Looking back, it’s almost hard to believe that Pivot has been around for less than 10 years. After a surprise launch at Interbike in 2007, in the words of founder Chris Cocalis, the brand has seen hugely exponential growth in a very short period of time. Compared to two other brands launched that very same year (Tomac and Corsair Bikes), Pivot has manufactured their own success through extremely tight tolerances.
Of course, that’s no accident. Pivot is far from Chris’ first venture into the bike business. While many may know Cocalis from Titus, his roots go even deeper back to the days of the Sun Eagle Bicycle Works Talon. Founded by Allen Vaughn in 1988 after he created an off road trailer, he would later focus on frames which led to the Talon mountain bike with elevated stays. After Vaughn taught Cocalis to braze, Sun Eagle Talon #2 (above) was born which was made by Allen with some help from Chris. Vaughn would only make around 20 of the frames, but it was enough to be named one of the “Bikes of the future” in 1988 by Mountain Bike Action.
Little did everyone know that Cocalis really would go on to create his own bikes of the future…
Looking positively archaic by today’s standards, the Sun Eagle Talon was one of the bikes in 1988. Including features such as a built-in Hite Rite tab (the original dropper post), Zefal pump tabs, and elevated chain stays, the frame design was drawn up on paper and then built out of PATCO 4130 tubing that was shaped with a Home Depot tubing bender. Looking back fondly on those days, Chris chuckles as he remembers how many tubes he went through to get each radius just right and the amount of work to cut all of the tubing with nothing more than hand files and tin snips. Of maybe 20 that were ever built, this is the only one Chris has left which is bittersweet since he was taken out by a car while riding the bike in 87/88. It apparently never rode the same after that.
After starting Titus Bikes in 1989, it was incorporated in 1990 and grown until 2001 when Chris merged the company with Viatech Composites. A smaller but still competitive alternative to Easton at the time, Titus worked with Viatech on the carbon front triangle and Titus provided the aluminum rear end. At the time Viatech was responsible for a lot of composites construction including the carbon legs for Amp forks, but due to a series of poor business decisions Viatech eventually ran out of capital and Chris wasn’t able to buy Titus back from the company. In 2006 Chris was bought out of Titus and then took a year off while working with the parent company of Fork Ups.
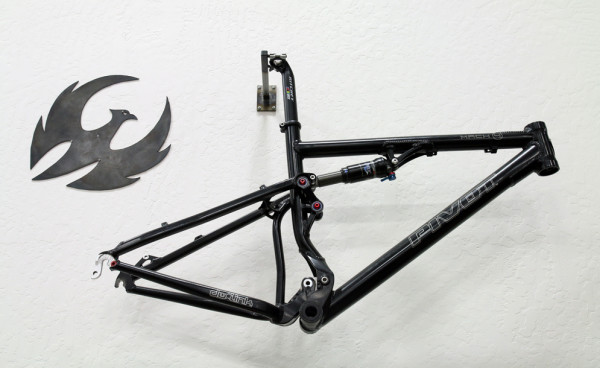
After regrouping and the initial launch at Interbike, Pivot bikes rolled out to the world in 2008. Pivot #1 still hangs on the wall in the machine shop which was assembled with tubing cut completely with snips and a die grinder harking back to the days of Sun Eagle. That first bike took 3 months to dial in, but today Chris thinks he could do in in about an hour. Cocalis points out half jokingly, half lamentingly that Pivot started with the Mach 4 and Mach 5 which used one wheel size, one triple crankset, one front derailleur, and came in your choice of black or blue. Compare that to today with 13 different models, multiple wheel sizes, and 6-7 build options per bike. And those numbers continue to increase rapidly.
