The latest onshoring move sees wheel brand Boyd Cycling adding rim rolling and sleeving equipment into their Greenville, South Carolina headquarters, and they’re using it to introduce new mountain bike and road bike wheels.
The move puts part of the manufacturing under their roof while still relying on suppliers to provide the rim-shaped extrusions to them, but all finishing work is done on site.

Boyd told us they bring in long strips of aluminum that are pre-extruded into the rim profiles they want, from both domestic and international manufacturing partners, and then their new machinery rolls them into shape.
Once cut, their budget-friendly Prologue wheels’ rim blanks are batch anodized before they’re rolled into shape. The Prologue’s rim profile didn’t change, but the process is a bit more efficient and eco-friendly. The flat extrusion saves shipping space, so more material can fit on the same truck, boat, or train. And they’re anodizing the extrusion prior to rolling them, which lets them do roughly 100 at a time, versus 16 when trying to fit round, finished rims into a vat of anodizing chemicals.
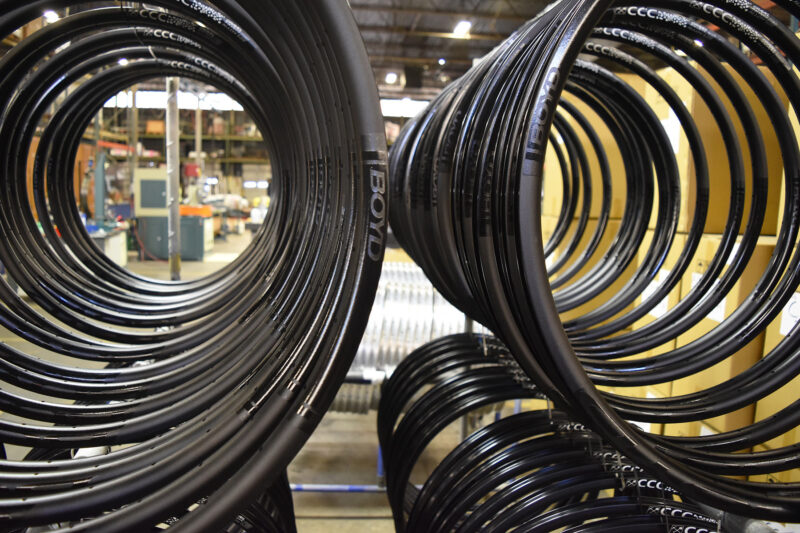
The higher end wheels are the revamped Altamonte road wheels and all-new Bracken MTB wheels are rolled first, then anodized. This results in a higher quality finish since the ano isn’t “stretched” as the rim is rolled, but means they can’t do as many at a time.
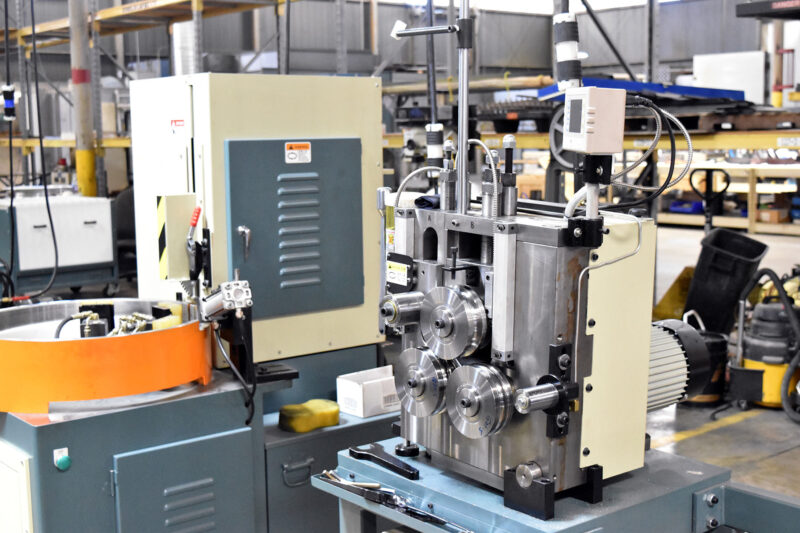
Sitting alongside their wheelbuilding equipment, the rim rolling machines arrived in Fall 2022. Working with the machine’s manufacturer, they brought in enough extruded alloy sections to make 500 of their Prologue GVL gravel rims and got to work. From that batch, they got 390 production-quality rims, having worked through the rolling process, cutting and drilling, sleeving and bonding, and other final finishing.

