Like so many great ideas, the BOA Fit System started off as a way for Gary Hammerslag to improve his hobby. Prior to moving to Steamboat Springs, CO in the mid-90s, Gary worked in the medical industry and revolutionized the angioplasty process with his patented devices that relied on thin metal wires. After selling his company, his new goal was to snowboard as much as possible.
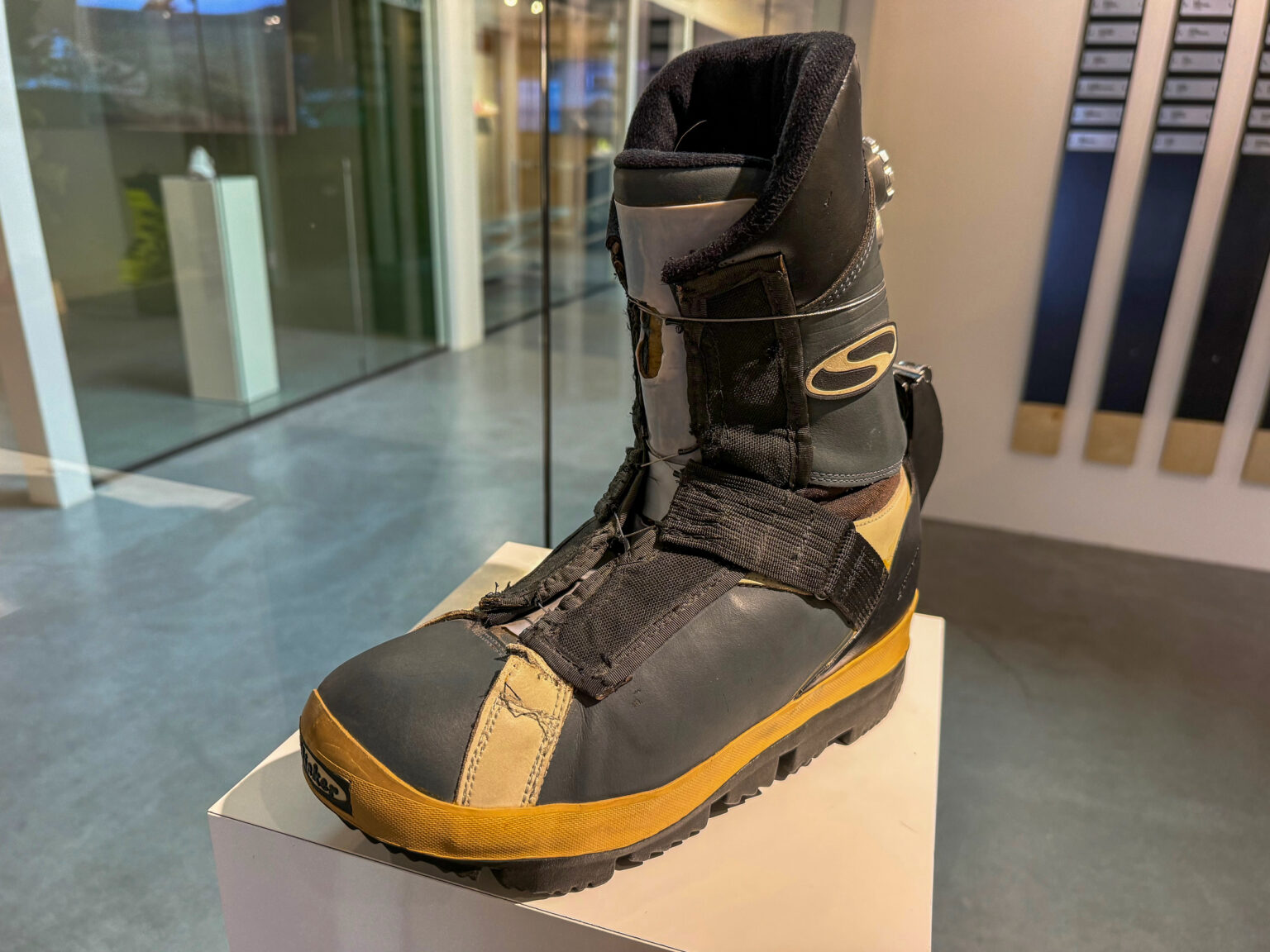
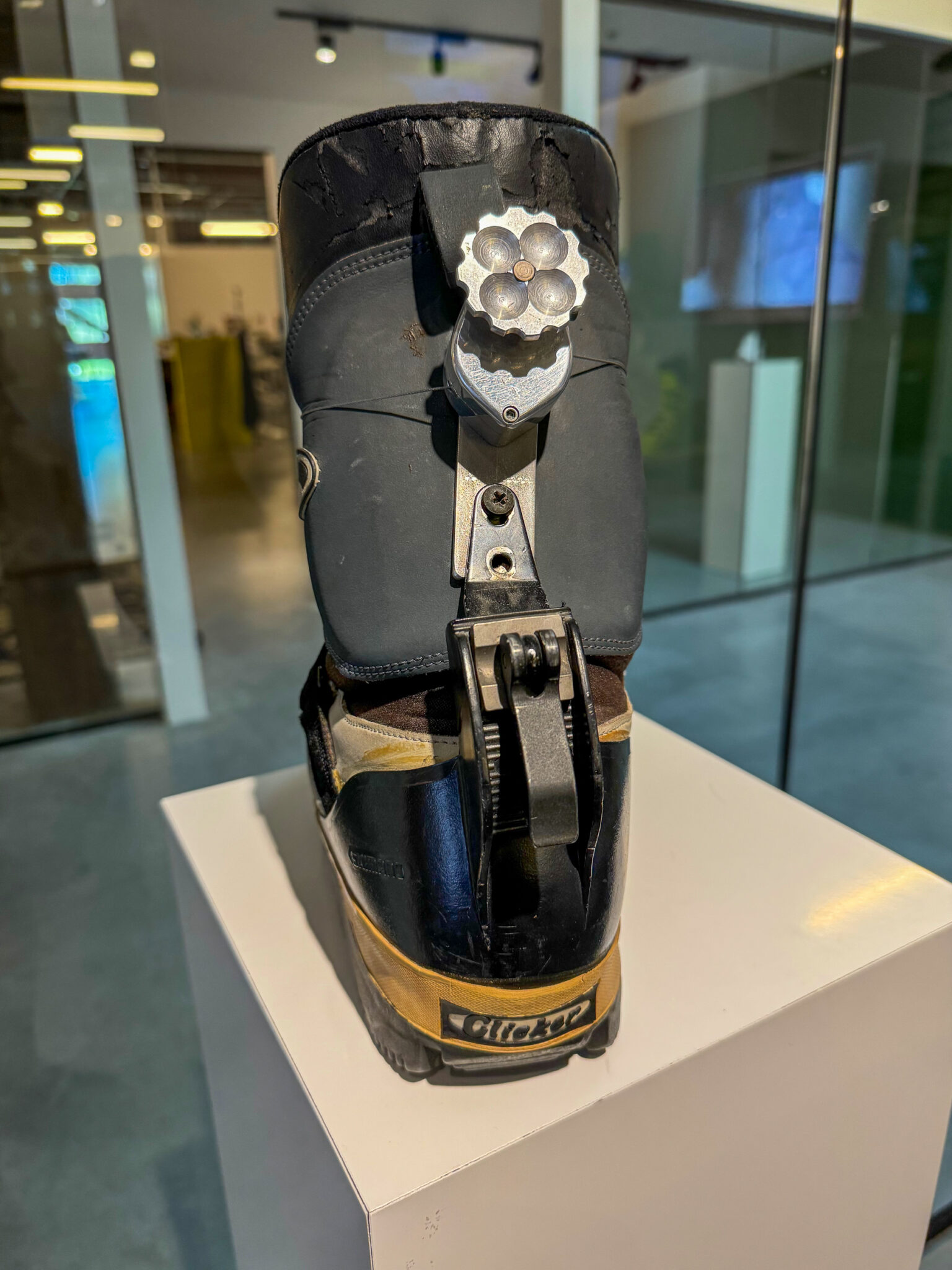
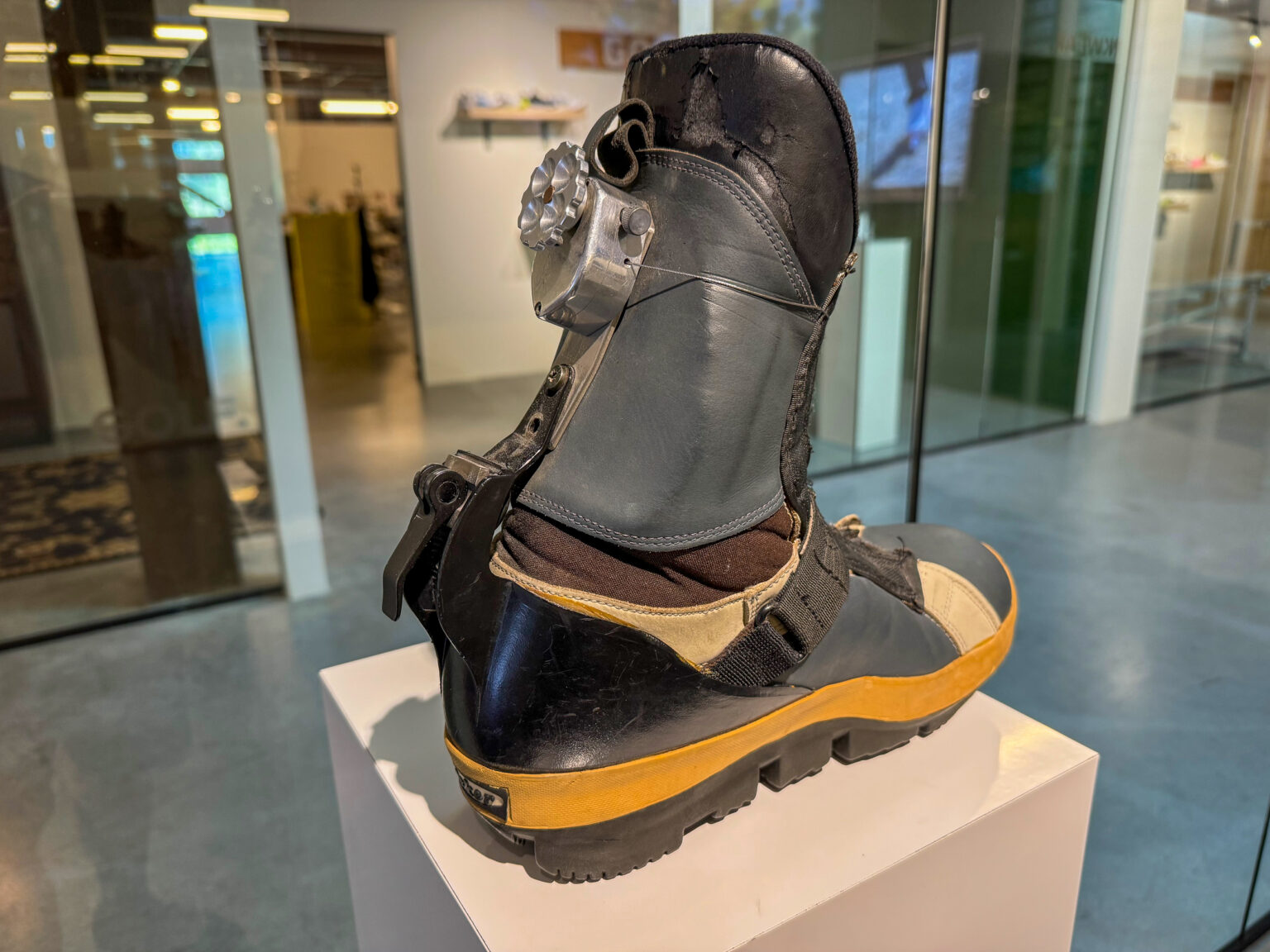
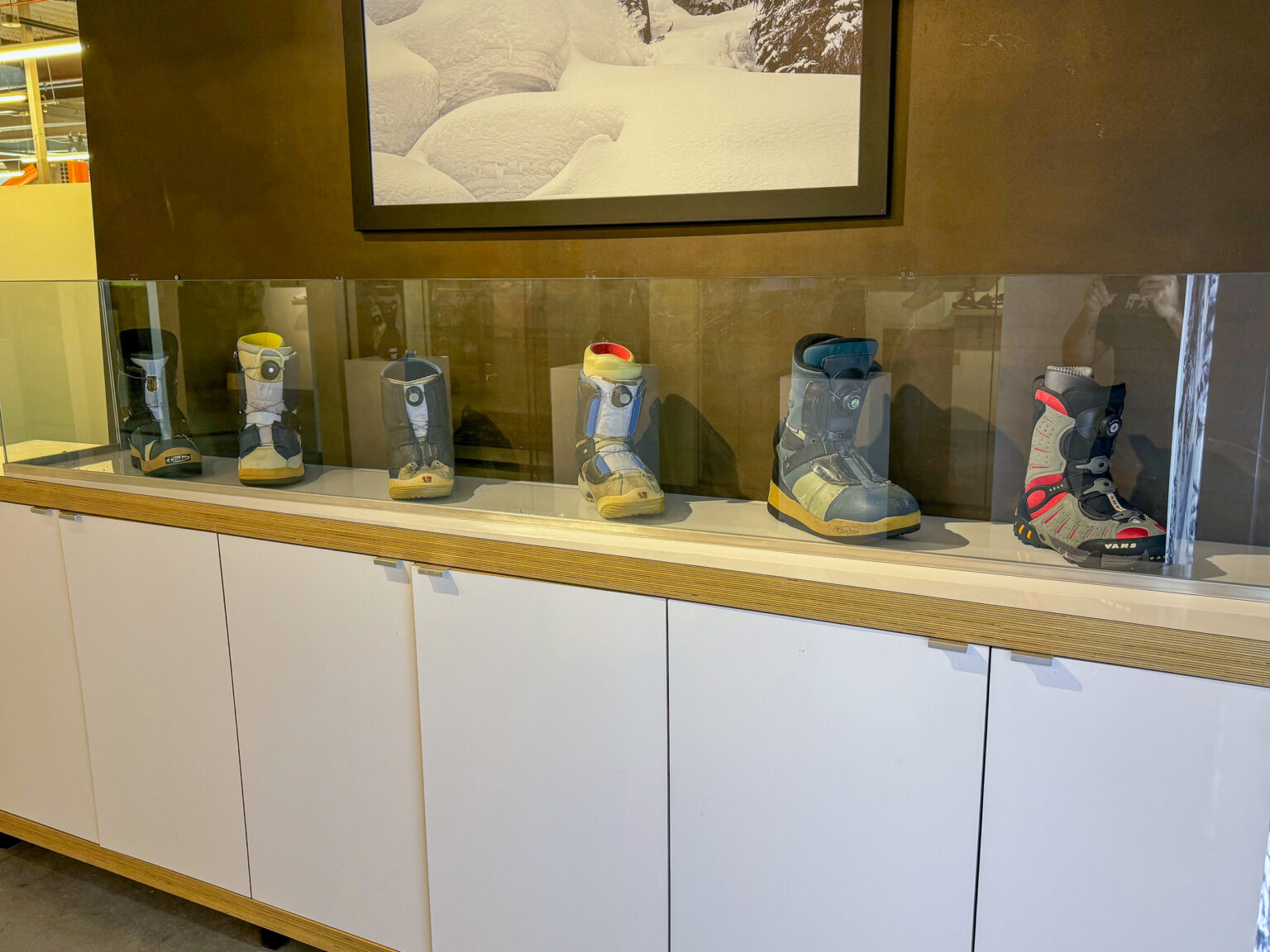
At the time, all snowboard boots relied on laces to tighten and Gary knew there had to be a better way. Drawing on his experience in the medical world, the first BOA prototype was born – a true boat anchor. Words can’t prepare you for how heavy the first prototype snowboard boot actually is. If you visit BOA in Denver, you can ask to feel it for yourself.
