It’s somewhat hard to believe that in all of their years of making bicycle tires, this was the first time Kenda has held a press launch at one of their test facilities. But in a roundabout way, that’s sort of why Kenda was welcoming us to the new Kenda American Technology Center in Akron, OH. First opened in late 2015, the KATC was part of the first major step in revitalizing Kenda’s product range. The company is dumping a ton of money and manpower into state of the art engineering, development, and testing facilities, and this was their chance to unveil it to the world.
First started out of the garage of the current Chairman’s father’s home, Kenda started in 1962 with 50 employees and a focus on bicycle tires and tubes. Over the years, the company has grown to include tires of all sorts including motorcycle, car, tractor, and even golf cart tires, while simultaneously opening new plants in Taiwan, Vietnam, China, and Indonesia.
The story of the KATC begins in 2014 when Kenda hired Tom Williams as their Vice President of Engineering. Thanks to a huge range of experience covering almost every major tire brand, Tom was in the unique position of knowing exactly how to set up and grow a facility such as the KATC, which is still in an evolutionary state today. Literally starting the process out of the back of Martin Wheel in Akron before the building was purchased, the actual home of the KATC has evolved in phases with more machines and employees added every year since.

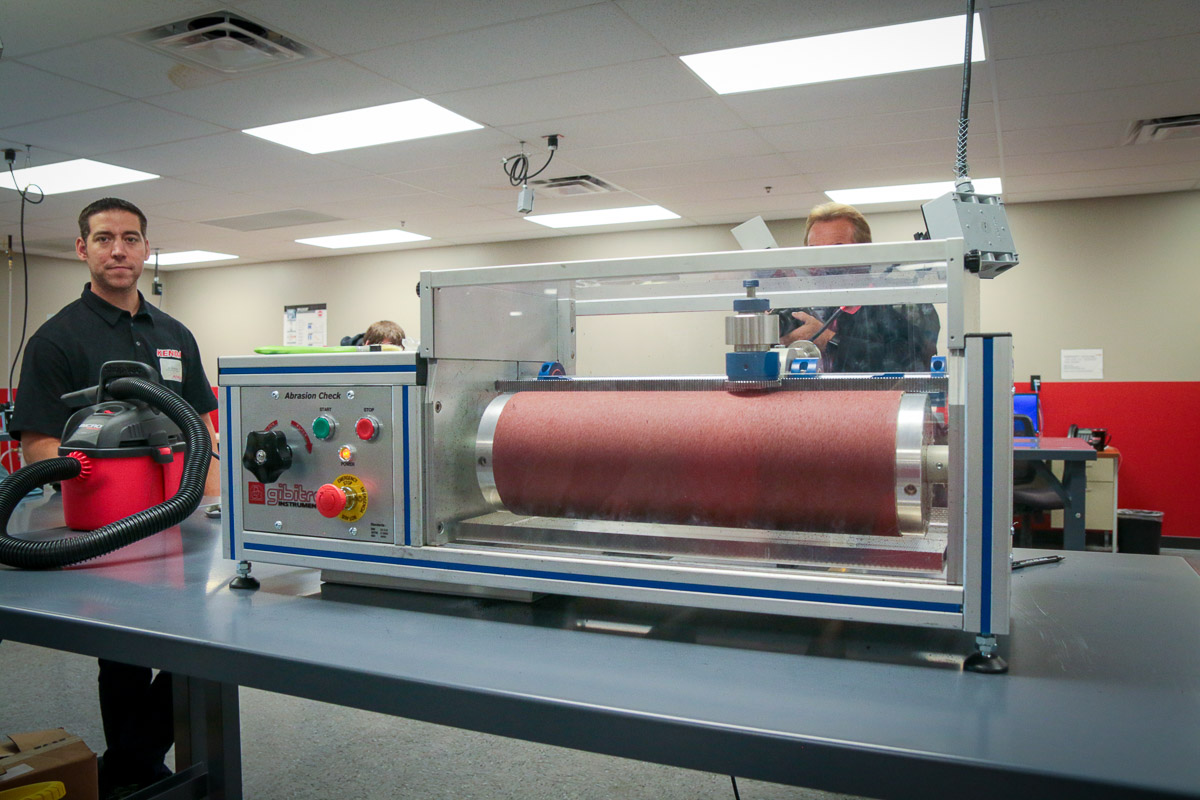
