We know, there’s no such thing as a stupid question. But there are some questions you might not want to ask your local shop or riding buddies. AASQ is our weekly series where we get to the bottom of your questions – serious or otherwise. Hit the link at the bottom of the post to submit your own question!
Mavic has a lot of history in the cycling world. That’s pretty clear when you glance over the massive amount of questions we received for this installment of our AASQ series. As such, we sent as many of them as we could over to Mavic’s Global Brand Manager, Chad Moore and Road Concept Manager Maxime Brunand, to get the answers. We honestly didn’t expect Mavic to be able to answer so many of them, which is why we are going to split this one into two parts (and may have Mavic back for a third, if you have more questions!). Today’s installment covers many of the tech questions we received from hubs to rims to dropouts, while next week we’ll dive into tubeless tires, rim width, and the company itself! Enjoy:

- I would like to know why your freewheel bodies are so unreliable (I never saw one last longer than 18 months, MTB or road)? What are you doing to solve that issue? Leo
Mavic: We have a few different freewheel systems that are still around and available. The older one, called FTS-L (using two pawls) used to present premature wear of the pawls by creating a “sludge” when not maintained properly. This would eventually damage not only the Teflon ring, but also the hub shell itself. From that point, exchanging the freehub body would not be enough, as the play would come back due to the damage to the hub shell. To solve this, back in 2009, we strengthened the pawl material and changed the tolerances and we have had extraordinarily few issues with the system since then. But people tend to live on old beliefs and opinions no matter how far in the past the issues are.
If you’re talking about ITS4, our four-pawl system used in our MTB wheels until 2019, we indeed had some issues with bearing wear and system play. Over the years, we’ve worked on new axle machining and tighter tolerances until we finally solved most of the issues, while always offering the possibility to upgrade an existing hub with the new parts. Starting with the 2019 range, the MTB wheels are now running on our new ID360 system (ratchet base) from which we’ve seen an extremely low return rate after four years of use in our road wheels and three years of internal testing for MTB.
In the end, all those issues discussed here are covered by our warranty program, within two years (three if you register your wheels at mavic.com). But we apply the two (or three) year “rule” with some flexibility. =-)
2. Why is there a bushing instead of a bearing at the low speed end of your freehub bodies? Ryan
Mavic: Hi Ryan. You’re describing the freewheel body of our FTS-L system and we’ve been using this design since 2002. Prior to 2002 we used a cartridge bearing, but this location on the hub sees very high loads. The maximum load of the cartridge bearings was about 300kg whereas the bushing can resist close to a ton before being damaged. Very often, we would service hubs where the bearing was totally destroyed. So, the Igus (self-lubricating) bushing is a stronger and more reliable solution. At one point, the bushing had the reputation to wear out and create some play – this was true until 2006 when we reviewed the design of the hub. In fact, what caused the bushing to wear out was the premature wear of the pawls which would create a kind of sludge (mentioned earlier). By changing the pawl material, we solved that issue and, thus, the bushing wear issue. All of that said, this hub technology is now used only in our entry level alloy rim brake wheel-systems.
3. Why did you stick with two pawl freehub body system that used a bushing that wore out and essentially rendered the hub useless if not serviced at the exact interval every time?
Mavic: See answer to question 2 and, by the way, we’re not sticking to it 🙂
4. Are you still using Delrin as a bearing in some of your hubs?
Mavic: Please see the answer to question 2.
