It’s been over 10 years since Fair Wheel Bikes in Tucson, AZ first shared with us their independent bar & stem testing, but they are back at it, measuring real stiffness in a new crop of 15 modern road & gravel bike stems. What do you prefer: absolute lightest weight, maximum stiffness, the highest stiffness:weight ratio, or maybe some happy medium that might not break the bank. Fair Wheel does the testing so we can all make more informed buying decisions.
Fair Wheel Bikes tests real road & gravel bike stem stiffness
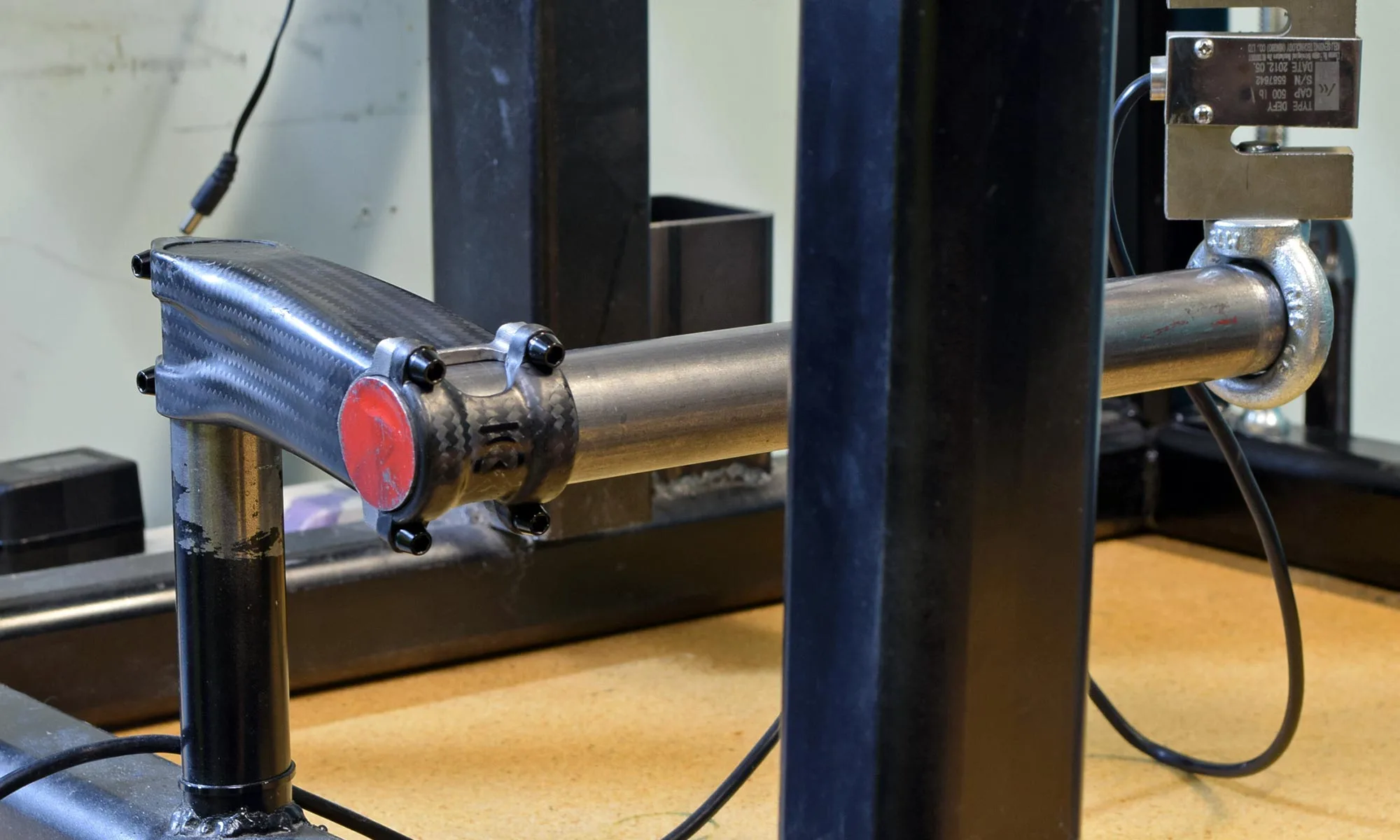
So why did Fair Wheel dust off their test rig? We spoke to long-time head of the shop Jason Woznick, and he said simply that, “it has been about a decade since we did testing…. [and] we wanted to re-test, bars, stems and cranks and see how things have changed.”
Sounds good to us.
I’ve personally known Fair Wheel since around 2001 or so. That’s when I was first introduced to the shop and their weight-weenie ways by a friend who’d worked in there before moving to the East Coast. And then, soon after I headed to meet them in Tucson in person when traveling out to race the 24 Hours in the Old Pueblo. Fair Wheel bikes has catered to both local looking for trusted service, and bike nerds from far & wide hunting the most exotic components and some of the world’s lightest bike builds.
Although we didn’t get to it then, Fair Wheel recently celebrated their 50th-anniversary last year by updating their road crankarm and handlebar stiffness tests with some more of the latest & greatest modern models. You can check out that May 2023 road crank test here or their updated November 2023 road bar test here.
But now let’s get back to stems.
Why do we trust Fair Wheel Bike’s independent component testing?
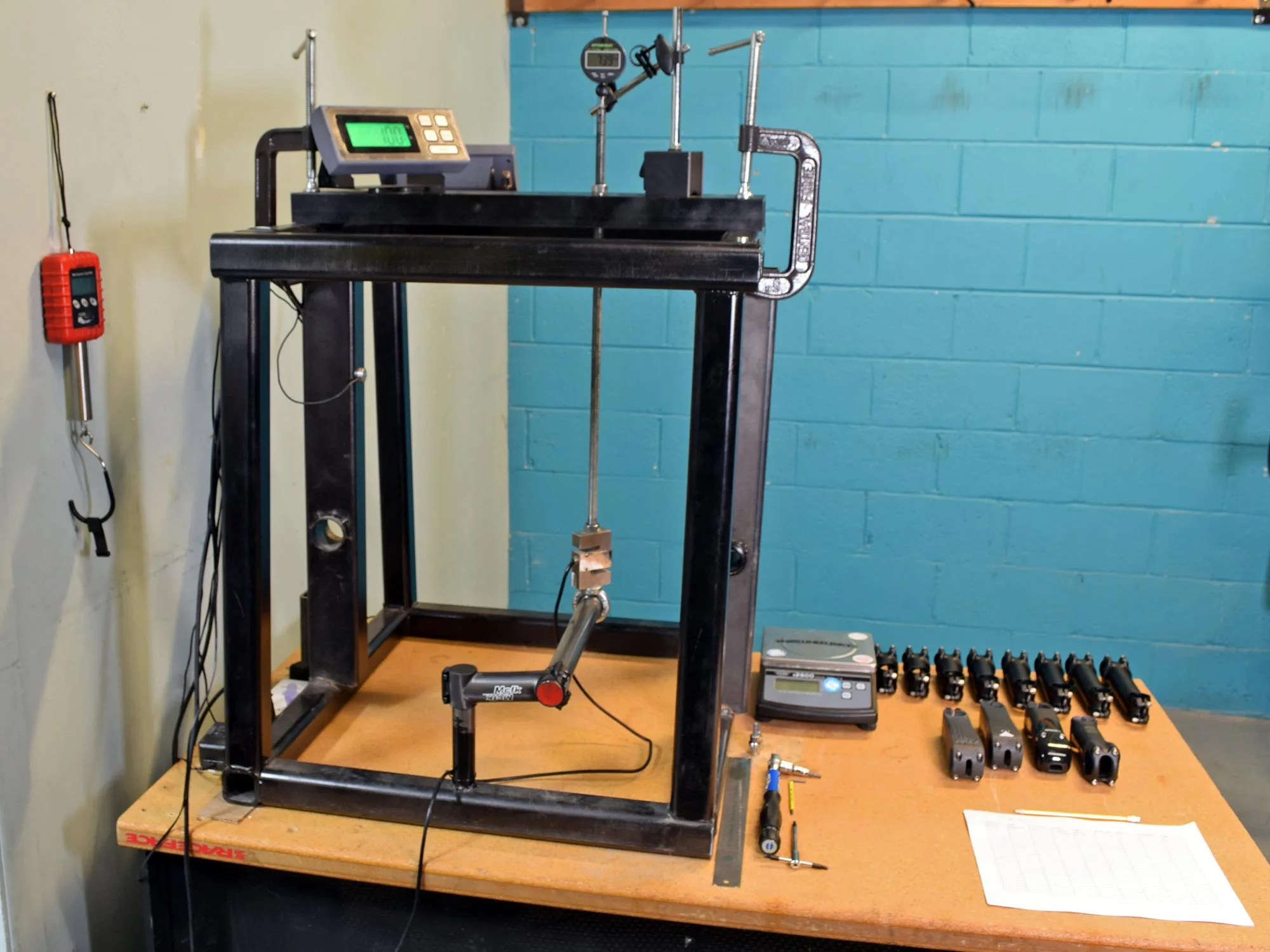
The beauty of Fair Wheel Bikes testing components is three-fold. First, they’ve been around for more than half a century, and they kept the same test rig in the back of the shop just waiting. Secondly, they are super analytical but practical, so they keep their tests simple and use the exact same test protocol today as when they started testing components.
