We know, there’s no such thing as a stupid question. But there are some questions you might not want to ask your local shop or riding buddies. AASQ is our weekly series where we get to the bottom of your questions – serious or otherwise. This one concerns all things crankset related. Hit the link at the bottom of the post to submit your own question!
Ever wondered what crankset material is most efficient for power transfer? Or what crank length you should really be running, despite what came stock on your new bike? We sent these reader questions and more to the experts at ROTOR, SRAM and Shimano. Thank you to Lori Barrett at ROTOR, Alex Rafferty at SRAM and Nick Murdick at SHIMANO for taking the time to respond.
How does crank length affect pedaling efficiency?
ROTOR: For most people, pedal stroke efficiency is more greatly impacted by an adjustable oval ring, like ROTOR’s Q Rings, than crank length. The ability to smooth out the application of power through the pedal stroke is easy to visualize on our INpower app, and modify with an adjustable oval ring.
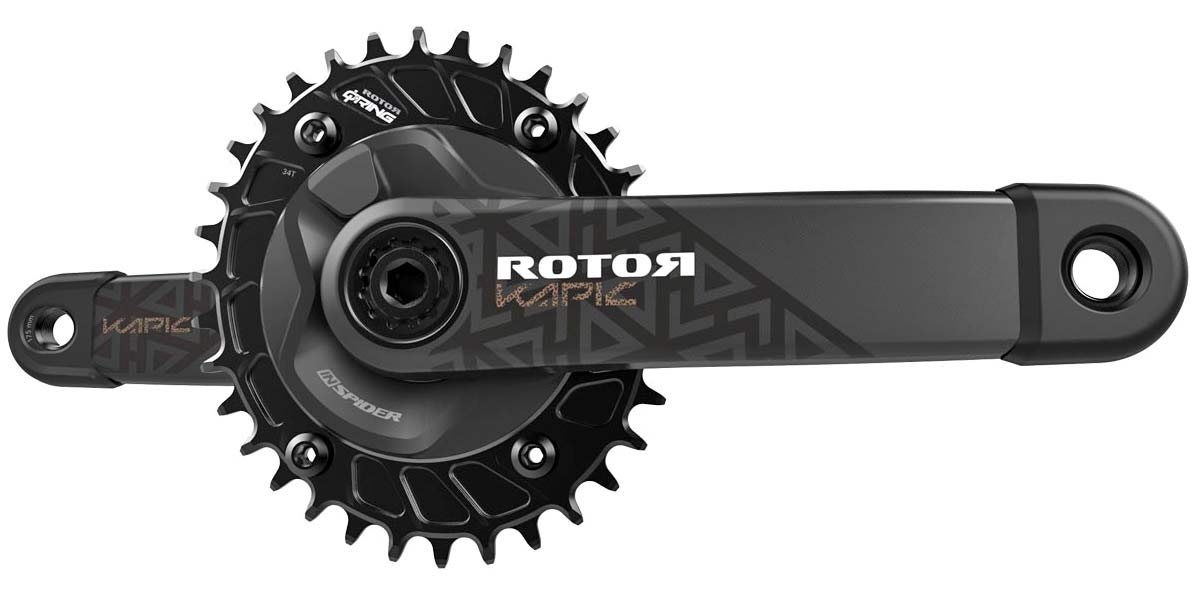
Coming back to the question of crank length, however, it’s most important to note that it is a very individual puzzle, dependent upon the biomechanics of the rider, the geometry of the bike and goals for performance.
1. First and foremost, determining crank length is a matter of proper bike fit. Incorrect crank length can lead to biomechanical issues and injury, which cause reduced performance. Shorter cranks do reduce the upper angle when the foot is traveling over the top of the pedal stroke: a hyper-flexed knee places excessive shear forces on the patella and associated articular cartilage, often causing knee pain. Shorter crank arms relax this angle, thus reducing shear forces on the knee.
2. Additionally, a properly sized crank can help the rider spin a more effective cadence by reducing the overall distance the foot has to travel in one rotation. While it’s true that peak power is somewhat reduced (torque=force applied x lever arm length) there has been some research into the overall effect of the crank arm length by Jim Martin, Ph.D. of University of Utah (Determinants of Maximal Cycling Power: Crank Length, Pedaling Rate & Pedal Speed. Martin, JC1, Spirduso WW.). That research showed a minimal ~4% difference in overall power output across an entire range of crank lengths.
