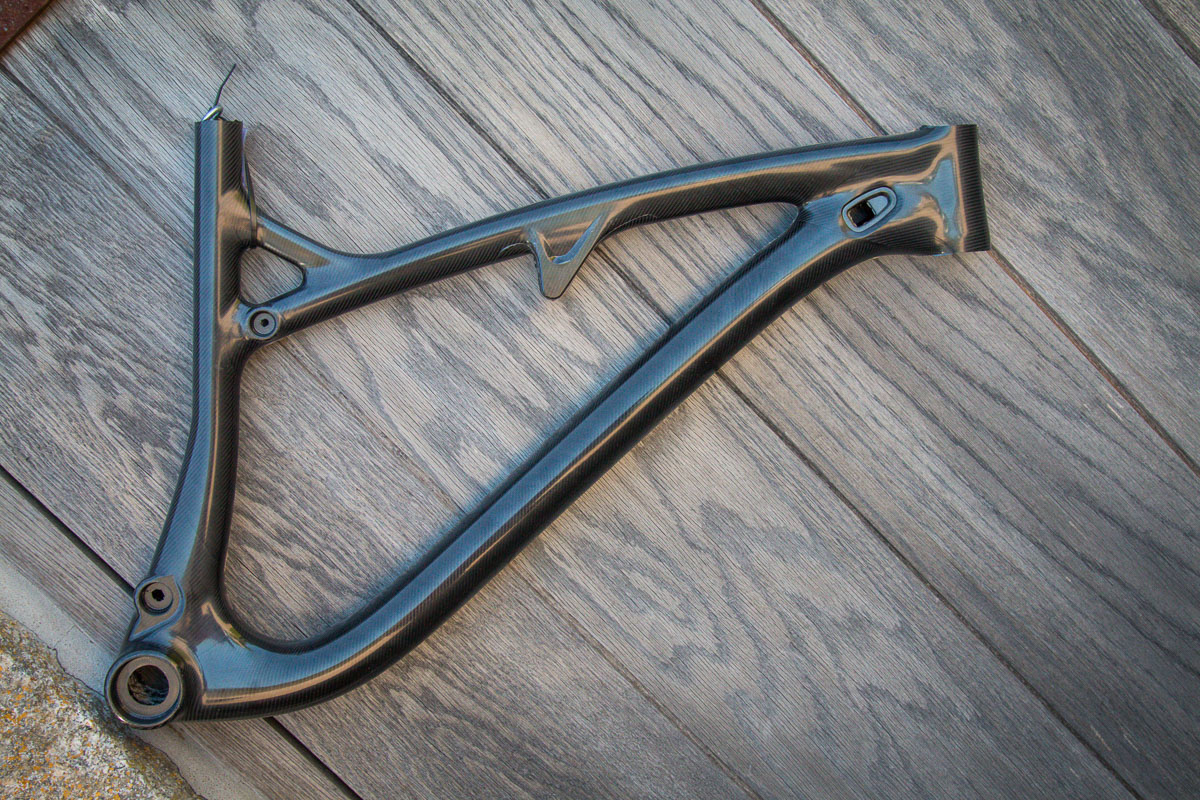
Sure there’s a tiny bit of flash that needs to be removed from the seams of the mold, and the bearing bores need to be machined, but the finish of the raw frames straight from the molds is stunning.
Once those frames are removed from the mold, they’re hand sanded and the final lacquer is also applied by hand.
