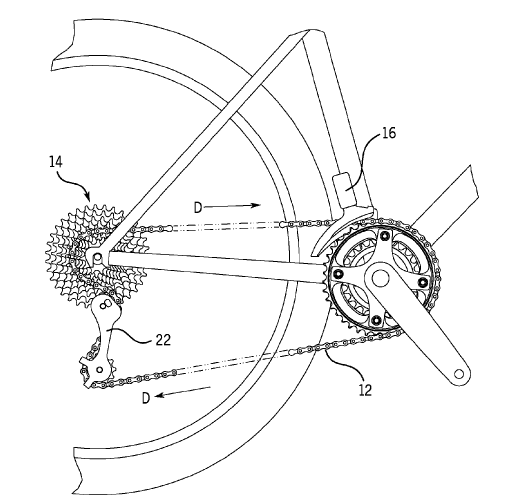
Electronic gear shifting is here to stay, and it’s amazing. But could it be better? Engineer Eldon Goates thinks so, and his patent application shows how. With a few sensors and some programming, he’s designed a way for electronic rear derailleurs to automatically adjust themselves to the perfect position for each gear, regardless of environmental conditions. But that’s the obvious and least impressive reason why this is exciting…
Say you’re on a seriously rough road and the derailleur’s jangling all around. This system could keep it perfectly aligned through all of your shifts. That’s great, but here’s where it gets really good: Say those rough roads send you to the ground and you bend your derailleur hanger a little. No problem, this will automatically fix the alignment and keep you shifting and riding smooth.
Or, say you flat and need to swap wheels (cyclocross, pro peloton, etc.). Just grab a wheel and throw it in there and the sensors will detect any difference in the cassette’s placement and realign the derailleur for perfect shifts. The patent even mentions being able to accommodate different numbers of gears, say, having to go from an 11-speed to 10-speed cassette in a pinch. It also enables the rear derailleur to slightly overshoot a shift to ensure the chain moves under high tension, then center itself in the proper position.
Lastly, this opens up the door to more gears fitting into the same amount of space. The gap between cogs on an 11-speed cassette is tight, but 12 speed is almost assuredly coming. If the electronics can precisely align the derailleur with the more closely spaced cogs, there’s less need to build in “room for error” and more room for another cog (or two).
How it works: There are two sensing methods described, though it leaves the door open to using other sensing methods as are available. The first is using vibration signatures to pick up on unwanted or abnormal sounds as the chain moves through the drivetrain. A small piezo or microphone sensor could pick up on the noises and create an ongoing feedback loop to maintain the optimum position.
The second is with a positional sensor integrated into the top pulley on the rear derailleur. Figure 4 shows a traditional layout, with a small degree of lateral freedom built into the pulley’s axle, allowing it to self center on the desired cog. This is the natural state of things and allows it to self center in a way that reduces drag and keeps it aligned. But, because there’s only a small amount of lateral “float” available, any misalignment in the system could prevent it from completely centering itself under the cog.
The solution is to introduce slightly more float (Fig. 5, shown mid-shift), then put a positional sensor (magnetic, capacitive, contact, etc.) in place so that the derailleur can know when the pulley is centered on its axle. Since the pulley will naturally position itself in alignment with the cog, the derailleur can then adjust itself to center the pulley on its axle, putting the entire system in perfect alignment. During shifts, contact sensors could feel when the pulley is pushed to one side then re-center it once the prescribed shift is made.
The two solutions could be combined, or other sensors could be used as such technologies are developed. The system records and learns the optimum position for each gear over time. It could also include wheel speed and other sensors to help the system fine tune its vibration measuring methods to improve overall performance and reduce processing power demands. It could even be programmed to monitor your cadence, speed, incline and other factors then perform shifts automatically to keep you in the right zone.