Tucked away on a rather unassuming business park on the outskirts of Glasgow is a new eBike Motor Manufacturer, FreeFlow Technologies. The start up company is producing an award winning and rather innovative 60 Nm Motor called the FF60. It is compact thanks to the nested motor construction made possible by a Strain Wave Transmission. It is said to be tuneable for any kind of bike. And, it is fully serviceable to boot, sold with an industry-leading three-year warranty.
It’s early days for Free Flow Technologies, but already their patented technologies have attracted millions of pounds worth of investment from none other than Williams Formula One. We had the pleasure of meeting Managing Director, David Hemming, at the Scottish Mountain Bike Conference where we saw two prototype eBikes sporting the system. Interest piqued, we headed out to East Kilbride to check out the FreeFlow Technologies HQ, and to get a closer look at that Strain Wave Transmission.
Who is FreeFlow Technologies?
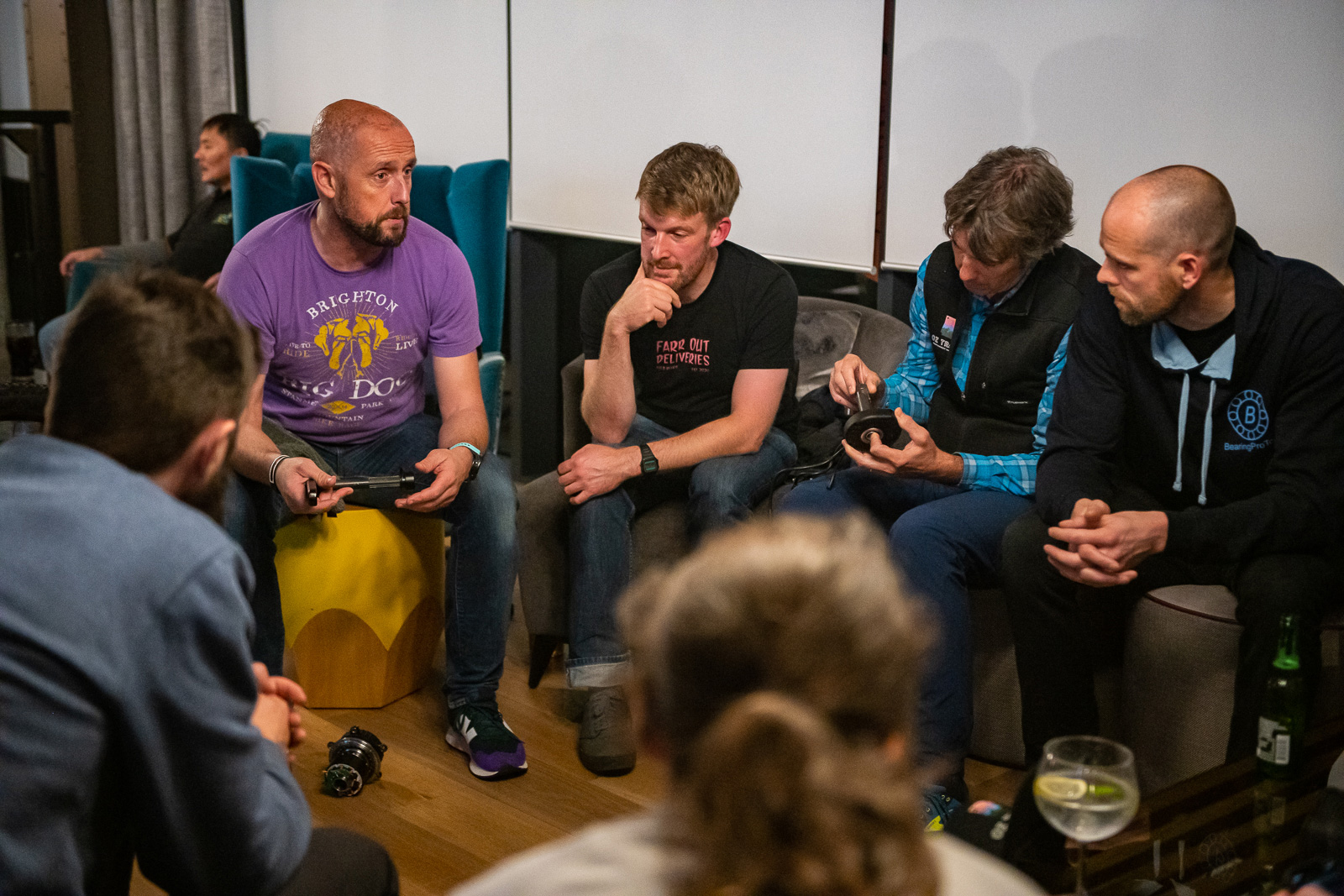
Entrepreneur and Inventor Neil MacMartin is the original founder of FreeFlow, having designed its proprietary transmission, electronic hardware and controls. He is still the largest shareholder in the company, but has taken a step back allowing a new leadership team to run the show. Heading up that team is David Hemming, a man some may remember as a Team GB Athlete who, during the 90s, was simultaneously racing World Cup Downhill, Dual Slalom and Cross Country.
Neil Edwards was brought in around 2018, sparking FreeFlow’s relationship with the Foresight Group, and the Foresight Williams Technology Investment Fund. The same folks that run the show at Williams Formula 1 took one look at FreeFlow’s Technology and subsequently invested £1.7 Million in its development – a stamp of approval if you ever did see one.
Fast forward to today; a handful of small engineering work spaces on a business park in East Kilbride, Scotland, are at the heart of FreeFlow Technologies. This is where the assembly and QC of every single FreeFlow eBike Motor takes place – approximately 3,000 per year (equivalent to around £14 Million worth of eBikes) – handled by a small team of mechanical, electrical and firmware engineers with over 70 years combined experience. Chief Engineer, Andy, gave us the walk around.
A Look Inside: FreeFlow Technologies Strain Wave eBike Motor
The FreeFlow Motor is called the FF60, principally because it has a maximum torque of 60Nm. Thus, in terms of its output, it is comparable to the likes of the Fazua Ride 60, and the TQ-HPR50, the latter of which is another example of an eBike Motor that uses elements of a Harmonic System.
FreeFlow Motor | Maximum Torque | Peak Power | Consistent Power | Weight | Torque Density | Reduction Ratio |
FF60 | 60 Nm | 290 W | 250 W | 3.8 kg | 50Nm/dm³ | 66 |
The FF60 design has come some way since 2018; around this time, the Harmonic Drive transmission, or Strain Wave Gear, came off patent, something that FreeFlow’s Consultant, Neil Edwards, was clearly paying close attention to. It was Neil who realized the system’s potential to make use of the Harmonic in order to turn the FreeFlow Motor into the more compact co-axle system it is today. So, what’s the big deal with the Strain Wave Gear?