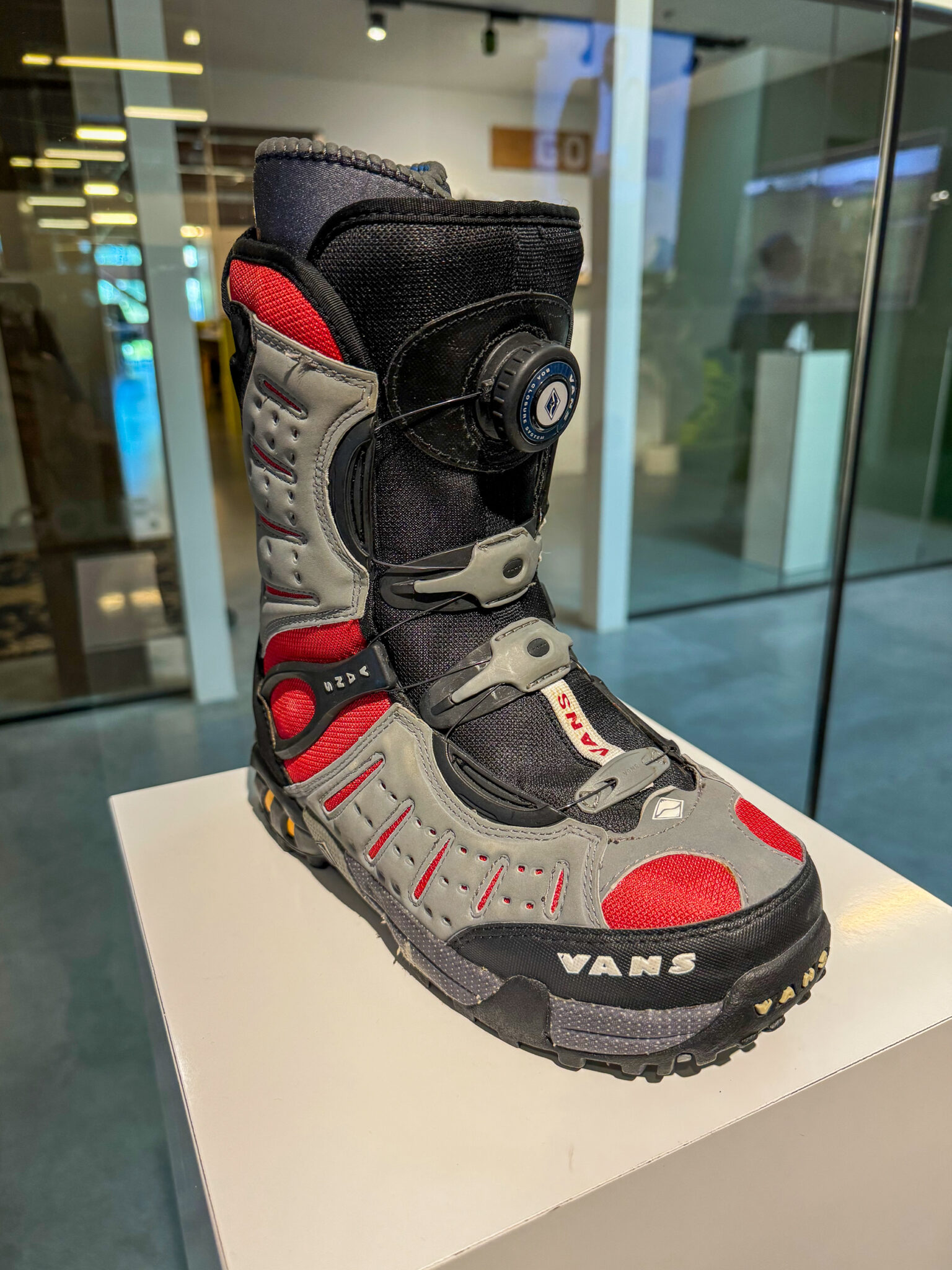
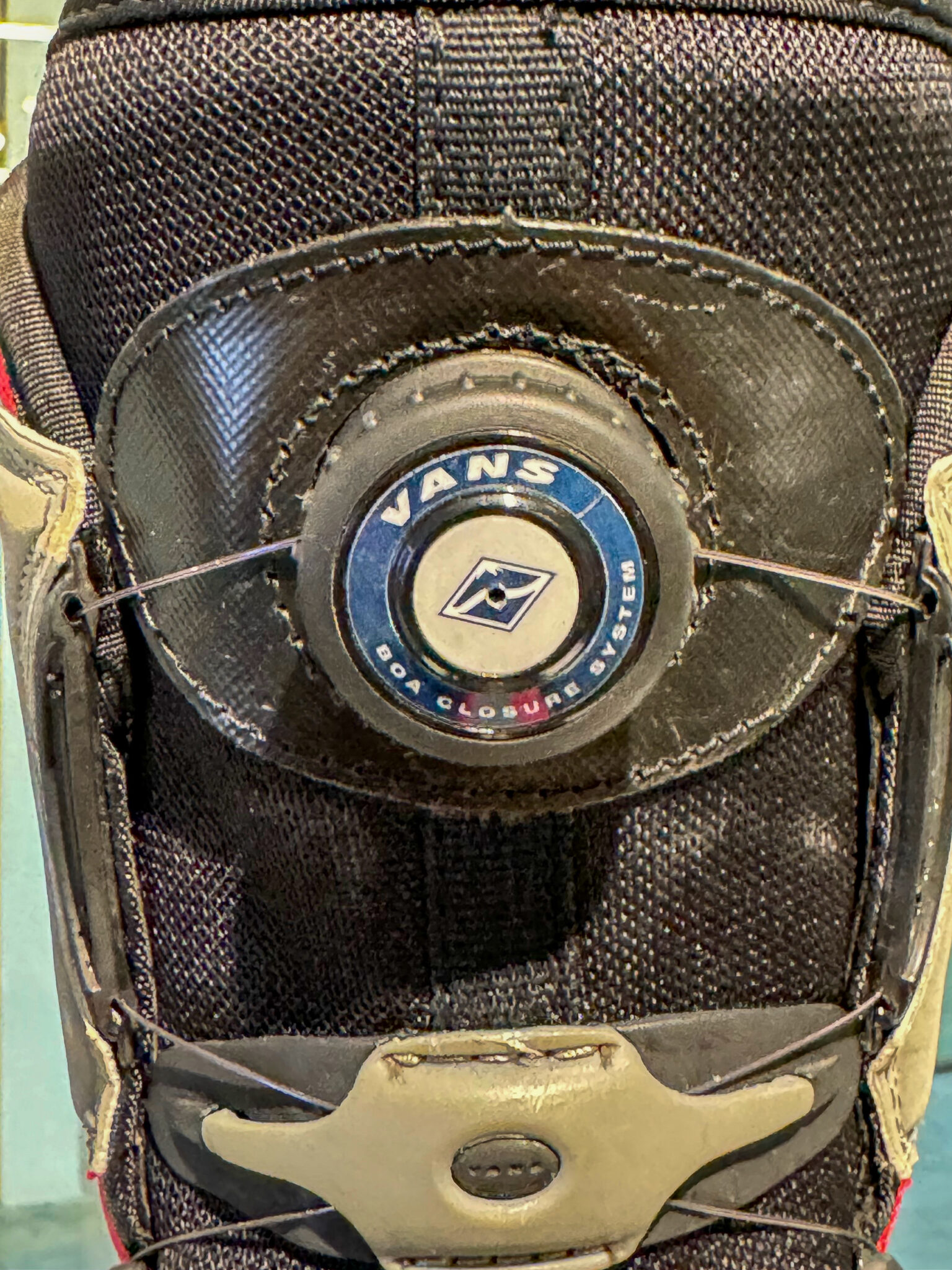
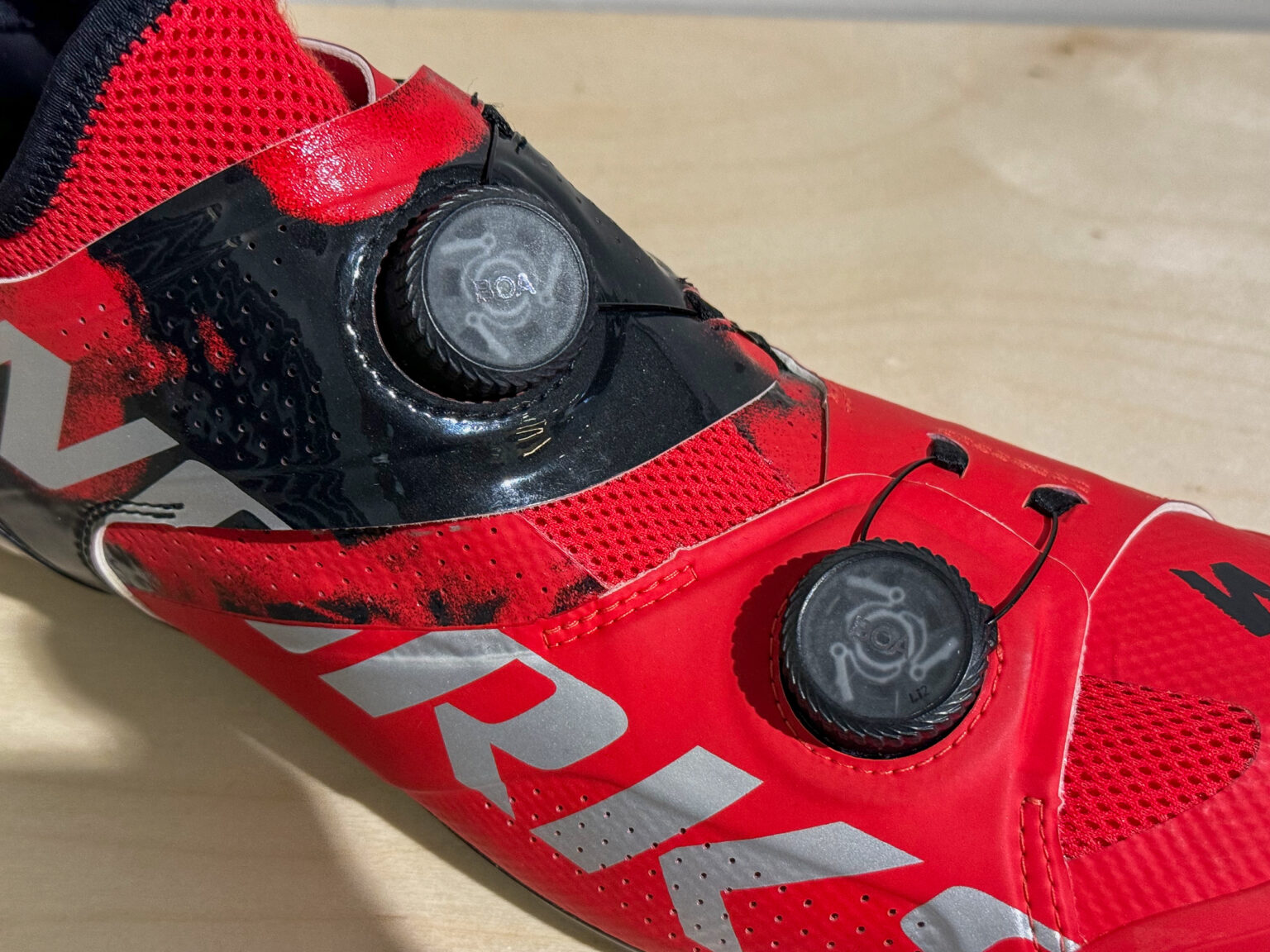
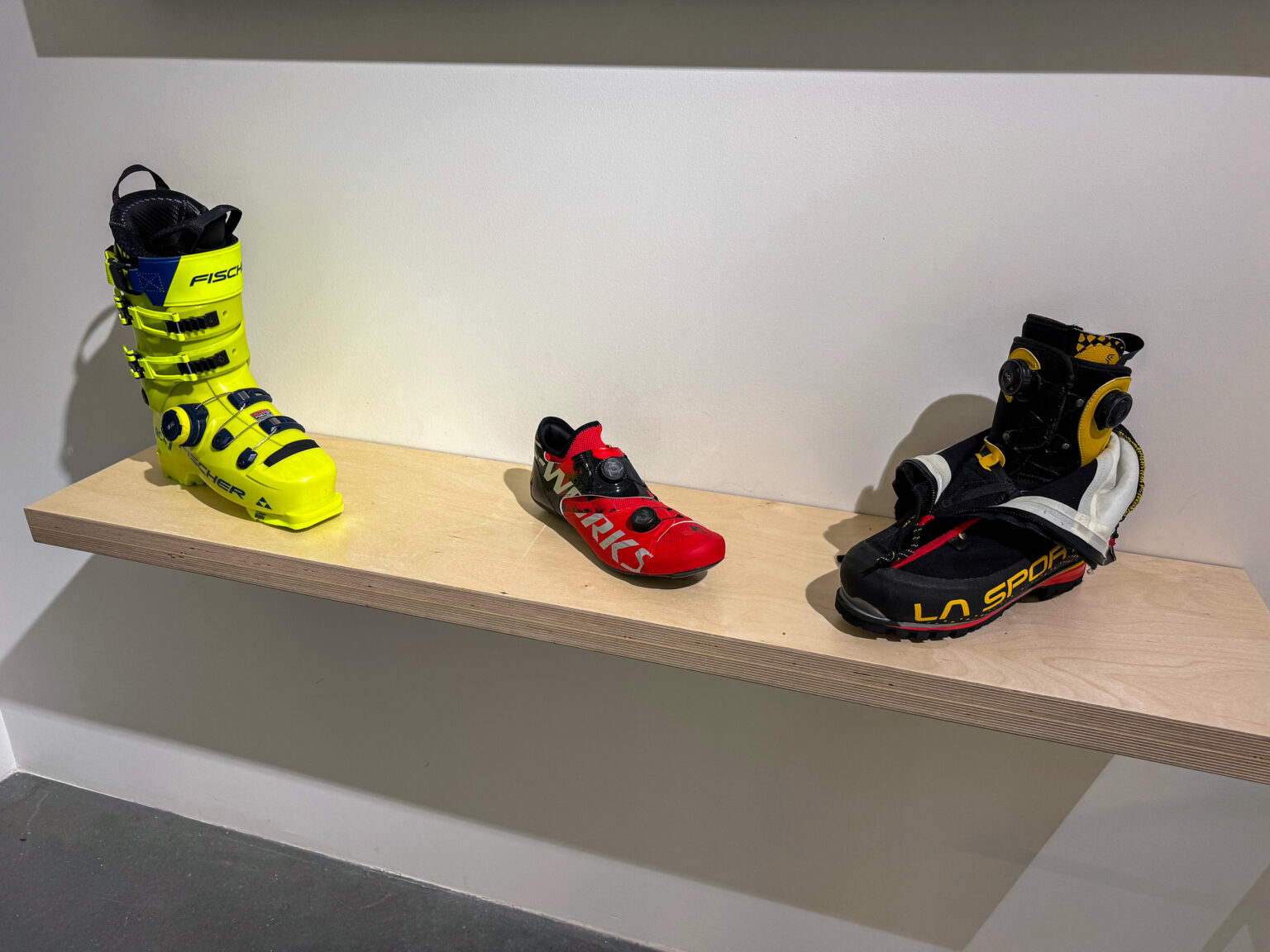
That first proof of concept quickly evolved into a much lighter and easy-to-adjust system that was first introduced in 2001 with BOA’s first two partners, K2 and Vans. After launching with snowboarding, BOA first moved into the world of cycling after partnering with Specialized in 2005.
Brand Partners and Categories
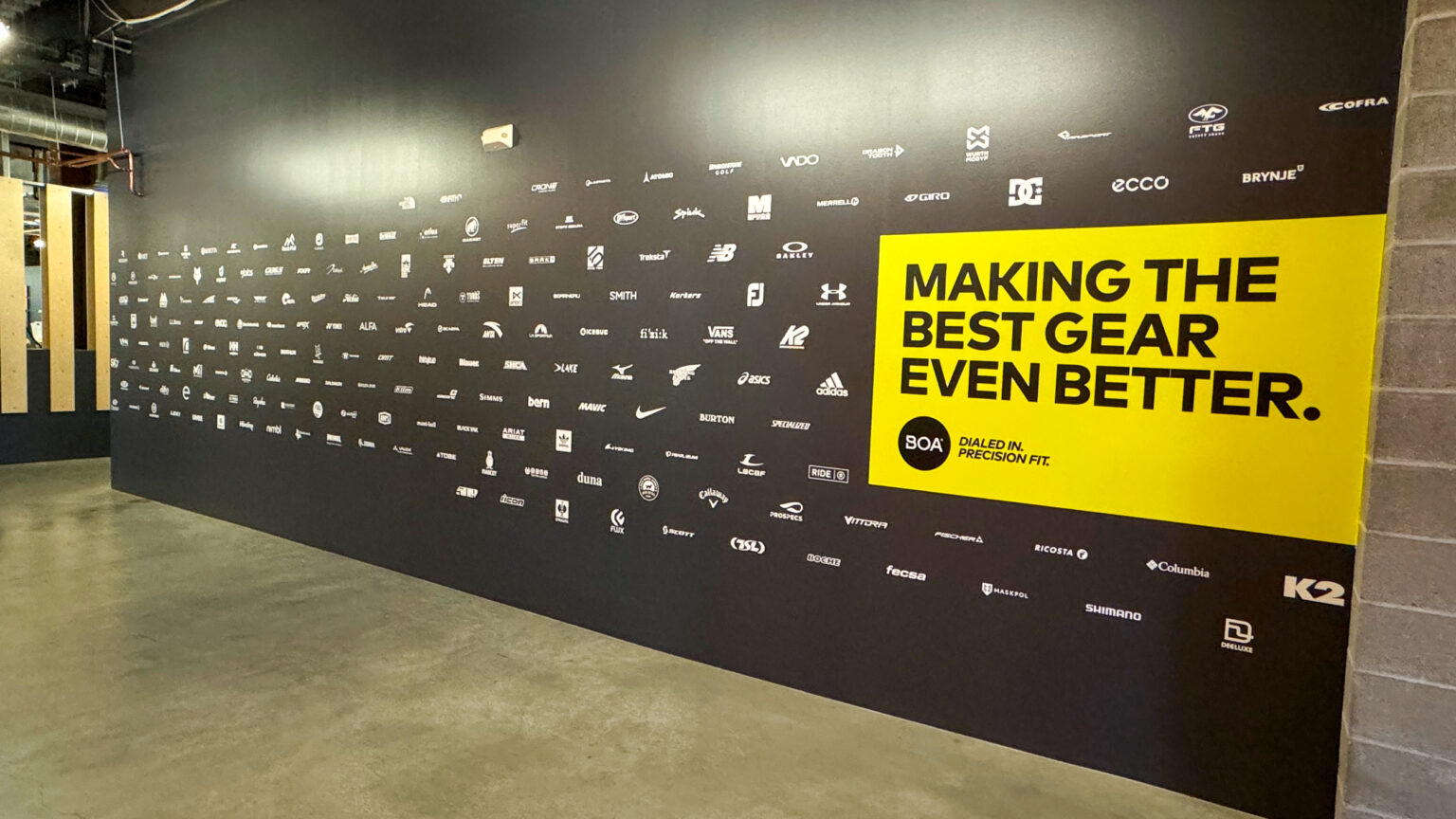
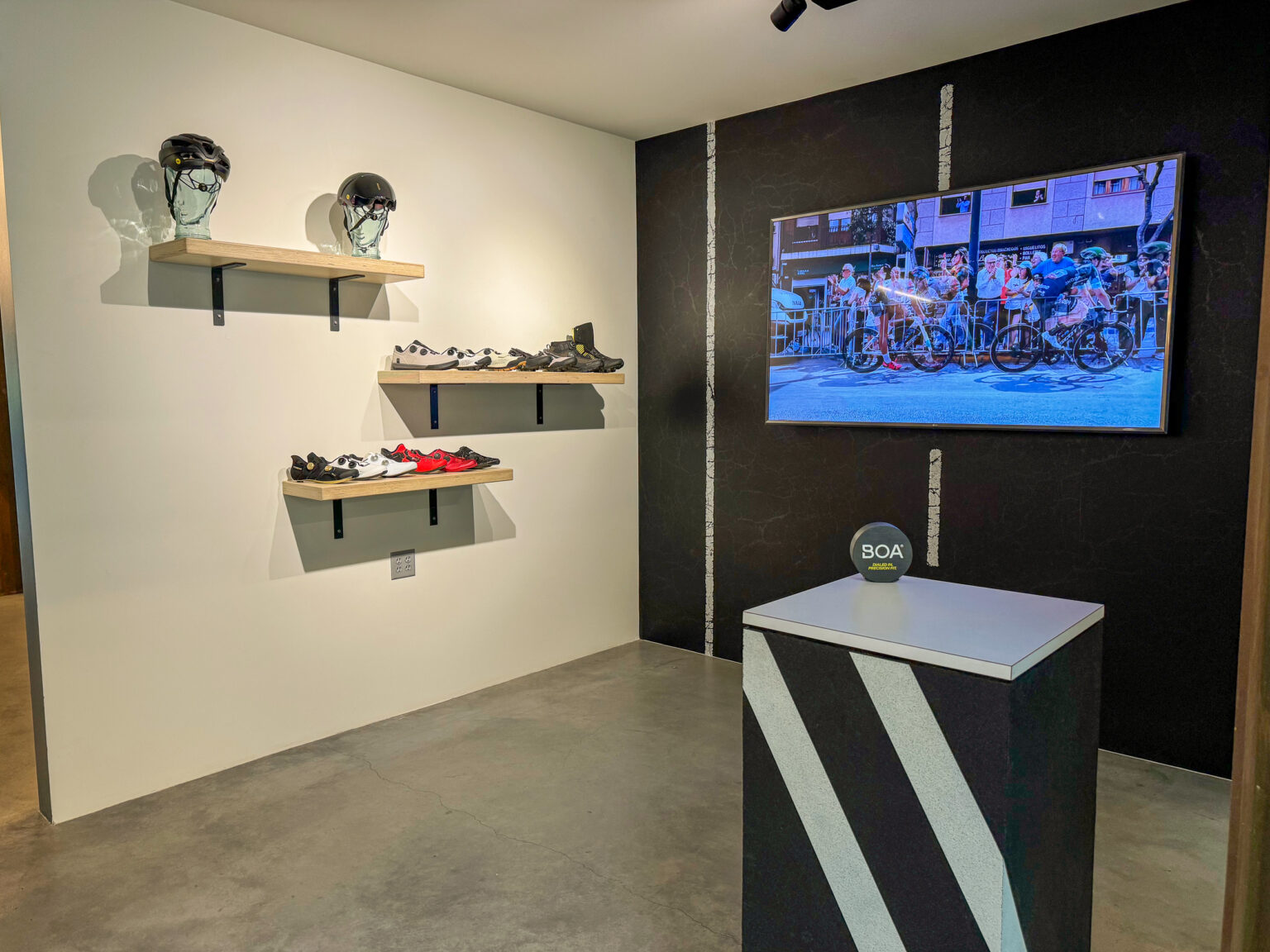
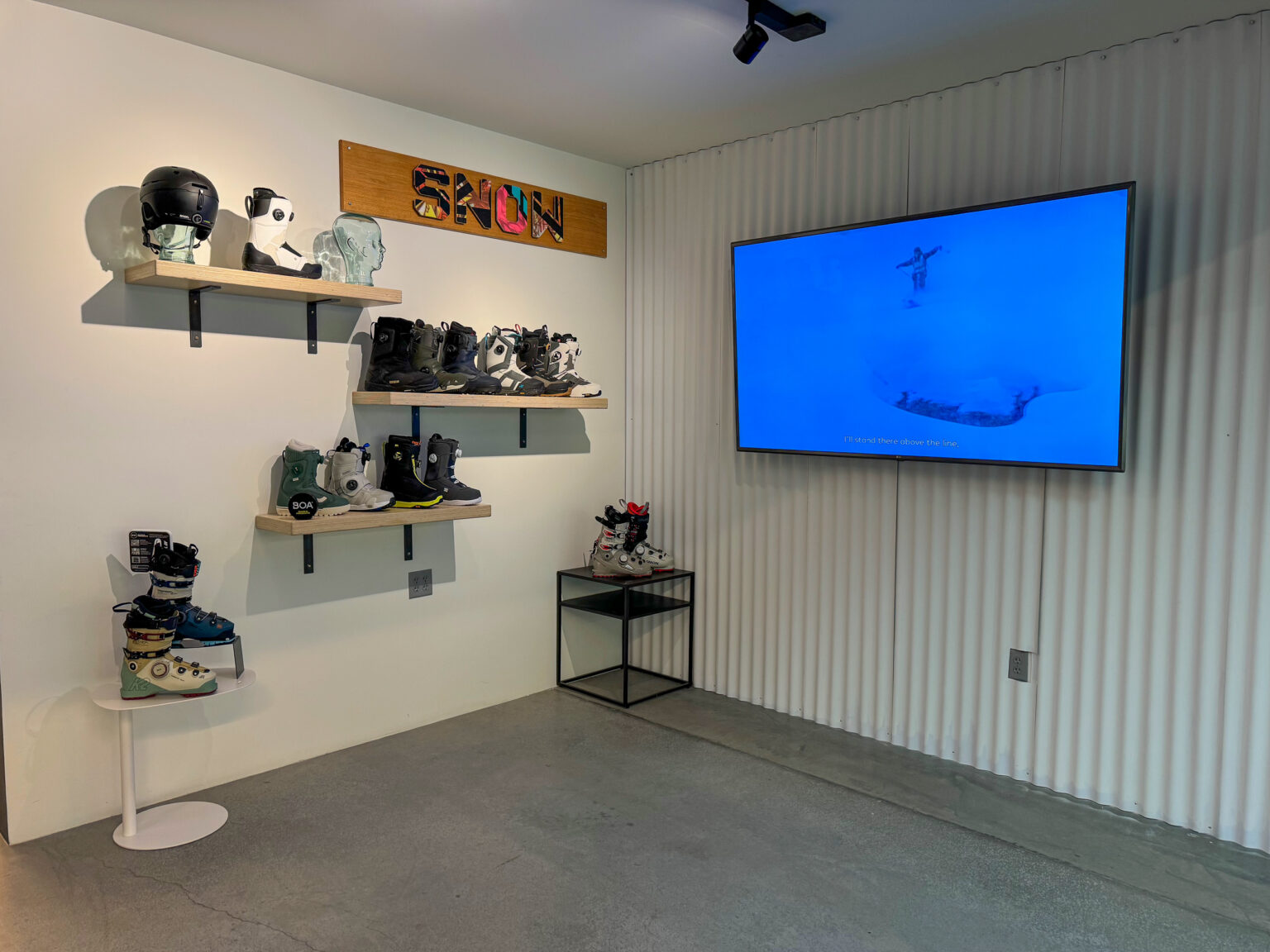
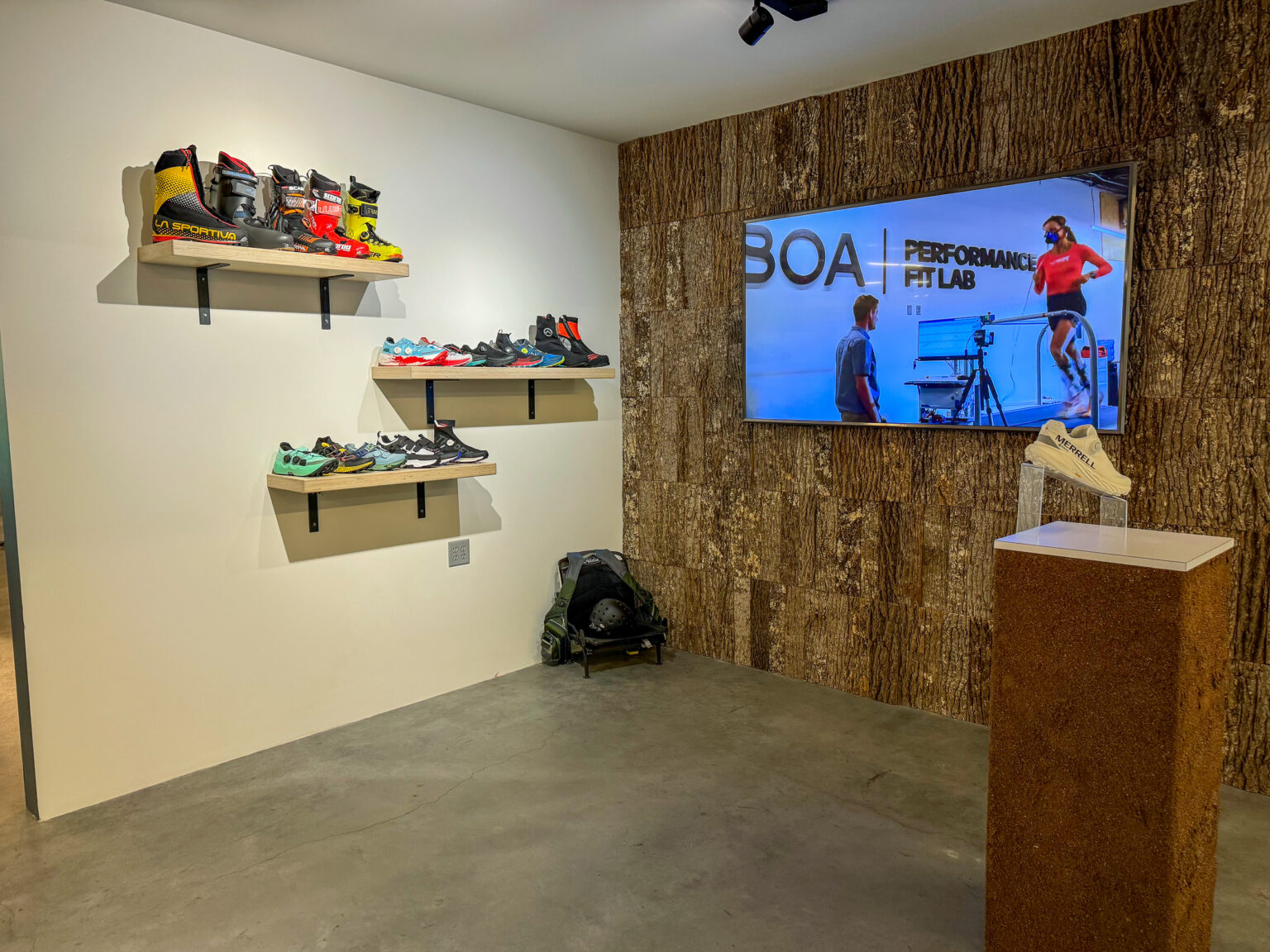
