CeramicSpeed has filed a patent for a “Rocker Joint Roller Chain”, adapted specifically to the needs of the modern-day bicycle drivetrain. Instead of making use of the traditional sliding surfaces of pins and bushings found within the conventional bicycle chain, CeramicSpeed’s concept chain utilizes three “rocker pins”. These literally rock against one another to produce the pivoting joint necessary for chain articulation.
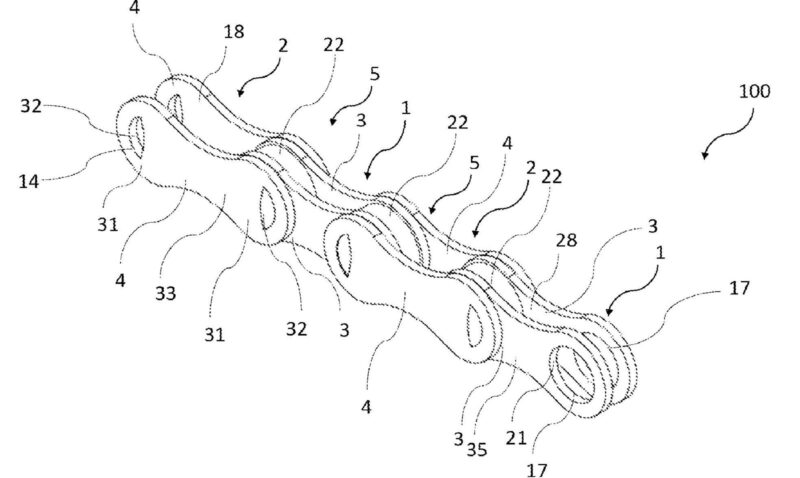
The rocker-joint chain design presented in CeramicSpeed’s patent (US 11608874 B2) does NOT look to be compatible with the cogs, cassettes, and derailleur pulleys of any production drivetrains, based on the unique variable chain pitch as the chain pins “rock” (read on for more detailed explanation). That suggests the brand may have an entirely new drivetrain under development.
We reached out to CeramicSpeed for comment who did not deny the possibility, and surprisingly give some interesting insight...
CeramicSpeed Rocker Joint Roller Chain
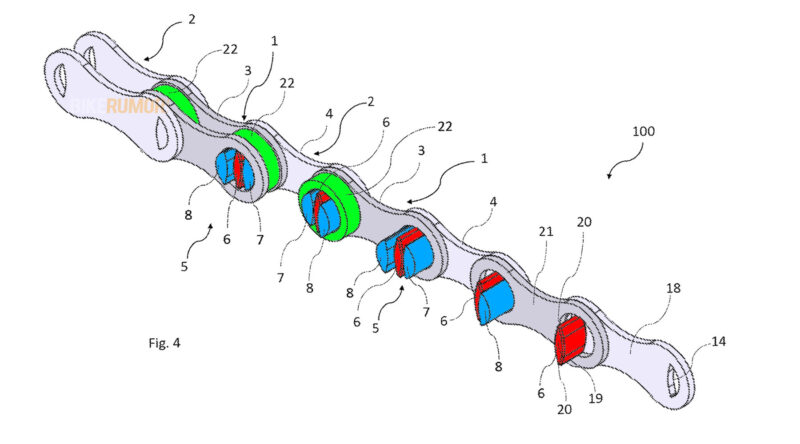
Before we get into the detail of CeramicSpeed’s patent on the Rocker Joint Roller Chain (colorized by us, above), it is pertinent to take a look at the traditional roller chain that is in use across all cycling disciplines today. What’s so wrong with it that CeramicSpeed would look to replace it with a new design?