Part of the process was learning how to “not” make rims, how to properly heat them so the anodization doesn’t crack, and how to design the sleeves so they fit the finished rim once it’s been curved, which stretches and changes the shape of the blank extrusion.
Boyd sleeves them together, with an adhesive bonding it all together without pins. They say the benefit of sleeving over welding is that you don’t have to smooth the weld afterward, which can leave a bit of a flat spot that’s virtually impossible to get perfectly matched to shapely modern rims.
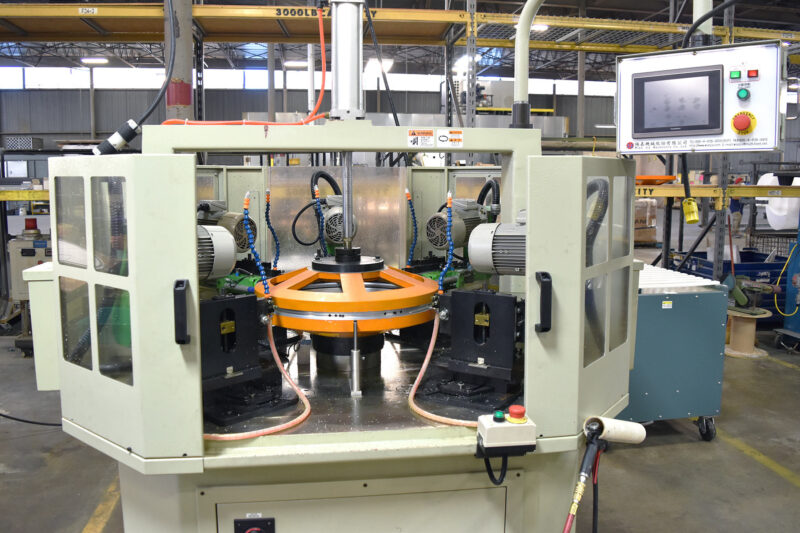
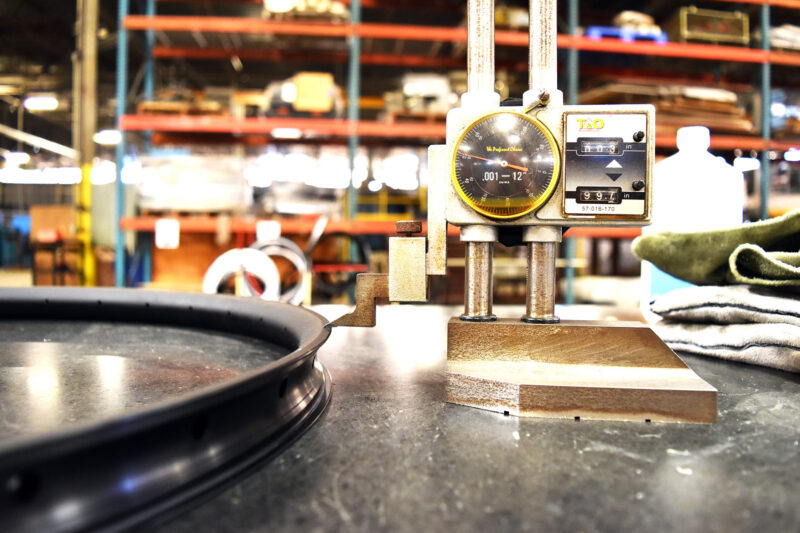
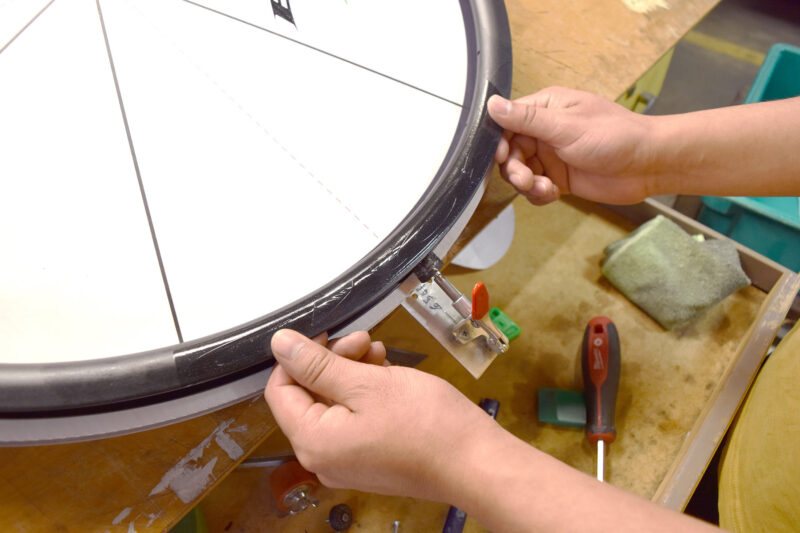
Lastly, they’re doing water transfer decals in house, too, which they say isn’t done anywhere else in the US.