And lastly, they’re kind of a bunch of nerds. OK, definitely fellow bike nerds… our favorite type.
Check out their original 2014 stem tests, here.
Stem deflection testing methodology
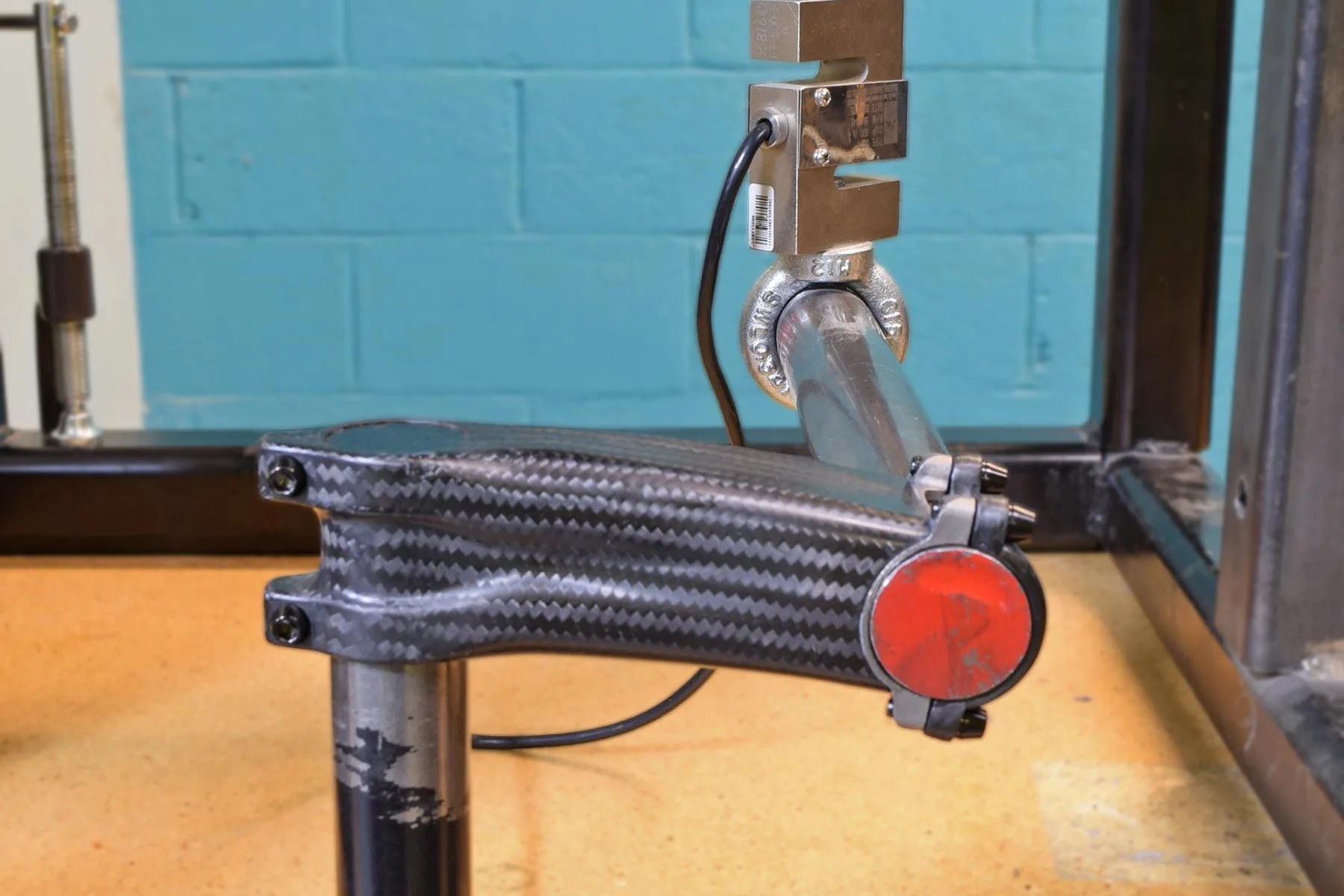
Their stem stiffness testing is just measuring stem deflection – how far a stem bends under a repeatable load. Again, Fair Wheel brought back their “favorite engineer” Jason Krantz to run the tests. He’s now a mechanical engineer at a global company developing testing & measurement equipment. But he also worked in the cycling industry over his career, for example designing bikes at Titus and sharing our journalistic focus at Bicycle Retailer and Industry News back in the 90s.
The stem deflection testing protocol he developed fixes the stem in a rigid frame, then applies a uniform 100lb (~45kg) load 10″ (~25cm) away from the centerline of the stem. The test simulates a reasonable approximation of the force when a rider is sprinting, pulling against the bar – up on one side, down on the other – as they try to pedal as hard as possible. But the exact force/load/weight doesn’t really matter, as deflection is linear, and they are comparing all stems with the same forces.
