We know, there’s no such thing as a stupid question. But there are some questions you might not want to ask your local shop or riding buddies. AASQ is our weekly series where we get to the bottom of your questions – serious or otherwise. This time it’s all about hydraulic disc brake rotor technology! Hit the link at the bottom of the post to submit your own question.
This week, the good guys at Shimano, Hayes, TRP Cycling and Magura are on hand to answer your disc brake rotor tech questions. I hope you’re ready to geek out, because this one pulls out all the stops.
Do the cut-out patterns on a brake rotor matter? I wonder if there is there an optimal shape, or an optimal ratio of rotor material to hole? I guess what might be considered “optimal” would be related to what kind of performance you’re looking for from a brake, right? Outright power versus fade and heat resistance, tendency to warp, etc. Can you give us some insight please?
Shimano: The cut outs in the rotors are mostly for clearing debris. There are better ways to manage heat, weight, and run-out. Honestly, the forms of the cutouts are about aesthetics as much as anything else.
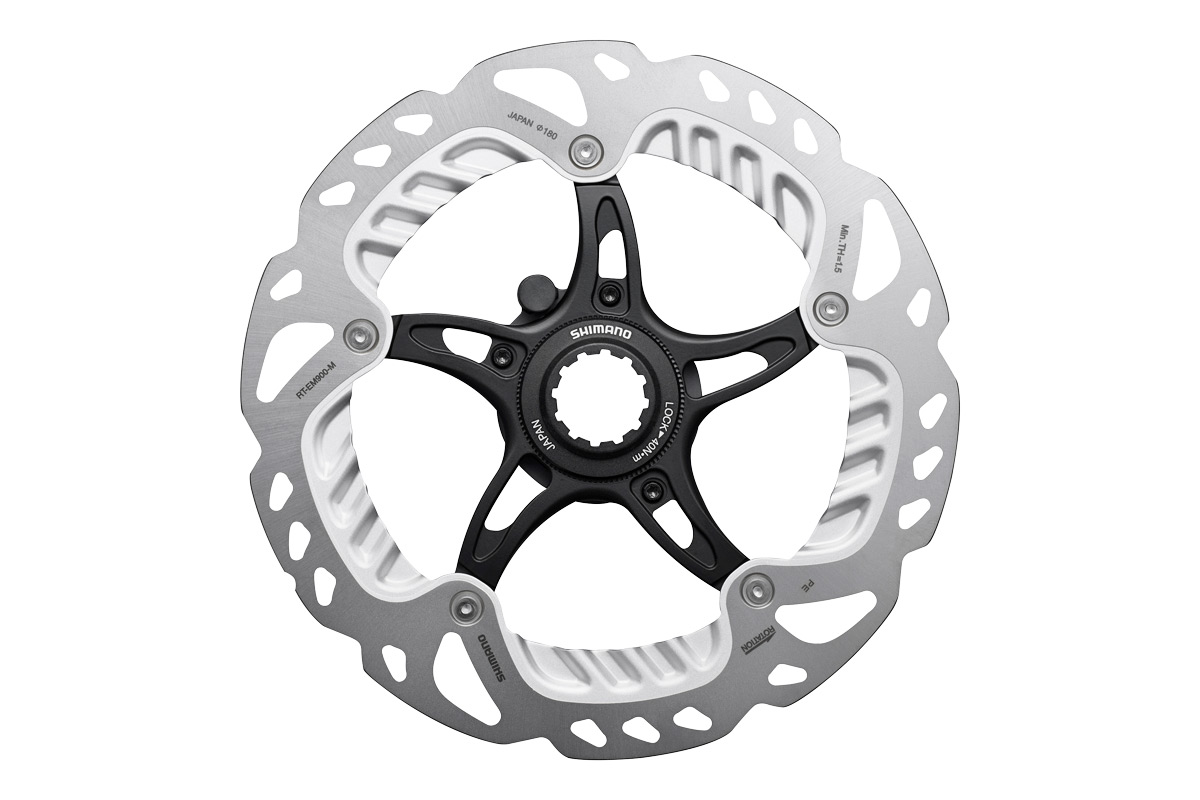
Magura: The two main reasons for the cut-outs on the brake surface on rotors are weight reduction and “cleaning” of the brake pad.
Obviously, more weight is saved on a rotor that features larger cut-out areas. Lighter XC-rotors have more cut-outs and bigger cut-outs than gravity-oriented rotors. More cut-outs save weight, but also reduce heat resistance due to the reduced mass of the rotor.
