It’s been just about 23 years since paired spoke technology was first licensed by prolific inventor Rolf Dietrich. Since then, an incredible amount of technology has changed when it comes to the humble bicycle. Batteries are everywhere, carbon fiber is common place, and every marginal gain is celebrated as the next best thing. In spite of that, Rolf Prima is still doing their thing – albeit under new ownership and under a new roof. While 2018 sees the introduction of a new brand for Rolf Prima which focuses on traditionally spoked wheels, it only seems to strengthen the brand’s resolve when it comes to building top shelf, paired spoke wheels. By hand. And predominantly in the U.S.
Before Rolf Prima was ever in Eugene or a thing for that matter, the brand started as a license to Trek for the paired spoke technology along with a few other patents, which lasted from 1996-2001. After their agreement ended, Dietrich wanted to start his own company in Northern Ohio. While this was taking place, Brian Roddy and two other product managers who used to work at Trek and had worked with Dietrich, relocated to Oregon to work for Burly in 1999. As fate would have it, Dietrich would end up contacting Roddy and the two other engineers in 2002 about getting the band back together so to speak. It was 3 vs. 1 on where to locate the business, and nothing against Ohio, but Oregon won out. Rolf Prima was born.
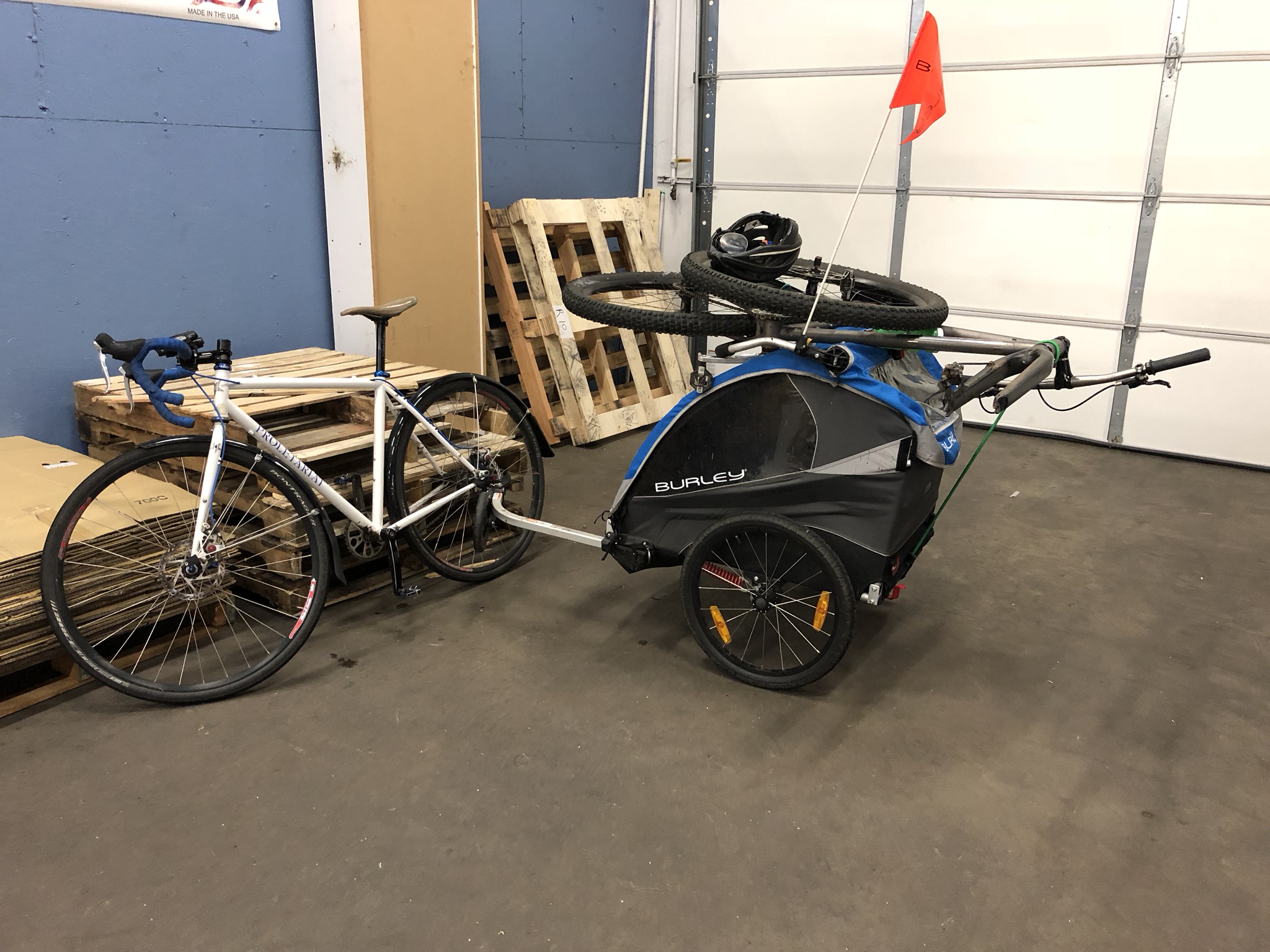
Dietrich continued to be actively involved until his retirement in 2009, at which point Brian and his business partner Steve Cash bought out the company. That brings us to today, where Rolf Prima is just getting comfortable in their newest location which was purchased about three years ago. Located in the heart of a small industrial park on the west side of Eugene, Oregon, Brian and his team are just a short drive from some of the best riding in the county (just don’t crash on the lava rocks, trust me) – and as evidenced by the amount of employee bikes inside, riding is a way of life.
As you walk in through the front door, Rolf Prima has a similar feel to many bicycle brands. The small space is homey, yet well decorated and serves as part meeting room, showroom, office complex, lunch room, and locker room to prep for rides. It’s nice enough that you sort of forget that there’s an entire manufacturing facility beyond the next door.
But first, as you walk through that door you enter the wheel building studio. It’s here that the wheels get laced, tensioned, and trued by hand, but also stickered, checked, and boxed.