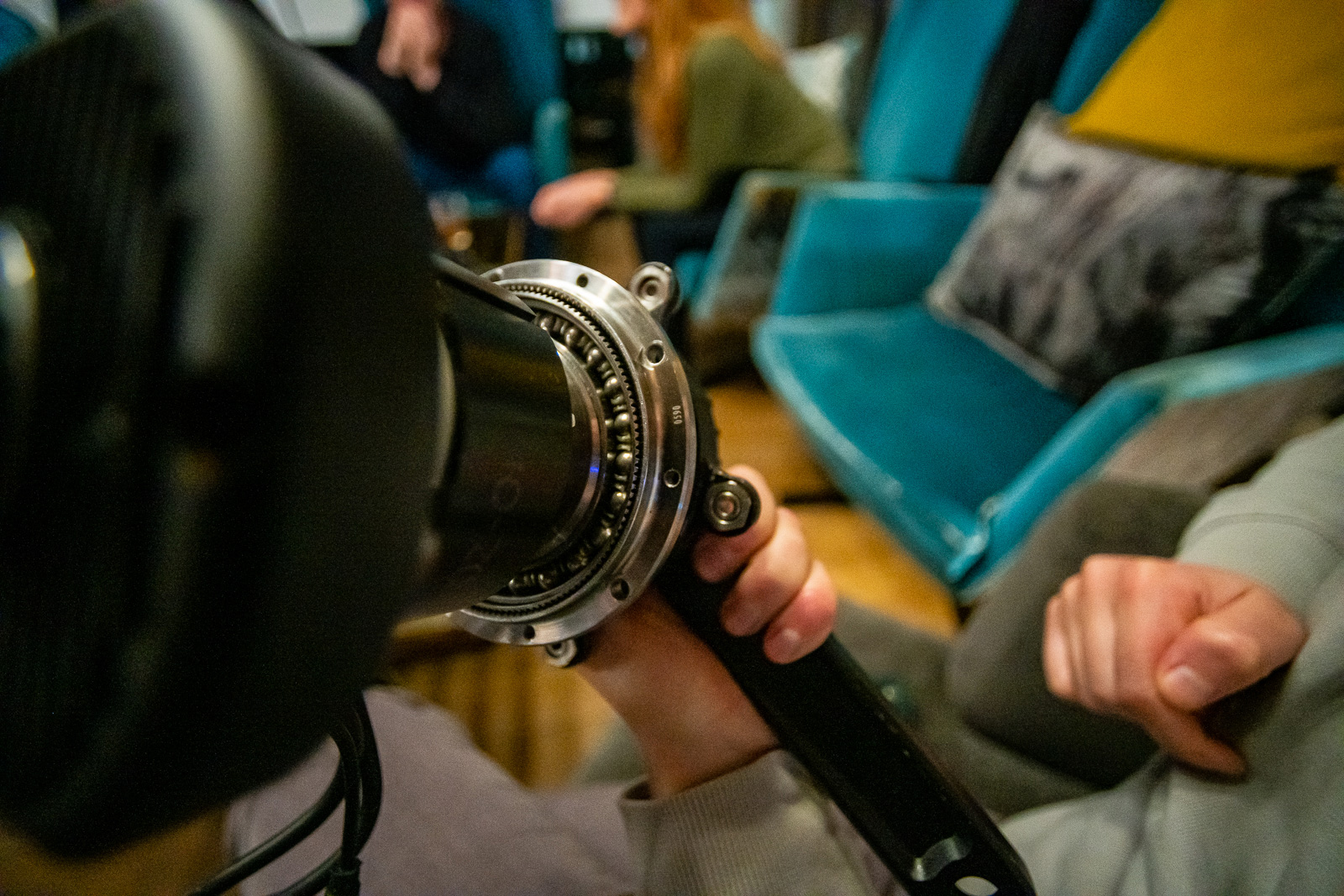
Reduction Ratios
Central to any eBike motor is the mechanism it relies upon to achieve the appropriate reduction ratio. What’s that when it’s at home? Well, every system has an electric motor that spins at a much higher RPM than the rider’s pedaling cadence. On the FF60 Motor, the electric motor spins at around 5,000 RPM for a pedaling cadence of 75 RPM. The reduction ratio refers to the mathematical relationship between those two numbers.
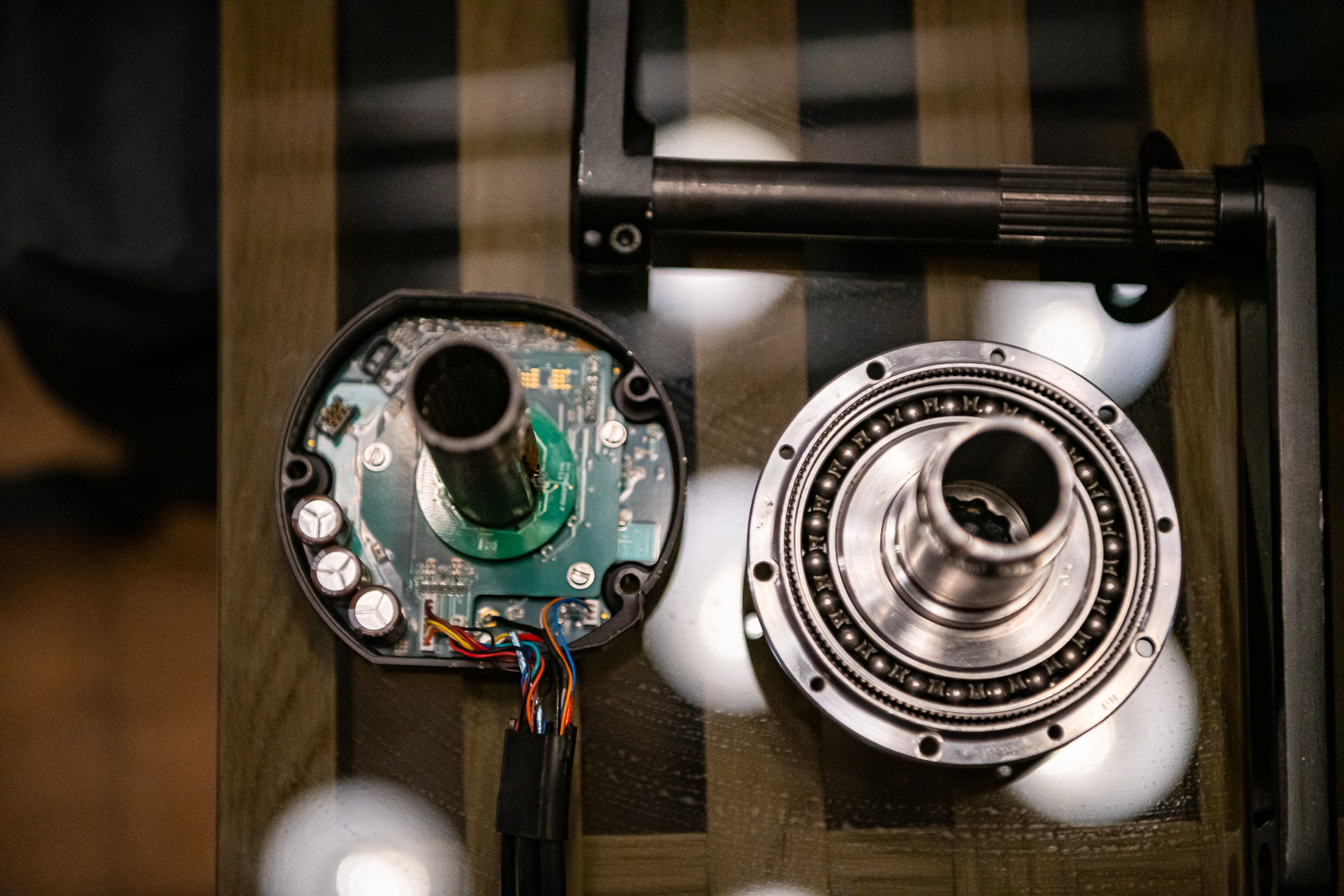
So, for example’s sake, in the case of the FF60, the reduction ratio is 66. Where the Strain Wave mechanism is clever, is that it is able to achieve this reduction ratio in just one step, as opposed to the several steps necessary with planetary gearing systems that are used by almost every other eBike Motor on the market today.
