- Lori Barrett, Managing Director of Rotor
- Ruben Torenbeek, Managing Director of RAAW Mountain Bikes
- Giulio Mancini of INGRID Components
- Christian, Owner of Ceetec
6000 Series versus 700 Series Aluminium for Bikes and Bike Parts
Why are some components and tubes 6000-series vs 7000-series? What are the pros and cons of each? What do those numbers mean? In which applications do each perform best?
Rotor: ROTOR Bike Components does all manufacturing of alloy bike parts at our factory near Madrid, Spain. As a disclaimer, this subject of alloy properties is one that we’re necessarily passionate about, and has had complete university metallurgy courses taught on it (sometimes by our Spanish staff!), but we’ll do our best to give a concise answer.
ROTOR uses a few different alloys based on the desired properties of the parts, focusing primarily on six- and seven-series aluminum. The six- and seven-series designations simply refer to alloy formulations, since all are aluminum alloys. The six-series alloy is a forged product, which is very strong under single-directional forces.
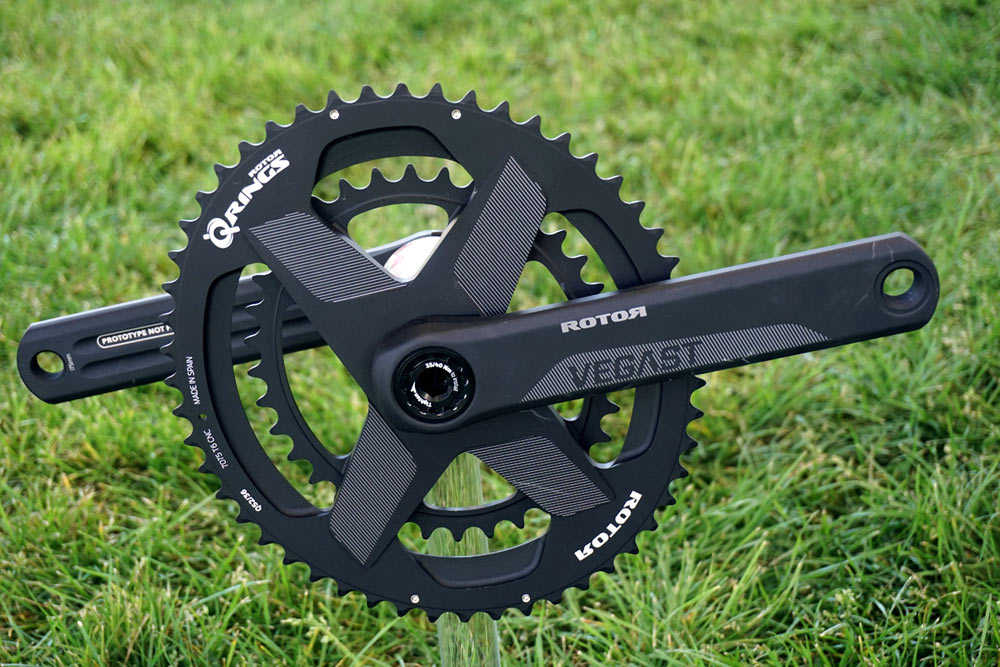
In order to manufacture six-series aluminum with the same strength as a CNC’d, seven-series alloy, it is necessary to leave additional material, which leads to a heavier product. Seven-series aluminum is a harder material, which, with proper machining, can make it stiffer, and allow us to remove more material in the CNC process, leading to a lighter bike part.
