Last week, Alto Cycling published a rim brake performance test showing eight different brand’s rims subjected to consistent rim brake pressure up to the point of failure. Not surprisingly, it generated a lot of comments. And a big response from several of the brands tested. And we do mean big, but it’s interesting reading. Here are reactions and comments from Boyd Cycling, ENVE and Mavic. We also asked Alto Cycling to provide a few additional thoughts and clarifications, which are included.
WHAT WAS WRONG WITH THE TEST?
BOYD: Let’s go back to fundamentals. Braking is about dissipating kinetic energy through friction to stop the bike. In theory, this is what our competitor’s test is trying to drive at. You need to remove energy through braking, and the heat generated can blow apart a wheel. The better a rim surface is at stopping (and they vary a lot from manufacturer to manufacturer) the less braking you will need to do get the bike to stop. So, in theory, if you had a really slippery rim surface, you could hold a brake lever at a given pressure for ever and never get enough friction to generate any heat buildup at all. But is that a wheel you really want to point down a mountain? This data point was not included in the test though the amount of kinetic energy asked of the tester’s rims was less than all others as it rotated at 1mph faster than all other rims included in the test, drawing the conclusion of having a very slippery brake track.
Boyd basically recreated the Alto test on professional equipment used by a lot of bicycle wheel testing labs. The video shows how braking force and temperature starts dropping. The image below shows the heat graph over time. Note where pads will start to glaze over and leave more residue on the rim, which produces less friction, and then the temperature starts to fall, too. Boyd says a better test is one that uses higher braking force and brings the rim to a complete stop repeatedly because it more closely resembles what you’re actually doing coming down a mountain. Using their 44mm carbon clincher and Black Prince pads, 7lbs of pressure at the brake lever at a constant 15km/h wheel speed, their rim lasted a full 20 minutes with no failure. Feel free to fast forward through the middle. The weird picture-in-picture at the end is showing the two different cameras to show both the wheel and screen. As for why Alto’s test showed completely different results? That’s a mystery to all of us.
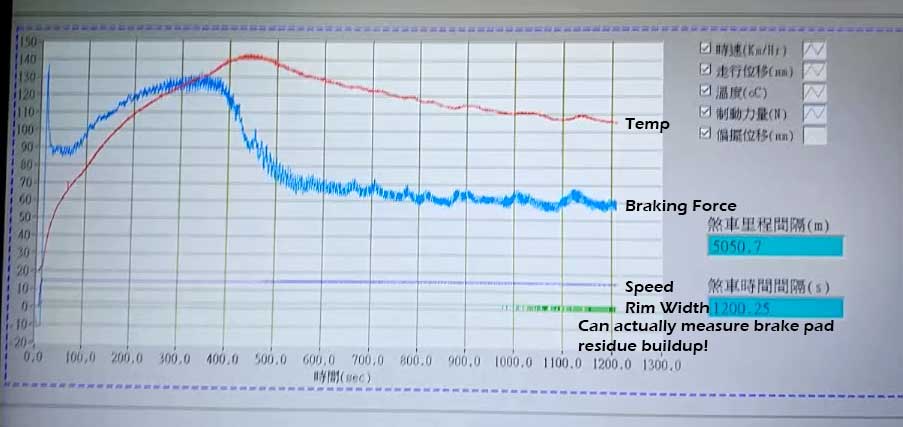
Conversely, if you have a better stopping rim surface, the same lever force over the same period of time will produce much more heat. However, with the forces that were outlined in the test, a rider would simply come to a stop (well before any heat damage occurred). If you had a large rider, strapped on a weighted backpack, grabbed only the rear brake, and continued to pedal down a very steep hill, then it would be possible to continue riding with the brake force (and generate the heat damage illustrated in that test. But those aren’t real world conditions).
The information needed to really to determine safety is a temperature measurement at time of failure. This is a much better indicator of a rim’s resistance to heat failure. Running a braking load for a period of time at a force that would cause any rider to stop is completely irrelevant to a rim’s safety.