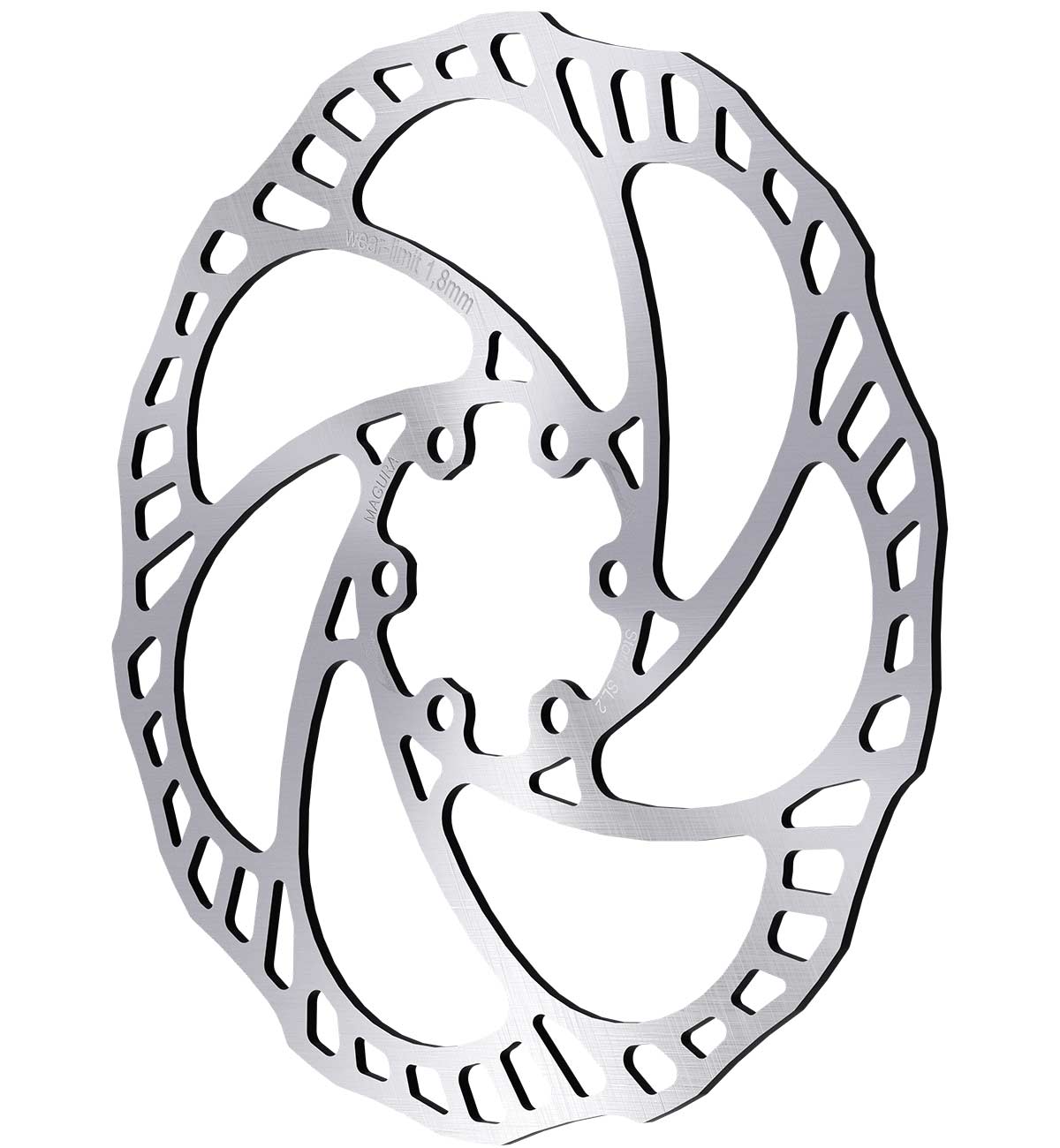
However, the cut-outs are limited in their size and shape, as the pads must have still sufficient contact surface in order to generate friction. The pressure of the pad against the rotors should no be smaller than a pre-determined threshold value to reduce the “cucumber slicer” effect with resulting excessive pad wear.
A solid brake surface without cut-outs would make the brake pads glaze, especially organic pads. The pads are “cleaned” by the cut-outs. On some rotors some circular rings do not have a cut-out; the corresponding surface looks different (mostly glazed) both on the rotor and the pad.
So, depending on the use, the cut-outs can be different. But brake power, heat resistance and friction, depend on so many rider specific values that they have to be considered on an individual basis.
TRP: The cut-out patterns on a brake rotor definitely have a rhyme to their reason. A consistent surface area on the rotor needs to be kept in order to avoid brake pulsing and the generation of noise, which would occur if you had alternating values of surface area passing over the pad.
For optimal performance of a brake (looking at stopping power and modulation ability only) a disc with no cutouts would actually be best as that would allow for full contact of the friction surface between the pad material and rotor. The same is true for a race car; the optimal grip is from a slick tire on perfect surface.
However, because a bicycle is not a race car and we don’t live in a perfect world, the rotor needs to deal with the issues of cooling and debris removal, along with providing ample stopping power. The cutouts are spaced so an opening passes the pad at some point during the rotation and allows for gas exchange to occur which dissipates the heat buildup along with providing a path for debris to be pulled out.