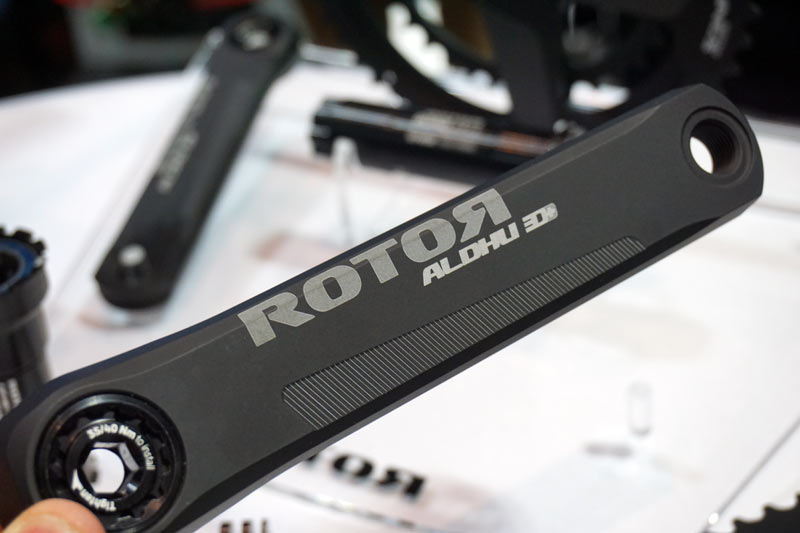
3. Lastly, a shorter arm will afford the rider a more aerodynamic position, resulting in a higher speed at a given power output. ROTOR offers crank options from 150mm to 175mm to accommodate most rider & bike set ups.
SRAM: I would suggest the best approach for this is factoring in the correct crank length for the user’s needs. Weighing up the rider’s height and also the desired pedal clearance with the ground.
A tall rider might prefer a 175mm crank whereas an average height rider may prefer 170mm or even 165mm. There is a notable difference on the amount of ground clearance on the shorter cranks that are better suited to bikes with lower BB’s.
SHIMANO: The short answer is that crank arm length doesn’t impact pedaling efficiency with the commercially available sizes on the market. Crank arm length selection does, however have other effects on riding, and it’s good to consider factors like back and knee pain, ground clearance, and center of gravity.
The recent trend in mountain biking is to use shorter cranks than the default selection of 175mm which began in the early days of mountain bikes. When using shorter cranks, your pedaling RPM will increase marginally to maintain the same power which is the consequence of reduced leverage.
Riders started using 170mm and shorter crank arms to improve ground clearance, especially because of the increase in pedal strikes from lower bottom bracket heights on modern MTBs. After all, pedaling won’t get you anywhere if your pedal hits a rock.
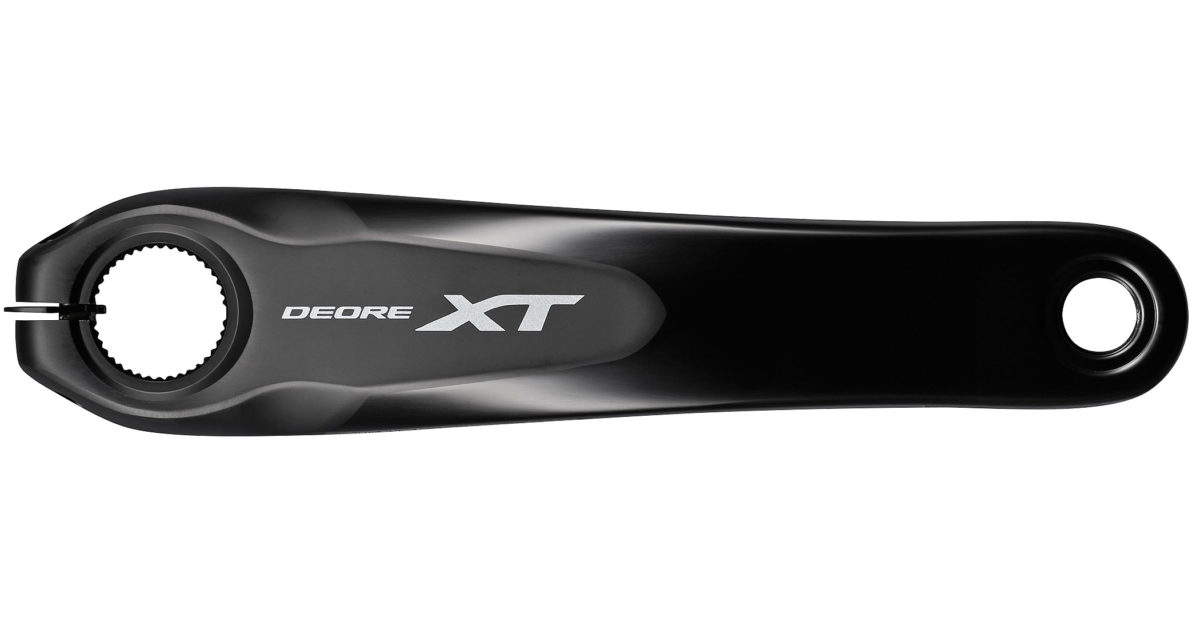
After trying it out, many appreciate the reduced back and knee strain from turning a smaller circle each pedal revolution, which can lead to a bit more left in the tank at the end of an epic ride. Of course, shorter cranks also means raised saddles. This can provide another benefit by allowing for a longer drop seat post, but it also raises the center of gravity during pedaling.
