A propeller makes for an easy example of cavitation. (Photo provided by Rockshox, via Wikipedia)
For the past two weeks, we’ve discussed IFPs and other methods of maintaining proper oil pressure and volume inside the fork and shock on your mountain bike. One of the reasons it’s there is to prevent cavitation, which is the formation of air bubbles inside the damping oil. Or, technically, it’s the formation of any type of gas bubble inside any fluid. Either way, it’s bad for performance. To explain why, I reached out to a number of suspension brands to see how they’d define it and what they do to prevent it.
Below, you’ll find answers from Chris Mandell (RockShox Rear Shock Product Manager), Tom Rogers (DVO Suspension Senior Engineer, Suspension Designer), and Ed Kwaterski (Manitou Chief Engineer). Here’s what they had to say…
BIKERUMOR: What exactly is cavitation inside a damping circuit? And why is it bad?
ROCKSHOX: In suspension cavitation is the formation of air bubbles in damping oil. It is bad b/c air acts differently from oil when passing through shims / orifices.
DVO: Hydrodynamic Cavitation describes the process of vaporization, bubble generation and bubble implosion which occurs in a flowing liquid as a result of a decrease and subsequent increase in local pressure. Cavitation will only occur if the local pressure declines to some point below the saturated vapor pressure of the liquid and subsequent recovery above the vapor pressure. If the recovery pressure is not above the vapor pressure then flashing is said to have occurred.
It happens when the IFP/bladder pressure is too low to stabilize the oil when it flows through the valves and circuits. This pressure works directly with the amount of damping any/all shocks are designed around. The amount of damping is determined by the kinematics of the bicycle frame design and it’s intended use. Cavitation can happen when either pressures are too low or damping and oil viscosities (saturated vapor pressure) is too high.
MANITOU: Oil generally has some percentage of air dissolved into it, just like water has. Vacuum filling systems can reduce the amount. Cavitation is caused when fluid flows across a restriction, and the differential pressure across the restriction is great enough that the downstream pressure falls low enough to pull the dissolved air out and create a bubble. Then when the system equalizes again, the bubbles collapse. The collapse causes a local shock wave and catastrophic destruction of components in a hydraulic system. Typically if the inlet flow of oil into a pump is restricted, there will be cavitation in the impeller area which can erode and fail the pump in hours.
In a shock, this happens in the compression stroke when the gas charge pressure is too low. The shaft side of the shock (which is growing larger during the compression stroke) falls too low in pressure. So let’s say your platform setting needs 300psi to blow off because 300psi acting on the system gives you the support you want. This means the restriction (shim stack) is strong enough that it builds up 300psi before oil can flow over to the shaft side. Now let’s say your IFP gas charge is 250psi. The oil will follow the path of least resistance, and push the IFP (floating piston) down excessively, instead of forcing its way through the shim stack and over to the shaft side. This means there is not adequate oil to fill the shaft side, and something must happen to fill the space so, the dissolved gas makes an appearance. The IFP should only move according to shaft volume, but because it didn’t have more resistance than the shim stack, oil moved in the wrong direction.
How about if the gas charge is 300psi, equal to the blow off pressure? The net effect would be the oil on the shaft side is at 0, and any air dissolved will come out. In reality the pressure will probably be lower yet since there is most likely to be further pressure drop across the piston due to whatever stroke velocity is occurring. Also, the oil is most likely warmed up, and more easily gives up the dissolved air. And of course over time, air enters the system either across the IFP or past the shaft seal, and the amount of dissolved air increases. So what we really need is the charge pressure to be some increment higher than the maximum the damping force will generate (max adjuster position at max stroke velocity.)
Why is the cavitation bad? It basically creates a big void in the damping fluid column that needs to collapse before the shock (or fork) can generate damping force in the other direction (generally rebound damping). So if a shock cavitates, it will feel as if it has lost rebound damping. If the shock is otherwise in good order, it will resume normal function when the terrain settles down, but who cares, you’ve already blown your line.
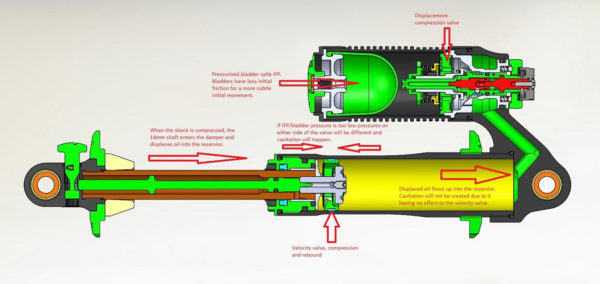
BIKERUMOR: How does your product deal with it?
ROCKSHOX: As a shock is developed the team will do a lot of dyno work to develop rebound, compression and lock stack tunes. During this time the team will also study the graphs produced by the dyno for signs of cavitation. When they see it they will adjust the IFP (internal Floating Piston) pressure accordingly.
DVO: So far, I designed all DVO shocks and fork dampers to work on displacement of oil more than the velocity of oil through a valve. For example, our Jade rear shock has a large shaft size (14mm) and a small main piston/body (25mm). The amount of oil that passes thru this velocity valve is minimal and the compression damping here is very small. As the shock compresses, oil is displaced by 14mm shaft. The running pressure (170-200psi) ensures that the oil will remain stable as it is forced through the main piston’s compression shims. If the pressure is too low, the oil pressures on either side of the valve (shim stack) can change creating “vaporization” or bubble generation. When the shock changes direction (extends) the pressures on either side of the main valve will stabilize but only after “bubble implosion”. This happens very rapidly on every cycle of the shock and will create inconsistencies and even an audible knocking noise. The bigger the rider, the more damping is needed and with that a higher pressure should be used.
