We know, there’s no such thing as a stupid question. But there are some questions you might not want to ask your local shop or riding buddies. AASQ is our weekly series where we get to the bottom of your questions – serious or otherwise. Hit the link at the bottom of the post to submit your own question!
This week, our AASQ is all about carbon fiber. Specifically, the fully custom monocoque carbon fiber frame production of EXEPT bikes out of Italy. However, the questions include far more than just specific questions about EXEPT’s bikes, and cover much of carbon fiber frame production as a whole. Enjoy.
MATERIAL SCIENCE
Are you experimenting with any fiber reinforced thermoplastics? Do you think thermoplastics have a future in bicycle frame manufacturing?
EXEPT: No, we are not experimenting with fiber reinforced thermoplastics. We do not believe that reinforced thermoplastics have a place in bicycle frame manufacturing due to the loads applied to a bicycle frame.
Although already lighter and stiffer, CF frames are still not proportionally as light as its density to strength ratio promises compared to metals like Aluminum Alloys. Is monocoque construction in your opinion the manufacturing technique that allows the best use of CF material and thus lighter / stiffer frames as opposed to manufacturing techniques that mimic more traditional tubing construction?
EXEPT: Monocoque construction only allows us to achieve our high performance targets and engineer the structure of our frames to a defined performance target.
The stiffness to weight properties of carbon fibers are far higher than those of – say – aluminum. On the other hand metals are isotropic materials (they exhibit same properties in all directions) while CFs are orthotropic (different properties in the three main directions, which are vertical, horizontal, diagonal), having stiffness in fiber direction up to 40 times higher than those of cross fiber direction. Therefore it is necessary to compare a balanced layup (same properties in all directions) to a metal, rather than a uni-directional layup. In this case the overall CF stiffness is comparable to that of Aluminum. On the other hand the Aluminum density is 80% higher than CF density (2.8 Kg/mm3 for Al and 1.5Kg/mm3 for CF). Putting all these numbers together, for an aluminum frame to be as stiff as a CF frame, it will be 80% heavier. For instance 800g for the CF frame against 1440g for the Al frame.
Why are there so few attempts (and none apparently successful) for honeycomb carbon parts? Trek started and stopped, as did FRM a few years ago. Would adding quadratic moment to the structure make it a lot stiffer (assuming that’s what we are after)? Thanks
EXEPT: Honeycomb material is perfect for panel structures, not tubular structures. Distancing the laminate by another structure such as honeycomb will increase bending stiffness exponentially. This works for panels very well, but not for a bike tube, where the distance and cross-section is fixed. The second question is a good one if we are after tremendous stiffness increases and covered further down.
Carbon frame manufacturing: what value does a high end carbon frame deliver over a basic low cost frame (e.g. T700 prepreg copy of mainstream design), that would be hard to notice to an uninformed buyer?
EXEPT: Our frames are not only produced by using solely high-end fibers, but mainly by using the right fibers in the best performing way. Using high-end material for the frame without optimizing fiber directions, tube shapes, and cross sections – and without considering load paths – will not result in a superior product. An entry-level open-mold design will not all of a sudden become the best high-end frame in the market, just by producing it with the best performing fibers. It is actually the opposite, for example it potentially can break in a normal situation or be just as stiff as a steel frame. The beauty of carbon composites is that it not only allows us to design all sort of shapes, but also to design the material the shapes are produced in, and therefore enables us to optimize the performance and characteristics of the final product.
Between mid-tier carbon frame sets and the highest end with high modulus carbon, is a mid-tier frame more durable?
EXEPT: I think this question gets into the direction of product safety. There are other aspects to consider which impact the safety of frames than the modulus of fibers used. Production quality, bond joints, adhesive contamination and expiration date of materials all have a huge impact on durability. All of them are quality aspects. And this is were we as high-end frame producers outperform our competitors and mid-tier products as we have the production control over these aspects on our side.