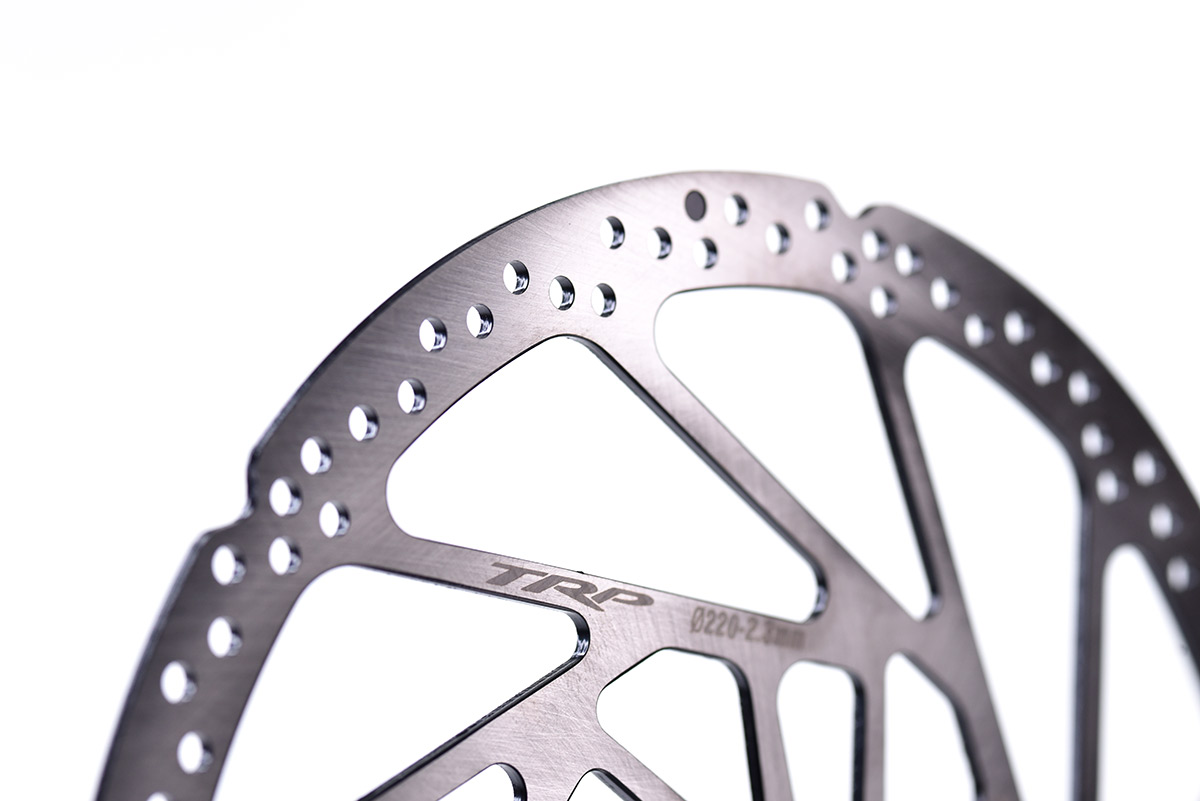
At the same time, if you remove too much surface area on the rotor to achieve a greater cooling ability, more surface friction between the pad and rotor is lost causing the overall reduction of deceleration forces. Therefore, optimal performance ratios on a standard thickness rotor are more or less a compromise between power and cooling.
However, with our thicker 2.3mm rotors, cooling is not a big goal of the cutouts because the thickness allows for extra heat-capacity leaving the cutouts to be designed for maximum surface area to the pad and consistency during high intensity usage.
Hayes: Yes, the cutout pattern matters. It impacts heat capacity of the rotor, water/debris/mud-shedding capability, heat transfer by convection and radiation, noise, out-of-plane (side-to-side) and in-plane (torsional) stiffness, weight, and manufacturability.
When developing a rotor, the engineer must balance all these aspects to meet the needs of the type of riding it is intended for. Without giving too much away, during the development of our D-series rotor the shape of the cutouts were tuned to significantly reduce any unwanted noise while the size of the cutouts managed their thermal characteristics.
I see a couple of manufacturers (TRP, SRAM) have added thicker rotors to their disc brake line-up. For SRAM at least, 1.55mm was the standard thickness, but now I see they offer a 2mm thick 200mm rotor. Similarly, TRP’s standard rotor thickness is 1.8mm, but they also offer a 2.3mm (in 223mm, monster!). I guess a thicker rotor will be more resistant to warping, is that correct? If so, can you put a number on it? The extra rotor thickness definitely comes at a weight disadvantage, however. Do the benefits actually outweigh the drawbacks? I’m thinking specifically about the fact that you’re now trying to slow something down that has a greater rotational weight.
Shimano: Larger and thicker rotors exist to improve heat dissipation, which is precisely why Shimano doesn’t make them. Shimano’s Ice Technologies are simply a better way to manage heat. Thicker rotors are certainly stiffer too but we could also increase stiffness with a thicker carrier and standard brake track, so this isn’t really the motivation for moving to thicker rotors.
It’s not necessarily obvious, so whenever I get the opportunity I point out that the real beauty of Ice Tech is that it allows you to manage heat separately from power, weight, frame compatibility, and ground clearance. A 160mm Ice Tech rotor has about the same cooling capability of a standard 180mm rotor. A 160 mm Ice Tech Freeza rotor would have about the same cooling as a 203mm standard rotor.
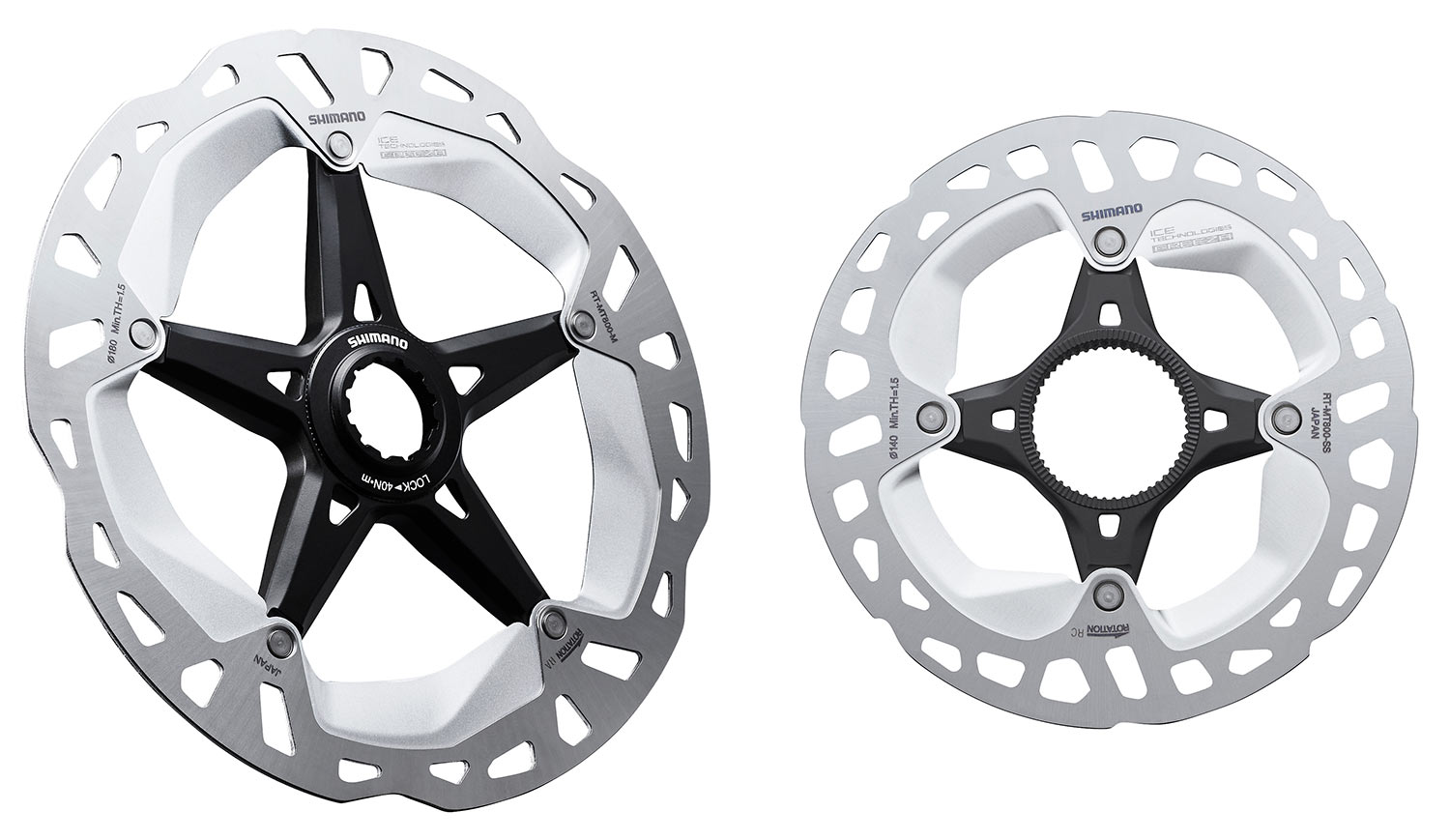
This is super valuable on XC, road, or gravel bikes that may not be able to fit larger rotors. You might not want the extra power, weight, or reduced ground clearance either. On bikes where those aren’t factors, a 203mm Ice Tech Freeza rotor simply offers better heat management than a 220mm/223 mm rotor could, even if the thickness goes up.
