We know, there’s no such thing as a stupid question. But there are some questions you might not want to ask your local shop or riding buddies. AASQ is our weekly series where we get to the bottom of your questions – serious or otherwise. This one is about wheel design, covering symmetrical versus asymmetrical rims, spoke butting, stiffness versus compliance and more! Hit the link at the bottom of the post to submit your own question!
When it comes to choosing wheels for mountain biking or road cycling, the choices seem endless. It can be a complete minefield, with asymmetric or symmetrical rims to choose from, on top of rim width choice, carbon or alloy, butted spokes, before you even start to consider that you might want a super stiff or compliant wheelset. Then you have to consider how your favorite tyres will seat on the rim! And that’s before you even get started on the hub.
To help you understand why different manufacturers build wheels the way they do, we sent a host of reader questions on wheel technology to the experts at Hunt, Crankbrothers, DT Swiss, Vittoria and Stans NoTubes.
It may not tell you specifically what your next wheelset should be but it should help you understand a little more about wheel technology so you can make a more educated purchase.
Why are some wheel spokes butted and others plain gauge? What’s best for stiffness?
HUNT: Butted spokes have different diameters throughout the spoke, usually thickest at the hub end, then taper thinner towards the middle before getting thicker again nearer the rim.
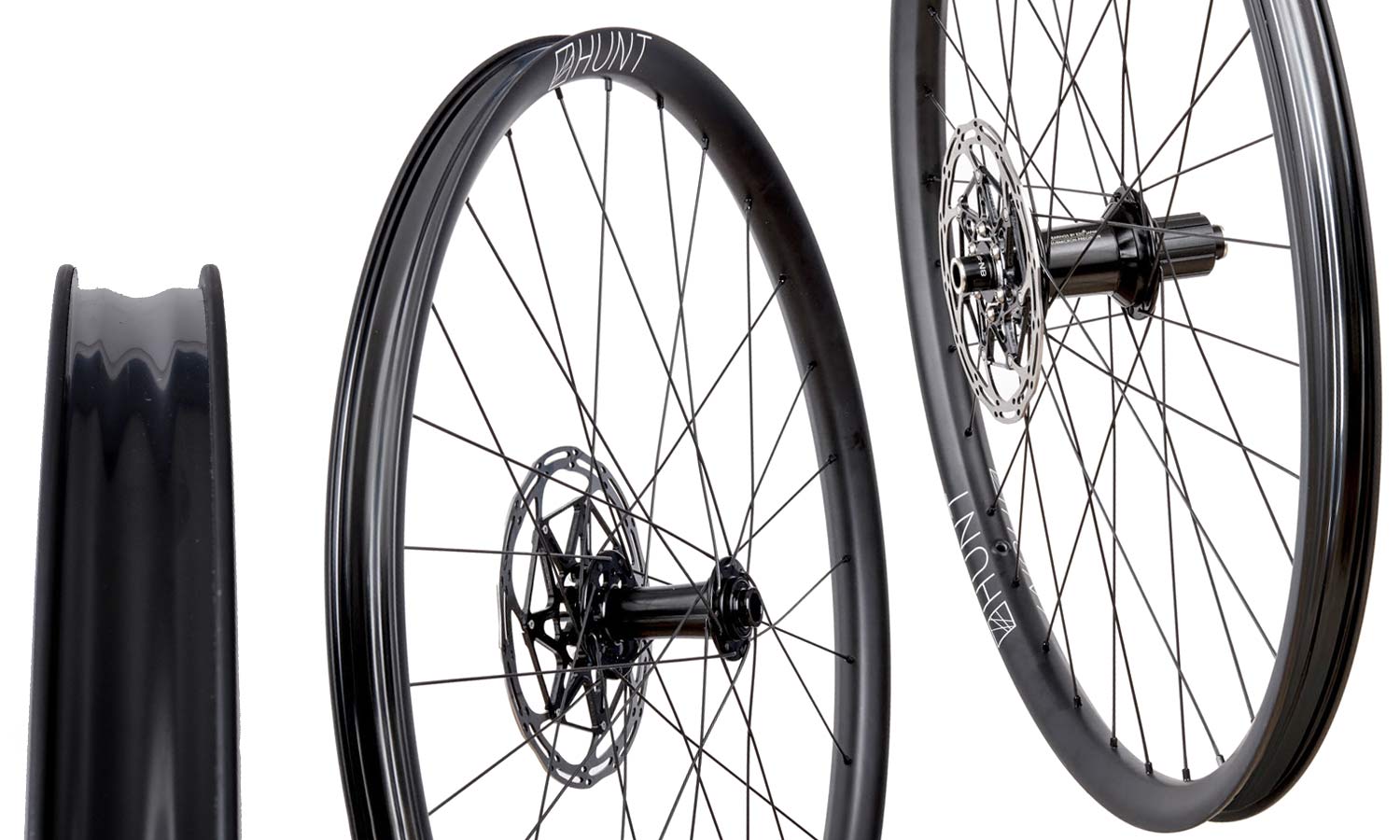
The key benefit of butting is lower weight and a more flexible, or elastic, nature, so are less likely to break under fatigue. Because of this, they tend to last longer than straight gauge spokes which have a constant wire diameter throughout their length.
Straight gauge spokes are therefore heavier than butted ones but do have higher lateral stiffness owing to their constant thicker cross section. The flip-side of this stiffness is that they are less elastic, and therefore are more likely to break under fatigue. They’re easier and cheaper to manufacture.
Crankbrothers: Different spokes for different folks… and also different applications. As the technology and manufacturing capabilities for spokes has evolved the shape and profile has been refined.
A butted spoke typically has more material at the thread or head ends with a thinner middle section. This means the material is where it is most needed to manage strength and fatigue requirements.
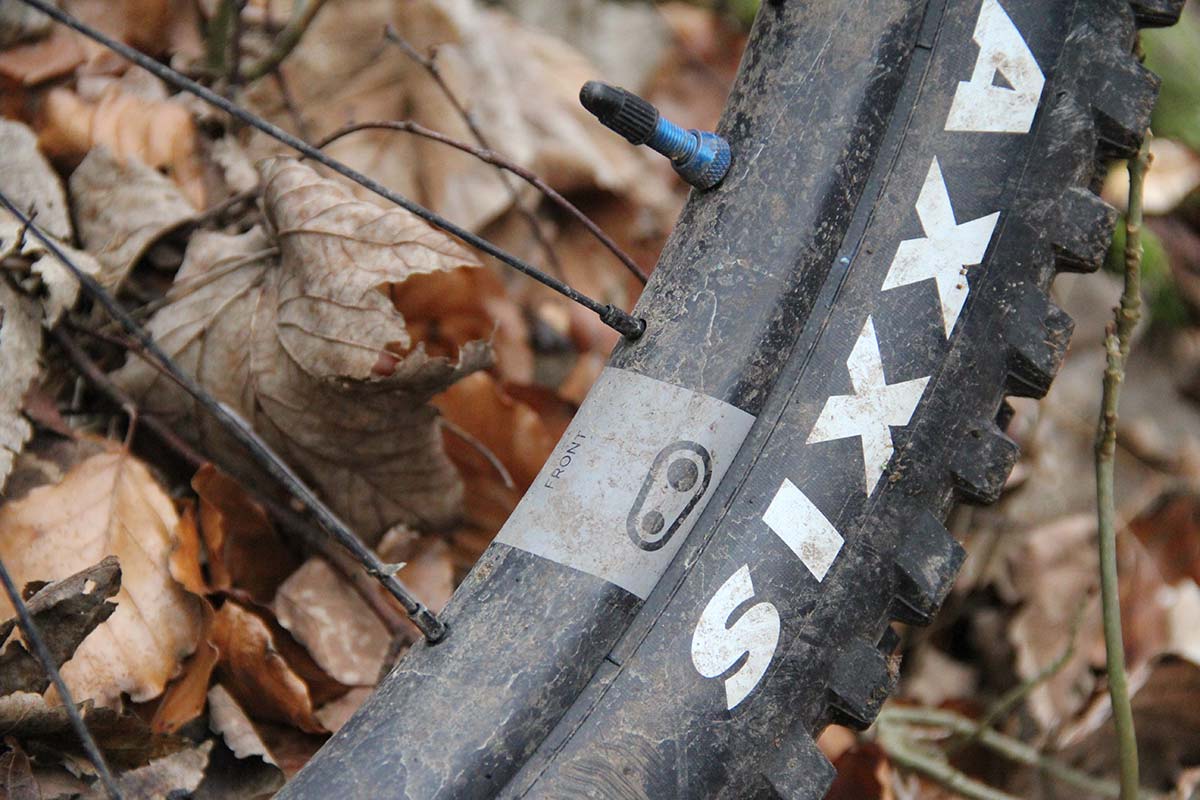
The other thing to think about with a spoke is this: imagine a spring, because essentially that is what a spoke is. People use stiffer coil springs for a stiffer ride and vice versa.