Durability of carbon fiber frames itself is driven by the bonding between resin and fibers. Frames fail durability tests mostly in the first hour of testing due to overloads. The failure modes of carbon frames are hard to compare to metal frames, for instance there is no crack propagation mechanism (how a micro-level crack is developing in the material structure until the part is failing for composite materials).
Over the lifespan of carbon fiber frames, the stiffness might decrease as the fibers detach from the resin matrix and start moving relative to each other. This is rather a matter of performance loss, than a safety issue and applies to any carbon frame – high-end, mid-tier and entry level.
What’s lifetime expectancy of a carbon frame?
EXEPT: Check above. Stiffness of a well-designed frame might decrease by 5% after around 100000km, but it is depending on many factors if the rider is feeling this effect.
What sort of UV resistance do modern CF resins afford, especially compared to what was available 10 years ago or 20 years ago?
We are offering some graphic options with lots of visible carbon fiber, especially our “La Bastarda” version. In order to guarantee UV resistance, we are using on the outer side a special resin system with increased UV resistance. In the last years these resin systems became very popular and there are now resin systems available not only for structural purposes, but also for aesthetic purposes.
PRODUCT AND CUSTOMIZATION:
What is the smallest 700C disk road bike Exept can make? Why does it take so long for CF builders to accommodate a strong market with physically small riders?
What is the average lead time for a Exept custom frame? Thanks.
EXEPT: We are able to produce down to a reach of 340 mm and a stack of 500 mm. The picture below for instance shows the minimum and maximum headtube we can produce with our adjustable custom monocoque tooling. We do not categorize our customers by size groups, gender, or specific markets. Each rider gets his or her custom EXEPT.
Small and bespoke builders always have the advantage of being more flexible to make products suited for customers out of the commercial target norm-type. We can only think of big brands putting their focus and R&D investment into a range of products suited to what they define as their commercial target customers or what they statistically sold the most over the last years.
Our lead-time is 8 weeks. Each order gets phased into production individually, which requires time to manage, plan and actually produce. But we try to be as fast as possible as the market is moving quickly with useful innovations such as disc brakes and sometimes also questionable “innovations” such as proprietary standards of big brands. In any case, we do not want to deliver an outdated bike.
Frames can be made in many sizes easily, why do most companies make use of a single fork for all the sizes? It is harder to make size specific fork than frame?
EXEPT: Our bikes are offered in two riding styles – race and endurance. We adjust this riding style by combining forks with two different rake numbers with an infinite adjustable head-tube angle, in order to create a defined fork trail per rider and riding style. We can do that, because our tooling is adjustable, whereas most companies are restricted to size-specific tooling and therefore limited to customize the geometry around the front end of the bike. Tooling investment, qualification and sourcing model surely plays a role for mass production companies when it comes down to how size-specific they want to be.
Are there limits to how custom you can go?
EXEPT: We freeze some design and spec aspects in order to simplify simulation, lay-up analysis and also product qualification. It is not possible to swap the BB area for one with a threaded bottom bracket for example, or create a frame with more than 30 mm tire clearance.
Do your frames include a warranty?
EXEPT: We are offering a limited lifetime warranty for first owner and also offer a crash-replacement program.
R&D
Where do you intentionally design the bike to flex? When and where on the bike can compromise ride quality by being too stiff?
EXEPT: We design our frames to be as stiff as possible under pedaling forces – BB stiffness. We are designing toward a sweet spot of torsional stiffness – called Head tube stiffness. This torsional stiffness highly impacts the ride quality. A frame with a headtube stiffness value that’s too high would end up being very nervous and harsh to ride, especially on fast descents. It would also lack character, which is hard to quantify but would be felt when riding the bike. Flex is designed into the seatstays. We uncoupled the torsional and pedaling stiffness from the vertical stiffness induced by forces on the saddle and by doing so, we define our level of comfort.
