Michael Moureček, the co-founder of Czech premium custom bike maker Festka puts into words what we’ve all been experiencing… an ongoing global coronavirus pandemic that has harshly impacted the lives of almost everyone in the world. Yet in the end, the cycling industry seems to be reaping great benefits from a boom in interest.
But there remains tons of uncertainty, from how bike companies big & small will come out the other side, to how the small & giant component makers will adapt, to when things will get back to normal? Will it be one year, two… or four or more?
Festka’s bittersweet view of the coronavirus crisis & bicycle boom
While we’ve been talking about adaptation in the industry, highlighting the demand boom, and significant supply chain shortages for over a year, Festka offers a different insider perspective. Combining what seems to be long-term growth of the general bike market across all pricing levels, Michael shares what this all looks like from Festka’s point-of-view, and with their own high-end, custom bike clients’ exacting demands.
So with that, we’ll just pass it off directly to Michael Moureček & Festka’s editorial unedited below… simply illustrated by photos from covering their craftsmanship in recent years…
(Full Disclosure: I happily ride my own personal all-road Festka that I bought years ago. You’ve seen it testing the likes of Campy Bora Ultra WTO, Super Record, H11 Chorus, Rapha saddles, QuadLock, among many other new products…)
Cycling a bittersweet winner of the coronavirus crisis
an editorial by Michael Moureček, co-founder of Festka
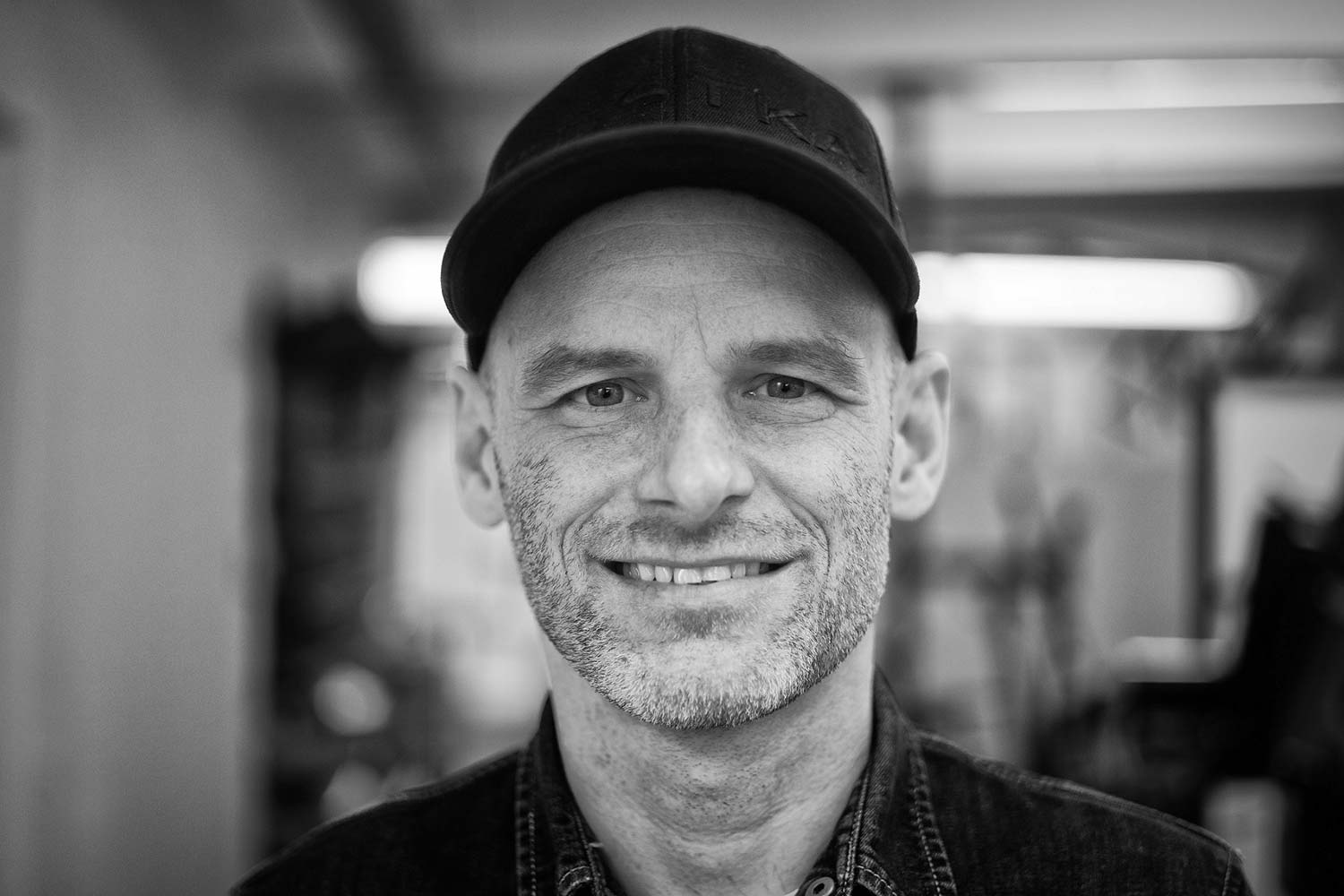
“The cycling industry is probably going through its biggest change since the invention of the bike. For now though, you have to wait to get a new bike longer than you would a new car.”
The coronavirus pandemic has accelerated the long-term growth of the bicycle market. As a result, bicycles, components and accessories have become scarce as the current boom reveals some weaknesses in the way the industry supply chain works. This will most likely have serious consequences for some manufacturers and sellers of bicycles or bicycle repair shops. So, what happened and what is in store for us?
Lack of components
As a result of the pandemic, supply chains in the bicycle and bicycle components industry have been severely disrupted. “Forecasts and B2B orders for components are usually made and placed three years in advance. Of course, in 2018 no one could have guessed what would happen between 2019-2021. When most large companies and distributors reviewed their orders last spring, they were afraid of further developments due to the pandemic and they cut orders for components whenever they could,” explains Michael Moureček, co-founder of Festka, a composite road bike frame producer. In the US, many companies in the cycling industry even laid off employees. Now, they are unable to get those employees back so they can ramp up production to respond to growing demand.