How does that work?
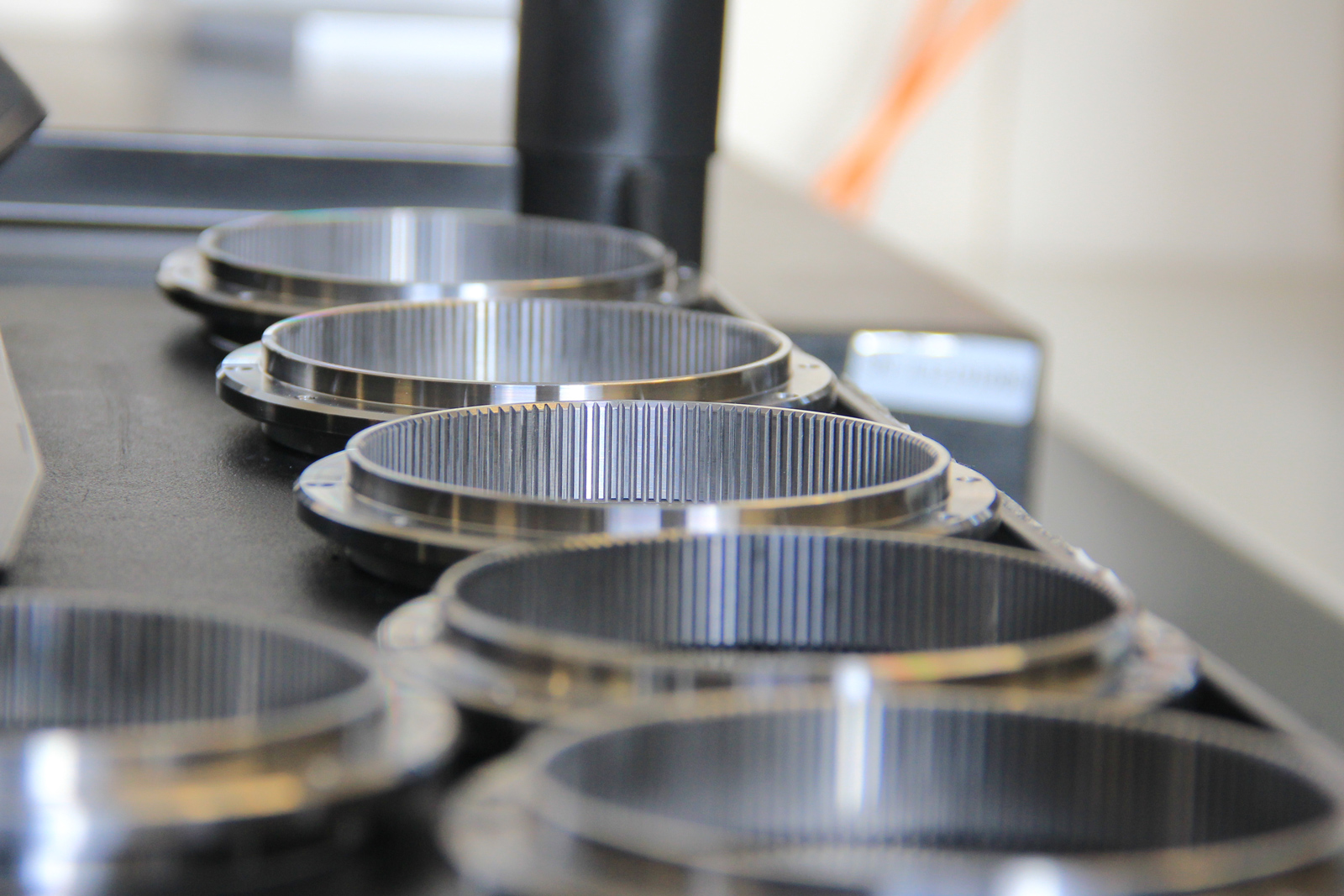
Indeed, it is conceptually very similar to the Harmonic Pin Ring Transmission that sits at the heart of the TQ-HPR50 motor. The Strain Wave Transmission is composed of a wave generator bearing that sit inside two concentric rings; the splines on the outer surface of the inner ring interface with the splines on the inner face of the outer ring. But, they don’t mesh perfectly.
Critically, the outer ring has 2 more teeth than the inner ring. The wave generator flexes the inner ring such that it “walks itself around” the splines of the outer ring. Sounds complicated, right? Well, that’s because it is… the video below makes it much easier to understand.
So, thanks to the use of the Strain Wave Gear as opposed to Planetary Gears, the FF60 can be constructed with a concentric layout wherein all of the hardware – the Strain Wave Gear, electric motor and stator – are packaged like a clam-shell so that the motor can sit neatly directly behind the 34T chainring. That differs to almost every other eBike Motor on the market wherein the stator is offset to the Planetary Gears to produce a motor with more of an elongated oval shape.
The concentric layout was of huge importance to the team, as they wanted to produce a motor that could cleanly integrate into any bicycle frame, such that most folk would have a hard time figuring out they were actually looking at an eBike, as opposed to a regular bike. Twmpa Cycles’s E-Flow Gravel Bike is a fantastic example of that (more on that later).
What else is unique to the FF60?
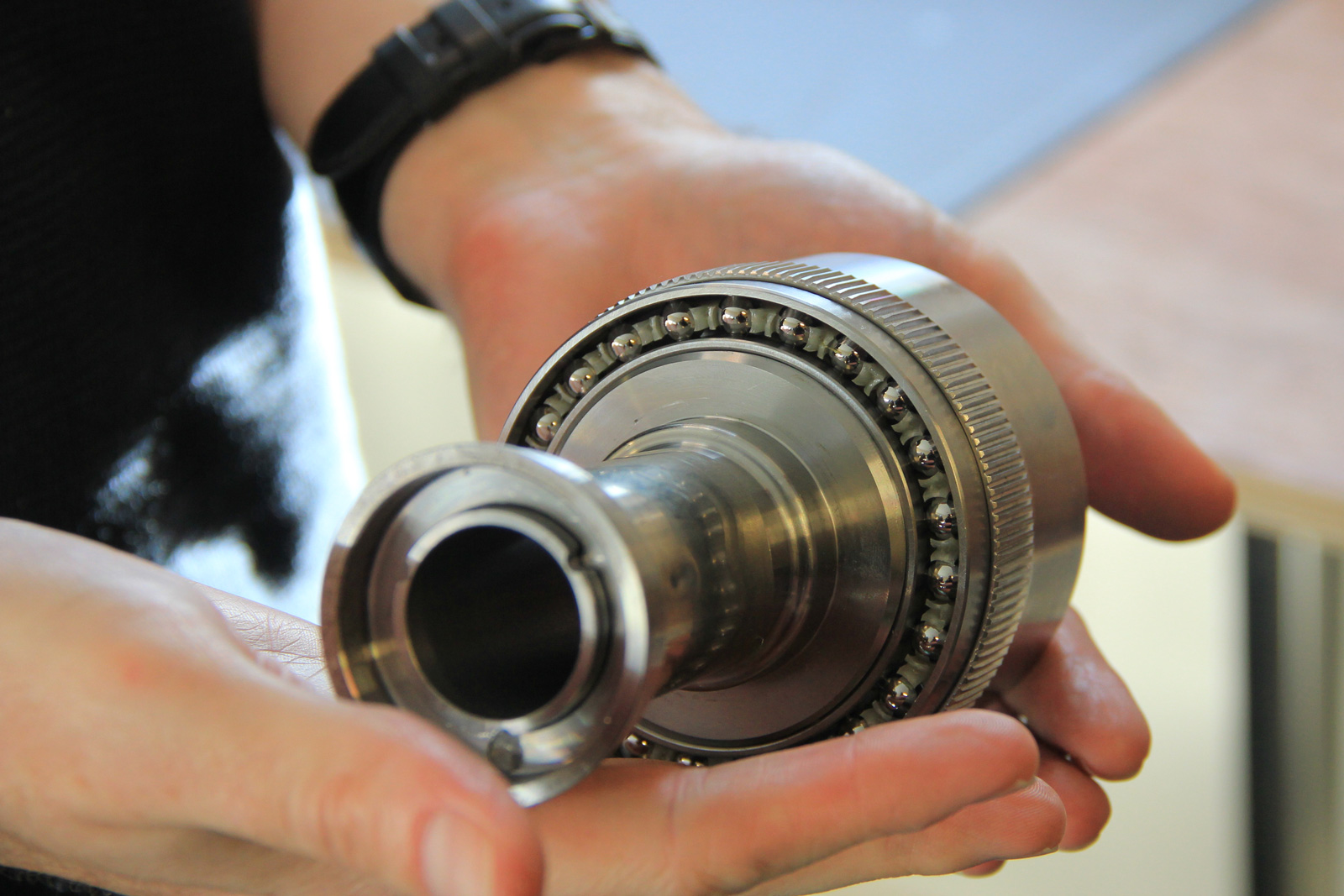
Managing Director, David Hemming, tells us that most of FreeFlow’s patented technologies are located “within the locus of the Harmonic, the dead space that no one else makes use of”. Herein lies a double sprag clutch and a one-way bearing, a layout that is exclusive to the FreeFlow Technologies system.
