Any story about Prologo starts at Velo. Stella Yu started Velo Saddles in 1979 and has been producing saddles for other brands ever since…to the tune of 15 million saddles per year across multiple factories. Chances are very good the saddle you’re riding today was made by Velo.
But her dream, according to Prologo brand manager Salvatore Truglio, was to produce something under her own brand and produce something at the top level that could compete with brands like Selle San Marco or Selle Italia.
Around 2006, Salvatore met Stella and she was looking for an Italian company to collaborate with. Meanwhile, he was working for various other cycling companies before becoming a regional sales manager for Columbus, which had developed the Cinelli and Gruppo brands. Stella was looking for someone to help drive the premium brand project, and Salvatore was looking to create something of his own. So, they set up headquarters in Busnago, Italy, which was near enough to many other major Italian cycling brands that it benefitted from that country’s cycling and manufacturing cultures, as well as their racing and teams.
To start, they had to consider what they could do that would be better, and different, than the competition. Their first product was called The Choice, which had an interchangeable top section.
With just two small screws on the tail, you could release the top section and swap the padding between mountain bike, gel and road racing options. It also introduced a new vacuum molding process and resulted in no stitching.
The Choice saddle debuted in 2007 and was raced by Tinkoff and Milram teams, capturing several podiums and Giro stage wins with Petaki on it. From there, he started with working with Bjarne Riis to get feedback from his athletes, going through several prototypes with something like 10 day turnaround between his comments and his athletes riding new saddles. This quickness helped convince the team Prologo was serious about making good saddles, so CSC switched all of their saddles over for the season. And Bjarnes was “maniacal” about providing detailed feedback, giving Prologo the information they needed to make top level products.
Then, in 2008, they introduced the first ever TT-specific saddle for Cancellara. The Nago Evo TTR debuted with a shorter nose, slide control embossing to keep him in an aero position without slipping off the nose, and a lifted tail. They launched in at the Tour de France in Monaco and took home the yellow jersey. Since then, they’ve switched the embossing to their vibration damping CPC material, and had to make the tail flat to comply with the UCI…the model is in its fourth generation for 2017.
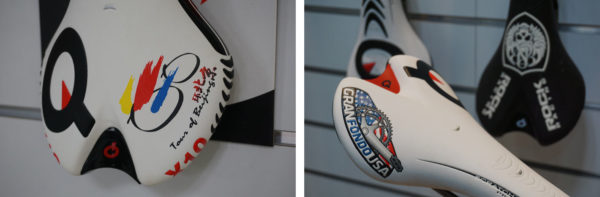
In the years since, they’ve partnered with doctors and universities to refine the shape of the saddles and develop their MyQ fit system to help riders find the right saddle for them. Options include flat, semi-round and rounded shapes, cutouts or not, and multiple widths. MyQ also incorporates a sit-and-fit pad and software system for retailers that takes riders’ height, weight, flexibility and riding style and experience into account before making recommendations.

In Italy, they run the company, manage sales, research and development, testing and design. All manufacturing is handled by Velo in Taichung area in Taiwan. Velo makes about 8,000 saddles per day at this factory. They also have Shanghai and Shenzhen operations, but this Taiwan factory makes the high end stuff. Here’s how it happens…
HOW PROLOGO & VELO MAKE THEIR SADDLES
They use various types of foams, covers, etc. Velo works with the brands and materials suppliers to make sure everyone gets what they want in the finished product. For other brands, they will explain what options are available and then advise on what to use. Because of the volume they do, they often get exclusive rights to some of the best materials…things like temperature stable foam, etc. Above is pre-made foam layers that get cut to shape for some saddles.
Others use injection molded foam, sometimes with the shell going into the mold so they’re sort of co-molded together. Above, you can see several shells laid into the foam molds.
Molds are slotted into a conveyer belt, then filled with a liquid that’ll expand into foam and bake itself into shape as the conveyor turns the corner and runs through an oven. This process lets them create multi-density foam. Each section is poured into it’s own section of a full sized mold, then they fuse into a single piece but maintain the zoned density.
Once they’re removed, excess foam is trimmed and they move on to be covered.
The covers are glued and stretched over the foam and stapled into place.
Then the excess material is trimmed off, and they move on for final assembly and packaging.