ENVE: Their rim doesn’t have any texture, but from our testing, we’ve established that our textured brake track requires 30% less lever force to develop the same amount of stopping power. This is compared to our previous textured braking surface. Compared to a completely smooth brake track… We don’t really know how much more force would be required to achieve the same braking power. So in this Alto test, ENVE’s rim could theoretically have been tested at a minimum 30% more aggressively than any of the others without texture.
Then there is the issue with pads… You cannot generalize or underestimate the value of the brake pad. I get the desire to normalize the test and focus on the carbon structure itself, but as many commentators pointed out, we develop rims and pads to work in harmony for best results. Pad compound is something we’ve spent years and years developing because it absolutely matters for performance and safety. The pads we’ve developed were done in conjunction with our latest textured surface to provide the best balance between heat management, wet and dry performance, modulation, initial bite, and longevity. This of course doesn’t take into consideration the level of refinement an ENVE rim must also receive to ensure impact durability, stiffness, ride quality, etc… There are certainly resin systems that are really great at managing heat, but they often require compromising on durability, weight, longevity, etc…
The ENVE brake track test has evolved over the years as we’ve made improvements to our design, materials, and processes, we’ve had to increase the power level by nearly 50% to produce a rim failure when testing our latest rims. Our test is more complex than simply fixing a lever force and running a motor. The braking force is constantly being adjusted to produce a consistent and specific wattage throughout the test. This is required because as you are aware as things get hotter, they tend to soften/wear/glaze, so the force being applied at the brakes needs to be adjusted constantly. Essentially, the ENVE brake track test is dynamic and the main objective is to maintain a constant power output. This is potentially a major flaw with the Alto test. If they are simply testing to a lever force, the wattage is not constant. In addition to temperature on the outside, we’re also measuring/monitoring temperature inside the rim, dimensional changes in the wheel and tire pressure.
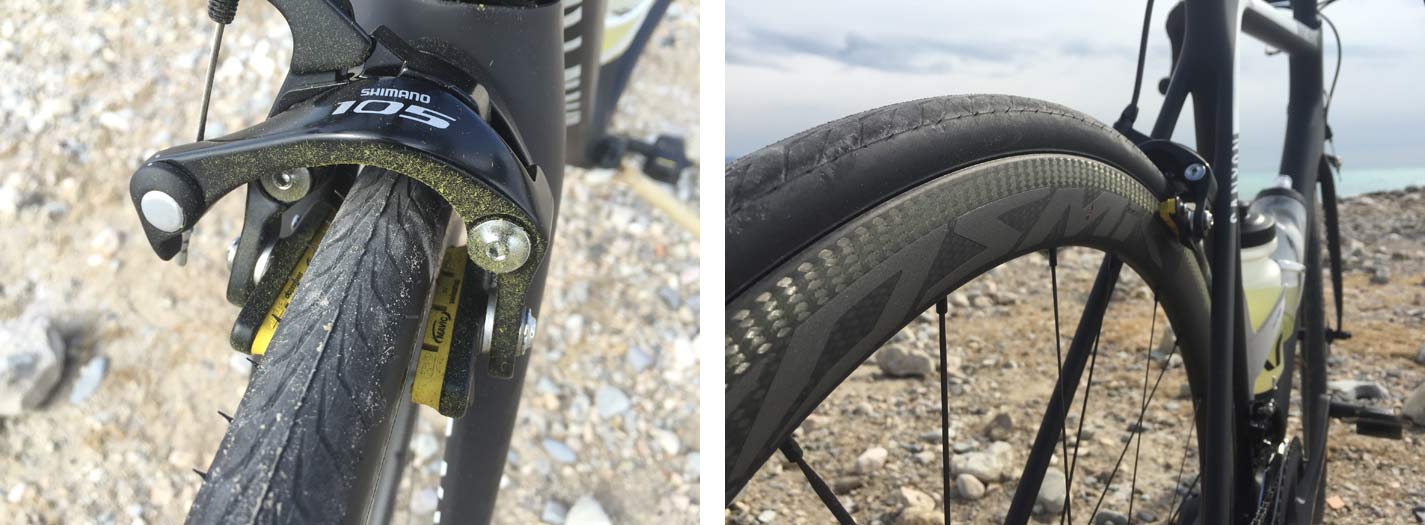
MAVIC: First of all, and probably the most obvious, the fact that they are not using the pads that each manufacturer recommends is a big issue. We chose the pads that we send with (and recommend as a replacement for) our wheels because it is the best option to meet our performance, safety and durability standards. Using a different pad will change the effect on our rim in terms of how it generates heat. Indeed, we have tested the Black Prince pad with our wheels and even if there is an improvement in braking performance (this is subjective for many reasons) the door is opened for bigger issues – shorter pad life, higher heat in the rims and reduced life of the rim itself. So, as you can see for not just us, but the others as well, there are real performance characteristics that come with the recommended pad and by not using those you are absolutely NOT establishing a level playing field.