A light spoke, less than 15 gauge/1.8 mm will have greater elongation properties, so it stretches more compared to a really heavy duty 13 gauge/2.3 mm spoke. So if you are chasing stiffness for a wheel, a higher spoke count (more spokes) and heavier gauge spokes will head you in the right direction.
DT Swiss: Until the early 90s there were just plain gauge spokes available for bicycles. Typical diameters were 2.0 mm or 1.8 mm. The larger the diameter, the stiffer the wheel and it also improved the reliability.
But, a larger diameter means a heavier spoke. The invention of butted spokes changed this: these combine stiffness and reliability with almost no weight penalty. At the same time, a butted spoke will better resist alternating stresses while the wheel is in use.
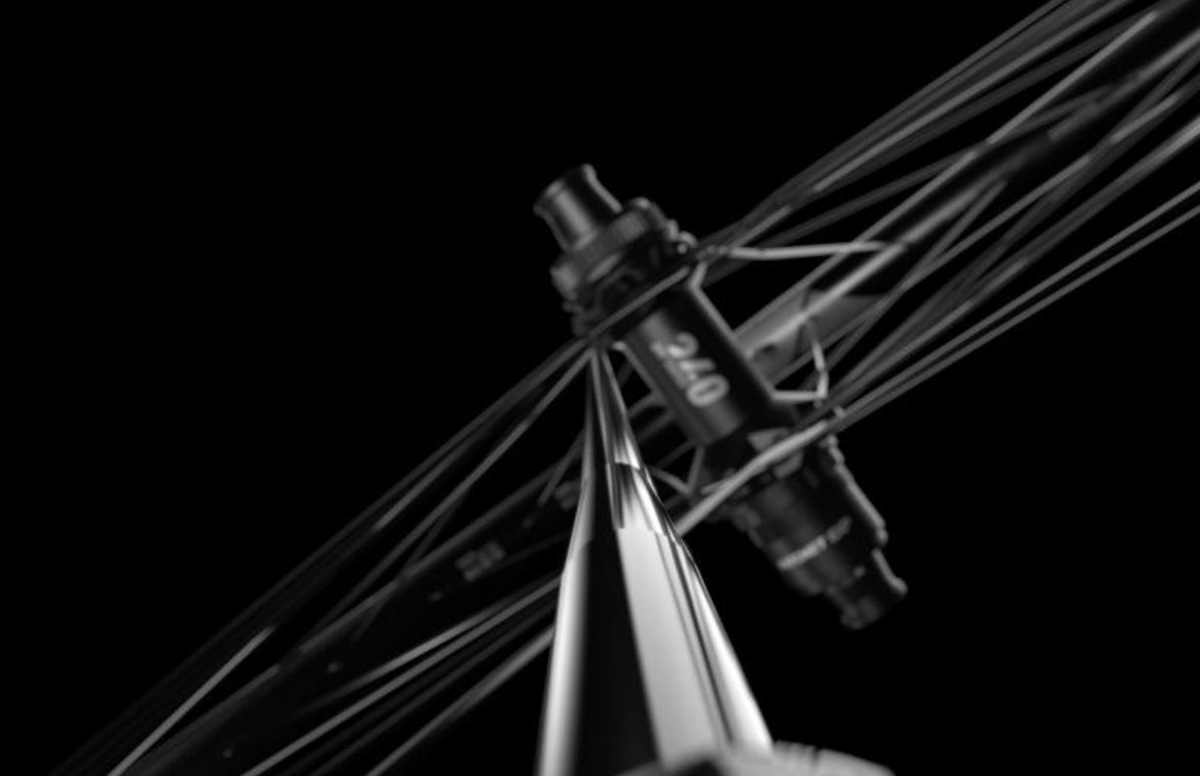
At least, this is true if the production process of the butted spokes is based on cold forging the material to make it thinner. From the technical side a butted spoke is every time the better choice for a wheel. As the production costs are higher the only reason to use plain gauge spokes is to save money.
Vittoria: A butted spoke actually allows for some elasticity, which in turn, reduces broken spokes. A non-butted spoke is more stiff, but can lead to damage as it is less resilient.
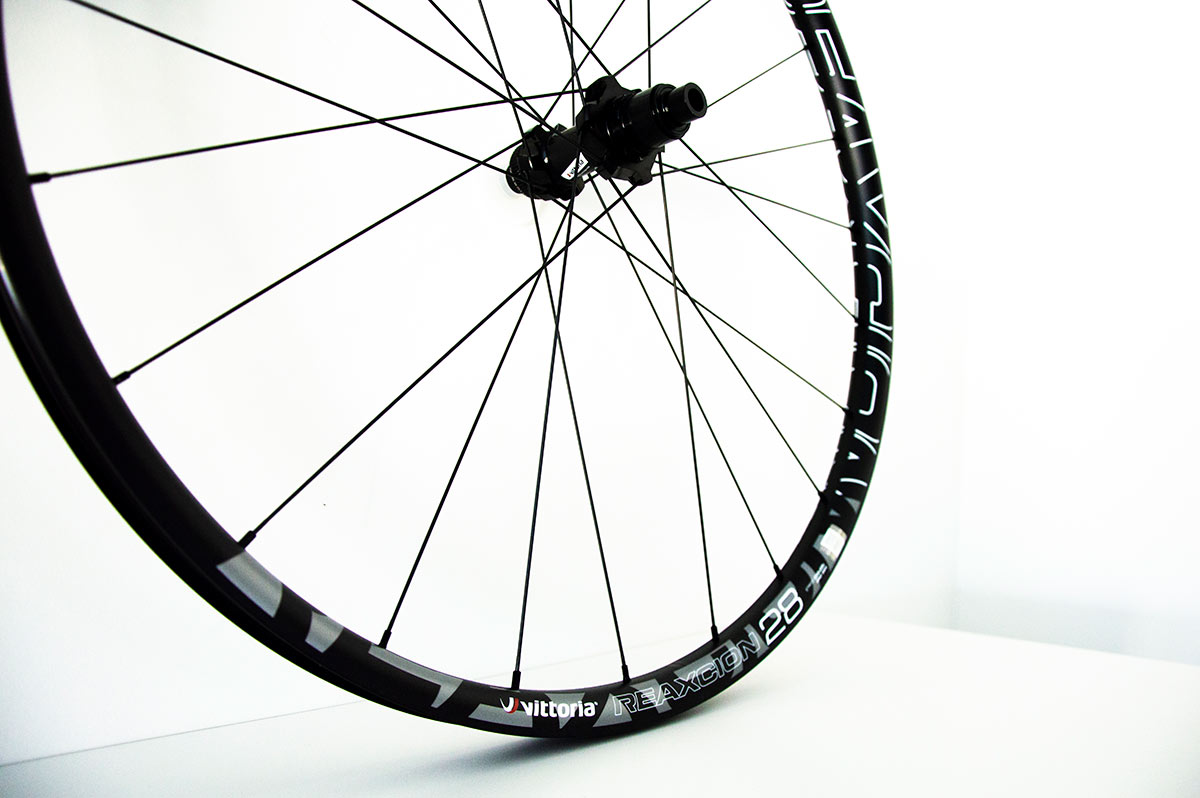
What type of rim is most likely to “ding”? An asymmetric rim or a symmetrical rim?
HUNT: The only reason some rims have an asymmetrical profile is to provide a better balancing of spoke tensions between the right and left side of the wheel, improving the bracing angles of a dished wheel.
