We know, there’s no such thing as a stupid question. But there are some questions you might not want to ask your local shop or riding buddies. AASQ is our weekly series where we get to the bottom of your questions – serious or otherwise. Hit the link at the bottom of the post to submit your own question.
Welcome back to the Bikerumor Ask A Stupid Question series. This week we’re taking on Press Fit Bottom Brackets with the experts from Hope, BBInfinite, Kogel and C-Bear. Your contributors are as follows:
- Sam Gibbs, Design Engineer at Hope Technology
- Gary Mailhiot, COO/Product Development at BBInfinite
- Ard Kessels, Owner/Founder of Kogel Bearings
- Bart Schouten, founder and general manager of C-Bear
Why do press fit bottom brackets always end up creaking so bad? And, why are manufacturers still spec’ing them when they know they suffer from this problem?
Hope: In theory, a press fit BB can offer a number of advantages. It can create more space to use larger bearings which have a larger load capacity, and usually the overall weight will be reduced. Depending on the design, the BB shell on the frame can be wider which allows the BB area of the frame to be stiffer. Generally, it also makes the frame easier and cheaper to make, especially on carbon frames where any aluminum inserts can be removed entirely.
The problem with press fit BB shells is really in the execution. The system relies on a precise fit of the BB cup or bearing into the frame. It can be hard for frame manufacturers to maintain the close tolerances required especially when the final size is molded into the part.
Also, there is no axial clamping force when compared to a threaded BB; this means the cups are much more likely to move relative to each other when under load and as the BB shell flexes. If any relative movement does occur between the cup/bearing and the frame, however small, this will cause wear resulting in permanent damage to the frame and your BB will always creak! Hope press fit BBs have a threaded center tube that pulls the two BB cups together to eliminate this problem.
I think we are seeing a lot more manufacturers moving away from press fit bottom bracket designs and back to threaded designs, either traditional or T47 type. In general, manufacturers work a few years in the future so changes like this can take a while to filter through as designs are fixed in advance.
Some manufacturers will continue to pursue the press fit designs due to the advantages listed earlier. Ultimately, any change will be consumer driven and whether the customer values lighter weight over longevity and serviceability.
BB Infinite: This is coming from a guy who manufactures and sells a lot of press fit bottom brackets, so here it goes: It is probably not the bottom bracket creaking when you pedal your bike. I am not even talking about our world famous, super-awesome, one-piece, hub-style press fit BB modules in particular. Let’s assume what we have is one of those plastic BBs they cram into production bikes. Yes, that one. It’s probably not creaking.
This article is sure to get into all kinds of technical analysis from the other contributors, and perhaps some bemoaning of the industry’s lack of standards, all of which will be valid i’m sure, but let us for a moment address the lack of proper diagnostic standards plaguing the industry. We’ve corresponded with thousands of people who open the conversation with, “My bottom bracket is creaking” and the first thing we want to know is how they came to that conclusion.
If you are riding along and your bike starts to creak, what should you do? First, do not assume. If you do you will fall into the trap of target fixation. A bicycle is a complex assembly with myriad interfaces and a host of moving parts with a person on top whose dynamic movements flex and stress the entire thing this way and that.
If you bring your bike to a mechanic, do not say, “My bottom bracket is creaking” because you risk prejudicing them. You want them to have an open mind. Just say it makes a noise when I pedal, or something like that. Next, listen to the response. If the first thing you hear is, “It’s these stupid press fit blah blah blahs”, that could be a bad sign. What you want is someone who immediately takes your bike out for a test ride after asking a few questions that may be in their mind. But the most important thing is the test ride. That MUST happen.
Next, they should start ruling things out. I always check the skewers/thru-axles first because that is an A-numero-uno place for a creak to hide. Then the ride. Always the test ride. Keep test riding as the process continues.
If creaking is confirmed, move on to swapping out the pedals for regular old platforms, no clips or cleats. Go ride it. It goes on from here. Check out our Kill That Creak blog for the full run down.
The key is that you should know what you are fixing before you fix it. It sounds trite but these things start out in the emotional realm. Your beloved bike is ruining your mojo like a puppy peeing on your favorite shoes. Take a breath and re-engage the logical part of you. Put all speculation out of your mind. Don’t guess. It’s a mechanical system.
The idea that, “Press fit bikes just creak” is preposterous. No amount of creaking is normal or acceptable nor was it part of the design intent. Creaks can always be fixed, and if not, such as with a cracked frame, you can at least know for certain what was causing the issue when you go through the diagnostic process.
When a press fit BB does creak it has likely come loose and can shift around inside the frame. Creaks are movement, so if it is moving it is creaking. Therefore, you should never install a press fit BB with grease. Always use the proper retaining compound like VibraTite530 or Loctite 609 or whatever the BB manufacturer recommends.
