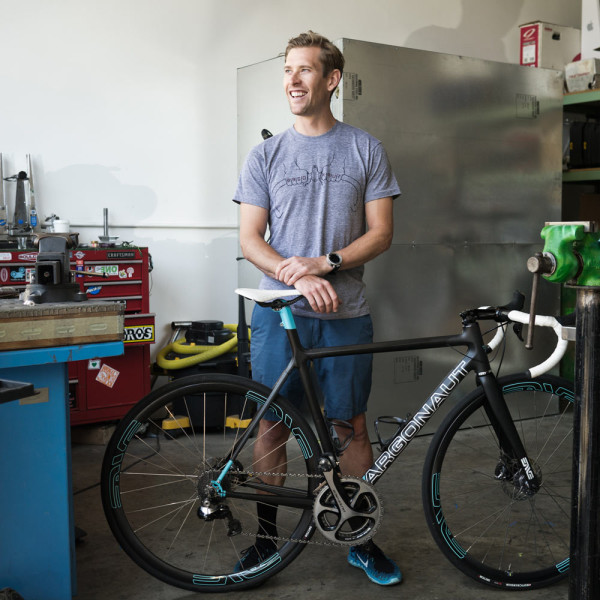
Ben Farver has an origin story in two parts. He started Argonaut as a steel custom frame outfit, first with TIG welded frames, then brazed frames. Despite early recognition of his work in steel, Ben made a sudden move away from the material to carbon only a few years into forming his brand. From the perspective of many who labor in metal, it was a polarizing move leaving many feeling like he was dismissing the material that they love.
But for Ben, this could not be further from the truth. Steel, in his mind, would never be able to give him the depth of control over the design and feel of the bike, and it would never allow him to make the contribution to the industry he wanted to make – not like carbon could.
In this phone interview, Ben discusses the initial journey into frame building, as well as his drive to accomplish the deeper level of personalization and material performance that compelled him to create his new approach to custom carbon frame fabrication…
BIKERUMOR: How did you get into bikes?
BEN: I grew up mountain biking in Aspen. I had a Gary Fisher Paragon aluminum frame and the summers I moved back to Iowa to stay with my parents. That’s when I worked at Iowa Bike & Fitness and got super geeky into it. Spent all the money that I made building up an Ibis Mojo with the Manitou fork with the carbon crown and 3cm of travel. I still have that bike. That was really my first kind of foray into really understanding how different bikes rode. The old aluminum Paragon was so harsh and jarring. Going to the Ibis Mojo was such a different experience mountain biking.
That was really where I got into biking and riding steel bikes. And then I really took a hiatus from being a bike nerd for a while after high school. I went to college in San Diego and got a degree in History and was surfing a ton. After college, I got into metal sculptural welding, essentially. I took some classes at a local community college and just got really into metal working.
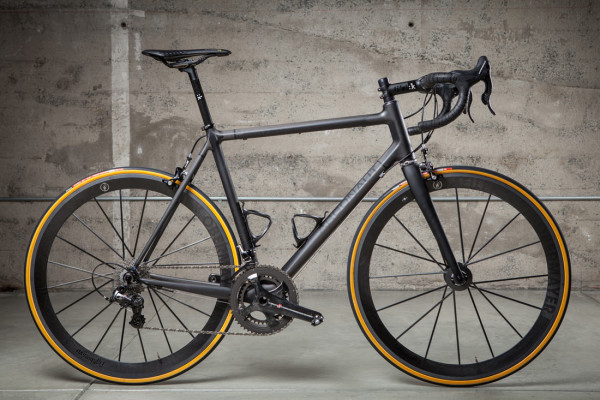
BIKERUMOR: So you have these experiences. When does this transfer over to bikes?
BEN: At that time, my wife and I moved to Portland. I was riding road bikes. I guess that was 2006. I had a fixed gear, you know, just sort of one of those. All the things in the universe kind of started to absorb into the frame building bicycle culture in Portland. I got turned on to custom frame building and as I was getting into metalwork, I was like oh man, this is awesome, this is what I want to do. I was super inspired by Tony Pereira, Ira Ryan, Sacha White… all these Portland bike builders. And I decided that that is what I wanted to do.