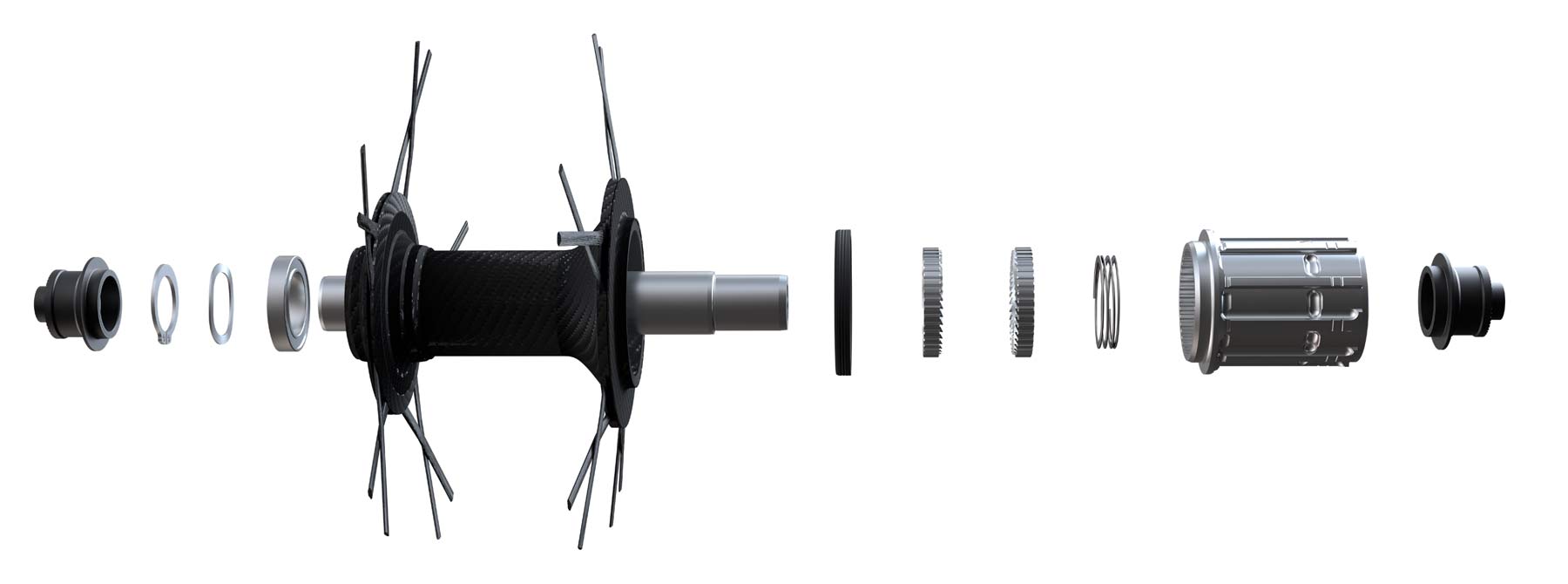
5. Your Mavic ID360 hub ratchet seems very similar to DT ratchets. There seems to be two notable differences, your ratchet system only uses one spring (one floating ratchet) while the DT Swiss design has two. The other difference is that you are using a wave spring while the DT Swiss uses conical compression springs. Can you give us some pros and cons of each design? Jason
Mavic: Another nerdy question – love it. Our research and testing on having the two ratchet rings “energized” with two springs have not shown any significant difference in performance compared to one spring. So, we decided to keep things simple with only one spring (reducing the number of hub parts). The wave washer is a very efficient way to automatically and continuously adjust the bearing preload over the lifespan of the cartridge bearing itself. It automatically compensates the changes in play that are inherent to a cartridge bearing system. Of course, the tension of the wave washer had to be fine-tuned to offer just the right amount of preload – too much and the bearing gets damaged and rough, not enough and you’ll easily get some play. One of those two results is often what you see on systems where the preload is not adjustable at all. The ID360 system has proven to be very efficient and has been used for almost four years on our road wheels. Most recently, ENVE has adopted it for their new carbon and alloy hubs.
6. After a teardown and clean on a set of older Mavic wheels, what lube should I use on the pawls…? Skip
Mavic: First of all, great !! You’re maintaining your wheels. If your hub has the FTS6L or ITS4 technology, you should only use a thin mineral oil. We do sell one that works very well, and it is available online or, possibly, through your local bike shop.
7. Why use an industrial bearing? I understand from cost point of view but looking at, for example SKF’s product information, bikes will never be in the optimal range for bearings. Also, the direction of the forces are against an industrial bearing. The only thing positive is the ease of change but who wants to service their hubs 3 times a year? Kimmo
Mavic: Great question Kimmo. Cup and cone bearing systems need maintenance that is both difficult and required regularly. Cartridge bearings (generally) last longer before failing and needing to be changed (much longer than 4 months!). Their wear has no impact on the hub shell itself, so the hub will last much longer.
Bearing construction is one thing, but equally as importantly is the way the axle and pre-load parts are manufactured and assembled – one does not go without the other. We use “industrial” bearings according to our axle and pre-load design choices.
Also, there is not only one type of “industrial bearing”. There are many different dimensions (usually, smaller are less durable) and within the same dimensions, manufacturers propose different grades of internal tolerances / play, different material for the races, the balls, the cage, the grease… All this needs to be taken into consideration by the hub manufacturers, according to how it will be assembled and preloaded. That’s what we do in order to obtain a balance between performance, reliability and durability.