One of the few constants through the Pivot line is the use of a PF92 bottom bracket (everything except for the cross and fat bike) which Pivot co-designed with Shimano. Cocalis is quick to point out that the pressfit bottom bracket is a solid design – the issues in the industry arise from poor quality control and sloppy tolerances which are both things that clearly drive Chris wild. If there is one thing you pick up on after touring the facility, it is how dedicated Chris is to maintaining the tightest tolerances throughout the entire process. Factory in Asia is struggling with alignment? Chris bought the exact frame table and brought it in house to perfect the process. Hardware isn’t meeting spec? Make it in house. Down to physically teaching their frame builders how to properly weld the frames, each Pivot is painstakingly created to Cocalis’ exacting standards.
All Pivots start with a concept where Chris will play with the basic design and layout. After he’s happy with the idea, the design will then be sent to Dave Weagle for the DW Link pivot placement based on rider size, wheel size, etc. From there three engineers at Pivot will finalize the rest of the frame and begin the prototyping process which is all done in house. Sometimes the design process doesn’t pan out as expected like the Phoenix Carbon DH bike that started with a two wheel size concept. Through the prototyping and R&D, the choice was made to stick with 27.5″ wheels only – though Pivot’s sponsored athletes are given exceptions. Since very few of us need to be able to backflip a 70 foot canyon gap at the Redbull Rampage, 26″ dropouts for the Phoenix are pro-only.
Manufacturing all of the prototypes in aluminum, Cocalis points out that all of the aluminum prototypes are made to carbon standards with the same stiffness and very similar weights. However, these one-off prototypes take a huge amount of machining time to produce and therefore aren’t able to be produced on a large scale which is one of the advantages to carbon. Above, the aluminum prototype of the Mach 6 Carbon sits next to the production carbon bike.
Sometimes bikes can take up to 5 rounds of prototyping with each prototype estimated at 200-300 hours of machining time according to production manager Bill Kibler. Individual parts like the bottom bracket assembly above can take 5-6 hours or more to machine and are usually machined in two or more pieces then welded together. The production quality on pieces like these is nothing short of impressive.
With a full machine shop at their disposal, Pivot goes through a lot of aluminum. Like any good machine shop, Pivot manufactures most of their own fixtures including pro-style customized work stands for their employees.
The shop also turns out its own hardware for certain instances using machinery like the broach above.
Other hardware Pivot has developed include pieces like these suspension pivot inserts which were designed to keep from rotating in the carbon, but still allow perfect alignment in the molds.
Just like any bike company, sometimes something pops up on a bike after it’s already in production that leads to further development. That was case with the “Lawwill Link” which got its name after Joe Lawwill. A Master’s World Champion and current MTB Marketing Specialist at Shimano, Lawwill knows his way around a bike and is also a big guy that as Cocalis puts it, “thunders through corners.” After voicing his opinion that he felt the rear of the bike flexing under hard cornering, Pivot created a new link that was quite a bit stiffer. After a string of prototypes, the final forged link is at least 25% stiffer but does come with a small weight penalty. Lawwill links will be available as an aftermarket item for any Mach 6 carbon in the future.
No stranger to developing their own processes to obtain the desired result with a bit of a MacGyver flair, Pivot has gone as far as using toaster ovens to cure rubber molds or a propane grill to anneal aluminum (apparently when combined with the Arizona summer heat the grill’s temperature is sufficient).
After owning his own machine shop and working with Chris on Titus bikes, Kibler was convinced to come work for Pivot where he oversees the incredible machining. ‘Old Man Kibler’ is also a bit of a tinkerer as it turns out, evidenced by this custom built “street quad” sitting in the parking lot which is the answer to – “what do you get when you cross the body of a Honda Pacific Coast motorcycle, a custom trellis frame, Miata suspension, and wheels from a car?”
Over on the other side of the prototyping facility lies the welding station along with the exact frame table you will find in Pivot’s Asian factories. The area also houses one of the first carbon frame molds for display and testing jigs for frame stiffness and other measurements. Pivot performs their own stiffness testing in house since it turns out to be quicker and easier for them to do it themselves, but they partner with a test lab in California for other proprietary testing. Many of the processes that Pivot uses to ensure perfect tolerances of their frames are trade secrets but we can tell you that they involves lasers and 1:1 blue prints. While we aren’t allowed to show you some of the proprietary the tools, seeing them in person left us feeling confident in the final product.