Further on the point above, we can now discuss the braking surface. As I just mentioned above, there are performance characteristics that come with the combination of pad / rim used. What we can say is that the Alto rim has very little, if any, texture on the braking surface. So, you can use any pad you like – heck, you could use SOAP – and there will be less heat in those rims. We are 100% sure that if we sent our Cosmic Pro Carbon SL UST rim to them, without the laser treatment we apply to our braking surface, that we would match or surpass their benchmark. So, as the interface between their rim and pad has less friction … there is absolutely less heat and thus, the wheel can run longer before there is damage.

So, the test doesn’t take into account braking efficiency. Meaning, if the braking efficiency is very bad, the pad will just slide on the rim without creating as much friction or resistance (as a more efficient braking system would). Hence, there is not as much heat. When the braking is more efficient, there is more friction, so more resistance and so of course, more heat. All this means it is more open to damage or failure at extreme temperatures. In terms of temps … based on our experience the max temps you might experience in “real life” are around 200º Celsius. (Ed. Check out some of Mavic’s carbon rim brake design in this post and our test impressions here.)
Next, let’s discuss the power delivery. There are many peculiarities with this part of the test. They mention the motor is set at 1200w and the force on the brakes remains consistent at 7lbs (for phase 1). However, when you look at the speed of all of the wheels, including Alto, it doesn’t add up. In our testing, we have seen up to a 50% change in speed depending on the braking surface being tested — we have even seen these big differences between some of the exact wheels they used in their test. So, with a wheel that has an aggressive / high performing braking surface – like the Enve, Mavic or Zipp – there should have been a much bigger difference in the speed if the motor was staying consistent at 1200w. Further, even if it WAS staying consistent at 1200w it creates, yet again, an unfair playing field. A rim with a high performing brake track will generate more heat when compared to a rim with a poor (or no) braking surface treatment and will of course reach a failure quicker. The issue is that in the real world that wheel would have adequately braked, or even stopped, well before failure.