And that brings us to a bunch of other questions:
Re: carbon bicycle manufacturing: Is the 5% stiffer every year and 12% lighter all marketing BS? I’ve seen no new materials, so is it all from the advertising section of the brand or the factory floor? Is there data to back up claims? Thanks
EXEPT: Surely every brand tries to present their data in a way that puts them into the best light. If it is all marketing BS or even false claims, it’s hard to tell. In recent years development has come closer to reach a sweet spot. Iterations from one bike generation to the next bike generation show smaller jumps in such performance metrics than when carbon fiber started to be used as the main frame material for performance bikes. Also new technology such as disc brakes have an impact as it opens doors for engineers to new design solutions. If these improvements are only an evolution or even a revolution — that can only be answered by experiencing the bike.
In our case, as shown below, we are designing and developing toward a defined target. That may be the right head tube stiffness, or being competitive within a pre-defined range of, for example, bottom bracket stiffness. It is secondary to us if our Classic version is 1.5% stiffer under pedaling forces than the Integrated version or 8% lighter (or heavier) than one of the race winning bikes seen on television. Our goal is to make the best fitting and at the same time, the best performing bike for each individual customer. The graph shows the distribution out of almost 1000 carbon frames produced and tested in the last years, our target, and how our EXEPT Classic version is scoring. We have to mention that some performance characteristics are in conflict with others; it is not possible to be the stiffest and lightest at the same time.
How ‘flexy’ could a frame be made and not break? I see airplane wing tests where they bend them 45 degrees without breaking. Can we do the same with bike frames?
EXEPT: Yes, it would be possible to create an extremely flexible bike frame. Generally speaking, there are families of fibers, some have high modulus and low strength and some vice versa. Using these materials it would be possible to achieve any behavior. Does it make sense is another question. We design flex into our road bike to offer a desired level of comfort on the back, but we are not after a sort of soft-ride effect or a certain amount of travel.
Are the labour costs the critical aspect in the carbon frameset prices?
Is it possible that a European made frameset can compete in price and quality with the Asian ones?
EXEPT: For us, producing in Europe is about more than only cost and quality. Obviously cost optimization is a very important topic for any production location. 20% is material cost and 80% is labor cost. But we are happily accepting a higher overall cost to guarantee the highest and consistent quality, best performance and more importantly – all made-to-measure for our customers. We are aiming high in all three aspects and found they can only be met by producing in Europe. More precisely in Italy, where there is a deep knowledge of carbon fiber design and production and a long history in making bicycles. Plus speaking the same language during the project phase helps a lot.
How much of a frame layup design is done using FE analysis and how much is down to testing?
EXEPT: Our frame layup design is done 100% using simulation, not only FE analysis of performances and impact testing, but also simulating of the layup process considering ply drapability. Testing is performed only to confirm the simulation results. We don’t believe in trial-and-error. This can be achieved only if the overall simulation process and the production process are fully under control. If so, the deviation between simulation and test is within a 5% of deviation range.
Below is an example for a ply definition for our downtube section.
What type of analyses are used to assess resistance to impact (direct to frame or through the “normal” introduction points like lugs, bearing etc) of carbon fibre frames?
EXEPT: We used FE direct transient analysis to simulate impact tests of our frames and traditional linear analyses to assess the frame performances. In normal words for those of us who are not stress analysis engineers, our standard for simulation and testing is ISO4210, which covers horizontal impact – crashing against an obstacle – on the front, and vertical frame falling – hitting a pot hole.
Interestingly the forces on the frame range up to 5000 N in some of the scenarios. We are looking at the frame and fork assembly as a whole and at points with high stress in detail, independent if they are bearing seats or connection points (we do not use lugs or wrap material but consider those areas as joints).
How is manufacturability assessed during the design phase and are layup defects such as ply migration, waviness and porosity a common issue during the dev phases?
EXEPT: We are testing frame stiffness for each one produced to detect defects in the lay-up during production by comparing it to our own internal standard. We also apply destructive testing per batches of produced frames. During the development phase it is not possible to consider these defects.
