Scottish brand, Deviate Cycles, is looking into a new manufacturing method for their line of high single-pivot mountain bikes. Today at Eurobike, we caught up with Deviate founders, Ben Jones and Chris Deverson, who are wandering about with a titanium-lugged carbon tube frame that is a working prototype for the brand’s first downcountry bike.
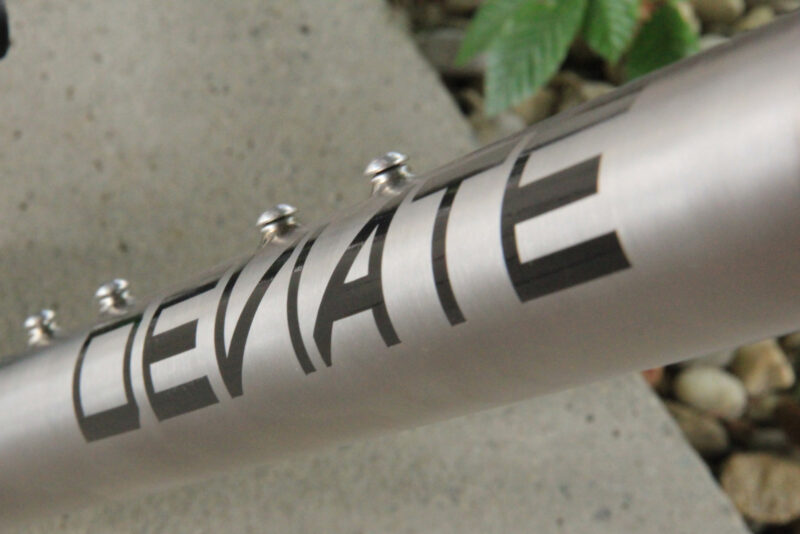
Deviate Downcountry Mountain Bike Prototype
Deviate Cycles’ downcountry prototype is part of a development series, the aim of which is to investigate the feasibility of bringing manufacture to the UK. Currently, the Claymore and Highlander