Ever wonder how all those marketing and braking performance claims from carbon wheel manufacturers would hold up if everyone were thrown into a giant test, all variables removed, and one winner could be announced?
Alto Cycling did, too. And they did something about it.
Partnering with Spark Wheelworks to create a test, because they wanted to know how much of what was being claimed would hold up in the lab. So, they called in rims from the following brands:
- Alto Cycling (CC52)
- Bontrager (Aelous 5 TLR D3)
- Boyd Cycling (60mm Clincher)
- ENVE (SES 4.5)
- FSE (EVO 55C)
- Knight (65 Clincher)
- Mavic (Cosmic Pro Carbon SLC)
- Roval (CLX 50)
- Zipp (404 Firecrest)
Then they designed the study to remove as many variables as possible. If you want to see the videos, skip to the bottom. If you care about how they designed the experiment and why some rim brands weren’t included, keep reading…
RIM SELECTION & PRE-PLANNING
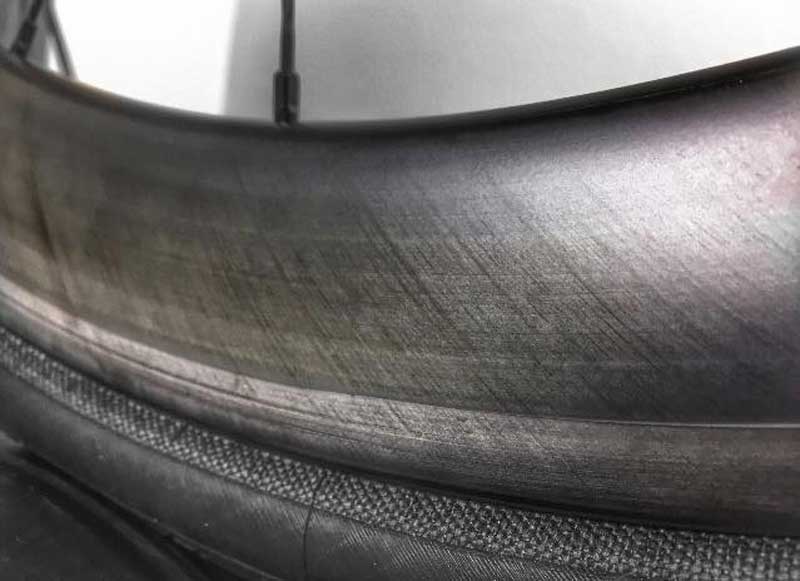
To be clear, this is a test dreamt up by Alto Cycling’s team and performed by Spark Wheelworks. Other than Alto providing their own wheelset for the test, all others were procured at wholesale by Spark as part of their sponsorship of the test.
Alto co-founder Bobby Sweeting says they wanted to include the best wheels, and they planned to publish the results regardless of who won and how their own rims performed. But they weren’t going into it blind. They’d tested prior generations of their rim brake carbon clinchers and new they could withstand a lot of heat. And then they made them better:
“We began processing different resins with different additives (which are now proprietary and will not be disclosed), and researching ways in which we could increase the onset temperature of the resin. Essentially, that is the point at which the resin begins to soften. We then decided to filament wind the brake track while infusing these additives, which gives the fibers much tighter compaction and allowed the resin to flow more evenly throughout the structure. In our first round of prototype testing we were failing tubes and rim strips (more on that later), but were never able to fail one of the new rims!”
I asked why Reynolds wasn’t included, and Sweeting says they reached out, but didn’t get a response in time for the experiment, and they weren’t available through Spark’s accounts. The other two that Sweeting says he really wanted to test against were Shimano and Campagnolo, but their budget didn’t allow for retail purchases of any wheels (hence Spark’s sponsorship support). He told us Campagnolo was willing to send their wheels on the condition that they be tested with Campagnolo pads, but as you’ll soon see, that would have introduced a variable that they couldn’t accept. Sweeting says they’d like to a second round to include more brands in the future, and they’re using the feedback from this first round to hear which brands all of you want to see tested. So, let ’em know in the comments.
