Earlier this autumn, I headed to northern Italy to ride my second 3T Jeroboam gravel event in two consecutive weekends (opting for manageable 150km Magnum versions of each). While in their neck of the woods, I dropped into 3T Cycling’s small Bergamo factory where every 3T Torno carbon crankset is made by hand, to see how it’s done. And to chat about what they have planned for the extra floor space on their production floor, hint: it’s going to be big, light & carbon…
3T handmade in Italy, starting with THM co-development
When 3T Cycling bought up boutique component maker THM Carbones a few years ago, the move was less about diversifying the 3T brand and more about expanding 3T’s in-house production capabilities. What 3T really wanted was THM’s superlight German carbon development & manufacturing expertise.
Ever since Rene Wiertz resurrected the iconic Italian component maker back in 2007, 3T always had hopes of figuring out a cost effective way to bring some production back to northern Italy.
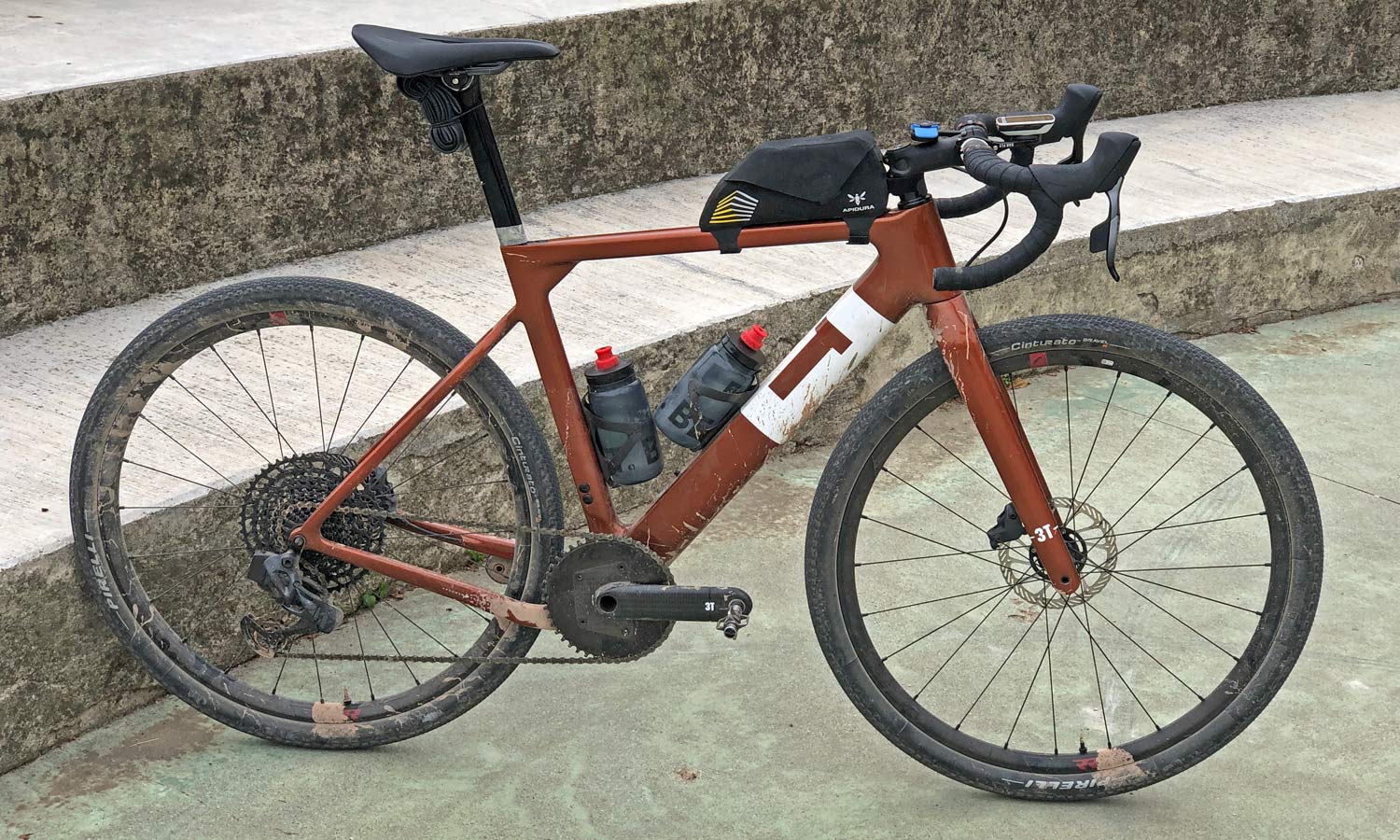
Introducing their first bike frame back in 2016, the unique & premium carbon aero gravel Exploro, which continues to deliver, got gears spinning about a possible way to do that (just a week after announcing the THM buy out). A year later, the Strada road bike popped up, but 3T still couldn’t justify the extra cost to build the carbon bikes in Europe.
