Editor’s note: This is a guest post, written by a friend of the builder, so it’s a bit of a different format than our usual Road to NAHBS. We’ve paraphrased and edited it slightly for length, but the spirit of the article remains intact. We like it because it provides a bit of insight into what many small builders go through to not only build the amazing bikes we feature here, but what it takes (especially for foreign brands) to ramp up then stop work to travel for the show. Big thanks to Peter Kortvel for the submission, and James D. Shepperd for writing it. Enjoy!
Most of Bikerumor’s readers are familiar with NAHBS, the North American Handmade Bike Show, center of gravity for the burgeoning handbuilt movement. What they may not know is how these builders prepare for this annual coming out. Writing as an amateur builder and enabler of other lunatic builders, painters and cyclists, I wanted to take this opportunity to share what goes on in a builder’s head when he commits to showing his work to 8,000 people in a weekend.
Building custom frames for a living is no easy feat. Marrying the skills needed to build appealing, durable and safe bikes is hard enough. Add to that artisanal skills, marketing know-how, accounting and negotiation, and you will start to appreciate how much is involved in bringing the custom bike of your dreams to reality.
In the last few hundred hours of work and worry before the show, builder Brano Meres of BME Design is making an even more demanding journey to bring his bikes to NAHBS and to the world. Based in Bratislava, Slovakia – a former industrial hotspot behind the Iron Curtain in what was Czechoslovakia – he is meticulous. He is taking the painful and uncommon for custom builders route of getting all his frames and components tested to EN14764 safety standards.
I asked Brano, why go through the trouble of testing with such small numbers of frames? “Well, since I first started with frame building, I have had much of my joy from innovating new materials and processes that allow them to achieve -I hope- similar tolerances to mainstream materials.”
He is bringing two complete bikes to Charlotte, two types of laminated bamboo frames, and two titanium/carbon frames to NAHBS. All have faced “the rack”…
It must be noted that I first cooperated with Brano for the 2008 NAHBS in Portland, after hearing his story, I volunteered to help with US side logistics, and manning the booth after his long flight from Central Europe. Back then he brought 2 bikes and 2 frames…all basically experimental. This time, he’s headed for Charlotte, NC, with 2 production bikes and 4 frames demonstrating his passion for materials science and mastery of the testing lab.
B-9 Nighthawk
First up, the B-9 Nighthawk. Its styling reminds of the original Stealth fighter, the F-117 Nighthawk, the bike is black… almost radar absorbent. Any eye that falls on this will be captured in its dark gravity. With flat paneling it looks like a veiled threat.
If you remember the 1st time you saw the Stealth Fighter and said “WTF” to yourself…that is the feeling inspired by these frames. A single speed -for now-, it will feature proprietary items including a one piece carbon stem-handlebar combination, carbon fork, seat and seat mount as well as its own designed matching crankset. In all its minimalist glory, he says “It’ll have to be tested, with each component making the grade…or not.”
I call it the “rack” cause it is in fact a hi-tech torture chamber, subjecting each component to the tests, eg. during the fatigue test of the frame, 100,000 test cycles of repeated downward pedaling force of 1000 N is applied to each pedal spindle. Another favorite includes the frontal impact test where the frame fitted with the front fork takes an impact of falling striker of mass 22.5 kg.
The first round of frames tend to be overbuilt (Who wants to destroy their own work?). After all, an independent builder is putting a lot on the line. On March 5th, the Nighthawk and all its parts passed.
LamBoo… A long awaited return to bamboo
Next up in the “Rack”, new laminated bamboo from BME Design. Brano’s company makes a long awaited return to…Bamboo. Having already qualified his “natural” frames to meet EN14764 in 2010, you’d think he’d be satisfied with his process control. But since then…he’s been back to the drawing board for Bamboo.
Enter LamBoo, nothing to fry your brain over, BME designed and developed laminated bamboo tubesets. Well how does it hold up in the rack?
Brano’s original tests on frames with natural tubing were done under real conditions and on the race circuit. The original design endured 7 years of hard use including a summer season with several MTB marathons. Facing the durability challenges thrown up by using a natural material, Brano opted to pursue the CEN certification for the second generation of frames to make sure he had it right.
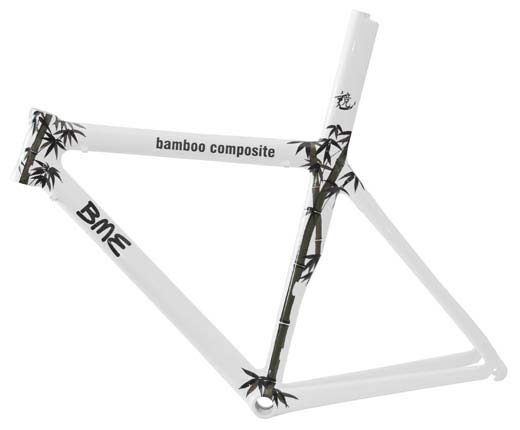
So began Brano’s quest for CEN’s certification. This was followed up by sending another pair of frames from Bratislava to Arizona for further abuse. After trying various experiments with bamboo textiles laid up like carbon fiber, at the end he turned to laminated bamboo, (therefore the name LamBoo) to control and adjust the strength, durability, weight and flexibility. The development of this laminated bamboo tubes material took to Brano almost 2,5 years.
Well, as of the 8th of March the Lamboo, BME’s 3rd generation Bamboo technology, passed and is cleared for take off to the show.
With the EN14764 quality stamp affixed and the process control used to gain the result ingrained in the builders head. All that remains is to set up at NAHBS. See you in Charlotte!
Look out for other exclusive photos of the LamBoo, Nighthawk and other BME frames at NAHBS on BikeRumor.com and Kortvel’s site Bikestein.com. Or follow along on Twitter at @IamBikestein and @bikerumor.
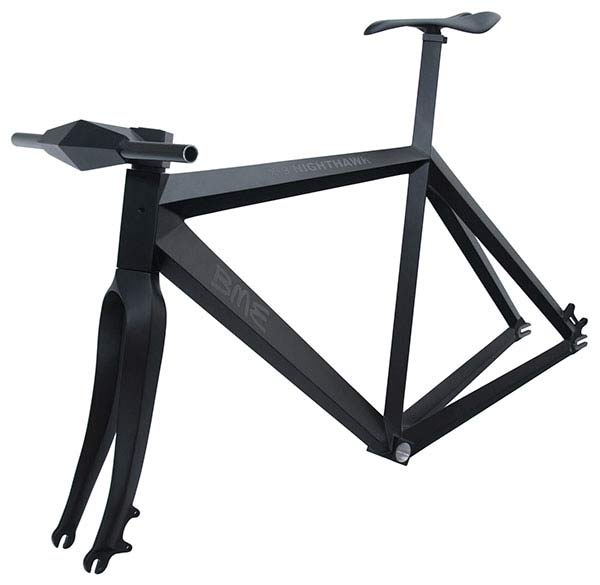