It can feel a bit strange during technical climbing, so that keeps people from going with super short crank arms on trail bikes. At the moment, we’re seeing 170mm emerge as the new default crank length on those bikes.
Is there a difference in the transfer of power between a direct mount chainring setup and spider plus chainring setup?
ROTOR: We created direct mount rings as the lightest, stiffest, best-shifting rings on the market. We do offer spider-interface rings with a greater variety of aero & BCD specs, but anytime you add interfaces there remains the potential for inefficiencies.
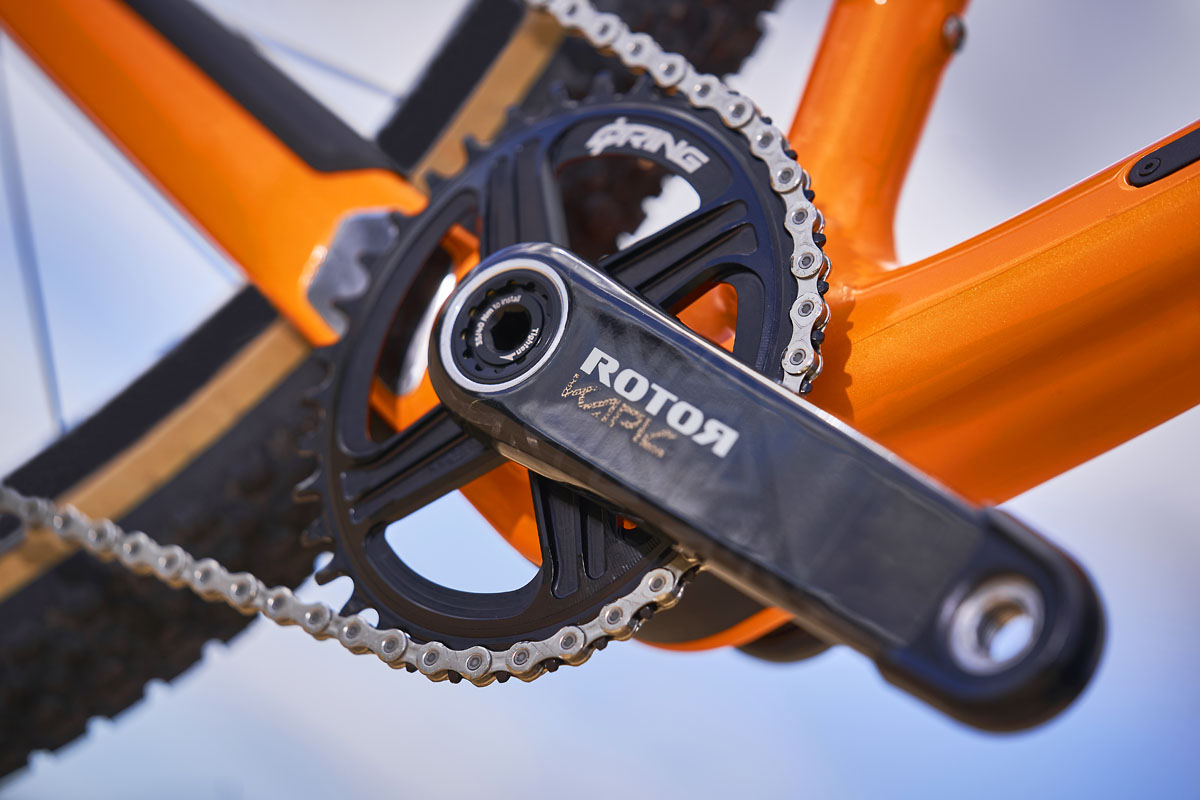
SRAM: It depends on the specific products you are comparing. There are many factors to take into account that would have to be considered in order to calculate the difference in power transfer. But to keep this relatively straightforward, I’ll keep this to stiffness and weight. In theory, the lighter and stiffer such a product is, the less loss there would be in power transfer through a reduction in rotational weight, and bending/flexion.