At one point, someone in the comment section called Rolf Prima nothing but “sticker slapping monkeys”. And while it’s true that they do apply decals to their wheels, there’s a whole lot more going on here than just applying stickers. To show that they have a healthy sense of humor about it though, their actual sticker slapping monkey watches over their work.
This is also where their hubs get assembled, using hub shells that are made in the U.S. from 6061 aluminum which offers high resistance to stress, corrosion, and cracking. Most Rolf Prima hubs use a larger non-drive side flange in the rear which is part of the Paired Spoke patent. Rolf Prima claims that the Differential Flange Diameter effectively increases the number of pulling spokes resulting in a stronger wheel.
As part of the building process, Rolf Prima Wheels are still put through a mechanical stressor which they say can drop the tension of a wheel by 50% on the first pass. The process makes sure everything is seated before final tensioning, which ensures a perfect wheel that shouldn’t need to be trued after the first few rides.
Step deeper into the home of Rolf Prima and there’s no mistaking the factory portion of the building. Back here it’s loud. Safety glasses are required. And raw metal extrusions are turned into rims.
Rolling
For their aluminum rims, each starts life as a nearly 14 foot long aluminum extrusion that comes from Arizona. Brian points out that just the raw material is about the same price as a finished rim out of Asia, but they feel it’s important to build their own here. While the extrusion sets the rim profile, the roller and the custom dies set the roundness, and the final cut on the saw sets the diameter. According to Brian, producing a round rim is the easy part – it’s that last 3% required to produce the perfectly round and properly sized rim that is so difficult. If the rim isn’t round and flat to start with, it’s pointless to continue.
After a full redesign of the process by their Manufacturing Engineer Willy Reen a year ago, their process is better than ever which has helped cut costs, increase production, and enable projects like Astral.
Cutting
Once the extrusion is rolled, the resulting coil is placed into a saw that cuts off the ends and cuts the two rims at the seam. As mentioned, this step is critical in making a rims that is the proper diameter as you have to account for the saw kerf and the material removed during facing. Cut rims are sent out for heat treating as the extrusions are only rolled in T4 conditions. When they’re back from heat treat, the rims are in T10 condition.