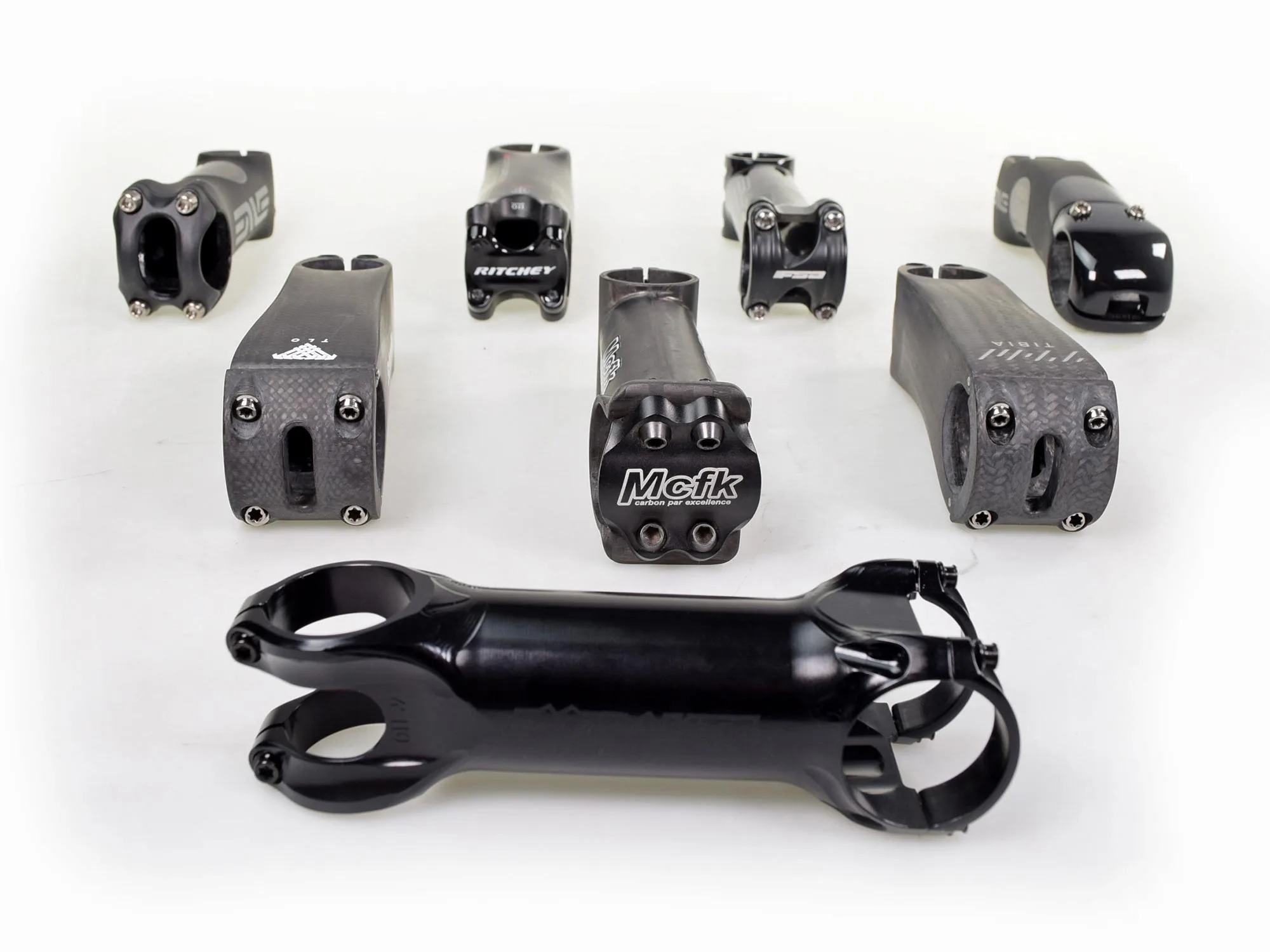
Fair Wheel has tried to minimize variables as much as possible. Their methodology says all stems should be 110mm long and -6° of rise, with a 1.125″ steerer clamp and 31.8mm bar clamp. But some stems tested were not available in that exact size, so there’s +1° variability in angle and -5mm variability for just two stems (105mm Pro Vibe Sprint Carbon & Syntace F119). But they explain why that may or may not matter.
What is stiffness?
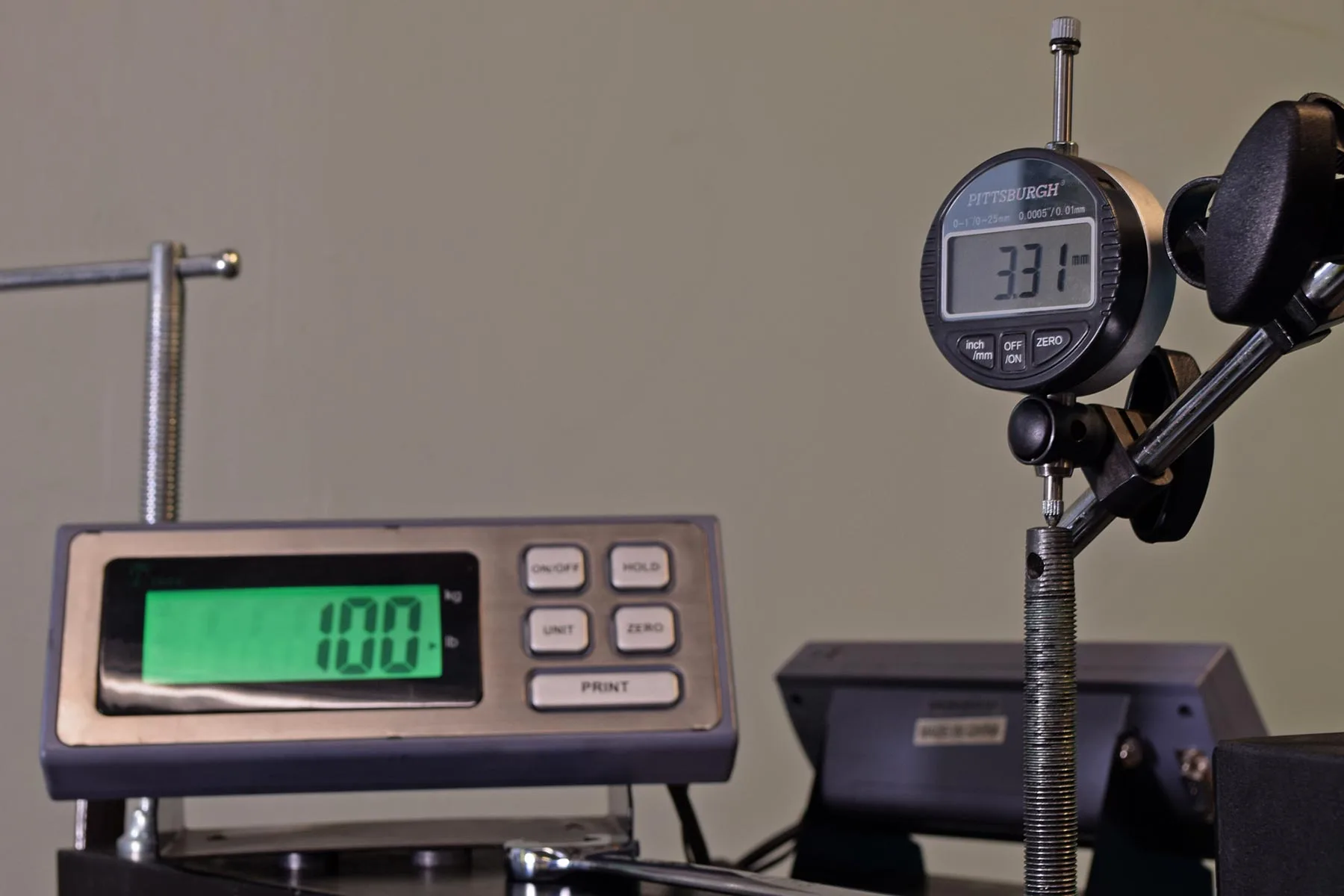
Something of a disclaimer… neither Fair Wheel nor us at Bikerumor are necessarily saying that greater stiffness actually means a better stem.
Maybe some lighter or even all-road & gravel riders might like a bit of compliance in their stem?
And the Fair Wheel test doesn’t even touch on the potential vibration damping that some materials can provide, independently of stiffness.