But the next spring in 2018 saw the first fruits of having THM on-board, with the 3T-branded Torno carbon cranks developed in Germany. Those Torno cranks are now entirely produced in-house by 3T, literally just upstairs from their European HQ offices & warehouse near Bergamo, Italy (after the first pilot run of 100 cranks were made in Germany at THM HQ).
Ultralight & aero 3T Torno carbon cranks, Made in Italy
So, how do you make a carbon crank? One at a time apparently in the case of the Torno. Building off the precision manufacturing expertise of THM, 3T uses resin-transfer molding to produce their Italian-made Torno carbon cranks. The process leaves out the resin that binds the carbon fiber together until the last step, offering more control over the resin:carbon ratio, but also eliminating the need to work in a cooled or hurried environment.
That allows 3T to craft the cranksets from a wide mix of carbon raw material (stored at room temperature), carefully selecting the precise fibers they want for each layer of the layup and allowing them to make two spec-levels of the same crank. It also minimizes the amount of waste both of carbon & cured resin.
3T builds the Torno cranks at their two higher spec levels LTD & Team.
3T Torno LTD vs. 3T Torno Team carbon crankset, detail comparison
The 1050€ Torno LTD (front) is constructive from thinner, finer & higher modulus woven & UD fibers that have a raw material cost more than 5x that of the Team edition. The LTD layup is also significantly more complex and a more closely guarded secret, at times with 3x as many layers to get to the same material thickness. Adding extra material, development & manufacturing labor complexity costs the extra 250€ cost is surprisingly small. This is after all an aero 1x carbon crankset with a claimed weight of just 300g (429g with pinch bolt & 40T chainring)
The 800€ Torno Team (rear) is laid up from a simpler lower tech mix of carbon and is identifiable by the slightly more coarse top layer weave. It is said to match the LTD in strength & stiffness, at only a 50g penalty.
How does 3T actually make a Torno carbon crankset?
3T opened up their production to give us a glimpse of what goes into the lightweight Torno cranks, for the most part limited to the Team version. Each individual patch of fiber is cut to shape and sorted according to its place in the cranks.
Trying to keep their actual layup a secret, 3T didn’t get into too many details on how the layers specifically break down. But they did share that the Team cranks are wrapped up in the mold around a preformed foam core.
All of the Torno cranks feature a structural outer woven layer to get the high stiffness to weight, which is then for the most part paired with additional alternating UD layers (identifiable by the thin white thread patter than holds it together as a sheet) and other woven layers. The entire layering or layup process happens essentially dry, without the final resin added. This allows 3T to be precise with fiber placement, without worrying about the workable time of a resin that has already begun to cure.
3T uses just a handful of custom developed molds for the RTM (resin-transfer molding) process that was perfected by THM together with German technical university research.
The crank molds are two-part interlocking (male & female), heated, and include ports to allow the resin to be injected once the mold is closed.
Because of the low number of molds and the time it takes to transfer resin completely into the closed mold, only a couple people are generally needed at one time to layup the Torno cranks by hand in Bergamo.
After cleaning & prepping the molds, carbon starts to get added. A precisely measured quantity of loose short fiber is packed around the base of the carbon axle before the outer layer of the spider is inserted into the mold. Since 3T doesn’t use any post molding filler or additional finishing, the small fibers are able to fill the gaps at the sharp angled bend in the mold without resulting in any voids.
Then, pre-stacked layers of fibers are placed over the form that will become the inner surface of the axle and over the alloy pedal thread insert, before the layers are carefully aligned and pressed together.
Next, the material that makes up the carbon axle, or bottom bracket spindle is interlaced into the arm & spider. And finally, that pink foam core would be inserted and the fiber wrapped over and tucked into itself from the sides. Then, the second half of the mold is slid down over the spindle and closed.
It then goes into 3T’s custom fixture that clamps the molds securely together, heats the metal of the mold itself to ~80°C, and then transfers the resin into the mold under pressure to ensure complete & even infusion of resin into the carbon fibers.
Each driveside crank arm with molded-in spider & axle is laid up one-at-a-time in a single mold, while the non-driveside crank arms come out of a shared mold producing three at a time. The efficiency & consistency of the RTM process means the cranks come out of the mold without voids, and without need for further finishing or processing. Besides cleaning off excess resin flash where the clamshell mold pieces come together, 3T only adds water transfer decals directly on the molded cranks.
No filler or paint needed.