TESTING PROTOCOL
New rims in hand, it was time to design the experiment so all brands would face the same test and results could be trusted. Here’s how they did it:
“We wanted to be absolutely sure that we were testing the heat capacity/dissipation of the rim, and not the tube, rim tape, etc. We didn’t want any premature failures other than the rim itself. In the prototype testing of our own rim we found two extremely interesting bits of information: a nylon rim strip would melt, and a small tube would fail pretty quickly! So the first thing we did was develop our new high temperature tubeless tape, which has a melting point of 915ºF. That solved that issue completely. For the tubes, we saw a massive difference when we switched to a 25-32c Continental tube, as opposed to their 18-25c option. Even though we were testing with 25mm tires, the wider rims allow that tire to have an actual width around 27mm. So the 18-25c tube was too small, and the wall of the tube was failing at sustained temperatures over 200ºF. So, as two side notes for customers to take away from this test: make sure you’re using quality rim tape and that you’re using the largest tube possible for your setup! Every rim in this test used our rim tape and the same sized Conti tube, of course.
“There are A HUNDRED ways that we could do this test, but we wanted to focus on eliminating as many variables as possible so that we could focus on the rim. That meant standardizing the brake pads, and using the same generic carbon pad on every rim. In this case, we used SwissStop Black Prince pads. Of course the times and temperatures will be different with brand specific pads, but we found that as long as the pads are the same across the entire test (regardless of what is used), the actual results of how brands compared with one another remained the same.
“We also decided to let the speed of the wheel be a floating variable, and to set the power input from the motor at 1200 watts. This way, the total energy into the rim would be constant, and the speed would simply be affected by whatever the rim manufacturer was doing to their brake track. We felt that this would be more accurate than controlling wheel speed and forcing the motor to do more work on some rims than others.”
The tires were inflated to 100psi. In addition to the heating and braking, they also tested how quickly the rims would return to 120ºF, which is a normal between-braking-efforts temp. Since few of us actually drag our brakes continuously for an entire descent, an important measure of performance is how quickly they can shed heat. The faster it cools, the more likely it is to make it to the bottom intact. When you’re watching the video below with the cooling times listed, keep in mind that in real world conditions you’d have a lot of airflow over the rim surface to aid in cooling, which would almost certainly reduce the times listed.
TEST VIDEO & THE AFTERMATH
The variation in results is dramatic, some definitely fared better than others. Here’s the “after” photos, as provided by Alto Cycling. In some, you’ll see some minor delamination, in others the resin softened enough to blow the sidewall apart. In both cases, failure ultimately happens because the resin softens to a point where the tire pressure is stronger than the resin’s ability to keep the structure intact. HOW the rim fails, as Sweeting explained it to us, depends on variables like onset temperature, fiber orientation and layup schedule, molding technique, etc.