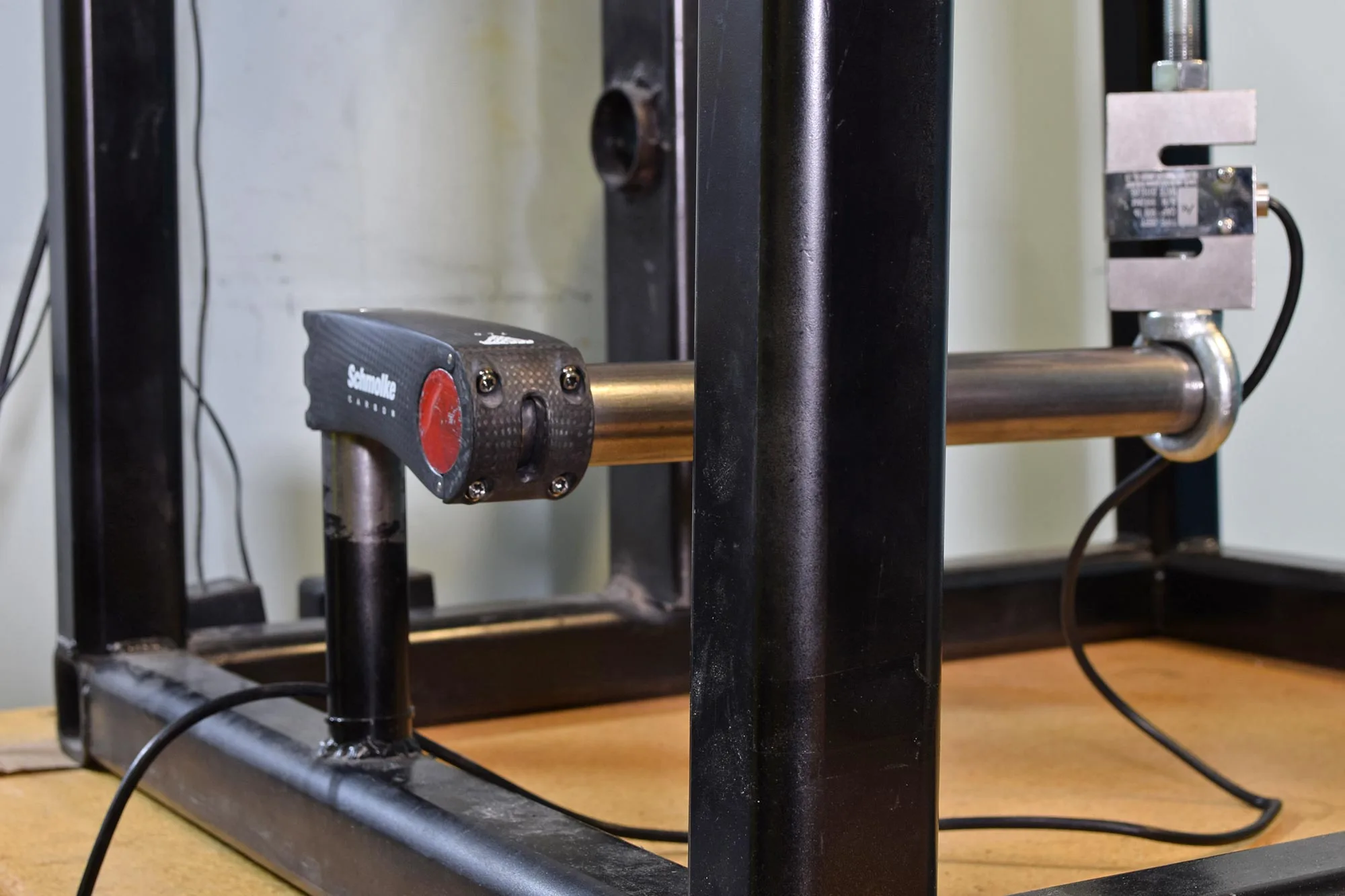
But if you are looking for cockpit rigidity for some reduction of energy loss or improved handling performance benefits, stem stiffness is certainly a good place to start in comparisons. And so, we’re pretty psyched that Fair Wheel is there out crunching these numbers for everyone to see.
Scroll down to the bottom of this article if you want to read Fair Wheel’s own detailed description.
2024 Fair Wheel stem stiffness tests’ results
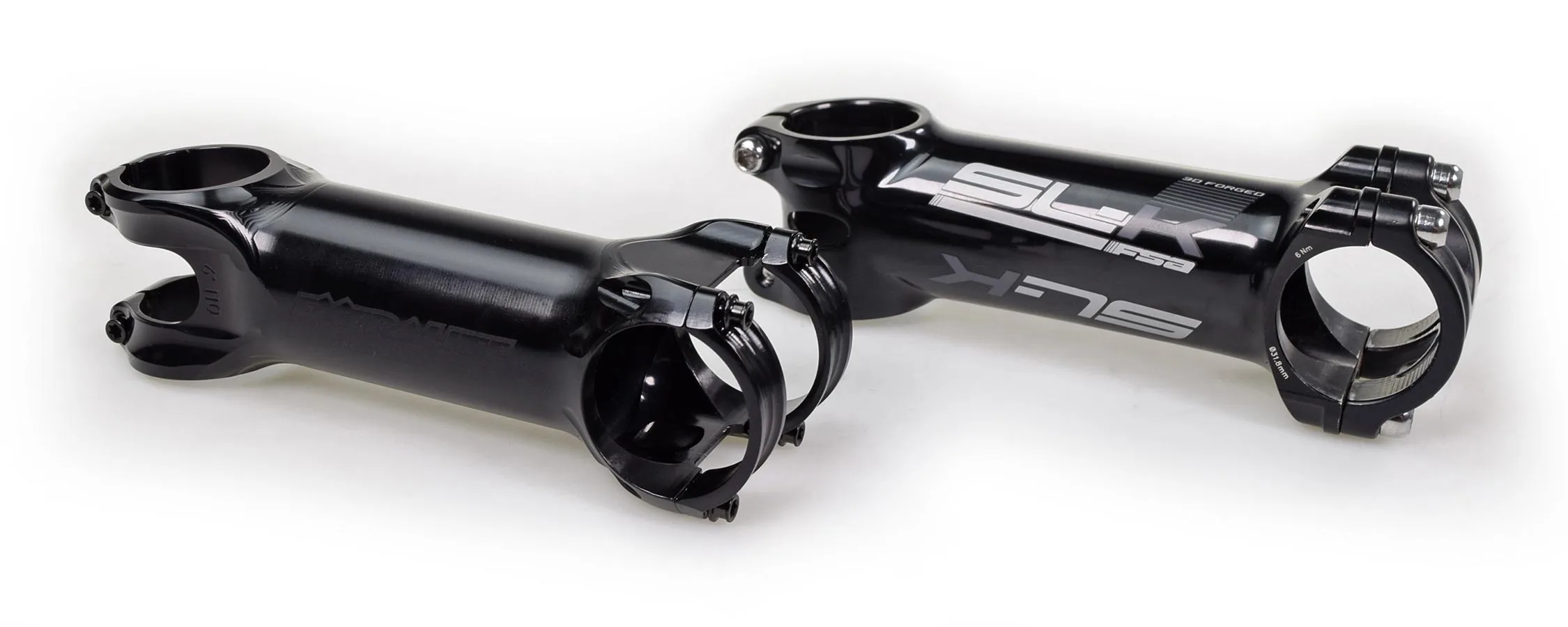
Top 5 Stiffest
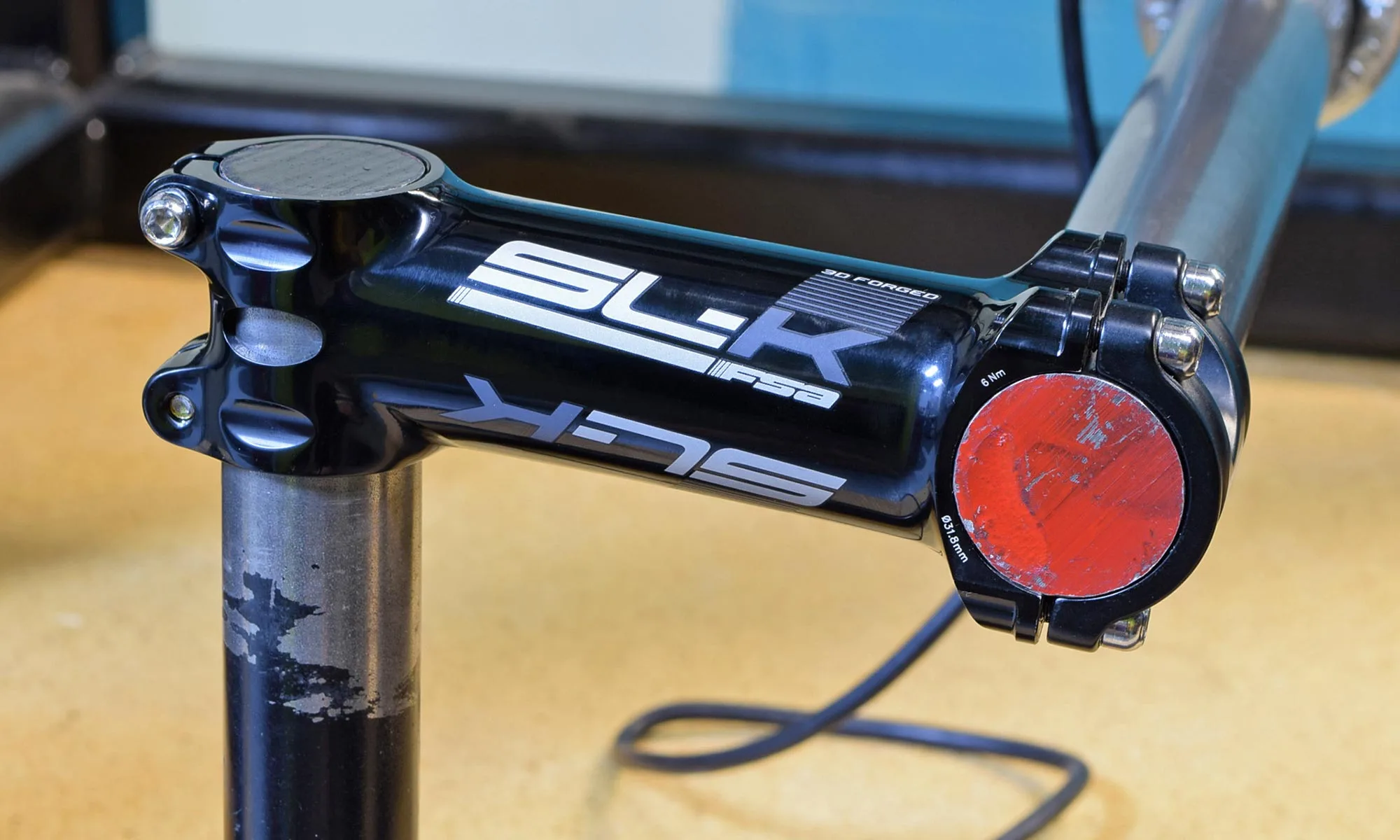
- FSA SL-K at just 3.7mm deflection, made of 2014 aluminum with steel bolts
- FWB machined Ti prototype at just 3.7mm deflection, made of titanium with ti bolts
- Ritchey Superlogic C260 at just 3.7mm deflection, made of 2024 aluminum with steel bolts
- ENVE Carbon at just 4.2mm deflection, made of carbon with ti bolts
- Uno Stealth at just 4.5mm deflection, made of 2024 aluminum with stainless steel or titanium bolts
Top 5 Lightest
- Extralite Hyperstem at 82.5g from 7075 aluminum with titanium bolts
- THM Tibia at 91g from carbon with titanium bolts
- MCFK Carbon at 92.3g from carbon with titanium bolts
- Schmolke TLO (ICR) at 94.5g from carbon with titanium bolts
- Uno Stealth ti at 104.7g from aluminum with titanium bolts
Top 5 Stiffness:Weight Ratio
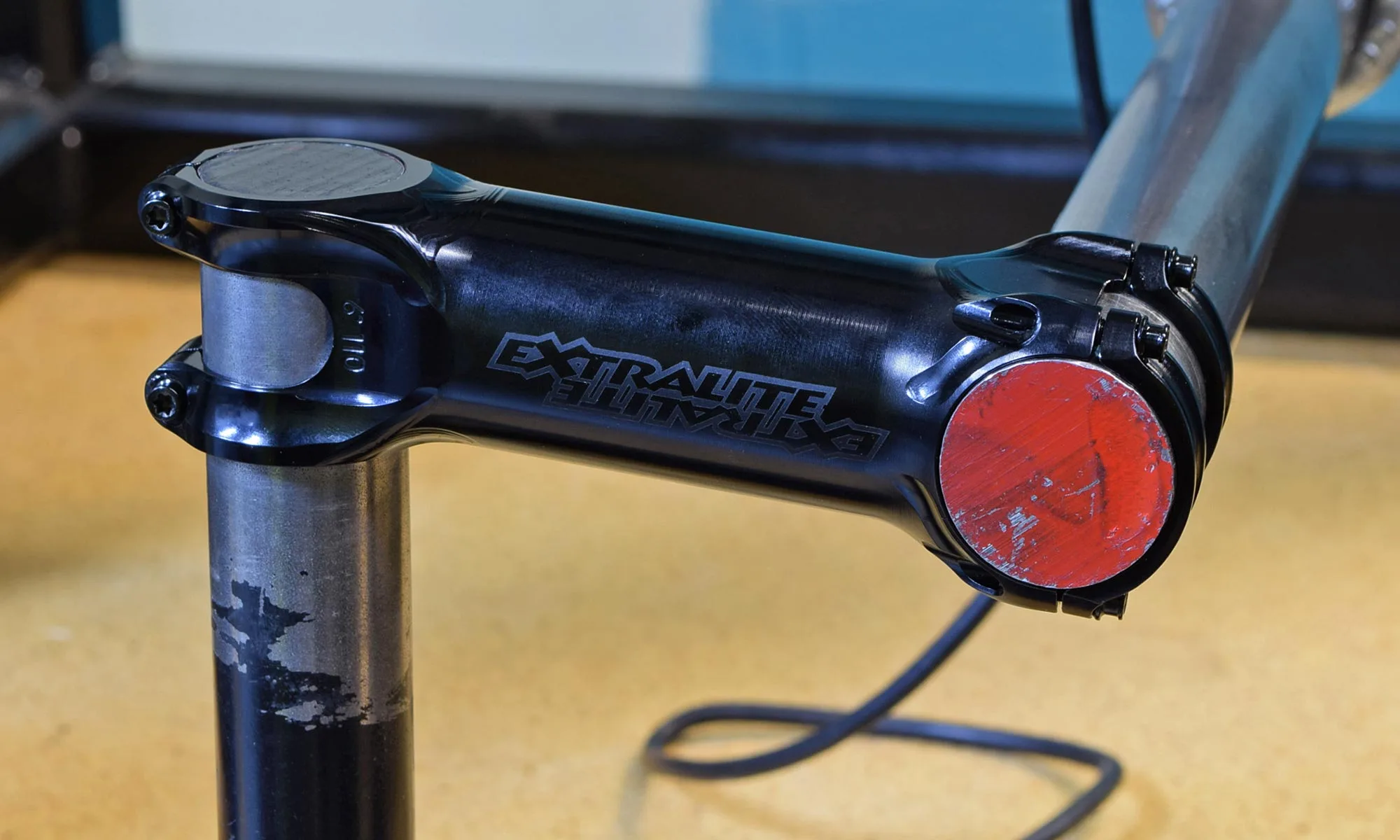
- Extralite Hyperstem with 5.6mm deflection at 82.5g for a 2.16 S/W ratio
- Uno Stealth ti with 4.5mm deflection at 104.7g for a 2.12 S/W ratio
- Ritchey WCS C260 with 4.7mm deflection at 108.1g for a 1.97 S/W ratio
- Ritchey Superlogic C260 with 4.1mm deflection at 128g for a 1.91S/W ratio
- FSA SL-K with 3.7mm deflection at 144g for a 1.88 S/W ratio
Complete 2024 Test Data
mfg | model | Deflect avg (mm) | Weight (g) | S/W | stem material | bolt material | angle (deg) |
---|---|---|---|---|---|---|---|
Bjorn | prototype | 5 | 110.9 | 1.8 | Carbon/Ti | Titanium | 6° |
ENVE | Carbon | 4.2 | 131 | 1.82 | Carbon | Titanium | 6° |
ENVE | Aero Road In-Route | 4.8 | 177 | 1.18 | Carbon | Titanium | 7° |
ENVE | Aero Road | 5 | 170 | 1.18 | Carbon | Titanium | 7° |