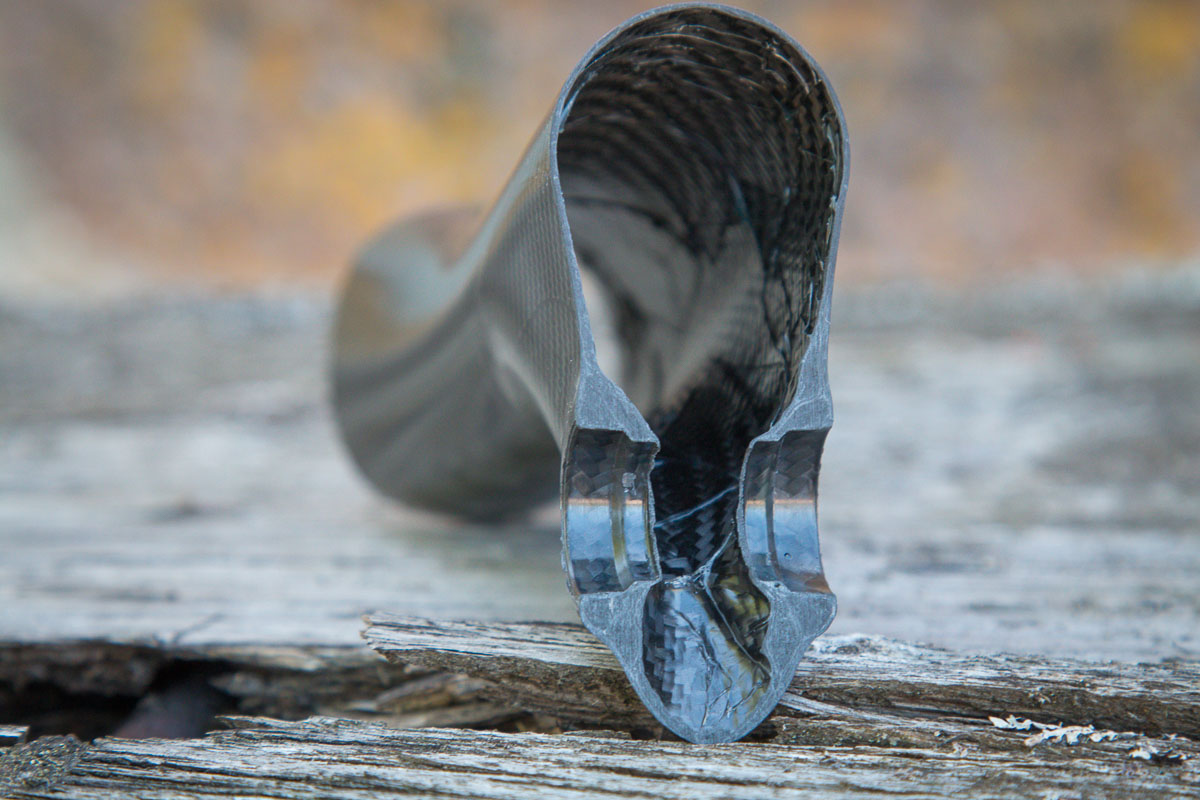
Through the use of more T700 carbon fiber Hope has reduced the weight of the HB.130 front triangle by about 100g, but it’s still built to last forever rather than being super light – though the actual frame weight was not available.
Machined & Bonded
Carrying forward from the HB.160, the HB.130 also uses a machined and bonded aluminum swingarm. Apparently Hope has considered the addition of a carbon fiber rear end but for now, the aluminum parts are allowing the bikes to get out the door and they’re also strong. Like, really strong. Hope points out that “as Engineers, they don’t really like glue, but we’ve come to trust it.” That trust seems to stem from the fact that in all of their fatigue testing, the bonded parts have lasted longer than welded parts with the welds always proving to be the weak link. With bonding you don’t have to heat treat anything, and the parts are perfectly aligned as soon as their bonded together. Apparently, the extruded aluminum tubes for the stays are the only parts not made in the Hope Factory.
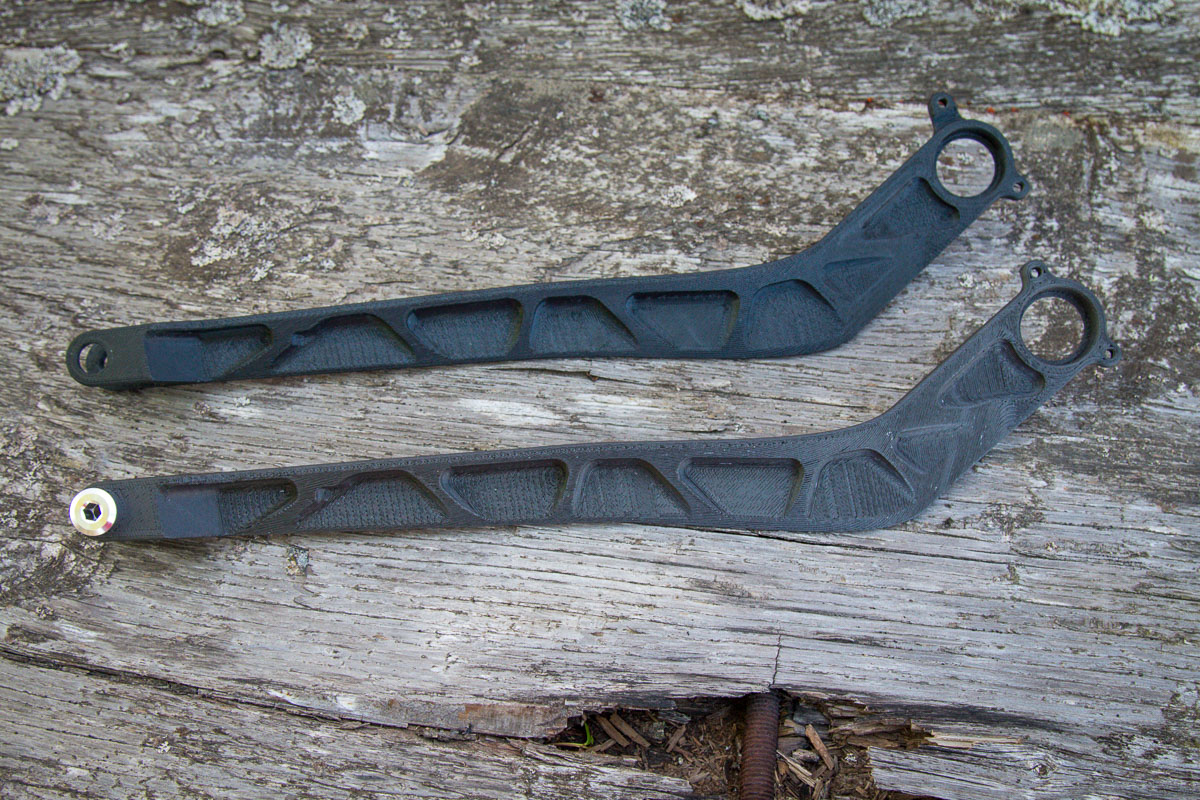
Custom 130 x 17mm rear end
Those aluminum stays also house one of the more interesting design features of the HB.160 – a 130mm rear hub with a 17mm axle. When you make the frame, the hub, the axle, and even the bearings, there’s no standards you have to adhere to. Rather than go super wide like the bikes moving to Super Boost, Hope wanted to make a frame with a stronger, stiffer wheel that still had a narrow back end. Most importantly, they wanted to build a rear wheel with zero dish (the same distance from each hub spoke flange to the outer locknut). To do so, the driveside of the hub is actually positioned in the same place as it would be on a Boost hub. But the non-driveside is shifted inwards, removing the gap between the hub flange and the rotor mount to remove unused material and create a centered wheel.