Is there a good place to start for beginners to building bikes/components out of carbon fiber; text books, websites, or similar?
EXEPT: Most of us in EXEPT touched carbon fiber and composite materials for the first time back in university while earning our engineering degrees. But the raw material is accessible, and getting your hands dirty with laying-up simple structures to familiarize yourself with the material is a good start.
What is the tooling like…do you use/have infinite molds ready?
EXEPT: Our tooling is adjustable and covered by a patent we are holding. We are having just one set of tooling, which can be adjusted to any geometry and the two riding styles we are offering: race and endurance style. In addition to its adjustability, it is modular, which allows us to create the two versions. We can change the head tube area, and the seat tube to seat stay joint area to include an integrated cockpit and integrated seatpost to improve overall aerodynamics in our Integrated versions.
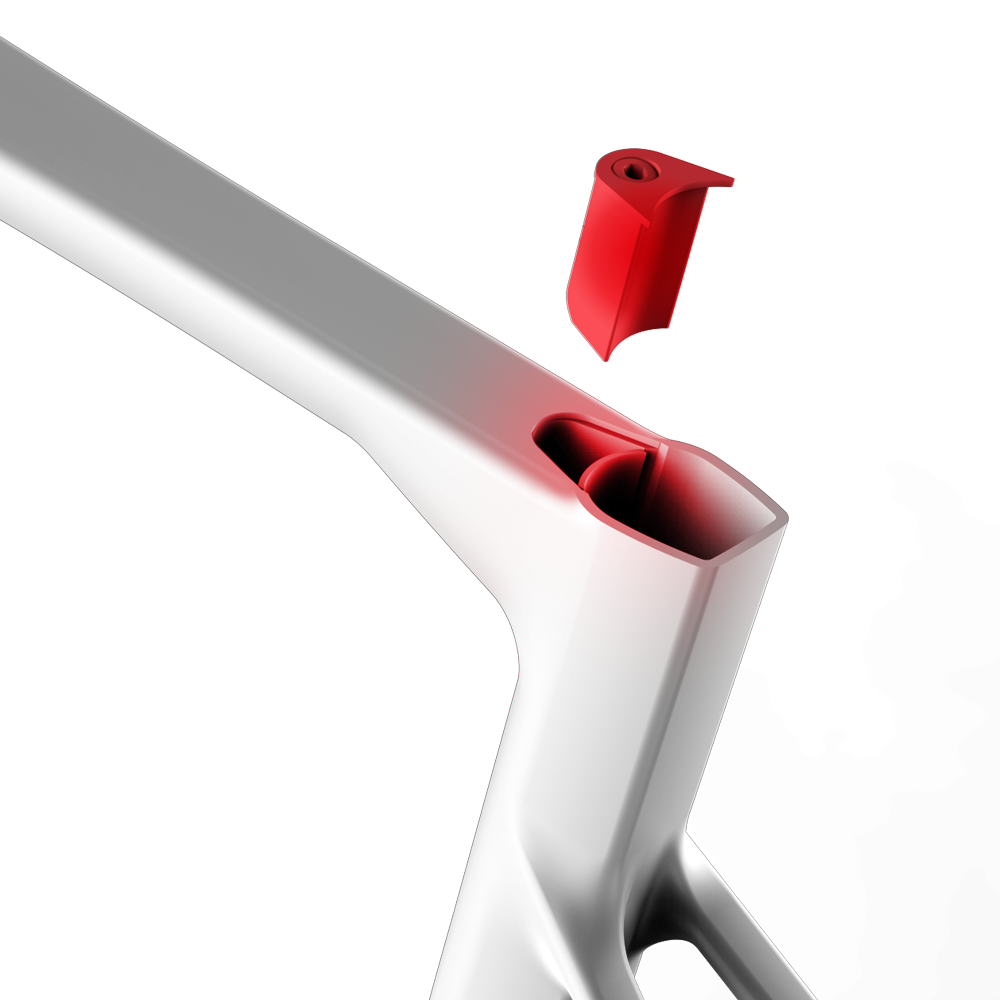
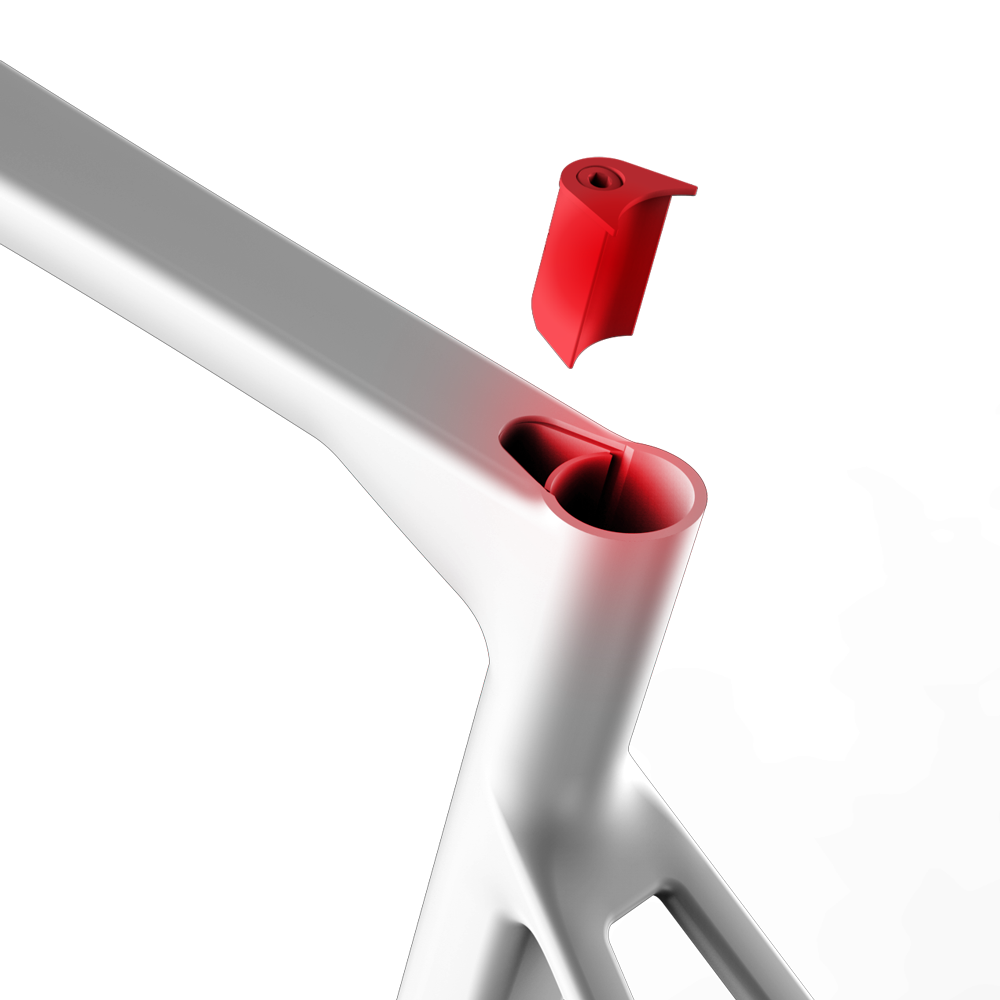
Can the customer dictate the carbon layup?
EXEPT: We are only applying our lay-up because a customer-dictated carbon lay-up would result in a frame not being ISO qualified. There is one slight exception as per the next question though.
Do your bikes have a weight limit? Or can you build them to suit riders of any weight or size?
EXEPT: Above 100 kg of rider weight we are reviewing the lay-up and modifying the lay-up for the customer to build a bike suited to any weight.
Got a question of your own? Click here to use the AASQ form and submit your own question!