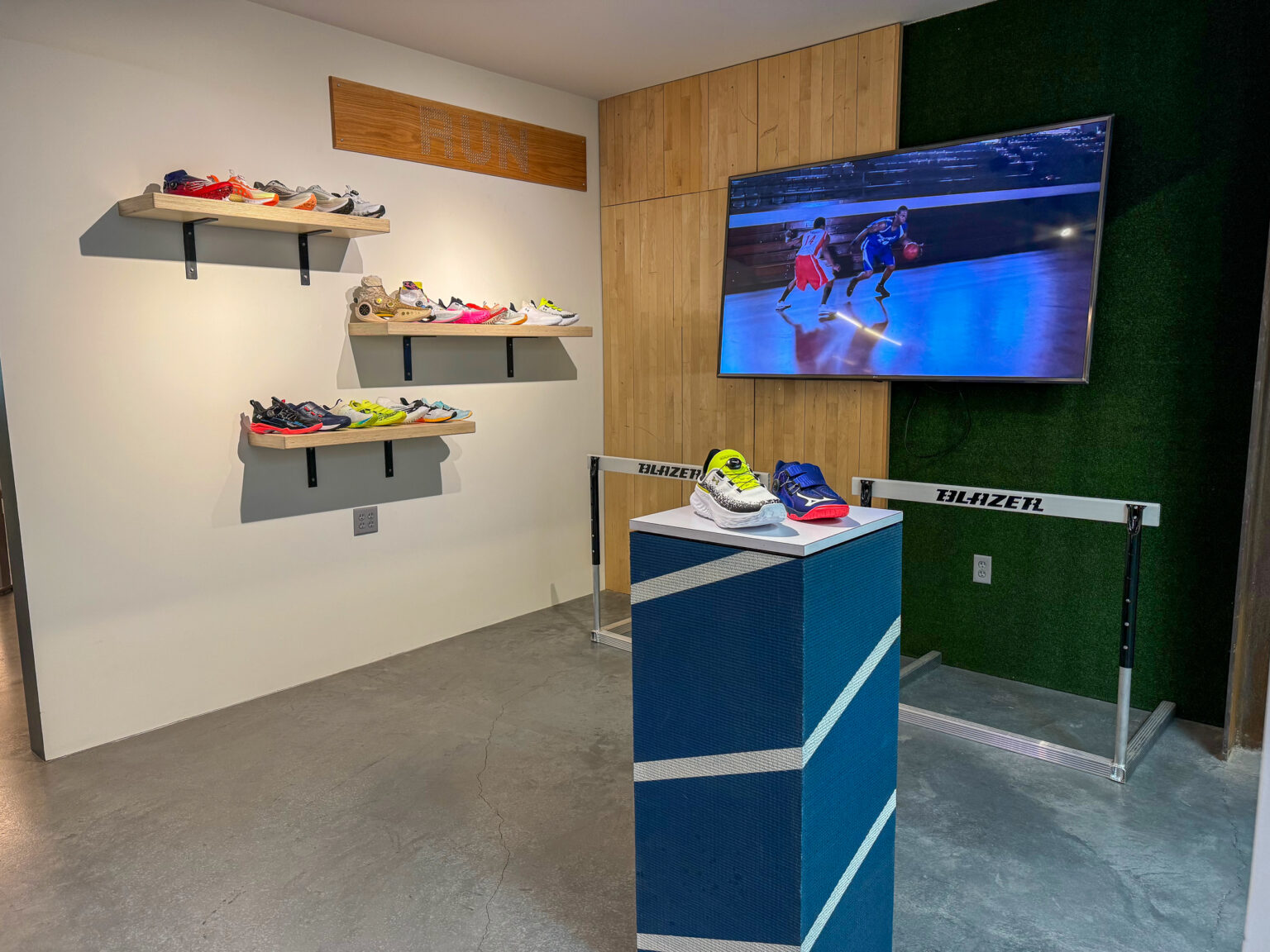
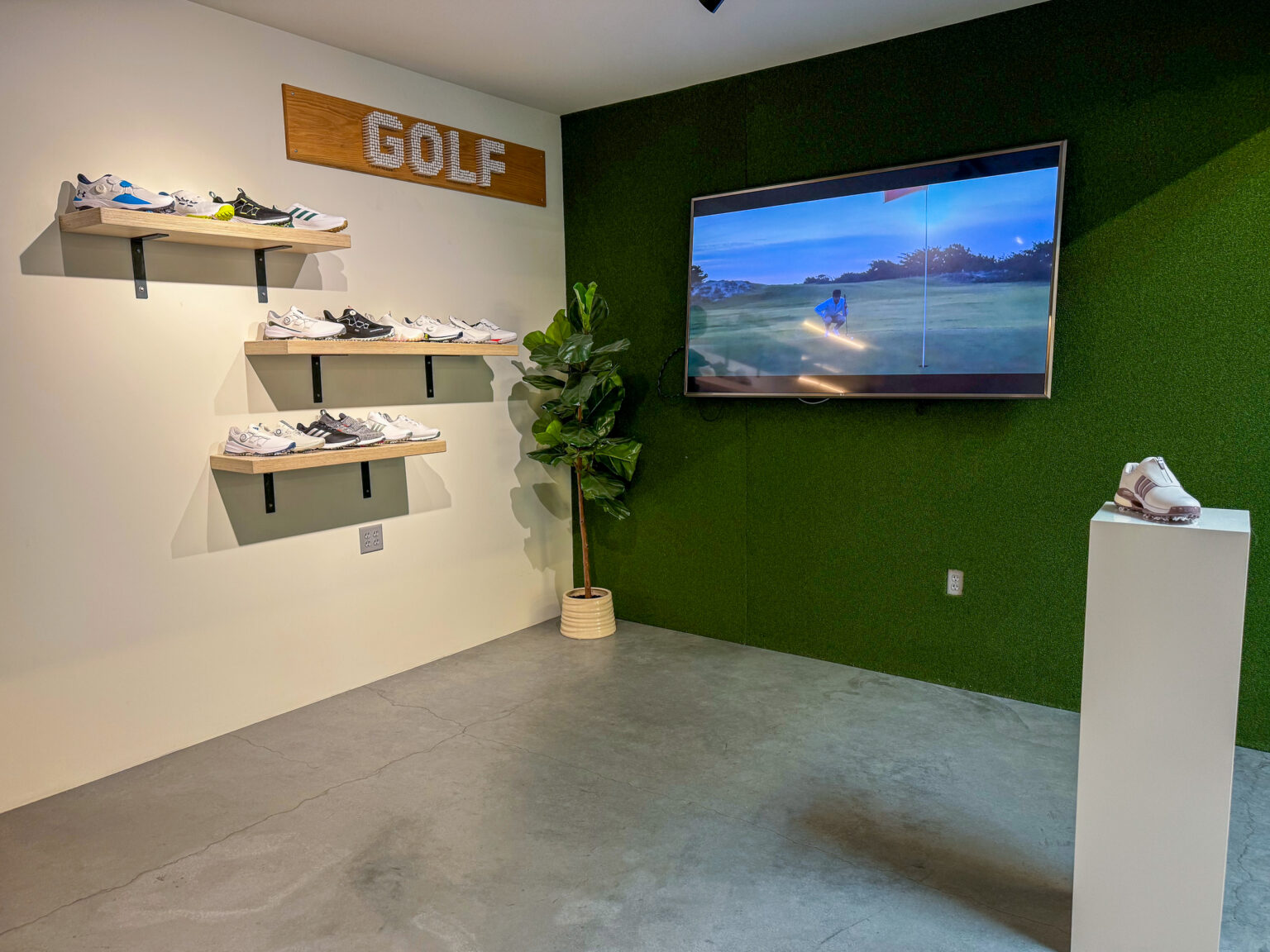
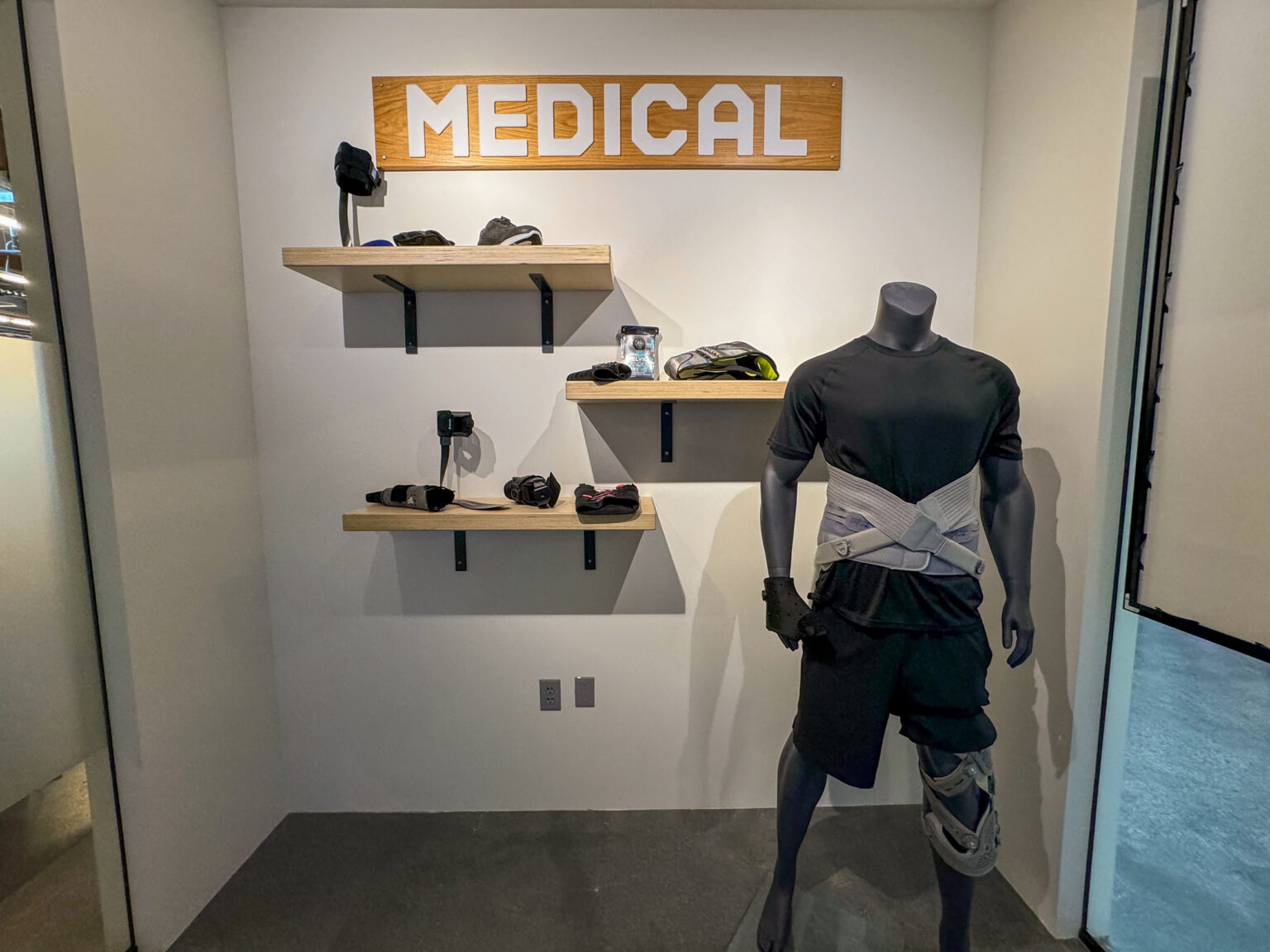
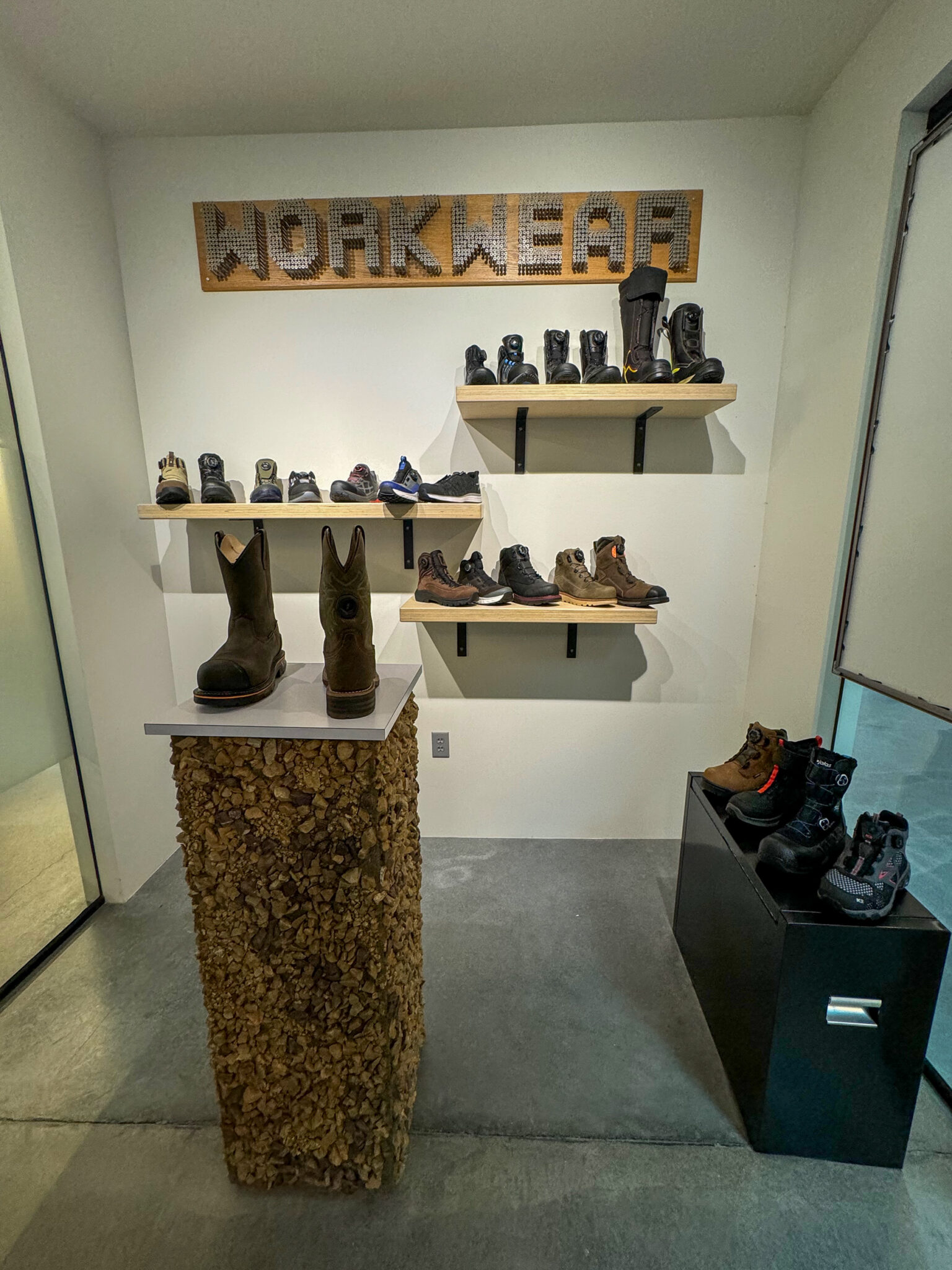
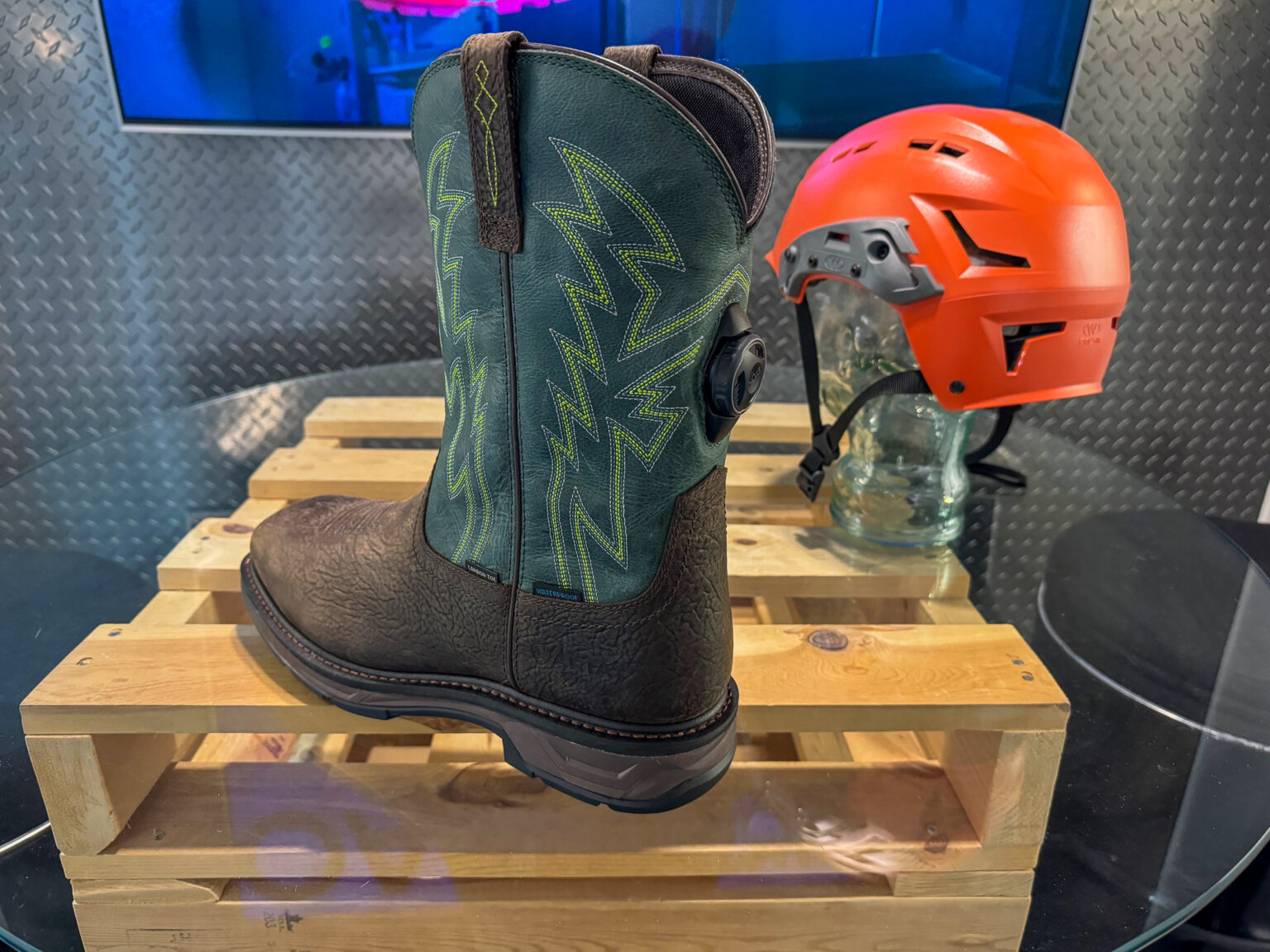
Fast forward to the present, and BOA currently works with roughly 350 active brand partners (35-40 of those are cycling brands). And that’s with “turning down 99.9% of new inquiries from potential customers.” That reluctance to take on new partners is due to BOA’s desire to work directly with the brands to make the best product possible – not simply to just send them BOA dials and laces off the shelf.
