While SRAM was founded and is based in the United States, they’ve managed to create quite a global footprint through both expansion and acquisitions over the years. One of their largest facilities outside of their Taichung factory and U.S. headquarters in Chicago is the drivetrain development facility in Schweinfurt, Germany.
This location is focused on drivetrain for both road and mountain bikes, but it also serves as a European sales and marketing support center. As you’ll soon see, it’s massive, with plenty of room to grow. Let’s step inside…
All drivetrain parts, including shifters, are developed inside. Around 160 people work here, 80 of them in product development. All European marketing is based here, plus sales and dealer service for Germanic shops. Numbers-wise, this is a small part of the approximately 3,500 employees globally (that’s an average throughout the year), of which up to 500 are in product development.
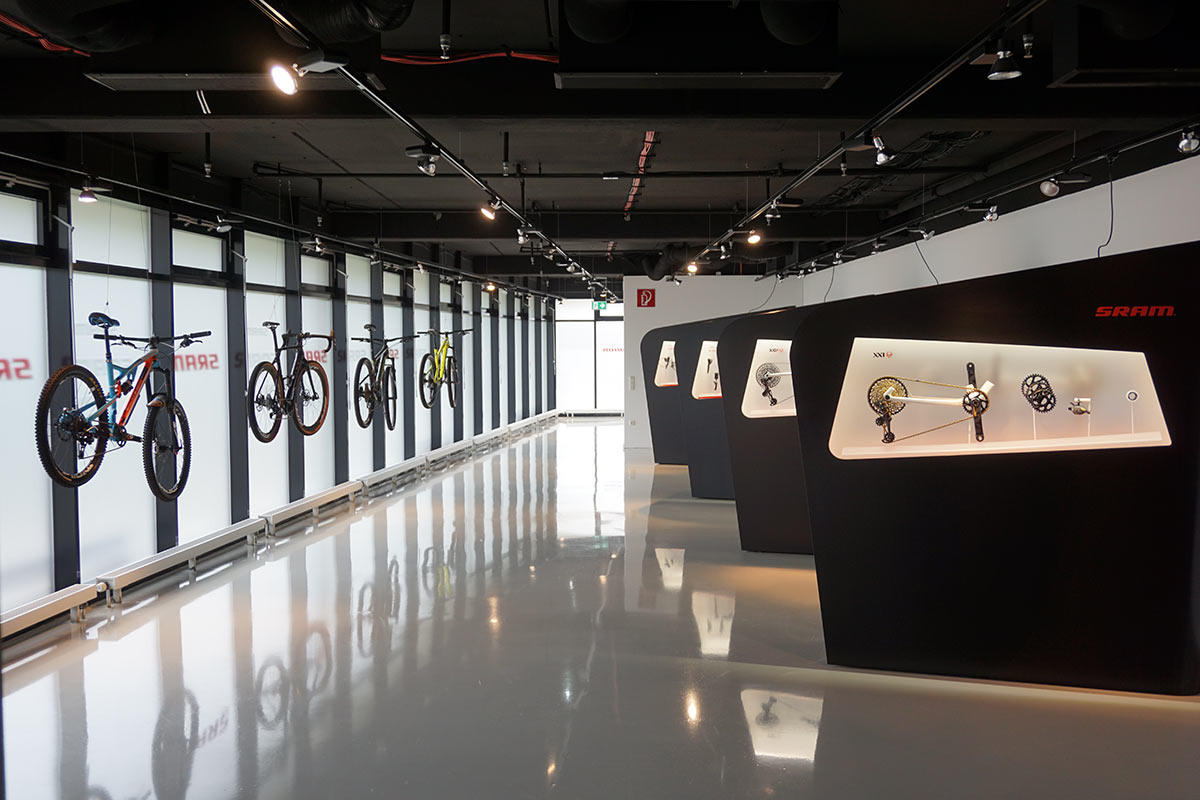
Many engineers came from the automotive and aerospace industries because they got tired of working on things they’d never be able to personally use or see. SRAM mostly designs the products in the markets where they’re used, but manufactured where the OEM customers are making their bikes. Hence suspension development in Colorado, drivetrain here, etc., but manufacturing in Taiwan so it’s close to the frame manufacturing and assembly.