“Our one way clutches disconnect the rider from the motor so when the motor is off they’re not turning the motor. We have nested the clutches within each other and inside the cup of the flex spline around the crank axle. A key aim of our design was to make the system concentric so the drive unit could be hidden behind the chainring even on steel bikes where complex tube shapes are not an option” – Phil Wood, Mechanical Engineer at FreeFlow Technologies.
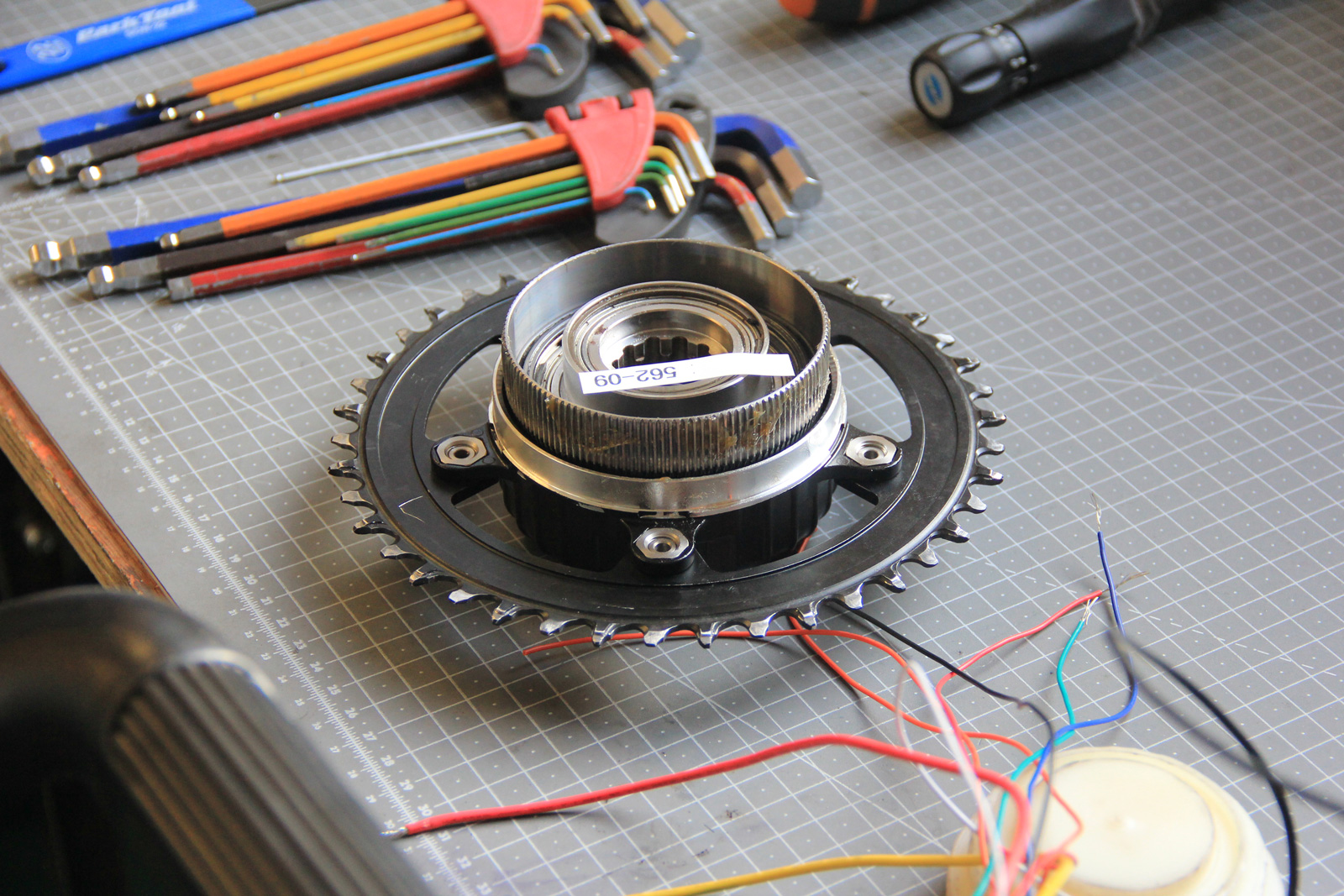
The axle running through the FF60 eBike Motor is home to a Strain Gauge which comprises the system’s Torque Sensor. On this system, torque is measured 15 times per second, allowing the system to react quickly to rider input, adapt its assistance level. The system is also home to a 6-axis accelerometer that can detect things like cornering, descending and climbing; its information is integrated together with information from the speed sensor and torque sensor to determine what level of assistance is required at any given moment.