So I went and took a frame building class from Steve Garn who used to make BREW bikes in North Carolina. He taught me how to TIG weld steel frames. I came back to Portland and I rented a small shop and bought a Bridgeport and an old Miller TIG welder and basically went after it. I started TIG welding, TIG welded a few frames, figured out that my bead would never be as good as Jeremy Sycip or any of those really high end custom TIG welders, and I started brazing and found that I really liked and preferred brazing over TIG welding.
BIKERUMOR: Are you talking lugs? Or fillet brazing?
BEN: Both. I just started building bikes for myself and my buddies and really enjoyed it and had a hand in it. I started getting really proud of the stuff I was putting out. I had a little shop in Northeast Portland on Martin Luther King, and that’s kind of where Argonaut started in late 2007, early 2008. Built bikes for friends at a discount, then started charging more, then selling bikes to people I didn’t know, and as the progression goes with most custom frame builders, that’s really how I started.
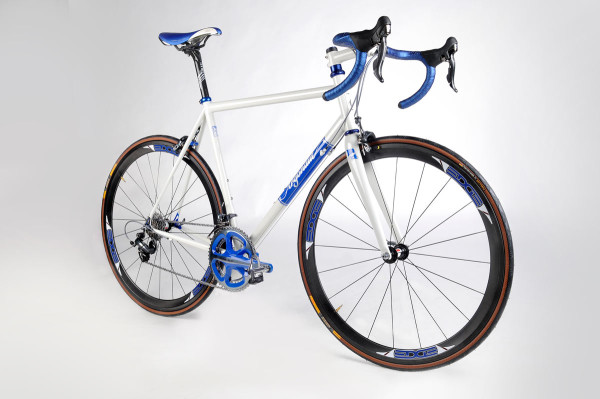
I didn’t really start progressing or getting to the point where I was doing something kind of unique and interesting until I started working next to Andy Newlands of Strawberry Bikes. He and I had become friends and he asked me to come work in his space. That was really cool because up until that point I was getting by, but potentially, you know, doing so many things wrong. And he’s been building bikes since the early 70’s. He has this huge garage with a lathe and a couple of Bridgeports and just watching him make bikes and having him teach me how to really machine metal properly, you know, building a proper bicycle, really, is really where I felt like I was contributing something to the custom bike world rather than just faking it to make it, if that makes sense.
BIKERUMOR: Well, you have to fake it to make it for awhile, right?
BEN: Yeah! Exactly. Totally.
BIKERUMOR: See, that’s interesting. You run into people or brands who are just making something to fit a price point or to just exist at all in the industry. Then you have these other people who are on a completely different level, who are like “I want to contribute to the dialogue of cycling,” and that was you very early on. That’s pretty unusual. What put you in that mindset so early?
BEN: Well it’s – I figure it’s just a struggle for legitimacy, really. My class of frame builders in Portland at the time was really fad-driven in a lot of ways. You know? Be a bike nerd and wear tight pants and ride a fixed gear bike and make some frames. It was cool and it was authentic in the grass roots part of it. At the same time, there was so much sameness.
There was a desire to transcend that sameness and be something and do something more than just the sort of “craft du jour” of the time. To me, that was understanding the history of bike building. That was understanding where things came from and then how to feel legitimate in that circle means contributing something new, and not just copying stuff that’s out there and rebranding it or repainting it or putting it in cool colors or making it all stainless. It was a desire to earn my place among my peer group.
BIKERUMOR: Yeah, that’s interesting… I don’t think about that a lot with Portland as a context. I could see how that supersaturation could sort of drive you to look elsewhere.
BEN: Totally. I think that at one point there were twenty builders in Portland.
BIKERUMOR: There’s got to be more than that…
BEN: There was a contraction for sure after the 2008, 2009 recession. Before that, it was insane.
BIKERUMOR: So you’re building in steel and clearly, clearly you had an early epiphany moment about materials with your Ibis Mojo.
BEN: Yeah, Exactly.
BIKERUMOR: Did that at all influence your shift in materials? Because in early 2011, you kind of just shift. That’s when you start building in carbon.