So what’s next for 3T’s in-house made-in-Italy carbon production?
3T is still producing Torno cranks at a relatively low volume, less than say a thousand a year which means this cart of over a hundred could amount to more than a month’s worth of cranks. A lot of that is due to the manual labor intensive production of the crankset itself. But remember, 3T started really looking at in-house carbon production with their eye on frame production.
While I was in 3T’s factory I did see some frame R&D projects in the works (that were not yet close to being finished, so 3T didn’t let me take photos.) Interestingly, 3T has set up a whole-owned internal subsidiary company to manage their in-house carbon production, separate from their Taiwan-based standard wheel & cockpit component division. That subsidiary, called Composite Jazz, just happens to have a prototype bike frame photo on their Contact Us webpage that could give a hunt as to what 3T are working on. Don’t tell anyone that I sent you there.
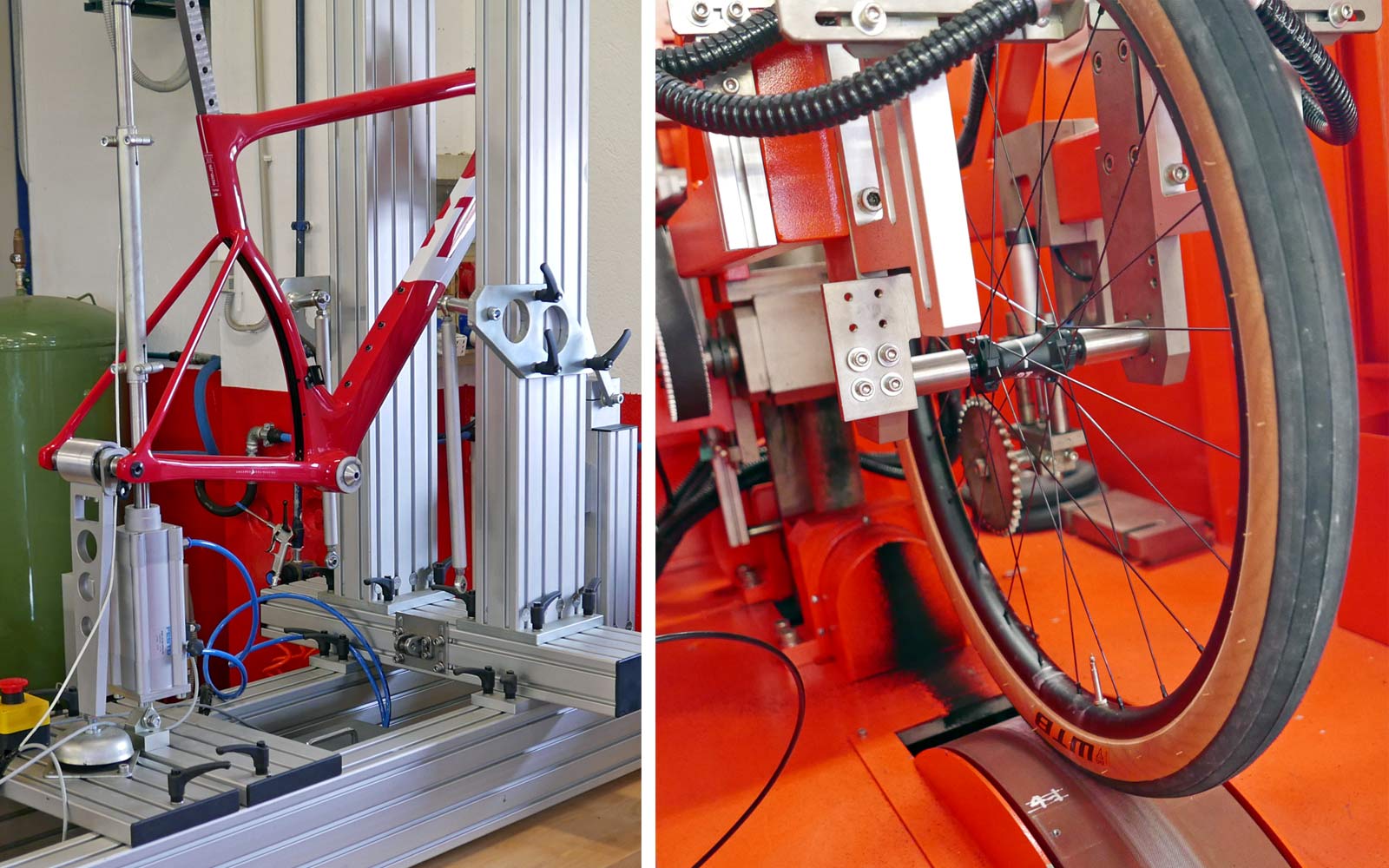
3T were working on some new automated manufacturing processes (and machinery) while I was there, that they are hoping to use to be able to create an Italian-made version of bikes like their Exploro & Strada that will be able to achieve similar price points to their current top LTD level Asian-made frames. There also just happened to be a well-respected carbon frame design consultant who had worked with one of 3T’s co-owners almost a decade ago on a <700g carbon road bike. And 3T or Composite Jazz, or whatever you want to call them is in the market for a new mechanical engineer with automation experience.