Of course, power increases with larger rotors too but at this time we’re not getting many requests for more power than you can get with 4 piston servo-wave brakes and 203mm rotors. If there are readers who do want more power than that, by all means please let us know in the comments.
Magura: Magura disc brakes with steel rotors are and always have been 2.0mm thick, since 1997 starting with Gustav (the first Gustav’s had 3.0mm thick aluminum rotors). We’ve found that this thickness gives the best compromise between round run, heat resistance, strength against side-on impacts, noise and weight.
An important factor in rotor design is the spokes connecting the friction ring with the hub interface. These spokes have to transfer the torque from the friction ring into the hub and have to compensate for heat expansion from the friction ring.
The generated torque with the same braking force and rotor diameter is always identical. But, in order to transfer that torque through the spokes, thinner rotors require more or wider spokes than thicker rotors. So, the weight savings might not be that big on thinner rotors…
Thicker rotors with the same shape as their thinner counterparts obviously can transfer bigger torques. A weight example: grinding down a rotor from 2.0mm to 1.8mm (difference of 0.2mm) saves 10% on weight.
TRP: That is correct, a thicker rotor will be much more resistant to warping especially in the larger 203mm and 223mm sizes. To put a number to it, our 2.3 mm thick rotors are 47% more resistant to warping under heat because of this added thickness.
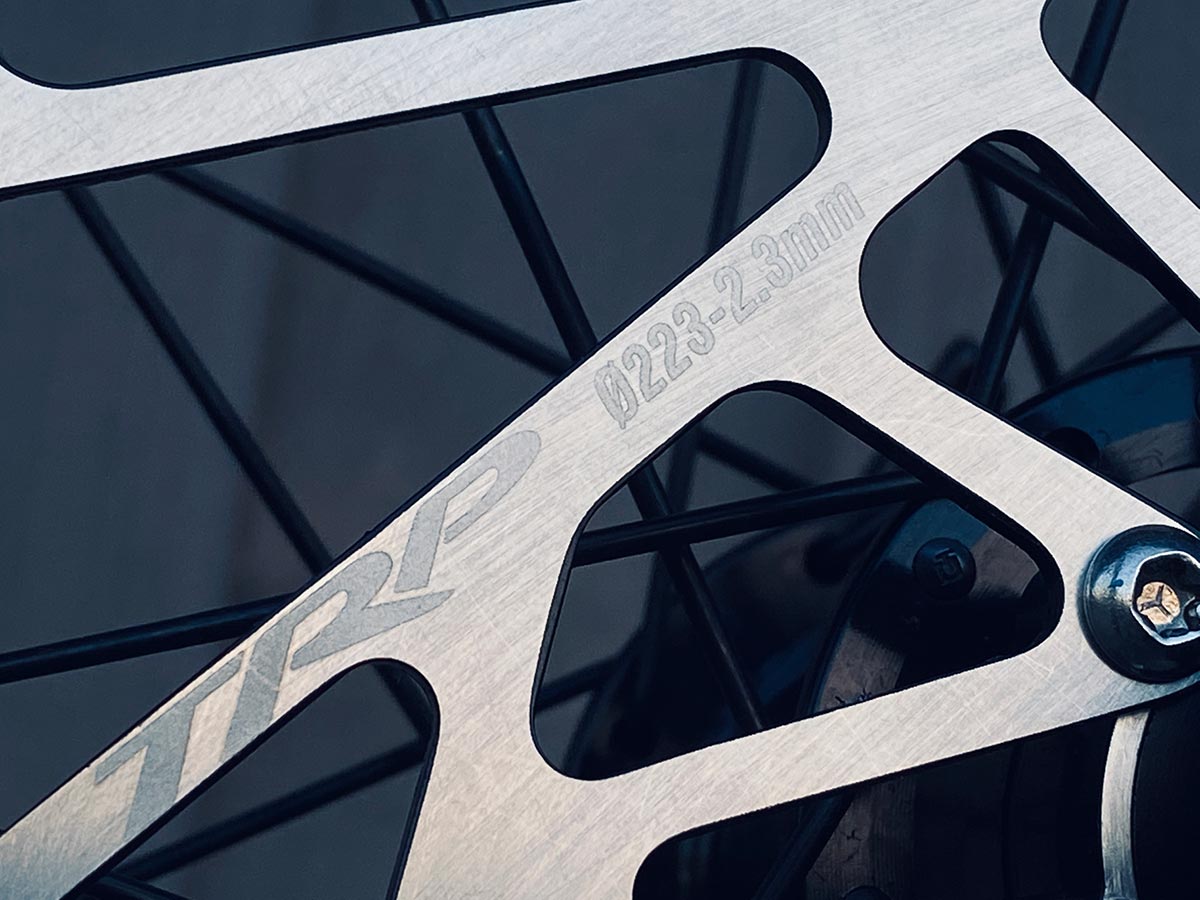
However, this is just one benefit of using a thicker rotor. There are also the benefits of having a larger heat-capacity, better durability against rock strikes, more consistent operating temperatures, and less vibrations or noise production.
This extra thickness does come with more rotational weight in the rotor, but this increase is nominal compared to the overall kinetic energy of your body and the bike that you are trying to stop.
Hayes: With the launch of Dominion in 2018 we introduced our D-series rotors which are 1.95mm thick. There are a variety of performance advantages: increased heat capacity in the rub ring (pad contact area), increased out-of-plane (side-to-side) stiffness, and increased in-plane (torsional) stiffness.
The disadvantage is an increase in rotational weight which does have an impact on braking and suspension performance. Since the weight increase is very small compared to the total wheel assembly and the added mass is near the axle the effect is quite small. In the majority of applications, the advantages outweigh the disadvantages.
For enduro and downhill racing, are 6-bolt rotors or center-locking rotors the preferred option, and why?
Shimano: Well, of course the Shimano guy has to say Center Lock is better. This question was specifically about enduro and DH racing though, so let’s look at it from that point of view.
Racing often means flying with the bike, and that’s one place where Center Lock makes a huge difference. I keep a bottom bracket lock ring wrench in my bike case so I can quickly remove my rotors from the wheels for packing and quickly re-install them when I get there.