BEN: That was a time when I sort of took a step back and looked at my operation, what I was doing, and then also, my peers. That was the point where I had a backlog of customers to make frames. I was making them inefficiently. Like, okay, enough screwing around. Is this going to be a business? Or is this going to be a hobby? And taking that hard look, I figured out that was going to be really hard to make a viable business as a craft, one-off steel bike maker. The numbers, in any industry you look at your peers, who is the most successful one and how successful are they. In Portland, who is the most successful builder and arguably it’s Vanilla and Speedvagen. And that’s commendable and enviable business for sure, but it isn’t like Sacha is bringing home 250k a year.
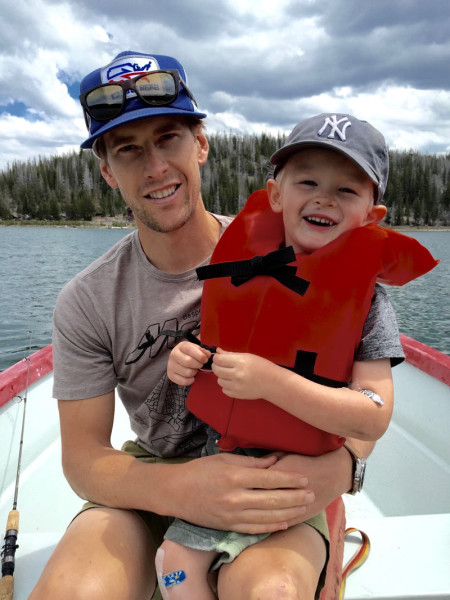
I’m not saying I’m doing this to get rich. But at the same time, you become an adult and you go, am I going to have kids? Am I going to send my son to college? And it was very apparent to me that, you know, the one off custom steel model was not viable long term as a career choice. At the same time, and sort of conflicting with that, I was frustrated with the sameness of my bikes to all the other steel bikes out there. Even TIG welded bikes were all buying their tubes from True Temper, Columbus. Columbus Life… OS Platinum… same configuration stuff with slight variations under paint. When it comes down to it, you know, after all the hand-waving and custom geometry and tube set and configuration, there’s not all that much differentiation. I found myself not having a very clear argument over why you should buy an Argonaut over a Perrera or an Ira Ryan or the litany of other builders across the United States.
It’s a shitty business model and my bikes are pretty similar to everything else – made me look to another material to make it work.
BIKE RUMOR: That philosophy – was it something you had along before entering it? Was it a sentiment that you developed or was it something you strived for off the bat? Did you strive to make your steel bikes an exception and hit this wall? Or were you just not seeing the opportunity in the material – like, it wasn’t a big enough jump for you?
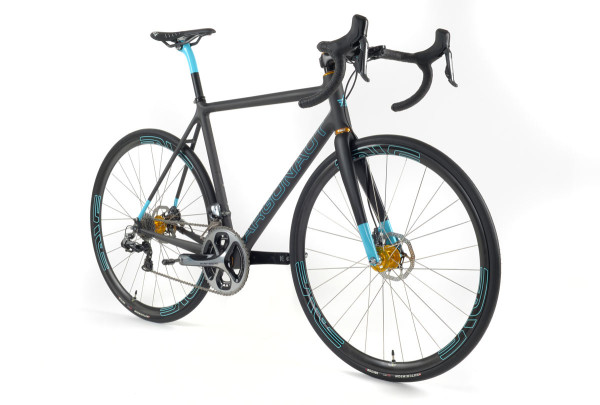
BEN: I was motivated by the race-style road market. That was really my niche in custom steel building – and ‘cross. When you get into that more performance focused, that weight focused – for me, bending tubes or hand-carved lugs or doing a custom set of butted tubing even from Columbus – it didn’t quite get me all the way there because I also wanted to be able to argue my race style road bikes and be able to argue their validity against production race bikes, essentially production carbon race bikes.
I felt that I could argue my bikes over other custom steel bikes and my fabrication mode and welding methods and my tubeset choice and geometry choices. But then when it really came down to it, going into River City and plopping down an S3 fillet bike against the new Venge or something, it’s a lot more difficult argument to make. And that’s where I also started to get frustrated.
BIKERUMOR: Sure. Totally get that. So why carbon? You jumped completely out of metal. Completely.
BEN: I had sort of successful and failed design ventures. Like I started to venture more into stainless stuff. Like silver brazing with stainless 953 as a way to explore different materials. Nobody was really doing much of it, so I sent some frames to fatigue testing and found that stainless is extremely unforgiving, that the juice isn’t worth the squeeze.
