At the beginning of 2015, Florida-based startup Alto Velo debuted their highly flanged hub design on some incredibly glassy internals. Called R-Symmetric, the design was built with complete wheels in mind since they designed and spec’d specific rim drilling angles and placement, and specific spoke tensions. The idea was to create wheel that balanced lateral stiffness with ride quality and rolled like it was on ice.
Then, at Interbike last year, they showed us prototypes of disc brake versions, with hopes to have them out early this year. That timeline came and went, but now, finally, they’re on sale.
“It was interesting, man. We had the 3D model at Interbike last year,” said co-founder Bobby Sweeting. “But we went back and forth on design and tolerances to really try to dial in on what people wanted most -the cyclocross people in particular- with an eye toward our mountain bike line that’s coming next year.”
Those design changes over the past year were done to ensure that their disc brake hub was good for anyone that needed a disc brake hub, regardless of discipline…
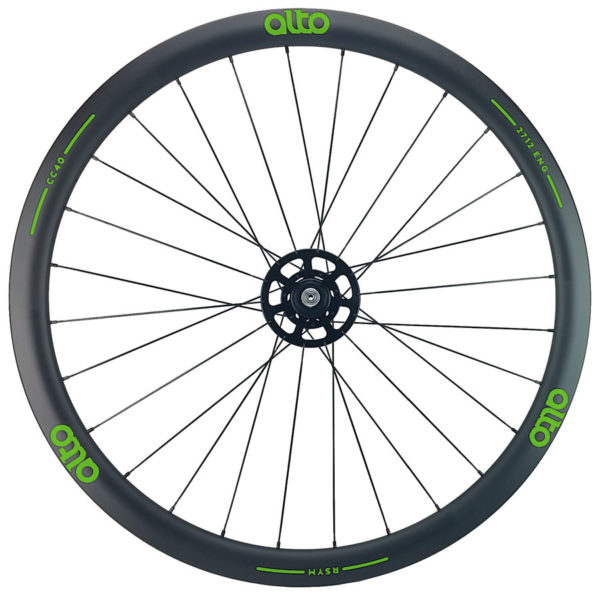
They kept their interchangeable axle design that lets you change out from QR to 12mm or 15mm thru axles in less than a minute. Each axle type does require a specific axle as opposed to end caps and spacers – it’s replacing one part with another single part, all of which are available separately. Check our original story for internal and tech photos.
The front hub uses the oversized flange on the non-drive side to make up for the offset required to make room for the disc brake rotor. Their testing showed that the widest offset and tallest flange isn’t necessarily the best solution because of what it does to spoke tension, and it’s doubly challenging to make a really good front disc brake wheel because there’s less width to play with. So, they did a lot of testing to balance ride quality with lateral stiffness at the right point. The result is an almost equal tension from left to right, which they say combines with their ultra-precise internals to make for a very smooth, balanced and strong wheel.
Internals are almost identical to their road hubs with the adjustable end cap, sealing system and freehub parts. The only key difference is a switch from 71802 bearing to a 71803 bearings on the front hub. Those are both angular contact bearings, the difference is going from a 15mm ID to a 17mm ID, which means you’re getting a larger, 17mm front axle inside the hub, which makes the hub stiffer and makes it compatible with all three front axle standards. That’s also why they went with 6-bolt rotor mounts rather than Centerlock, as it made it much easier to use their interchangeable axle design. That’s not to say you won’t eventually see a Centerlock option, but it’s likely a ways down the road.
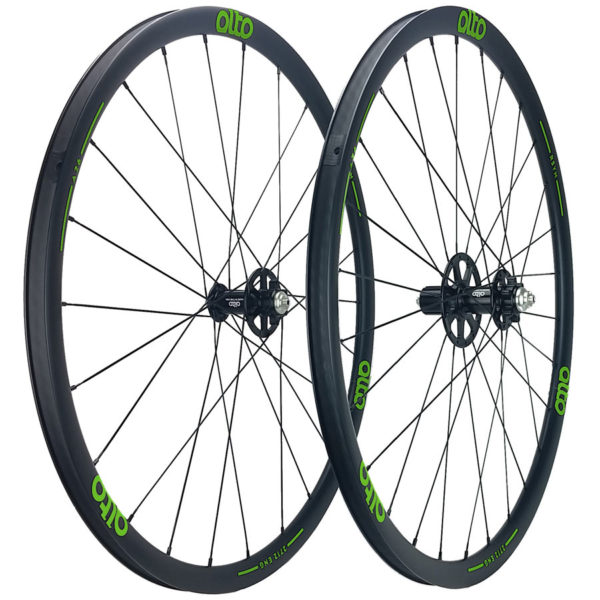
The rim also saw changes. Anytime we made changes to the hub, we had to change the rim, because the UD fibers in the carbon rim are all specific to the bracing angle of the spoke and the lacing pattern. So every time we made a change, we wanted to see it proven on the computer but also in real life. I think we went through four or five laminate structures. They’re very subtle, appearing almost inconsequential from a 10,000 foot view, but when you see the data from the testing, it was totally worth it to take our time and make sure that what you’re getting is exactly what you expect. In true engineering fashion, we overanalyzed everything until we were six months late. But just in time for ‘cross season…the following year.
The alloy rims are tubeless ready, and they’re made by Velocity in Jacksonville, FL (just up the road from Alto Velo’s HQ). It’s a custom drilled version of Velocity’s 26mm deep Aileron rims.

The carbon rims are made by one of the top Asian suppliers using Alto Velo’s own molds and design, which is necessary to work with their unique spoke angles. These are not officially tubeless ready yet (they’re working on it), but they’re using a new multi-angle drilling pattern to match both the bracing and lacing angles to have exactly linear placement of the spoke – there’s no bending tension or kinks in the spokes. That’s why they really strongly recommend buying a complete wheel from them rather than just the hubs for your own custom build.
Weights are lower than they expected, with all of the gram here, gram there trimming helping shave 50-60g of comparable hubs from competitors. The rear is 270g and front is 114g. Complete wheelset weights and specs are:
AX26 claimed weights are 707g front, 878g rear.
The carbon options weigh in at (claimed):
- CCX40 Clincher – 693g F / 873g R
- CTX40 Tubular – 591g F / 771g R
- CCX56 Clincher – 750g F / 926g R
- CTX56 Tubular – 598g F / 774g R
All are laced 24 front (2x/2x) and 28 rear (radial/2x). They’ve already shipped the first few sets, and they’re available now through their website. Demo sets will be at Interbike’s demo day, too. Retail ranges from $1,385 for alloy, carbon starts at $2,050 and runs up to $2,195 depending on rim depth. Choose from eight logo decal colors.