In this scenario, the frame is essentially dished around the rear hub. That places the rear derailleur in the same spot as it would be on a Boost 148 bike, but the disc rotor is farther inboard, making for a narrower rear end that’s easier to thread through tight trails. The hub itself it held in place by a 17mm axle. Why 17mm? That happens to be the largest they could go while keeping the same large, durable bearings in the rear hub. Thanks to the burly axle and stout chainstays, the rear end is plenty stiff and Hope says that the design has actually led to improved bearing life out of their rear hubs.
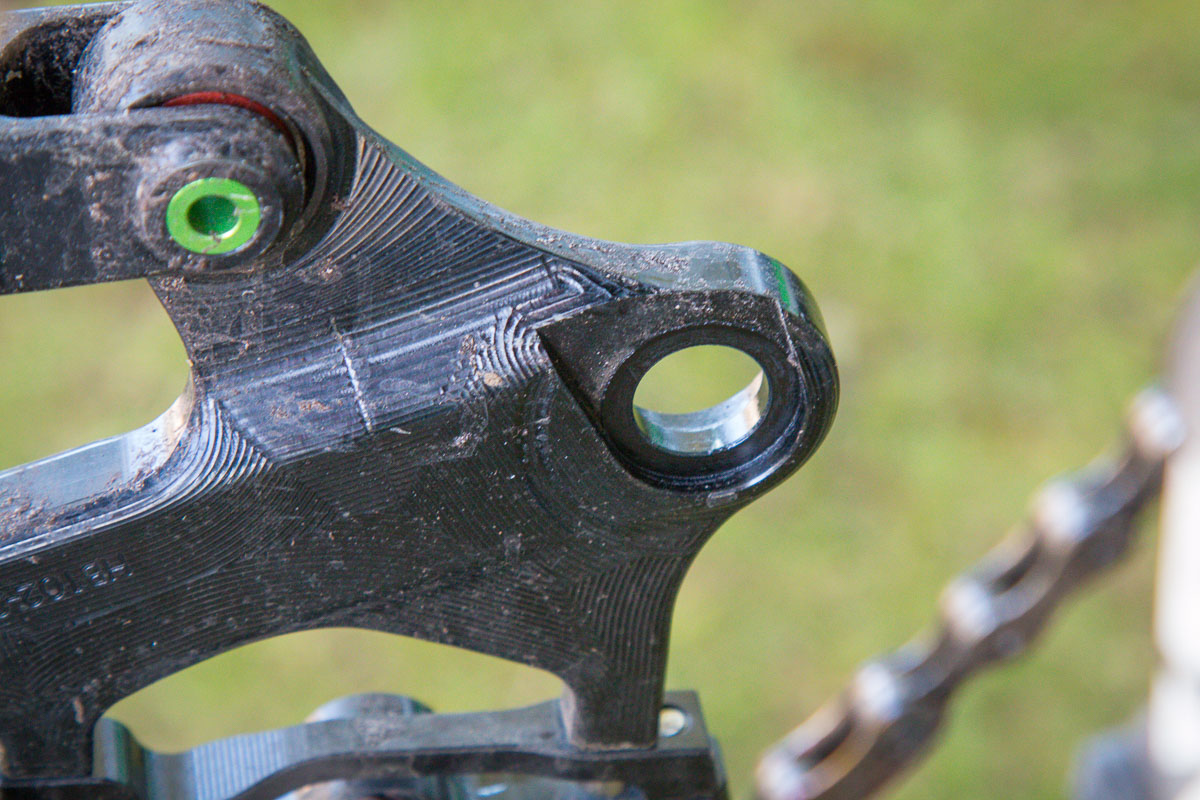
One thing to note however – the design of the hub means that when the wheel is out, the cassette feels loose. This is completely normal. Tighten the axle down and that play goes away. There’s also a retaining clip to keep the freehub from falling out while the wheel is removed. The design of the hub and the frame also means that the rear hub is specific to the frame. That’s why framesets will include a proper HB branded hubset that you can lace to your preferred rim.
The HB.160 also made the move to radially mounted rear brakes since once again, Hope was building everything so they could build a better system. But in order to give riders who purchase a frame more rear brake options, they’ve moved back to standard post mount to make it more standardized.
It’s worth noting that there is plenty of mud clearance for a 29 x 2.3″ tire in the rear, but not much more. The bikes are speced with a 29 x 2.5 WT Maxxis Minion DHF out front and a Minion DHR 2.3 out back.
While we’re on the topic of proprietary parts, the HB.130 has a custom bottom bracket. This will require you to use a Hope BB, but you can run any 30mm spindle crank (with a Boost offset chainring). Apparently the threaded BB uses an M46 thread which sounds awfully similar to the T47 bottom brackets but it seems to be just enough difference to require a different bottom bracket. There’s also no current option to run a 24mm spindle crank on one of the Hope bottom brackets without the use of an aftermarket spacer kit. We’ll see if that changes if Shimano ever gives Hope permission to create a Micro Spline compatible freehub…