That desire to create the best product possible is on full display at their newest headquarters in the RiNo area of Denver, CO. While the new building is just a stone’s throw from the previous one, its increased size has allowed BOA to gain the necessary space to essentially create a miniature shoe factory and test facility.
Creating their own prototype shoes
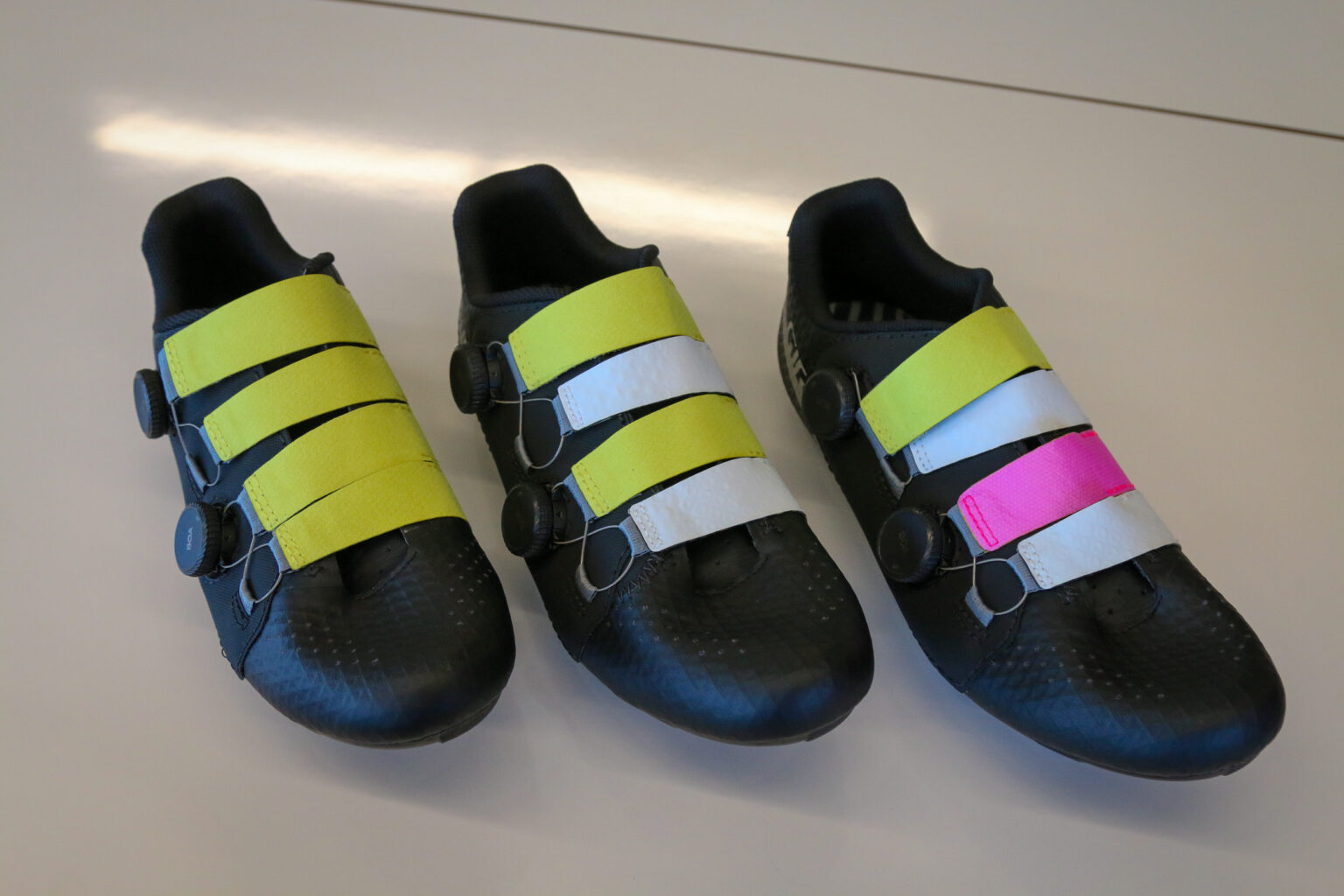
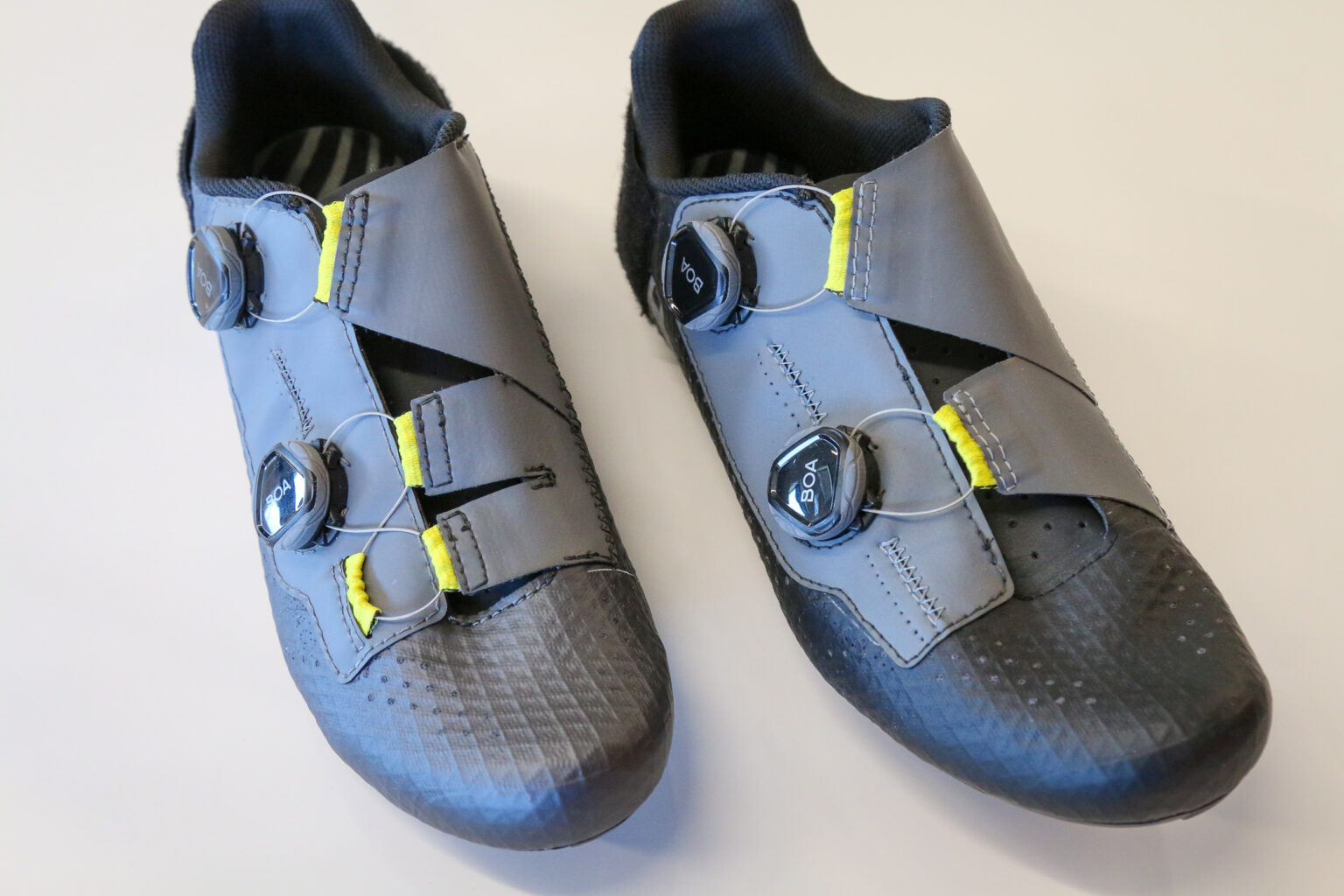
While BOA doesn’t have the ability to create the lowers and outsoles of shoes on-site, they do possess everything necessary to build a shoe upper on-site. That allows them to reverse engineer and rebuild existing models in the quest to build better systems.
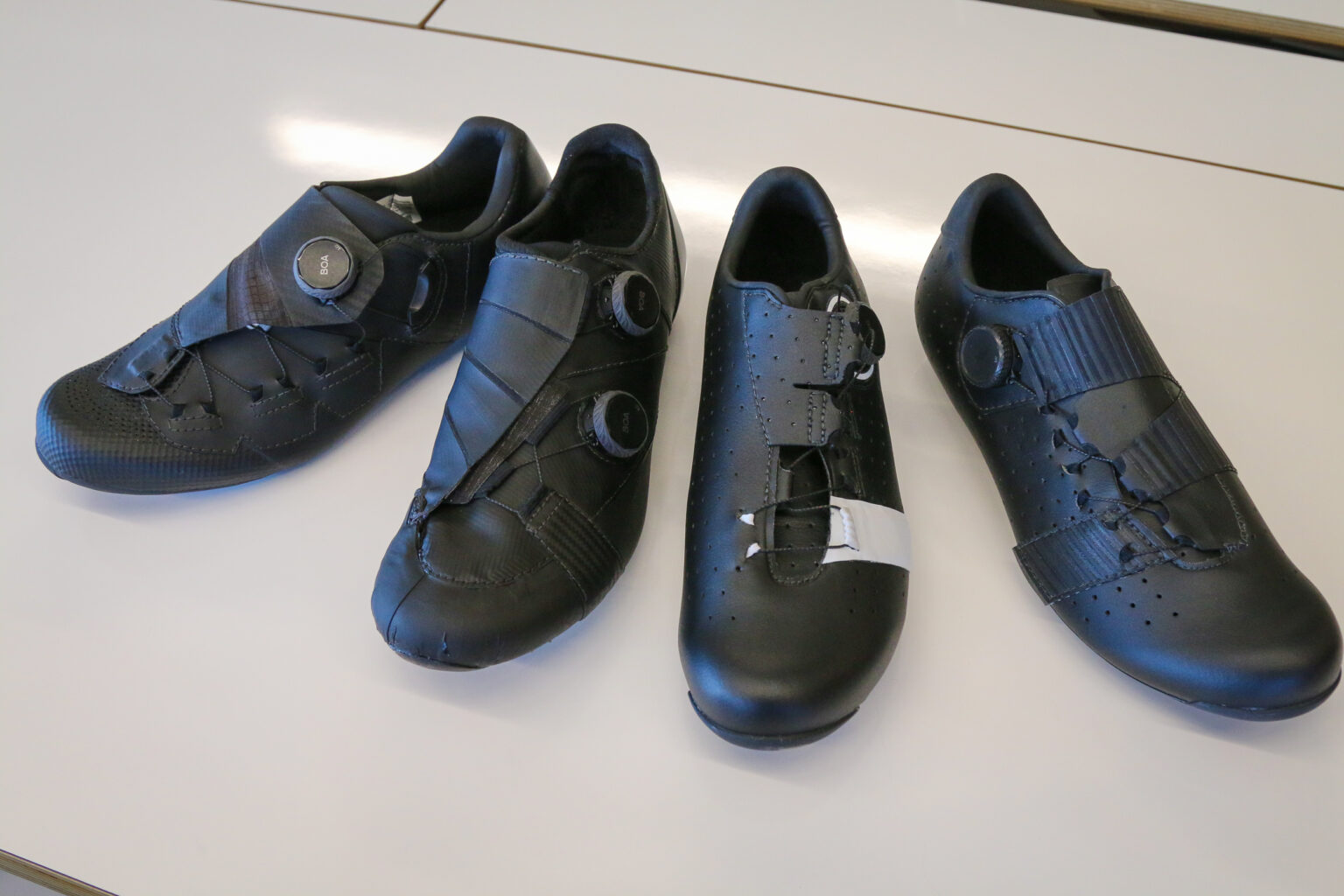
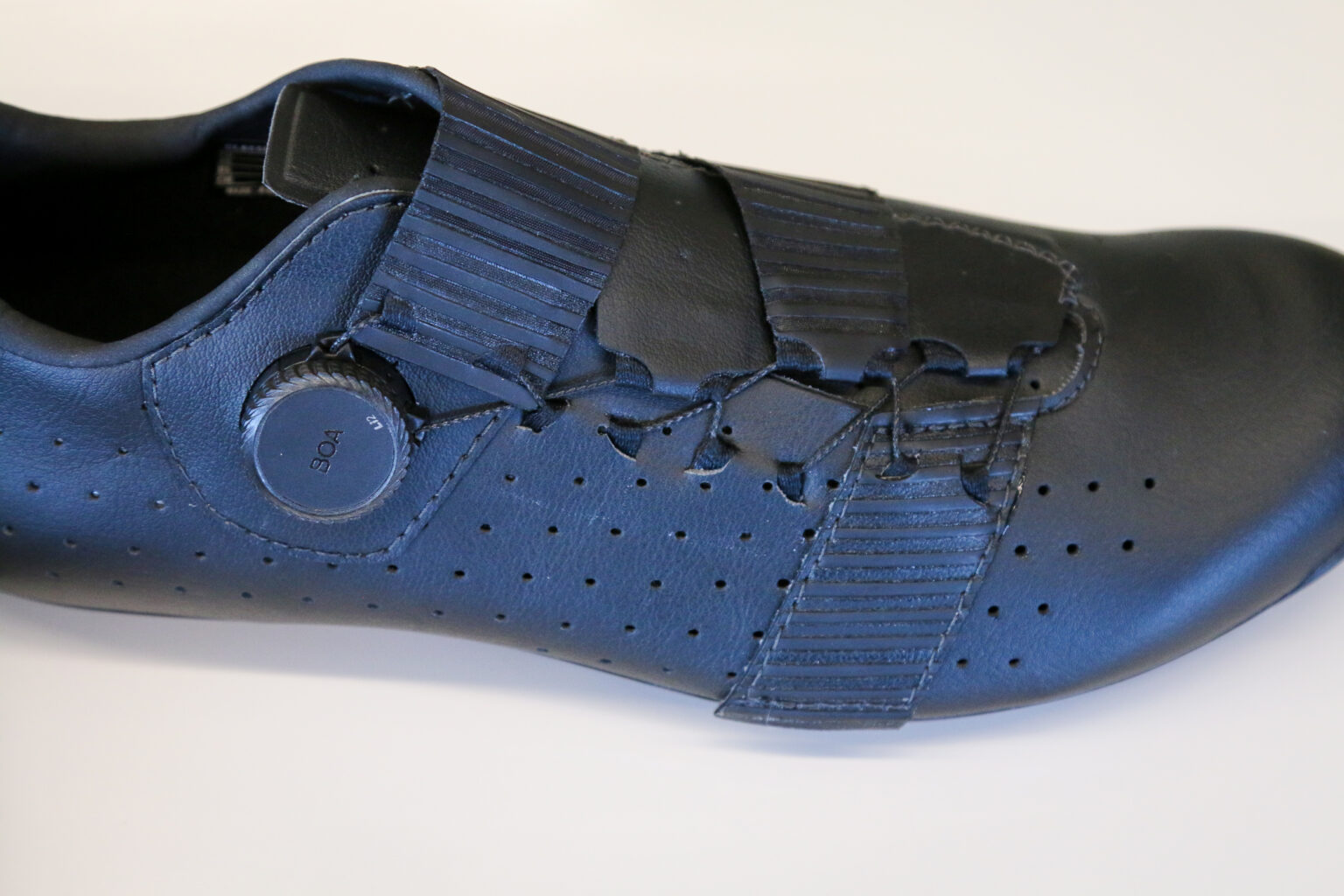
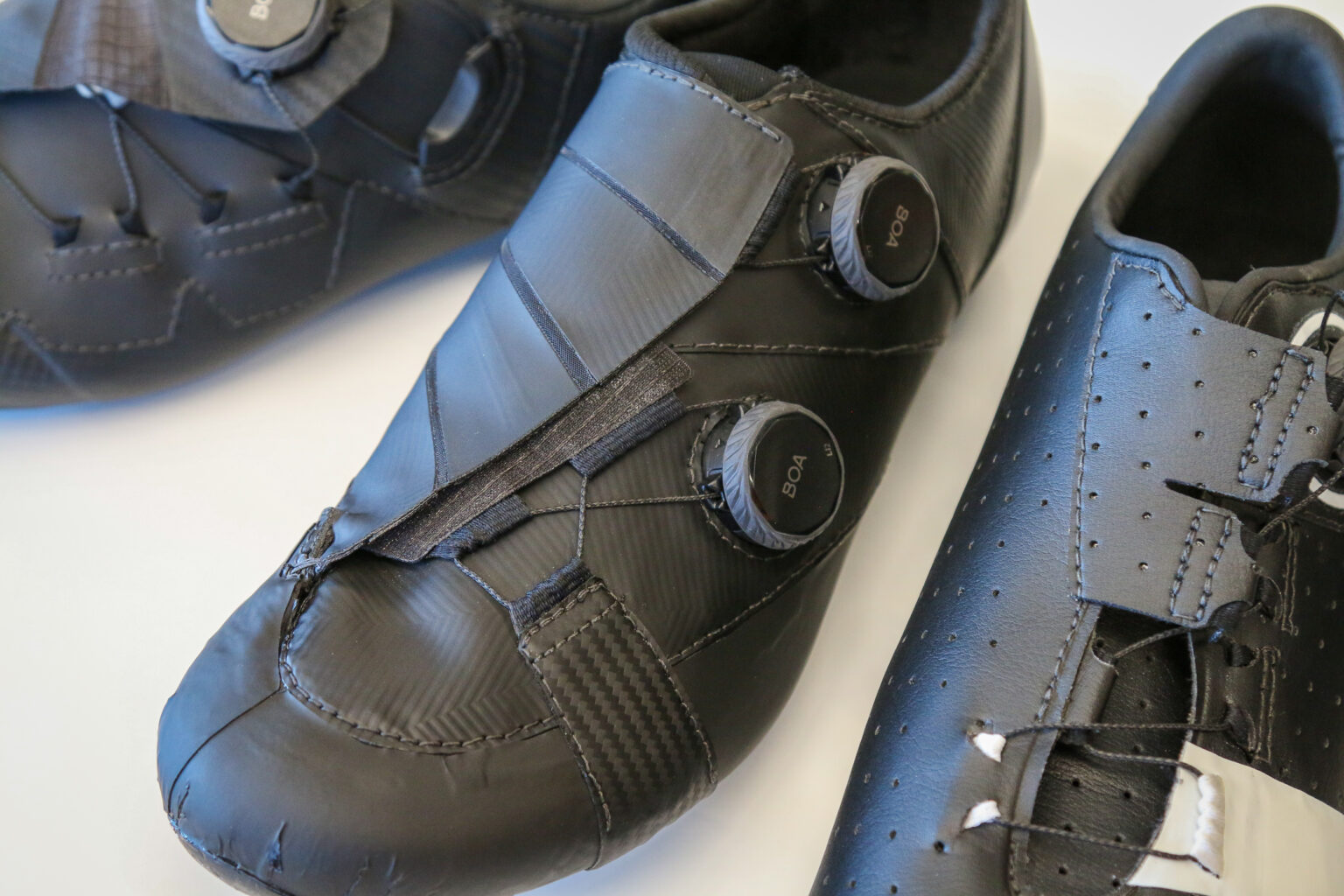
During one of the presentations, we were shown shoes that could easily be mistaken as production models. Only they were one-off prototypes created by the BOA lab. Even with the ability to clearly create their own shoes, BOA says it will probably never happen – they don’t want to compete with their partners.
Instead, they want to see how the shoe looks, how it can be executed, and maybe most important of all, how it will affect the biomechanics side. The quest for a more efficient fit is a big reason we were brought out to BOA HQ as it coincided with the launch of two new shoes featuring their PerformFit Wrap concept.
