There are definitely some things ENVE wouldn’t let us take photos of. But our factory tour video exposes a lot more about the process they use to make their new custom carbon road and all-road bikes.
Watch, and you’ll get a good sense of how they’ve taken their carbon fiber expertise honed from so many years making high-end rims in house in Ogden, UT, and applied that to making a really killer frame.
What stood out to us is how they’re able to make advanced aero shapes and still do full custom sizing. This isn’t as easy as it seems, and it’s not common. Yes, there are a lot of great custom handmade frame builders out there, but few are using aerodynamic or other complex shapes.
The challenge lies in being able to make those shapes and still offer a wide range of frame sizes, let alone a nearly infinite range of sizes to fit any rider. ENVE’s figured it out, and had the resources to make it happen. Below are a few select photos from the tour to complement the video…
How ENVE road bikes are made
This is what a raw, finished ENVE road bike frame looks like before any paint or hardware. It’s been bonded and overwrapped, and that’s been cured and dried. But it takes a lot to get to this point.
From the customer’s perspective, it starts with giving them your fit and geometry numbers. For ENVE, it starts with making the tubes. Yes, they make the tubes before they have your data…
And that’s because all of the tubes are made longer or taller than necessary. They have 2, maybe 3, molds for each junction on the bike, which gets them in the right ballpark for the angles.
Above is a headtube-top tube piece (upside down) wrapped around their proprietary “soft mold” (which we weren’t allowed to photo). This method gives them something that they’re able to force into complex shapes that are firm enough to wrap carbon plies around, yet then still be removed after production. It’s clever, and it’s reusable, but we can’t tell you what it is.
These are the individual tube molds that are used to shape the mandrels that they wrap carbon around.
The reason they can make only a few different parts for any size frame is because once the longer-than-necessary tubes are made, they simply cut off the extra. If you need a short seat tube and head tube, they’ll cut off more. Taller, longer riders’ bikes would have less tube removed. Then it’s all bonded together, overwrapped, and cured into a final frame.
From there, it’s on to finishing and paint. Above, a couple of bikes are finished in paint and waiting to be moved to assembly. Behind them on the wall are customer builds waiting for paint, with notes to the painter on which colors to use.
Before paint, bikes go into this sealed room for any final sanding and touchups to smooth things over. Then they’re into the paint booth…
Each bike starts with a glossy clearcoat to prep it for the final paint. After that, they’ll apply one of 38 colors in one of four templates. You can also choose gloss or matte for each color within the templates. Which basically means 10,000+ combinations. Or you can go full custom, like these:
These bikes were in the stands during our visit. The darker one in the background is for an employee, the middle one’s for a customer, and this green one is for…
Check the video for a few closeup details on it. Our guess is we’ll see it as a promo bike from Chris King very soon.
The bikes are sold as a “Chassis” including seatmast topper, fork, thru axles, and their full custom one-piece handlebar and stem. That means you get to specify the exact width and stem length you want, and then it’s cut, bonded, and molded into a one-piece unit.
Cables and hoses and wires run internally through the bar, into the stem, and then into the head tube through oversized spacers and/or top cap. Nothing’s visible from the outside, so it’s an incredibly clean look.
Add wheels and it’s a “Rolling Chassis”, or you can spec the drivetrain and order it as a complete bike.
This one’s an employee’s bike with custom paint and a nice example of how detailed they can get.
This white bike is another employee’s bike, belonging to the ever-faster-than-us Neil Shirley. Doesn’t even matter that white is literally the heaviest color you could choose, there’s still no way we’ll ever catch him.
The ENVE Custom Road has a very aerodynamic front end, with flattened handlebar, hourglass headtube, and a fork crown that blends into the head- and downtubes for smoother air flow. Impartiality aside, it’s gorgeous.