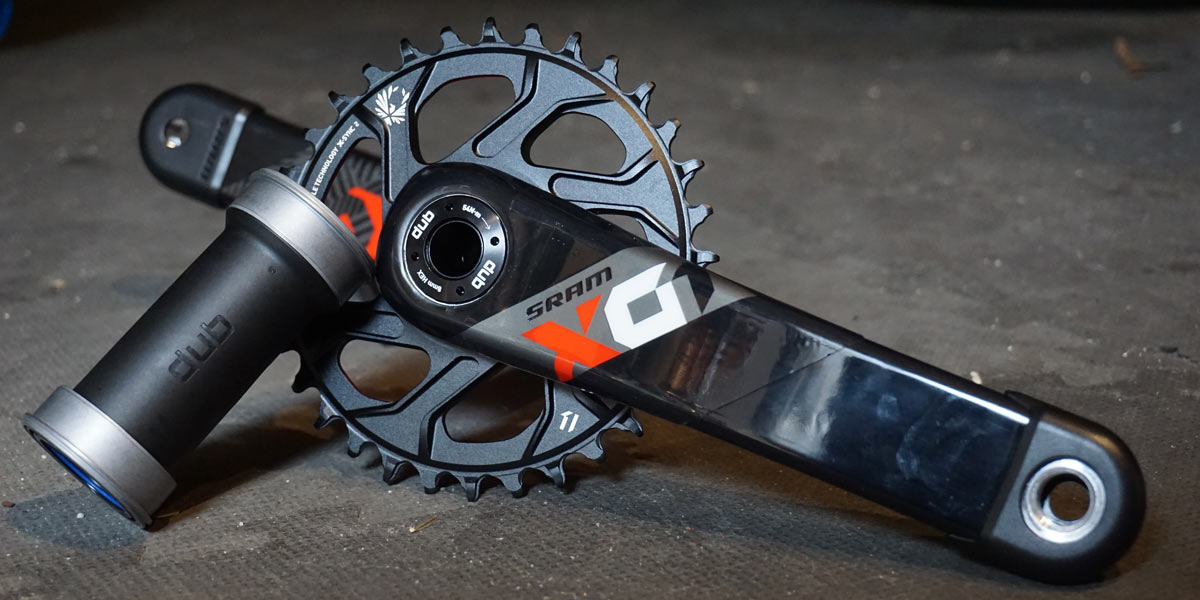
However, that’s not to say you should necessarily make a product as stiff and as light as possible – there is a delicate balance between compliance, comfort, stiffness, weight, materials, durability, structural integrity and more. Regarding the question on cost, this might give some further insight into why the costs of developing and prototyping such components is significant.
SHIMANO: I wouldn’t necessarily assume so, since an efficient power transfer can be achieved with either design. Shimano’s most efficient design in terms of power transfer would be found on our DURA-ACE crankset.

This integrates the chainring spider into the arm itself, extending the hollow portion all the way out to the chain ring bolts, which are placed as close to the teeth as possible for greater efficiency. The chainrings themselves are also a hollow aluminum construction to further reduce weight and increase efficiency. As you can see, the question is often really about efficiency vs weight.
What’s the best material for a crankset in terms of optimal power transfer?
ROTOR: In terms of optimal power transfer, different materials have different strengths and weaknesses. Of course, the stiffer a material is, generally the better the power transfer will be, but everything comes at a cost.
Steel and titanium both tend to be flexible (thus the “lively” feel of steel-framed bikes and the spring of ti,) while aluminium and carbon provide the best stiffness to weight ratio in components.