I got in touch with Rob Vandermark who was a huge resource for me at that point at Seven and chatted to me about some of the testing that they were doing. He basically said it’s kind of not worth it for the headache. And at the same time I started doing more, I got into heavier dropout design. On a steel bike, that’s one of the ways where you can focus and drive innovation in terms of both materials and aesthetics and usability.
BIKERUMOR: It’s the easy way to differentiate your stuff from everything else.
BEN: But that was super fun for me. I got into figuring out how you can do it with machine parts. Incorporating different kinds of metals. We came out with that two part dropout system with the titanium inserts. Being able to run single speed, geared. Horizontal and vertical dropouts for cross I thought was really cool. So that was, from a design standpoint, a really successful foray.
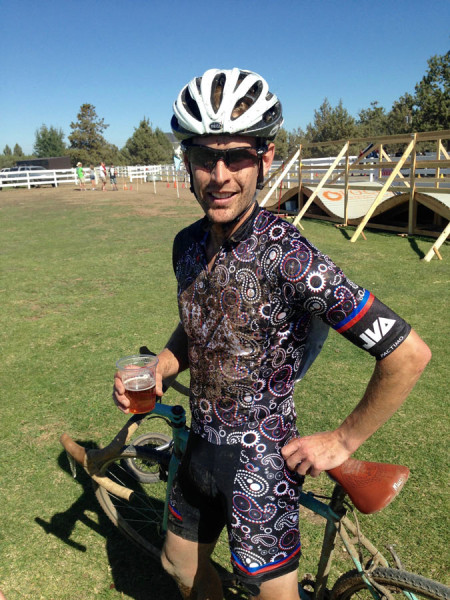
Dropout design, that innovation, I was super stoked on those and I was like, I can come up with new stuff and innovate and make it and it can work, potentially. So those two things at the same time where I had this sort of thirst and desire to innovate and design and have more control over the full fabrication of the frame and at some point along the way a sort of lightbulb went off for carbon and composites. There is way more ability to do that on a small scale more one-off basis than there is with steel because it’s much more sort of like, it’s just newer, you know? There’s not as many people doing it. You can, what I started to learn about was different layup patterns for different tubes for the bike. The anisotropic properties of carbon versus metal. The more I looked into it, the more excited I got.
BIKERUMOR: It’s a “choose your own adventure” material. So coming from metal, there’s just so much negativity around carbon, especially in the community you were in. Did you run into it? How did you face it?
BEN: Yeah, you know, I guess I didn’t really feel that negativity about it at the time because by that time I had sort of tired of the “steel is real” cliche and saw through it a little bit. People that I respected in the industry were those that were making stuff really well and weren’t necessarily that concerned about beating the steel drum. I don’t know. I didn’t really feel that much push back, or I didn’t care, or I think I had just sort of become, I wouldn’t say disillusioned… the artist-in-steel craft just wasn’t as shiny for me as when I started out, you know? The realism of that industry and seeing people that had been in that side of the industry for 20 or 30 years, both in Washington and Oregon and across the country, made me a lot more realistic about the whole thing and not care as much.
BIKERUMOR: So it sounds you were all about the forward momentum, rather than being sentimental of the material or bummed about its limitations. Like, carbon is the next thing, this is how I can do my high performance product.
BEN: Totally. It was, “I think I can make this mine. I think I can contribute something new and innovative where other people haven’t… and what I’m not able to do with steel.”
BIKERUMOR: Fantastic. So how do you even get started with that?
BEN: Right?
BIKERUMOR: So you call up ENVE and go, “Send me some tubes, bro?”
BEN: Yeah!
BIKERUMOR: Really?
BEN: Yeah! At that time, there were a few other custom builders that had ventured into carbon. One of which was Carl Strong. Another was John Slawta. And also Indy Fab with their Corvid. Your question is exactly right. So I want to make custom carbon bikes… how do I start?
BIKERUMOR: You need your tube kit.
BEN: Exactly. I looked at that. There are sort of off the shelf kits you can get from Columbus and Dedacci of custom tube sets. But I very quickly saw, in looking at Carl Strong and John Slawta in how they were buying tubes from ENVE or Dedacci, of all of a sudden being in the same situation I was in with steel but with carbon, you know? Like, buying tube sets, picking the right ones. Getting the fabrication down, then selling a different version of the Strong or the Slawta or the Crumpton, essentially, you know?