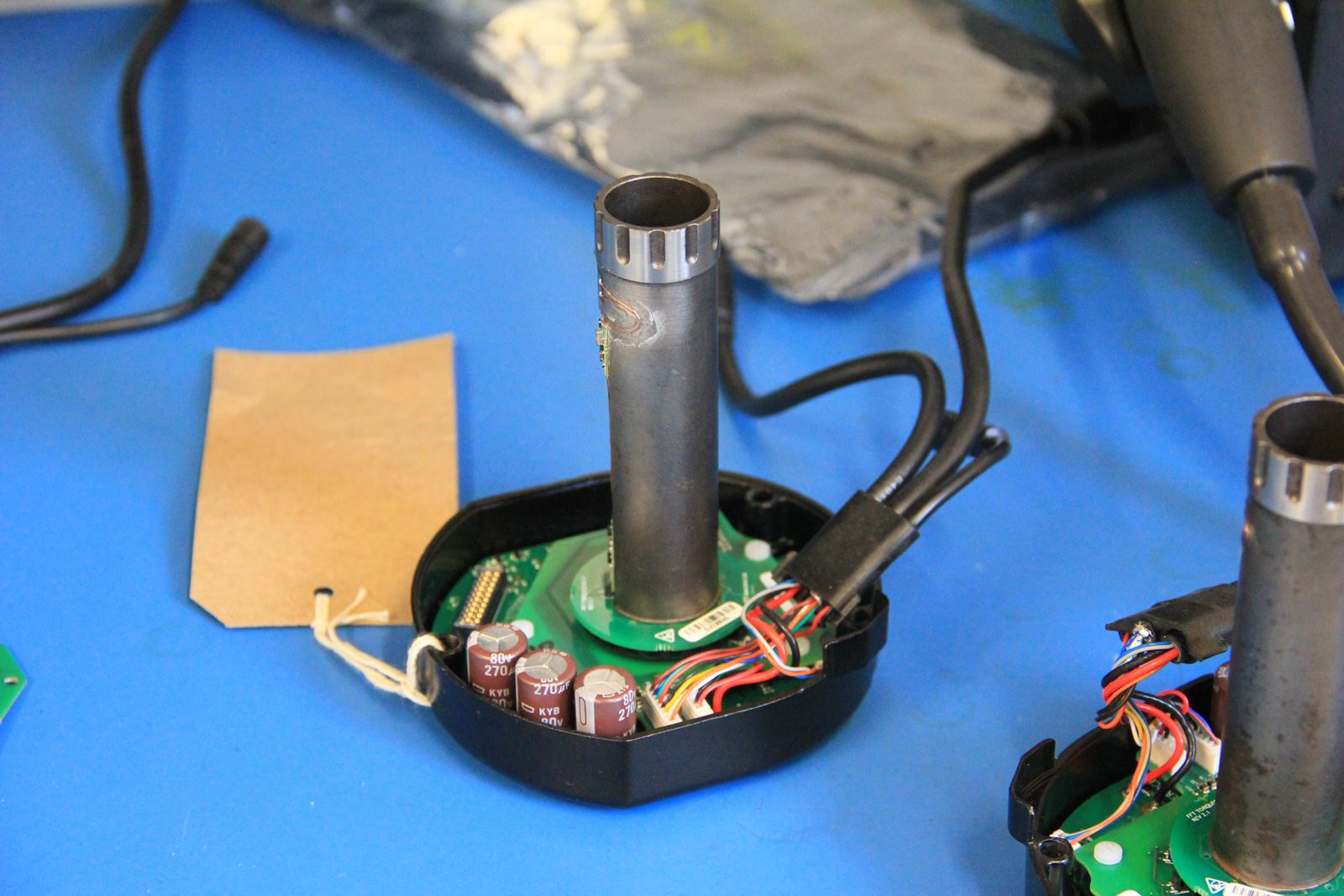
What about its serviceability?
While the FreeFlow motor isn’t the lightest, or most compact eBike motor around, the serviceability aspect is set to be a real strong point. Continuity of riding is important to the team at FreeFlow; they want the FF60 System to be easily serviceable at a local bike shop, such that if the motor encounters a problem, the rider isn’t without their bike for weeks on end. For the commuter cyclist, the importance of that cannot be overstated.
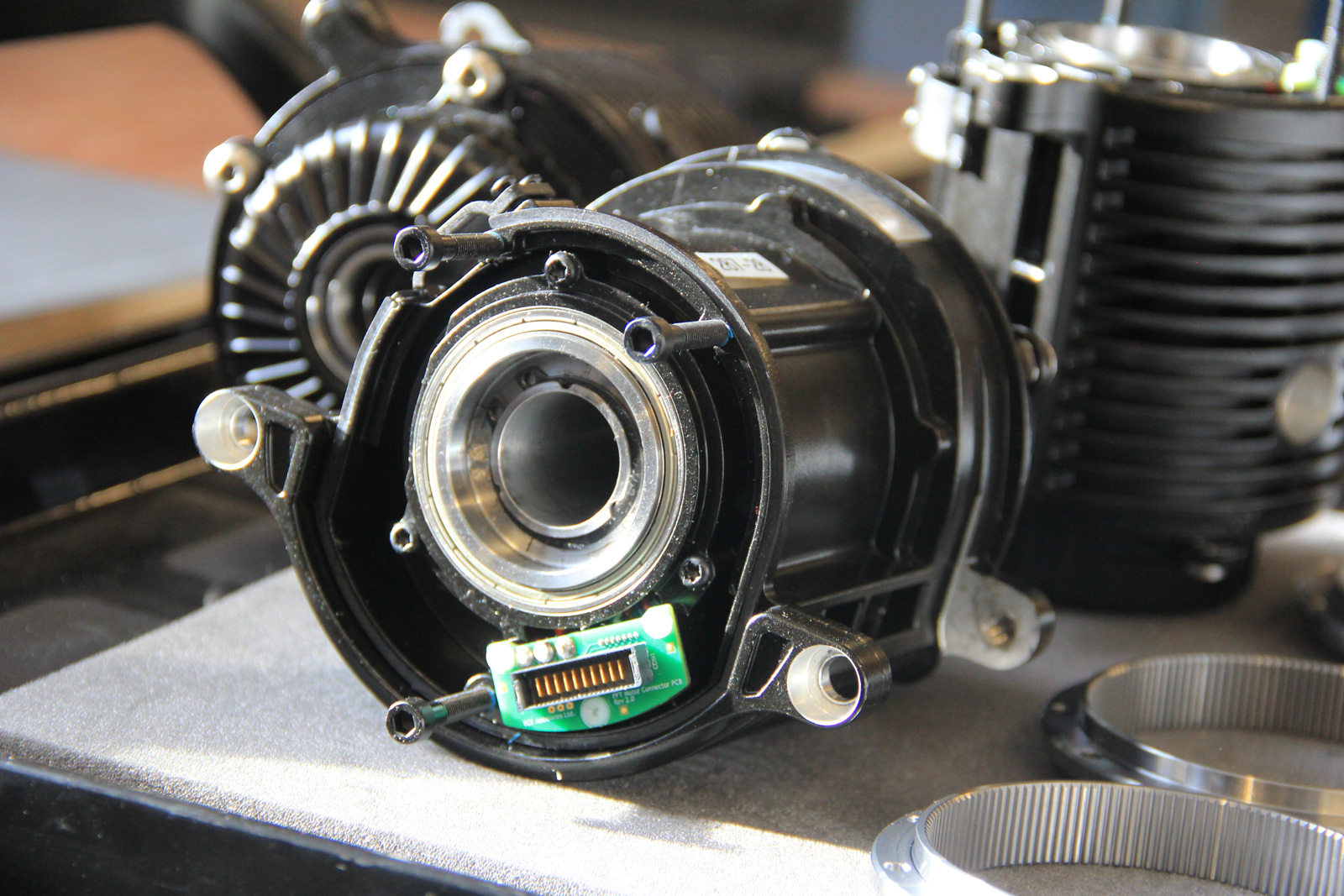
With that in mind, FreeFlow says it has engineered the FF60 Motor such that basic, simple repairs can be turned around within 48 hours. The team are proponents of the circular economy concept, too. Almost everything within the FF60 is replaceable; the BB bearings, the Harmonic, the Outer Ring Gear, the Clutch Package, the Chainring Bolts, the Crank Arms, the Crank Axle, the Torque Sensor, the Electronics Boards… so, if any one of those parts fails, it can either be fixed at the local bike shop, or it can be replaced in isolation of everything else, meaning very little material actually goes to waste.