BOA Performance Fit Lab
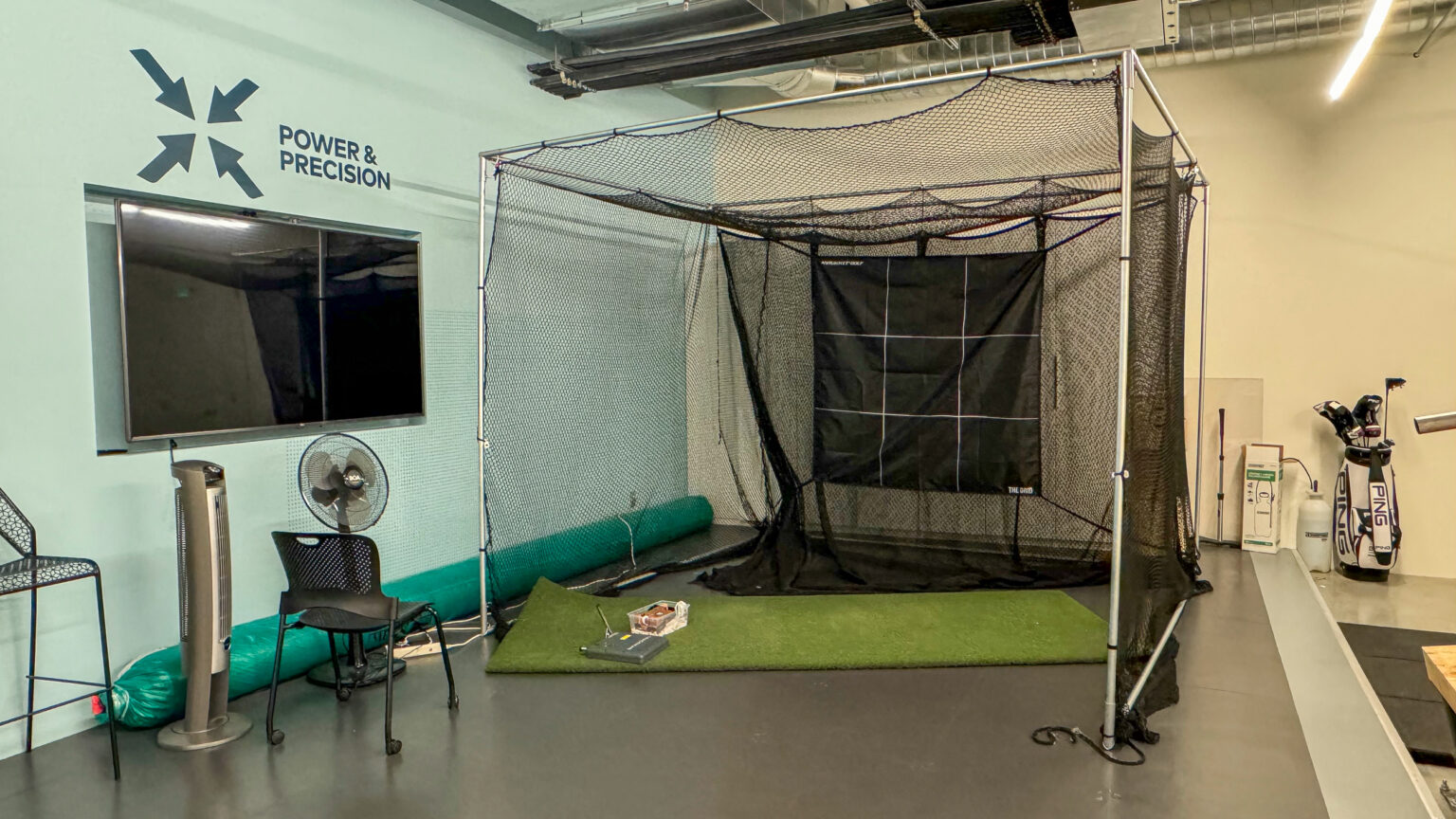
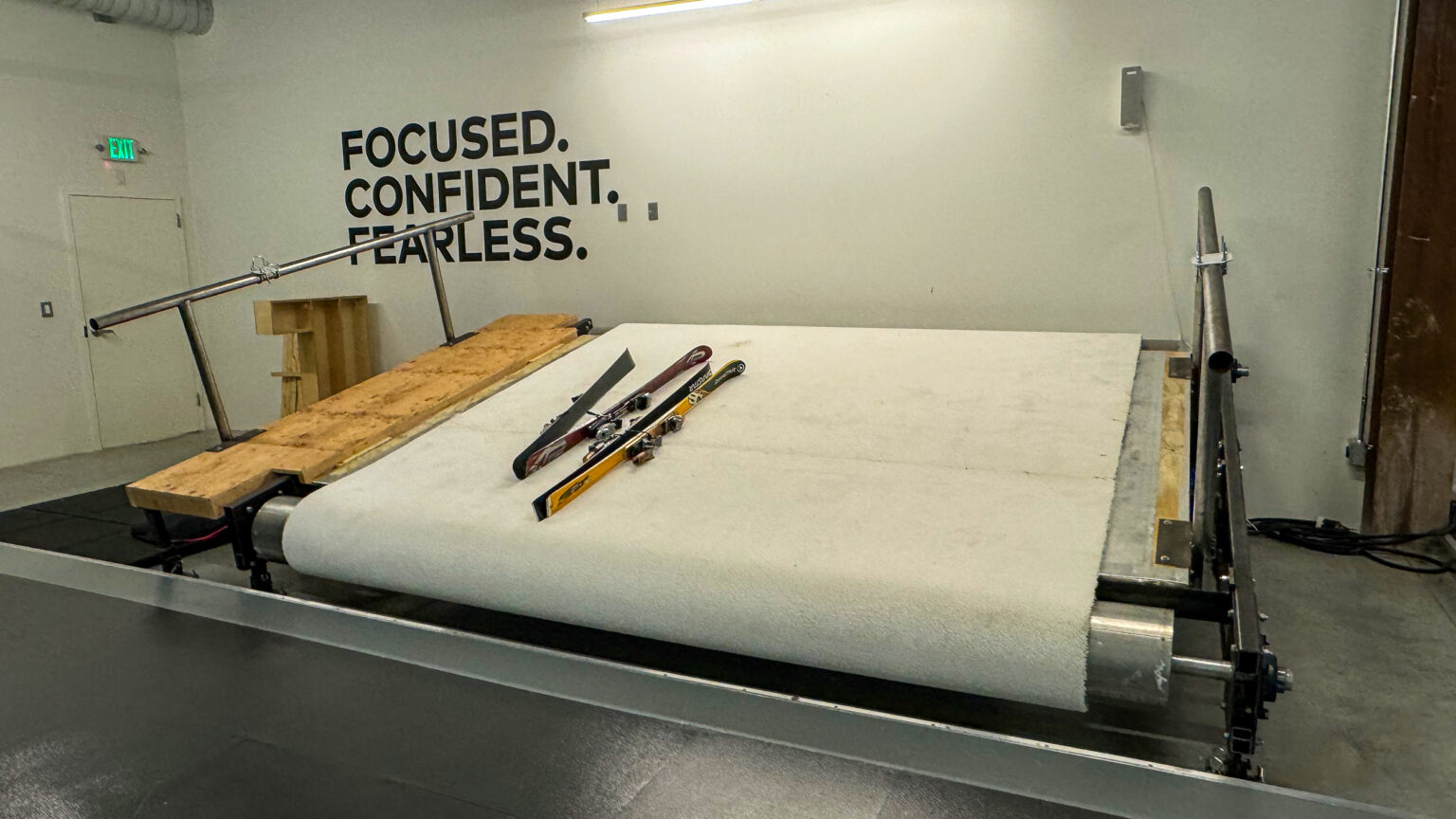
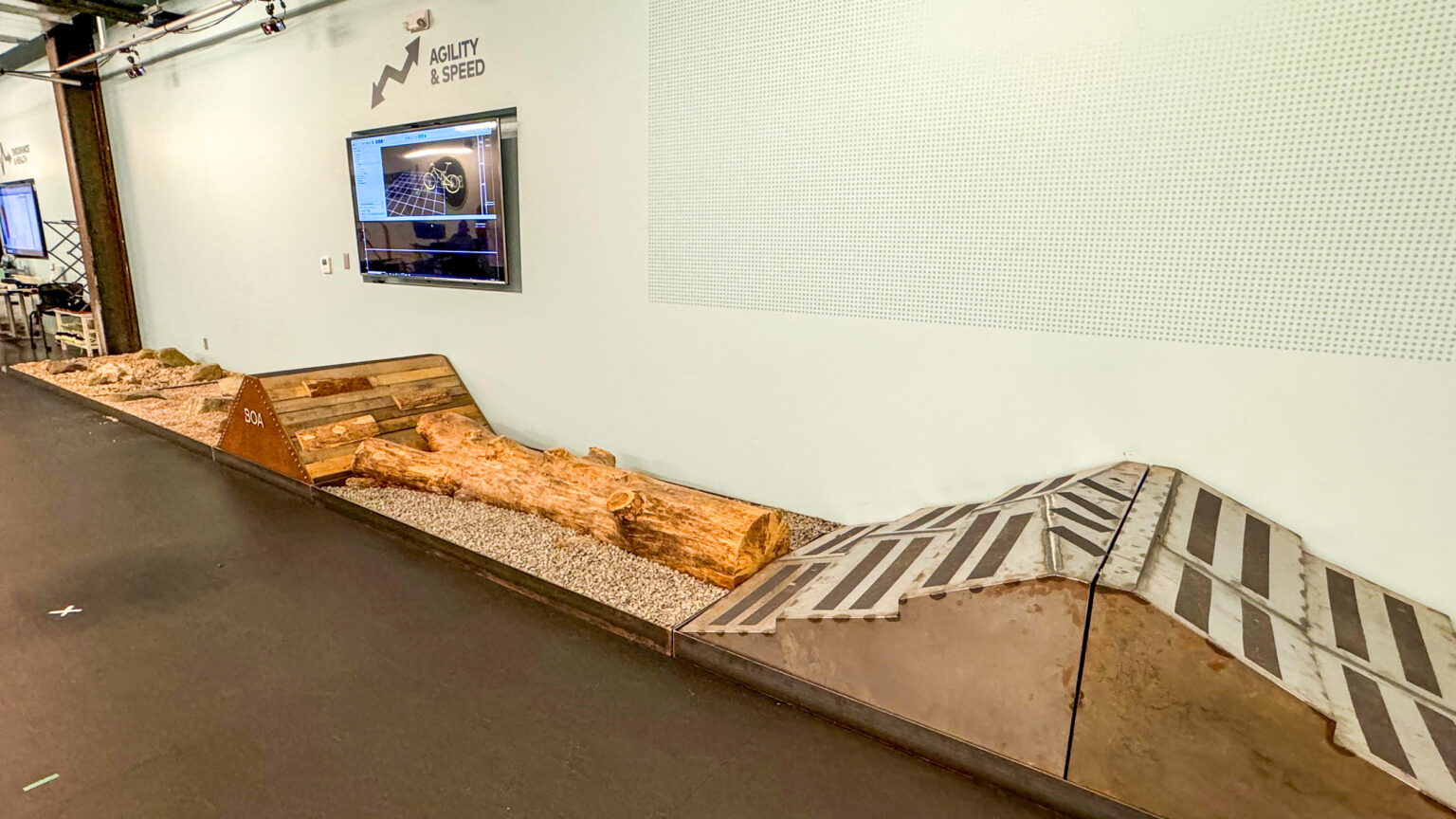
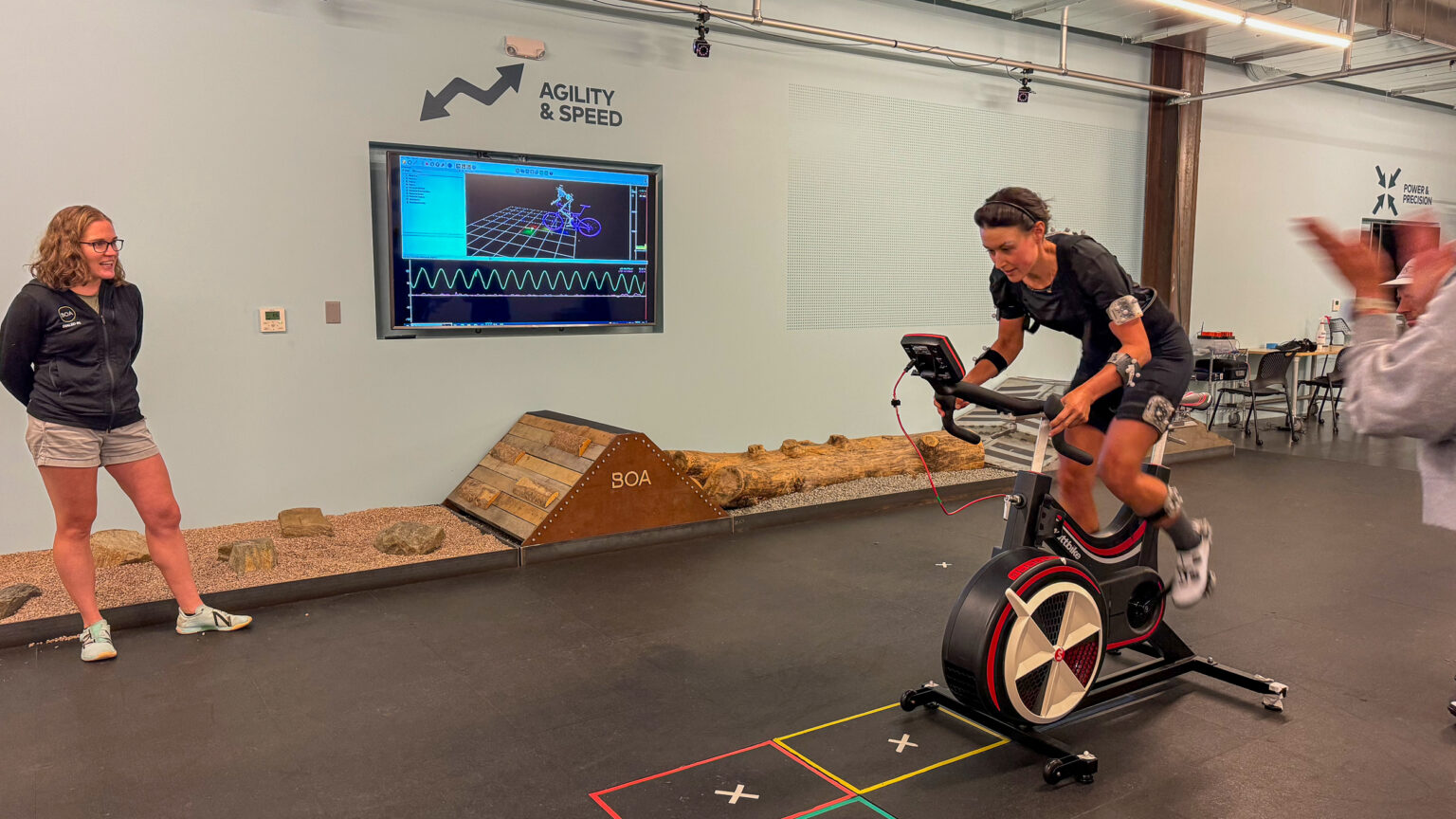
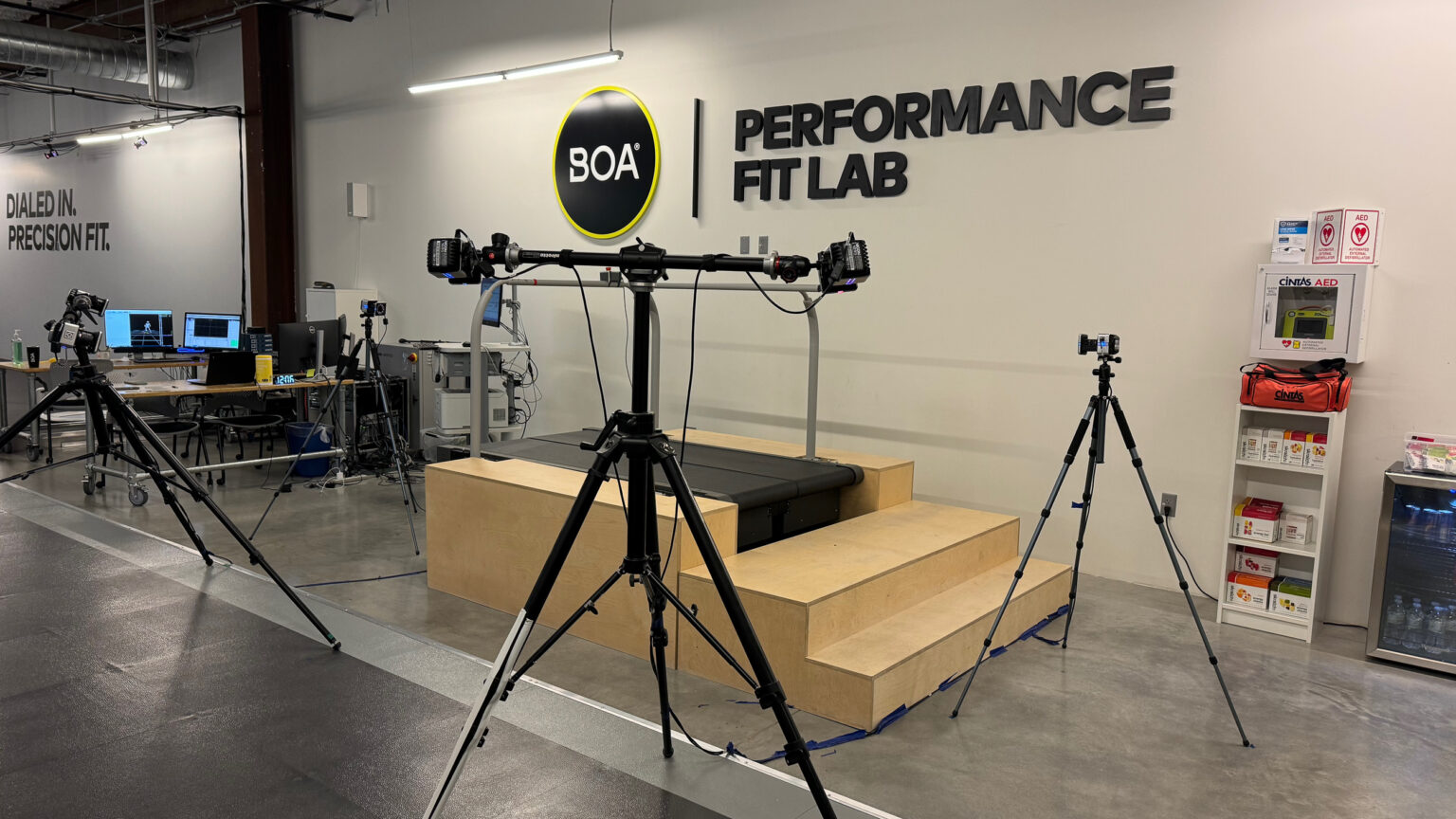
From the beginning BOA has been not just about replacing laces, but elevating the fit. Research in their own BOA Performance Fit Lab has confirmed that a better fit will yield better performance. By wrapping the midfoot and locking in the heel rather than pinching down the center of a ‘u-throat’ design, BOA has measured some impressive gains in the lab.
Broken down into the Endurance & Health, Agility & Speed, and Power & Precision areas, the BOA Performance Fit Lab has everything from force plates that measure impacts up to 1000x per second, to advanced motion capture cameras, and a metabolic cart for a complete measurement of the athlete’s vitals.