A good example of dealing with cavitation is when you tune a shock to have a lock-out. A lock-out shock stops all oil flow thru the velocity valve (moving piston) and valving (shims). In order to eliminate cavitation the IFP/bladder pressure goes way up somewhere near 500 psi for a complete lock-out. With trail dampers, with climbing features, the pressures are lower (170-200psi) due the way the compression feature is designed and the amount of damping created. It is a different design than a lock-out shock and controls oil flow from the displacement of the shaft entering the damper. Oil speed on displacement is much slower and is easier to manage. With the Jade shock we displace a good amount of oil with the large 14mm shaft. This displaced oil flows up into the reservoir and thru the compression shim stack at around 1/3 the speed of the main piston.
MANITOU: We make sure the charge pressure is properly balanced with the damping force in the shock. Testing and more testing. Our forks deal with this differently than our shocks.
In our forks, and indeed in the forks of many companies who license our TPC patent, we use a different piston for rebound and compression damping (all Manitou forks use some version of TPC architecture). The architecture of the fork creates an oil flow that is always physically pushed thru the damping circuit by the movement of hard parts, with no reliance on charge pressures. For example, the restriction of the compression damper builds pressure to push oil across the low-restriction rebound check valve, while at the same time, the rebound shaft acts as a pump to force oil through the compression circuit and generate the compression damping. We use larger ports and light spring action to ensure that during the compression stroke, pressure is basically equal on both sides of the rebound piston, and higher than ambient because of compression damper influence. During the rebound stroke, oil is squeezed between the rebound piston and the end cap of the fork leg as spring force drives the assembly to extend. So if you think about it, the shaft side of the rebound piston is at a higher than normal pressure during BOTH rebound and compression cycles. The pressure only falls to ambient when the fork stops moving.
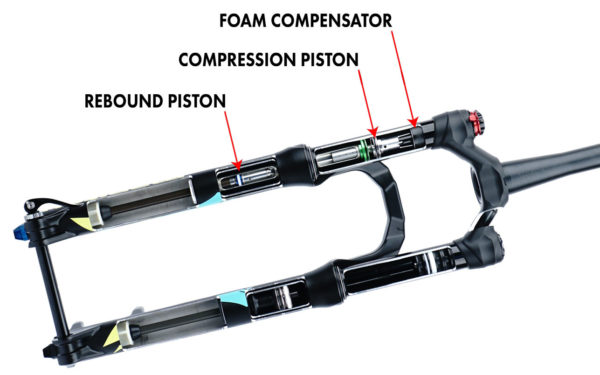
BIKERUMOR: Are there specific port, shim or shaft shapes that minimize or exacerbate cavitation?
ROCKSHOX: Properly setting IFP pressure in a shock is what eliminates cavitation.
DVO: Port sizing on pistons and shafts is very critical. Too small of a ports, the pressures on opposing sides of valves will be different at lower shaft speeds and the potential for cavitation is very high. Having too large of ports with large shim stacks will make it very difficult to achieve good damping and a balance with external tune-ability features like rebound and compression adjusters and also with dispersing heat.
MANITOU: Smooth oil flow helps so a local low pressure area is not created due to turbulence, but mainly it is balancing pressure drops and charge pressures or push, rather than pulling oil. For our forks, it would be a bad idea to try and build a “mid-valve”. A mid-valve replaces a free-flowing rebound check with a restriction. Since this restriction works on the entire piston area, rather than shaft area, more force can be created at lower pressures. This is good for response if the system is designed for it. An example would be a moto fork such as a Showa Twin Chamber, which is pressurized via a spring backed IFP in order to behave more like a shock.
BIKERUMOR: How “real” is the problem of cavitation? Are regular riders going to experience it?
ROCKSHOX: It is a very real and well understood phenomena. Google image it and see the damage it can do to boat propellers (Editor’s note: Or don’t. Ugh. Unless you like weird fat loss procedures.). If the shock is designed properly and serviced at proper intervals no rider (regular or professional) should experience it.
DVO: Nowadays, cavitation is rare if you are using a brand name shock or fork. It can be an issue if you like to tinker and tune your own shocks and forks or if you neglect to check your air pressure settings or service your product regularly. The base settings in production product has been tested, tuned and confirmed using riders and a dyno to confirm. If you tinker with your shim stacks you can only go so far before you run into cavitation or non-effective damping. Best thing to do is get in touch with the manufacturer and ask. Here at DVO we do a lot of custom settings because the design allows it. Other brands might have more limitations in this area.
MANITOU: Anyone will experience when their shock has lost enough gas charge. It does not require any talent to reach it, just poor design or degraded service.
BIKERUMOR: Anything else you’d like to add on the subject, either in general or specific to your brand/products?
MANITOU: Aeration has a similar influence on damping loss, but happens when air and oil mix during operation. Since it is not caused by low pressure, aeration will require more time to settle out. Many of our forks use a foam compensator to separate the air and oil via the use of closed cell foam to basically create thousands of mini bladders. It blends super-easy service (no fussy bleed process) with a better performance compared to an open air space around the compression damper at the top of the stanchion.
UPDATE: We invited every major suspension brand to chime in on cavitation. Bob Fox, founder of Fox Racing Shox, was out of the office, but he still took the time to respond, and his response is solid. Check it out separately in our follow-up post.
The fun never ends. Stay tuned for a new post each week that explores one small suspension tech, tuning or product topic. Check out past posts here. Got a question you want answered? Email us. Want your brand or product featured? We can do that, too.