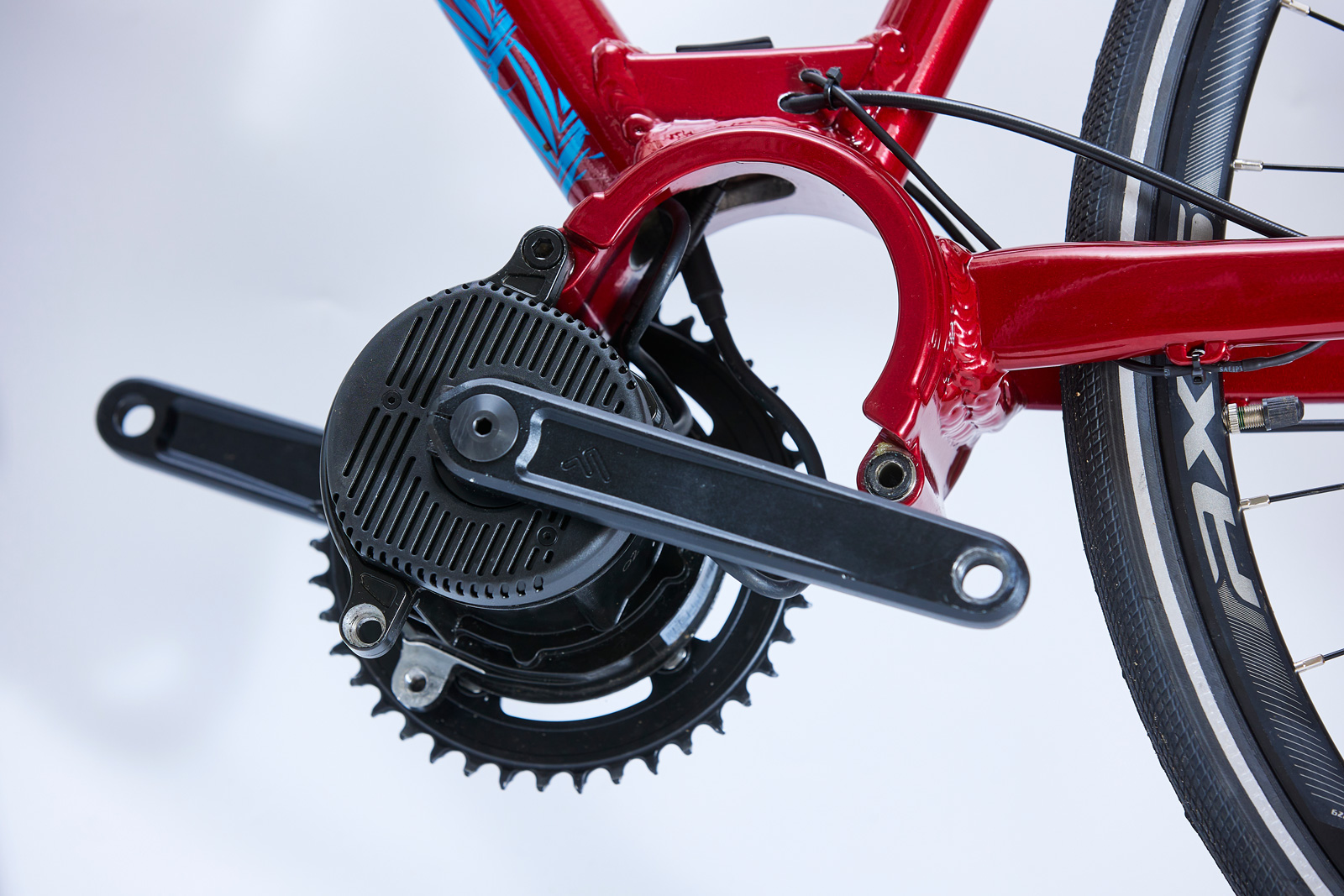
Sounds ambitious, right? FreeFlow Technologies is serious about this aspect, though. They have even begun training Cytech, the internationally recognized training and accreditation scheme for bicycle technicians, to ensure that the basic servicing procedures for the FF60 become somewhat common knowledge among bike mechanics likely to come across it.
Show us the eBikes
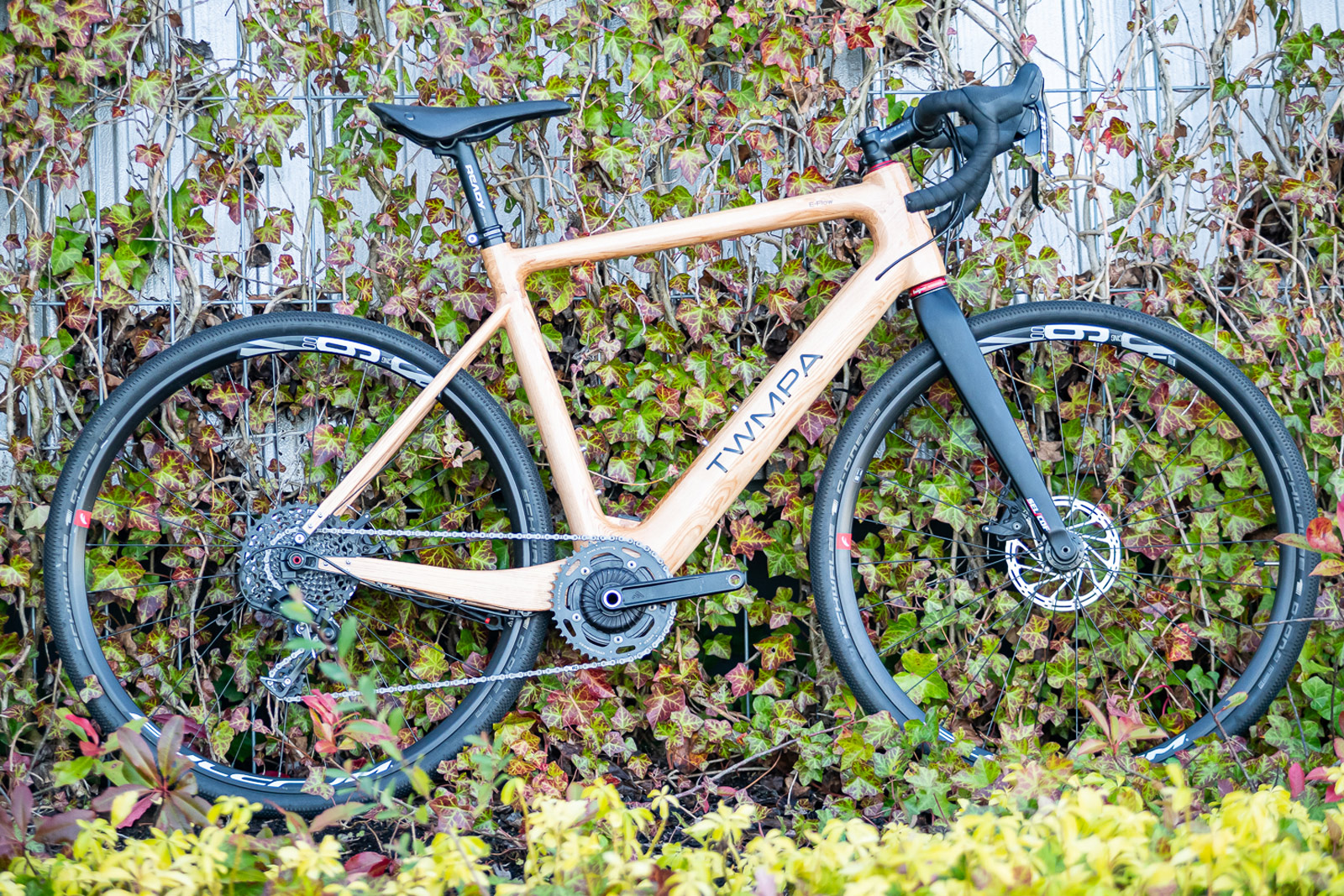
So, are there any production bikes actually running the FreeFlow Motor? No, all are still under development. It is the handmade bicycle brands that are taking the leap with FreeFlow, as they have been allowed to place very low volume orders. Wooden Bike Manufacturer, Twmpa Cycles, and Steel Mountain Bike Manufacturer, Starling Cycles, are two brands currently developing eBikes around the FreeFlow Motor. We got to see both at the DMBinS Scottish Mountain Bike Conference in Aberdeen, where FreeFlow Technologies took home an Award for Best Product.