Cycling is an extremely globalized industry. Let’s take wheels as an example: carbon rims are produced in China where production was disrupted in the spring of 2019. As soon as China got going again, the pandemic had reached Portugal where wheel hubs are made. It then spread to Belgium where the wire production is concentrated and then on to the Czech Republic where wheels are built. This is what the situation looks like around the world: one type of bicycle component is made from various raw materials found in different parts of the world where mining and processing had been disrupted at various times during the first wave of the pandemic. When these materials are not all available at once, the entire supply chain breaks down and huge delays occur.
Many manufacturers are currently experiencing a lack of production materials. For example, wax, which is necessary for the manufacture of some high-end handlebars, is nowadays extremely hard to find. Another important ingredient that is lacking is acetone needed for the production of paints. “We can’t get wheel hubs. It is not that our German partner cannot produce them, but there is currently not enough high-quality aluminium on the market,” explains Moureček. The pandemic has caused a lot of micro-crises and shortcomings, which are now further linked and interconnected, causing longer and longer delivery times. For example, the lead time for carbon composite forks has grown from a couple of months to a couple of years!
It is not only production that is affected by all this. The pandemic is also causing delays in R&D. This has certainly been the case at Festka. “Because of this, we were unable to complete the planned launch of two new frame models, as we are not independent here. The lab that issues the ISO tests is currently closed due to covid. Specialists who normally do the complex calculations needed in R&D often have to give their production colleagues a hand while their own daily tasks have to wait,” explains Michael Moureček about the delay. “All these delays piling up mean that the bike model we wanted to launch in December 2020 has not yet been completed. Based on how things are going now, we’ll be lucky if the final delay is less than a year,” he adds.