Honestly, when transporting a bike with 6 bolt rotors I am very likely to skip this step and just hope the rotors don’t get bent or cut anything inside the bike case. Racing can also mean damage to the bike, like wrecking a rim during practice and needing to rebuild the wheel before race day. When time isn’t on your side, Center Lock is definitely nice to have.
If you walk around the pits at a World Cup DH race in the evening after practice, there is often one lonely mechanic lacing a hub to fresh rim under the trailer lights. If his team uses Center Lock, he gets to eat dinner a little sooner.
For better or worse, though, enduro bikes have gotten so good that the industry isn’t selling as many downhill bikes anymore. That means everyone has a smaller catalog of DH specific parts, which includes hubs. There are more and more 157mm rear hubs with Center Lock because of Super Boost bikes, but many brands do drop this spec for their 157mm hub.
20mm boost hubs are much harder to find though since they are basically a downhill standard. believe that Onyx may be the only brand offering a 20mm boost front hub in a Center Lock option. At this point I believe that all Shimano sponsored DH racers use 6 bolt rotors.
Magura: That’s mainly a matter of hub choice. Both versions are good. For example: most racing cars or motorbikes have center-lock wheels for rapid wheel changes. Six bolts have a higher redundancy than one lockring.
TRP: Both are solid attachment styles and are going to have the same performance, it just comes down to preference. Some race mechanics like to use center-lock because of the ease of use and speed of assembly, while others prefer 6-bolt for its reduced weight.

Hayes: You can obtain the same braking performance with either a 6-bolt or Center Lock rotor design for any riding discipline. Center Lock provides a quicker method of installing and removing rotors. It is a licensed technology that typically requires a 2-piece rotor design so the cost is higher.
It is up to the rider whether the quicker installation is worth the cost. It usually comes down to whatever type of hub came with the bike! It should be noted that adapters are available to install a 6-bolt rotor on a Center Lock hub but not the other way around.
What are the advantages of a two-piece rotor over a one-piece rotor? Is it stiffer, does it dissipate heat more efficiently? What performance advantages does it offer for the additional weight?
Shimano: You’re on the right track. The aluminum carrier does indeed help a little with heat dissipation and offers a good improvement in stiffness. It’s actually lighter too, even though it doesn’t look like it. We’re replacing steel with aluminum so the rotors still end up being lighter with the thicker carrier.
Magura: The biggest advantage of a two-piece rotor is the fact that the friction ring is separated from the hub interface. As braking generates heat, the friction ring can expand in diameter more easily as it is independent from the rest of the rotor. This also means there is a reduced chance of warping.
Single piece brake rotors are, depending on the design, easier to warp, as the friction ring is tightly connected to the spokes and the hub interface. The design of the spokes will determine how easily a rotor will warp.