Extralite | Hyperstem | 5.6 | 82.5 | 2.16 | 7075 alloy | Titanium | 6° |
FSA | SL-K | 3.7 | 144 | 1.88 | 2014 alloy | Steel | 6° |
FWB Ti | machined prototype | 3.7 | 149.2 | 1.81 | Titanium | Titanium | 7° |
FWB Ti | welded prototype | 4.9 | 139.2 | 1.47 | Titanium | Titanium | 7° |
MCFK | Carbon | 6.8 | 92.3 | 1.59 | Carbon | Titanium | 6° |
Ritchey | Superlogic C260 | 4.1 | 128 | 1.91 | Carbon | Steel | 6° |
Ritchey | WCS C260 | 4.7 | 108.1 | 1.97 | 7050 alloy | Steel | 6° |
Schmolke | TLO (ICR) | 5.8 | 94.5 | 1.82 | Carbon | Titanium | 6° |
THM | Tibia | 6.1 | 91 | 1.8 | Carbon | Titanium | 6° |
Uno Stealth ti | 110 | 4.5 | 104.7 | 2.12 | 7050 alloy | Titanium | 7° |
Uno Stealth | 110 | 4.5 | 117 | 1.9 | 7050 alloy | Stainless | 7° |
Combined 2014 & 2024 Test Data
mfg | model | year tested | Deflect avg (mm) | Weight (g) | S/W | stem material | bolt material | angle (deg) |
---|---|---|---|---|---|---|---|---|
3T | Arx Team | 2014 | 3.8 | 129.4 | 2.03 | 7075 alloy | Titanium | 6° |
Bjorn | prototype | 2024 | 5 | 110.9 | 1.8 | Carbon/Ti | Titanium | 6° |
Bontrager | XXX | 2014 | 4.59 | 129.8 | 1.68 | Carbon | Steel | 7° |
Control Tech | Ti-Mania | 2014 | 4.01 | 132.1 | 1.89 | Titanium | Titanium | 5° |
ENVE | Carbon | 2024 | 4.2 | 131 | 1.82 | Carbon | Titanium | 6° |
ENVE | Aero Road In-Route | 2024 | 4.8 | 177 | 1.18 | Carbon | Titanium | 7° |
ENVE | Aero Road | 2024 | 5 | 170 | 1.18 | Carbon | Titanium | 7° |
ENVE | Carbon | 2014 | 4 | 120.1 | 2.07 | Carbon | Titanium | 6° |
Extralite | Hyperstem | 2024 | 5.6 | 82.5 | 2.16 | 7075 alloy | Titanium | 6° |
Extralite | Hyperstem | 2014 | 5.76 | 81.4 | 2.29 | 7075 alloy | Titanium | 6° |
Extralite | OC Road | 2014 | 5.26 | 87.7 | 2.25 | 7075 alloy | Titanium | 8° |
Far and Near | S1 | 2014 | 3.92 | 144 | 1.77 | 6061 alloy | Steel | 6° |
FSA | SL-K | 2024 | 3.7 | 144 | 1.88 | 2014 alloy | Steel | 6° |
FSA | SL-K | 2014 | 3.78 | 167.2 | 1.58 | 2014 alloy | Steel | 6° |
FWB Ti | machined prototype | 2024 | 3.7 | 149.2 | 1.81 | Titanium | Titanium | 7° |
FWB Ti | welded prototype | 2024 | 4.9 | 139.2 | 1.47 | Titanium | Titanium | 7° |
KCNC | Arrow | 2014 | 4.28 | 138.6 | 1.68 | 7050 alloy | Titanium | 7° |
