There are a number of things that come to mind when thinking about Taiwanese manufacturing in the bicycle industry. On the small island you’ll find every level of producer making complete bikes right down to the individual bolt. Much of the production is similar to what you would find in the US with companies getting a number of different parts from their suppliers and then assembling the final product on their own factory floor.
Then there are companies like VP Components. Where raw materials are swallowed up by the gargantuan facility only to be spit out as finished goods. VP may be a relatively new name to the US market on the consumer side, but if you’ve ridden bikes for any amount of time you have probably used their products without even knowing it. Situated as one of the largest suppliers of OEM headsets in the world, VP is also one of the last producers of high quality, inexpensive square taper bottom brackets. Oh, they played a big roll in the development of reliable methods to mass produce the ISIS BB standard in Taiwan as well.
All of the buildings on VP’s campus work together in harmony to fulfill VP’s specialty of one stop production. Their customers receive completely finished and packaged products that are ready for the store shelves, or to be assembled into bikes. Capable of producing up to a half million items in a single month, bottom brackets, headsets, and pedals all roll out of the facility on a regular basis. And yes, they have their own BMX track….
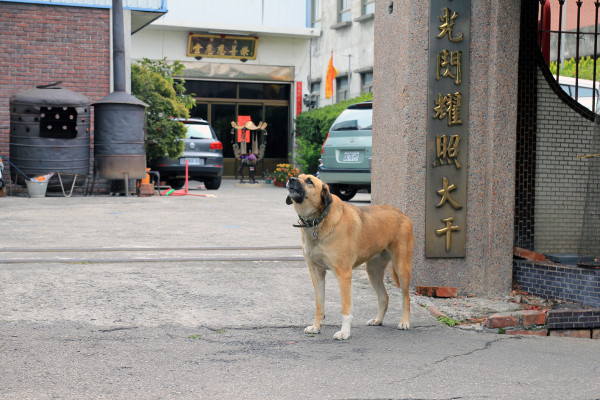
Located just outside of Dajia in Taiwan, the VP campus is an ever expanding mix of industrial buildings on the outskirts of town. VP is currently constructing two completely new buildings to house their new offices and their own extrusion plant. The green structure will be their new office building while the other building is longer to house the extrusion machines. If all goes according to plan, the building will be pumping out extrusions by the end of the year.
VP also has a hub division called Modus that was started 6 years ago. Also specializing in OEM hubs, VP initially purchased a factory in Japan and moved it to China for continued production. Now, Modus has a new factory here in Taiwan that is focusing on the high end of their business.
VP makes a lot of products and the list is ever increasing. Now that the company has their sights set on aftermarket sales in addition to OEM, they’re going to need a bigger cabinet.
A common sight among manufacturing floors, examples of many of their products are hung on the wall for employees to use as a reference.
Most of the assembling is done by hand in numbers as little as 20 to as many as 50,000 units. Above, workers assemble basic pedals which are then shrink wrapped for OEM packaging. Operating off the JIT (Just In Time) principle, everything is made to order including packaging which is tailored to the individual customer.
Key to many of the VP designs is the extensive use of complex machining. Even with warehouses full of CNC machines, this 5 axis is important enough to be given its own room. Apparently requiring defense department clearance to purchase, the 5 Axis is capable of incredibly intricate machining all without having to reposition to the work. Machining with fewer axis machines adds time and complexity to the process, incurring extra cost and increasing the chance for error. On this machine though, simply place the piece of aluminum into the chamber, and out comes the finished piece.
Just how capable is the 5 Axis? When we asked if VP used 3D printers for the prototyping phase, we were told that they used to but have been using them less and less. The reason? Apparently they can machine a fully functional prototype in aluminum in the same amount of time as it would take a 3D printer to make a model.
While the 5 axis is the star, VP has rows and rows of 3 and 4 axis machines that do the bulk of the work. In order for pedals to be durable in the long run, precise dimensions for the bearing bores are critical. This is where the multi axis machines really shine since they ensure perfect accuracy. Aluminum headset cups are another part that requires exact tolerances which VP proudly pointed out that they are able to use a single machine while competitors must use two.
Over the past 5 years, VP has been working to integrate as much automation into production as possible. Instead of technicians for every machine, now workers load raw materials into trays for the robotic arms to process. Automated machines are programed to grab each piece of work from a tray, load it into the machine, complete the machining operation, and then deposit it back into the tray and move onto the next. Technicians simply need to make sure the machine has plenty of material to work with and then periodically check the output to make sure it is running smoothly.
Technicians are capable of operating up to 8 machines at a time, with separate technicians to perform QC checks. That also means caring for the machines themselves, which is very important when some machines run more than $300,000 a piece. Maintenance means lubrication illustrated by the lube station above. Just don’t mistake the pitchers for drinks…
Just as we’ve seen in many factories, every area has its own QC station.
