The word Gamut means broad or far reaching, and judging from the Gamut’s presence at all levels of racing, it’s easy to imagine they’re a large corporation. Yet despite the polished website and big name sponsored athletes, Gamut is actually a small, rider-owned company.
Their idea for a better chain guide came about because Co-Founder Juan Graziosi wanted a lighter & more reliable solution for racing. Working in conjunction with his father Ed Graziosi, a machinist, they fabricated a working prototype in their garage. The idea would have likely ended there, but soon friends and fellow racers wanted guides as well, and selling the home made components quickly became a way for Juan to offset the cost of racing. The project began to look like a viable business venture when older brother Mateo and riding buddy Michael Poutre joined to to help crank up production and craft a business plan.
Today, Gamut continues to produce a large quantity of their products in the garage where Juan and his father created their first chain guide. Learn more about the process after the break…
This is the Gamut garage. The Graziosi brothers grew up calling it home, and each of the tools here has a story attached to it.
All of the of equipment were slowly assembled during the course of Ed’s career as a machinist. Meticulously maintained and carefully modified, the well cared for machinery still churns out new components every day.
The first stage in the process is cutting the raw materials. When Gamut was first starting out, the boys had to be frugal, and would order large sheets of material. These would then be cut down to the size required to fit inside the CNC machine.
After Juan nearly lost a finger to the table saw, the fledgling business decided it was far safer to purchase precut sheets.
The raw materials are then fed into a three axis CNC machine.
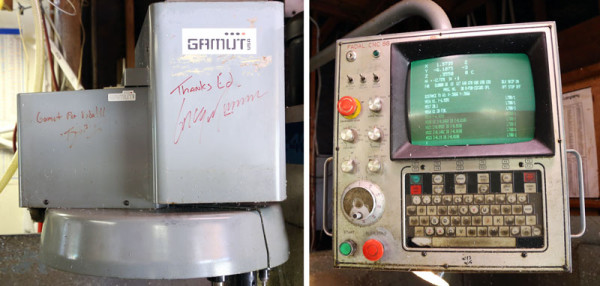
The mill was built in the mid 80s and was acquired by Ed when his employer was running low on funds. In order to continue his work, he offered to purchase the machine and rent it back at an hourly rate. When Ed left the company, he took the machine home with the intention of using it for miscellaneous side projects, and (more importantly) to make components for his Alfa Romeo track car.
For the home tinkerer, this machine is a dream come true, but it’s a bit slower than more modern machines. It also requires a manual operation.
So when Gamut received it’s first big OE order, and all of the co-founders still had full time work obligations, they were forced to take turns tending the machine throughout the night for weeks in order to meet their shipping deadlines.
Fresh from the CNC machine, the components are cleaned and double checked for quality.
Before they could afford to outsource the most manually intensive tasks, the group would find ways of building every component in house with their existing machinery.
One of the most labor intensive was converting set screws into the hardware needed for roller assemblies. It was at minimum a two step process and the most arduous part was converting the the hex heads from American to Metric. This was done with a manual broaching tool, which works by slamming a die into the head of the bolt. It’s a physically demanding process that caused more heated arguments than any other part of the business whenever others suspected someone wasn’t doing their fair share.
Across from the house is an empty plot of city owned land where the boys started shredding.
These youthful forays inspired a life long passion for bikes and racing, both of which seem to have deep roots in their family history.
In the 193os, Juan and Matteo’s grandfather Eduard Sr. was riding and and racing motorcycles in Buenos Aries.
Grandpa could also flat corner a bicycle!
Co-Founder and family patriarch Ed also has a passion for racing – of a four wheeled variety.
During the early years when Gamut was growing steadily, but not quite enough to finance a warehouse, his track car was forced to live in the driveway under a tarp.
Gamut’s early success with chain guides also funded other experiments. At a time when the average trail bikes weighed more than current DH bikes, Juan was fixated on building the lightest bikes possible.
This aluminum rotor was a project from almost ten years ago, which was quickly sidelined. While the rotor was incredibly light, it also folded shortly into the parking lot testing phase.
As one of their Skunk Works projects, they also developed a drop in damper for the 2006-2008 era Boxxer forks. This generation RockShox fork had a reputation for spiking, so Gamut collaborated with local racer Evan Turpen to create a better system.
Their damper was aimed at the racer looking for the utmost in customization and performance but it’s lack of external adjustments limited its appeal.
They tested the product with some success, but because each damper was essentially a one-off, it was too time consuming and expensive to manufacturer. In the end, they never made more than a half dozen, and none of the founders could agree upon how many they actually sold.
Just a short drive from the garage is the new office. The back houses a spacious warehouse, while the front has a meeting room and assembly area.
Here the guides receive finally assembly…
are tagged…
…and then bagged.
Finished product is stored in the warehouse area, where spare parts and complete guides await shipping.
The walls throughout the office feature signed posters from friends and athletes.
And an entire wall is filled with jerseys bearing messages of support.
While there, we were able to see a series of new products that are in development. In addition to their ever expanding line of drivetrain and retention components, Gamut is also developing a line of stems and handlebars – which are named after the street the brothers grew up on.
Also in development is a direct mount stem. As you can see from these two prototypes, the stem has gone through a variety of different iterations in order to find the proper balance between stiffness and weight.
Both the DM and trail stems should be available by end of year and will retail for $109.99.
A matching handlebar is also close to final production.
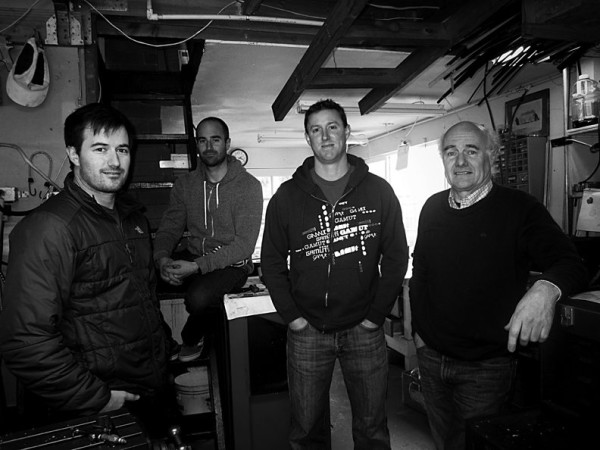
Gamut continues to produce a wide range of products in their garage, and their home machine shop will continue to be an integral part of their R&D and prototyping phases. What else does the future hold for the small company? We can’t say for sure, but if their beautiful new stems and recent acquisition of Point One Racing are any indicators, the company’s future is bright.