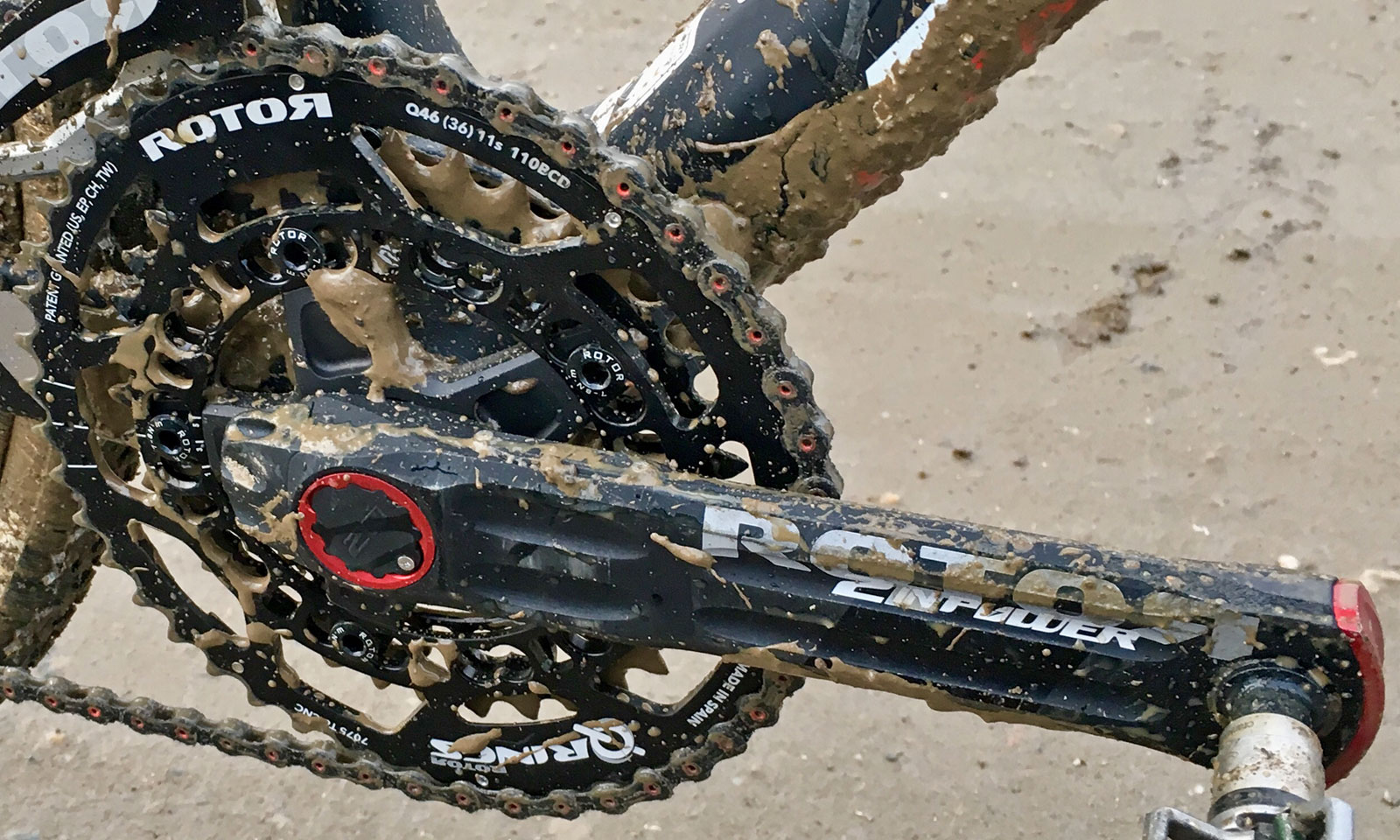
That being said, six-series aluminum is the most commonly used alloy in the bicycle industry: it is strong, easy to weld and work with, and cost-effective. We use six-series aluminum in our mid-level Vegast cranks, which are very durable but carry slightly more material to make the same strength as the seven-series, fully-CNC’d 2INpower and Aldhu products.