One of the big costs of production is tooling up to produce the actual fixtures that hold the work in the machine. VP makes all of their own tooling which increases accuracy and decreases time for production. As tooling is used they do get worn out, so having their own tooling department allows production to continue running smoothly.
Injection molded parts might not have the same appeal as a beautifully CNC machined pedal, but the technique is an easy and efficient way to make a high strength part. In addition to making high quality parts, VP is also on a mission to make sure that even cheaper pedals look good. It may seem fairly simple on the surface, but injection molding is more than just filling a mold with plastic. The process requires expansive knowledge of different materials, flow of materials into the mold, how to make a mold, and how to make material flow into mold smoothly without air pockets.
As one of the fastest growing segments of VP’s business, VP sees injection molding as a technology that can be used to make make higher and higher quality parts. Many parts that used to require CNC machining, VP feels they can be replaced with injection molded parts in the future as they add new machines like the Arberg 720. Because of the machine’s abilities, parts can be molded with much higher pressure and stronger, heavier tools.
VP is using injection molding to create products out of a number of different materials including Polypropylene, TPE, and even carbon fiber in strands up to 12mm long. Advanced production methods like co-molding and in-molding allow pedals with an aluminum body, polypropylene cage, and TPE lugs to be created in a single mold.
Nowhere was the raw material in, finished product out mantra more visible than in the room with the heavy machinery. One stop production means stamping, forging, pressing, die casting, finishing with stone grinding, heat treating, injection molding, CNC machining, painting and packaging all happen under one (collective) roof.
If you’ve ever been curious what forging looked like, these towering machines are used to forge axles for bottom brackets, pedals, and bottom bracket cups. Here machines also turn flat plate steel from rolls into future headset pieces. Between the size of the machines, the heat, and the noise, this building was overwhelming.
It’s hard to imagine the amount of force needed to turn these little pucks into bottom bracket cups, but we’re glad they do. The result is inexpensive bottom brackets that still use steel cups – something I always appreciated as a mechanic.
If it’s not forged, injection molded, or CNC machined, there is a good chance casting played a role. Here, aluminum ingots are melted down in massive underground furnaces and poured into molds. When the parts are finished and cooled, the sprue are trimmed and recycled.
Any parts needing hardening are also heat treated on site as well. About as long as two buses end to end, the heat treating oven is a huge contraption both above and underground. Parts including axles, nuts, bolts, spacers and cleats receive either T4 or T6 heat treating.
Across the street, hubs are manufactured in another building devoted to Modus. When VP bought the company they started from scratch on the hub design on all of the thru axle products. Now, they are able to offer almost unlimited options to their customer thanks to the interchangeable architecture of the hubs. Just like the VP products, everything except anodizing is done in house for Modus.
Parts destined for a shine end up in one of the several stone polishing tumblers. Water mixed with polishing stones take raw parts to a near mirror finish, while hand polishing is used for a few products for a perfect finish.
Products that aren’t polished either end up painted or anodized. Out of all the processes done in house, anodizing is the only one VP sends out. The painting is done in house however, with two full paint lines running through the factory. Products travel on a conveyer system with hooks to the paint booth where they’re finished, then sent off to cure in large racks.
Air and water quality is very important to VP, and it shows. Understanding that their employees live in the area surrounding the factory, VP has been aiming for high levels of environmental standards and certifications. Products like the VP-R73 have already been given green certifications with more on the way. Air and water are the two main environmental concerns so the factory has a huge air filtration system to keep the air inside and outside clean. The same goes for water, with any water used for production cleaned and purified before it leaves the factory.
Certainly very different than some of the more touristy cities in Taiwan, Dajia seems to provide a great home to VP’s employees as the view from the top of VP’s dormitory would suggest.
One of the big benefits to producing everything on site is that production is never far away from their testing facility. Here VP is able to test for failures, adhere to standards, and investigate any problems with the products and make changes quickly for production. Most of the testing for VP is done to EN or JIS standards for the European or Japanese markets, though all of the products are tested to VP’s own internal standards which are considerably higher.
Chock full of measuring devices, the QC lab is where issues with current products or future designs are worked out. Look around and you’ll see a Universal Material Tester, Microview, CMM, and more.
In addition to fatigue and cycle testing, the QC lab includes a deep freeze for testing products at extreme temperatures, a salt spray tester, and other machines to test the durability of finishes. The salt spray machine comes in handy when testing chrome plating, though VP seems to have a handle on that – they own their own CP factory in Changhua. The majority of the chrome plating isn’t for the bike industry though, since over 60% of the factory’s CP business is for IKEA.
Just as impressive as their production facility, VP also has their own BMX track, dirt jumps, and short XC trails which are open to the public. Built as a way to bring cycling to the local people, the venue plays host to events where locals can learn to ride on a fleet of demo bikes. Considering Taiwan is where a large portion of cycling products is born, cycling for fun is less popular than you would expect. Thanks to the efforts of companies like VP though, it won’t be long until the little rippers tearing around the track have something to say about that.