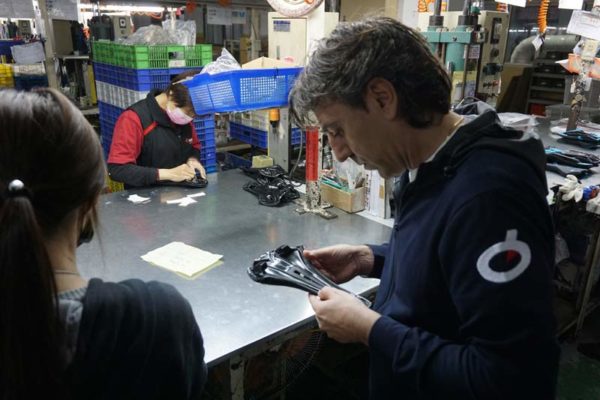
Rails used to be hand bent, now they’ve designed their own machine to automate the process and bend the rails in a matter of seconds. This not only creates massive efficiencies, but it ensures the saddles are perfectly level. In the pic above, a spool of wire gets pulled through a cutting machine.
Those sections are then placed into another machine that bends them into shape. This one is an older machine. Stella’s newest one is their own design that works much faster, is absolutely mesmerizing to watch as it pulls wire through and bends it in real time. It was awesome, and all photos and video were 100% off limits. She doesn’t want anyone else copying that technology. The carbon fiber based and rails are manufactured in a totally depart building, and even Salvatore isn’t allowed there…Stella likes to keep that process secret, too.
Just down the road is another of her factories, which is more modern because it’s newer. Here, they do the plastic and composite injection molded bases for the saddles. They also make handlebar tape and grips there.
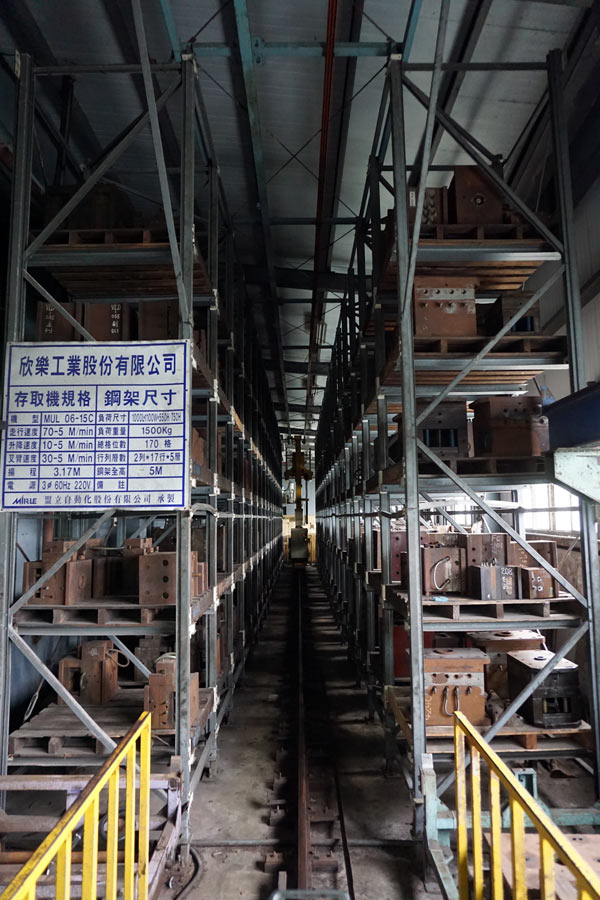
They make 800 pair of grips per machine per day. There are 43 machines for saddle shells and grips, plus another 33 grip machines in another building. Tri-density grips come out from a single machine, and they have three of those machines.
In total, they make one million pairs of grips per month and have no warehouse – they’re shipping them as fast as they can make them.
QUALITY CONTROL
Inside the QC lab are machines for testing both durability and quality of manufacture.
Inside the weather tester, one hour is equivalent to one month. Temp range runs from -20° to 80° C (-4º to 176º F), and it tests for UV color stability.
Saddles get pounded with 110kg over 200,000 cycles to meet 10% higher than ISO4210 standard. Also tests for graphics and material longevity.
Lastly, saddles are measured for balance and even-ness.
The end result is a high end saddle with features that won’t make its way to any other brand’s seat. We saw a lot of other brands there, and Velo seems to bend over backwards to continually find new materials and better designs to offer their OEM customers, but there are a few things they reserve for their own baby. Or that Prologo brings to the table, like the CPC Airing vibration damping, a technology they developed and patented.
Huge thanks to Salvatore and Stella for the tour and hospitality!