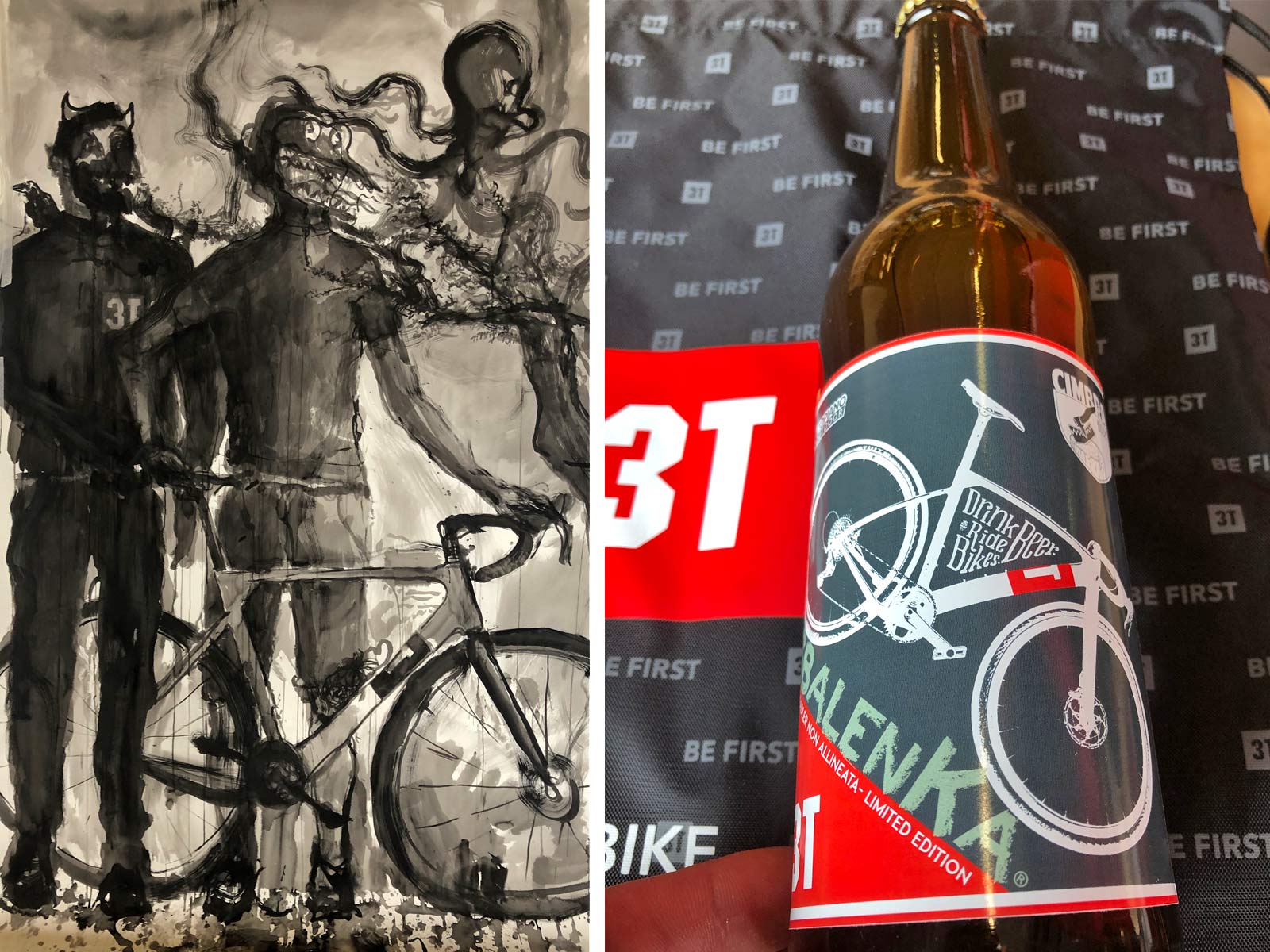
Suffice it to say, 3T isn’t entirely hiding the fact that they are planning to bring some frame production back to Italy by the end of next year. It’s not ready yet, but they promise to give us more of an update in spring 2020.