Over the years Pivot has also become a firm believer in the use of 3D printing for prototyping needs, especially since they machine parts for the manufacturer of their printer. In a bizarre arrangement, Pivot machines parts for the company that makes printers that can make many of their own parts. Someday 3D printers will just print other printers in a never ending cycle.
The sum of all of the different parts equals the printer that was on display but Pivot is in the process of helping to create a much larger printer that they hope will be able to print an entire front triangle. This will be a huge improvement over ordering ABS models like the hard tail above which are extremely heavy, fragile, and very expensive. It’s hard to tell from the picture, but that base for the new printer leaning up against the wall is about 2.5-3′ in diameter. Compare that to the base of the current printer on the table which is no more than a foot wide and you get start to get an impression of just how big the new printer will be.
Operating for the first 5 years in a 7,000 square foot building, Pivot recently moved to their current space which was quite an upgrade at 27,000 square feet. Even so, they’re already almost out of space. Which brings up an interesting point – I wasn’t quite sure what to expect at Pivot’s Tempe, AZ headquarters. As with most of the big players in the bike industry the majority of Pivot’s bikes are made overseas so what would we find inside? A surprising amount, actually (including the Cocalis family’s new puppy).
In addition to all of the design, engineering, prototyping, and machining, all Pivot bikes are assembled, packaged, and shipped from the warehouse. Bulk storage is housed in the warehouse next door from which parts are pulled to stock the cage over by the builders’ work benches. This warehouse also serves as storage for the demo fleet, vehicles, even the photo studio.
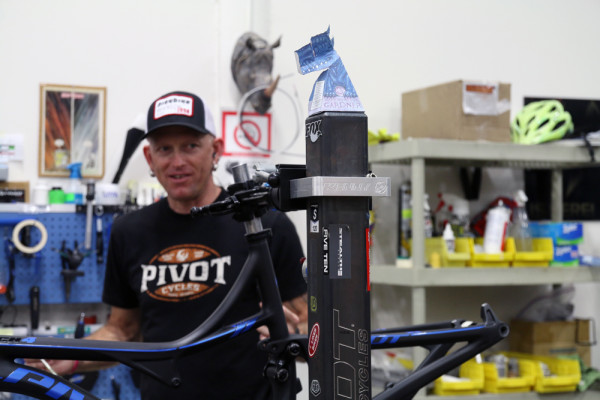
Complete build kits are pulled from the cage piece by piece and assembled into kits which are lined up to be built. Pivots are shipped out 75% assembled which allows better shops that are Pivot dealers to put their own finishing touches on complete bikes.
Going back to creating processes, the color matched fork program was a hit with consumers but Pivot had to figure out a way to quickly and precisely apply their own fork decals. That meant the creation of machined aluminum fork fixtures that allow each decal to be perfectly applied to the lower, one by one.
The whole process ends here, with finished bikes awaiting their departure in their temporary cardboard homes.
Perhaps just as important as what’s inside Pivot is what’s around Pivot’s headquarters in Tempe, AZ. After falling in love with the mountains after growing up in Illinois, Cocalis has been a resident of the desert ever since. Just a short drive from the office are world class trails in the form of South Mountain. After getting up pretty early in the morning to avoid the heat, we were treated to an amazing ride which included some of the best techy downhills the National Trail has to offer. Riding the chunky, techy rock sections, it’s easy to see the inspiration behind bikes like the Mach 6.
I imagine that riding a Mach 6 carbon fully decked out with XTR and Reynolds carbon wheels at South Mountain is similar to something like driving a Ferrari at Monza. There is just something so special about riding a bike that was built with so much passion at one of the very trails it was conceived for with the guy who designed it. The next time you’re out riding South Mountain keep your eyes peeled – you never know when you’ll catch Cocalis out testing the next Pivot.