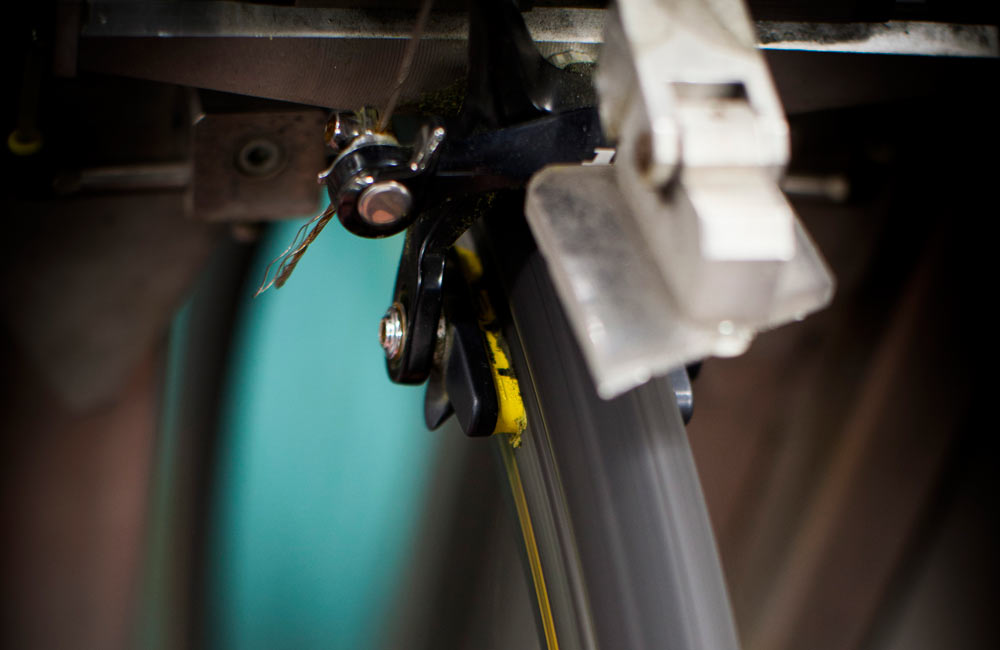
Another point regarding speed of the Alto wheel between phase 1 and phase 2 should be mentioned. There is nearly no difference in the speed between the two tests even though there is around 30% more braking force being applied (7lb -> 9lb). Our engineers say that this is simply not possible. The speed should be something around 16mph in phase 2.
Braking power – again, there is a flaw here. There is a weight being applied to a lever which is then putting the pad onto the rim. Again, this is simply not accurate. In order to have a reliable test the pressure should be applied mechanically to the pad and not through a lever and cable with a free hanging weight. Further, it is not effective to apply equal braking force when testing different wheels. In our test, and those you’ll find from other brands I’m sure, we maintain a motor at 600w-700w and adjust the braking force based on the resistance on the motor. This completely levels the playing field for the brake surface treatment. Slicker surface means more braking force because there is less resistance on the motor. More aggressive braking surface means less braking force because of more resistance on the motor. I hope that you can see that this easily points out how they have created a very biased test. Their wheels have little or no brake surface treatment so not only will their wheels have inferior real-world performance compared to us, and others in the test, but their wheels do not have the appropriate braking force on the rim to show how their rim reacts when all of the wheels are tested fairly.
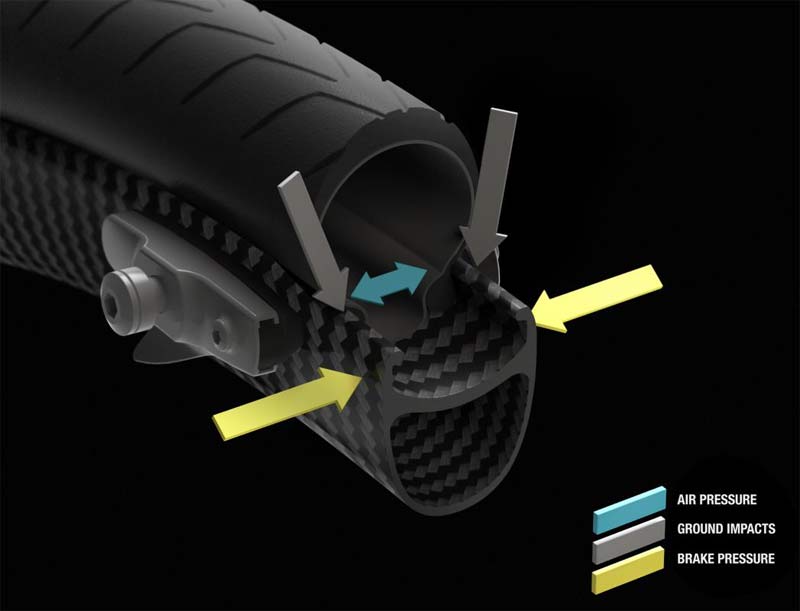
Now, let’s talk about the heat measurement. In the test Spark was using infrared to measure the heat on the braking surface. Not only is that a poor place to measure the heat, infrared is incredibly unreliable and inconsistent. In testing our wheels, we measure the temperature on the inside of the rim, at the top of the rim hook, using accurate and intricate methods that are exponentially more reliable and consistent than infrared. Our carbon clincher wheels are required to reach or pass a temperature of 200° C (392° F), which is well beyond any real-world circumstance. Further, as we can see by the max temperature they show for our wheel in the test, it is far from our benchmark. Based on the level and frequency of our testing we are 100% sure that there is an issue with their temperature measurement.