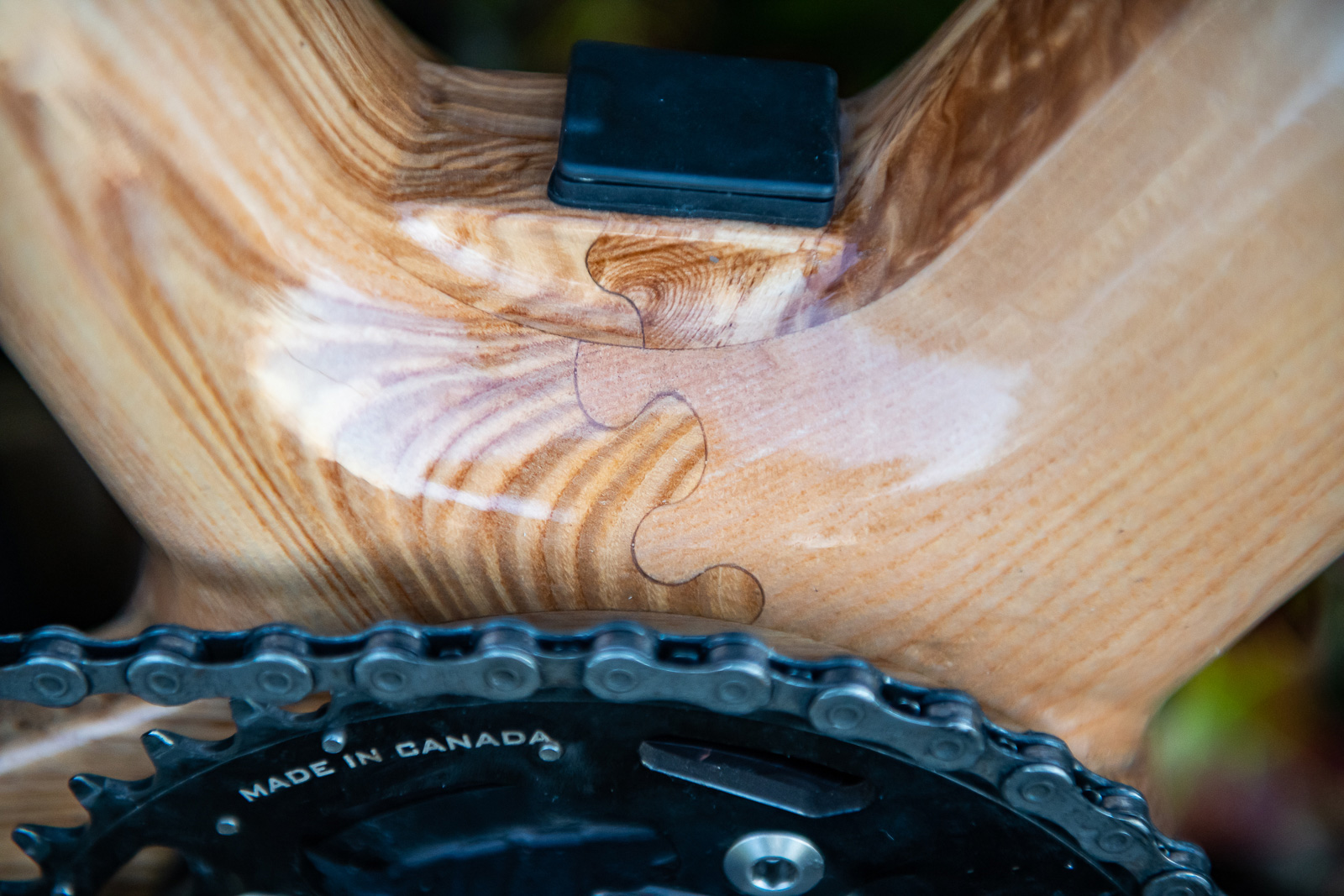
While the Twmpa Cycles’ E-Flow Gravel Bike is a fantastic example of the seamless integration FreeFlow are going for with the FF60 eBike Motor, Starling’s prototype eMTB is less so.
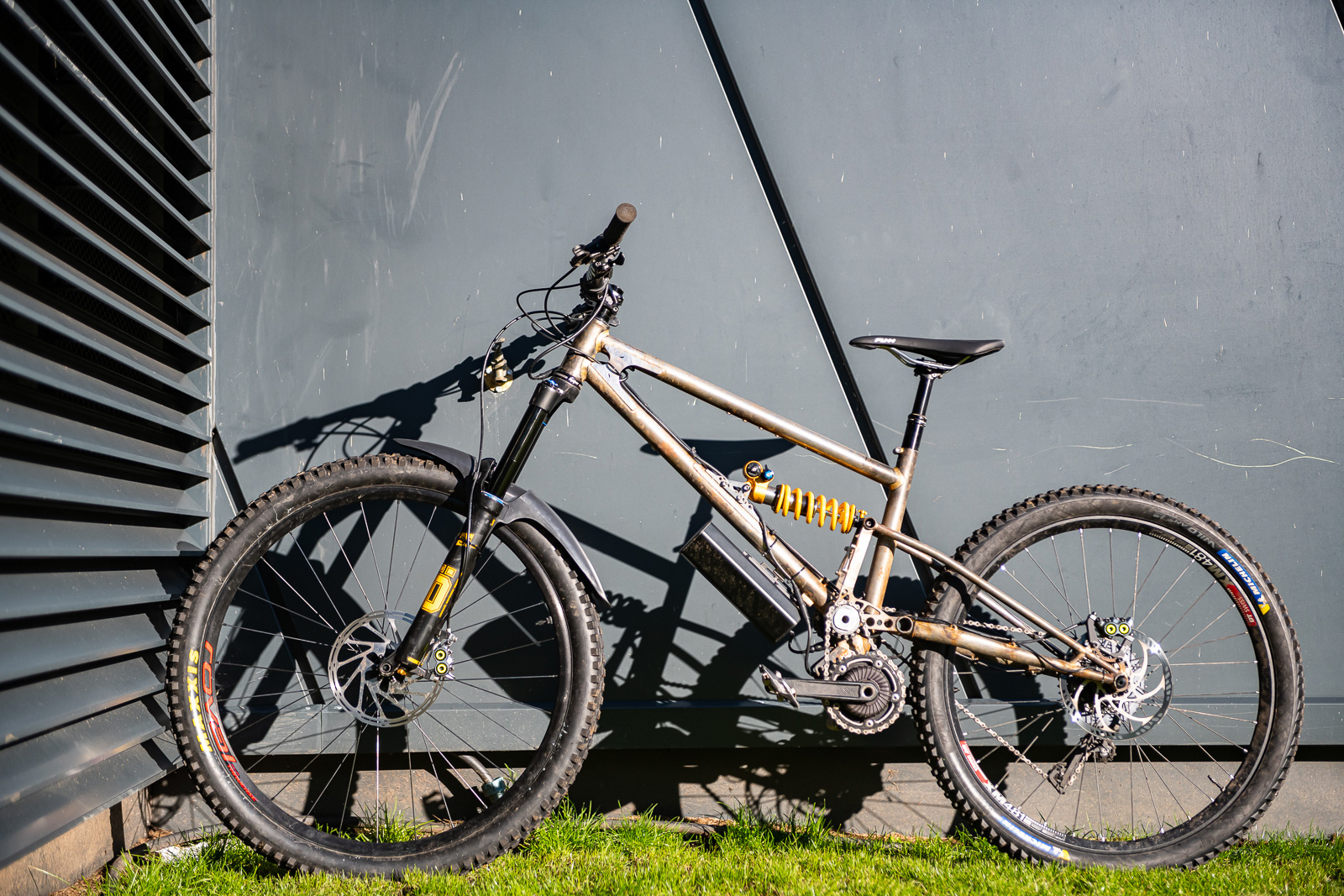
How does the FreeFlow eBike Motor Ride?