bikes are constructed from an epoxy resin carbon fiber, and are manufactured in Asia – where exactly in Asia, we don’t know. But, Ben and Chris foresee a future in which their mountain bike frames are manufactured in Scotland out of 3D printed titanium lugs and recyclable nylon-based thermoplastic tubing… at a price competitive with the cost of manufacturing a full carbon frame in Asia.
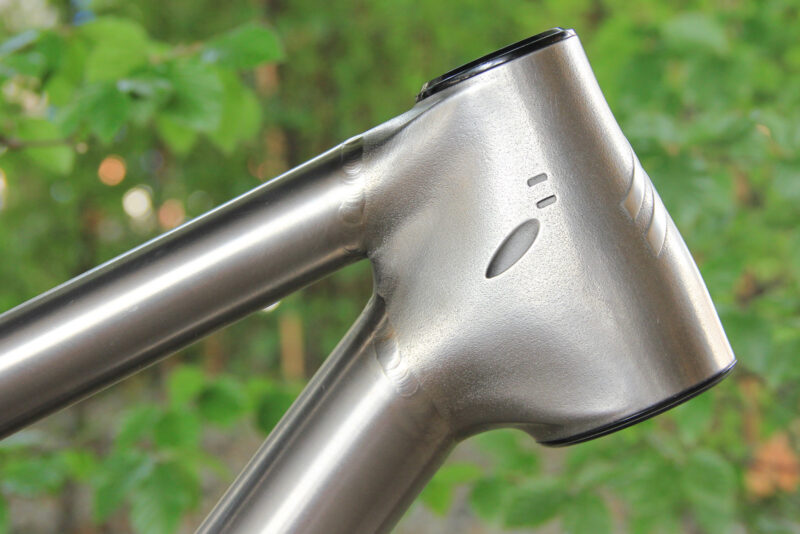
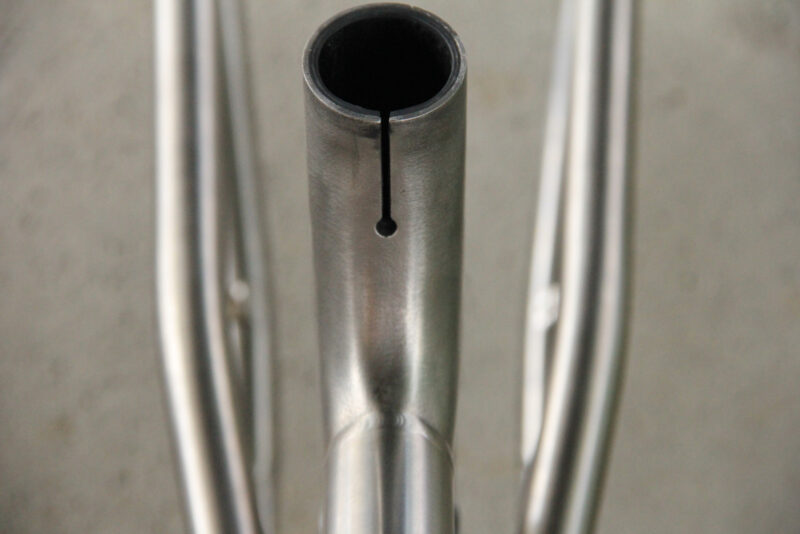
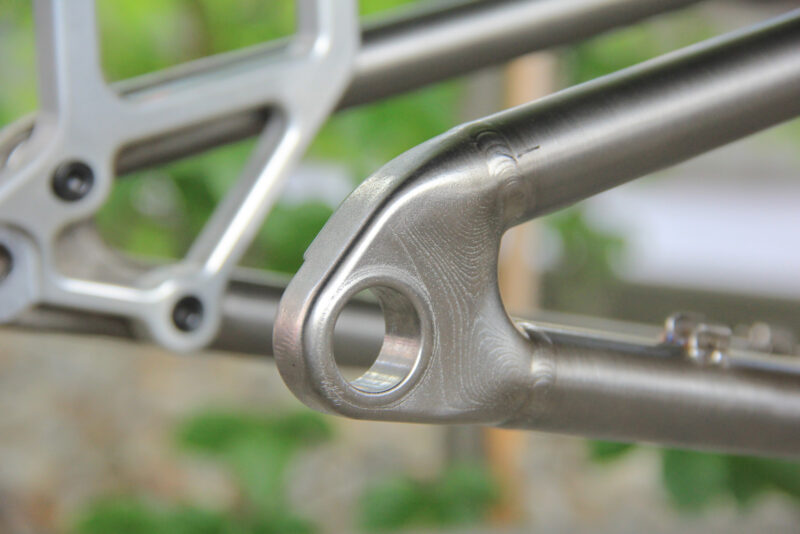
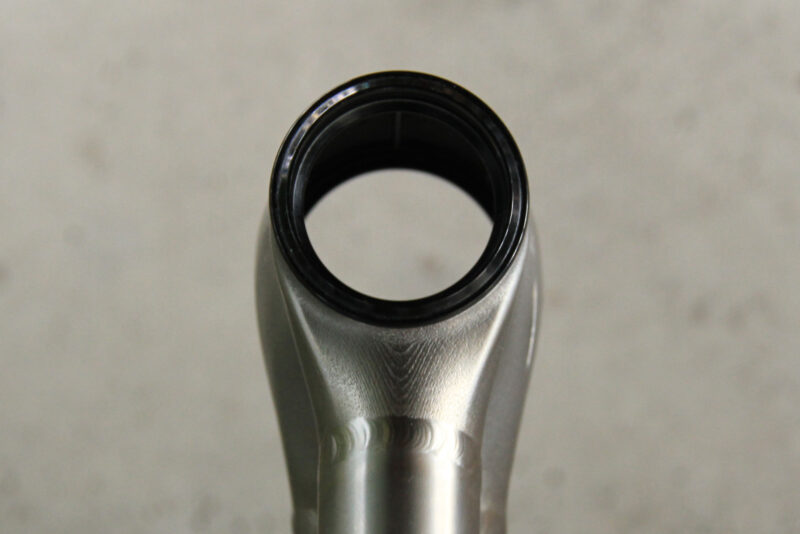
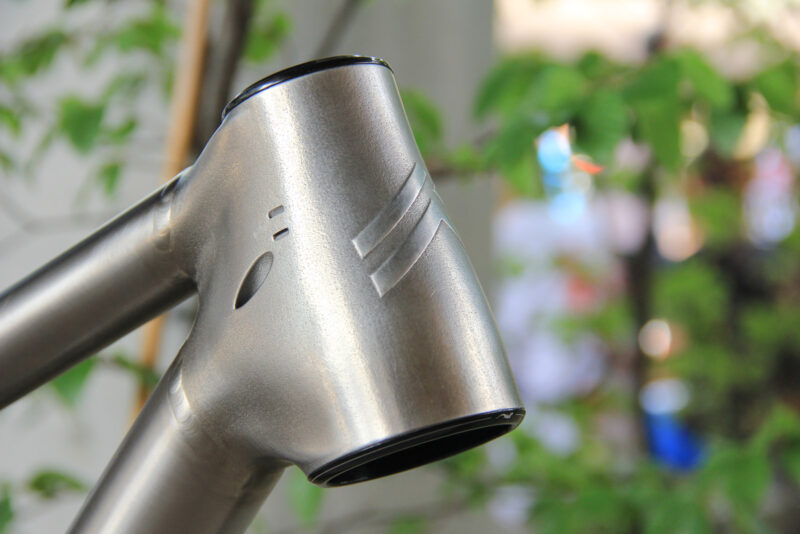
How do they propose to do this?