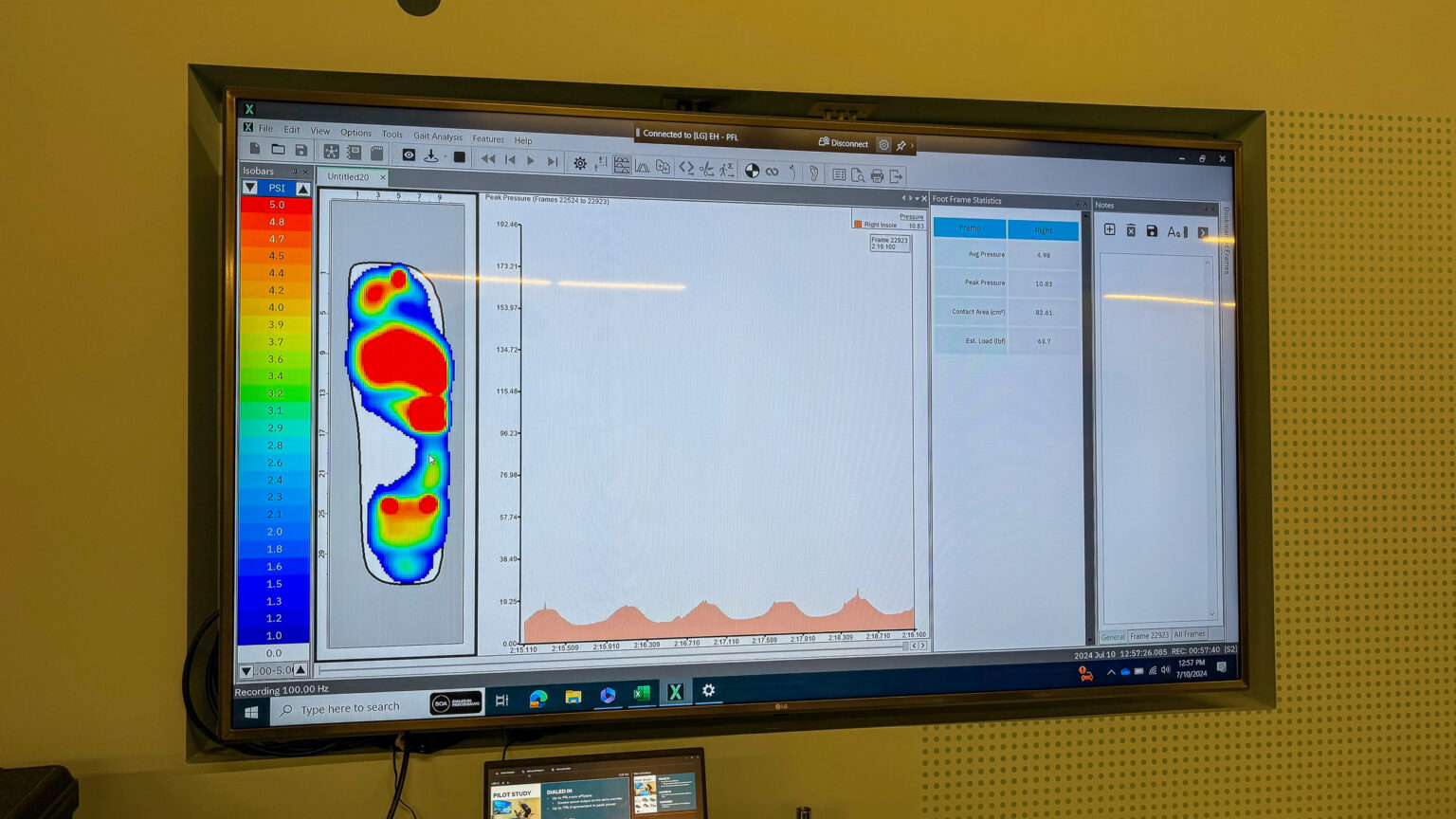
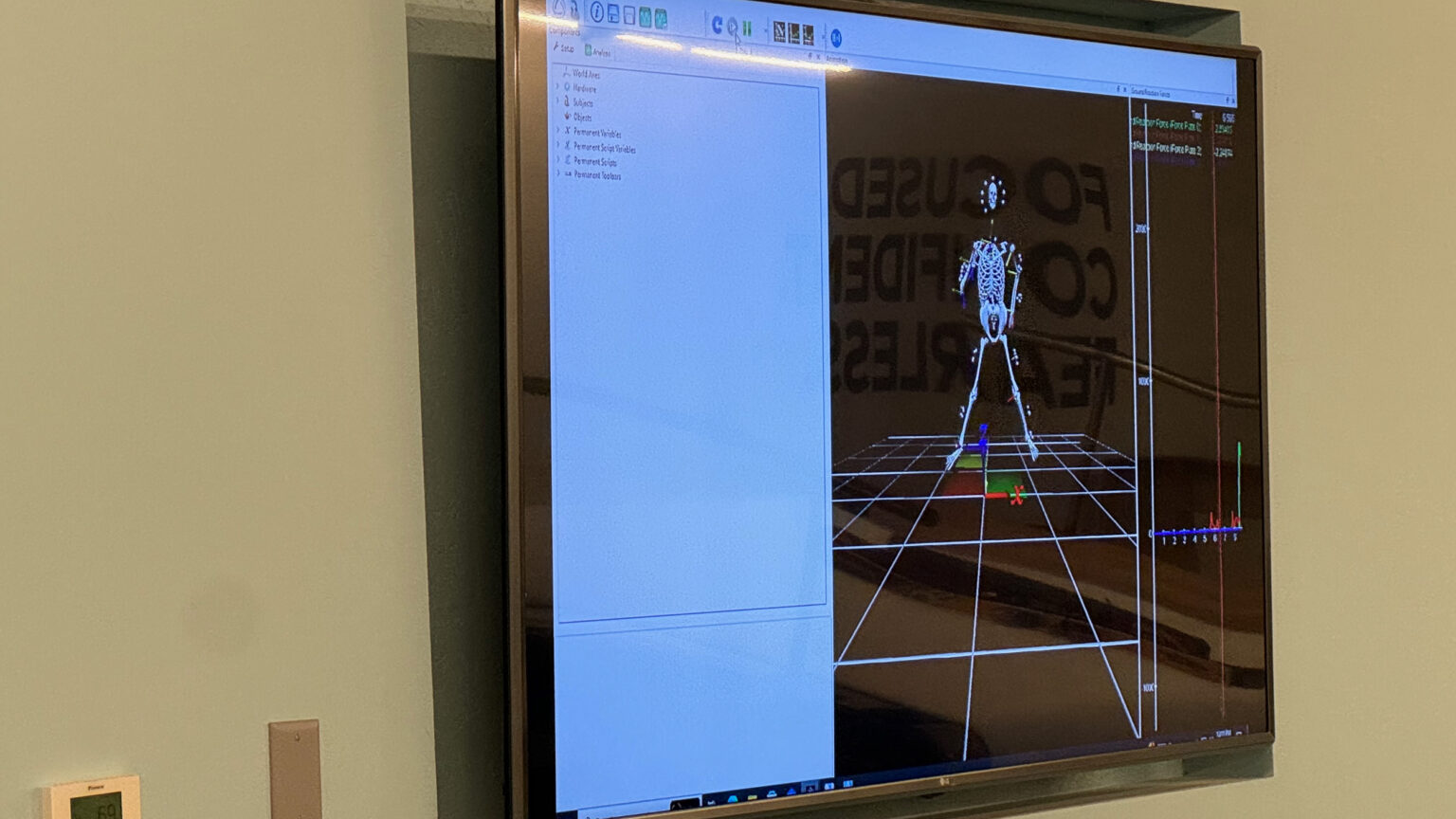
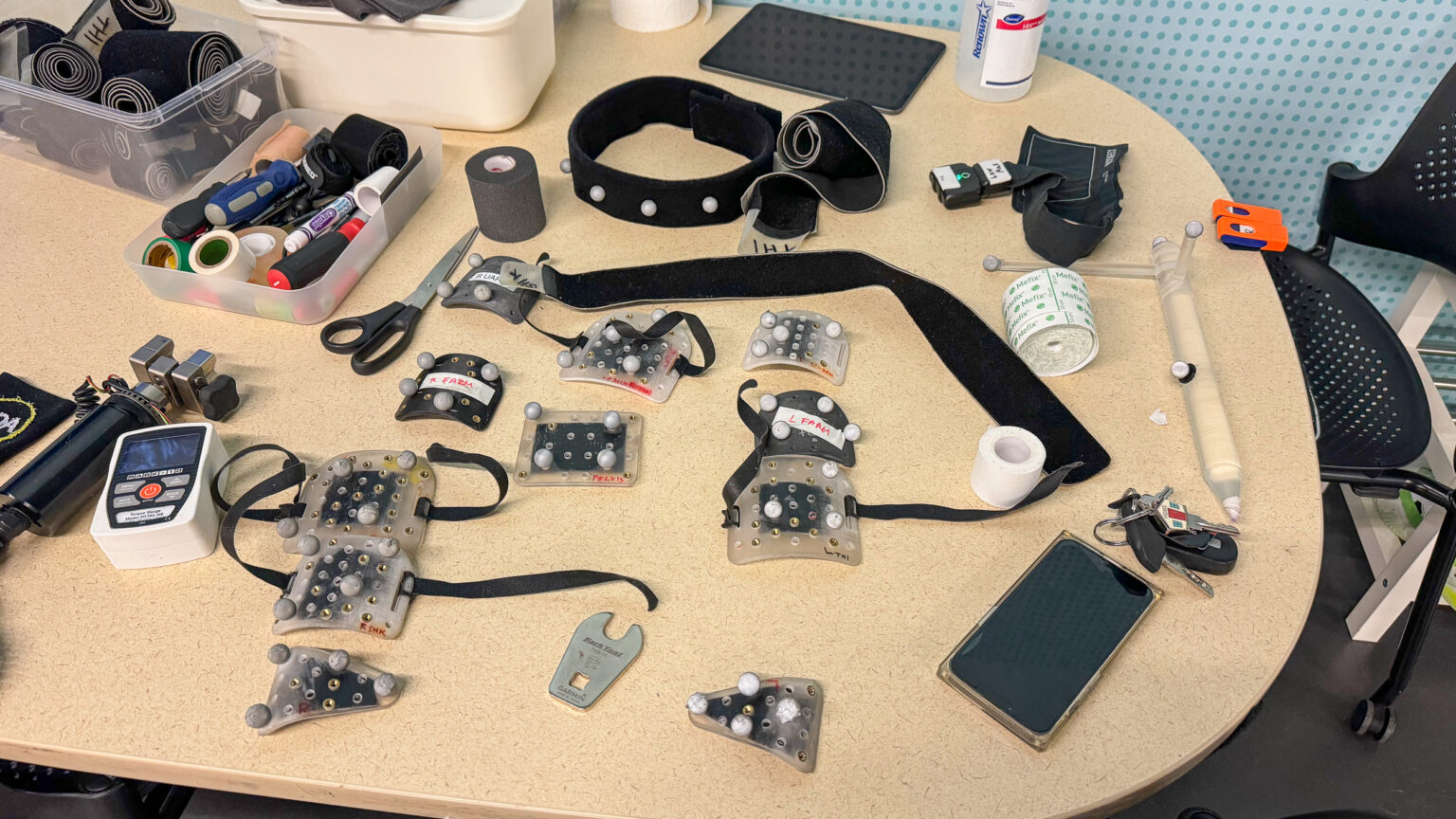
In a pilot study, BOA had 13 athletes test three different shoes – a Velcro strap model, one with a single BOA dial in a classic arrangement, and one with their most advanced PerformFit Wrap. Utilizing pressure mapping insoles, the metabolic cart, power cranks, and motion capture, they had each tester ride for 5 minutes steadily followed by 2×15 second sprints. The results showed up to a “9% increase in power output while maintaining equivalent metabolic expenditure,” plus an “11% increase in peak power output during the sprints with the PerformFit Wrap shoe. Additionally, the shoe improved “pressure distribution by up to 10% for improved performance during both sprints and sustained riding.”
“Thousands of hours of testing demonstrate that wrapping over the midfoot, locking the heel, and reducing stress on the body materially enhances fit and performance. Our lab, in conjunction with our design teams, systematically evaluated how to optimize PerformFit Wrap in cycling through specific materials and panel structures that effectively conform to the foot, enabling more efficient riding and greater peak power output during sprints.”
Dan Feeney, Ph.D., BOA Senior Director of Partner Product Innovation and Development.
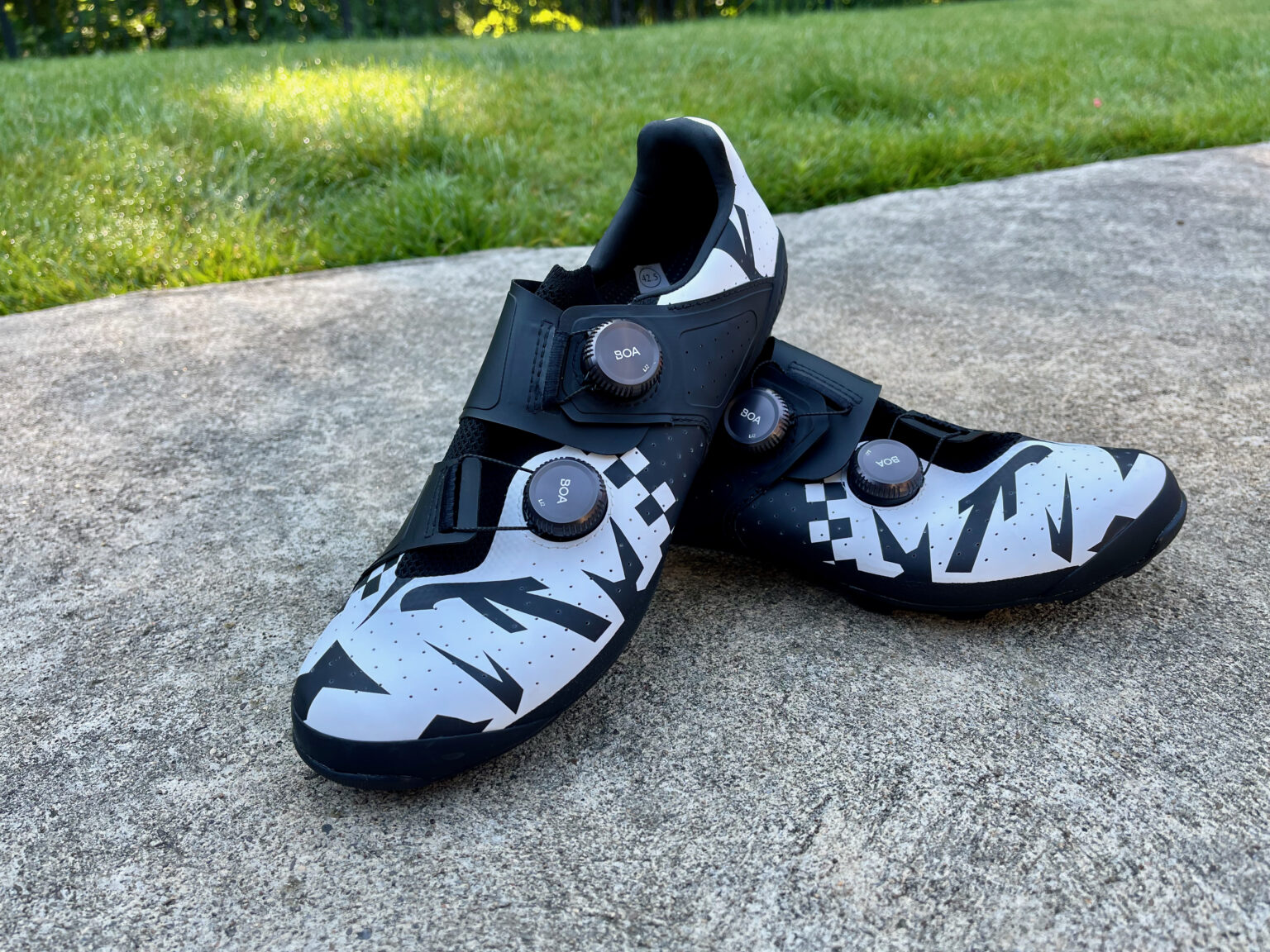
After listening to the presentation on PerformFit Wrap and visiting the Performance Fit Lab, one of the questions that came to mind was how this concept compares to existing shoe designs like the Shimano XC903. According to BOA, “while the Shimano XC903 (and other road models link the Nimbl Ultimate Glide, Trek RSL, etc.) leverage wrapping