Other proprietary parts are more exciting like the integrated chainguide and chainstay protector that also serve as housing guides. These seemingly brilliant pieces highlight the attention to detail that has gone into this frame. Not only is the chainguide adjustable and easily removable, but the upper mount serves as a guide for the rear derailleur cable. Then the cable routes underneath the chainstay protector which has two bolt-on clamps that pull the guard down and simultaneously anchor the cable.
Similar detail has gone into the rear brake hose routing with small bolt-on clamps neatly guiding it down the chainstay.
Cable routing through the front triangle is internal, with the cables entering in through ports at the head tube and exiting just below the bottle cage. Yes, the HB.130 has a bottle cage. That was part of the reason for moving the upper shock mount to the top tube from the downtube.
The cables are not captured inside the frame but Hope does wrap them in foam to cut down on rattles. To route new cables and hoses, it’s best to work from back to front, with the removable cable guides at the head tube providing large access holes.
Suspension
Mentioned earlier, Hope was quite happy with the original suspension design of the HB.130. Guillaume is fond of saying that every suspension design has benefits and drawbacks and that there is no ‘magic formula.’ With that said, they did move to a Metric shock after starting with an Imperial shock which required a change in mold to accommodate the 210mm length. After experimenting with a 50 & 55mm stroke, they settled on 50mm which yields the leverage curves shown above – roughly 18% progression in High, and 20-22% in Low position.