“The biggest challenge and unknown is that it is impossible to predict what might still happen, what will still be missing, what items will become more expensive in the coming months and what will affect our business,” says Moureček. “Our production capacity has actually not changed much. Our key product is a carbon composite bicycle frame and that is something we can make pretty much on our own using locally produced composite tubes. Even so, we had to extend our usual three-month lead time to six months but that is caused in part by a huge spike in demand. Still we can cope; we are a small, yet very flexible, company,” he adds.
Even a frame manufacturer such as Festka needs some subcontracting support to be able to put together the most basic form of its product – a frameset. Many customers prefer to buy framesets only and then get them built into full bikes by a trusted mechanic. Frame manufacturers typically do not make forks and they rely on those being supplied by specialists. “For example, at the beginning of April, one of our American component suppliers extended delivery times from five weeks to five months. They recently added another five months to that. So their lead time is close to a year now, and we have several dozen bikes on order that we cannot finish without forks,” says Michael Moureček.
It’s not just about new bikes
Those lucky individuals who do not need to buy a new bike will also soon encounter problems caused by the pandemic. Bike shops will simply not have spare parts needed for repairs and maintenance. “This is a topic that is not so visible, or talked about, at the moment because reports concentrate on new bike sales,” says Moureček. “One of our clients who recently bought a bike happened to damage his derailleur in a minor accident. He came to us at Festka asking if we could help him. We then had to tell him: Yes, of course, but you are in for a fourteen-month wait. It’s unbelievable!”
The components necessary for the most basic bike servicing but which are currently most scarce on the market include brake pads and chains. “We would normally buy chains by the hundreds, but this is not possible anymore. Neither directly from manufacturers nor in their e-shops because you can now only buy one piece of any given component per day,” says Michael Moureček. For large bike shops or bike service stations, one hundred chains equals roughly a week’s supply. If these repair shops can only buy seven chains a week, they cannot do their most basic job. Stretched, worn chains gradually wear down more expensive components such as chainrings and cassettes.
Covid and the revolution in cycling
Covid will certainly bring a fundamental change to the relationship between people and their bicycles. Sales of children’s bicycles in the US are growing by hundreds of per cents. Interest in kids’ bikes is also growing dramatically worldwide.
“I believe that many of those children will remain true to cycling and carry this hobby with them into adulthood. Cycling may be facing its biggest change since the invention of the safety bike. This is something we are really looking forward to and which we would like to be a part of. The opportunities are huge,” estimates Festka’s co-founder. “I hope that people will also start to give more thought to their bike buying,” he adds.
Twenty, thirty years ago, when you decided to buy a bike, you thought about it for a long time. Once you made up your mind about what to buy, you had a three-month wait because someone had to manufacture the bike or at least import it. You did not expect your purchase to be available for pick-up, let alone direct-to-door delivery, within twenty-four hours.
It was very much like buying a car. In the last twenty years, however, mainly due to the rise of e-commerce, most companies have developed systems that enable them to offer next-day delivery. The system worked fine as long as the gears in the production and supply chain functioned as a well-oiled machine.
“Our advantage is that we are smaller and therefore more flexible. We don’t print catalogues; we don’t have to plan everything years in advance. So, we can replace the originally selected fork that’s become unavailable with another one that we can get on the market. Thanks to this, we are still able to sell bicycles; however, our lead time has grown,” describes Moureček.
“Unfortunately, we are currently unable to do something that we would normally love doing: satisfying our customers’ every whim as regards virtually unlimited sourcing and supply of components for the fully built bikes that many of them like to order from us.”
“In the current situation we have to be very creative and flexible which is a big challenge; especially for our customer service personnel. We have cases where the whole bike is ready except for the saddle the customer selected. In such cases, we try to agree on a temporary solution,” says Moureček.
But such a model cannot work for large companies whose customers expect to get exactly what they see online or in the catalogue. That, however, is what these companies taught them to expect. “I believe that the repercussions from our current problems will still be felt within our industry in three, or even four, years,” he estimates.
The current situation has also significantly disrupted the development of standards in the cycling industry. Let’s take gears. For many decades now, bicycle gear systems, known as groupsets, have grown by an extra sprocket every ten years.