They moved to Schweinfurt when they bought Sachs in 1997, which was their first acquisition, and moved into this building in 1998. Sachs’ internally geared hubs (IGH) were made here originally, but that has moved to Asia. Chains are made in Portugal, where Sachs had been making them for years before the acquisition.
Use this lounge area for product launches and OEM, industry and other related meetings, there’s also a small Biergarten outside. Behind it are meeting and conference rooms.
Behind those is the dealer service and tech training area. They offer training classes for dealers that costs about €90, but they go home with a set of SRAM specific tools and hands on, one-on-one training, and it usually sells out in two weeks for the entire season (Nov – March). They also use this area to host OEM customers to show them how to use the new parts on their bikes or train their own support and tech staff.
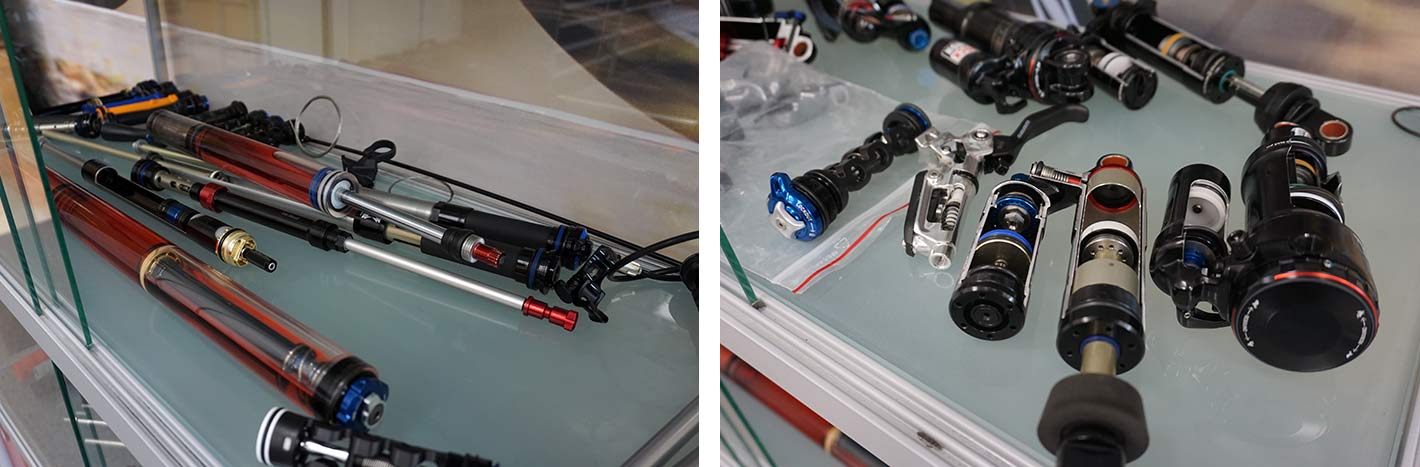
These training bikes hanging from the rack have errors intentionally built into them to see if people can catch them. The Pinarello is likely there to show how things should be.
Their Dealer Service area has 12 employees to handle call in questions and also work on maintenance, repairs and upgrades sent in by shops. Turnaround time is 24 hours most of the time, 48 hours max during the busy season. The goal is that if you break something on the weekend, you could drop it off at the shop on Monday and have it back and ready to ride by the following weekend.
They typically stock parts to service brakes, suspension and drivetrain parts as far back as 10 years old, depending on the part, and some older IGH’s.