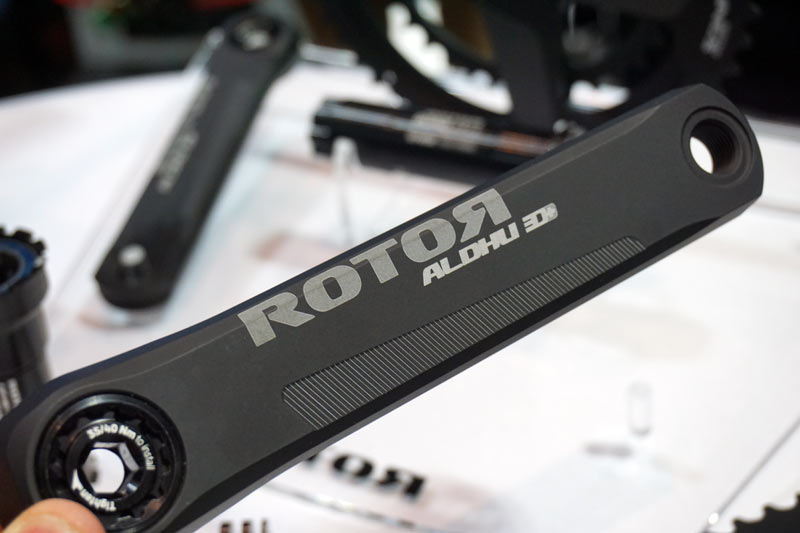
After the CNC process, we anodize to reduce corrosion and improve the abrasion resistance, as well as giving our cranks and rings their signature “any color as long as it’s black,” industrial look.
Additionally, we use a few different alloys within the seven-series to gain maximal performance: the aeronautic-grade 7075 on our chainrings is even harder than a 7055 for cranks, since rings need maximum stiffness and little allowance for deflection. This allows us to offer the 5-year warranty on cranks and rings. Every single bar of raw material is checked by ultrasonic inspection to guarantee freedom from internal defects.
At the end of the day, ROTOR has done an extraordinary amount of research into the best alloy for each product we make. Manufacturing in-house allows ROTOR to rapidly prototype and test products to ensure we’re offering customers the best-performing, lightest and most durable crank, ring and power systems.
INGRID Components: We actually don’t use 6000 series, it’s not enough strong for our stuff. Actually, we could use it for some parts, but very few. The advantage of 6000 series for us would be its corrosion resistance, at least. Of course, we don’t weld, so for us it’s not a point.
For cranks we use 2024, which you may describe as the middle-ground when talking about mechanical properties between 6000 series and 7000 series. For all the rest, if not steel, we love 7075, sure. But, it’s quite “delicate”. It all depends on what you are using the alloy for.
By the way, answering in a stupid way; I see the 7000 series like the beautiful, clever and rich woman/man anyone could wish for, and the 6000 series as your best friend that listens to you when you tell them you can’t handle her/him.
Ceetec: Thank you for the question. In order to answer it appropriately, it is necessary to first explain the nomenclature system for aluminium alloys. We explain the “EN AW-1234 X” naming system as follows:
- EN = Euronorm
- A = Aluminium
- W = Product Form (W = wrought alloy)
- 1 = Main alloying element
- 2 = Alloy Modification
- 3,4 = Designation for different alloys in the series (without significance for the user)
- X = Designation of different national variants
6000 series alloy (with Magnesium and Silicon) and 7000 series alloys (with zinc) are both very high quality; both have high strength and are often used for structural parts. The 7000 series alloys which contain Zinc, and even Copper, have the highest strength values.
6000 series has a higher elongation at break; that is, it has a greater deformation before it breaks, while 7000 series has a much higher tensile strength. Both alloys (6000 and 7000) are of very high quality. There are differences in regard to practical processing with, for example the following pipe profiles: e.g. 7020/7022 /7075 vs. 6061/6081.