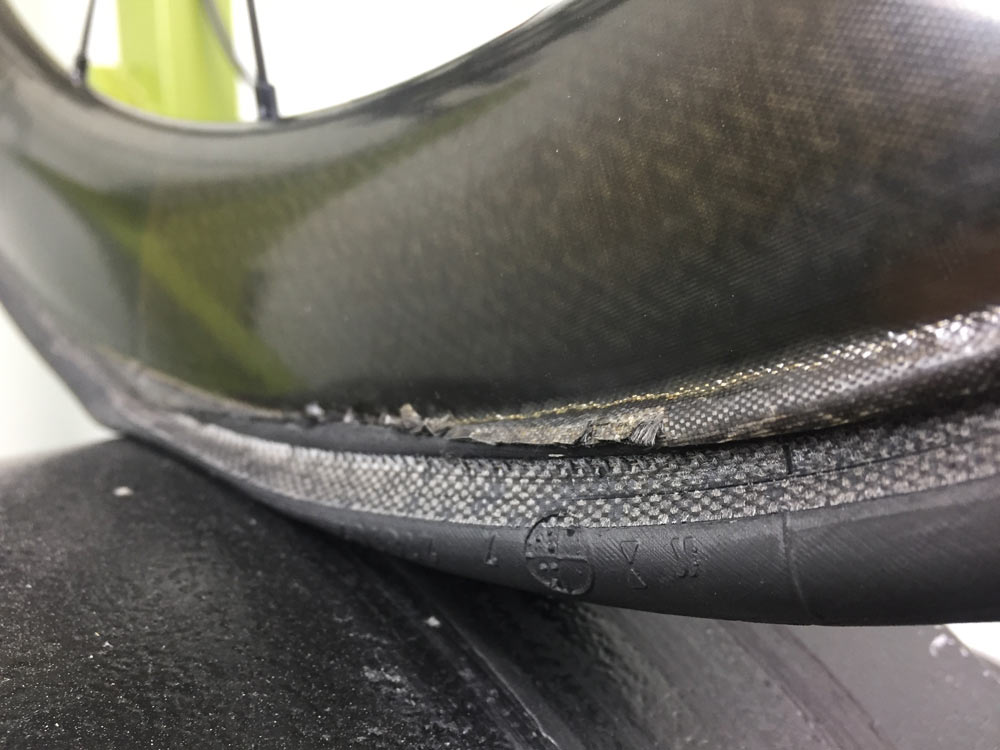
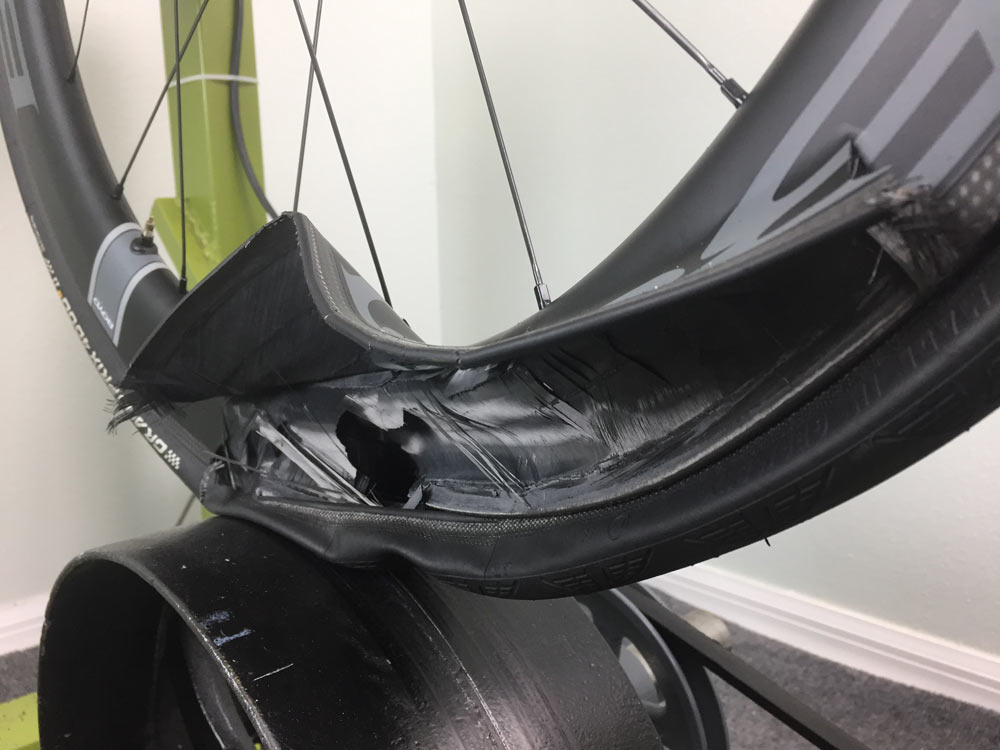
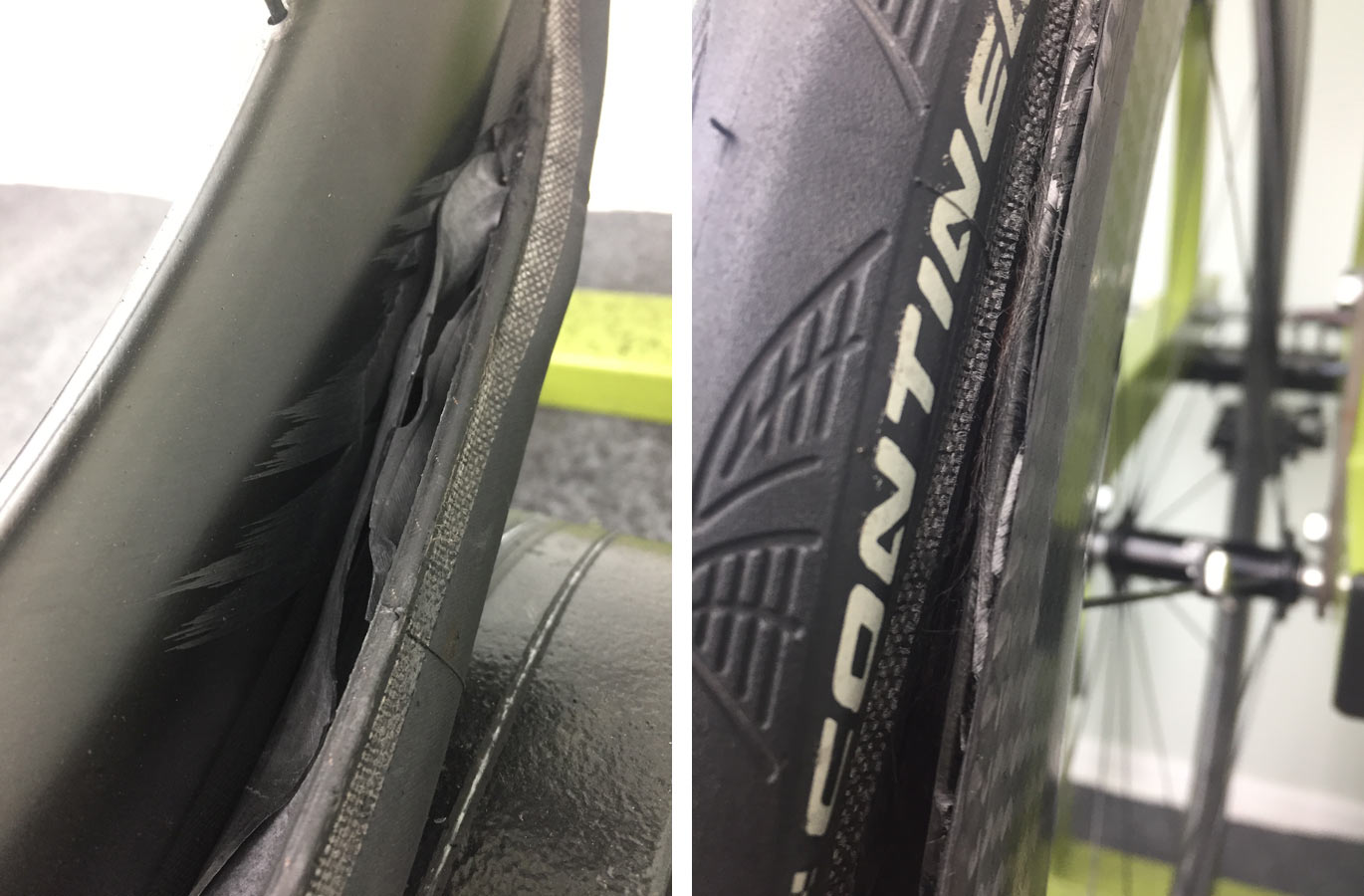
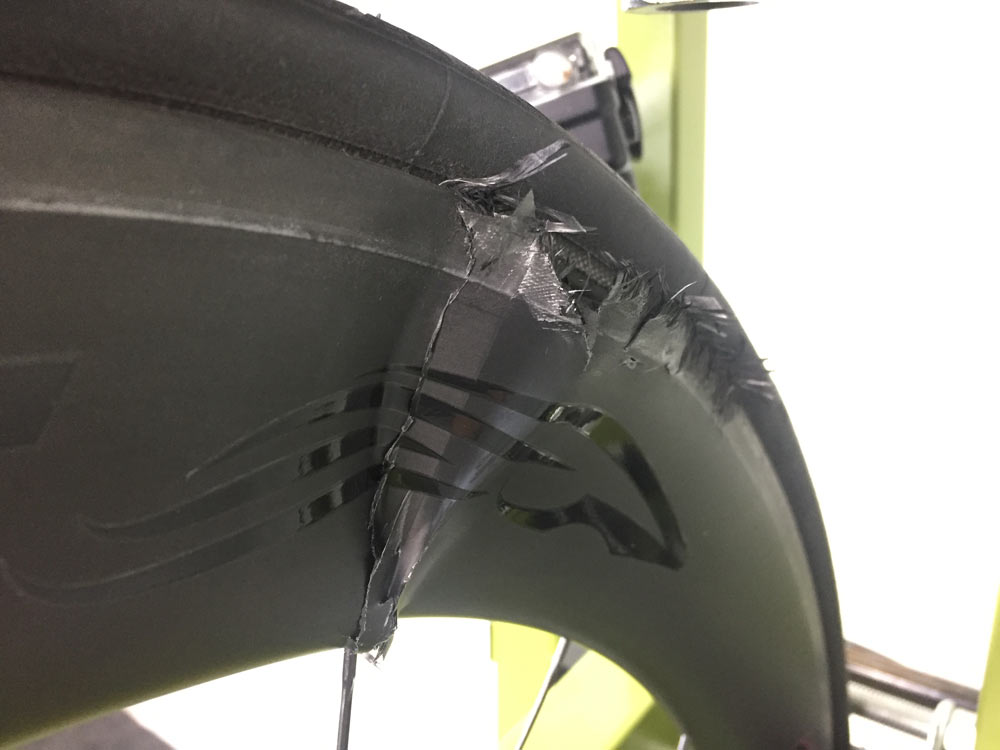
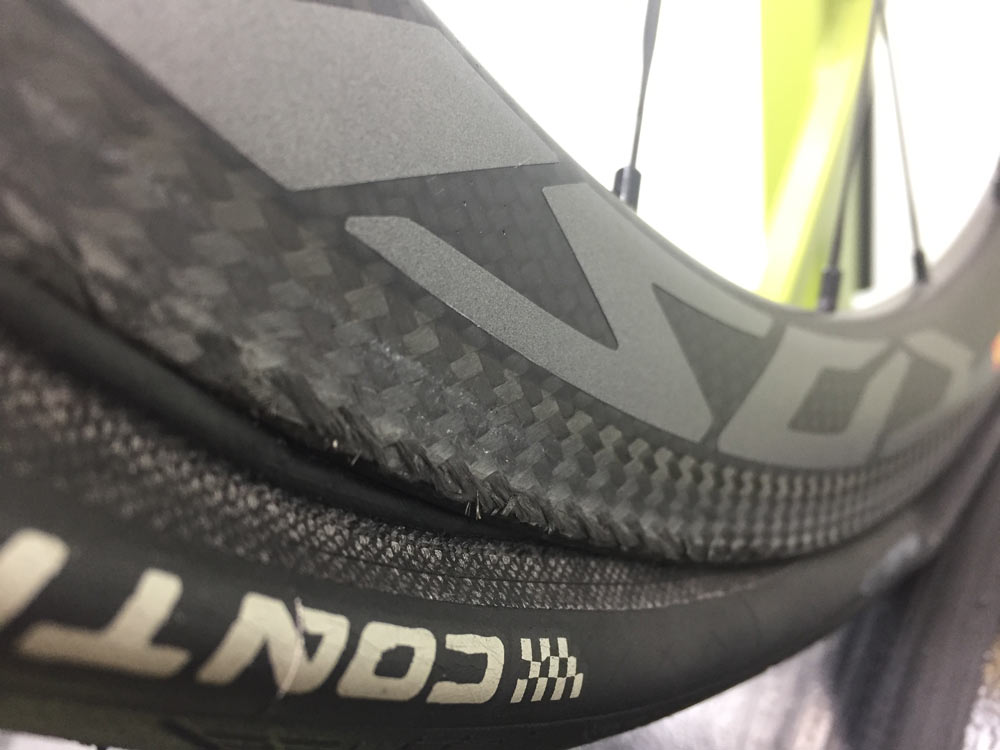
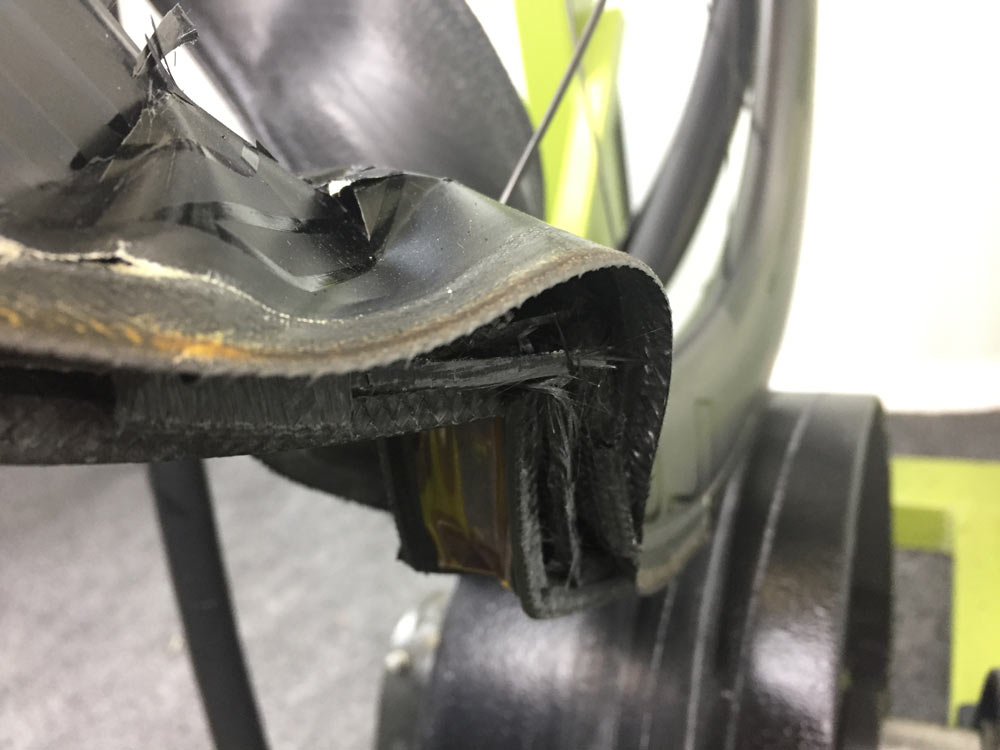
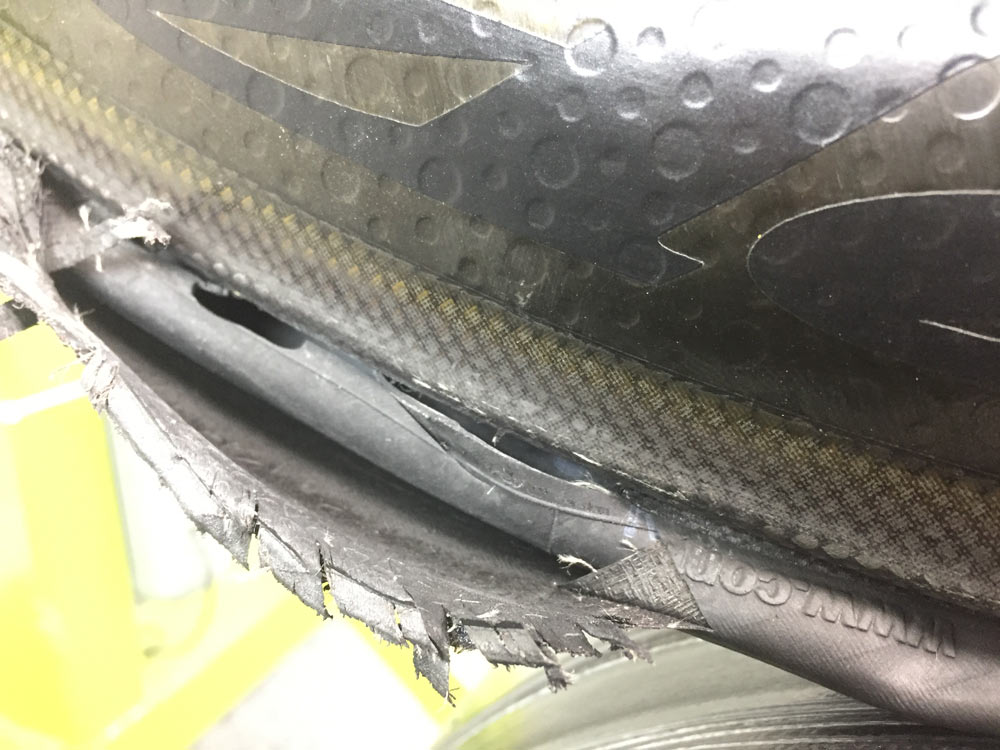
…and how did Alto fair? Here’s their rim after Phase 1, which used 7lbs of brake lever force for all of the rims tested:
After 20 minutes, it hadn’t failed and showed no signs of damage. So they increased the brake lever force to 9lbs and ran it again…