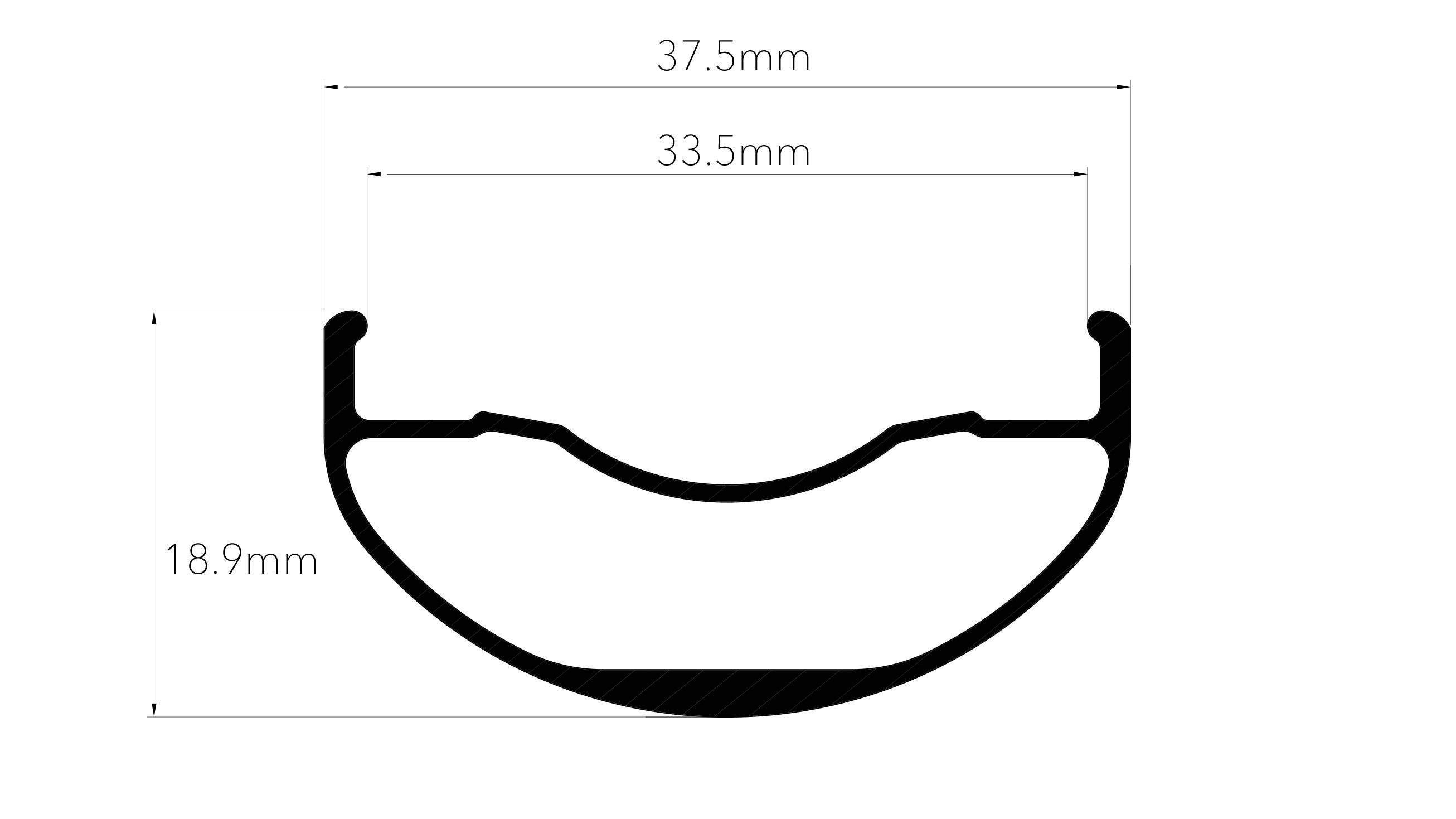
From our experience of designing and impact testing rims, to achieve the same strength benchmark you have to make an asymmetrical rim approximately 20-30 grams heavier.
So, if you have two rims of the same material and weight, the asymmetric rim will likely be slightly weaker in at least some characteristics. However, ‘dinging’ a rim is a very specific measure of strength and is heavily dependent on the material used and rim design itself.
Crankbrothers: This really comes down to the design and how it was engineered. If an asymmetric aluminum rim is designed well it should have similar resistance to dents on both sides of the rim wall.
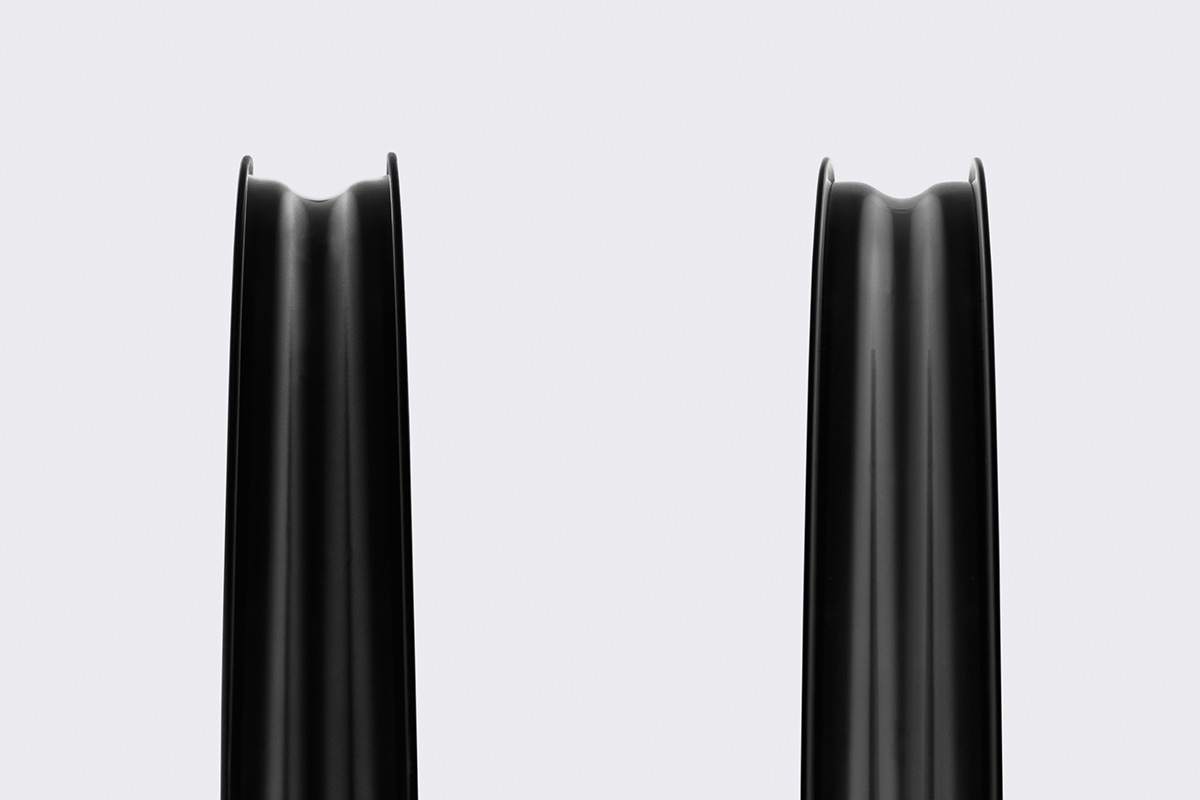
That being said, it is harder to achieve from an engineering perspective. Another factor to consider is this: the industry is always chasing reduced weights for rims which often means asymmetric profiles are not balanced in strength characteristics.
DT Swiss: This is a question which is not that easy to answer. It is not just about symmetrical versus asymmetrical. You need to consider construction of the rim itself as well as the width of the rim. These factors will have a high impact on what could be the better choice.