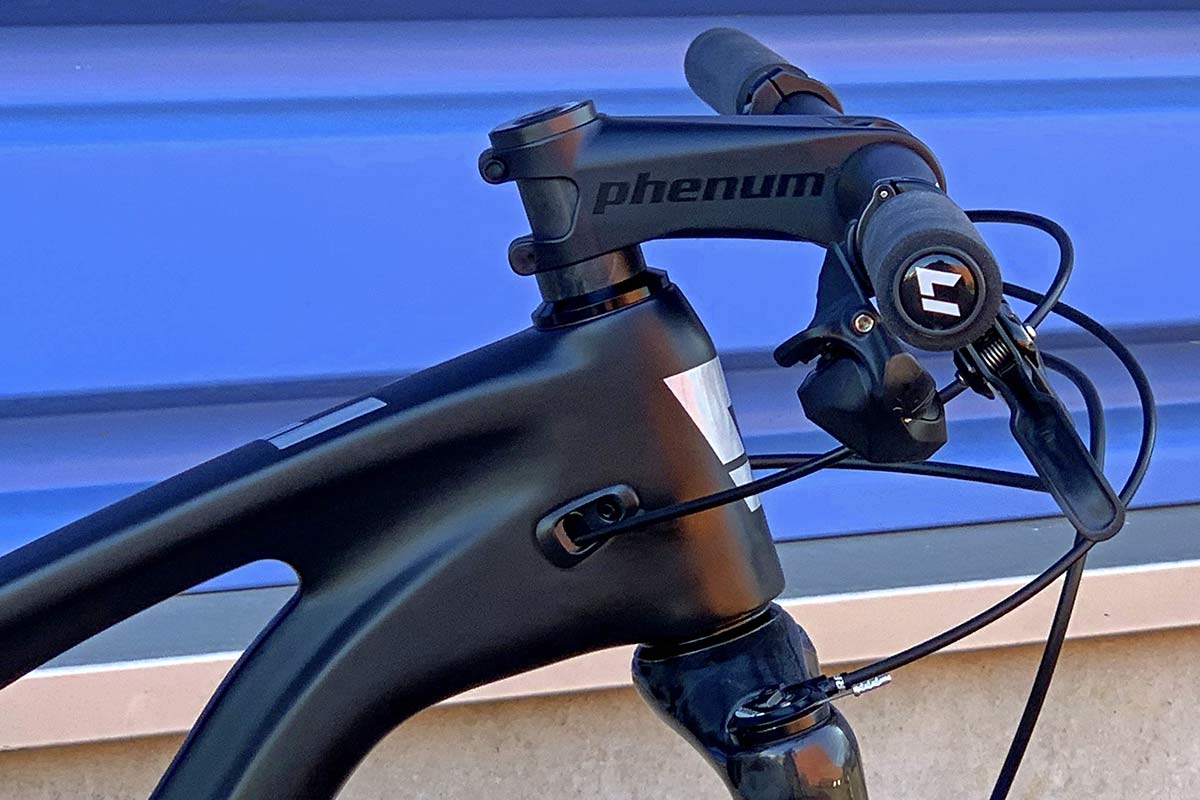
As mentioned above, the strength of 7020/7022 is higher than 6061, but above all, simpler
processing steps can be assumed (so-called artificial ageing). The increase in strength of ultra-high strength aluminum alloys is often accompanied by a loss of corrosion resistance. While 6000 series alloys with Magnesium and Silicon content exhibit very good resistance to various types of corrosion, 7000-series alloys with high Copper, Zinc and Magnesium content require special processing.
The greatest challenge here is stress corrosion cracking, which occurs at points with increased chemical corrosion sensitivity and under stress from tension. This involves not only external corrosion, but also inter-granular corrosion, against which it is not
possible to protect with coatings (anodizing) and sealants, etc.
So, if the strength is higher and the processing of 7000 aluminum is easier than that of 6000, why are there still manufacturers who build frames from 6000 series aluminum?
There are two main reasons: First, the strength of 6061 is very low immediately after quenching. This means that the frame can be straightened very well without large residual stresses resulting from the straightening process.
Secondly, the so-called elongation at break is higher in 6061 than in 7000 aluminum, so in the case of damage, the tube deforms a little more before it breaks; therefore it is safer in this regard. Both reasons can make a manufacturer decide to use 6061. Ultimately, however, one material is not significantly better than the other.
So, the reasons can also be found, for example, with the suppliers of the tube material. At least with the manufacturers who have offered very early welded aluminum frames such
as Cannondale, the availability of the material will also have played a role. Actually, the use of 7000 series aluminum clearly predominates.