components, the upper configuration Canyon Tempr CFR and Ride Concepts Tallac Mid BOA models utilize independent panels activated by the micro-adjustable BOA Fit System and wrapping from medial to lateral. Additionally, at least two panels wrap over the dorsal ridge, which is a key component of our wrapping panels not seen with the other brands.
It is this specific configuration we’ve scientifically proven to secure the mid-foot and lock the heel back and down for the shared percentages around increased peak power and efficiency. PerformFit Wrap is the term we use at BOA to denote this type of configuration scientifically validated to improve performance.
BOA-powered models like the Shimano RC and XC902, 903, as well as a few other select models do not directly match the tested configuration, but offer some degree of wrap, and thus, likely offer some degree of similar benefits.”
Development & Testing Lab
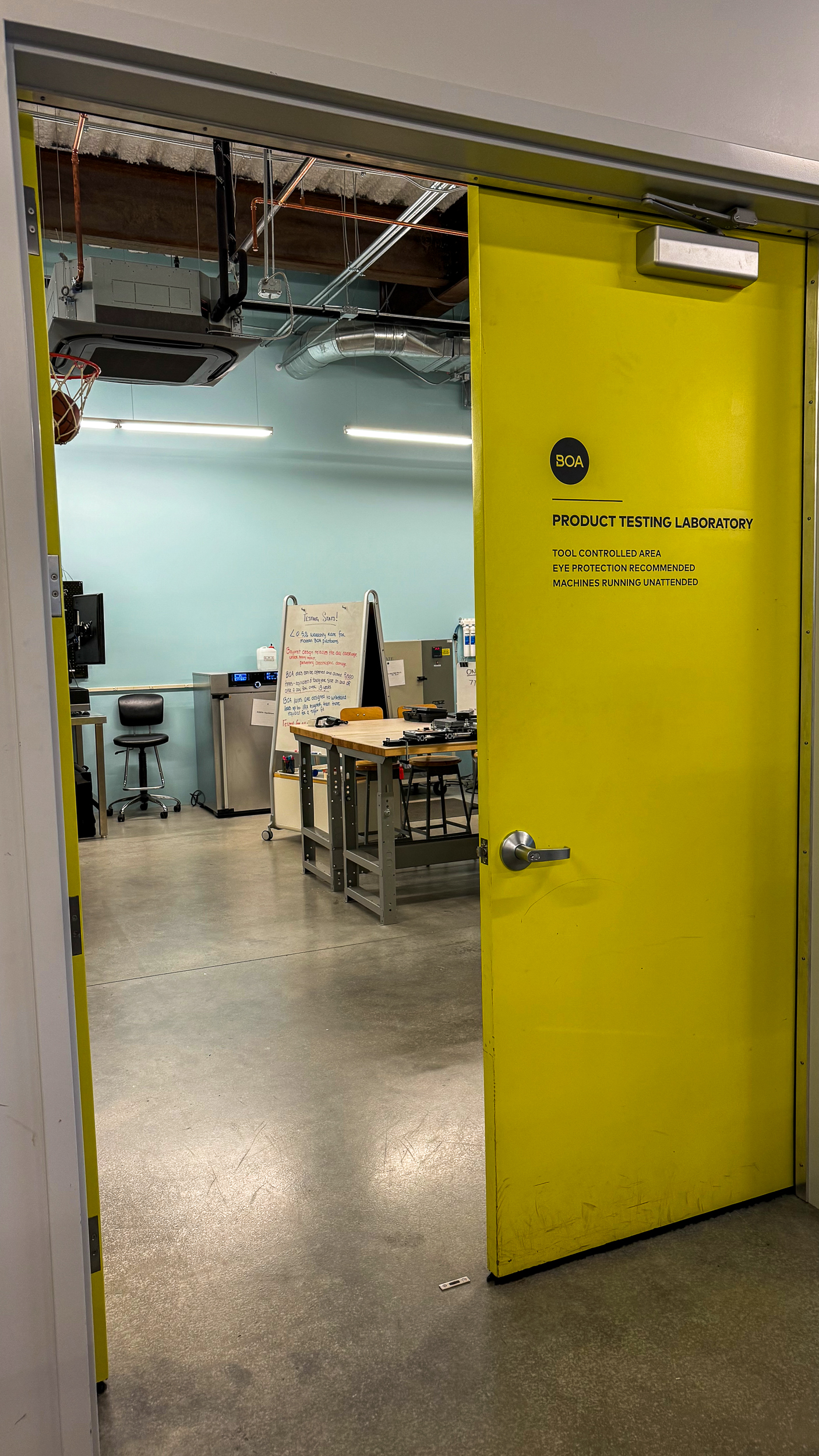
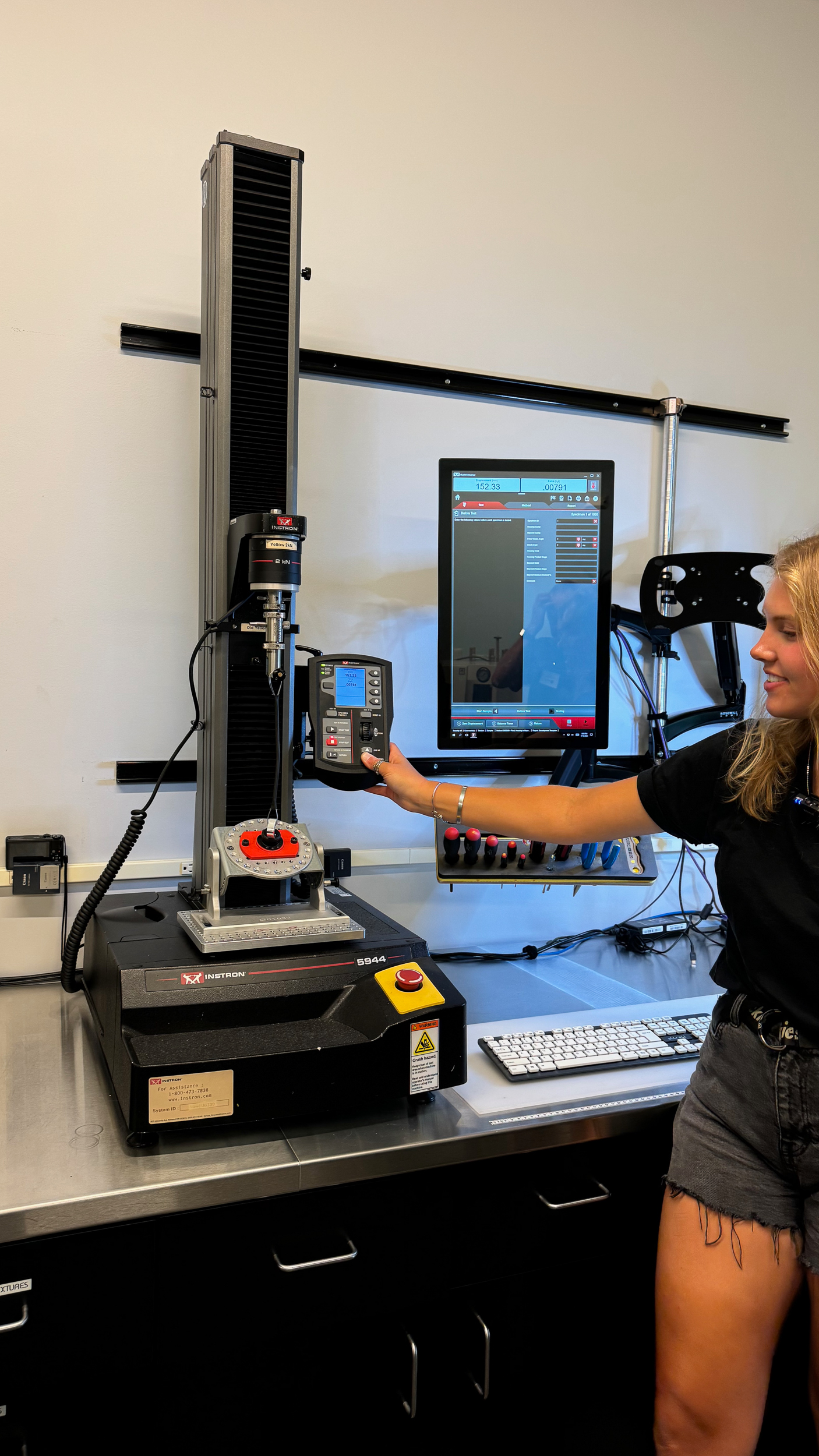
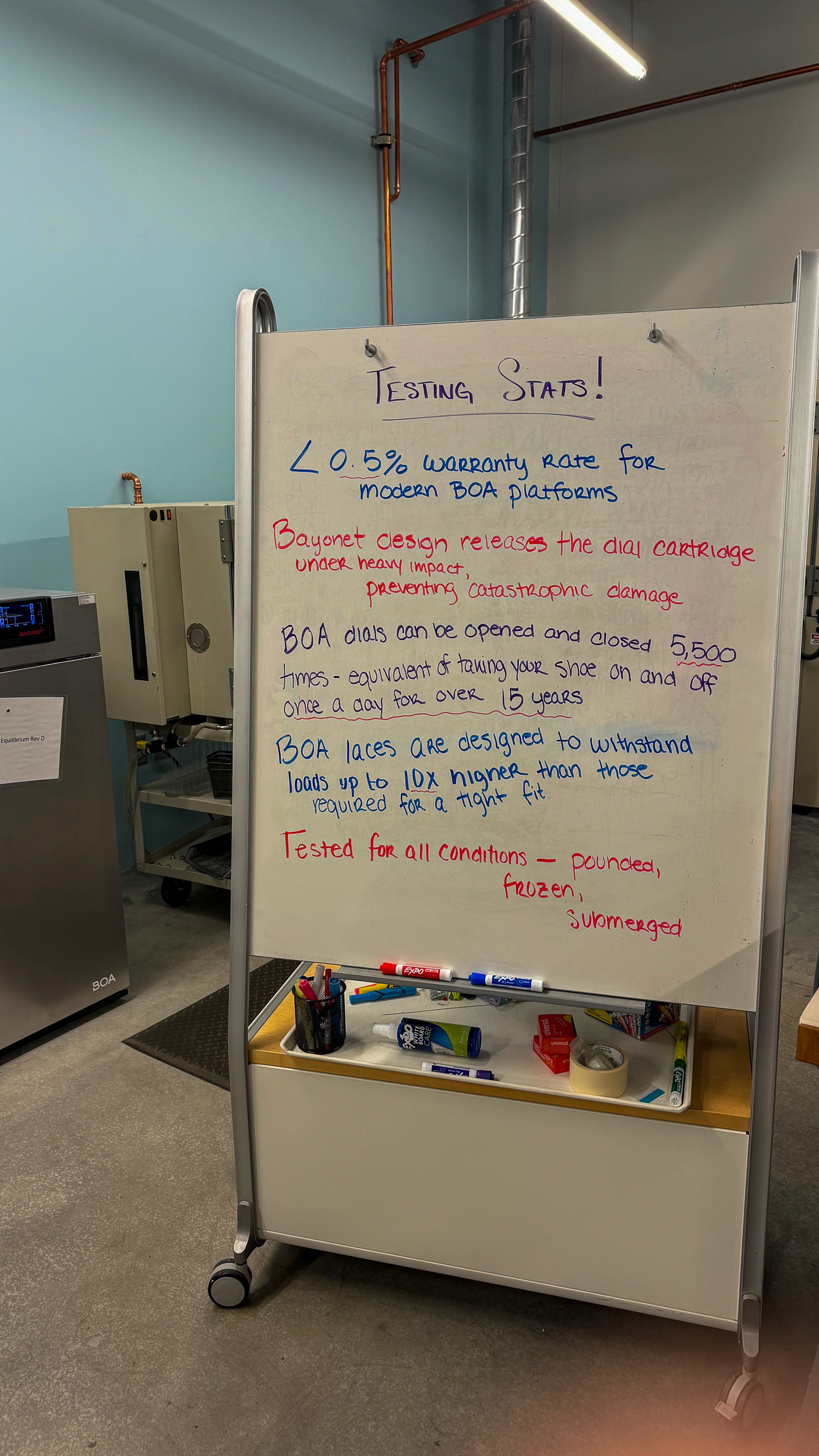
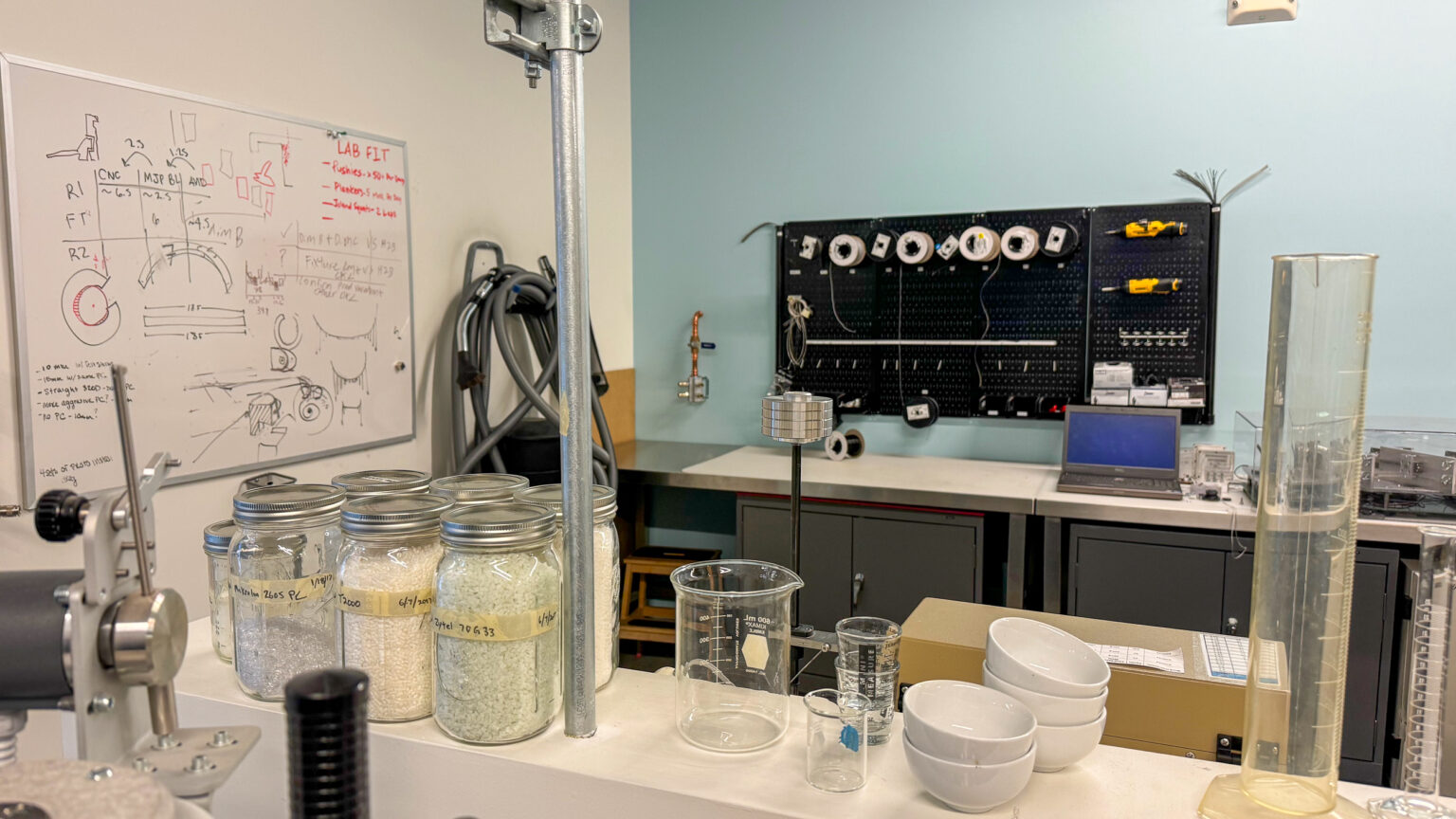
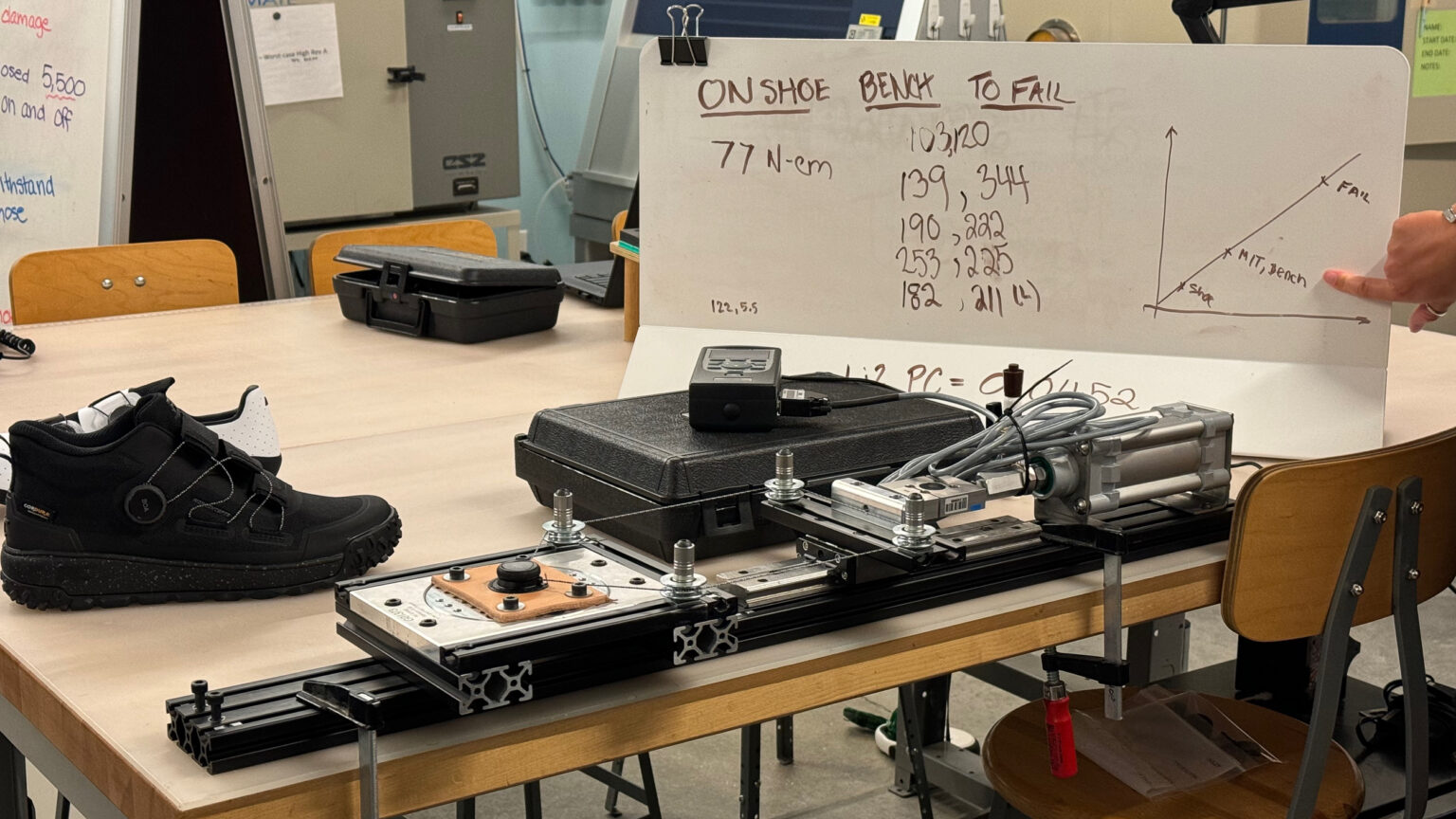
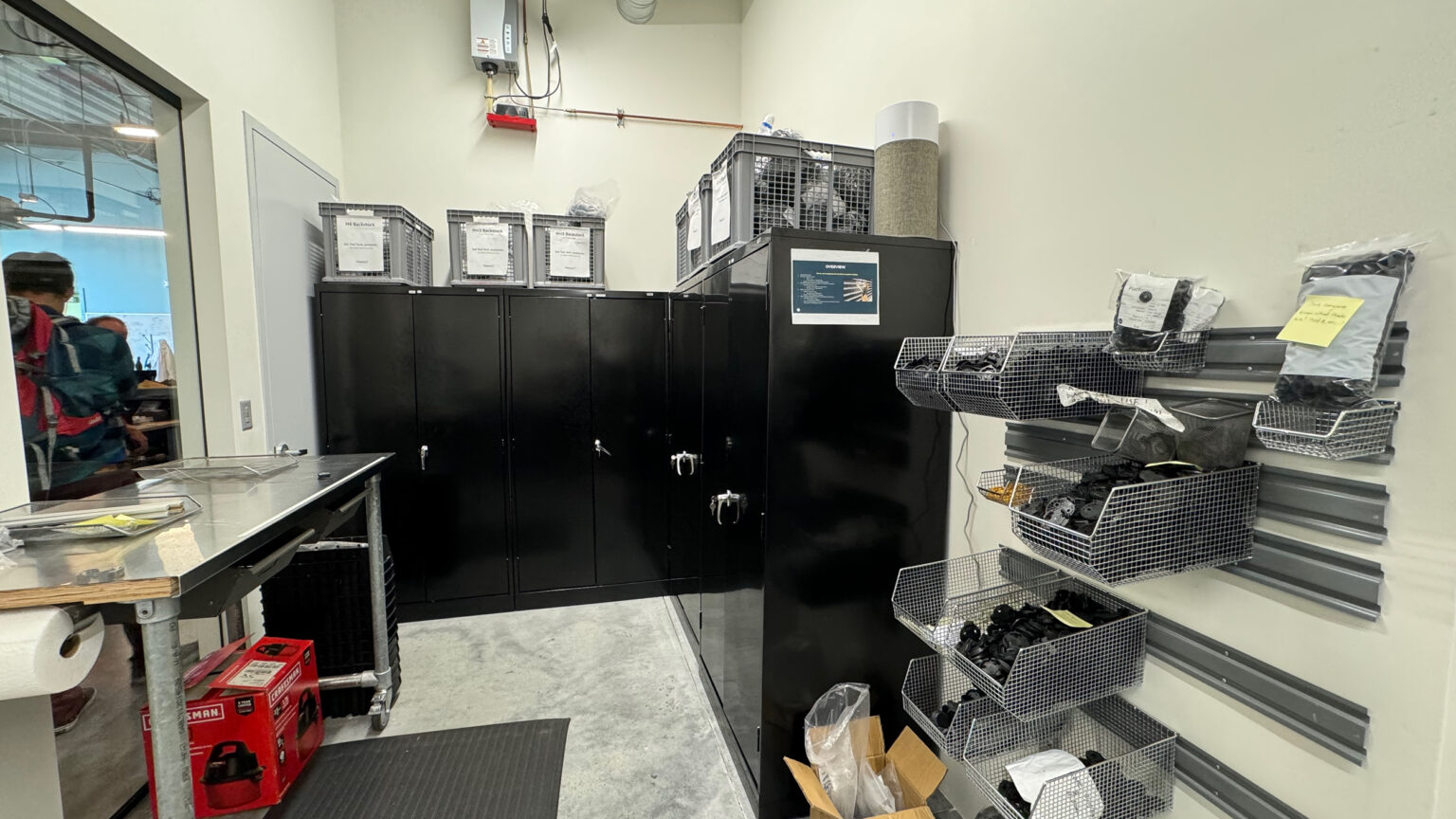
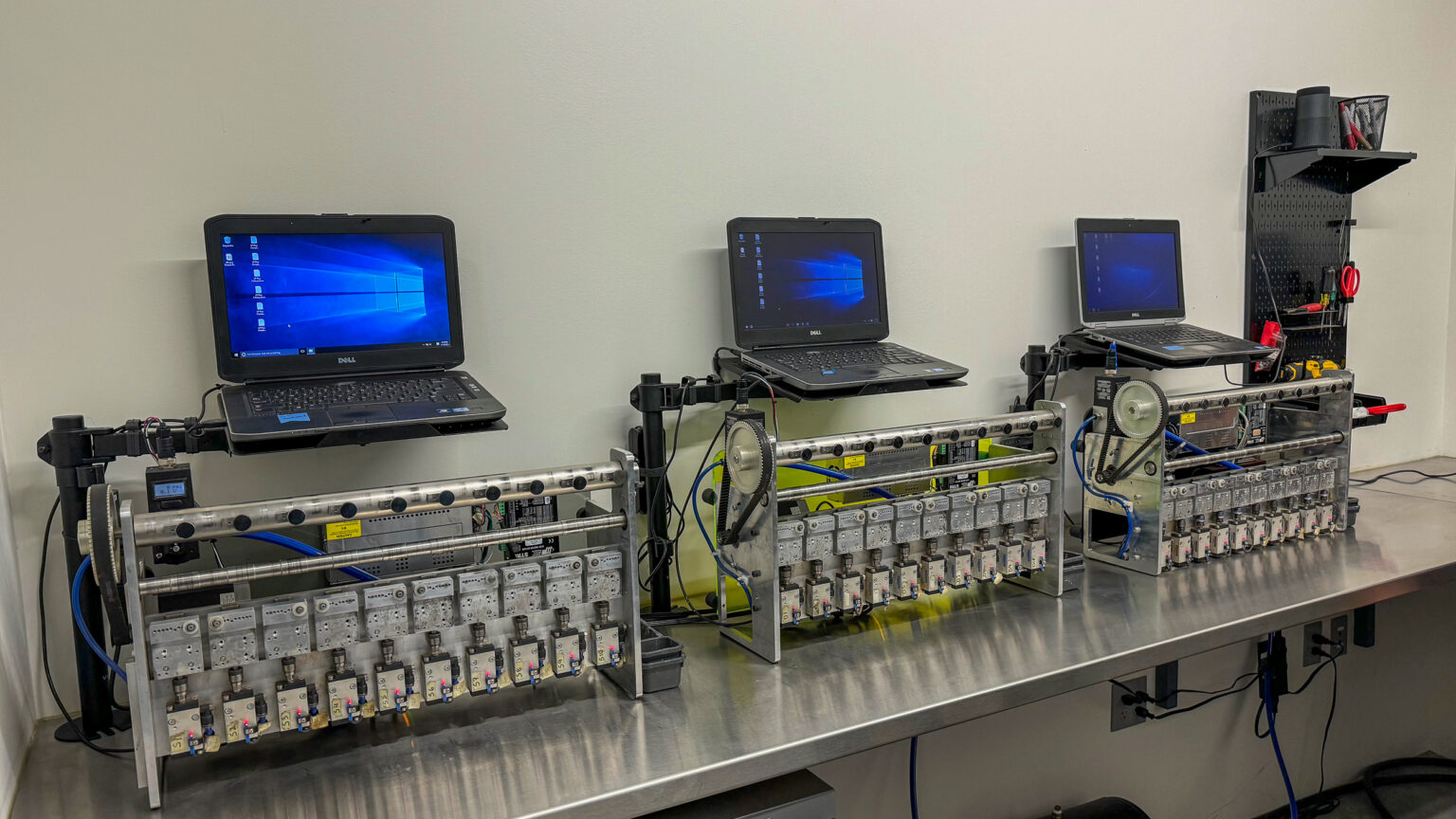
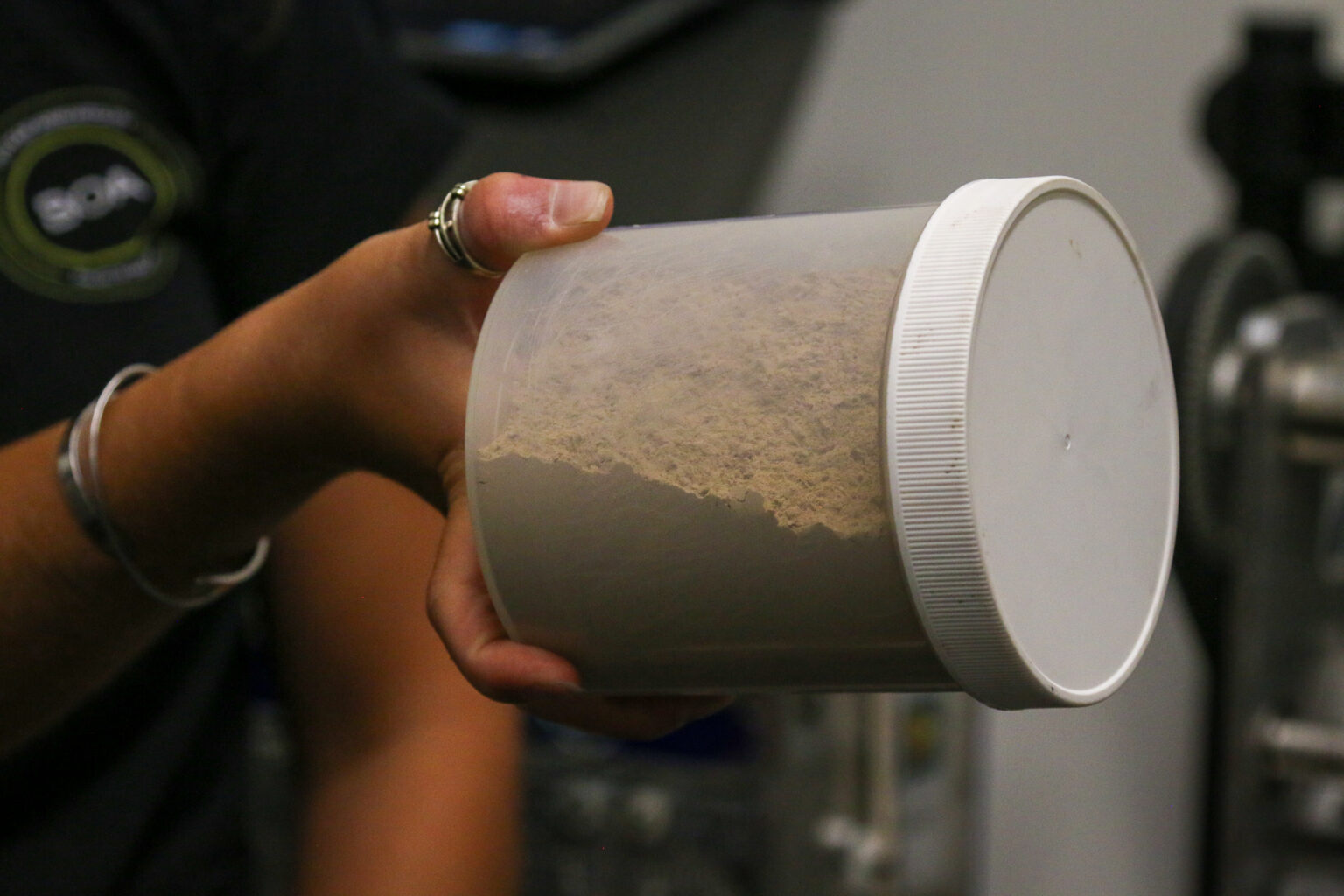
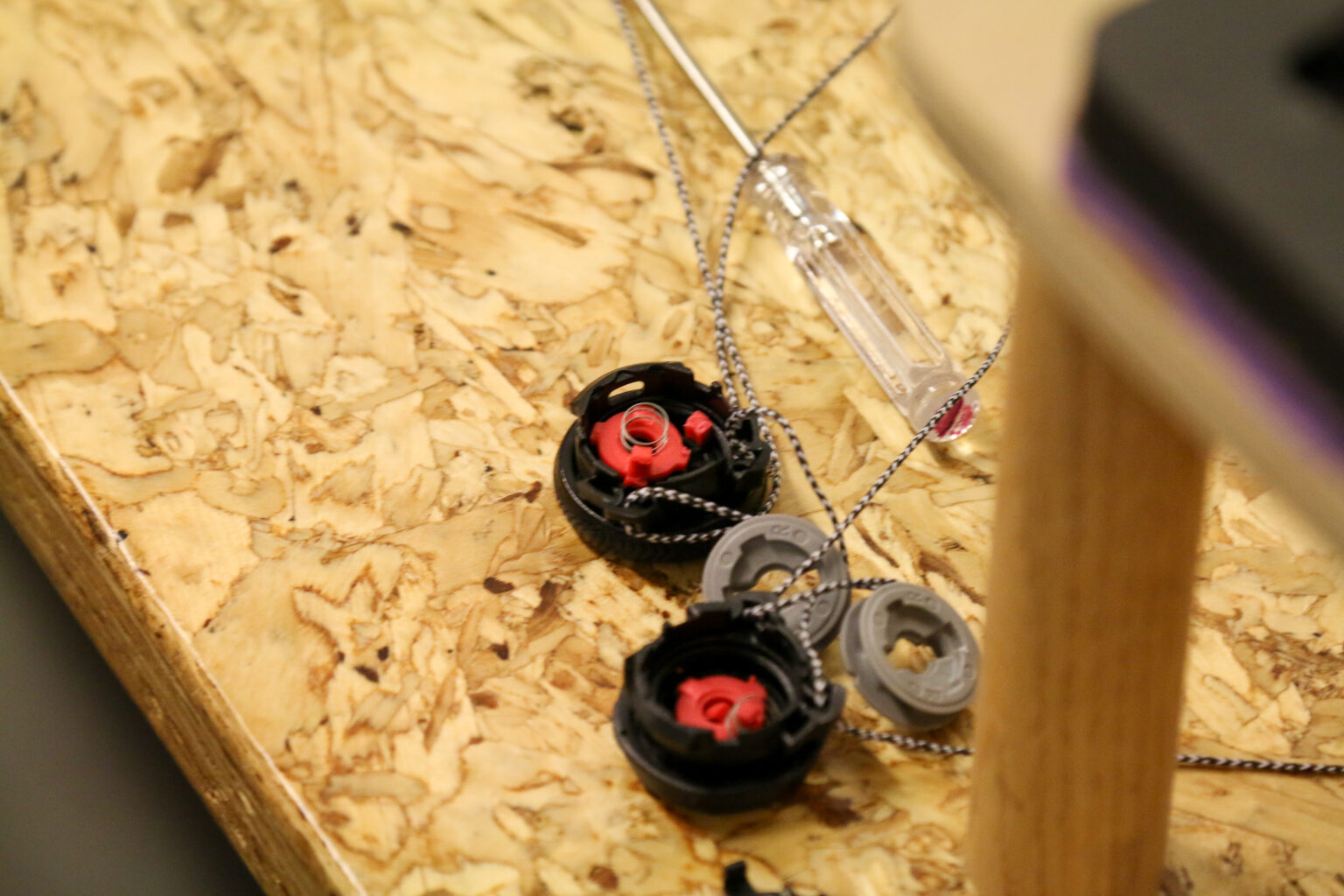
In addition to the Performance Fit Lab testing, BOA also has a full test lab on-site to ensure the dials are easily closed, opened, will last the life of the product, and shouldn’t break easily. Their test facility includes torque gauges for maximum input torques, the ‘Mr. Twister’ to test dials to failure, a ‘cartridge to bayonet’ pulling test, environmental chambers with calibrated ISO sand, and lace guide interaction tests which run until laces or guides fail.