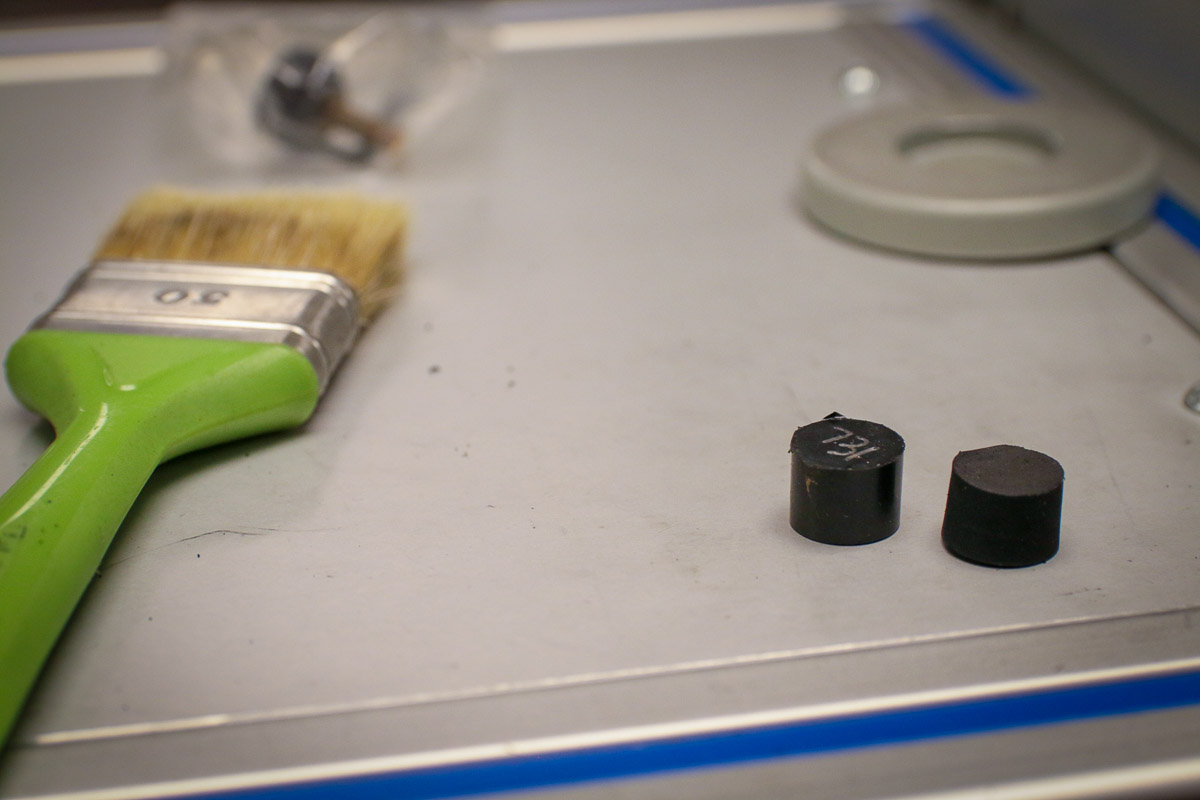

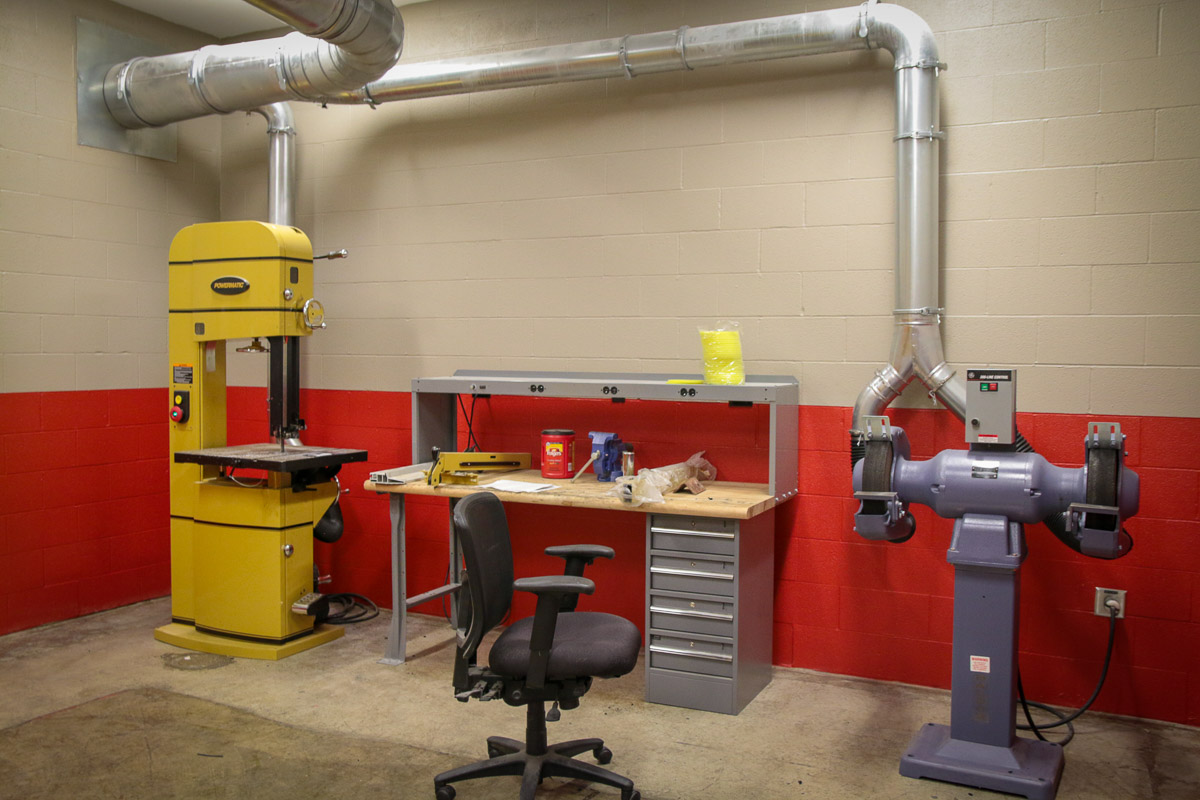
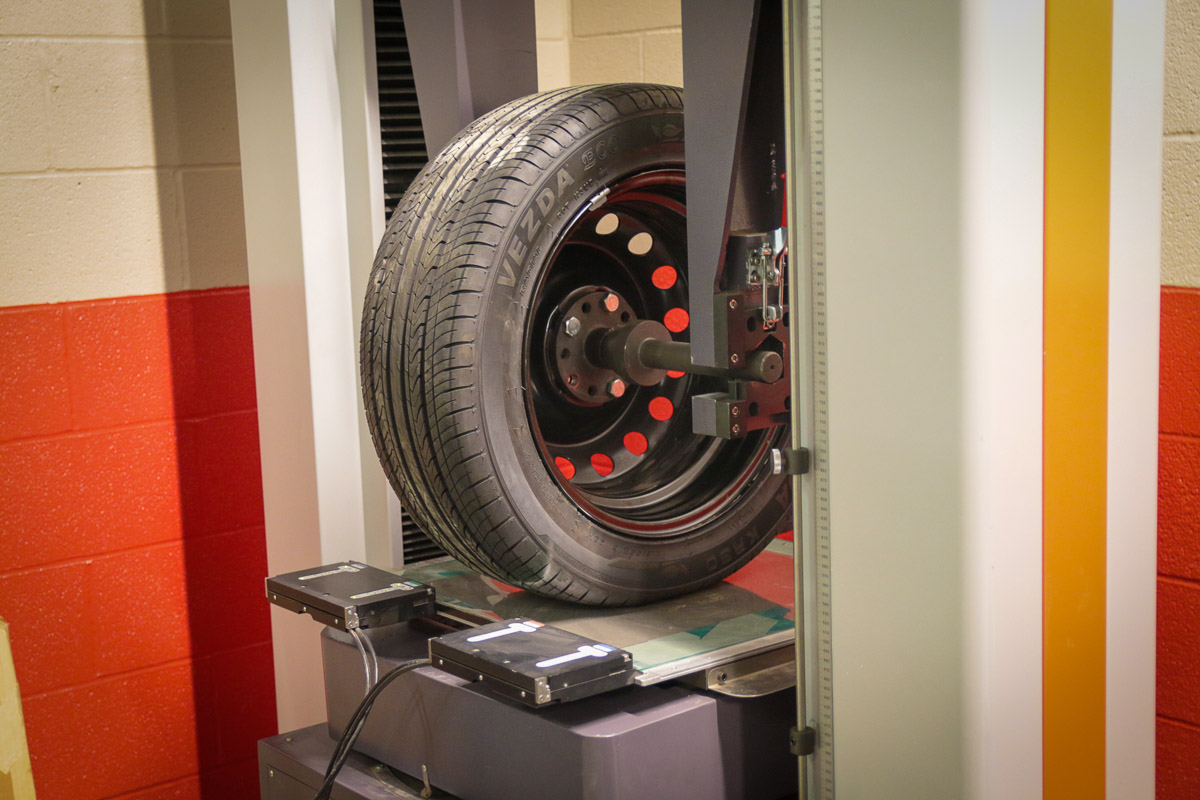
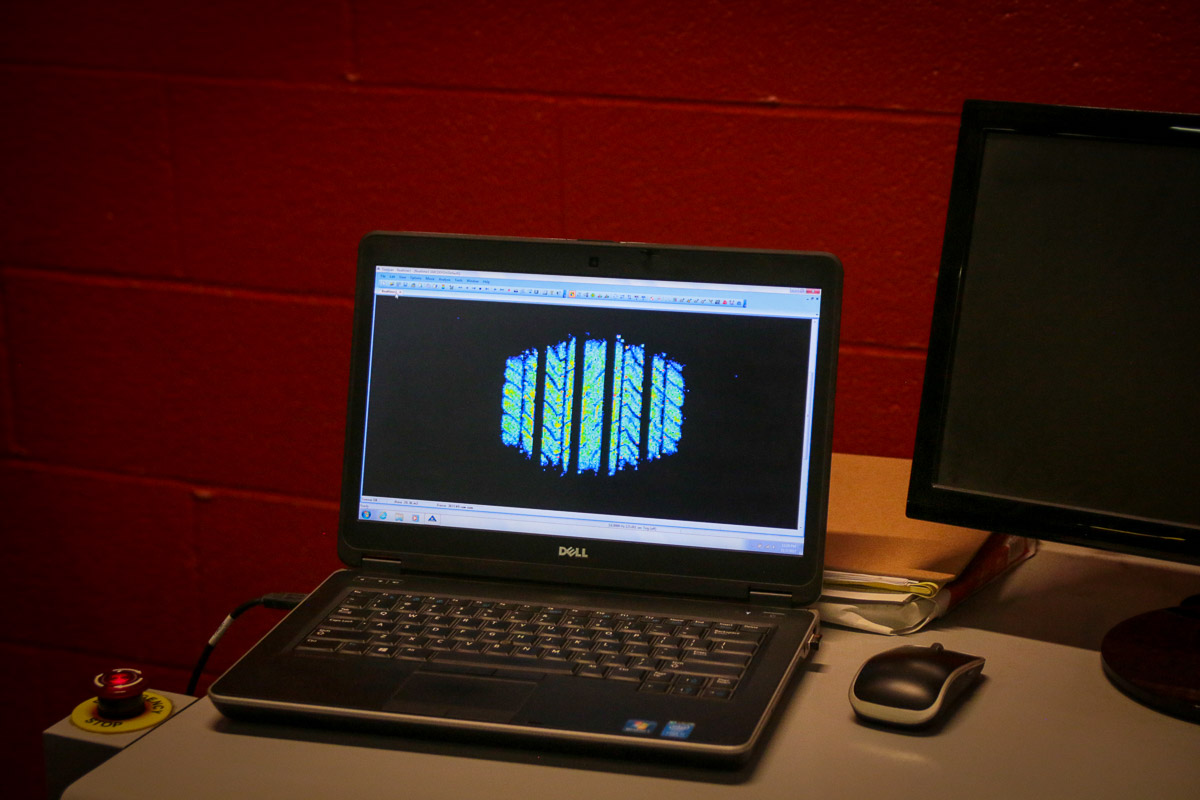
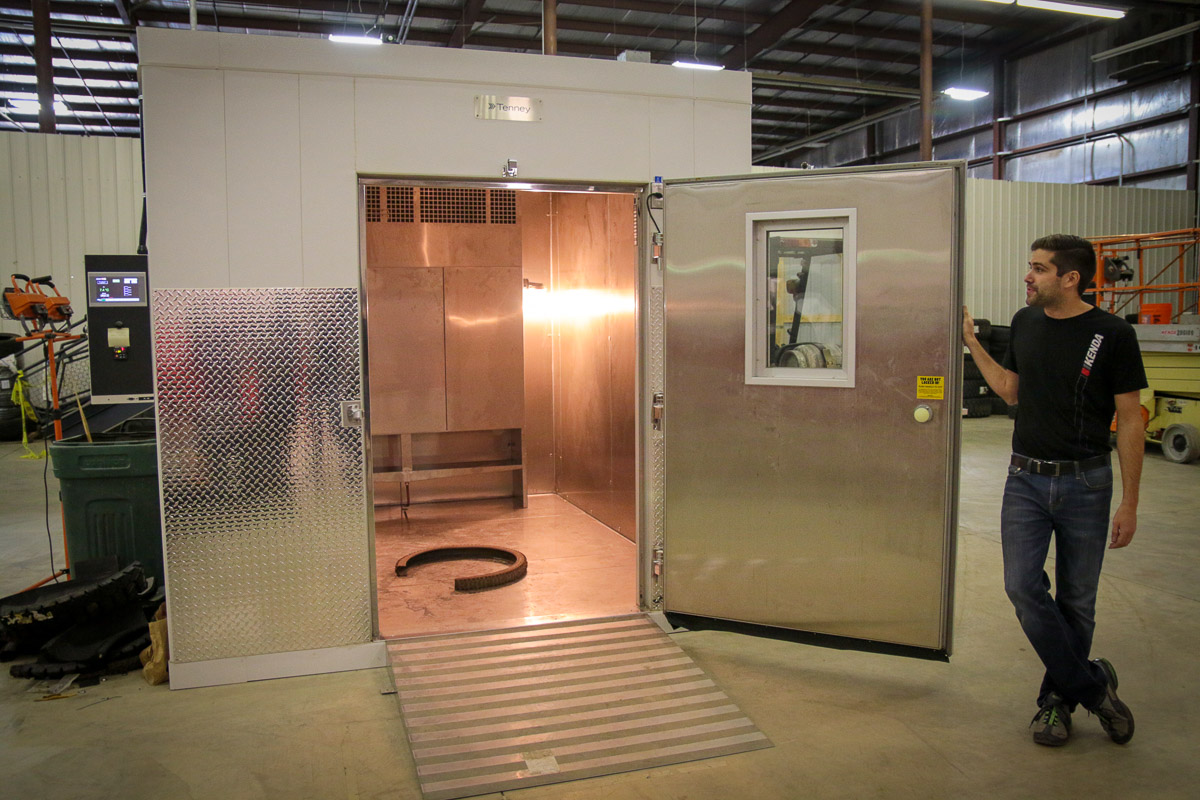
Currently, the 50,000 square foot building houses 32 employees with over 250 years of cumulative industry tires experience with almost every large brand. Of those 32 employees, only five are dedicated to the bicycle side, though Kenda points out that there are a number of engineers like those who specialized in compounding that work across all departments. Built with 18k square feet of office space, Tom expects the building to house up to 60 employees, with the rest of the space devoted to testing, warehousing, and other tasks.