With the use of a more affordable method of 3D printing titanium. Indeed, cold metal fusion of titanium, as implemented by Huhn Cycles, is cheaper than the laser-sintering method employed by the million pound Renishaw machine you’d see at Atherton Bikes HQ. Apparently, the equipment necessary for cold metal fusion of the lightweight material is vastly more affordable.
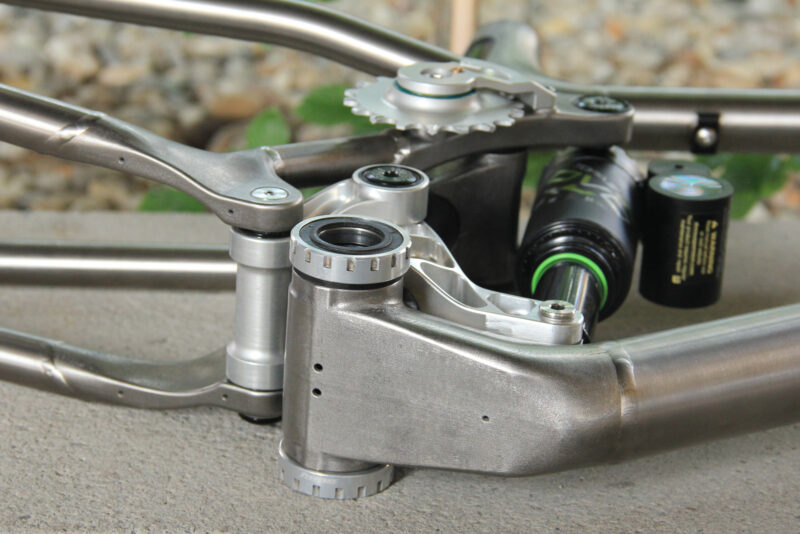
The result is a 3D printed lug that does have quite a different finish to that of the Atherton Bikes lugs. And, their production is said to require a lot less post-processing. Less post-processing means less manual labour, and thus, a reduced cost. Deviate hope to adopt this method of production