“Now is the time when 11-speed sets are being replaced by 12-speed ones. However, due to delays in deliveries, it is no longer worthwhile to order the older standard with a lead time of fourteen months. In a year’s time, no one will want to buy an 11-speed groupset. Currently, however, we also cannot get 12-speed sets without waiting fourteen months. This means not only can we not finish bikes for our customers, but we also complete bikes for ourselves to photograph, film and send to specialist media for testing,” says Michael Moureček.
Everyone in the cycling ecosystem is affected in some way by the coronavirus crisis. Of course, not as fatally as in industries such as hospitality or tourism. “The inability to travel and meet our customers in person affects us as well,” says Moureček.
“So does the fact that we can’t travel to attractive places to take photos and make videos for marketing purposes. Cycling iconography demands we film in certain places that are simply not available in our homeland.”
Prices
All the situations described above are inevitably going to cause an increase in prices. “Luckily, in terms of the materials we use in our production process we haven’t seen any major price changes yet. The only exception is transport where the jump in prices has been dramatic,” explains Moureček, adding:
“Transport costs can amount to up to 25% of the total cost for a bicycle made by Festka. The cost of air freight to some destinations has doubled and sea freight has gone up manyfold. The biggest increase in the price of bicycles will certainly occur at the cheaper end of the price spectrum. In our case, it will probably not be so significant because we have most of the production process well under our control locally. Even if the raw carbon fibre our Czech tube producer imports from abroad goes up in price or the cost of bringing it here increases, the impact on the final price of a Festka bike frame will not be significant.”
Return of bicycle production to Europe and smaller manufacturers
Michael Moureček believes that many companies are already rethinking the set-up of their supply and production chains. “I see smaller and smaller companies beginning the process of becoming less dependent on China and other countries outside Europe. Many firms will try to create some backup alternative in Europe. It is clear that Europe-based manufacturers have been less impacted by the pandemic. The business that is closer to the factory that produces what they need wins.”
“One of our suppliers is a large distributor who represents various brands. You can tell from the availability of products in their portfolio who produces where. Manufacturers based in Europe are doing much better than those that had moved their production to China, India and elsewhere in Asia,” explains Moureček, adding that this may also be a new opportunity for European companies and manufacturers. “There are still enough companies in Europe that produce some components for bicycles, cycling shoes, etc. They make great stuff but they cannot afford to invest as much money into marketing as the global giants do. I think the current situation presents a major opportunity for them.”
One such manufacturer is the Spanish brand Rotor which produces groupsets on its home turf. Groupsets consist of front and rear derailleurs, crank sets, chainrings, brakes and cassettes; that is, the most important components you need to turn a frame into a bicycle. The giant Shimano is a world leader in this field. “Shimano has been hit very hard by the global crisis, while Rotor is doing relatively fine. Their lead times have extended but they are still reasonable. This means that we will spend more money on their products this year than for the whole period that we have been in business, because they provide a viable alternative for our customers,” describes Michael Moureček.
Again, reaching more people and serving them well, may give that company a huge boost. “Consumers will find out that the products are excellent, and many will remain loyal to them in the future. This is how smaller producers can benefit from the current stalemate,” estimates Moureček, but at the same time he adds: “Unfortunately, the risk for them is that they may suffer the impact of a lack of raw materials as their production stands and falls with the availability of high-quality aluminium.”