After another 20 minutes, there are initial signs of delamination, but the tire hadn’t popped yet. Full results are:
Does this prove who makes the best carbon clincher rim? No, but it’s a start. More brands will need to be tested, and we applaud Alto and Spark for putting all the information out there for us to see and process. Adding to the appeal for other brands to be involved, Sweeting added:
“I’d also like to be clear that this was simply one way to do this test in order to collect a specific type of data. We haven’t tested every rim with their brand specific pad, and we only tested one rim of each brand. So results in the field could vary, but we think this test is the first publication that gives a snapshot into the reality of carbon clincher heat transfer and braking performance. And we want to test as many brands as possible, or more rims from the brands that we’ve already included! So if any company feels left out or if anyone wants to be retested, please send them our way (or fly to Sarasota!) and we will do it all again. The more open and all-encompassing this can be, the better it is for the customer. At the end of the day, that’s what it’s all about. Please check out Spark Wheelworks and you can order any of the products we tested in any custom build that you choose!”
We’d add that, if you’ve switched to disc brakes, this test isn’t very applicable as all of the braking forces and heat are at the rotor. The main braking stresses applied to the rim in a disc brake set up are at the spoke holes, and we’re betting your wheel is more likely to lockup and skid the tire before you start ripping spokes out of the rim. It’s also worth pointing out that all of these wheel brands have been on the market for years and have solid reputations and that this test was intentionally a test to failure that, for many riders, may not replicate real world conditions. But it sure was cool.
So who’s Spark Wheelworks? Founded in October 2016 by Ryan Mason and Jonathan McKenzie, they’re a custom wheel building company out of Long Beach, CA, that picks and chooses from premium component brands to build wheels tailored specifically to the rider as well as pre-built wheels from curated parts.