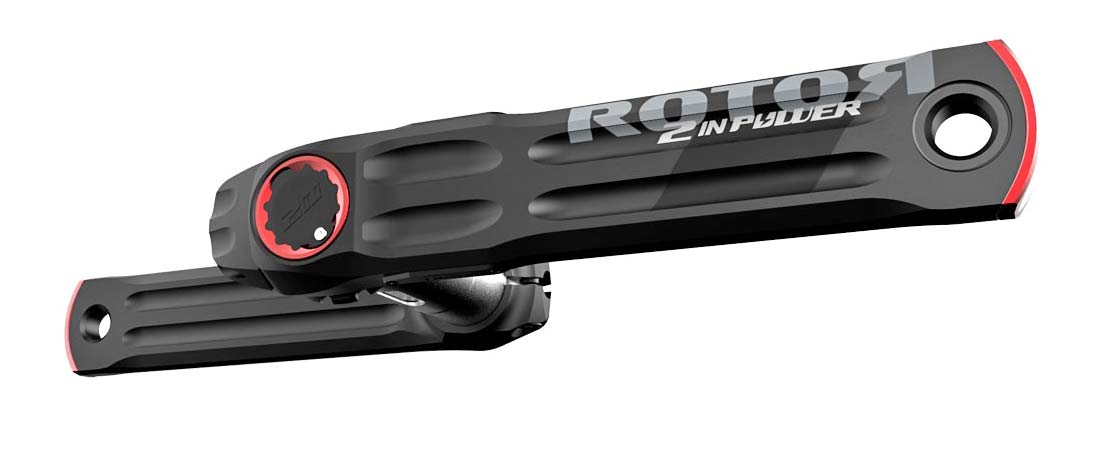
Carbon is more complex, however: the strength depends on the direction of the fiber and the resilience of the resin used to bind it, creating a wide array of potential outcomes from heavy and not-that-stiff, to quite stiff and light. A high grade of aluminum, like ROTOR’s 7-series used in our 2INpower and Aldhu cranks, is incredibly strong.
Combined with our Trinity Drilling System, it allows us to remove all excess material weight without sacrificing stiffness or performance.
SRAM: Carbon. With our manufacturing processes we’re able to consider the right amount of compliance, comfort, and material amounts to optimise performance delivering a crank with minimal loss of human induced power.

It’s entirely possible to use more material or even a different material to increase/reduce one performance component, but none of those components are mutually exclusive and will all be affected by the change in given material or process in some way. More research and development to explore (there’s a theme here).
SHIMANO: Shimano’s entire crank lineup is aluminum, so clearly we firmly believe it is the best material for a crank arm. We do make a lot of things out of carbon and our story has basically been that we’ll happily make a carbon crank if it means we can make the product lighter, stronger, stiffer, more durable, and more efficient.
We don’t have specific data to share about driving efficiency of different materials, but I would encourage riders to think about the entire package. For example, our bottom bracket uses a unique bearing and seal design that is very competitive out-of-the-box but compares even better with age.
We actually use smaller bearings at the DURA-ACE and XTR level in order to decrease the area of the seal exposed to contaminants. That’s because the number one factor in bearing performance is eliminating contaminants.
The seal is also a three-piece labyrinth seal design which is very effective at keeping the bearings turning smooth when the training is done and race day comes. We could state that larger bearings empirically have less resistance to rolling, but that is far from the complete picture.
Can I use a 10-speed crankset with an 11-speed drive chain?
ROTOR: Our 2x rings are 10 & 11 speed chain compatible. Although chain width has narrowed over the years as gears have been added, chain pitch has remained consistent between 10 & 11 speed drives.
Additionally, crank and spider design are unchanged between the eras of 10 & 11 speed drivetrains, still relying on our Universal Bottom Bracket spindle concept. Chain requirements have demanded a greater variety of 1x ring tooth profiles, however, so it’s important to be sure you have a matched-speed compatible-ring to your desired 1x drivetrain. ROTOR makes rings compatible with all current drivetrains, including AXS, Eagle, XTR, and numerous others.
SRAM: It’s important that you use the designated chain ring with the number of gears for the given drivetrain. Eagle chainrings are backwards compatible to 11-speed. The chainring on a 10-speed crankset is not specifically designed to work with an 11-speed chain.
SHIMANO: The design of our non-shifting chainrings is the same for 10 and 11-speed systems. So in that case, yes. It works because the chain’s inner dimensions and the thickness of the gear are the same.
However, the outside dimension of the chain is different and this is a key specification for front shifting. The rings on a 10-speed crank would be too far apart, so using one with an 11-speed drivetrain would result in slow shifting and chain drop.