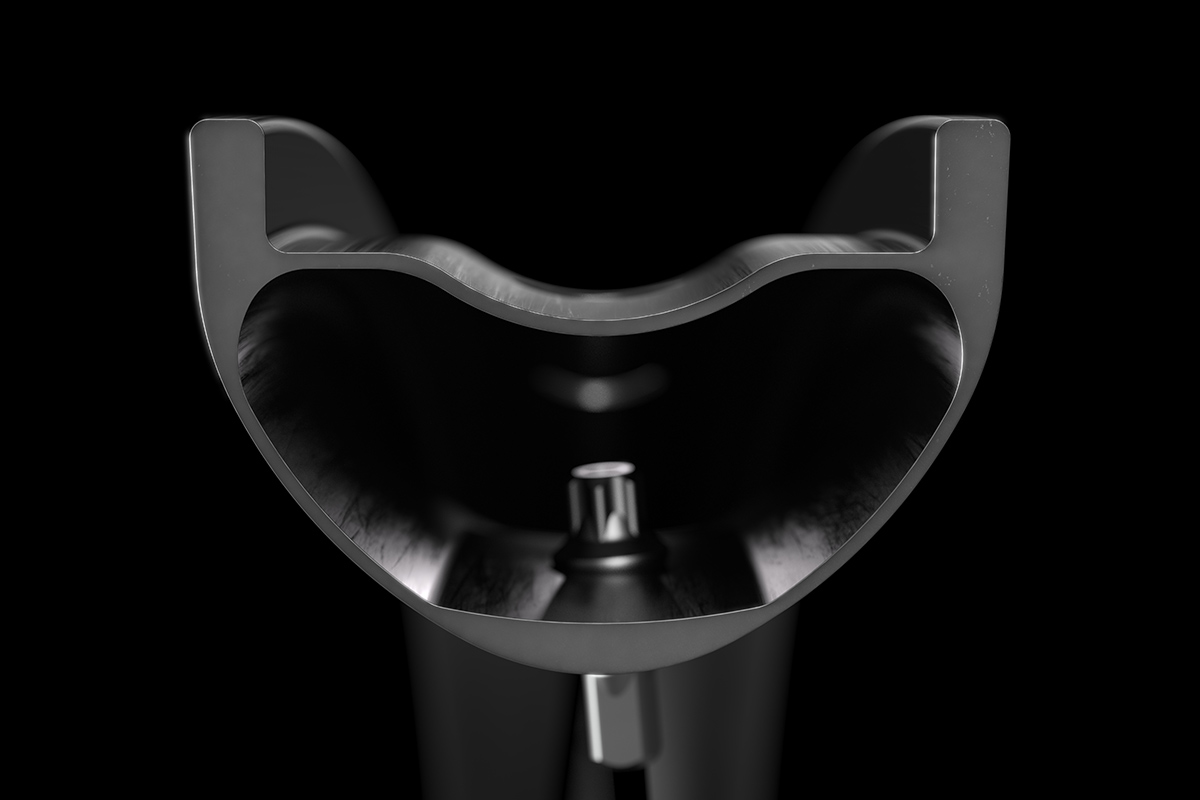
Let’s consider narrow rims like road rims or classic cross-country rims. For an inner width of up to 20 mm, it could make sense to use an asymmetrical rim to enhance the lateral stiffness of the wheel and keep the stress of the rim lower.
Vittoria: To me, a ding means a dent, so this one is a tie. Rim symmetry doesn’t really affect (or prevent) dents, as dents occur as a result of a sharp impact in the rim bead area.
Rim beads are symmetrical, even on asymmetrical rims.
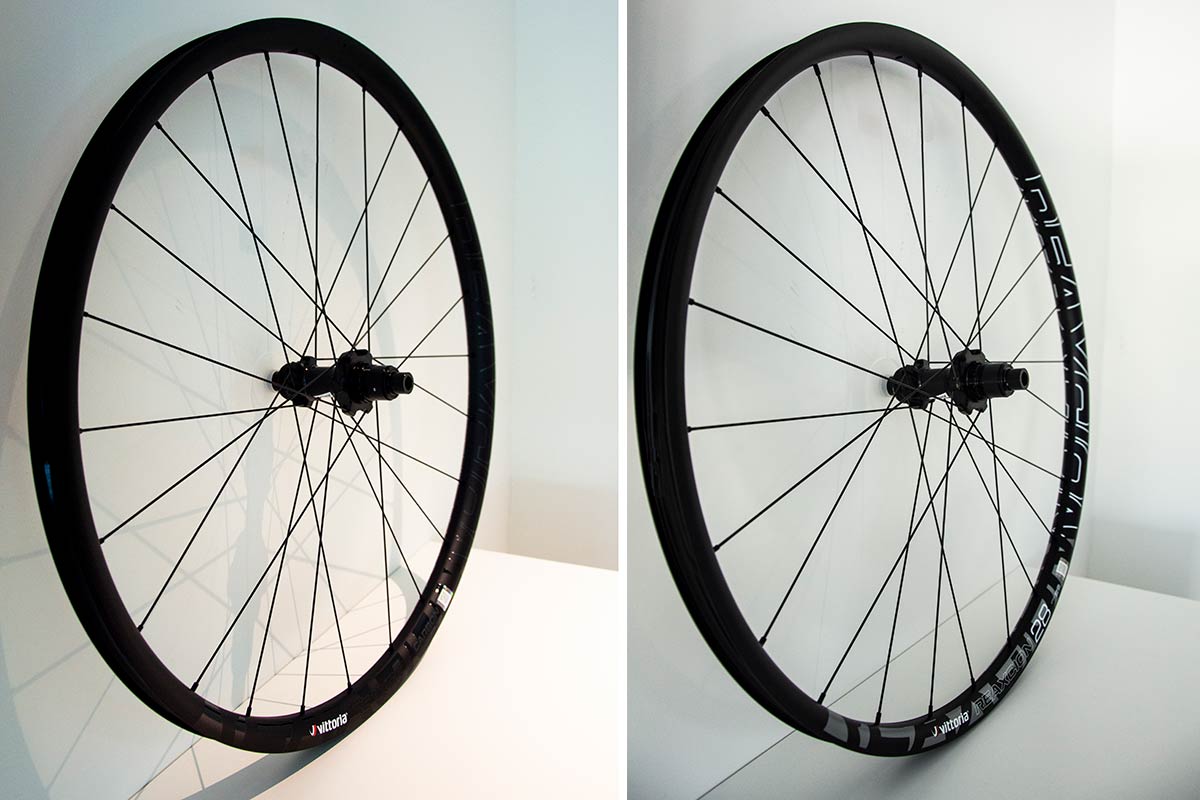
Now, if you are talking about the wheel coming out of true, then an asymmetrical rim/wheel will be stronger. The reason the rim is asymmetrical is so the spokes from opposing sides are closer in length, creating a more even triangulation.
A non-asymmetrical rim would have a longer spoke on one side, which can lead to a weaker wheel when comparing impacts from one side versus the other.
Stan’s: Both of these designs are equally likely to “ding” or dent. The only thing that changes on an asymmetric design vs a symmetric one is where the center-line of the rim is, allowing more balanced spoke tensions. Either design is not more or less likely to be dented while riding.
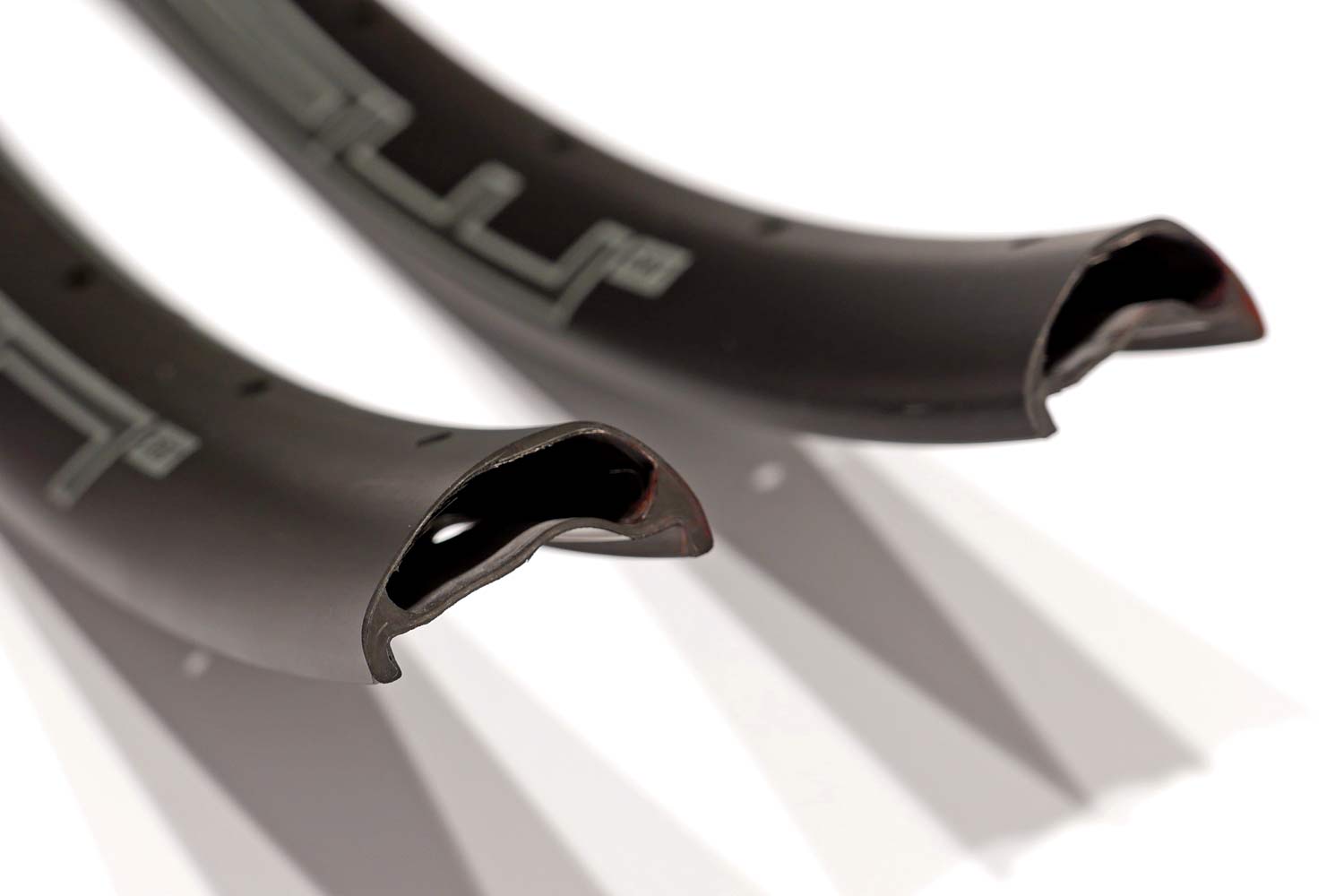
Are rear mountain bike wheels stronger on the drive side or non-drive side or is there no difference at all? I’m just wondering whether the different dish of the spokes makes a difference. I’ve noticed that when my spokes start to become loose, it doesn’t happen equally on both sides.