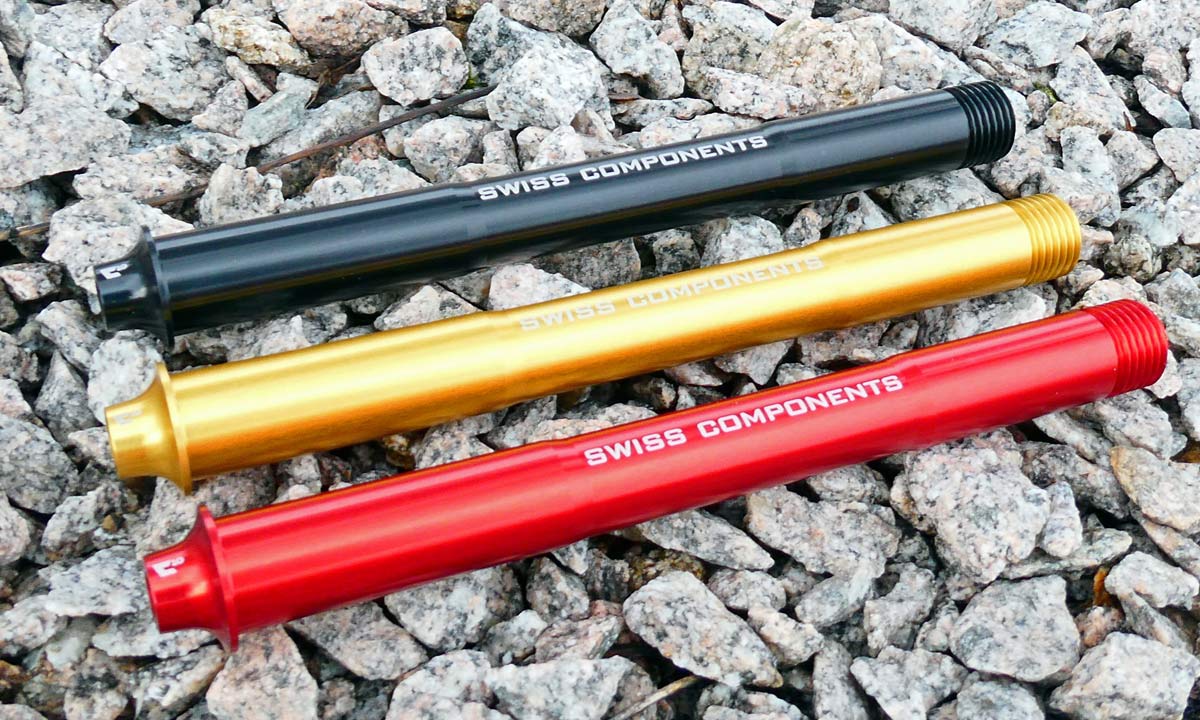
So, still very often economic decision parameters are factors, not to mention the market price to be paid and the how the quantity influences what the manufacturer buys. All or several factors can be taken into account by the manufacturer.
It is not possible to say that one is better than the other. It always depends on the application, their processing, whether they are to be welded or machined, etc., and their desired end product and their desired goal. If necessary, it also depends on the availability, as well as the experience the manufacturer and its processing technology has to hand.
At Ceetec, we use aluminum made of 6081, 7022 and 7075 alloys for our components, depending on the product and its intended use. Accordingly, the processing technology and machining must also be adapted in order to introduce a durable and reliable product
into the market.
A static component does not require the same properties as a dynamically (torsion
and shear) loaded component. Accordingly, different dimensions can be designed, which in the end is partly reflected in the total weight. Of course, a large portion of experience still plays a role. A manufacturer must know how the material behaves and what qualities can be achieved by its safe and stable processing.
The main focus for us, however, is solely the performance goal and the application purpose of the component (product), which is why we select and use one or the other material.
So, for our latest product, the Phenum C10 stem, the starting alloy is 7022.
RAAW: There are a number of different aluminium alloys commonly used in the bike industry. 6061, 6066 and 7005 are probably most widely spread. We use 6066 for our frames. It’s a bit more expensive than 6061, but also is stronger, both in tensile (single impacts) and fatigue strength.