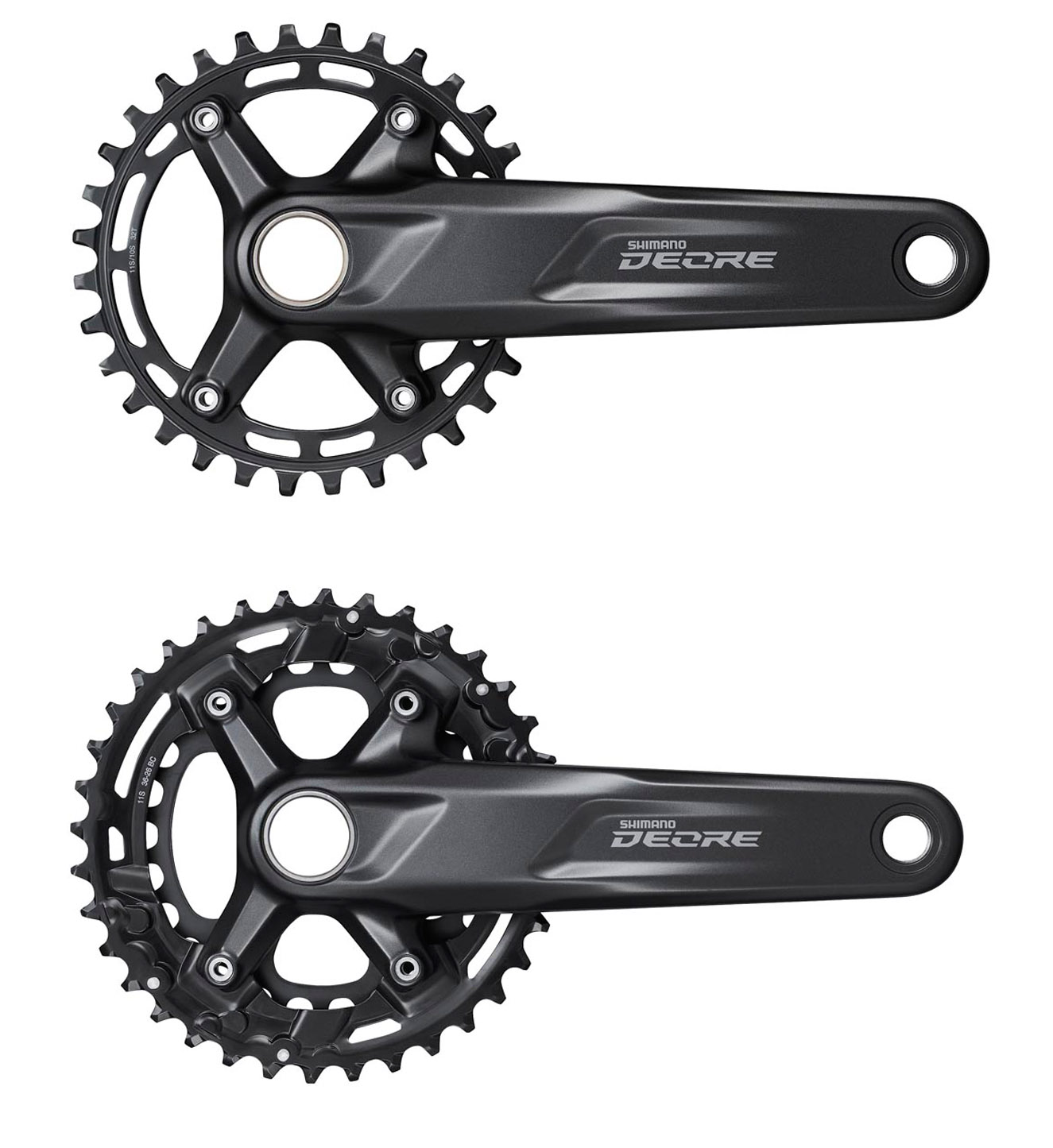
The tooth profiles are also different between 10 and 11-speed front chain rings. If you used the wrong crank, you could have unexpected chain drop when pedaling under power even if you aren’t in the process of shifting. This can be very dangerous and should absolutely be avoided.
Where can I buy a replacement spindle for my SRAM BB 30 crank. I need a 104mm to fit my threaded 30mm bottom bracket. The spindle is about 10mm too short.
SRAM: You cannot buy a replacement spindle alone.
What’s a FAT4 and FAT5 crankset spindle standard?
SRAM: These cranks sets are available to suit the needs of our OE customers equipping SRAM products to their frames. It’s literally the measurement of the spindle in inches.
If I smash the end of a crank arm off a rock is it still safe to ride with? Are crank protectors actually necessary?