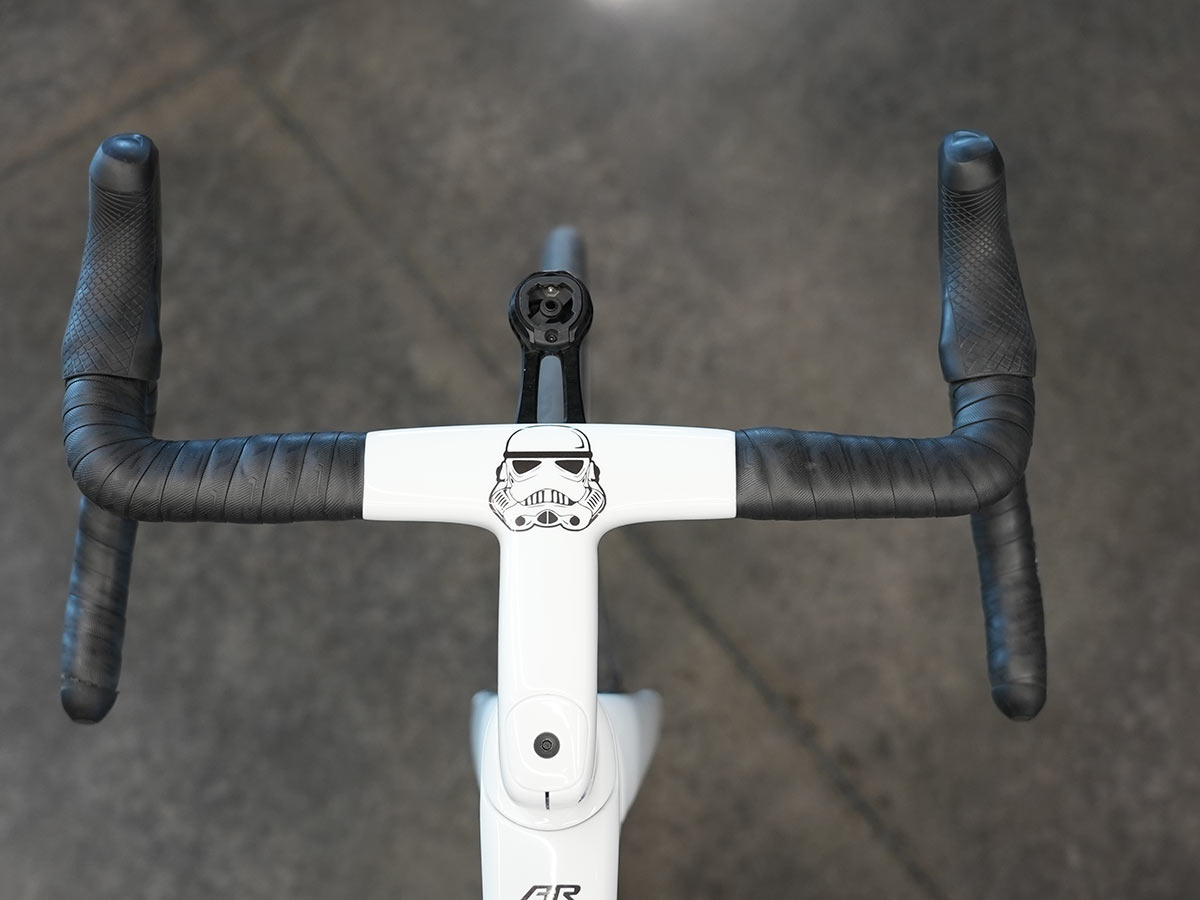
Their handlebar allows for the cleanest bar tape wraps we’ve ever seen. Neil says he starts at the middle, right up against the raised section in the center, then wraps outward to the drops.
ENVE’s handlebars use a tapered, rounded conical end with a rubber booth that flaps over the tape, allowing such a wrap.
The rest of the bike is fairly normal looking through the BB junction, seat tube and stays.
The complete bike includes this custom embossed, carbon rail Selle Italia saddle with the ENVE logo on the nose.
Most of the actual carbon fiber layup and production method are the same as used to make their wheels. Check out our photo tour from the grand opening of their new HQ to see more photos of that process and the rims. Get all the details on the new bike in our launch coverage.