Regarding the 34 second cooling time in Phase 1 for the Alto wheel, this is completely impossible and there is no explanation that this can be accurate. When you look at the drastic difference between the Alto wheel and the nearest “competitor” it should automatically tell you that there is a flaw in the measuring. You might argue that Alto is using a proprietary carbon and / or resin to achieve this but again, that is simply not possible. How could it be that they have found a material, or mixture, that is that far advanced when compared to the brands in the test? Do those materials exist? Absolutely … but using them in an application like this the wheels would be astronomically expensive and simply not viable.
WHAT DO THOSE NUMBERS REALLY MEAN?
BOYD: Resin is the glue that holds carbon together, and when it softens that is what can cause the damage to the rims. When we looked at the results from the published test, we saw that the Boyd 60mm clincher rim was able to reach a higher temperature than any other rim. We also saw that our temperature rose quickly compared to the other rims (under admitted non-real world conditions). We can draw a conclusion from this that the braking performance of our rims was amongst the best out there, and the temperature rating was amongst the best out there. This is on par with what we experience in both lab and real world situations with our test riders and professional athletes who race on the wheels. We work with a professional criterium focused cycling team and even in rainy criteriums the team prefers to ride carbon wheels compared to alloy.
With the resin, we partnered with a manufacturer who actually produces their own resin in house. Versus ordering large rolls of pre-impregnated carbon fiber that has to sit in large freezers for months on end, our carbon manufacturer makes the resin, takes carbon from raw strands, and produces their own pre-preg. All carbon fiber goes from being made into a sheet of pre-preg to a finished product within a week.
WHY ISN’T THERE AN INDUSTRY STANDARD FOR BRAKING PERFORMANCE?
ENVE: The reality as I see it is that we, along with Zipp, Mavic, and whomever else, have spent oodles of money, time, resources to develop our brake track tests. So put us all in a room together to establish an “industry standard” test is simply highly unlikely. You could say well, don’t you care enough about the safety of consumers that they should all have access to safe rims? Well of course they should, but is it ENVE’s or Zipp’s responsibility to spend all the money, do all the work, and then give our technology to a competitor? At ENVE, we own our responsibility to ensure our customers have a safe product. Ultimately, consumers vote with their wallets. We’ve continued to grow over the years in terms of road market share and it’s not because we make an unsafe product.
I think the reaction we had to this test was more related to the assumption of guilt that it placed on our brand. Like a good old fashion witch hunt. Call them a witch, and you must be a witch. This test is no different than throwing someone in a lake to prove they are a witch.
The reality for ENVE is that this hasn’t been a conversation for us for some years now. As far as we’re concerned, we’ve solved this problem given we’ve had zero returns for heat damage on our latest rims. If a consumer on older rims has an issue, their rim is replaced with the latest technology.
WHAT’S ALTO’S TAKE ON THE FRICTION ISSUE?