ROTOR: Smashing a crank and taking off the end of your crank demands case-by-case evaluation: if a strong impact is sustained, it will be worthwhile to visit your local bike shop and have the crank checked for further damage.

That being said, certain materials are more impact resistant than others. This is part of the reason why ROTOR offers the majority of our cranks in a 7-series alloy, to be as durable as possible, while maintaining KOM-friendly weights.
SRAM: It very much depends on the impact. As with any product it would be sensible to inspect for any signs of damage or fatigue. If you are not comfortable with the appearance or performance of the product after such an instance then it should be taken to an expert to examine.
Crank arm protectors will protect the pedal eyelet area of the cranks on a given impact. On carbon cranks they certainly help with reducing the impact force and protecting the structural integrity of the product.
SHIMANO: Generally speaking, mountain bike components are designed to withstand some impact normally associated with riding off-road. The local bike shop should be the one to make the call about the safety of a crank after a particularly large impact. Shimano cranks are 100% aluminum, so crank arm protectors would only be useful for cosmetic purposes. We do not produce or recommend any.
Why do cranksets cost so much money?
ROTOR: Cranksets take a lot of time, engineering and testing to develop: at ROTOR Bike Components, we work to ensure our cranks fit every frame standard, past, present or future!
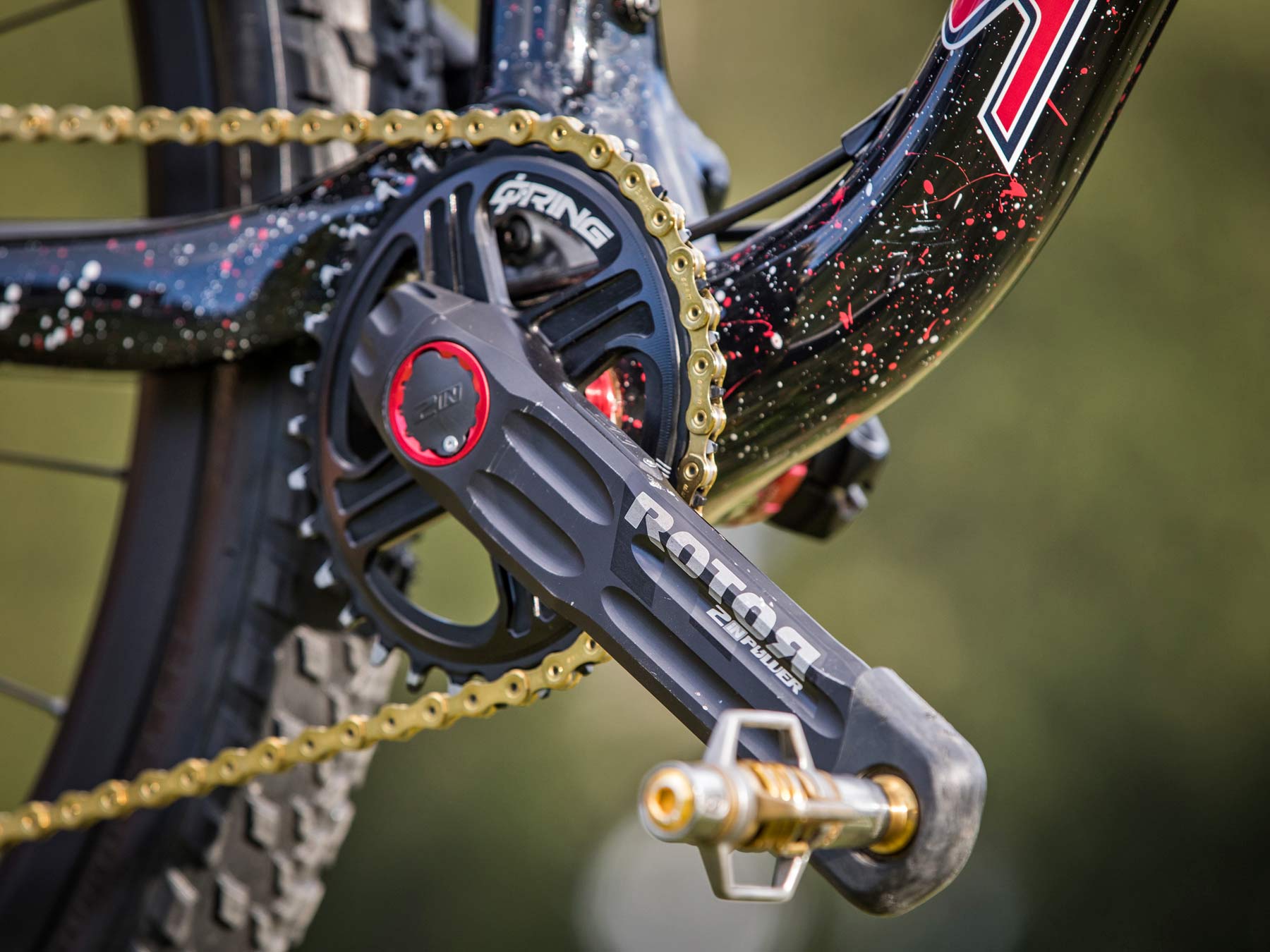
The product itself starts with the highest-grade aluminum for best durability, and in order to make a lighter product, we invest in additional development and machining to winnow the materials down to the strongest but lightest product possible.