One of the common questions seems to be, “why Akron, OH?” – especially, when Kenda already has a sales office in Reynoldsburg, OH which is about two hours away. For Tom, the answer is simple – Akron used to be known as the tire manufacturing capital of the U.S., and because of that the local colleges still have some of the most advanced programs when it comes to the science of compounding and polymer engineering. Stating that with the KATC close to the universities, prospective engineers don’t have to relocate right out of school which makes it easier for him to recruit top talent. It also happens to be located in a beautiful area with access to great riding and Ohio’s only National Park is about 30 minutes away.
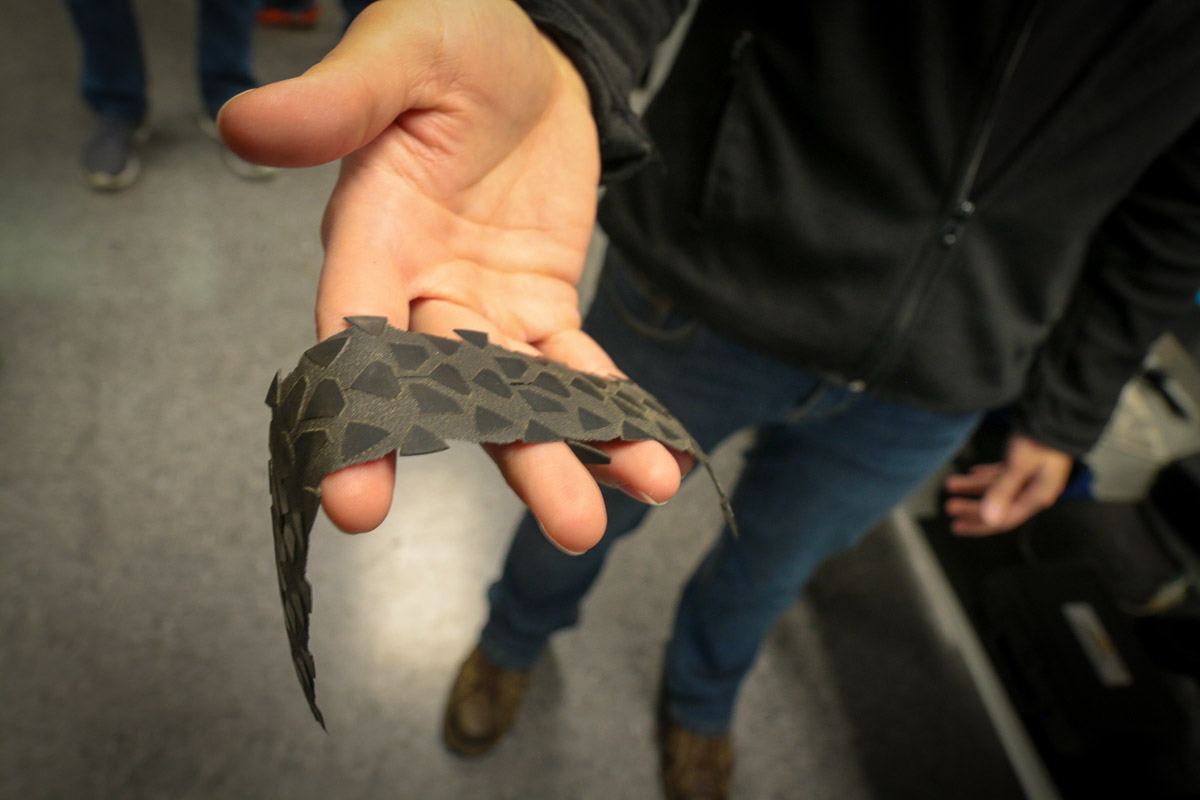
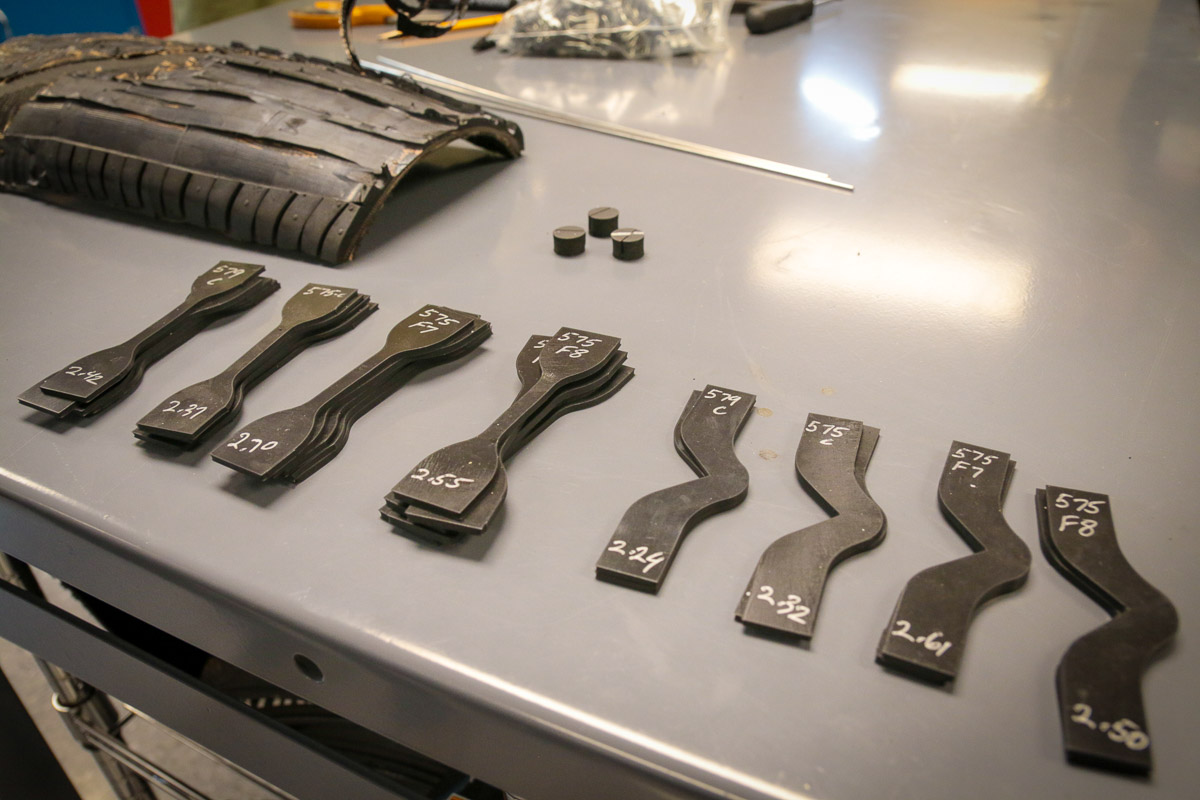
That same engineering talent has turned the KATC into a truly state of the art facility with an impressive array of machines. It’s easy to think of tire development as simply the construction of the casing, tread pattern, and maybe the durometer (hardness) of the rubber, but there’s so much more that goes on behind the scenes. That was immediately apparent as we were whisked through the full tour complete with enough acronyms and scientific terms to make your head spin. In phase two of the building remodel the compound labs (shown above) along with the High Speed Uniformity lab were added, which were then followed up with the endurance machine, tire carving, and air loss testing labs in phase three. Next on the agenda is the addition