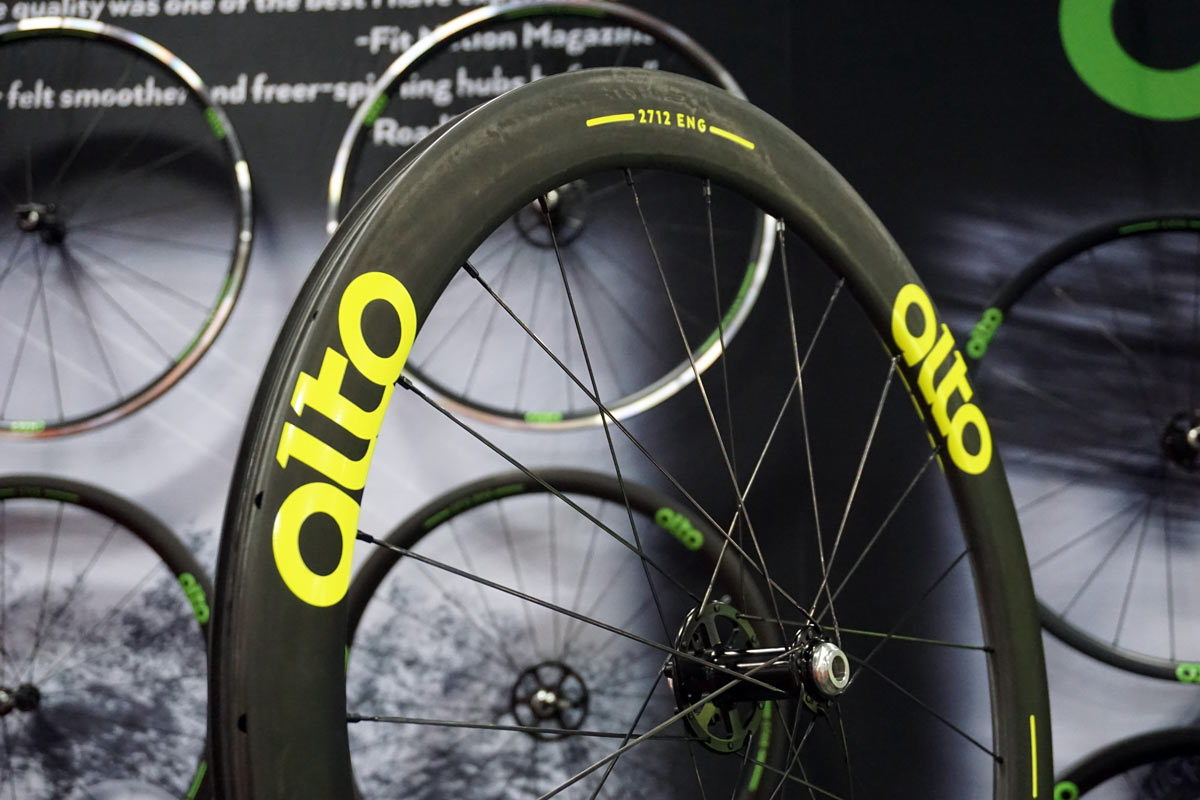
BIKERUMOR: Do your rims have adequate friction to produce the stopping power that cyclists will want?
ALTO: Of course. All of the rims ran between 19.4 and 20.3 mph during phase 1 for the first 3-5 minutes. After 5 minutes, you’ll notice that the Alto rims speed up. This is because the pads were over 200ºF for so long, they begin to gloss over and lose power. This is a function of the pad and not the rim, and would happen on all of the rims if they were able to get to this point without failing. You’ll notice it happening at the end of the Zipp test. Also check out the phase 2 Alto test and you will see that the rim is running slower than most others, around 19.3mph. This is with 9lbs of lever load instead of 7lbs. So what does that mean? The average grip strength of an adult is 100lbs, which is what you would apply during panic braking. If you are slowing down and you need more power, going from 7lbs to 9lbs isn’t even a noticeable difference. From a subjective “ride test” standpoint, the braking power of all of the rims in this test will feel identical. The difference that you’re seeing in the test is literally only measurable in the lab, but isn’t a large enough difference that anyone would be able to feel it.
BIKERUMOR: If so, how do they provide the stopping power without producing the same heat or resin softening as the others?