Additionally, since we believe it’s important to manufacture sustainably, we pay to recycle the cast-off material, and of course pay standard EU wages since we have opted to keep all key production in Spain.
SRAM: The SRAM products which are available in the marketplace are delivered to meet the needs of the consumer. We make cranksets at £80 RRP (SRAM SX Eagle DUB) for the consumer who’s looking for a reliable, long lasting, solid performance and cost-effective solution for their bicycle.
We also make cranksets for the cyclist who wants the very best in terms of technology, materials, engineering and performance designed to win World Cups, such as the SRAM XX1 crankset.
Just like all of our products, the cost of an item at retail is reflective of the entire process of bringing the product to market. Research and development, prototyping, manufacturing, materials, logistics and all the other operational costs. We are proud to be able to give the consumer a wide choice of products to suit all riders.
SHIMANO: Not all cranksets cost a lot of money. Rather the light, strong, stiff, and durable ones do. The answer to that question is probably simply that there is more we can do to a crank to make it lighter, stronger, stiffer, and more durable, but since that component is under some high loads those improvements can be costly.
For cranks, as we move up in the lineup the materials used changes. At the lower end we have a solid aluminum crank arm with steel hardware, steel bolted on (or riveted on) chain rings, and a separate square taper bottom bracket.
At the higher end, the XTR crank is all aluminum, except for the integrated spindle. This is a rare case of a bike component being made lighter out of steel since we can use less material.
This crank uses a high tech hollow bonded construction for maximum weight savings, and an aluminum direct mount chainring with a special surface treatment to make it as durable as other steel chainrings without the weight penalty.
Tyler Benedict joined us for a factory tour in Japan to see XTR crank production first-hand back in 2018. He saw the extra steps required to make the XTR and DURA-ACE cranks; a combination of forging processes, additional machining after forging, and the clean room where the proprietary bonding techniques takes place.
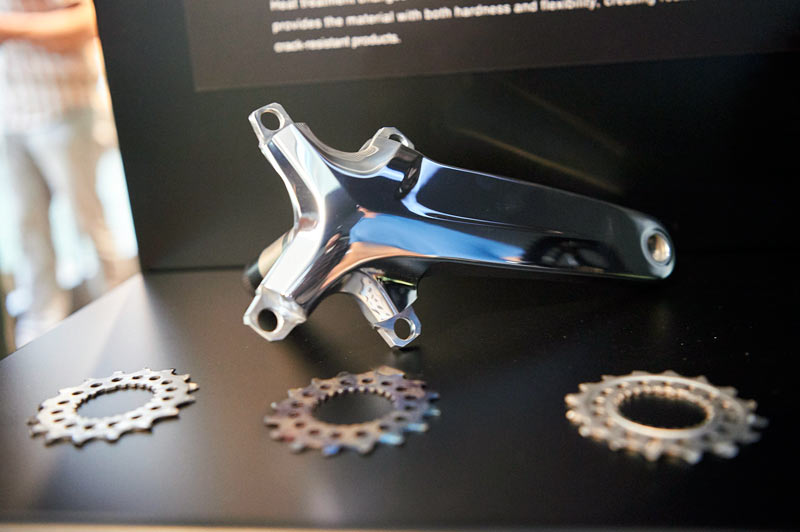
He didn’t get to see the surface treatment area, but that is where we harden aluminum XTR chainrings to make them durable enough to stand up to the rigors of riding in the dirt. One last important factor is that our best components are made entirely in Japan by our most skilled workers.
Got a question of your own? Click here to use the AASQ form to submit questions on any cycling-related topic of your choice, and we’ll get the experts to answer them for you!