To that effect, BOA claims to have a less than 0.5% warranty rate (which they cover with a lifetime guarantee). Their most common source of cutting warranties? That would be consumers accidentally cutting the cables when trying to remove the tags on new shoes. Oops.
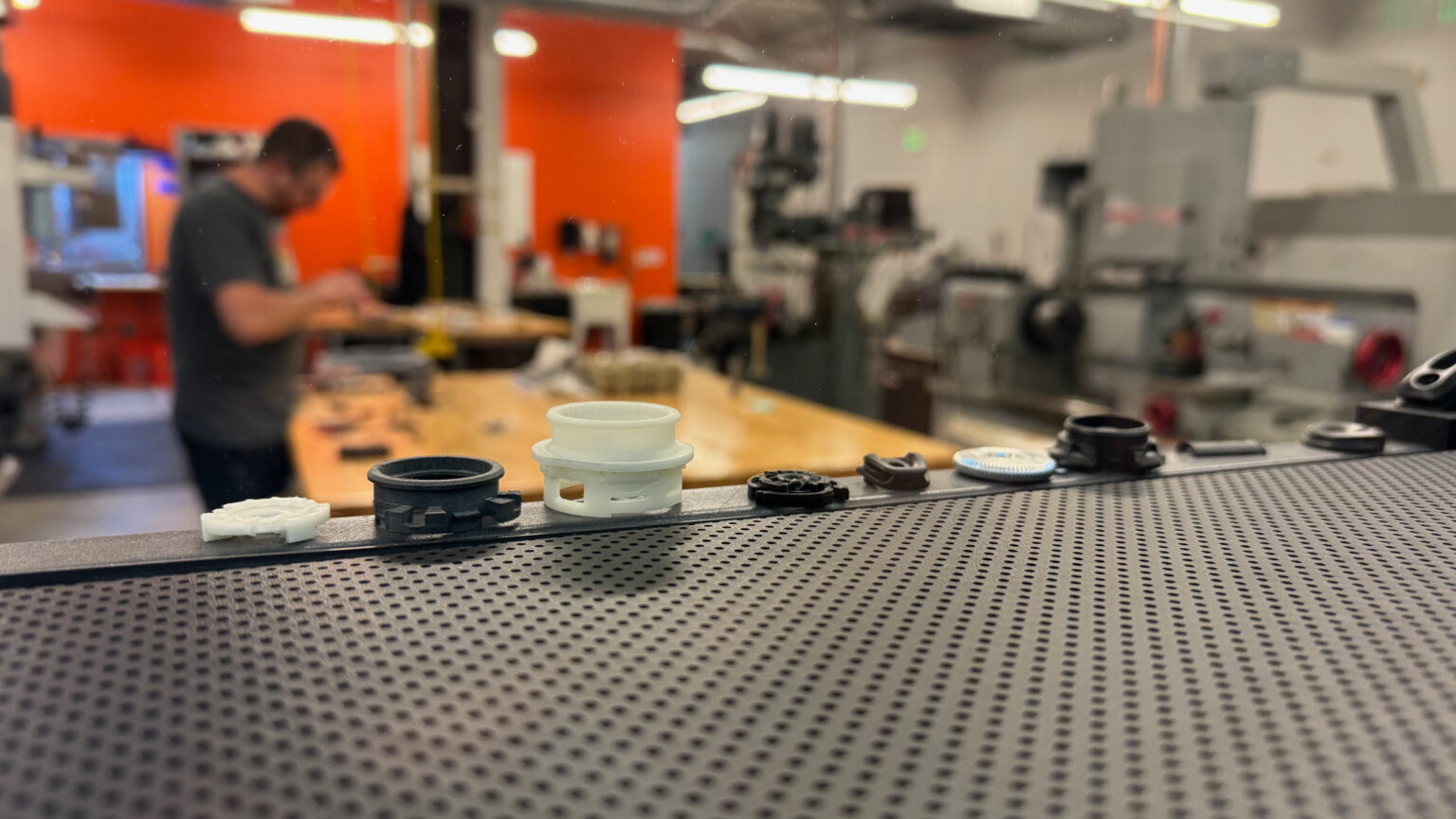
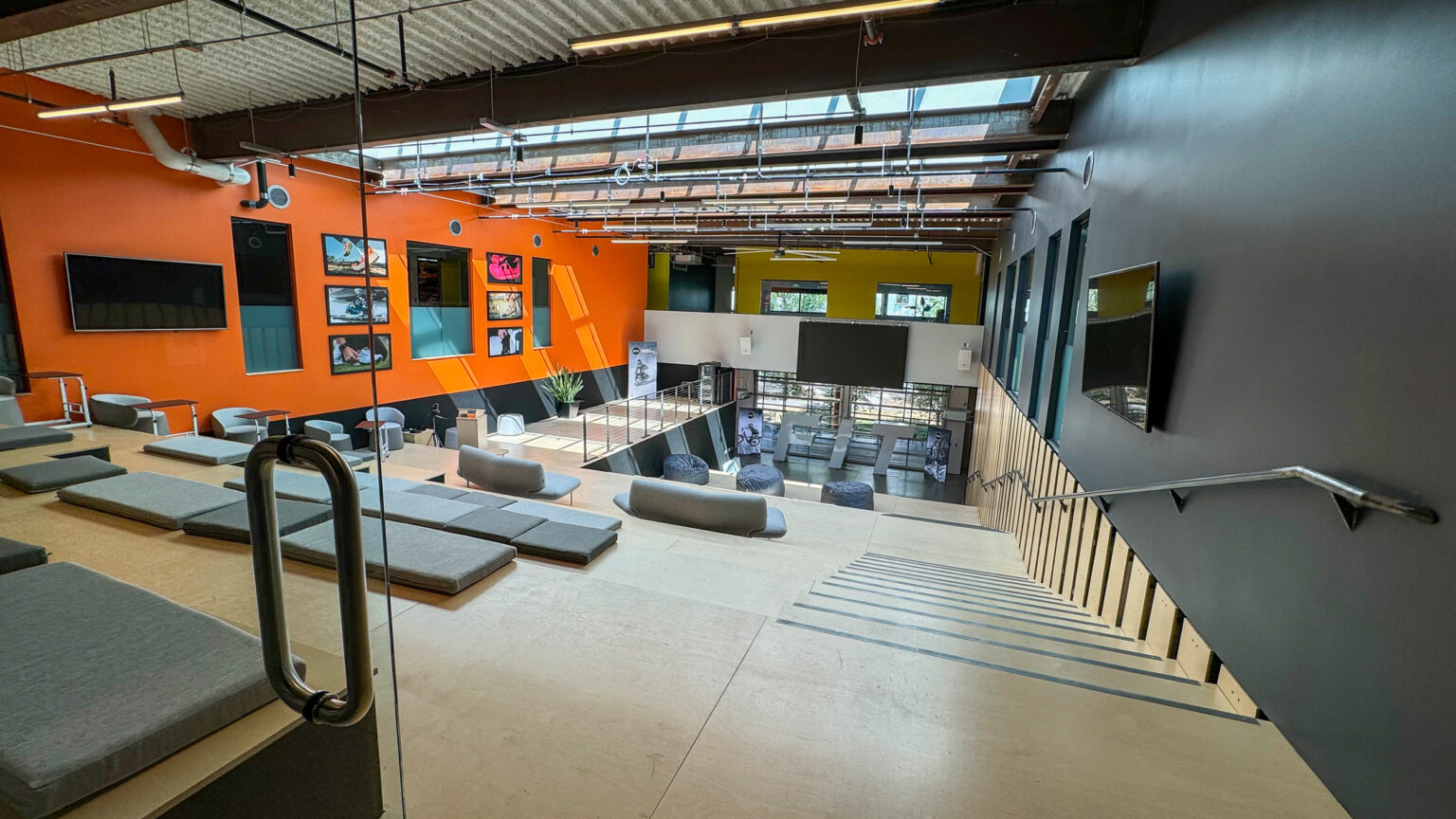
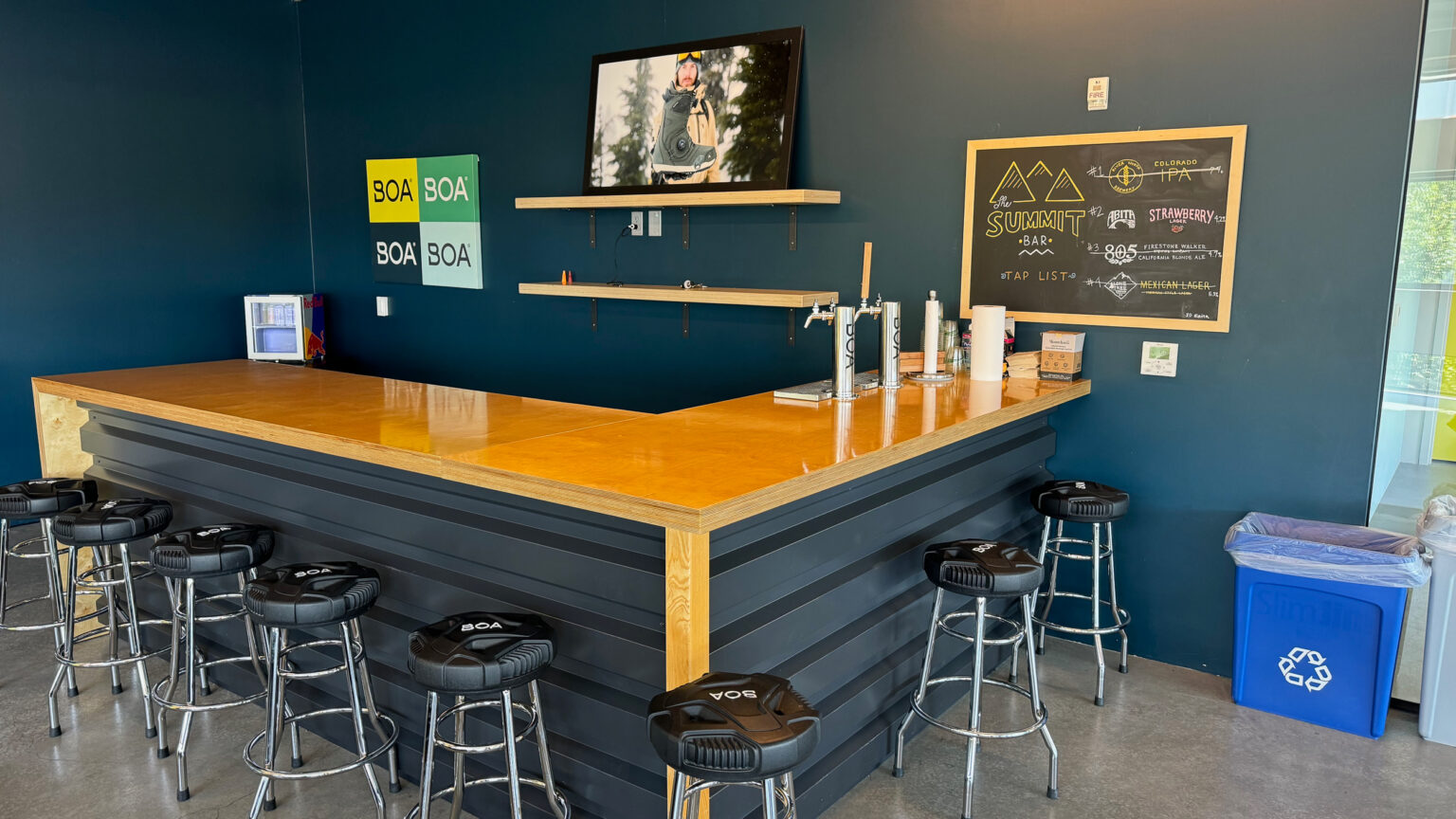
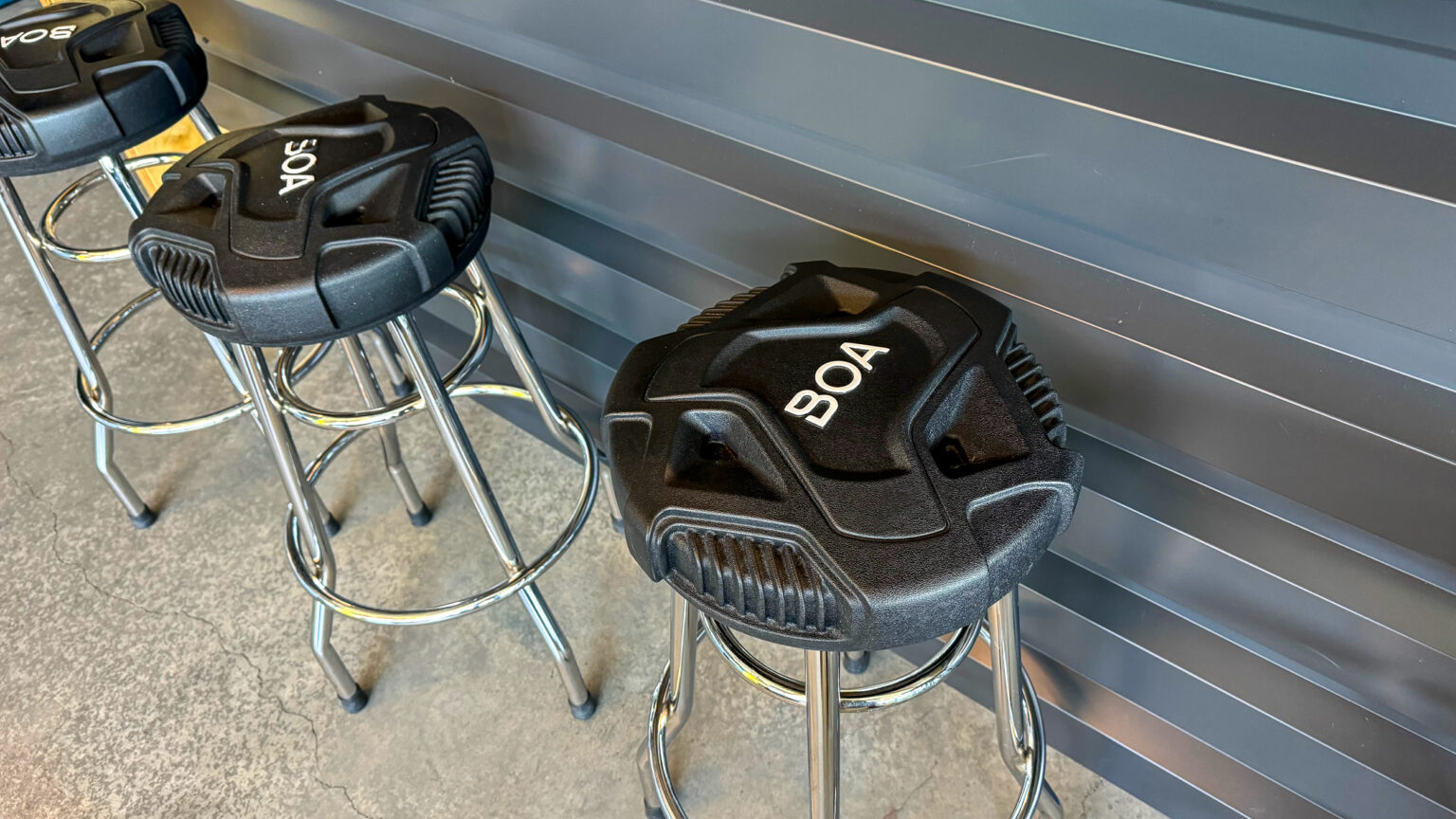
All this is to say that while it may seem like your favorite shoe brand may have just slapped a BOA dial onto their latest upper, behind the scenes there is a massive amount of testing and development that has gone into that new shoe. Now, more than ever, that testing is looking into performance benefits and not just improving the fit.
And it often starts right here, in Denver, Colorado.