Finally, depending on the design, two-piece rotors can be lighter than one-piece rotors, especially when aluminum is used for the hub interface.
TRP: The advantage of a two-piece rotor is that it allows for better alignment when using thinner rotors and larger diameters. Going to a 200mm or 223mm diameter with a 1.8mm thickness makes for a very flimsy rotor and, when bolted to the center of rotation, warping due to uneven heating and cooling is more likely to occur.
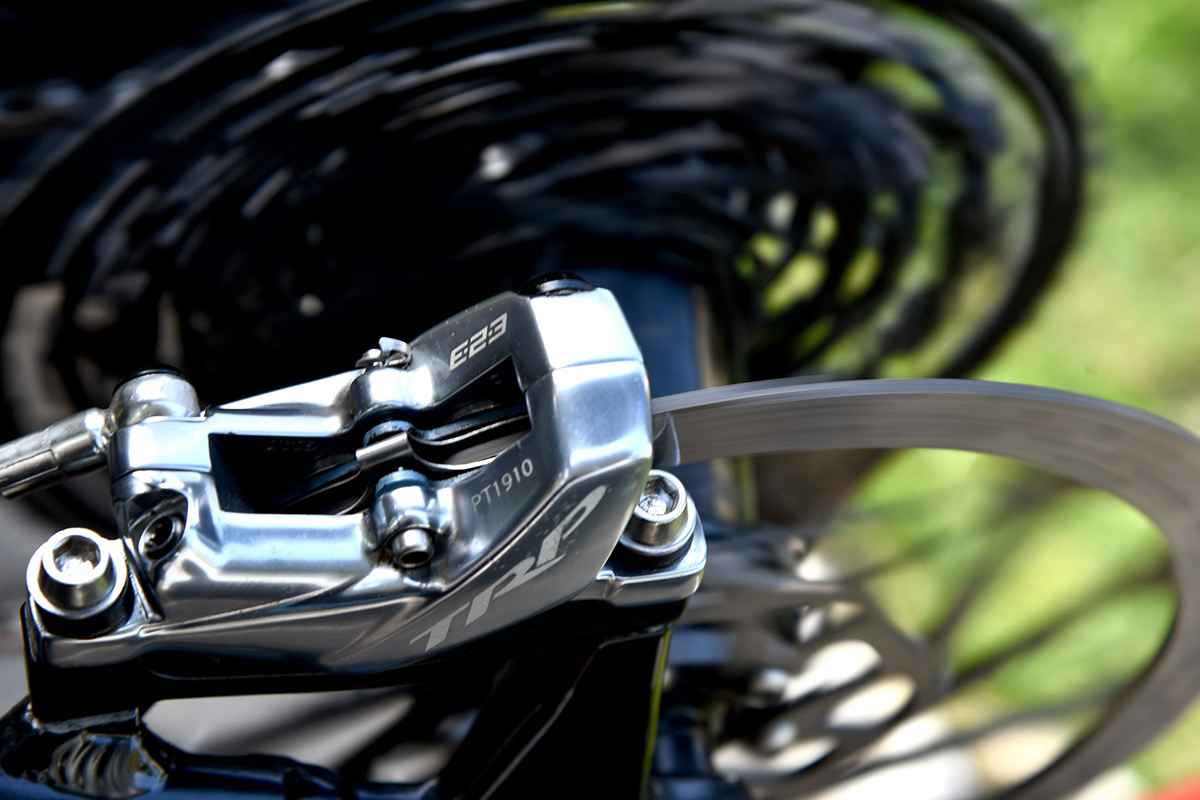
So, a heavier and stiffer carrier could be used to hold the diameter stable and then a thinner rotor bed can be attached to the outside of the carrier. With the advent of our 2.3mm thick rotors though, we are able to reach bigger diameters of 223mm without needing to use the extra weight of the carrier.
Hayes: There are two different types of 2-piece rotors. The fist type which are more common on motorcycles are floating rotors: the rub ring (outer ring) is allowed to expand radially relative to the carrier. The second type which are common in the bicycle industry are pinned rotors: the carrier is fixed to the rub ring allowing for no relative movement.
For both types the carrier can be made of a lighter weight material, usually aluminum, which results in lower overall weight on larger rotor sizes. On smaller rotor sizes the carrier weight savings may not surpass the pin weight. For both types the carrier can be a more complicated shape allowing for features such as Center Lock. Floating rotors have the added advantage of allowing the rub ring to freely expand with heat thus reducing propensity to warping.
Is the surface of a disc rotor designed with a specific brake pad material in mind? Does anyone offer rotors specifically optimized for organic or sintered?
Shimano: We don’t have different materials to optimize a pad compound. It’s an interesting question, but I wouldn’t think this would be worth the complication of having pad-specific rotors. What we really want out of a brake is a like-on-like interface between the pad and rotor, that’s why bedding in the brakes is so important.
The pads don’t grip onto the steel rotor, they grip onto the pad material itself that’s embedded into the rotor surface. The rotor’s job is to hold onto that pad material, resist overheating, bending, and cracking, while keeping weight and cost to a minimum. At this time, there isn’t much reason to look beyond steel for our rotor surface material.
One thing to note is that we do make some rotors that only work with resin pads. They are entry-level rotors that skip the heat treating step in manufacturing. If you used metal pads with them you would destroy them fairly quickly and make a lot of noise while doing it. These are typically used on bikes with brakes that can only take resin pads anyway, so it’s a great way to save some money for those riders.
Magura: The brake rotor material has to fulfill different needs: generate friction, low wear, and it must have a wide temperature range under which it can operate. The materials being used on bikes are very similar to those used in automotive applications.