Oh, and cranks creak too. Check out our blog on that one here. You should also check out this video on spline interfaces.
One other thing I should mention about cranks creaking is the issue with Shimano, bonded-together hollow crank sets coming apart. It is uncommon but not rare. If you have a creaking problem, you should inspect the box structure of the arms for cracks as part of the diagnosis. Now, on to hawking the BBInfinite wares.
Multi-piece press fit BBs can work fine. If, by fine, we mean a crank can rotate in it. Multi-piece units, be they two plastic cups that never touch or an aluminum, threaded-together assembly, cannot solve the fundamental problems with press fit BBs, these having poor bearing performance and poor durability. The first wastes your hard-earned wattage and the other wastes your hard-earned money.
Poor bearing performance has little to do with bearing quality and everything to do with bearing alignment. Carbon frame bottom bracket shells are laid-up by hand and then hand sanded, so the outside of the BB shell is not straight up and down, or square, meaning that the left side of the shell and the right side are not parallel. Once you install the two halves into the frame, the left one will not be perfectly aligned with the one on the right.
Check this out. The red BB above is one of our one-piece bottom bracket modules. Note how a 1-piece module corrects the misalignment.
This kind of frame shell misalignment is typical and not unique at all. You have probably never noticed this because the independent halves of multi-piece systems, be they pressed in or threaded together inside, conform to misaligned frame shells.
Now, imagine how the bearings react to this situation with one sitting at one angle and the other at yet another angle and the crank spindle forced between them. With every pedal stroke the right bearing will be fighting the left bearing. This action is what loosens two-piece cups and walks them out of the frame, which causes creaking.
When the BB is held rigidly in place in a misaligned state by threads or retaining compound the result is degraded bearing performance and accelerated wear. Here’s a 3-D animation that breaks it down.
As an aside you could not use angular contact bearings in a system in this condition. Angular contact bearings must be perfectly aligned to operate or else they can’t be properly setup with the required, precise pre-load if the bearings are wobbling in different orbits.
Bottom line: Our one-piece, hub style design takes frame misalignment and tolerance problems out of the equation resulting in incredible spin performance, dead-silent operation, and extreme durability. It is that simple.
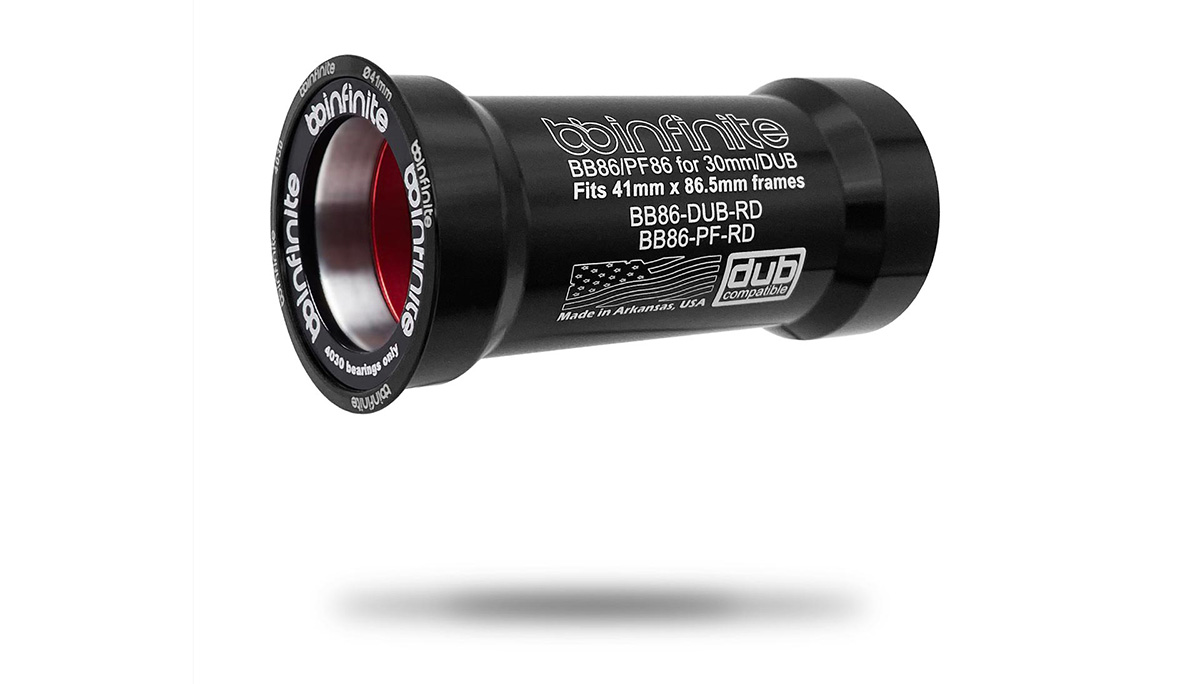
As to why the bike industry continues to product press fit bikes “…knowing they suffer from this (creaking) problem”, I say go back and read what I opened with: The creaking is generally not coming from the bottom bracket. It’s commonly a problem of misdiagnosis.