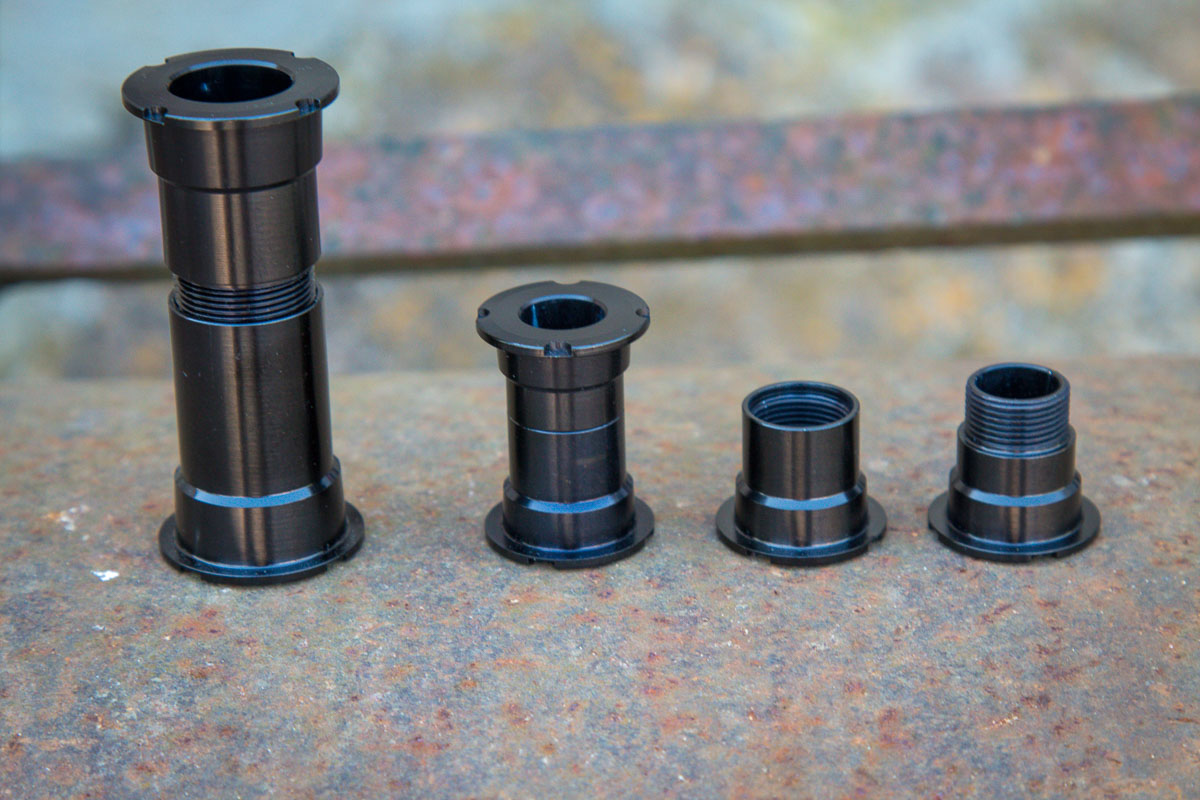
Giving away the bike’s true nature, Hope has chosen to spec every HB.130 with a 140mm travel Fox 36 Factory fork with a 44mm offset. That’s a lot of fork for a 130/140mm travel bike, but it fits with the all around intention of this build. This is a bike that Hope’s employees will ride trail on one day, and then take to the bike park the next.
Currently, Hope has medium, large, and extra large frames ready for production. Ride a small? Unless there’s enough of a demand, you may be out of luck. Hope states that the small frame isn’t ready yet, but if there are enough consumers with the money to buy, they’ll produce them.
Complete Builds, framesets, pricing, availability, & colors!
With so much detail that has gone into the frame, it’s almost easy to forget that Hope parts are included in much of the spec as well. Sold in one stock configuration for $8,400 , the complete bike will include Hope Tech 3 E4 brakes, hope Pro 4 Boost or Fortus 26 wheels, Hope carbon bars, a Hope SL AM stem, Hope SL grips, and the appropriate Hope headset, bottom bracket, and spacers. Most of those parts include an option on color with seven stock anodized options available (red, orange, blue, purple, silver, black, and green).