Organic pads are generally less abrasive than sintered/metallic pads, creating less wear on rotors. Sintered pads require hardened rotors for a longer lifetime.
Magura brakes are only approved for organic Magura pads due to the reduced heat transfer into the caliper compared to sintered pads. Metallic sintered pads have a higher heat transfer rate than organic pads.
TRP: The surface of a disc rotor can certainly be mated with a specific pad material in mind, but this leaves the rider limited in their tuning options to one. TRP tests all pads to a constant rotor surface to get optimal results for each compound. This allows us to provide multiple tuning options for our riders to dial in the perfect braking feel for their style.
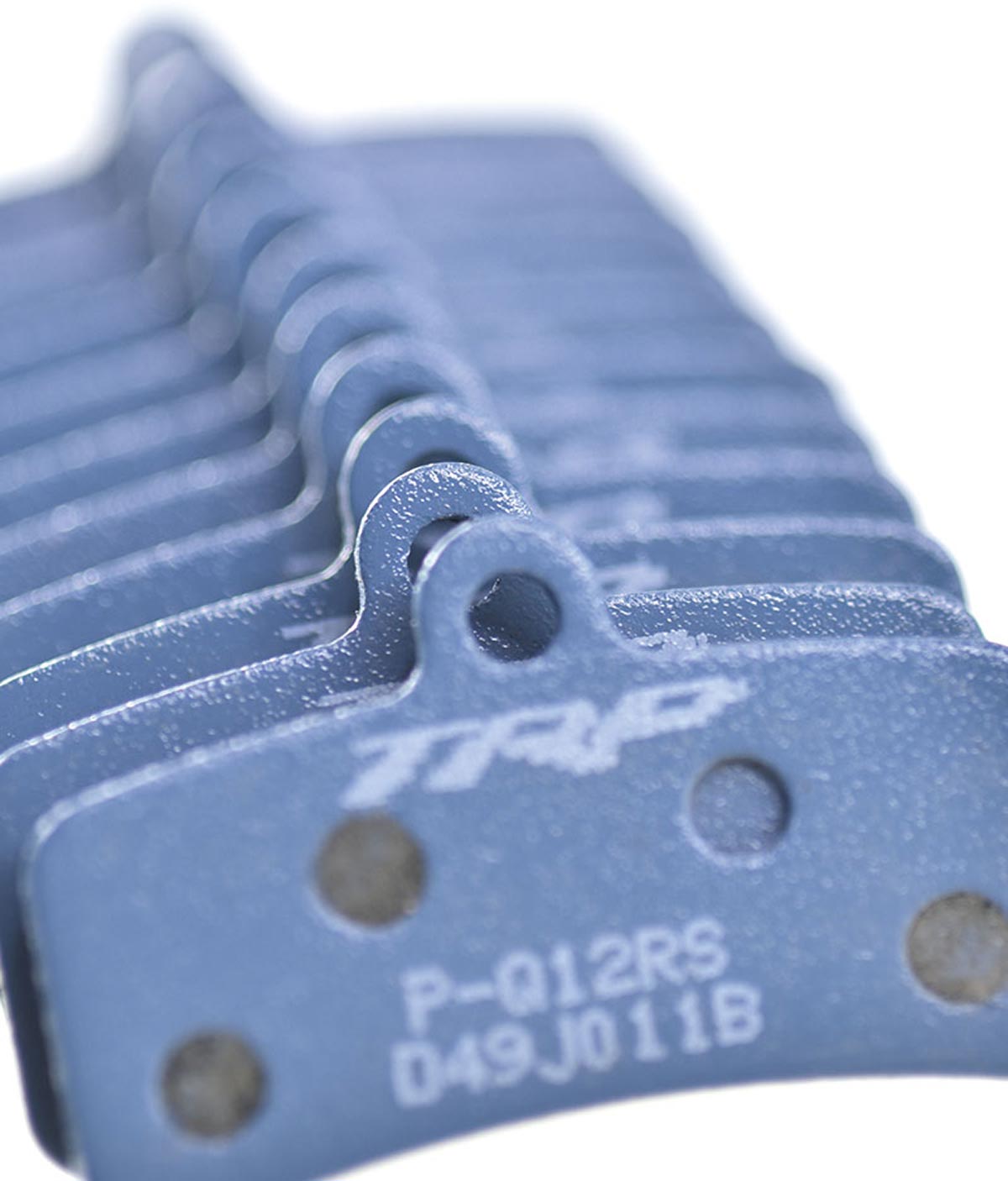
Hayes: Rotors and pads are designed to provide the wear and friction characteristics desired. Some rotor materials are compatible with a larger range of pads than others. Lower cost rotor materials typically can be used with a smaller range of pads.
The surface of the rotor can also be modified through various processes and treatments to modify braking performance. We introduced QuickBite technology on our D-series rotors which results in a quicker and more consistent burnish.
Can I run SRAM rotors with my Shimano SLX brakes? I run a 180mm rotor out back and a 203mm rotor up front. Do I need some kind of spacer or adaptor to make it work?
Shimano: The standard answer is that Shimano doesn’t test for compatibility with any other brands’ products, but maybe I can share some helpful information. Rotor thickness, diameter, and brake track height are all important factors and they are not standardized across the bike industry.
If the pads don’t line up with the brake track properly you could end up with a hidden problem. Things can seem fine at first but then the uneven pad wear starts to cause piston migration issues, loss of power, or damaged pistons. If you’re shopping for new rotors, go the safe route and keep rotors and calipers matching with the same brand.
If you’re trying to evaluate if you can keep using the rotors on your bike after upgrading brakes, work with the local bike shop to make sure everything will work together properly even as the pads wear.