I figured out that the opportunity was to make custom, bladder molded or monocoque-style frames. And I decided that that was the opportunity to make something new that nobody else was doing, and also had a lot more barriers to entry and also had a lot more control over how the bike rode. I had a lot of conversations with ENVE and the engineers there, and sort of had a handshake agreement that we would do a similar project that they did with Indy Fab on the Corvid.
So I started going through design options and at that point Aaron Hayes of Courage bikes in Portland is a good friend of mine, and he has a really good industrial design background and so he was helping with a lot of surface modeling to sort of figure out how do you figure out this puzzle of making molded-style frame assemblies, complete bottom brackets and top and downtube and seat tube pieces. Like the larger production companies do, but not in an overly capital intensive way, where you’re spending hundreds of thousands of dollars on one size, which is the key piece of the puzzle.
So as the progression went, I got so far with ENVE and went out and saw them in Utah and it turned out that they had a pretty big engineering hangover from the Corvid project with Indy Fab, and they were sort of like, “that was a lot of work…”
BIKERUMOR: “We’re not stoked anymore.”
BEN: Yeah, you know, and I come along, like “hey guys! I want to do that too!” And at one point they essentially stopped answering my phone calls. So this was like an 18 month process from when I said, “Hey, I want to make carbon bikes,” and seeing the DIY options out there, deciding I didn’t want to do those…
BIKERUMOR: No bamboo, huh?
BEN: Yeah… that’s a whole other thing. And, you know, sort of, if I’m going to do this, I talked myself out of continuing to make steel bikes. I felt like that shift – there wasn’t really anything for me there. If I was going to make carbon bikes, this is what I wanted to do. This is what I wanted to try to accomplish. ENVE wasn’t going to do it. I was flailing in a lot of ways. Like, shit man, should I go back to school? Should I go figure out something else to do, you know? I was at this weird spot where the frame parts, how I wanted to go about making a high-end carbon bike. Small shops – they didn’t have the technological capabilities to build what I wanted. And then the bigger composite shops that did are all too busy making stuff for aerospace to even want to talk to a bike maker. So I was in this non-space.
BIKERUMOR: If you were walking around talking about to this stuff to people, like to friends, you must have sounded like a crazy person. Like, oh, he wants to reinvent the carbon bicycle, take it to a whole other level technically but also make it custom per rider… but with low-cost tooling. Like, okay, that’s interesting.
BEN: Good luck with all of that!
BIKERUMOR: You’re going to do this thing that no one else, not even the experts, has figured out yet. And you’re going to have magic money for this. This is hysterical. So what the point where you were like, “I’m actually going to do this crazy thing?”
BEN: It was funny because I got tagged on some weird design challenge, the Oregon Manifest design challenge a few years ago in Portland, where they teamed up some bike builders with college design classes, essentially a virtual bike build off. I was on this panel for the University of Oregon Engineering team, and they were looking at Dave Levy and I as consultants. Dave Levy and I would go there every couple of weeks and help these college kids out. He and I would get to chatting and we’d have beers or see each other and I would give him updates on what I’m working on.
BIKERUMOR: And he’s like, “you’re a crazy person.”
BEN: Yeah! But he was like, “You should talk to my friend Steve who I race cars with. He’s got a composite company in White Salmon, Washington.”
I was like, okay! Sweet! Give me his contact information. At this point, it was kind of a last ditch effort, so I wrote Steve an email at Innovative Composites, his company, sort of very high level talking about what I wanted to do. About a week later, he got back to me and he was, “Actually, we’ve made composites up for other companies like Indy Fab before and it sounds like a cool project. Why don’t you come out and we’ll talk about it.”
So went up to White Salmon and sat down with the guys at Innovative Composites and got to know Steve, and it was just kind of total luck it worked out that way because their shop is that shop that makes stuff for Boeing and oil and gas and Baker Hughes and all these huge companies, but they are total bike nerds. The owner raced competitively in college and then they actually helped Guru with a whole bunch of their original frame tooling when they started out. He sort of had a concept in his head about how he wanted to go about building a carbon bike too, and that’s sort of how the whole thing started. It’s my relationship with Steve and what he was trying to accomplish and his expertise in composite molding and how I wanted to approach the carbon market and marry this sort of unmarriable custom molded carbon bike frames, you know?