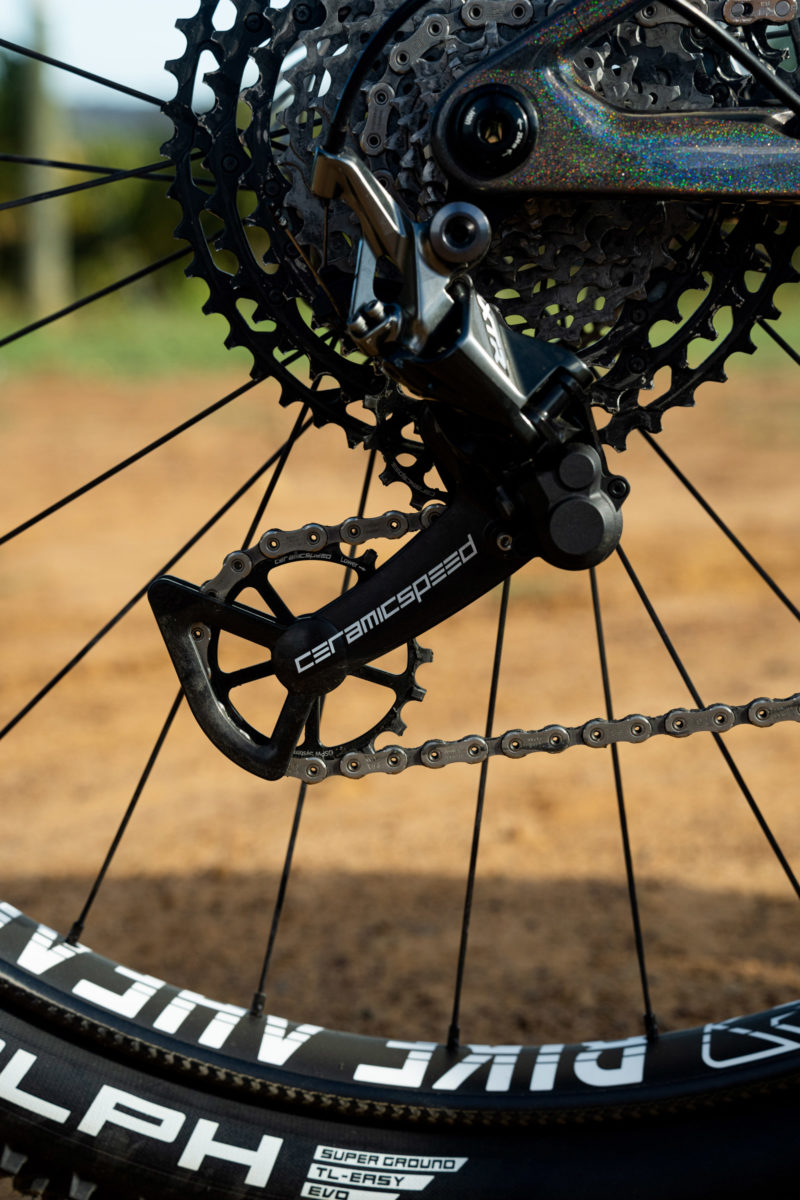
CeramicSpeed is well known for its friction-reducing drivetrain lubricants, and of course its OSPW derailleur cages. The latter, thanks to their over-sized pulley wheels, reduces the overall friction within a given drivetrain. It does that by reducing the required articulation angle between links of the chain and thus reducing the amount of sliding between the constituent components, i.e.: the pin, roller, and inner and outer plates.
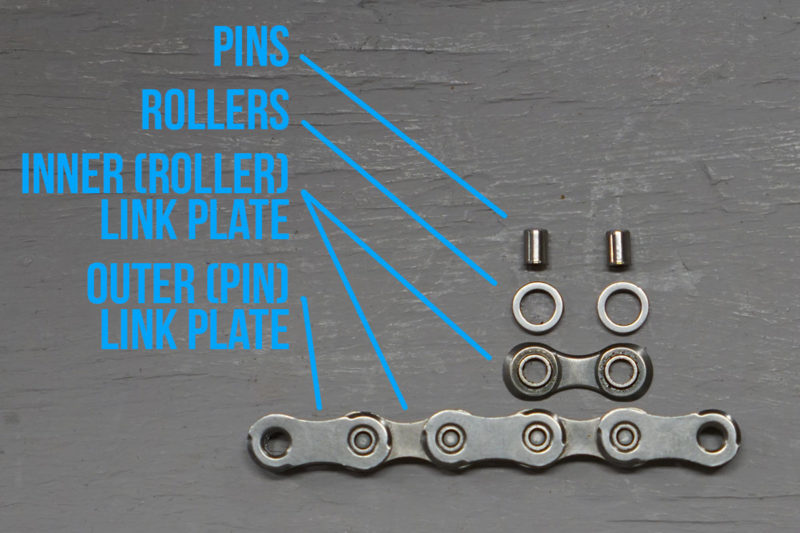
Indeed, the roller chain does generate undesirable friction thanks to those sliding surfaces – pin outer surface to roller inner surface & roller outer surfaces to inner plate inner surfaces. Increased friction equates to increased drag in the system, and that translates to the loss of precious Watts that could otherwise be dedicated to forward propulsion. The CeramicSpeed Rocker Joint Roller Chain does away with most of those sliding surfaces to create a bicycle chain that exhibits less frictional losses.
Chains that use a Rocker Joint between links are nothing new. They have seen widespread use in higher-load industrial applications, particularly in the automotive industry, but their use on bicycles has been prevented due to the fact that they do not satisfy the requirements of a modern bicycle drivetrain.