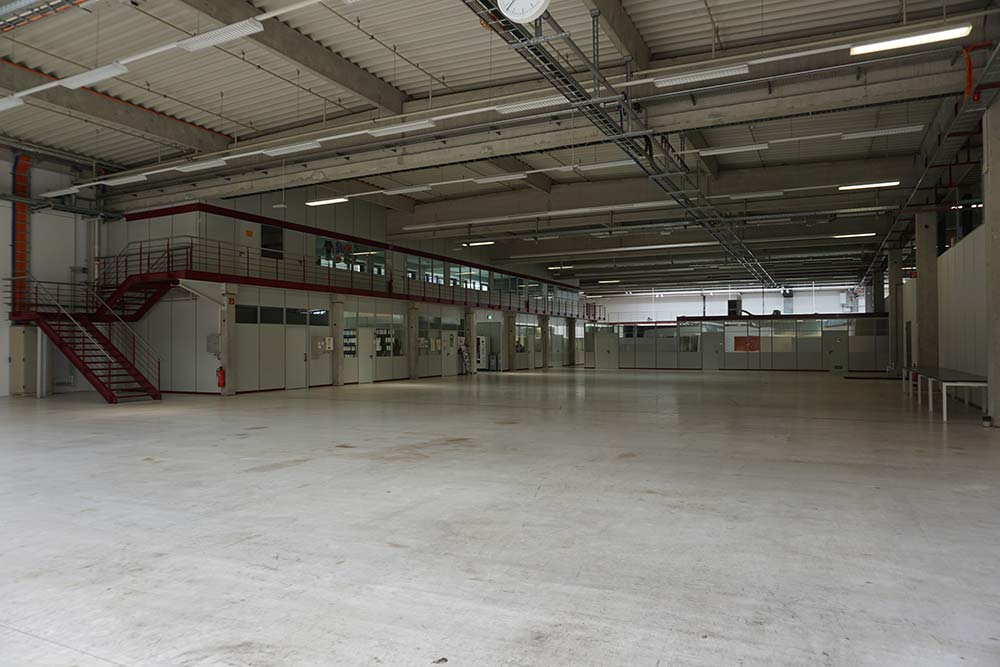
Sachs’ 3/5/7-speed IGH manufacturing was in this open space, now it’s used for temporary storage.
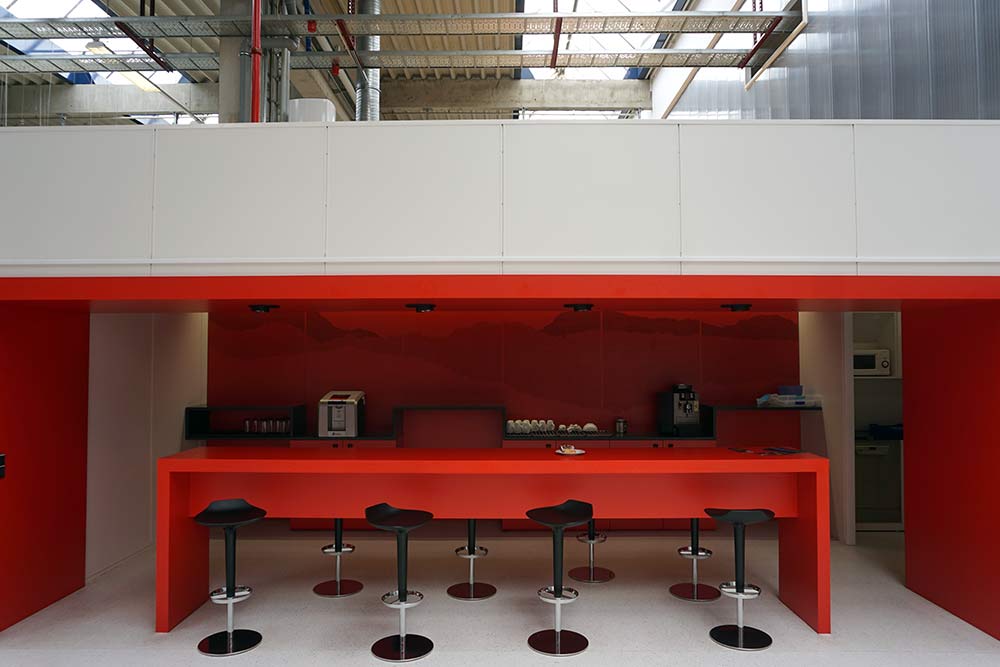

Turn around and you’ll find the entrance to the engineering room, where they have a mix of engineers, designers, patent attorneys and others that all work near each other to facilitate quick and open communication. Their timing allows them to communicate with Asia in the morning and the US in the afternoon, too. This is as close as they’d let us get.