ALTO: It all comes down to heat dissipation. As I mentioned above, in phase 2 you can see identical stopping power (on a rim that was already tested for 20min in phase 1) with the Alto rim and you still get significantly better heat dissipation. This is for two reasons: resin quality and construction process. The resin contains multiple additives that allow it to flow more readily through the carbon matrix, allow us to use less of it while better filling any voids. It also has better conductive properties, and an aerospace grade glass temperature that keeps the resin from beginning to soften well above the temperatures that you would see under brake loads. For the construction process, we are filament winding the brake track to provide more compaction and an even tighter matrix. Instead of laying up pre-preg plies by hand, we use a machine to pull and wrap the fibers, keeping them taught as they are laid down. Both of these processes result in a composite that is extremely compact with zero filler material and voids. That means that when heat is transferring through the material, it isn’t hitting air pockets, wrinkles, and voids where is can build and cause critical failure modes. The conductive and heat dissipation properties of our new rim are simply better than anyone else’s.
BIKERUMOR: Do you recommend a specific brake pad for those rims?
ALTO: Nope! We send Black Prince pads with every wheel set because you get great power and modulation with them. But you can use any carbon pad with our wheels. It will not void the 5 year warranty and there isn’t one on earth that would damage them.
WHAT’S THE TAKEAWAY? ARE YOUR CARBON RIMS SAFE?
From our (Bikerumor’s) standpoint, the test was interesting if only to see what happens when a rim overheats. To be fair, Alto made public all of the parameters and put everyone through the same test. But as the brands here have explained, the results don’t necessarily reflect real world conditions. We see the real value as simply being a conversation starter and an opportunity to learn.
ENVE: The reality is that since year one (ten years ago now), we’ve been pushing to develop not only safe, but bombproof braking on carbon. Today we are at a point where what used to be our most common reason for a rim warranty is now non-existent. We literally haven’t had a heat related warranty on any of our wheels that are using our latest materials, processes, and resin systems.
Finally, if you’re starting a wheel company, and find that your wheels are testing 10x better than every leading wheel manufacturers’, with generally good reputations for producing high performance wheels that are also safe, maybe you should ask yourself, “what’s the matter with my test.” There are certainly some brands who are behind the times in terms of braking performance and unfortunately they’ll have to figure it out just like we’ve had to do. The real world results are certainly backing up our lab results and indicating that for ENVE’s consumers, heat damage to brake tracks is a thing of the past.
In summary, regardless of this test and the questionable protocol, we have 100% confidence in our latest carbon brake track technology. The texture is meaningful and for this reason: Given the higher amount of friction and initial “bite” you get a feeling closer to that of disc brakes. Riders then have a more tactile braking feel. Lost is that terrifying feeling that accompanies most smooth carbon braking surfaces where you aren’t sure you’re actually slowing down or braking at all despite your death grip on the lever. Ultimately, our brake track texture results in less contact time between pad and rims and therefore better braking performance.
Starting at about 4:15, the video above shows Mavic’s brake dragging descent test on their “Ventoux Test”. This test puts a 220lb (100kg) rider on the bike, then they ride down the steepest 10km of the Ventoux decent (avg ~10% gradient) with the ear brake engaged for the duration of the test. All of their carbon wheels must pass this test. The first part of the video shows some of their testing and measurement equipment.
MAVIC: I would argue that we have the most stringent testing methods in the world for bicycle wheels and it is not a topic we take lightly. Consumers need to know that this test does nothing but show a biased test that was run in a way that the only outcome would be that the Alto wheel performed better than some of the best wheels in the world.
I am not at all criticizing their motives – I have to believe that their intentions where noble – but this was simply a failure in terms of offering consumers reliable information in terms of making an educated and confident purchase. I am more than surprised that when they saw the results that they didn’t question their testing method. It is unfathomable that a wheel company, that has only existed for less than five years, could suddenly have a wheel that performs so dramatically better than the others in the test.