of a bicycle specific (BC) rolling resistance and endurance lab. If this wasn’t enough to highlight Kenda’s commitment to top of the line products, a new R&D center is in the works for Taiwan as well. With R&D on both sides of the pond, the KATC has two lead engineering groups, one for bicycle, trailer, lawn & garden, ATV/UTV, and motorcycle and the other for passenger car, light truck, and SUV. But the staff at the KATC is also tasked with collaborating with the Taiwanese R&D team to develop engineering tools and materials for better performance and development cycles.
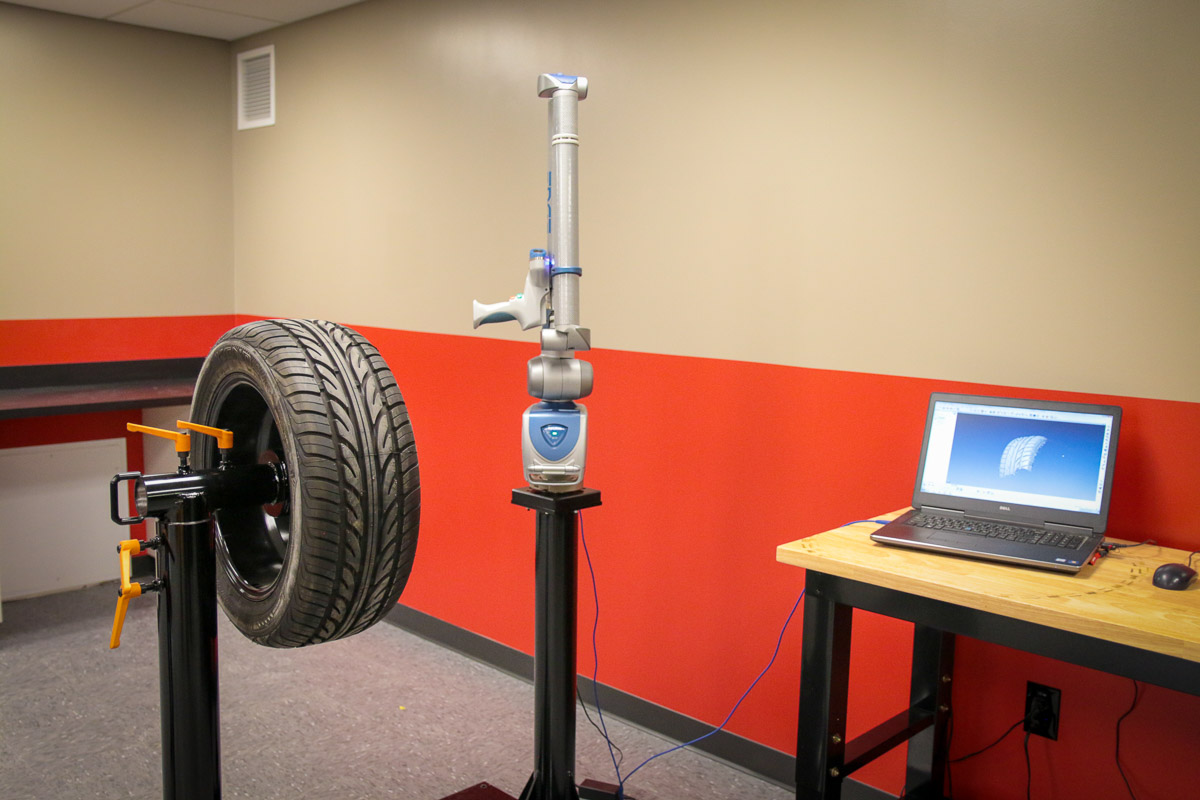
That pursuit of better development has led to the KATC to be the first office within Kenda to work with technologies like FEA (finite element analysis) for tread design. These days, FEA is quite pervasive in engineering, but for tire development Kenda says it was a lot harder to perfect than it would seem. Citing the fact that non-linear materials such as rubber are extremely complex to model, Kenda’s engineers had to test and measure the physics and material properties in order to create an accurate replication of an inflated tire. But the payoff was being able to see how a tire would react under load, how it would corner at a 10° angle, and how the tread would react differently to braking and acceleration – all without creating an actual tire. The program has resulted in decreased development times and the ability to get the performance they were hoping to get from a tire the first time it comes out of the mold.