It went from beers and napkin sketches to the whole thing. And back to my relationship with ICE, their composite engineering expertise and wherewithal was the missing key to the whole thing. Once we put that piece of the puzzle in there, it all sort of falls together.
BIKERUMOR: So that’s the story up until carbon… wow. It’s interesting to figure out how to set this up, but you’re at production now… what are the volumes for Argonaut?
BEN: Last year we did 60 bikes. This year, we’re hoping to do 100. And 200 is kind of my production goal where I’m able to still concentrate on giving individual customers enough attention, but have some economy of scale to do fun stuff with. To grow, to reinvest in innovation and improve the product, but at the same time, I don’t have all this overhead weighing me down all the time. That’s kind of the ideal.
BIKERUMOR: The sweet spot.
BEN: From the get go my goal has always been very singular: to make the best road bike on the market. So what is that? It’s custom to the individual rider so they get exactly what they want. And it’s carbon because that’s I think the best material for making high-end race-style performance bikes out of, and it’s also made in a way that carbon should be made. It’s molded in aluminum molds with inflatable bladders, controlling wall thickness, controlling layup pattern- it’s made in the best way possible. Everything that I’m doing is around that singular goal of making the best road bike on the market.
BIKERUMOR: How much time do you, personally, spend with your hands on a bike that goes through your operation? You’re not gluing, assembling the frame anymore. You were for a time, right?
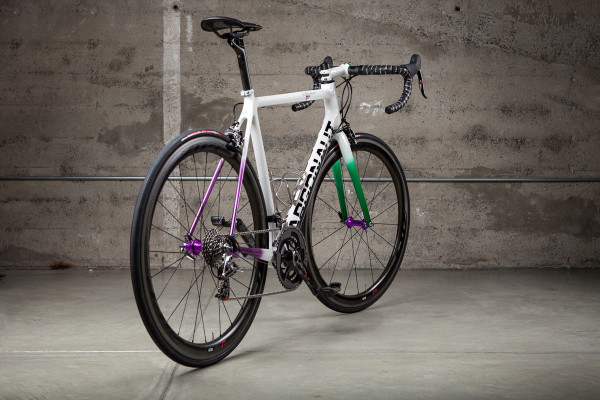
BEN: Yeah. I worked alone for almost ten years. Listened to a lot of podcasts. And then, about two years ago, I hired Boone, who is doing the frame building for me full time. He came from Cielo before me, he was working steel fabrication there. He was at Zen Bike Fab doing aluminum stuff. So he’s been building bikes forever. He’s doing all the actual frame assembly. All the individual frame parts are made up in White Salmon, Washington. We just set up a frame booth in-house here, so we’re going to paint our NAHBS bikes here.
Right now, my job is basically sales, marketing, and design. I work with each one of the customers to define their geometry and layup pattern. I submit PO’s to Innovative Composites specing the individual frame parts that need to be made and the layup pattern of those parts. They are made there. We get frames in sub-assemblies of seven pieces. We prep and bond the pieces here in-house and then paint and ship the frames.
BIKERUMOR: So essentially you’re designing custom kit bikes.
BEN: Right.
BIKERUMOR: Submitting the kit design, and it pops out from Innovative Composites on the other end.
BEN: At ICE we made all of our own frame tooling, so it’s essentially a set of adjustable frame tooling where the entry angle between the seat tube and the downtube, the head tube length – essentially all the frame angles are resolved inside the tube. They are all made essentially in the longest length, but a different layup pattern. Each frame is designed in 3D CAD before it goes into production, and that 3D CAD model is sort of the guide for the geometry of the bike, and the layup pattern is specific to the rider.