Given that certain brands are now selling really thick rotors (2mm+) is anyone redesigning hydraulic disc brake calipers to accommodate them? With a fresh set of pads and pistons pushed right back into the caliper housing, it can be a nightmare to get the caliper centered. There is so little space available on either side of the rotor! My brakes have got to be 100% dialed for it to work well. Otherwise, even the slightest hint of piston migration causes rubbing on one side. Surely, someone must be making us some new brakes to accommodate these extra wide rotors?
Shimano: This is a spot on observation, we would indeed need to redesign our brakes to make them compatible with thicker rotors. As noted, with fresh pads there might not be enough room for the pistons to work normally. Centering the caliper becomes more difficult, and the free stroke at the lever would be reduced. Even worse, as the pads wear, the free stroke would slowly go back to normal, changing the way the brake feels over time.
Magura: Calipers are always designed for one specific rotor thickness with the allowed tolerance for wear. Thinner or thicker rotors than approved by the brake manufacturer can make the brake fail with worn pads or as a result of overheating the system.
Generally speaking, the distance between the pad and rotor is always constant, no matter how thick the rotor is (given normal tolerances with wear), as the pistons adjust automatically. Pad retraction is defined by the design of the groove of the quad seal and the design of the quad seal itself in the caliper.
Brakes are safety-relevant components on a bike. Always keep to the original spec otherwise warranty cases can be very nasty!
TRP: For those exact reasons, our EVO calipers are designed to accommodate thicker 2.3mm rotors the exact same way a standard caliper would accept thinner rotors. This ensures the caliper can be centered without trouble, and because of the added thickness, warping and issues from rotors falling out of true are a thing of the past on our brakes.
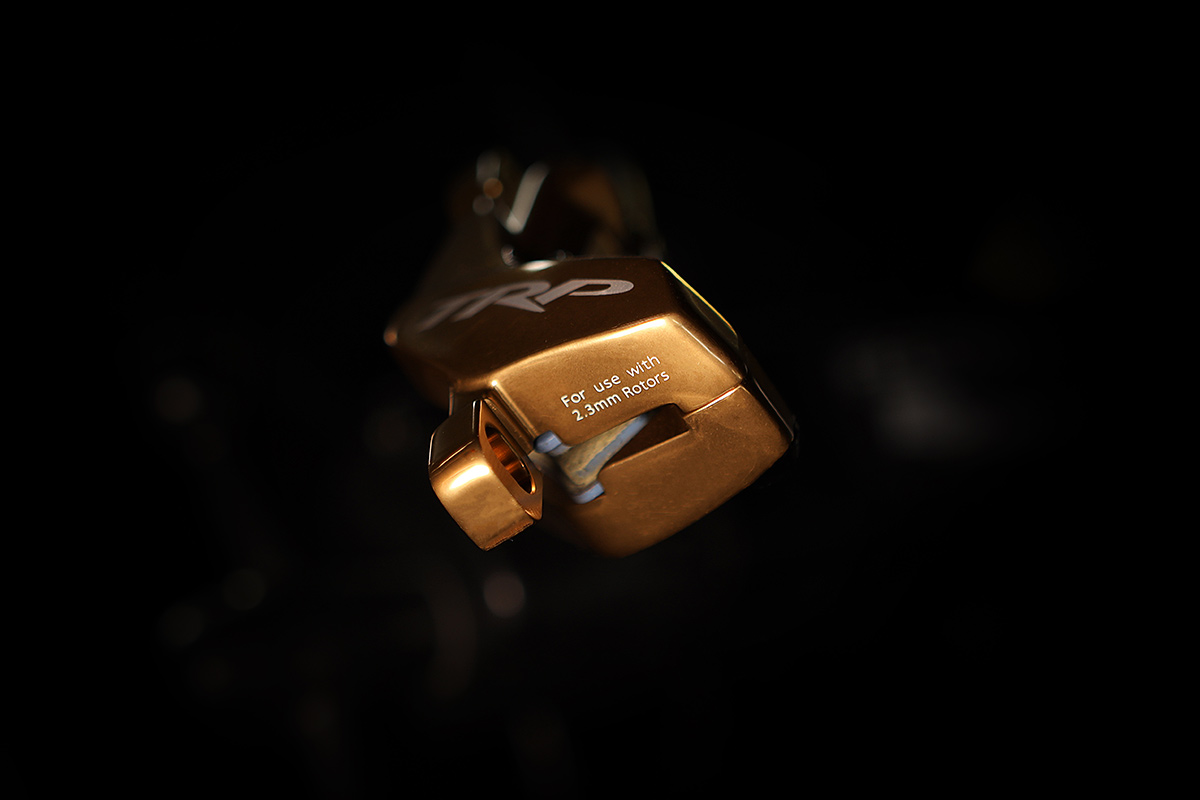
Hayes: It is important that you use the correct rotor thickness for a specific brake. Minimum and maximum rotor thickness must be accounted for in the caliper design.
During development a tolerance stack is used to ensure that within the allowed manufacturing variation of all components new pads will always have sufficient clearance to new rotors and also the pistons will always have full seal engagement at full pad and rotor wear.
The Dominion brakes were developed with the D-series rotors, so they are intended for the increased thickness, but they are also backwards compatible with our thinner L-series and V-series rotors.
Thank you so much to Nick Murdick of Shimano, Jude Monica and Stefan Pahl of Magura, John Thomas of Hayes and Sean Doche of TRP Cycling for contributing to this week’s Ask A Stupid Question.
Got a question of your own? Click here to use the AASQ form to submit questions on any cycling-related topic of your choice, and we’ll get the experts to answer them for you!