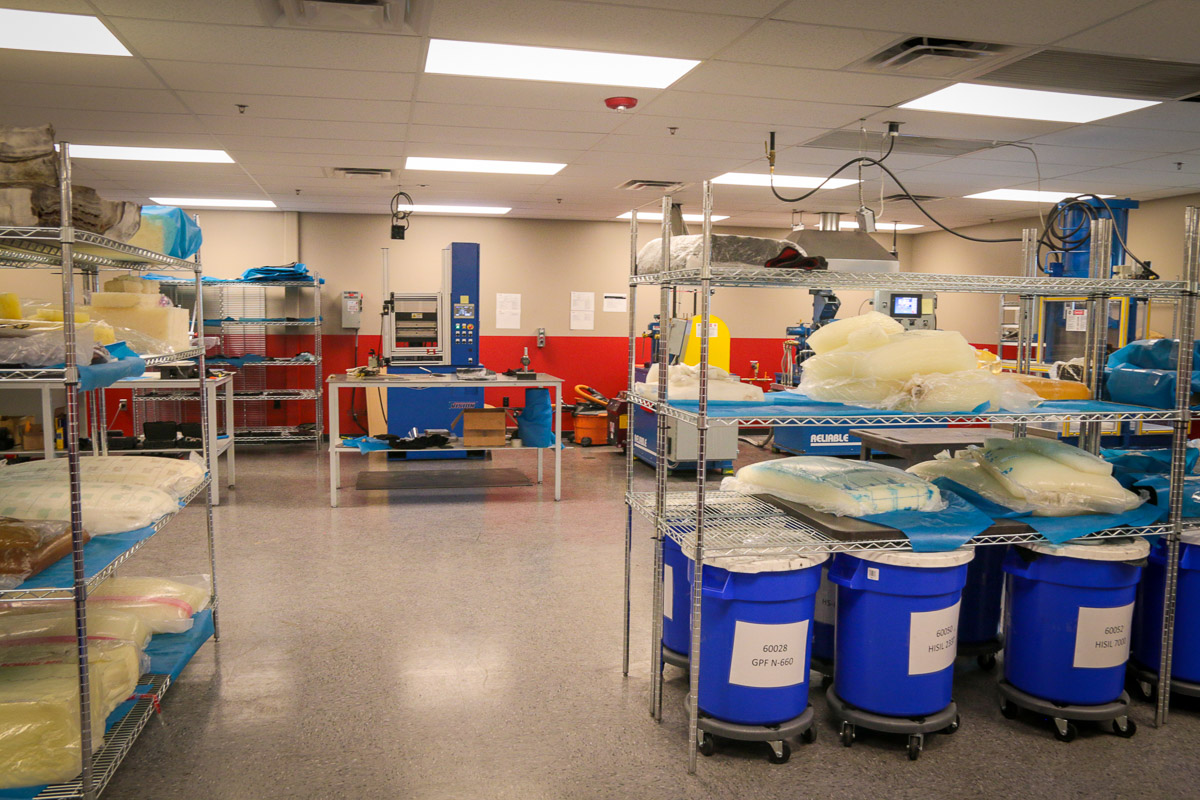
If FEA allows Kenda’s engineers to nail the design of the physical dimensions of the tire, the compounding lab is responsible for what goes inside the rubber. Just as important as tread design, the rubber compound will have a huge effect on how the tire performs. Using a battery of advanced testing machines, Kenda is able to perform complete compound analysis on-site and can predict how the compound will perform along – regardless of the tread pattern. Using a mixture of natural and synthetic rubbers, compounds are tweaked with the addition of silica, clay, resins, oils, and more which can produce different results. In the case of the new Nevegal 2, the new compound was designed from scratch which resulted in not only drastically improved dry traction and cornering, but also better wet traction overall and less rolling resistance.
