Admittedly, most cyclists’ thoughts probably turn to inexpensive forks when you mention SR Suntour, and that’s a shame. It’s not that SR Suntour doesn’t produce these forks. They do. And in large quantities. The truth of the matter lies in the fact that the company has a long history of technical innovations in the bike industry that just happen to allow them to produce that suspension fork you’ll find on a bike under $500 and make it affordable while still working exceptionally well for the price. That, and a vertically integrated company that allows them an economy of scale. As the continuation of SunTour which started as Maeda Iron Works in 1912, SunTour is responsible for bringing us technologies we still use today, like the slant parallelogram rear derailleur.
In 1988 when the Japanese founded company moved to Chang Hua City in Taiwan, Suntour brought with them a new casting technology based on the melt-forging process. They called it Accurad forging (AC4C) and it involved injecting molten metal at high pressures into molds. Sharing a lot of similarities with casting, Accurad forging meant that the finished product was free of air bubbles or inclusions which can plague standard gravity casting. Combining the benefits of forging and casting, the process allowed for complex parts to be produced much more cheaply, giving rise to affordable components. Low end components aren’t as sexy as many of the forks you see splashed across our pages, but when you’re talking about producing something in the millions of units rather than the thousands, it takes some serious manufacturing skills to ensure repeatability at that scale.
However, SR Suntour isn’t about inexpensive parts, rather value and performance at any point in their line. The company’s Taiwan headquarters and factory is actually geared towards production of their higher end products – basically Taiwan produces forks with magnesium lowers and China makes forks with aluminum lowers. While the Chang Hua factory is capable of producing up to 5,000 complete suspension forks in a single day, their factory in Shenzen, China handles their higher quantity goods and is capable of making up to a whopping 20,000 forks in a single day. As you can imagine it takes a lot of people to keep a facility that size moving so you’ll find around 500 employees in Taiwan and around 900 at Shenzen. On top of that SR Suntour has a third facility in Kunshan, China that employs another 400-500 people. All together SR Suntour produces around 10,000,000 suspension forks per year with their Taiwanese facility running 8 hours a day, and usually two shifts in China. Together that makes them the biggest fork producer in the IBD market.
Earlier this year we found ourselves in the Fu Hsing Industrial Zone where SR Suntour Taiwan calls home. Take a look around the factory next…
Situated in the middle of a bustling street in a modern industrial district, SR Suntour finds a home among a row of palm and well manicured trees.
The oldest building on the campus now serves as the office space for the accounting and purchasing departments as well as meeting rooms and dormitories upstairs.
The facility is a cacophony of manufacturing. Loud crashes intermingle with the nearly constant drone of forklifts and trucks dotted with the warning beeps of heavy equipment in reverse. To produce 5,000 forks a day, you have to move. The facility in Shenzen must be deafening.
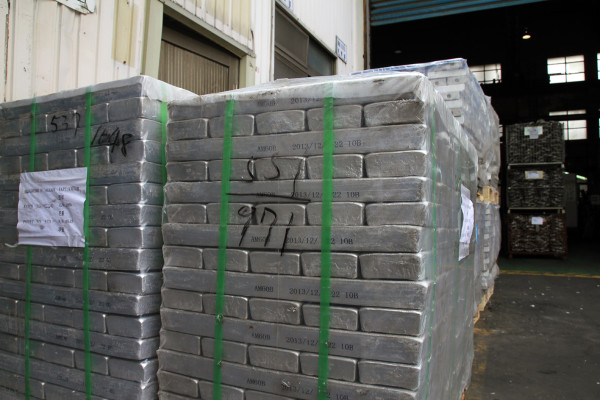
Raw ingots of magnesium alloy await their turn at becoming fork lowers. Before going any further we should point out the obvious – SR Suntour is very protective of the proprietary technologies involved in their casting process so there was quite a bit of the facility that we weren’t allowed to photograph.
Over the years more and more casting machines have been added to the facility as production has ramped up and their technology has improved. Ingots are melted down in special tanks that allow for the proper blending of alloys then are injected into molds with high pressure in specialized casting machines that clamp down on the dies with hundreds of tons of pressure.
Just being in the casting room is an experience in itself. Between the heat radiating off the molten metal and the steady percussion of the casting itself, suddenly I felt as if I was an extra in the Temple of Doom.
The whole melt-forging process is very efficient but still leaves cast parts with excess material. After the large pieces have been removed, and things like disc brake mounting holes are machined, parts are individually inspected and hand filed or sanded as needed before the head out for finishing. In the whole process, only the polishing, plating, and painting is done elsewhere. In addition to suspension forks, the Chang Hua facility also produces cranksets among other parts.
SR Suntour is also working on a full cabon fiber production facility on site that will continue making products like carbon fork lower, and cranksets.
Meanwhile other suspension parts are turned out to all the finished fork lowers and crowns for assembly. Like many of the factories we have seen, large bays of CNC machinery work to turn bar stock into end caps.
In other parts of the factory rolled steel is stamped into chainrings as it travels through an automated machine.
Finished parts gather before assembly including giant drums of suspension oil. One of the newer technologies that SR Suntour is quite proud of is their QSP or Quick Service Product cartridge design. Instead of waiting around for a complicated and expensive damping cartridge rebuild, all of their QSP forks use a sealed cartridge design that is designed to be completely replaced if it needs repair.
On the 2nd floor of the casting building, the finished parts are assembled into complete forks. Cellular manufacturing methods use small groups of employees to assemble a certain model in one are of the factory.
Step through into the quality control area of the factory and it gets impressively quiet. Among a host of manufacturing acronyms, SR Suntour also uses the ERP or Enterprise Resource Planning program to streamline production. Additionally as with any quality manufacturer, the parts go through rigorous QC checks and batch testing before they leave the factory.
Up another floor and there is more assembly, but this time for parts like rear shocks and suspension seat posts.
Among the other products produced in Taiwan? E-bike parts and gear boxes. SR Suntour actually produces quite a few e-bike sensors, motors, and batteries but mostly for the European and Japanese markets. Speaking with SR Suntour, it seemed that the company feels e-bikes will really take off in the next few years in the United States but currently most companies seem to want more power than SR Suntour thinks is necessary. To SR, e-bikes should be more about range than fast, 500w plus motors. Keeping in mind that the average cyclist is typically capable of 100-150w, adding an additional 250w motor nets around 400w total. And with that power level the SR Suntour e-bikes are capable of up to 110km in a single charge.
Often, cyclists are quick to dismiss e-bikes as tools for the lazy, but in countries where driving is not an option, e-bikes can provide an effective alternative to scooters or motorcycles. Since many countries limit e-bike speeds to 25 km/h they maintain larger motors aren’t needed.
Since the e-bike components are made on site, they have also had to develop testing equipment which is all custom built.
Without diving deep into the tech of their e-Bike platforms, SR Suntour currently offers front or rear hub motors using their HESC Twin Sensor technology.