KCNC | Flyride | 2014 | 4.55 | 127.3 | 1.72 | 6061 alloy | Steel | 5° |
MCFK | Carbon | 2024 | 6.8 | 92.3 | 1.59 | Carbon | Titanium | 6° |
Mcfk | Carbon | 2014 | 6.74 | 88.6 | 2.39 | Carbon | Titanium | 6° |
New Ultimate | Evo | 2014 | 5.3 | 110.8 | 1.7 | 7050 alloy | Titanium | 6° |
Pro | Vibe 7S | 2014 | 4.06 | 137.3 | 1.79 | 7075 alloy | Steel | 10° |
Pro | Vibe Carbon | 2014 | 5.24 | 138.4 | 1.38 | Carbon/7075 | Titanium | 10° |
Pro | Vibe Sprint Carbon (105mm) | 2014 | 2.69 | 199.4 | 1.87 | Carbon | Steel | 10° |
Pro | Vibe Track Carbon | 2014 | 2.73 | 186.9 | 1.96 | Carbon | Steel | 10° |
Pro | XCR | 2014 | 5.38 | 117.6 | 1.58 | 7075 alloy | Steel | 5° |
Race Face | Turbine | 2014 | 4.38 | 144 | 1.59 | 7075 alloy | Steel | 6° |
Ritchey | WCS C260 | 2024 | 4.7 | 108.1 | 1.97 | 7050 alloy | Steel | 6° |
Ritchey | Superlogic C260 | 2024 | 4.1 | 128 | 1.91 | Carbon | Steel | 6° |
Ritchey | 260 | 2014 | 4.81 | 113.5 | 1.83 | 7075 alloy | Steel | 6° |
Ritchey | 260 Carbon | 2014 | 4.67 | 128 | 1.67 | Carbon | Steel | 6° |
Ritchey | 4-Axis Carbon | 2014 | 5.73 | 120.2 | 1.45 | Carbon/7075 | Titanium | 6° |
Schmolke | TLO (ICR) | 2024 | 5.8 | 94.5 | 1.82 | Carbon | Titanium | 6° |
Syntace | F119 (105mm) | 2014 | 4.55 | 132.2 | 1.66 | 7075 alloy | Steel | 6° |
THM | Tibia | 2024 | 6.1 | 91 | 1.8 | Carbon | Titanium | 6° |
Thomson | X2 | 2014 | 4.2 | 146.8 | 1.62 | 7000 alloy | Steel | 10° |
Thomson | X4 | 2014 | 3.41 | 168.2 | 1.74 | 7000 alloy | Steel | 10° |
Tune | 4 | 2014 | 4.47 | 109.4 | 2.04 | 7075 alloy | Titanium | 8° |
Uno Stealth ti | 110 | 2024 | 4.5 | 104.7 | 2.12 | 7050 alloy | Titanium | 7° |
Uno Stealth | 110 | 2024 | 4.5 | 117 | 1.9 | 7050 alloy | Stainless | 7° |
Bonus stem stiffness content
Quoting Woznick again, “If you’ve made it this far, you’re probably quite interested in the topic in general. For some bonus content we decided to run a test of the same stem in 8 different lengths. You may be surprised how predictable the differences in the results really are.“
model | length tested | Deflect avg (mm) | Weight (g) | S/W |
---|---|---|---|---|
Uno Stealth | 60 | 2.91 | 90 | 3.81 |
Uno Stealth | 70 | 3.21 | 94 | 3.31 |
Uno Stealth | 80 | 3.59 | 98 | 2.84 |