The warehouse in the back holds parts for their other DSD service centers, helping them get parts quickly without having to have their own oversized warehouse. They used to store more catalogs and marketing materials too, but now most of that is digital so there’s a bit more free space.
Out back is a pump track with test ovals on the outside that have different surfaces to test on. At the back is a steep hill where they can test shifting under load. In the center is a massive pump track with wall ride (just off image to the left), but it was a bit overgrown during our visit.
On the other side of the building is the test lab, where they can put drivetrain parts through their paces. High power motors let them test the lifespan of a component in about 7 days. Different settings let them test under loads that simulate the riding behaviors if pros, average riders and “lawyers and dentists”.
Different machines can simulate environmental factors like heat, cold, wet, dry and pressure washing. Much of the testing equipment is duplicated in Asia so they can test simultaneously after parts are coming out of final molds and off production lines.
High speed cameras can watch shifts happen at 2,000 frames per second, with machines able to know when something isn’t going right and save the three seconds of video before and after the error so they can see how it happens.
The next major stop is the machine shop, but to get there, we passed by these reprints of original Sachs and SRAM patents.
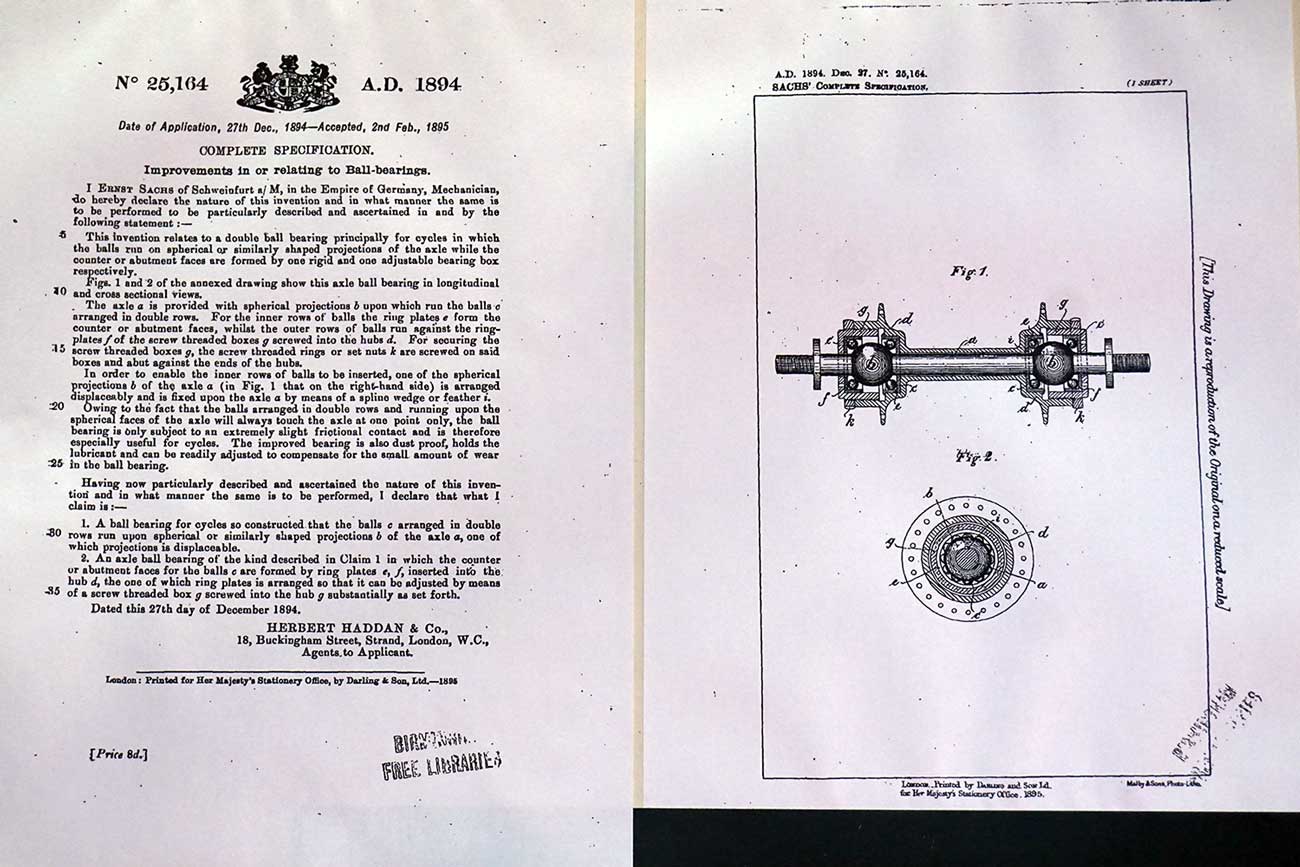
…and some original parts:

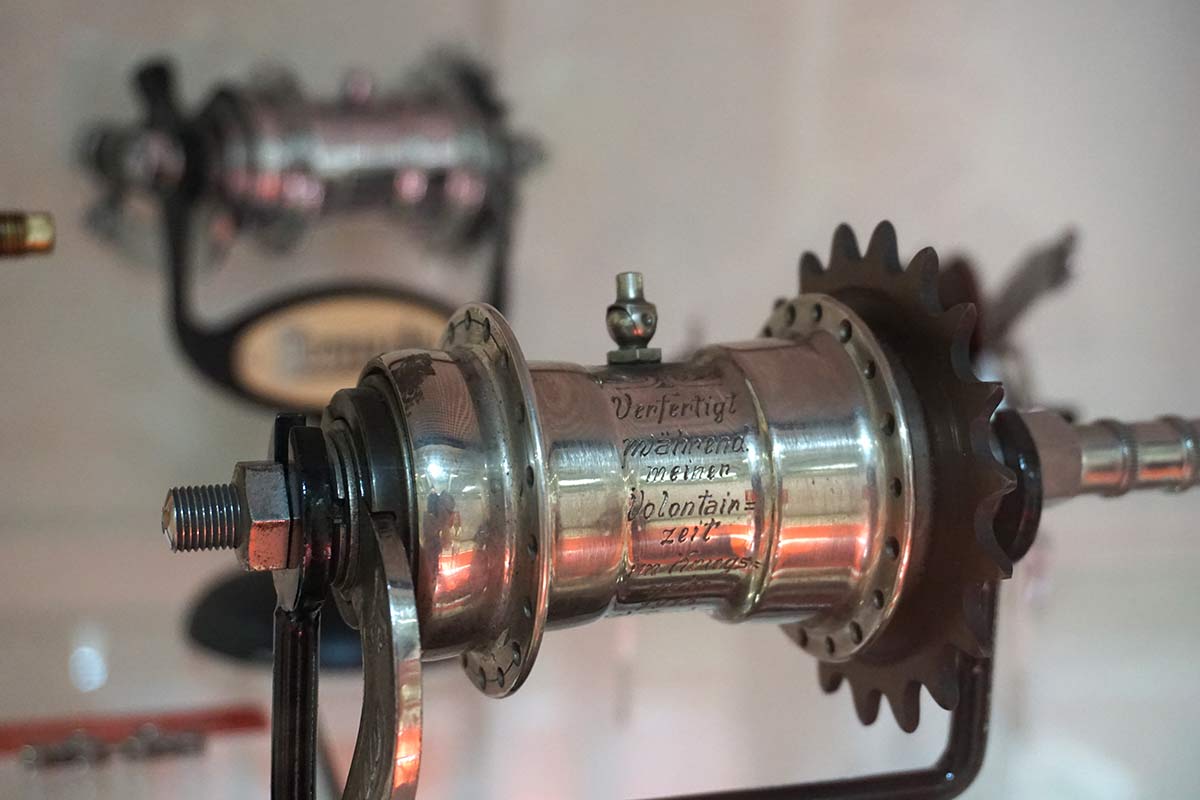
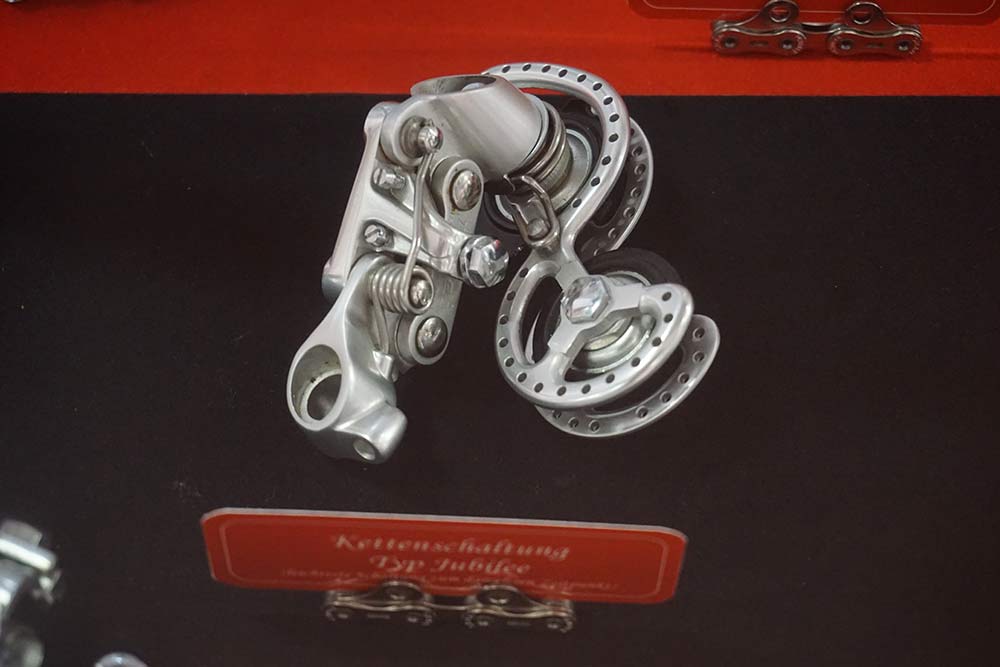
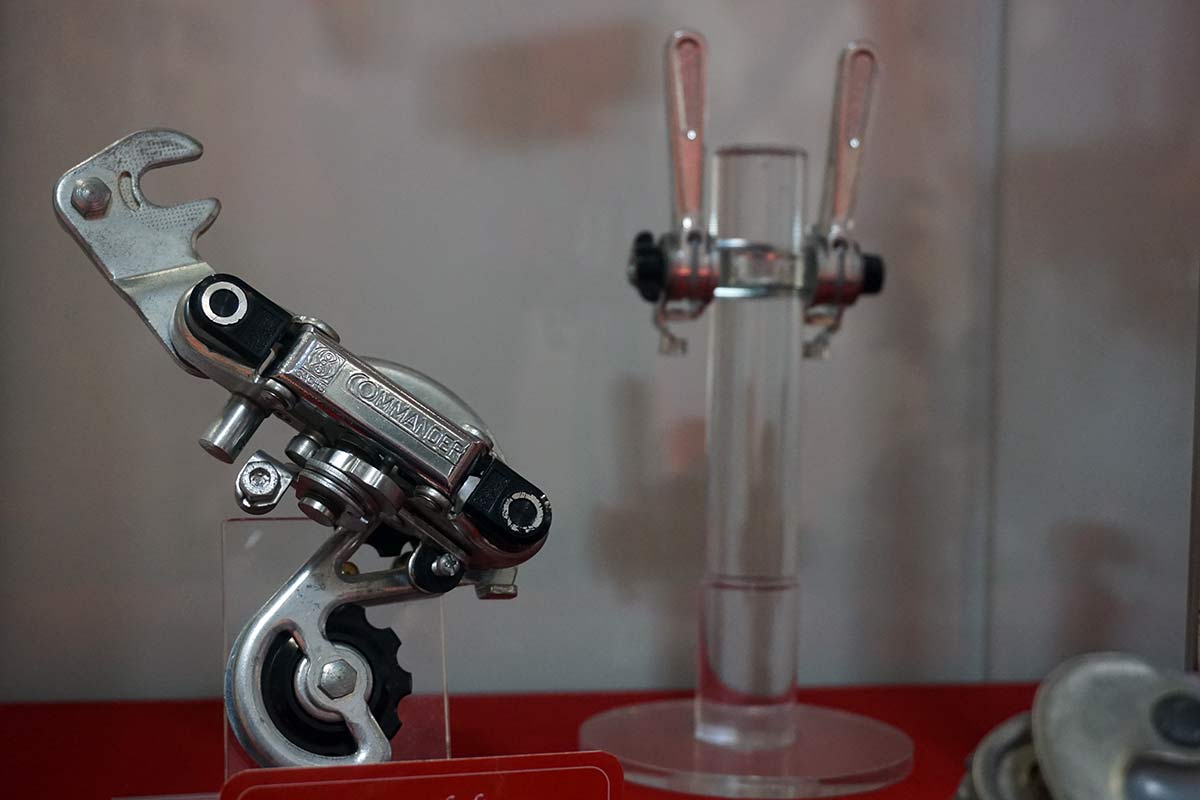
Now at the machine shop, which continues with their wide open, spacious layout, they can go directly from computer to machining and prototyping. This means they can make gears, shifters, cogs, derailleurs and more. They can work quickly, too, sometimes delivering a prototype piece to the engineers by the time they get into work the next day.