8. What kind of front QR dropout design do you recommend to OEMs to avoid braking forces from affecting wheel alignment? Visa-Matti
Mavic: Very nerdy question … but these are the ones we love. It is a matter of hub design, wheel/fork or frame interface but also axle clamp design. With disc brakes, like (almost) everyone else, we recommend thru axles. 15mm works great but it seems 12mm is more easily accepted by road riders – so we followed.
In general, the greater the contact surface between the hub and the fork, the higher the stiffness. But here again, some (Shimano) have decided to set the outer diameter of the contact at 21mm for 15mm axles and 19mm for 12mm axles. Say what you will, but at least they set up a standard that everyone is using. Phew.
Usually, with a bolt on axle, you generate enough torque to avoid any misalignment and/or loosening. That said, some odd axle “levers” can show some limits here. So, we co-designed an axle system called “Speed Release” that is not only faster to operate and super light, but also ensures that the proper tightening torque is always achieved, thanks to its integrated torque control. However, it does require specific drop-outs to take advantage of the special features that make it faster and more user-friendly. The list of compatible frames and forks is constantly growing and currently includes Cannondale, Look, Van Dessel, Lapierre, Stinner, Caminade, Victoire, Origine, Sunn, Votec, Moots, Argonaut and several more.
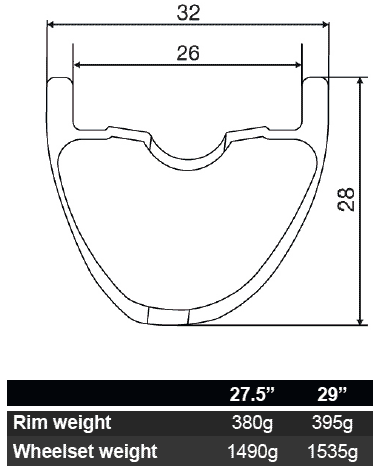
9. What are Mavic’s thoughts on hookless rims for road and cx wheels?
Mavic: We do offer hookless rims in our MTB range and Allroad / Gravel line. Those wheels are also great for CX. However, we don’t recommend hookless rims when the pressure will be higher than 4 bars / 58PSI. That makes hookless irrelevant for most road uses, with tires 28mm and below.
10. Why do Mavic Tubulars weigh so much?
Mavic: This is an interesting question! Mavic tubular tires weigh 240 grams, which is light compared to many others. The Ksyrium Pro Carbon SL Tubular (rim brake) comes in at 1190g. Not so bad, eh? The Cosmic Pro Carbon SL Tubular is indeed on the heavy side since it was designed to tackle the Paris-Roubaix cobbles (winning it in 2011 with Johan Vansummeren). The rim is reinforced for impact protection and ads a bit of weight. It a great option for rough roads and CX (disc brake version).
11. Why so many proprietary parts? Steve
Mavic: As mentioned, we are engineering and manufacturing “Wheel-Systems”. It means that in order to improve the balance between performance, weight, reliability and safety of our wheels, we are doing everything possible to optimize rims, spokes and hubs to better work with each other to achieve our goals. Sometimes, the un-proprietary parts available can’t get us there so … we develop our own parts to produce the best products. So, to be precise, the only proprietary parts are the spokes (and sometimes nipples when used with ISM) because there’s no such things as generic (un-proprietary) parts when it comes to hub internals or rims. DT, i9, Chris King, etc. … they all use proprietary internal parts.
12. Any word on Microspline compatibility? I have dirty gravel plans for my XA Pro Carbons… Celest
Mavic: Ah Celest … your adventures would surely make us jealous. We are working on Microspline but so far, Shimano has not been an easy partner to deal with in terms of offering the specifications needed to develop their system into our products. We will have the first freehub body ready to ship late April 2019. That said, it will only work with our new freewheel platform called ID360. So unfortunately, your XA Pro Carbon won’t be compatible. You could go XD? Or switch to a new pair of Mavic wheels, dedicated to gravel, with a carbon rim, that JUST might be available before the summer. =-)
Stay tuned for part 2 next Friday!
Got a question of your own that Mavic didn’t answer? Click here to use the AASQ form and submit your own question! If we get enough of them, Mavic could be back for part 3!