while offering frames at a similar price to what they offer now. That is, around $3,200 USD for a Claymore frame and shock.
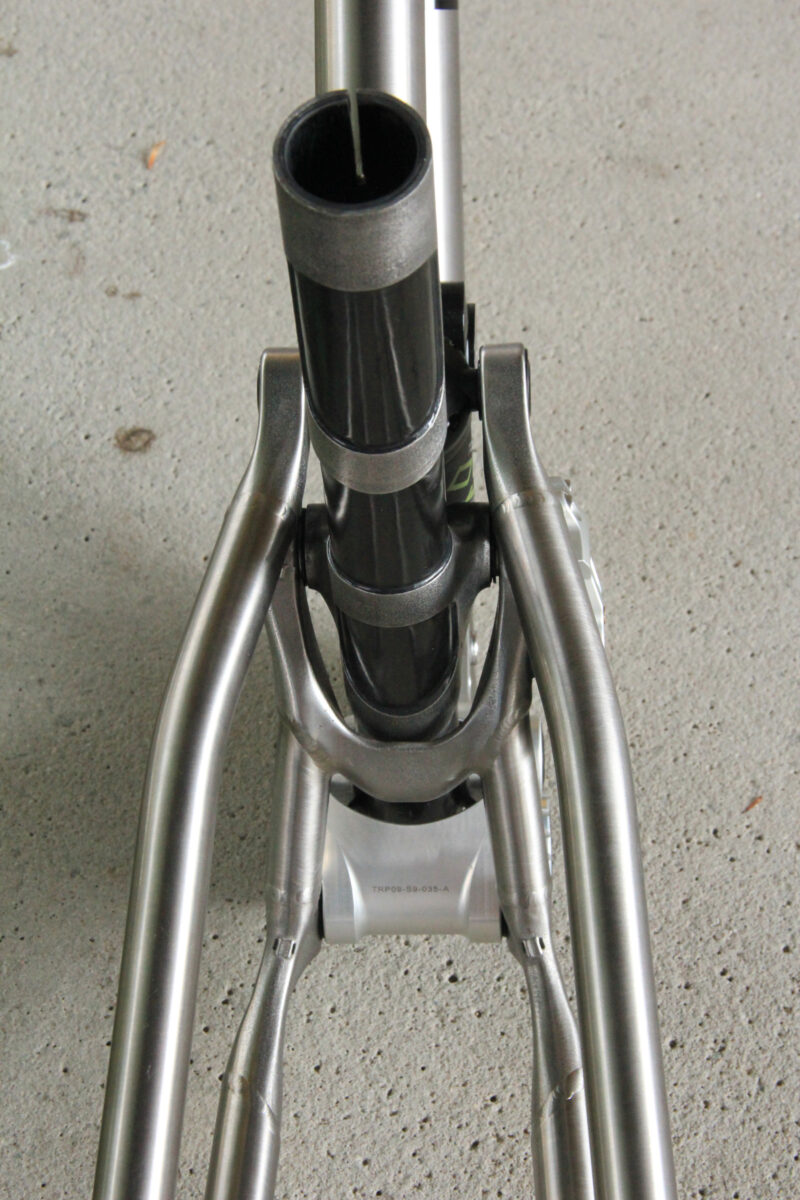
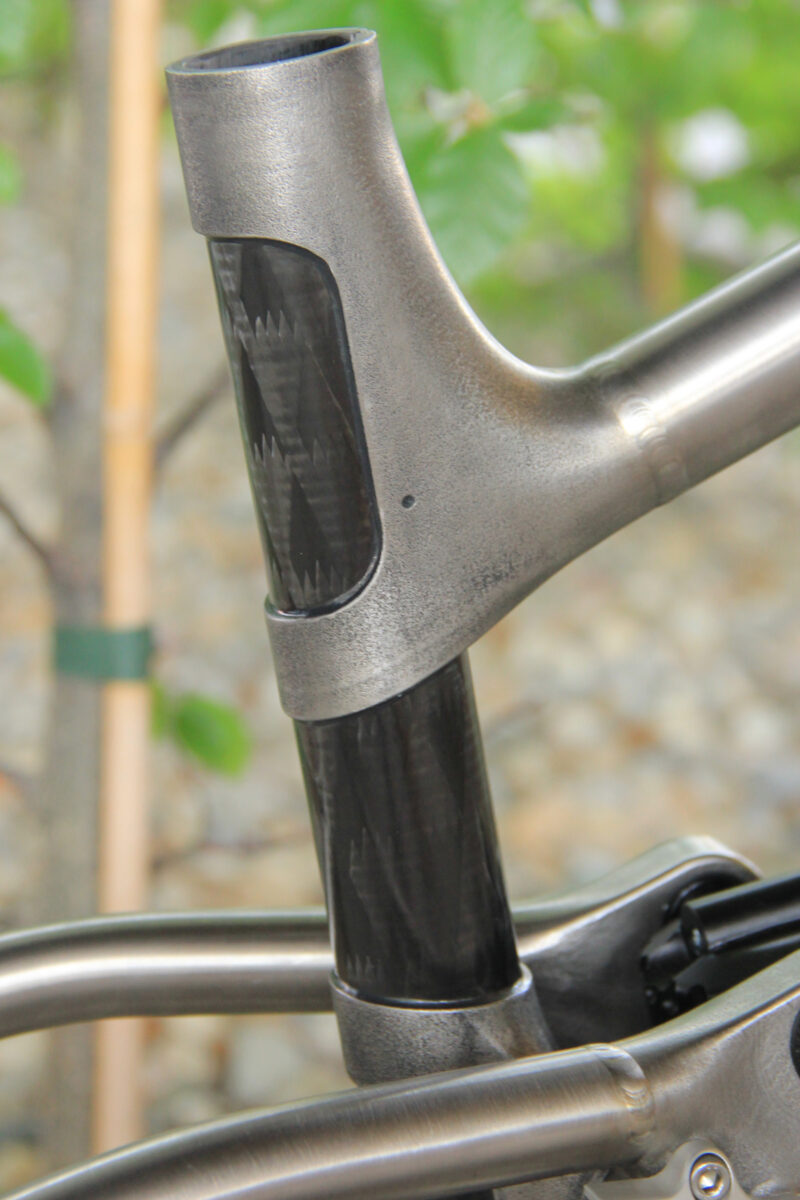
The pair admit they haven’t yet hit that point with the cost of manufacture, but they are pressing on with development because the plan is attractive for many other reasons, too; namely, the supply chain will be shortened to the point where they can make to order, and there’s the improved sustainability of it all with reduced shipping, and the end-of-life recycle-ability of most, if not all, of the frame components. Also, we are told the titanium powder used to form the lugs is carbon-neutral, too.