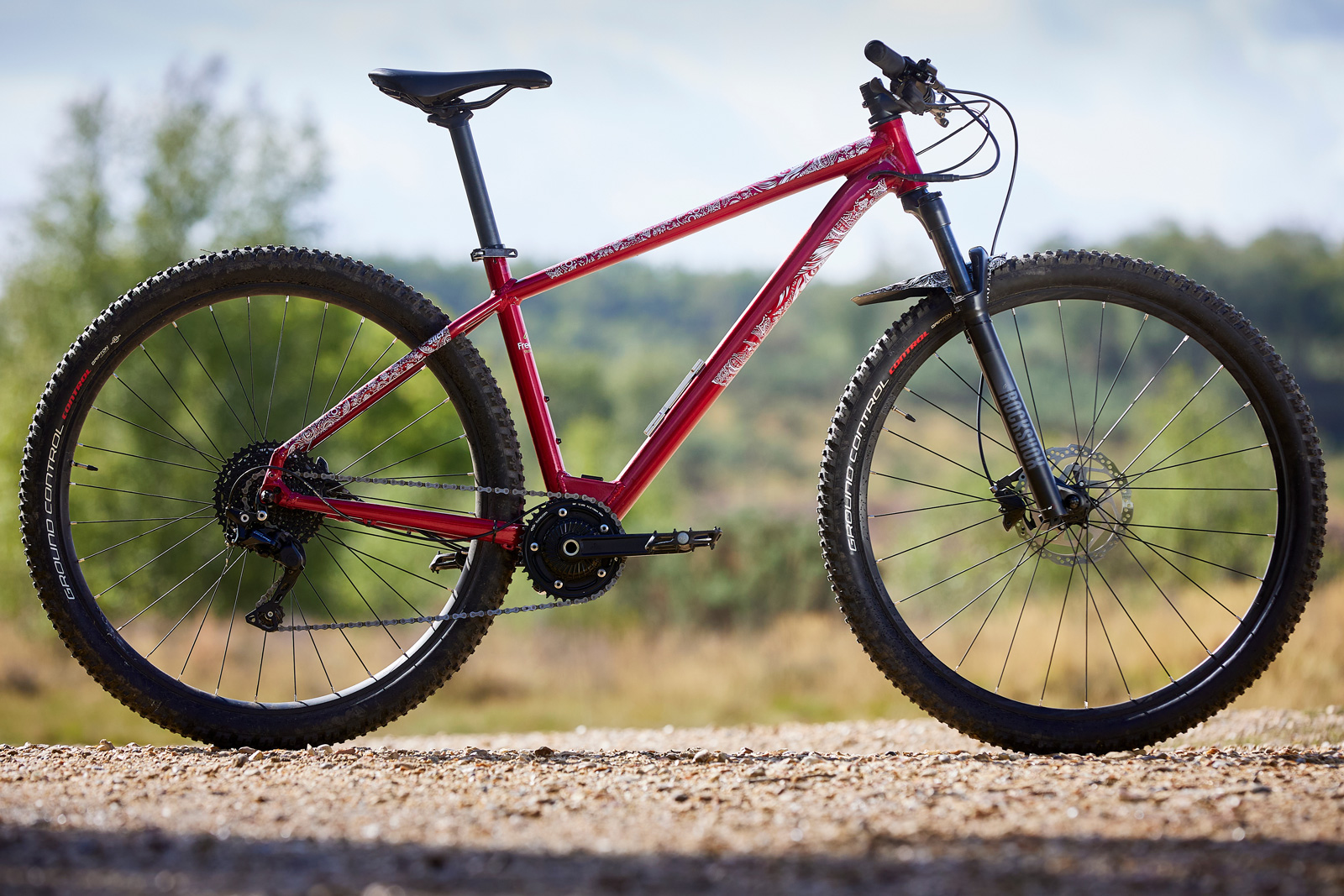
As there aren’t yet any production eBikes running the FreeFlow Technologies eBike Motor, the team has taken it upon themselves to cut and re-weld a fleet of Specialized Rockhopper hardtails to create something of a demo eBike fleet. During our visit to FreeFlow, we got a very quick shot on one of these to get a feel for the FF60 Motor.
I set off with the system switched off, to get a feel for how much drag is present in the system. I’m happy to report it felt just like a regular mountain bike, if a little heavy. It pedaled like a normal drivetrain. Nothing replaces a direct bike-to-back comparison of course, but I can’t honestly say I was able to feel any perceptible drag in the system.
The FF60 has three modes; Eco, Trail and Boost. It will have a Walk Mode in future, but the team hasn’t quite got around to that yet. Switching the system on, I have to say it does have that “prototype” feel about it. As you put the power down, vibration can be felt through the pedals as the motor kicks in and begins to provide assistance. This could very well be down to the fact the motor is on a bike that was literally butchered for the purpose of installing the motor; this was certainly not designed from the ground up, as any production bike with the FF60 motor will be. We’ll let them off on that point!
The FF60 seems to slowly build up its assistance level; it seems to feel less on/off than some eBike motors i’ve ridden such as the Shimano EP8 and Bosch CX Performance Line motors. That may be because this is a 60 Nm system, as compared to their 85 Nm, but it certainly feels a lot more subtle than the aforementioned.
It is quite loud, however; certainly the loudest eBike motor i’ve tried. Of course, Free Flow are aware of this and their development efforts are currently prioritizing how to make the system quieter and smaller.
What’s next for FreeFlow Technologies?
At the moment, FreeFlow is assembling around 3,000 units per year out of its East Kilbride facility, with plans to scale than up to 10,000 units per year. Their goal is to be able able to service demand from all UK and some Central European brands directly from the facility in Scotland.
Managing Director, David Hemming, tells us that the FreeFlow model is to make a complete system that can be delivered at the point of origin for many of the big brands’ assembly in Asia. They are also considering an Eastern European facility to assemble motor systems in that region in order to better serve brands in Mainland Europe.
Over the next few years, FreeFlow will be working on three new eBike Motor Systems that will be smaller and lighter than the FF60 seen here; they will also work on a system dedicated to eCargo Bike usage.