HUNT: Almost all rear wheels, but also front disc-brake wheels, have less spoke tension on the non-drive side due to the hub offset. These lower tension spokes are more likely to come loose first over time.
Moreover, the drive side of a rear wheel usually has a lower bracing angle. Combined with the higher spoke tension and pedaling force, this makes it slightly weaker, with the spokes on the drive side more likely to break.

As mentioned before, an asymmetrical rim profile would reduce this issue by improving the bracing angles, as the spoke tension between the two sides of the wheel are closer to being equal.
Crankbrothers: It’s quite a complex question as there are so many variables. Looking at the basics, a dished wheel is not as strong or as durable as a balanced wheel of the same hub flange spacing using a symmetrical rim.
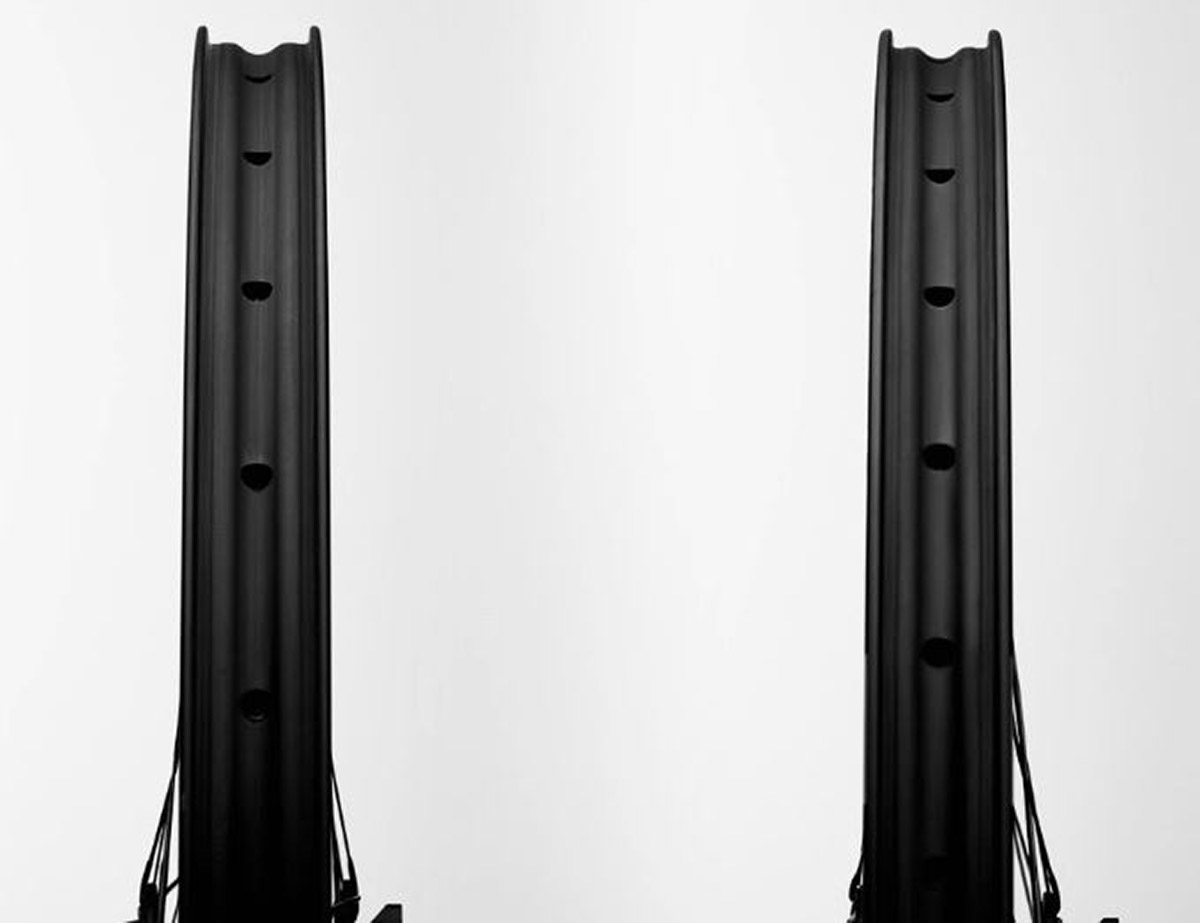
A balanced wheel means the drive side and non-drive side spokes have equal bracing angles resulting in even spoke tensions. A dished wheel with an offset will not have even stiffness characteristics due to bracing angles and spoke tensions varying from each side.
Due to geometry restraints with the front and rear wheels, rotors and drive systems, most wheels have to be dished to give clearance and are engineered to meet fatigue standards, etc.
The other effect that is present is the loading and unloading of spoke tensions. These vary between drive side and non-drive side spokes in a dished wheel. So, when you notice your rear non-drive spokes loosening earlier, this is a direct effect of them being under lower initial tension.
This is why most manufacturers use a liquid thread lock or mechanical lock in the nipple to reduce the chances of the non-drive spokes loosening.
DT Swiss: Most rear wheels do not have equal spoke tension on each side. Usually, the drive side has a higher spoke tension. As a result, the lateral stiffness will be higher on this side.

With changes like Boost (12 mm x 148 mm) or even the old Downhill standard (12 mm x 150 mm) you can try to balance this out.
Vittoria: Basically, it comes down to the angle of the spokes when looking from the rear of the bike. Notice how the drive side is at a steep angle, but the non-drive side is at a less steep angle? If both sides had the steeper angle (of the drive side spokes), the wheel would not be as laterally stiff, which would lead to breakage.
Stan’s: The wheels aren’t stronger or weaker to one side, however, the spoke tension is generally higher on the drive-side of a rear wheel. Different dish, or having an asymmetric rim design will allow those spoke tensions to be more even from left to right. Make sure you check your spoke tension after the first couple of rides. Spokes can settle a bit on a brand new wheel.
Why do wheel manufacturers obsess over building ultra-stiff wheels? I would have thought a bit of compliance helps with traction. Is there a balance to be struck?
HUNT: Stiffness is one of the main targets to achieve when designing wheels meant for climbing or sprinting efficiency. For wheels intended for rougher terrain, a bit of compliance will help avoid riders pin-balling down technical sections and provide more grip.
However, too compliant and the wheel could feel flexi or vague, plus higher impact loads may deform the rim.

This is why a combination of rim profile, material choice, spoke number and butting has to be taken into account when designing a wheel. The purpose of the wheel is always key when developing a new wheelset. Hence the need for developing front and rear specific wheels to suit their very different roles.