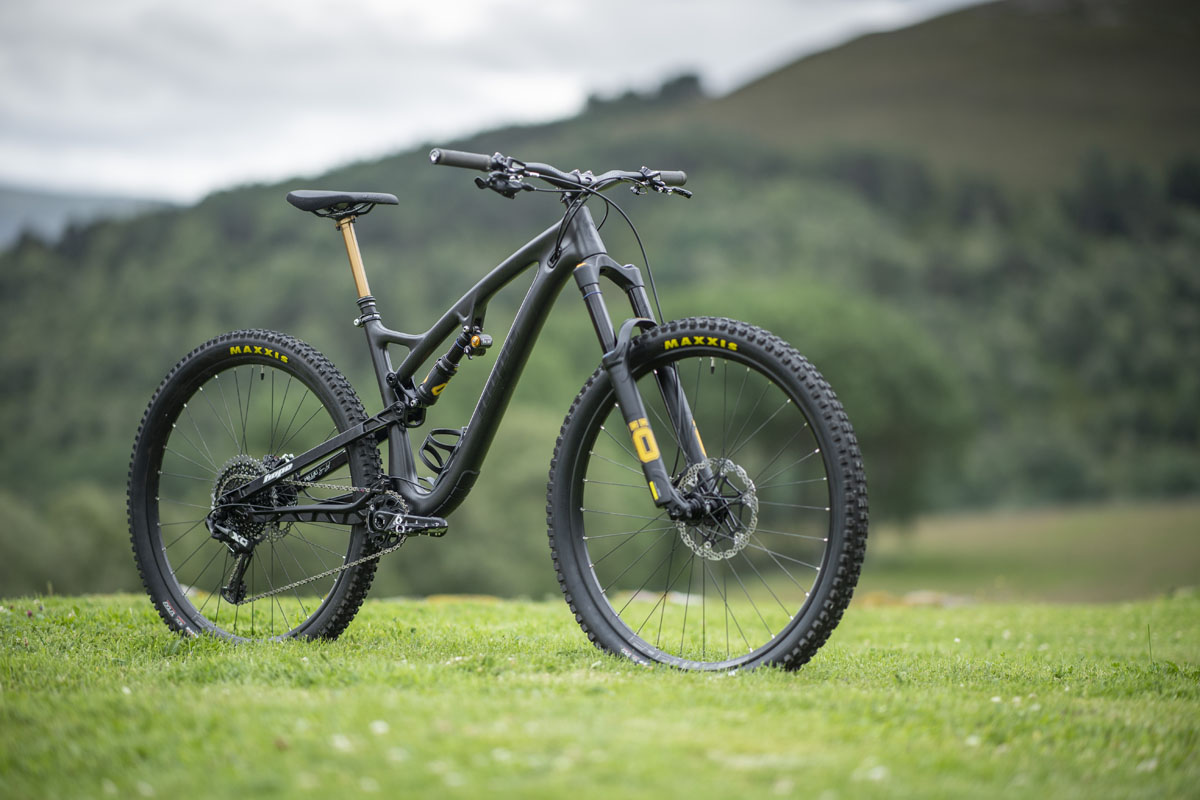
You can also choose the hardware color for the frame itself. Do you match the frame hardware color? Go all black? Or all the colors? The choice is yours.
For drivetrain duties, the HB.130 runs a SRAM Eagle X01 group complete with SRAM carbon crank. That crank was a stipulation from SRAM in order for Hope to be able to purchase complete groupsets to sell of their bike. Obviously, Hope thinks you’re better off riding their Evo cranks, so they’ve priced an Evo upgrade kit to be about the exact price you could sell the take-off SRAM cranks for.
There’s also upgrade packages available for a SRAM AXS wireless drivetrain with Reverb dropper, matching decal kits, Santa Cruz Reserve carbon rim options, and an Ohlins Suspension package. The Ohlins package is offered at no additional charge and includes an RXF 36 EVO Air or coil fork in 140mm and a TTX Air shock tuned for the HB.130.
The frameset package includes a frame with your choice of hardware color, a Fox DPX2 or Ohlins TTX22 shock, the proper BB and headset, a pair of HB Pro 4 hubs in your choice of color, and a seat clamp for $4,950.
Each bike is made to order with the lead time expected to be around 3-4 weeks depending on the demand. All prices include shipping and taxes, and the frames carry a lifetime warranty to the original owner plus lifetime bearing replacement which will be serviced through Hope USA.