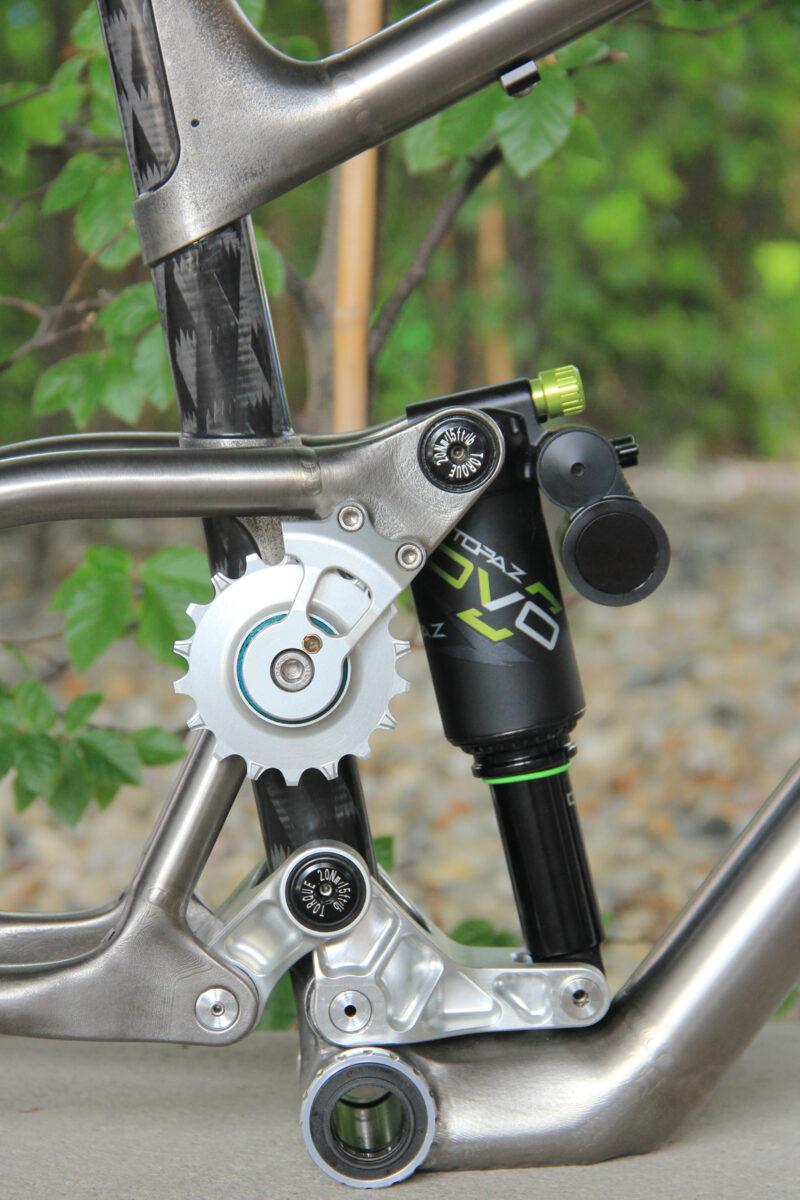
What about the linkage?
Deviate is continuing its use of a high single-pivot suspension platform that delivers a 100% rearward rear axle path, but here on the downcountry prototype it is packaged a little differently to the linkages we’ve seen from the Scottish brand previously.
Where the longer-travel Claymore and Highlander II bikes have a lower linkage positioned concentrically to the bottom bracket, this downcountry prototype keeps everything north of the BB. As the rear wheel is displaced, the lower linkage extends as the solid rear triangle moves back and upwards as it pivots about the main pivot positioned around half way up the seat tube. In this scenario, the shock is simultaneously driven from both ends as it is sandwiched by the lower rocker and the swingarm.

And, this being a high-pivot mountain bike, there is an idler pulley positioned near the main pivot to reduce the negative effects of chain growth.
We are told it could be many, many years before Deviate fully adopt this manufacturing method, and a lot will depend upon whether they can automate it to a point where the frames can be priced competitively against Asia-made carbon frames. It is currently undecided whether the Deviate downcountry bike will first materialize in titanium or complete carbon. We’ll do our best to stay tuned on this one!