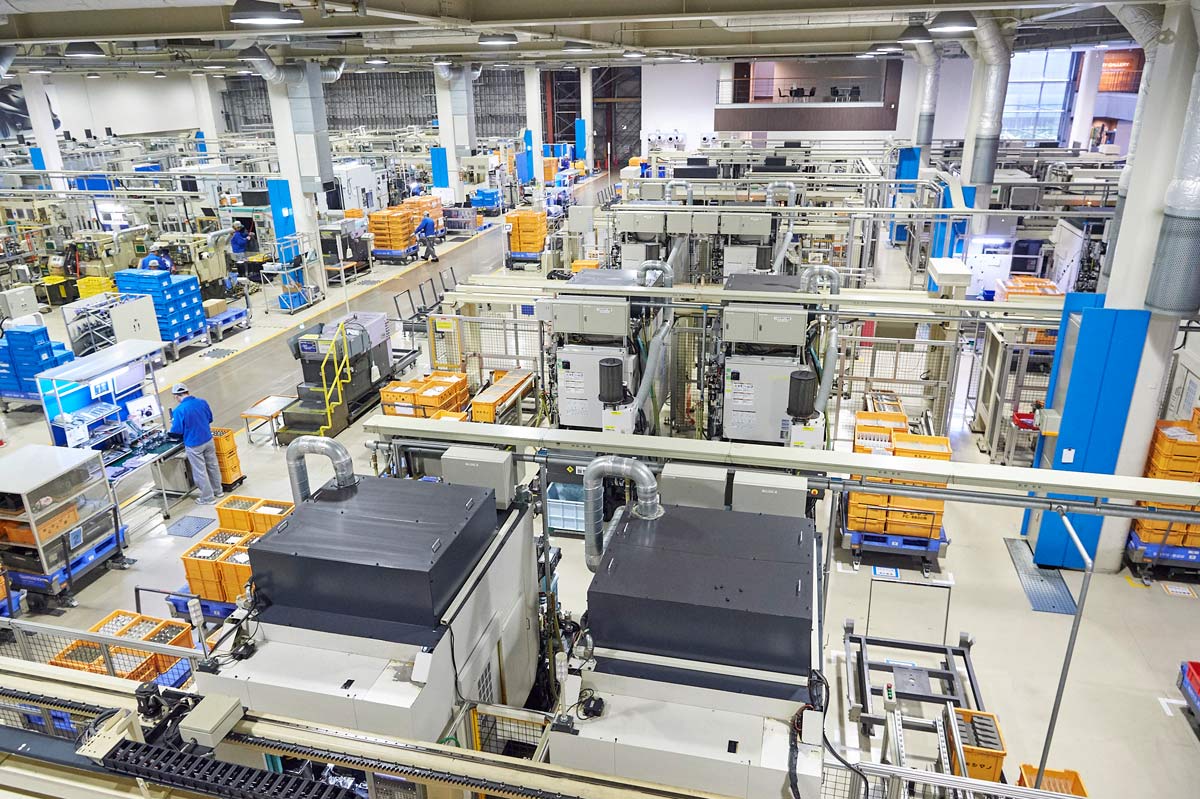
Parallels with other affected industries
There are only a handful of companies in the world that make chips. In the cycling industry, the all-important groupset manufacture is dominated by Japan’s Shimano and the US producer SRAM. If these companies are in trouble, the whole industry is in trouble and the bike market goes to pot. When the situation with these large manufacturers stabilises, they will surely prioritise the biggest bicycle manufacturers. Both SRAM and Shimano have most of their production in Asia, but they also operate factories all over the world.
One of Shimano’s production sites is even based here in the Czech Republic while SRAM makes some components in Portugal. “We’re lucky in that the high-end Shimano components we fit on our frames are manufactured in Japan, where production has not been so heavily affected by the coronavirus crisis,” says Moureček. Another important producer of groupsets is the Italian brand Campagnolo, which operates factories in Italy and Romania. “Theoretically, they too could be one of the winners of this crisis.”
So those who produce in-house, and do not have production concentrated solely in China or scattered around the world, have the upper hand now. Small independent producers who survive this difficult period can profit from the current crisis. It would be a mistake to think that manufacturers can go it completely alone and show everybody. The companies that make up the cycling industry are interdependent, even if they do not wish to admit it. In this respect, the sector is perhaps a little different from the automotive industry where companies tend to own the producers of vital components such as lights for instance.
That gives those businesses a greater opportunity to manage crises. “In our industry, both small companies like us and the giants like Trek or Specialized are – to a great extent – in the same boat, because of our dependence on the big component manufacturers. Today we are all more or less looking into a crystal ball trying to figure out what awaits us in the next three to four years. I believe that people’s interest in cycling will continue to grow and that our industry has a new golden age in store for it,” concludes Michael Moureček.