The front needs compliance to help track the ground and provide grip, whilst the rear will usually bear the brunt of impacts, so a stronger and stiffer wheel is more desirable.
Crankbrothers: I believe there is a balance to be struck with wheel stiffness, and there is also rider preference to take into account. Too stiff and the ride becomes harsh and your wheel loses its ability to move with the trail and maintain traction.
On the flip-side, not stiff enough and the wheel will become vague and not able to support lateral and radial loads correctly. The easiest comparison is your tires: too hard and it skates and struggles for traction, too soft and it wallows on the trail and doesn’t support loads.
In 2014, in contrast to the many ‘stiff’ carbon wheels on the market, I developed the first solid single wall carbon MTB rim. This compliant wheel offered greater deflection, more dampening and reduced trail chatter, resulting in better traction.
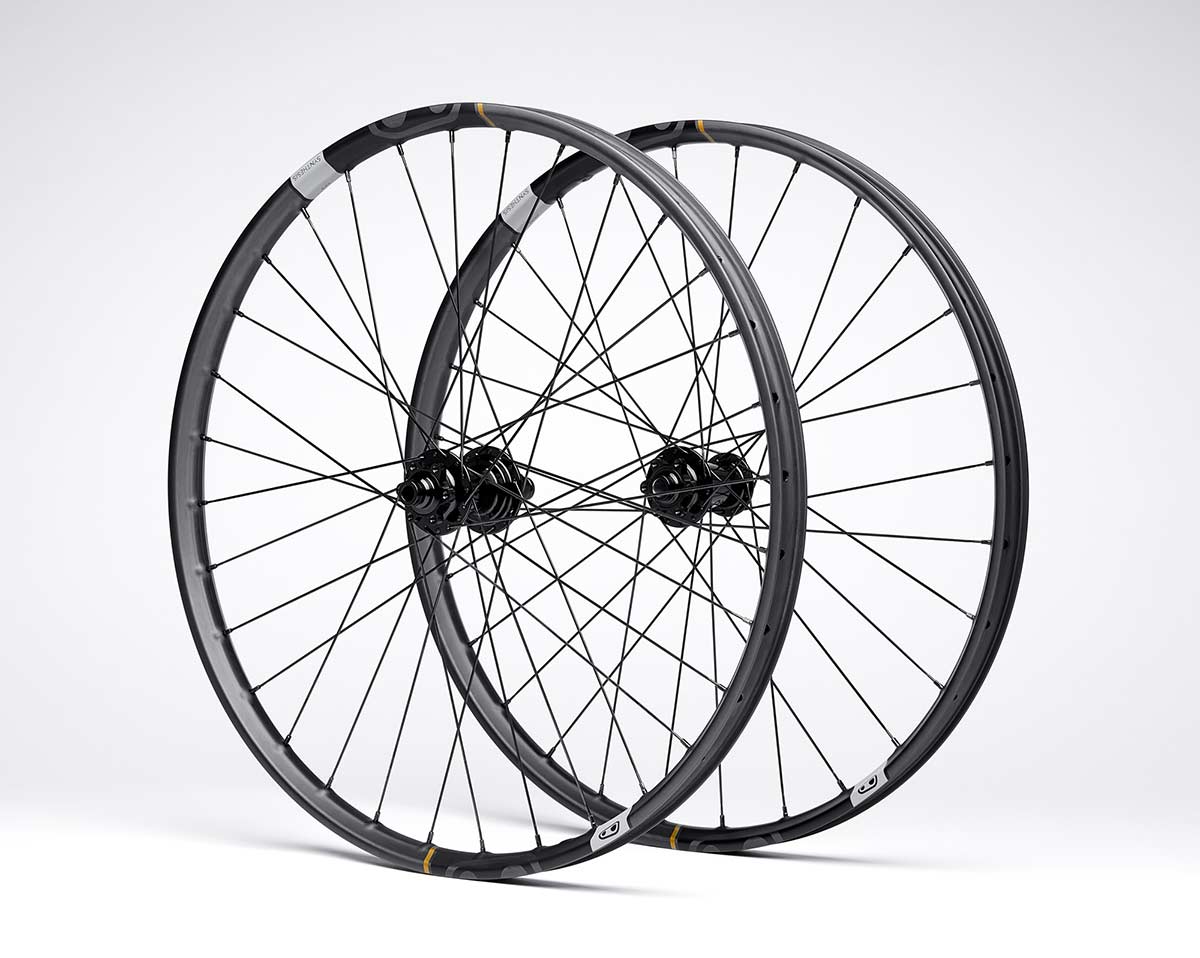
The evolution of this rim is the Crankbrothers Synthesis range with a super shallow compliant rim but adding another element, treating front and rear wheel stiffness independently.
The Synthesis wheel system combines a compliant front wheel for improved handling and control in turns with a stiff rear wheel for stability and tracking at speed.
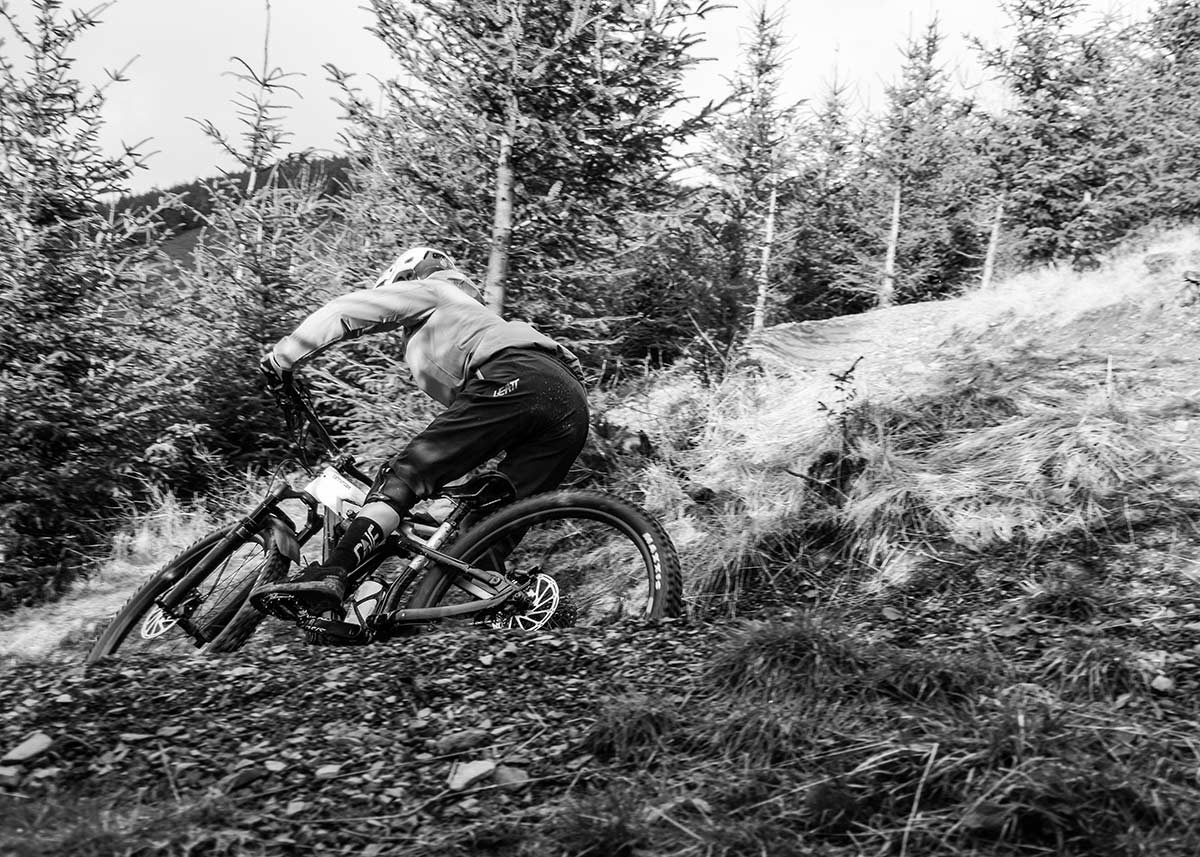
This is quite relevant to your original question about finding the balance of stiffness, as the front and rear wheel do different jobs on the trail so they should have different properties to meet those demands.
Jumping back to the example of tire pressures, most people also run lower front tyre pressures for traction and ride feel, then higher pressures in the rear to support peak loads. I feel this tuned approach and having specific front and rear wheels will evolve. Riders are seeing the advantages of it for performance and ride quality.