Joining
The next step is to join the two side of the rim with a sleeve joint. When it comes to rim joinery, there are three options – pins, sleeves, and welding (sometimes a combination of two). Rolf Prima views sleeving and welding as the top options and while Brian will tell you that there are great welded rims out there, they prefer the sleeving method. And Brian was quick to point out that it’s not because they can’t weld the rims. As he walked over to show me their complete welding set up which is currently shrink wrapped on pallets, he explained that when you weld a rim, you still have to sleeve it and you end up adding a ton of heat to a very small section of the rim. Their claim is that heat then makes that the weakest part of the rim, while a sleeved joint that isn’t welded becomes the strongest part of the rim.
With that said, sleeving is not that simple. Rolf Prima has a whole process complete with its own training program to make sure any employee is fully versed on the ins and outs of cleaning the rim, applying the epoxy, and bonding the two sides together.
It’s important to note that the epoxy is purely for silence, and not structural. The sleeve is big enough that when the rim is pressed together it forms a structural joint. The epoxy just ensures that years down the line the sleeve won’t start to make noises while you’re riding. When the rim is finished, the valve will be opposite of the sleeve which helps balance out the weight difference.
Brake Tracks
Rim brakes may be slowly disappearing, but Rolf Prima (and Astral) still make plenty of rim brake wheels. Another area where Rolf Prima prides themselves, the brake tracks on each side of the rim are machined at the same time. That ensures that the two sides are perfectly parallel to prevent brake shudder.
Drilling
From there a series of machines and drills are used to drill out the spoke and valve holes in the rim. Their computer automated spoke drilling machine was actually built in house – and can clearly drill both paired and traditional spoke patterns as well as tangential or angled, aluminum or carbon. Unlike the bigger machine, this smaller drill can drill both the access hole and the spoke hole at the same time.
The big red machine above is used to drill Rolf Prima rims which use internal nipples. The machine drills two nipple access holes, then two spoke holes, turns the rim, and continues to drill until finished.
Finishing
All of that moving around and clamping the rims into various machines results in traffic – or wear marks on the surface of the rim. The rims are then tumbled and buffed with scotch bright and polished to make sure they’re nice and shiny before heading out for anodizing. This step isn’t really necessary and is apparently often overlooked on less expensive rims, but again Rolf Prima wants to create the best product possible, which includes ensuring the best finish. Both anodizing and ceramic coating of their rims and hubs are done locally, which is what allows Rolf Prima to offer custom builds for customers.
Engineering and Testing
To become a complete wheel and end up on the Rolf Prima or Astral catalog, rims end up here in the Engineering and testing lab.
The room also houses a number of reference wheels like their 10/12 spoke TDF TT85s.
On the engineering side of the lab, there are a number of devices and tools that have been developed by Rolf Prima Engineers from spoke tension meter calibration units to a lateral stiffness tester, spoke pull through tester, and more.
On the other side of the wall is where the more, uh, destructive engineering takes place. In addition to a UCI impact test rig, Rolf Prima employs their own impact test which uses more weight, and a solid, curved anvil with the tire on the rim. The UCI version uses the rubber block shown above without a tire and 40 Joules, while Rolf Prima’s spans from 50-110 Joules.
Then there’s the fatigue test unit which was built in partnership with Michigan Tech. The tester simulates speeds up to 47 mph, with a 150lb load on a single wheel. Based on the ISO standard Rolf Prima again kicks it up a notch with three times the speed for increased impact. The test will run until failure, though there are sensors to detect if the tires get a flat. If a flat is detected, the rim is pulled upwards to prevent it from being prematurely destroyed. On each drum, two 1cm bumps impact the rim and tire every time it goes around. During the process, engineer Joel Wilson uses a microscope to take pictures of every spoke node every 100 minutes of testing to find if and when cracks begin to propagate and how.
The test rig is also capable of preforming brake track heat testing which Rolf Prima credits for vastly improving their own resin and layups for carbon rims. While some carbon rims are made overseas, Rolf Prima’s high end carbon rims are made in Washington through a joint collaboration with an unspecified aircraft company.
Final Build
For wheels that get the green light, it’s back to the assembly room to be built by hand. Every Rolf Prima wheel gets the hands on treatment, with decals as the finishing touch.
The end result is a beautiful, high performance wheel that in many cases is completely built in the USA. Thanks to almost doubling their catalog with Astral by Rolf Prima, that’s something they don’t plan to change any time soon.