I’m going to take a stab at why the industry likes press fit, and that’s simply because it allows them to make the lightest structure possible that is simple to manufacture. It also solves the problem of bonding dissimilar materials together, such as carbon and aluminum, that expand and contract at vastly different rates and temperatures, thus reducing frame warranty issues due to delamination.
So, are there tolerance problems in the industry? For sure. We address these with our design and with corrective measures that we advocate, just go check out the vast collection of videos on our YouTube channel and Facebook page. Do press fit BBs creak? Yes, they can, but generally they don’t. What you should be concerned with isn’t the potential for creaking but rather how poorly that multi-piece press-fit bottom bracket is performing, sapping wattage and making you work more for less.
Kogel: A creaking bottom bracket is a quick way to ruin your ride and send your mind into overdrive. I understand how it has frustrated riders since the days of square taper bottom brackets.
In theory, all press fit bottom brackets are great, but they suffer from a range of micro problems that lead to creaking and premature failures:
The reason: cost and weight
The main reason why frame manufacturers choose press fit bottom brackets is to save weight and production costs. Since it is virtually impossible to cut threads in carbon, a threaded aluminum sleeve needs to be placed inside the bottom bracket shell for a BSA, ITA or T47 set up. This adds complexity, cost and a little weight to the frame. For these reasons, frame builders will use a press fit bottom bracket to make a lighter, cheaper frame.
Problem: frame production tolerances
The diameter between the largest and smallest acceptable size in a Press Fit 30 bottom bracket is only 0.05mm. In the real world, at Kogel we consider any frame that is +/- 0.20mm workable. We have seen production frames that are off by 0.50mm. Carbon cannot be produced to the same precision as metal parts and to think it can be done at scale within 1/20 of a millimetre is wishful thinking.
Problem: narrow bearing stance
In a BB30 or Press Fit 30 setup, the distance between the bearing seats is around 68mm. In a BSA threaded setup it is closer to 90mm. This extra width reduces the load on the bearings. The narrow stance is more prone to wear out the bearings or make them move inside the BB shell.
Problem: Plastic cups
Often, component manufacturers use plastic bottom bracket cups, because they are flexible and easily adapt to imprecisely manufactured frames. While that sounds great, plastic is just not the best material to be loaded thousands of times on each ride. At one point it will deform or crack.
Problem: installation
Ask five mechanics about their way of installing pressed bottom brackets and you will get five different answers: one cup at a time or both at the same time? Dry or Loctite or grease or copper paste? Since there is no clear industry wide consensus from the brands, it’s only logical that some of these methods are superior to others and the not-so-great ones lead to creaking.
Solutions
Since our first product line at Kogel was a range of bottom brackets that guarantee your bottom bracket to stop creaking, we have spent an unhealthy amount of time analyzing the problems and coming up with solutions.
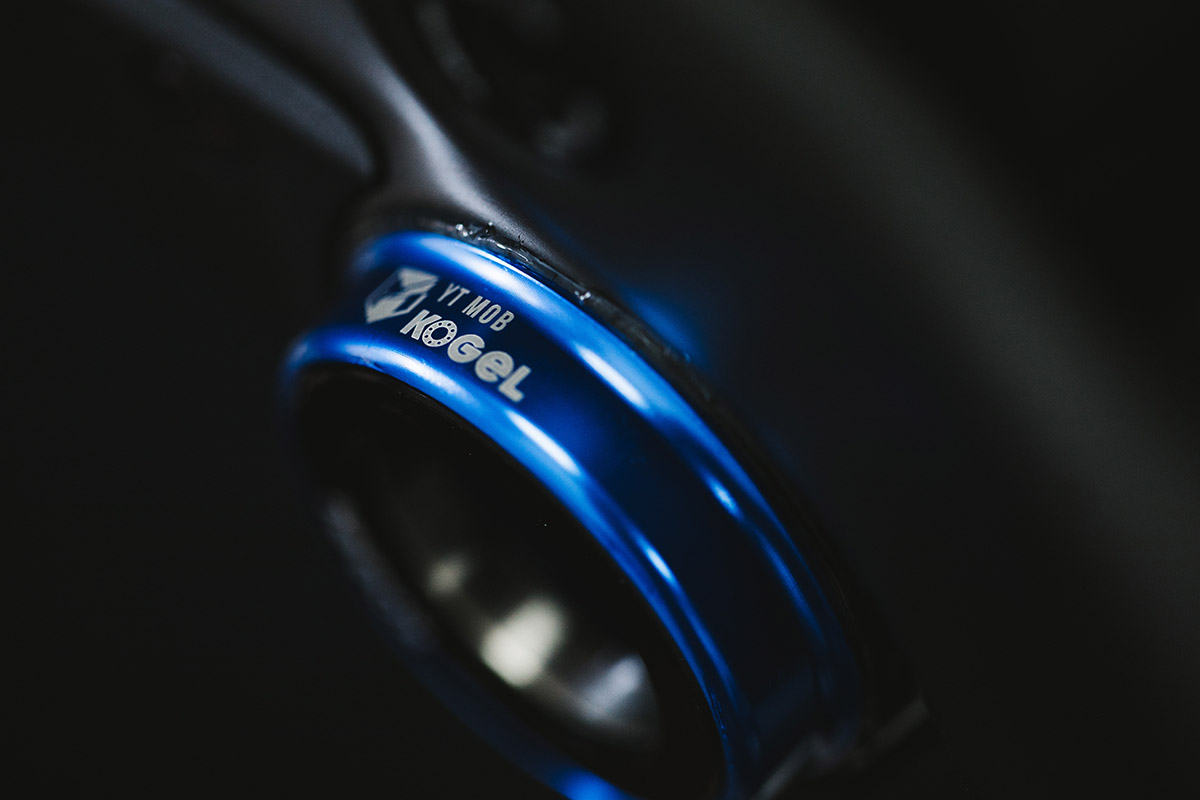
Using aluminum cups and high quality bearings is a given. Through precision machining we can cut our cups slightly larger than others: we cut our PF30 cups to the upper tolerance of the Press Fit 30 standard and discard any cups that are larger and would potentially void a frame warranty. We reduce the diameter of the cup sightly for internal bearings to avoid compression.