Finally, I would like to add that as a brand that has made some of the best wheels in the world for more than a century, we are 100% sure that our carbon clinchers are reliable and safe. We do not have the conversation about safety in carbon clinchers like the industry has in the past because we are totally confident in our research, engineering, development and testing. Now that we have added UST rim technology to our road range, we are also confident that we have the very best carbon clinchers available in the world. They perfectly balance performance and reliability and are the only standard for having all of the benefits of a tubeless system that is also user friendly. I hope that you can share that sentiment with your readers to ensure that they are hearing from the other brands in the same way that they have now heard from Alto.
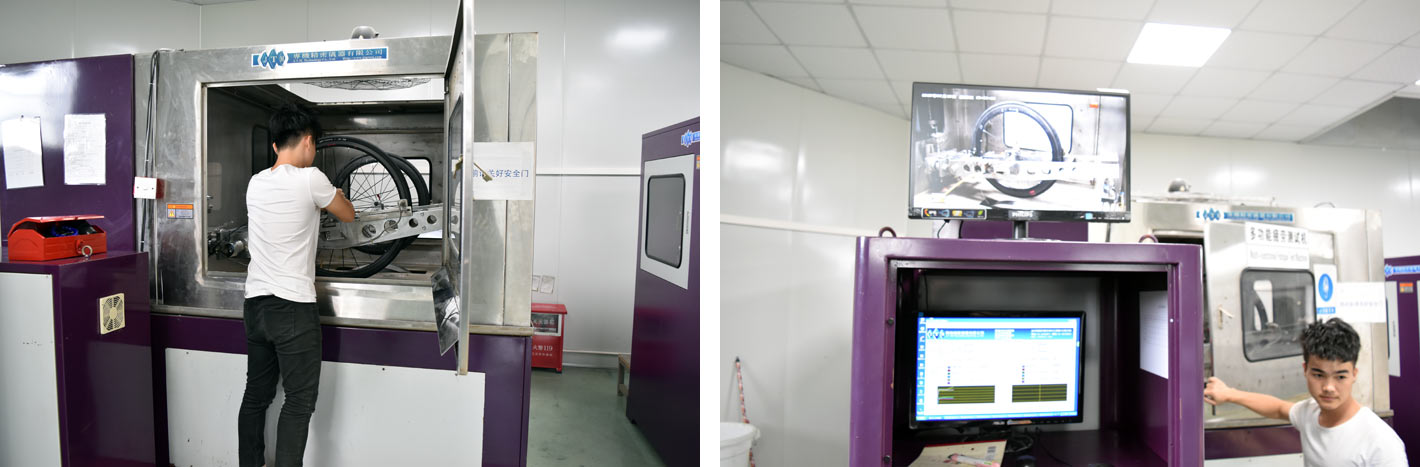
BOYD: Heat is only one thing to talk about, but there are so many aspects to focus on rim and wheel development. Recently, the UCI has developed a test that wheels need to pass in order to be used in the highest level of competition. That test involves dropping a known load from a known height to calculate the impact in joules of force. The UCI sets this at 40 joules of force to pass the testing. It is well know that as you increase the temperature rating of the resins, that brittleness of the rim increases. Zipp, when they developed the Firecrest series talked about how hard it was to find a resin that could handle the high temperatures, but also be suitable for the impact demands of riding a bicycle wheel. You don’t want to be going down a mountain, hit a pothole, and have a rim shatter under you.
As part of having a great relationship with our manufacturer we were able to develop a resin that can withstand temperatures of 205 degrees Celsius before failure. This is over twice the temperature to boil water. Impact strength and ensuring the rim did not become too brittle was also key. We were able to work with them to develop a high temperature resin that can withstand multiple impacts at almost 2.5 times the UCI testing protocol!
Further Reading:
One of the engineers that does CFD work for Boyd Cycling wrote a very detailed post evaluating the Alto experiment from an engineering point of view. Geek out on that, here.
Huge thanks to ENVE, Boyd, Mavic and Alto for their responses, photos and time!