Others, like a working rear derailleur can take 6-8 weeks to complete.
Their top end cassettes start life as a solid block of metal. Having these resources lets them refine the production process, too, before volume scales up.
The marketing department looks almost like a warehouse, holding all the parts for their road, mountain and cyclocross teams and athletes, as well as media samples. They also store demo bikes for events, which could mean consumer demos or pro-level neutral support wheels, etc.
For example, this car just got back from one of the cobble stages at Le Tour (we visited them in July), where they’ll drive ahead of the peloton with a car full of wheels and water bottles, because the team cars can sometimes be so far behind that if something happens after a cobble section, they can get a rider back on the road quickly.
Sometimes they get pros’ bikes in here to install and set up the parts, particularly if they’re running new or prototype parts. The red “driveway” is large enough that their full size support tractor trailers can pull in, restock, and then get back on the road.
Employee bike parking, showers and laundry. Most of the employees ride either road, mountain or both. Head back into the main office area and you’ll pass through a small dealer showroom mock-up that shows how the products can be displayed and merchandised in a bike shop.
On the way, you’ll pass the measurement lab, where they test the size and shape of finished parts, as well as checmical analysis to make sure the parts are made of the right materials. There’s a similar lab in Asia to check things once they’re in mass production but the initial parts are always checked here before ramping things up to full speed.
And that’s what goes on at SRAM’s Schweinfurt, Germany, headquarters. Thanks for the tour!