Uno Stealth | 90 | 3.91 | 105.2 | 2.43 |
Uno Stealth | 100 | 4.22 | 109.5 | 2.16 |
Uno Stealth | 110 | 4.55 | 115.8 | 1.89 |
Uno Stealth | 120 | 4.88 | 119 | 1.72 |
Uno Stealth | 130 | 5.1 | 124.5 | 1.57 |
My Bikerumor Takeaways from Fair Wheel’s stem tests
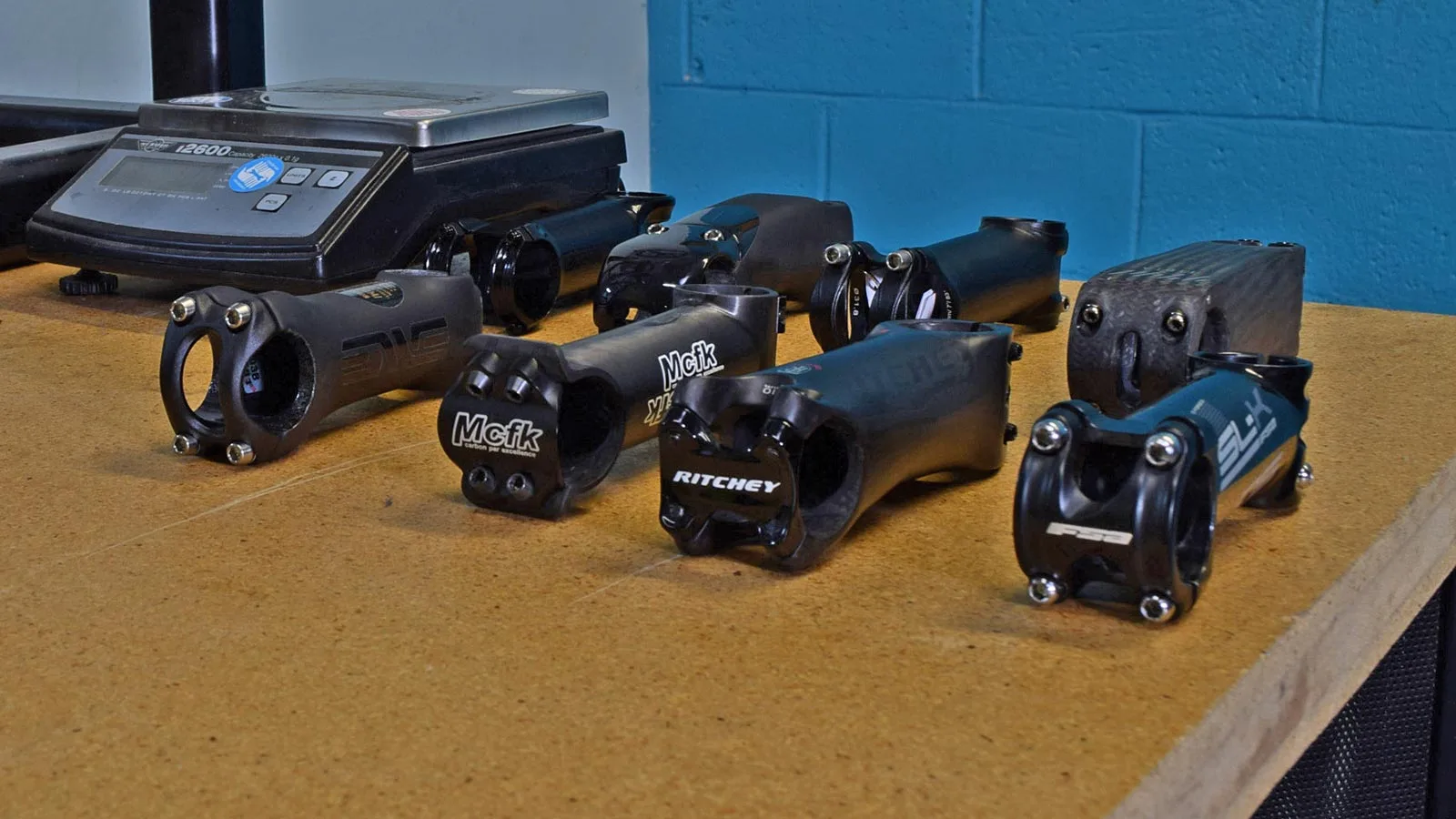
My first impression when looking at the new data and comparing it to the old was that on average the new stems are 7.1% lighter but 8.9% less stiff, giving them an average 2.7% decrease in stiffness:weight. Fair Wheel clarified a bit that we probably can’t so easily compare the figures overall, as the individual stems mostly fell in similar ranges. But they did note that new to the 2024 testing were some prototype titanium stems, which are stiffer, but also heavier, skewing the averages a bit.
It is hard though for me to overlook that there were already 8 stems in 2014 (out of 25) with ~4mm or less deflection, while only 2 were so stiff in the new 2024 batch (of 15). I take that to suggest that the industry as a whole might not really be trying hard to make stems stiffer, as much as they are trying to improve aerodynamics & integration.
On the other hand, looking closely though at like stems (Ritchey & FSA, for example where there are essentially the same models in 2014 & 2024), it seems the newer iterations are either a bit lighter or a bit stiffer. That fits with the idea that component engineers are trying to incrementally improve performance, even on basic components like stems.
Fair Wheel’s Takeaways
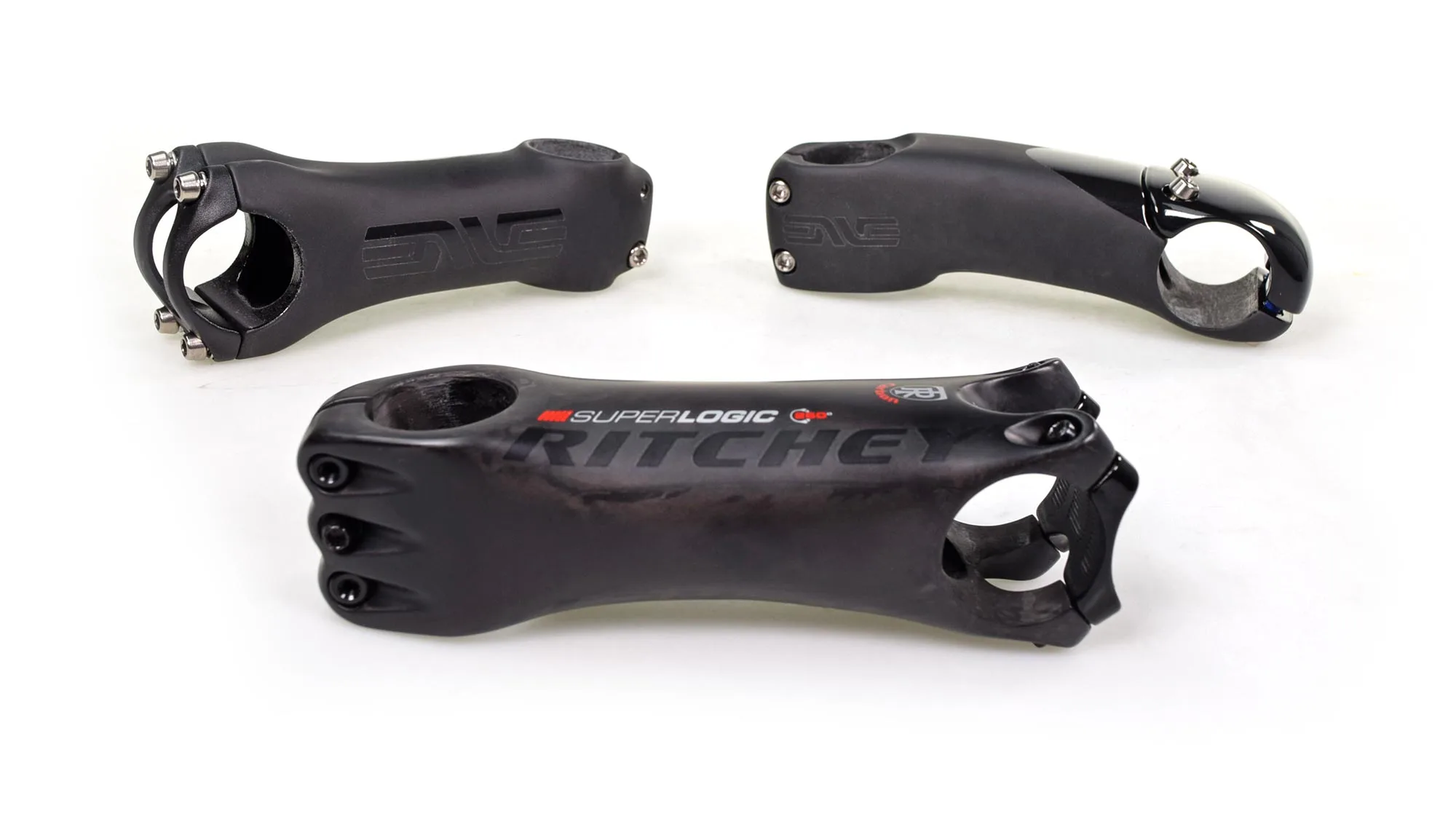
Jason Woznick of Fair Wheel Bikes did say that he sees, “that as an industry trend, stems have gotten disproportionally heavier than they have stiffer. This is likely due to more modern stems accommodating internal cabling. We plan on doing more testing with more internally routed stems to bear this out a bit more.“
Of note outside of just looking at the numbers, Fair Wheel also adds that their testing shows for road components “the more aero a bar or stem is the more compliant it will be since flat surfaces deflect more than a round one“. So that’s also a bit more context on interpreting their data.