DT Swiss: I would like to say first of all that this is not a wheel builder thing. It’s more related to the perception of the customer: the stiffer the better.
But, as there are a lot of alternating stresses for all parts of a wheel (spokes, rims, hubs, nipples), it is necessary to avoid too much play in between the multiple connections in a wheel.
Therefore, you need to consider carefully the reactions of the different components before combining them into a wheelset. This is the essence of good wheel building. It requires a lot of experience to succeed.
Vittoria: Stiffness means predictability, which means control.
In the early days of MTB suspension forks, there was much talk about lateral stiffness. A few people wondered if a bit of lateral flex might help, but that was quickly disproved as control was impacted.
Remember, wheels are unsuspended, so they must be stiff to provide a consistent feel. Wheels also have the double duty of putting power to the ground, so the transfer of power is more efficient if the stiffness of the wheel is greater.
How come some wheel manufacturers offer their alloy and carbon wheelsets with the exact same wall thickness? I would have thought the different materials had a different strength to weigh ratio.
HUNT: I cannot talk on behalf of other wheel manufactures, but we specifically study the thickness distribution of our rims. Not only do our wall thicknesses vary from our alloy to carbon rims, but also according to the disciplines and intention.
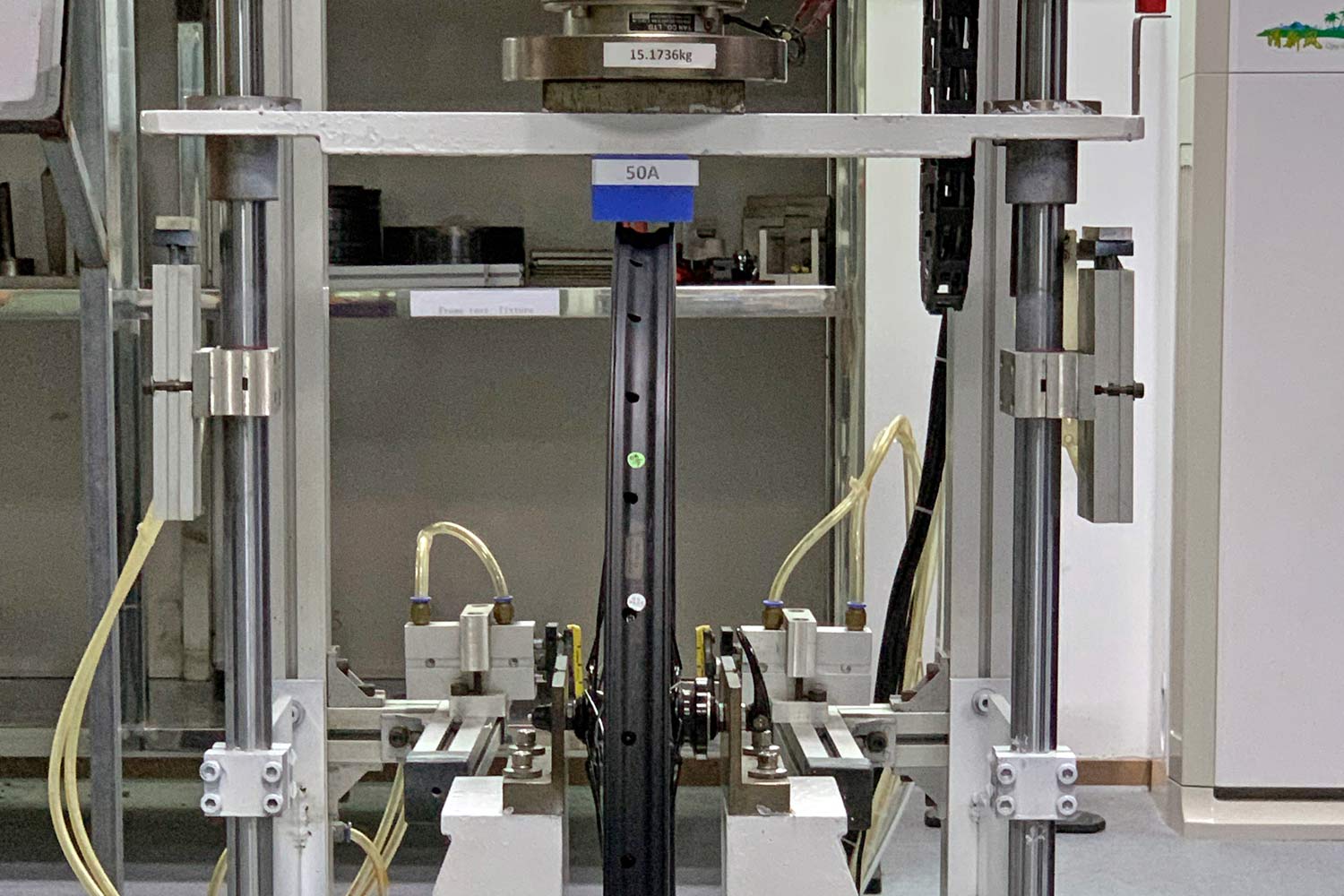
When designing wheels, we develop both alloy and carbon independently to make the most of each material. They both have pros and cons and our engineers work hard to design profiles optimised for material and usage.
However, it isn’t as simple as carbon vs aluminium, within the material families themselves is a vast array of options which is why two rims similar in appearance or shape could ride very differently.
Crankbrothers: From a design standpoint they need to be managed differently as they have different properties. Our rims have different thicknesses, profiles and geometries between alloy and carbon.
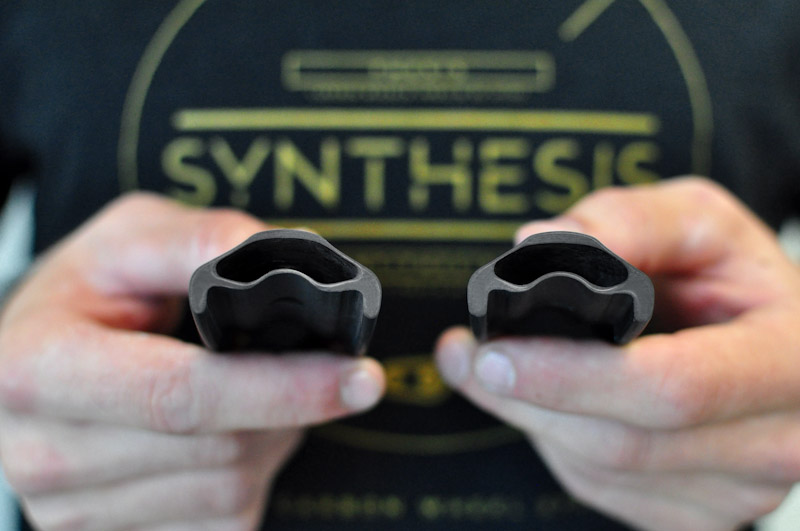
So, when I’m designing a rim I need to take the material properties into account to make them work to their potential. Carbon fiber also has the advantage of intricate laminate design and optimization; this means you can change the characteristics of the rim’s profile in different areas depending on your fiber type and ply orientation.
For impact areas you will focus on managing crack propagation, whereas in the spoke bed you’ll enhance stiffness and load properties. Aluminum, however, is isotropic, meaning it has the same properties in all directions, so the extrusion profile heavily dictates the performance and properties of the rim.
DT Swiss: Using the same material thickness for aluminum and carbon rims would not work, in my opinion. Or, at least it would not make sense to make the aluminum walls as big as the carbon ones without a huge weight penalty.
In our case, we develop all our rims for the specific needs for the field of application combined with the latest materials.
Vittoria: Great question. You are right, those materials are quite different, so it may be coincidence, or it may have to do with their tooling. With Carbon, it could also have to do with the lay-up process, which can be manipulated based on the goal of the product.