It’s one thing for all of these traits to be verified on a roller or analyzed through a machine, but how they perform in real life is the ultimate test. Which brings us to the latest addition to the KATC – their new Bicycle Test Track.
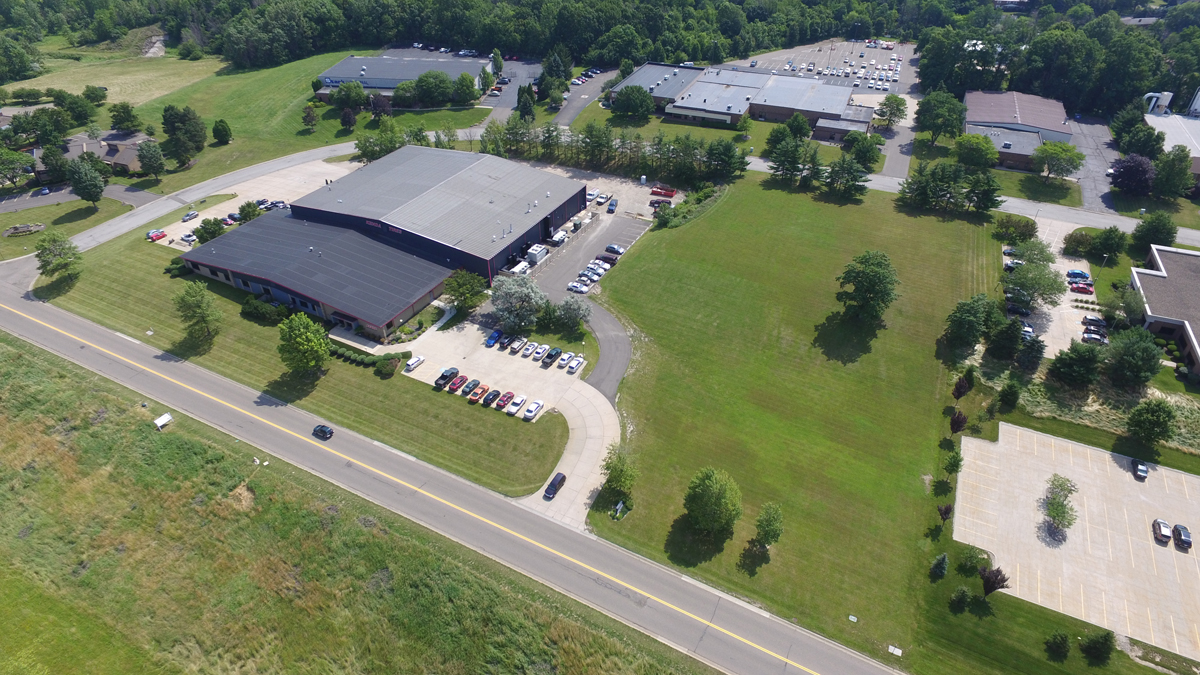

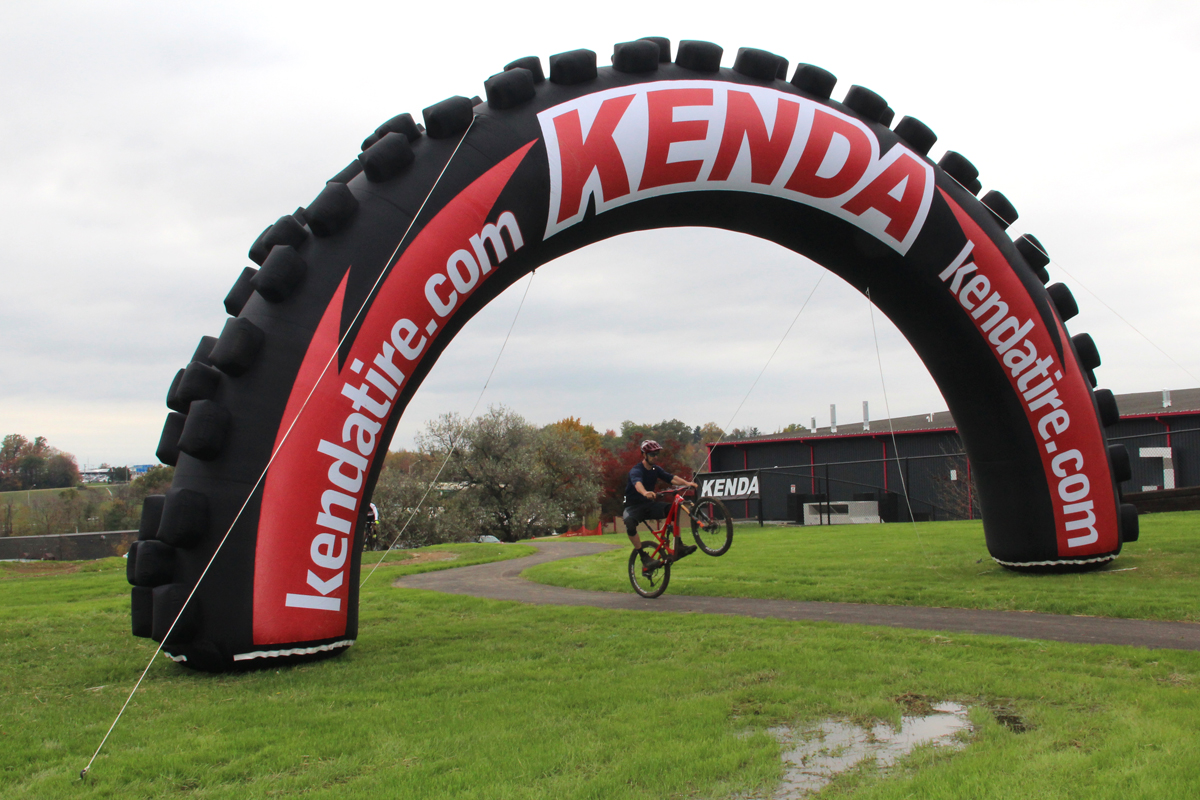
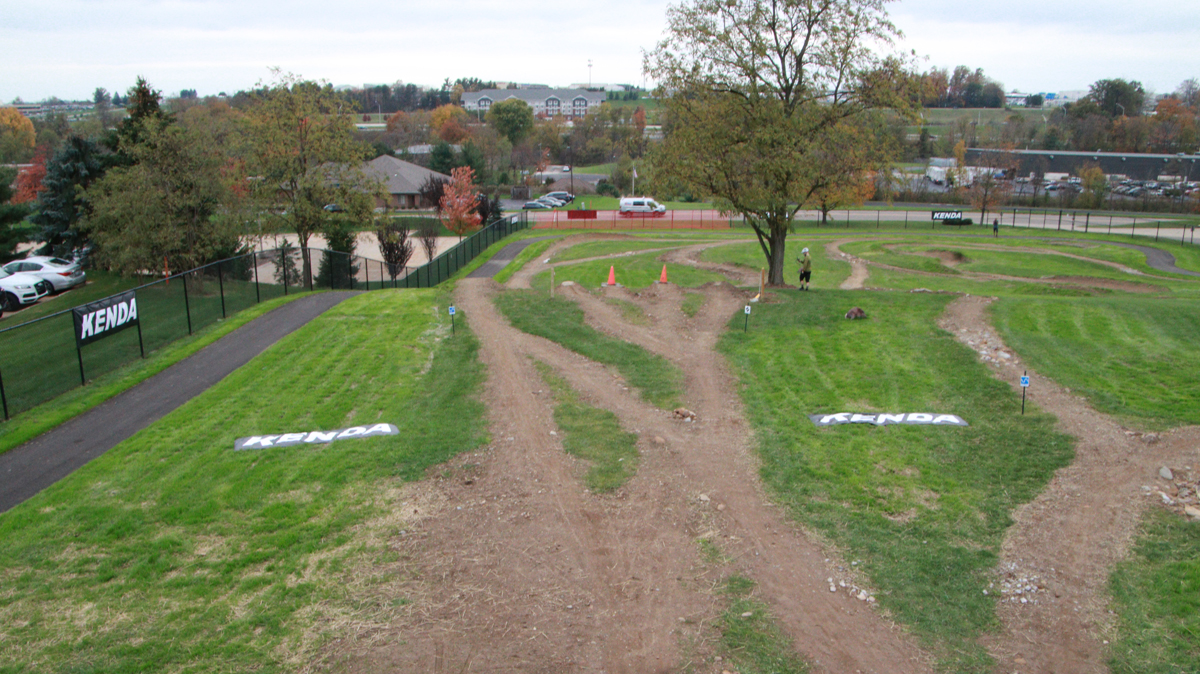
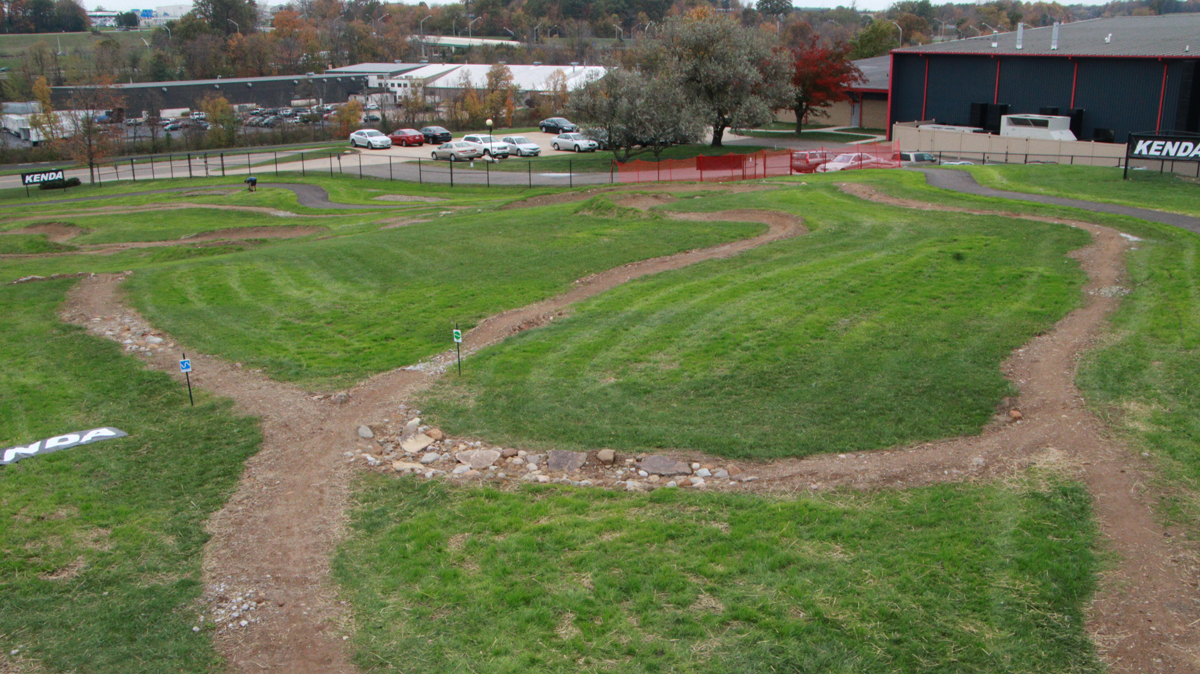
Who hasn’t dreamed of having their own test track in their back yard? Even though the track is certainly fun to ride, for Kenda it’s more about being able to test out the product without leaving the premises. Housed right next door to the main building, the Test Track features a number of different lines from green to black along with a paved outside loop that measures 1/5th of a mile. There’s also a sand pit, gravel pit, and a pavilion for the drop in. Built by Momentum Trail Design to test very specific things, there are a number of track features