Lastly, let’s all thank Fair Wheel for doing the work to help us pick what components we want on our bikes!
Complete Fair Wheel Bikes description of their stem testing process, in their own words…
Stem Deflection Testing:
We’ve once again brought back our favorite engineer, Jason Krantz. Jason’s a mechanical engineer whose graduate work focused on the intersection of composite materials and finite element analysis. Jason has worked for several companies in the bicycle industry and never fails to amaze us with the depth of his cycling related knowledge.
Disclaimer: A lot of typing and numbers have gone into this article and we apologize in advance for any typos should they happen, but would warn that the possibility of mistakes is present.
Some Initial Notes on Testing
Testing Method:
Each stem was mounted in the fixture and the testing performed 3 times and then averaged. All stems tested were 11cm with the exception of a few which are not available in those lengths. Each stem was mounted with its recommended torque specs and preloaded with 20 pounds of force applied 10 inches from the stem (about half way between a road bar and mtb bar) Once preloaded the equipment was zeroed and another 100 pounds of force was added and a measurement recorded. The measurement was taken at the point of load, again 10 inches from the stem centerline.
Loads Tested:
While the actual load doesn’t matter because the response of the structure is linear. [That is, a stem with a stiffness of 150-foot pounds per degree will deflect one degree with a torque of 150 foot-pounds and two degrees with a torque of 300 foot-pounds.] Jason selected a load of 100 pounds because it’s a nice round number, and pretty realistic to what some riders may experience.
For a sprinting rider, let’s say he is pushing on the left pedal with 300lbf (in other words, he can squat 600lbs). The pedal is about half as far from the frame centerline as the handlebar is, so it would take a reaction force of 150lbs at the right-hand bar to counteract the pedaling force. This is the same as applying 75lbf up on the one side of the bar and 75lbf down on the other; the moment at the stem is the same.
Normalizing for Stem Length:
In theory, it’s possible to measure a particular stem of one length and extrapolate its results to longer or shorter versions of the same stem model. In technical terms, this is “normalizing for stem length.” We can do this because torsional displacement is directly proportional to length for a tube of a given cross section. It’s true that a good engineer will use thinner walls on shorter stems (which see lower stresses) and thicker walls on longer stems (which see higher stresses). Still, normalizing to length within a single stem make and model is valid to a first approximation, at least with metal stems. A composite stem is a different beast, because layups (AKA laminate schedules) can vary significantly with length.
While torsional displacement is directly proportional to stem length, bending displacement is proportional to the cube of the length. Our first pass at a stem test setup measures combined bending and torsional displacement, so it would not be valid to extrapolate to longer or shorter stems, even within the same model, at least if you’re looking for absolute values.
If you’re interested in relative values–for example, if you want to know whether stem A is stiffer than stem B–then these results should be quite useful regardless of the actual length you intend to use.
For this test we used 11cm stems in every case except 2 (Pro Vibe Sprint Carbon and Syntace F119) which are both 10.5cm. The stems were similar enough in length that we did not normalize any stems in this test, but in the future we may test some stems that need to be normalized for a fair comparison.
Stiffness to Weight Ratio:
This was calculated using =((1/avg. defl) / weight) * 1000
Bolt Material:
One question we wanted to answer was if there was a noticeable difference between stems with titanium and steel bolts. We selected a few random stems and tested them both with titanium and steel bolts and found no meaningful difference in deflection in stems with one material over the other.
Mounting Direction:
We also wanted to see if mounting a stem with a rise vs a drop made a difference in the deflection. While we were able to measure a difference, less than 0.1 mm at 100 pounds, it was not enough to say that there is a meaningful difference, and was likely within the margin of error of the testing.
Notes about Stem Angles:
One other item we wanted to test was the difference in like stems with different angles. We tested a couple of stems that are available in both 7 and 17 degree angles and found that 17 degree stems deflected an average of 7% less. The tested stems vary from 5 to 10 degrees which should result in deflection variations of up to about 3%, so keep that in mind when comparing two stems of different angles.
Carbon Fiber vs. Aluminum:
Carbon fiber stems don’t offer the weight savings that, say, carbon fiber rims do. There’s a reason for this: stems are regularly stressed in three ways: bending, torsion and shear. In other words, the stresses in a stem are nearly isotropic (uniform in all directions). Carbon fiber is highly anisotropic (stiffer/stronger in one direction than in the others). When you try to lay up anisotropic carbon to deal with isotropic stresses, you end up with what engineers refer to as “black aluminum,” or pseudo isotropic carbon–and a weight that’s very close to an aluminum stem.
There may be other advantages to a carbon stem; vibration damping is one that is often put to the forefront of the debate. It’s true that composite structures generally damp vibration better than metallic ones, and there may be real-world damping benefits to a carbon stem. One way to test stem damping would be to wire an accelerometer to the stem and then strike it gently with a hammer, reading the accelerometer data to see how quickly the vibrations dissipated. This ring-down test may be on the Fair Wheel menu for a future article, but is outside the scope of this test.
Mixed materials:
Hybrid stems, a carbon overlay on an alloy stem. We tested only a couple of these but neither did well, we’ll do more testing on others in the future to develop our thoughts on this medium further.
We tested two similar stems one in full alloy (7s) and one in hybrid (vibe carbon) to see if there was an advantage to the hybrid stems. Both are the same weight and same dimensions with the same puzzle lock clamp. The difference being that the Carbon has thinner alloy, reinforced with carbon. Deflection was noticeably different, the full alloy was significantly stiffer than alloy/carbon.
To speculate on why tests put carbon/aluminum stems on the flexible end of the spectrum, one might consider two competing design constraints. First is galvanic corrosion. When aluminum and carbon touch each other, they’ve made a weak battery. The electron-swapping that goes on will cause an aluminum/carbon part to fail in short order. To avoid this, manufacturers use a layer of insulating material. This layer is often a fiberglass/epoxy composite but could be plain epoxy. Neither material is as stiff as aluminum, so you’re taking a stiffness loss right away.
Secondly, the market won’t tolerate a carbon-wrapped aluminum stem that is both more expensive and heavier than its plain-aluminum counterpart. So manufacturers are forced to use thinner-walled aluminum forgings for their carbon-wrapped stems than they do for their straight-up aluminum stems. Effectively, they’re replacing relatively stiff aluminum with relatively compliant fiberglass and/or epoxy.
Making matters worse, some carbon-wrapped aluminum stems use a 0°/90° weave for aesthetic reasons. This weave’s stiffness reflects the dreaded pseudo isotropy referred to earlier, and is particularly compliant in shear–which, in a stem, determines torsional stiffness.
The net result is a carbon-look stem that has adequate strength but more compliance (and possibly better vibration damping) than a “pure” aluminum stem.
To be clear, the above is what engineers call a SWAG: a Scientific Wild-Ass Guess. It’s a reasonable first pass, but there may be other factors at play that we haven’t considered and which will be further explored in future tests.