After just a short period of time, it’s easy to forget that Wolf Tooth Components has been on the scene for less than three years. After starting with essentially one chainring that was slipped into NAHBS on board a Black Sheep Highlight ST fat bike, WTC quickly followed up with the official launch of just 3 chainring models. Fast forward to 2016 and WTC is turning out new fitments before many of us even know they exist. Add in their range of accessories, bags, and soft goods, and their catalog has grown substantially.
We initially checked in with WTC to get a tour of their production process which is split between two different machine shops. Now, with business apparently booming, Wolf Tooth is moving into a new, larger facility with plans to bring some of the production in house. Just because all of the production isn’t currently in house though, doesn’t mean it’s not local. WTC will continue splitting their machining time between two local machine shops, 401 Manufacturing and Integrity Tool and Engineering. While both shops do a lot of work other than Wolf Tooth Components, each of them attribute a large part of their total production to WTC’s growing business…
401 Manufacturing
After Mike started out in 2010 with just two lathes and his brother Steve starting in his garage with a Haas machining center, 401 Manufacturing is now a family business that is the result of the Anderson brothers combining their operations. While it’s easy to tell by the paraphernalia around the shop, Mike happily mentioned he has been a mountain biker since 1991, which is one of the things that attracted him to the WTC operation. Now with 22 employees, Mike says 401 would absolutely not be the size that it is without WTC.
Yes, all of those things in the cabinet are items 401 has produced including the Ryan Dungey Axle blocks which were on his moto before he went big time. Mike actually bought them back off eBay because he didn’t make any extra at the time but wanted them for display.
Considering the volume, 401 Manufacturing is fairly small, and arranged in a horse shoe. Having moved into this builing in 2014, their 10,000 square foot facility offers room to expand in the future.
Part of what allows 401 to make items like the chainrings and GC cassette adapters quickly, efficiently, and without a lot of room is a few pallet changing mills. These machines use shuttles or rotary platforms that allow for different pallets to be loaded up with the work. While one pallet is in being machined, the other pallets allow for work to be installed, removed, or flipped for the other side of the ring to be machined. Originally, the chainrings were machined on a Doosan mill, but the move to the pallet changer allows for up to 6 rings at a time and sped up the process. The GCs are machined on a rotary pallet mill instead of the shuttle versions like the chainrings.
The major steps of WTC’s GC cassette adapter shows how it gets from the plate of aluminum to the final, anodized product.
At the time of this tour, they were running 7 days a week with day, night, and weekend shifts.
Integrity Tool and Engineering
Just down the road, Integrity Tool and Engineering was started in 1998 by current president/CEO Greg Johnson. Currently occupying 11,500 square feet, Integrity comes from a high technology background and specializes in state of the art, extremely accurate machining. The kind of accuracy needed to produce hard drives, microchips, medical devices, and things like that. That kind of precision is not exactly needed for bike parts, but their experience has really helped WTC grow their options in stainless steel.
Part of what makes SS narrow wide chainrings so great, also makes them harder to machine. We were told that each stainless chainring takes roughly four times as long to machine as their aluminum counterparts.
Many products are split between the two manufacturing houses meaning you’ll see chainrings and GCs being turned out at both locations. Without getting too specific, Integrity mentioned that Wolf Tooth is now a substantial part of their business.
Even though wire EDM (electrical discharge machining) isn’t used for any of the WTC components, it was still pretty cool to see. A lot of their machining with the EDM uses 0.0012 and 0.002″ wire! To put that in perspective, the average human hair is about 0.004″. The wire is electrically charged and never actually touches the work – the electricity does all the machining. The one-time use wire is then collected in bins making eerie shapes out of hair like metal wire.
Along with some of the most advanced machines, Integrity also has a state of the art inspection room. The star would probably have to be the Keyance IM instant measuring machine – just by taking an image of a part the device can produce all of the measurements to 0.00008″ accuracy and provide instant feedback if a complex part is out of spec. Of course you’ll also find microscopes, a comparator, calibrated surface plates, and a just about anything you would expect of a place that can’t discuss all of their various projects.
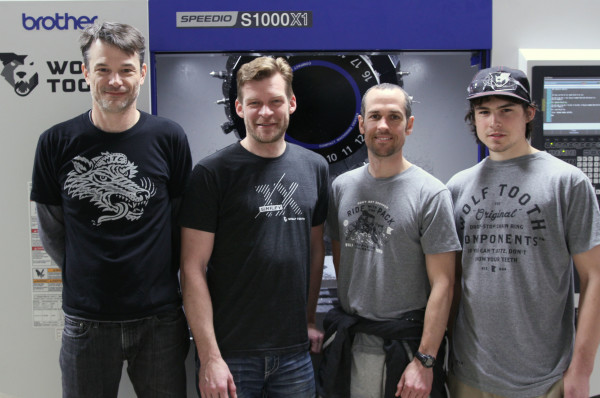
WTC Headquarters
One of the best parts of the Wolf Tooth Components story is that it is a true American success story. WTC was initially started by Mike Pfeiffer basically out of his house. Brendan Moore and Dan Dittmer joined the party at a time when they both still had “day jobs.” It’s one of those stories where their collective skills and passion for cycling came together at just the right time – the rise of 1x drivetrains. For the past three years, WTC operations were basically run out of their houses with manufacturing either at 401 or Integrity.
Now WTC just hired another engineer to run their CNC equipment as well as add to the product design team making a total of 5 employees as well as the 5-6 contractors they use on a regular basis. Like proud new fathers, Brendan and Mike (Dan was off in Alaska racing the ITI!) were very excited to show off their brand new headquarters which will serve as their design center, R&D facility, laser etching facility, shipping operation, and even handle some of the production load. After officially moving in around December 2015, WTC had to gut the 4,000 square foot building and even install a new HVAC unit.
Increasing production means new machines. Big ones. Tool geeks will surely drool over the brand new Y Axis CNC lathe with live tooling and their 3 axis vertical machining center with a pallet changer. Equipped with 2 pallets, each can hold 8 GC cassette adapters at a time allowing for 16 total.
While we were visiting, WTC was in the process of whipping up a few new items including the Tanpan derailleur adapter. WTC plans to use their new machining capacity to run smaller batches of parts as well as turning out prototypes to cut down on the lead time for development.
About a year and a half ago, WTC invested in their own laser etching machine which at this point they say has paid for itself. Now they’re marking everything from their new headset spacers to flasks. If you had access to a laser etching machine, what wouldn’t you try to burn?
After parts come back form the local anodizer, they are etched, packed, and then shipped out to consumers and dealers world wide. Keep an eye on this space – by the looks of things, WTC is just getting started.