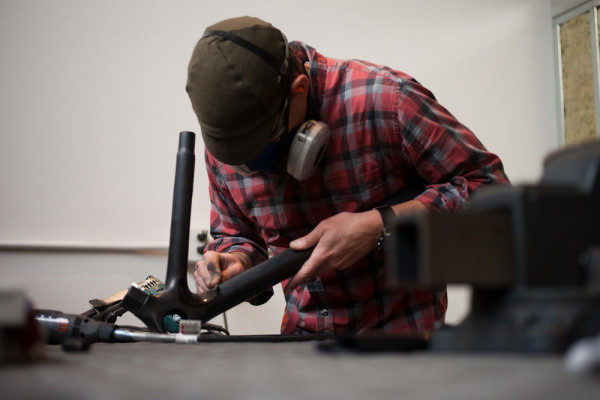
BIKERUMOR: Sure, so you talk about making things custom to the rider, and that’s not just geometry for you. You have an opportunity to tune the material ride experience. What goes into that?
BEN: So we look at, for each part of the bike, two and three sets of data points. We look at torsional stiffness, bending stiffness, bending stiffness in two directions – horizontal and vertical. For the downtube, for example, we’ll look at torsional stiffness and vertical bending at a rider’s given size and weight. So I want the bike to respond to twisting forces, pedaling forces, proportionate to the amount of power they want to put into it. And this is where my background in steel and my own sort of ideas on how a really great bike should ride comes in. I think that most production level bikes are over-built, are too stiff for the vast majority of people who ride them.
BIKERUMOR: Well, they have to be, right?
BEN: They sort of have to be as stiff as the highest common denominator.
BIKERUMOR: Or the worst rider.
BEN: Right. Women – it’s a great example. A woman buying a bike who is 115, 120 pounds who can put out a decent amount of power for her weight, which is maybe a functional threshold power of 280 watts, 3 minute power of 275 watts. At 115 pounds, they are flying along. But the torsional forces they are putting through the bottom half of the bike, they are just much lower than someone who is 170 who can put out 400 watts over 3 minutes. By being able to reduce torsional bending values in the bike, I’m able to give this lighter rider a really great, lively, dynamic feeling bike. And at the same time, for the bigger guys, I can make that same bike appropriately stiff so that when they step on it, it does the appropriate thing as well.
And that’s what I sort of figured out early on, where the real value in a custom bike that somebody gets isn’t so much how it fits because fit is kind of easy and it’s also dynamic. Your fit changes over time and getting a bike that fits properly isn’t that hard. Getting a bike to handle properly for you and feel good, it harder to do. That’s something that I feel I can do really well with the medium I have at my disposal.
BIKERUMOR: That’s super exciting. Small, lighter riders… women get the shaft.
BEN: Totally!
BIKERUMOR: You talk about how steel as a background has been advantageous for ride-tuning. How else has that been advantageous for you to have that background? You have taken this serpentine route through all these other materials. What is the value of that path?
BEN: Building my own and riding steel bikes over the years has given me the sense for, and this is arguable and where it gets a little touchy feely… I’ve had transcendent experiences on steel bikes that I’ve made. Like, this thing that’s under me is doing these amazing things beyond what you can really perceive it doing in the here and now. You know, like where you have like a $15 bottle of wine and a $200 bottle of wine – there is something going on in that $200 bottle of wine that’s exceptional. And that is harder to replicate with carbon, even though it’s better suited to do so many things at the same time.
So my approach to making carbon bikes is that I feel like I want it to do so much more and continually more, this search for this perfect riding bike, and that’s a lot of the reasons I moved to carbon from steel, like, this is a great steel bike, what’s the next level you can do? And there’s not really. With carbon, there are all these further levels because it’s not just carbon fiber, it’s a composite. It’s an assemblage of a few different materials and there’s always new materials coming out and new things you can do with those materials. And so I think it’s just that knowing that there’s even more out there than what we know now, and sort of that search for it to do something more than I get from steel, that kind of motivates me to keep trying and keep improving this thing.
BIKERUMOR: So final question: so there is a kid at the show who wants to grow up to be the next Ben Farver, who has literally created this crazy unique niche for himself. What do you tell that kid who wants to be you when they grow up?
BEN: That’s a good question. Just do not be afraid of “no” and don’t be afraid of picking up the phone and asking. So much of what I do now and continue to do comes from, I don’t know how to do that! Who knows how to do that? Okay, I’m going to call them up. Be like “Hi, I’m Ben, I do this. I’m trying to do this. What do you know about it?” Most of the time they’ll be like, “Fuck you,” like “I’ve got other things to do.” A lot of times, people are super open to talk about it and sharing their expertise and growing that way. Just understanding your limitations and understanding how little you know and not being afraid to ask people you think you might.