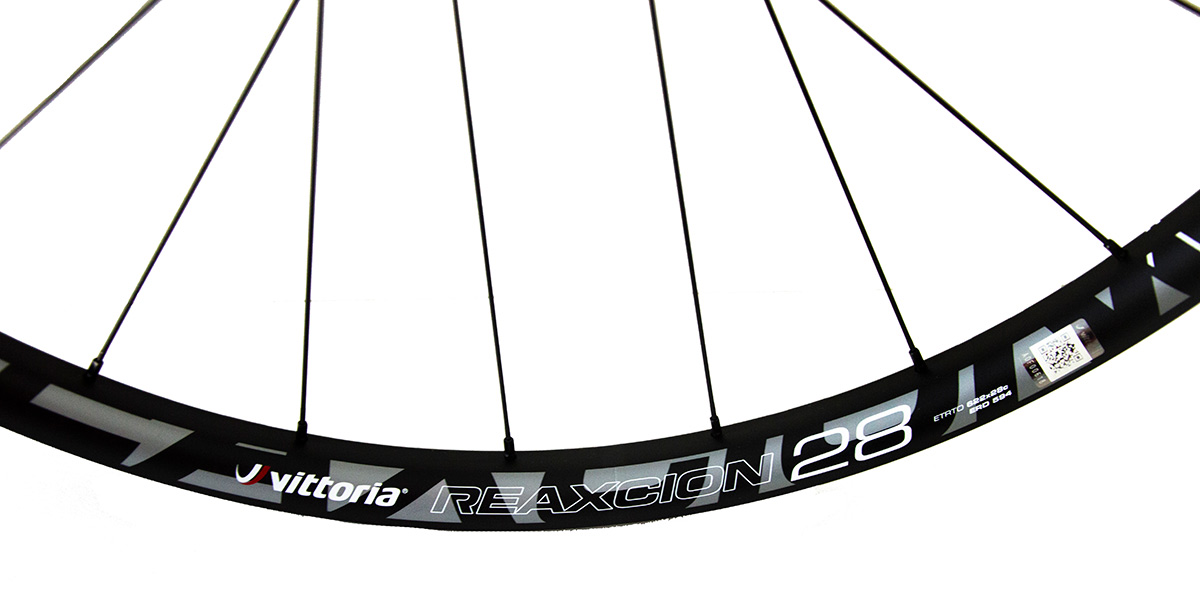
How does the depth of a rim change the profile of a tyre seated on it? What are the merits of a deep rim as compared to a shallow one?
HUNT: All other things being equal (internal width and bed profile), a taller sidewall would constrict the tyre sidewall for longer, resulting in a more mushroomed tyre profile. A shorter sidewall on the other hand creates a more rounded tyre profile giving a larger tyre volume, often considered closer to the ‘true’ tyre shape.
As hinted at earlier, there are number of dimensions within a rim profile that affect the tyre shape and it is a measured balance of these, based on the wheel’s intended use (along with consideration of the ETRTO standards), that drive the sidewall height.
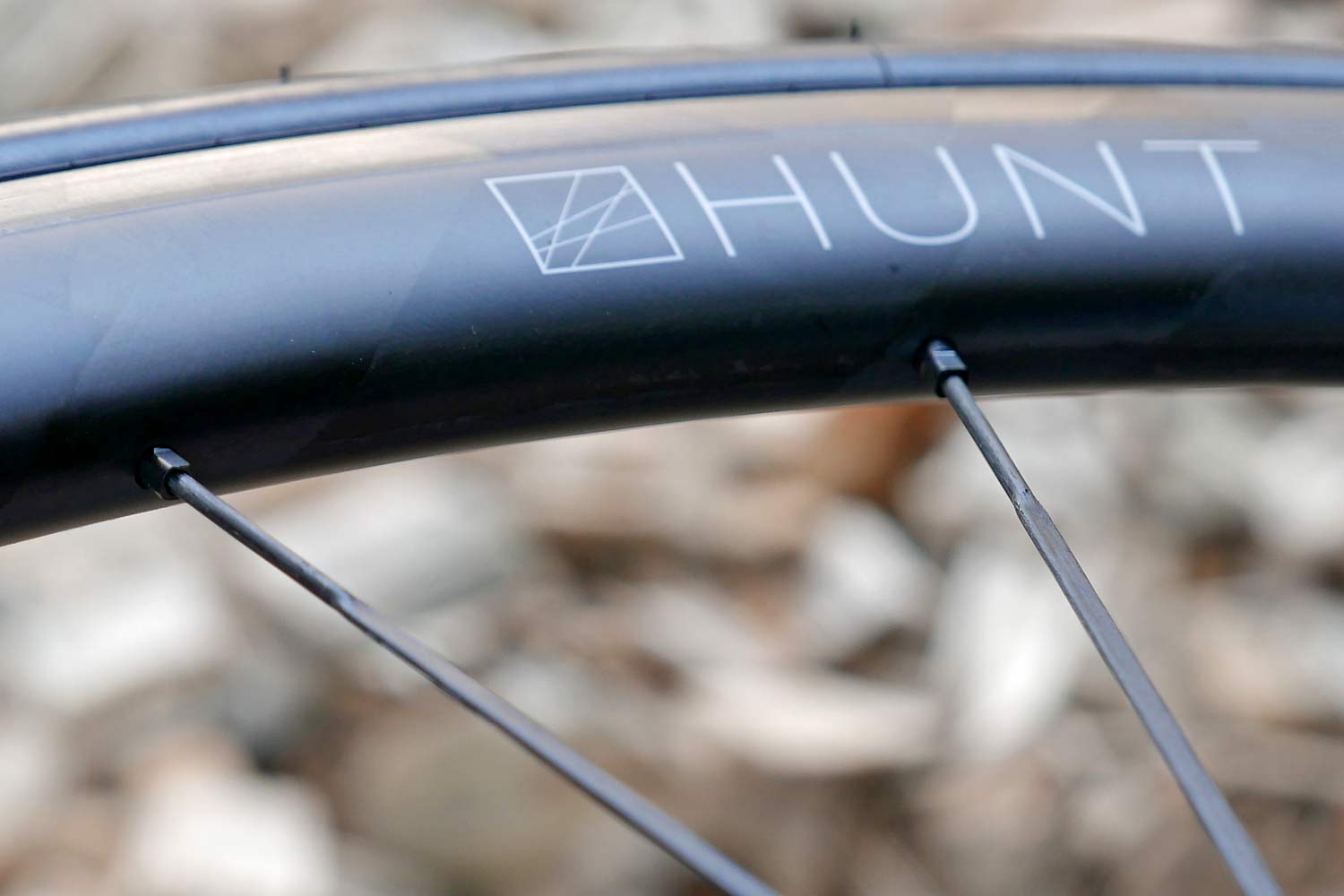
It’s worth noting as internal width increases, the resulting effect of sidewall height on tyre shape diminishes. Externally, the depth of a rim does not affect the tyre shape, however deeper rims are stiffer and more aero than shallower rims.
Crankbrothers: The total depth of the external profile of the rim should not affect tire fitment. The internal profile, however, of the rim channel and bead seat (bead seat is where the tire is located during use) will have a large effect on tire fitment and how secure it is.
There are a few industry standards that are used to reference the internal geometry such as ETRTO. Most manufacturers follow similar geometries to achieve a ‘tubeless ready’ system.
Some companies go outside the norm and this is when you can get issues with tire mounting, seating and sealing. Another factor that can affect tire fitment is inconsistent manufacturing tolerances, both from the tire and rim manufacturers side.
DT Swiss: Firstly, it’s important to note that with tubeless systems becoming more and more the standard on any bicycle, the sizing of tires has changed a lot. This means a modern tubeless tire will have its seat in the corner of the rim sidewalls and the rim bed.
To get the tire mounted the rim needs to have a section in the middle of the rim which is deeper than the rim bed on the sides. The sidewalls are therefore just to make sure the tire will not fall of the rim. The overall rim height, on the other hand, will have an impact on the stiffness of the rim. Usually, the bigger the overall profile the stiffer the rim will be.
Vittoria: Per ETRTO, the rim bead and tire bead will be designed to match. Once the tire is inflated, the beads find each other, so the depth of the rim won’t change the tire profile.
However, rim width will change the profile, as the wider the rim, the more square the tire becomes. The opposite is also true, where a more narrow rim will make the tire profile more round.
Stan’s: The depth of a rim will not change the profile of the tire. Rim width, bead seat, and sidewall height will all change the tire profile in subtle ways. Deeper rims do offer an aerodynamic advantage over shallower wheels, but that aero advantage sometimes comes at a weight penalty.
Thank you to Sam Meegan of Hunt Wheels, Mello Bouwmeester of Crankbrothers, Friso Lorscheider of DT Swiss, Ken Avery of Vittoria and Drew Esherick of Stans NoTubes for contributing to this week’s “Ask A Stupid Question” feature!
Got a question of your own? Click here to use the AASQ form to submit questions on any cycling-related topic of your choice, and we’ll get the experts to answer them for you!