that you just wouldn’t want to ride on a regular basis. Things like a drop to square edged rocks that are planted in the ground and intended to cause damage to your tire and possibly your rim. Or reverse berms with the ground sloped the wrong way to force your tires to slide off the surface to the outside.
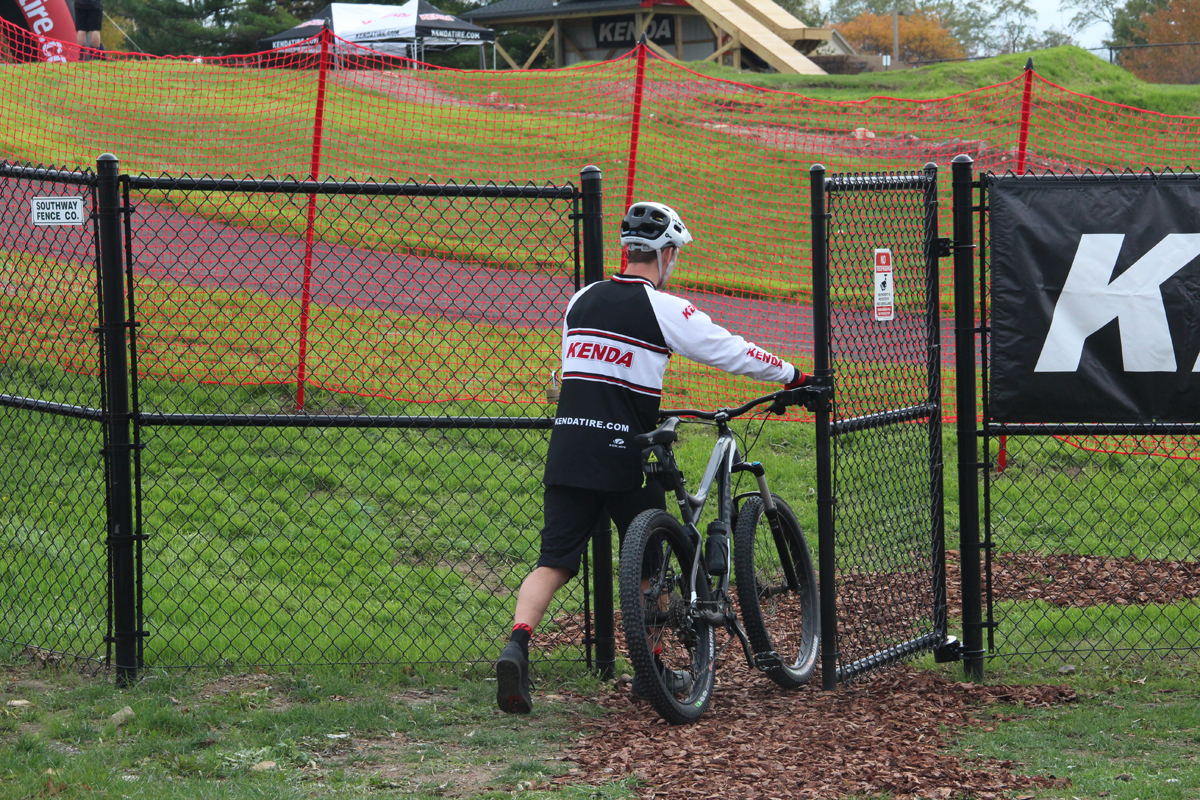
It’s clear after riding the course that the track was designed through an engineer’s eyes to recreate engineering problems when it comes to creating new tires. While Kenda will certainly continue to test elsewhere with their engineers and sponsored athletes, the Test Track seems to offer the unique ability to retain complete testing control and repeatable conditions which are critical to testing.
All of this just seems to reinforce the idea that with the addition of the KATC, Kenda is now more focused than ever and hell bent on creating the best tires possible.