So, what are the chain requirements of a modern-day bicycle drivetrain, exactly? Beyond the chain’s primary function of transferring load, it must have the following features:
- A high degree of chain articulation for use with small cogs and pulley wheels
- Reversible chain link articulation for routing around a derailleur’s pulley wheels
- Links must be able to bend/flex laterally to work in multi-speed applications where chainline varies
- It must be sufficiently narrow, such that it doesn’t interfere with neighboring cogs of a multi-speed cassette
In order to access the low-friction benefits of a Rocker Joint chain for a multi-speed bicycle drivetrain, CeramicSpeed have come up with a new chain design that could see light of day on an all-new drivetrain. We reached out to Paul Sollenberger, Senior Product Manager at CeramicSpeed. Below is his pleasingly insightful response which, to no one’s real surprise, makes reference to reduced friction and wear.
From Paul Sollenberger, Senior Product Manager at CeramicSpeed
“This rocker chain concept that our R&D Team developed was born from our continual study of drivetrain friction and how to further reduce inefficiencies wherever possible. A traditional rollers chain doesn’t actually benefit from rolling surfaces in regards to its mechanical function. The roller rests against the tooth trough and slides against the pin and inner chain plate, which also slides against the outer chain plate”.
“We are very familiar with how various liquid or solid lubricating materials can affect efficiency and wear through these sliding surfaces. Our UFO Drip chain coating performs extremely well through various environments for keeping friction and drag to a minimum – but as long as some measurable friction is present, we know there is further room for improvement. Currently, that is between 2 and 3 Watts of friction in the best conditions. When factoring in extreme conditions of mud and contamination, that drag can also be multitudes higher”.
“Rocker-style chains are commonly used in industrial and automotive applications, and excel at transferring load with minimal added drag, as well as presenting outstanding durability due to utilization of a rocking pivot point rather than sliding pivot point”.
“Recognizing these benefits, our team took on the challenge of overcoming design limitations that prevent existing rocker-style chains from being adapted for cycling use. Primarily, the amount of chain articulation required for smaller gears/cogs, the necessity of reverse articulation (required by the guide pulley of a derailleur), varying chain line, and overall chain width confines”.
“The novel inventions on the patent from the CeramicSpeed R&D team answered these limitations to press forward on developing the most efficient drivetrain solution possible”.
Paul Sollenberger, Senior Product Manager at CeramicSpeed
“The team were able to achieve their goals and prove the concept of utilizing a rocker chain link interface within the design of a traditional derailleur drivetrain. However, the rocker chain pitch increases and decreases throughout its range of articulation and this means special cogs and gears are required to enable the adoption of this rocker chain design. Solving certain design challenges often leads to new concepts to explore. As such, we do not have any timetable to share related to a rocker style drivetrain”.
“Our R&D team continue to test various concepts that can disrupt the status quo for drivetrain efficiency and durability. We remain confident our range of UFO Products and CeramicSpeed components equipped with hand built hybrid ceramic bearings are the best solutions available today for all riders looking to get the most of their riding efforts”.
How does the CeramicSpeed Rocker Joint Roller Chain work?
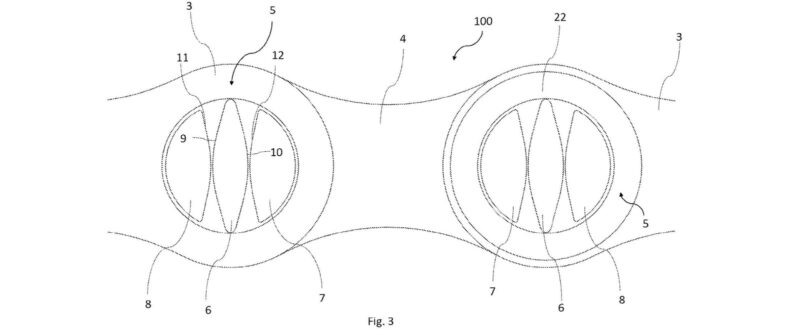
The Rocker Joint Roller Pin design centers around use of two rocker pins (7 & 8) sandwiching a “floating” center pin (6) with a roller (22) encompassing them, in an arrangement referred to as the “connecting pin assembly”. The radii of the rocker pins’ surface arc determine the maximum articulation angle between neighboring links. The patent reads as follows:
“In particular, for the bicycle chains described herein, the rolling contact angle θ of each rocker pin 7, 8 allows for twice the articulation angle of a traditional rocker-joint chain with no center pin. With this, higher articulation angles can be produced while maintaining larger radii rocker pin surface arcs, and larger radii rocker pin surfaces produce less sliding (and therefore lower wear and frictional losses) at the higher articulation angles. In some embodiments, the articulation angle θ is from −40° to +40° relative to the horizontal axis (e.g., 80° total articulation), such as from −36°and +36°.“
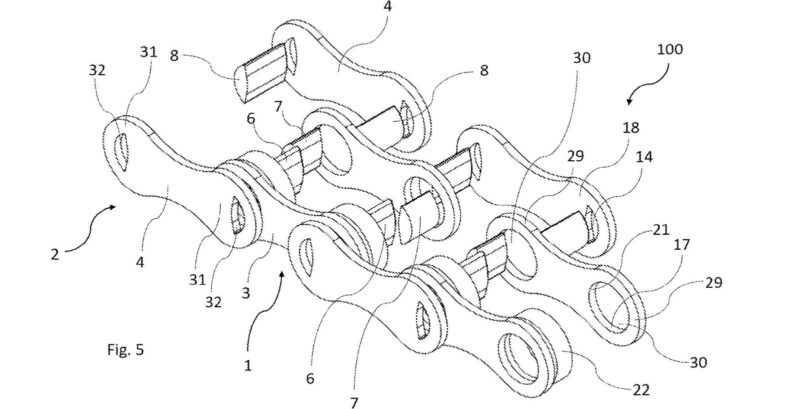
As you might imagine, multiple embodiments of the design are described. In some, one of the rocker pins is fixed to the outer plates either because it is integral to one of them, or because it is press-fitted to them. Either way, that rocker pin extends through an aperture in the inner plates. In some scenarios, the second rocker pin in the arrangement is fixed to the pair of inner plates, but the patent acknowledges that it would be more beneficial overall for the inner plates and the second rocker pin to be more loosely associated. It reads as follows:
“Additionally, the bicycle chains described herein may allow for the lateral flex of the chain. As a non-limiting example, the rocker pins may not be firmly affixed to the associated pair of inner plates, and the inner links can pivot (yaw) somewhat in relation to and at the contact point of the rocker pin in response to forced chain skew, thereby allowing an increase in the lateral chain bending ability. Alternative embodiments with alternative design elements between the inner plates and the rocker pins are provided to allow pivoting of the inner plates, ultimately providing for increased chain lateral flex.“
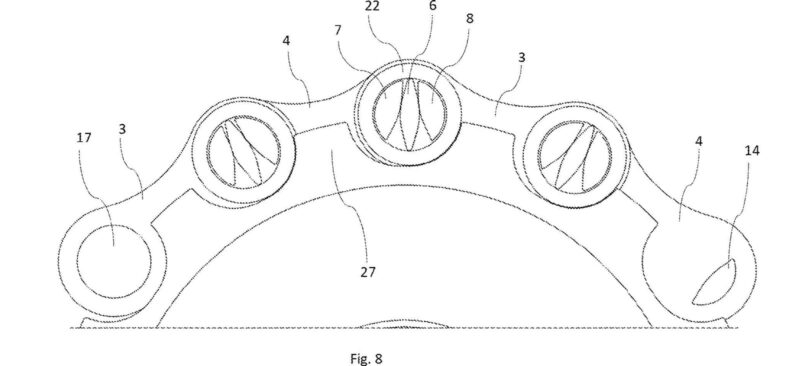
In all of the separate possible solutions, the center pin (6) that each rocker pin rocks against is described as ‘floating’. The roller (22) surrounding the whole assembly looks to be, in the very least, essential to prevent debris from accessing the rocking surfaces, and likely to help contain lubrication.
As Paul Sollenberger mentioned, the pivot design will actually result in the chain’s pitch varying slightly – dependent on the articulation angle – a feature that would prevent the use of this chain with traditional cassettes and chainrings designed for use with the regular conventional roller chain. It’s a small, but quite possibly critical difference in exact dimensions. However, the patent does include this statement on compatibility:
“The roller 22 may be utilized to allow the chain to be compatible with standard tooth profiles of modern bike sprockets”. It goes on to say, “In one non-limiting embodiment, the inner diameter of the roller 22 may be oval”.
What kind of bike would use the CeramicSpeed Rocker Joint Roller Chain?
It seems quite unlikely CeramicSpeed’s Rocker Joint Roller Chain would end up on bikes destined to go off-road. Any debris entering the space between the rocker pins and the center pin could limit articulation of the links and prevent the chain running at all consistently. It seems to us it would require ultra-clean road conditions in order to see its proposed lower friction benefits come to fruition.
But CeramicSpeed also are big lubrication nerds, so maybe they could and would design some treatment to keep debris out and give XC racers and edge too?
Regardless, it is cool to see ever more innovation in this (small) space. With CeramicSpeed’s solid history of investment in products that promote drivetrain efficiency, it seems logical that they will one day take it to the next level and attempt to design the most efficient bicycle drivetrain possible. In fact, they’ve been at it for some time – who could forget the CeramicSpeed DriveShaft?
This Rocker Joint Roller Chain may present a more palatable alternative.