Bringing the process in house gives them more control, and because of the efficiencies gained in shipping and production, they’re able to keep the US-made wheels the same price as before. The real benefit is that they have more control over their supply chain, which COVID proved could be a critical factor in a brand’s ability to thrive versus survive when things go sideways.
Boyd’s new US-made alloy wheels
The Prologue is their existing budget-friendly alloy wheelset, available in rim and disc brake versions, that come in at just $425 now for a US-made rim that’s built into a wheel in house in Greenville, SC.
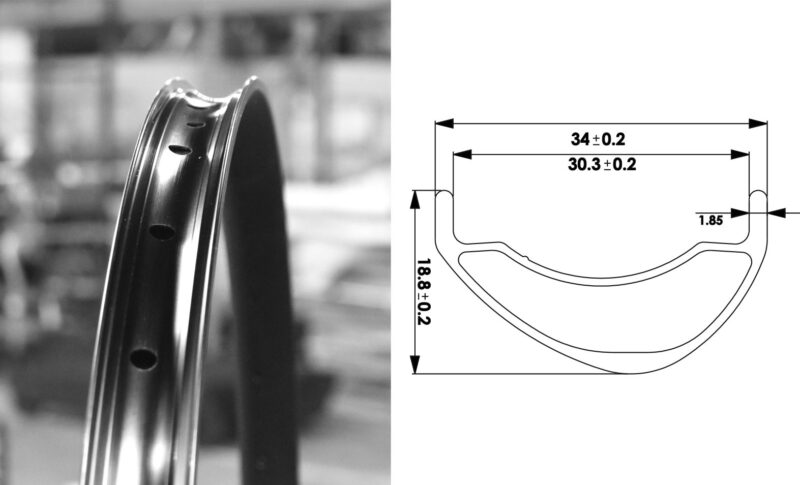
The new Bracken mountain bike rim is a new wide, shallow rim with thick hookless sidewalls aimed at the enduro crowd. Optimized for 2.4″ and larger tires, it has a 5mm offset spoke bed to help even out spoke tension. Rim weight is 485g, and 29er wheelsets come in at a claimed 1,850g for the set built on their Tripel MTB hubs with Pillar Wing 21 spokes (laced 32 spokes front and rear).
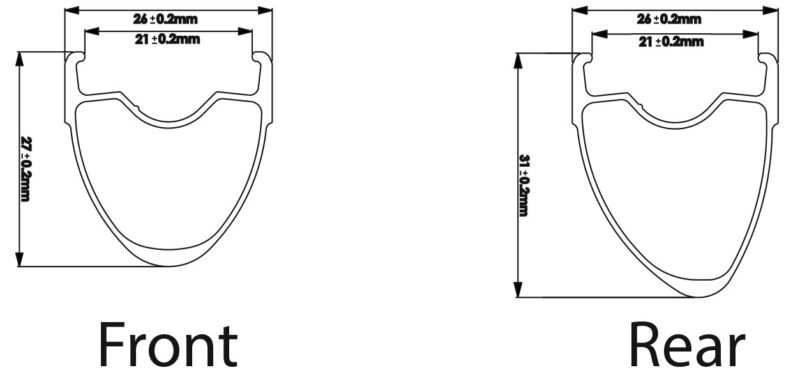
Boyd’s Altamont Rim Brake wheels provide a quality option for the holdouts, and now these rims are made in house, too. They feature front- and rear-specific profiles can can be built with 24, 28, or 32 spokes. Claimed weight for a 24/28 combo build is 1,620g.
Boyd says they will open up the rim manufacturing for third parties, too. They’ll take a client’s rim design and manage the extrusion, manufacturing, and rim rolling and finishing for them. This opens up more options for domestic brands who want to on-shore production and sourcing to better deal with supply chain issues and rising transportation costs.