Kogel places the bearings right next to the crank arms, the widest possible stance guarantees a stiffer setup and less bearing wear.
On a side note: the bottom bracket takes blame for a whole range of creaks that are not the bottom bracket: crank arms, chain ring bolts, shoe cleats, a loose thru-axle, suspension pivots, all sound very similar to a creaky bottom bracket. We published a blog a few years ago to tackle this problem. Find it here.
And finally: use our Aqua Proof Paste! We private labeled this product from another company and sell it at low margin because it is just so darn good. It is developed for the off-shore industry: salt water resistant, it does not degrade over time and does not affect your carbon frame. You can use it on all bolts or to waterproof head set bearings as well. We call it Shut Up Grease in our office and it lives up to that name.
C-Bear: To be fair, is this a factual statement. Or more a general impression and with labeling effects and any noises that seem to be from the BB get lumped into BB creaking. This impression turns into general consensus/fact.
However, the fact that bonding a press fit into a BB shell has become the norm, is an alarm bell. It may be a precautionary measure but should not be a rule, in our opinion.
For C-bear, we take pride from the fact that our design does not need a bonding agent. We are the first to offer our entire range of PF BBs in an aluminum housing as opposed to a Delrin material. This allows for a more custom fit than the “add this, add that bandage” approach, which subsequently has become an industry trend.
As a matter of fact, we are known across the industry as the silencer. We keep to our classic style without over engineering. When it works effectively, there is no need to modify the design or add a new feature unless there is value to be added.
Press Fit itself, when made well and within the required tolerances, is not the cause of creaking. It takes each part of a bike to be correct to get a completely satisfactory performance.
Consistency = control = costs. Different brands have different operational philosophies and structures, therefore different quality and pricing. This is true even for us where the bottom bracket manufacturing process is much simpler and involves fewer parts and types of material. It is still a process that needs to be controlled every step of the way. There are two things to consider:
- Material
- Its type, source and batch
- Production
- This refers to the machine, the process, each cutting tool, and periodic checks during each production batch
- Anodization
- type of anodization, evenness, consistency, batch, operation labor
- Quality Control of even the simplest step, checking with standard measurements… this is simple but still needs to be observed and observed consistently
A simple BB is itself more complicated than what you see. We have still not touched on other component parts of a bottom bracket.
What about installation, usage, and maintenance… All are influencing factors in the entire equation. A Press Fit BB shell is comparatively easy. I suppose that is one of the reasons manufacturers keep using the standard.
As to why manufacturers are still spec’ing them, this question is for the bicycle manufacturers. Press fit itself is not the problem, the more pressing question is why has it not been a priority to get it right?
Got a question of your own? Click here to use the Ask A Stupid Question form to submit questions on any cycling-related topic of your choice, and we’ll get the experts to answer them for you!