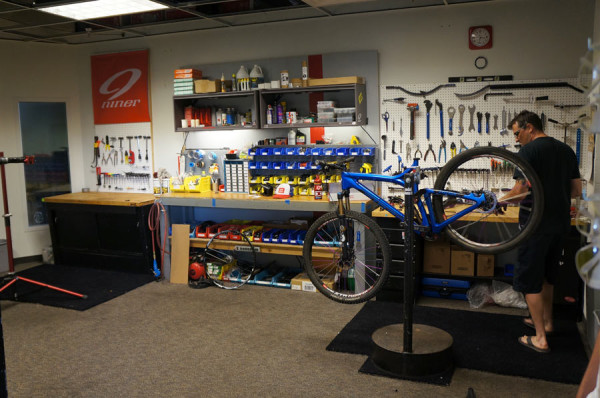
As a company, Niner’s somewhat spread out around the U.S. Some accounting is done offsite, assembly and shipping of complete bikes for resale is in California, and their president resides in Las Vegas. But the main office is in Fort Collins, CO, and that’s where the day to day magic happens.
Product development, testing, demo bike programs and marketing all come together there to keep the brand steadily humming along from scrappy startup with crazy big wheels to mid sized player in a global market.
We swung by Niner HQ on one of our summer trips and, after a delicious burrito at the neighboring Mexican restaurant, took a tour of the facility. Here’s your look inside…
The exterior is intentionally nondescript since there’s no real showroom or rider-oriented features, and the lack of signage keeps passersby from swinging in for impromptu tours. Walk in and you’ll find a few customer service desks just before the two-story conference room slash sales office.
Off to the side is the requisite ping pong table and frame display wall.
In the back is the kitchen and bar area, complete with everything you’d need to cook a real meal…for the whole office.
More importantly, there’s the beer fridge, which is serviced by none other than New Belgium’s own brewmaster, who ensures the CO2 levels are correct for whatever’s on tap:
Word is the fridge has seen several more RDO upgrades since our visit.
The kitchen area opens out onto the deck, where there’s plenty of seating and views of the Rockies. Below it is the testing center and demo bike build room, but we’ll get to that later.
First, we head back inside to see the engineering department.
George Parry, who came to Niner from Cannondale Sports Group in 2010, is the engineering and production manager. They use SolidWorks for 3D modeling and design work, but first the bikes start life as ideas, prioritizing function over form. They have their patented CVA suspension platform to build on there. But it has to look good, too.
Studio West provides industrial design work on some of the frames, most recently with the new RIP9 RDO. That gives them a look and a starting point.
All that’s then done up as line drawings with target geometries and sizing, starting with the front triangle, then the rear, usually starting with the medium frame size. These let them play with the axle path, linkage and pivot placement and shock ratio. Once it’s dialed, it moves into the 3D software to create the actual tube shapes based around the desired strength, stiffness and aesthetics. They have FEA packages for both programs and do that development and testing in house.
Full size rapid prototype frames are 3D printed to check for actual clearances.
For alloy bikes, their factory will make rideable prototypes. Niner’s so confident in their designs that typically by the time they’re ready to build test mules, they’ve already committed to the hydroformed or airformed molds and are testing near-production level frames.
The carbon frames are usually going off similar alloy models, which has generally proven the geometry, but it’s still a big commitment to open tooling at about $10,000 per frame size. Once the molds are made, they’ll test their layup schedules with the factory that’s actually making the bikes and work with them to finalize the carbon build process. These prototypes won’t leave the building until they pass lab testing. George says typically they’ll go through three or four lab samples, which can take a couple weeks, before they’ll send one back to Colorado for ride testing. That testing double checks for clearance issues, bearing life and other things as they’re pushed through three or four months of several frames under multiple riders. Early prototypes might start with three to five ride samples, and as they get closer to production, they could have up to 10 samples that are being ridden hard and also used for photo shoots. At this point, all the little stuff like cable routing and paint issues have likely been put to bed and the early test bikes are double checked for any long term surprises.
In addition to the ride testing, samples (and production frames) are run through their testing apparatus. Shown above with a RIP9 RDO, “Betty” is used to test all the frames, and there’s a duplicate jig at their factory in Taiwan.
It can test the influence of pedal loads, rear triangle / headtube / full frame stiffness, handle bar loads (like when sprinting out of the saddle) and more.
The motorized jig is used to test bearing life and cable routing durability. Fosdick has other plans for it and says the whole workshop is very modular, letting them switch things around to let them do what they need to do or try something new quickly.
The alignment table, which is cut off at bottom of this photo, lets them check that everything’s where it should be. All the prototypes and warranty frames get tested here, production bikes are spot checked at the factory.
The machining tools and lathe are used only to make test fixtures and tools, they’re not really doing any prototyping onsite other than the 3D printed visual samples.
As mentioned above, the demo fleet, media bikes and special projects are assembled and repaired here. Customer bikes are assembled in California. Frames arrive from Taiwan and meet the parts, they’re put together and shipped to dealers.
In a separate building nearby, they’ve set up their own photo studio and art center. Since hiring Ian Hylands to shoot all of their photography, Niner’s put in a big effort at creating great visuals for their website and ads, and this lets them control it all in house.
There’s a separate workshop here so they can quickly build bikes for photo shoots, switching parts as necessary to match the different trim levels.
Then all those 1’s and 0’s go from Ian’s camera to the screen and the rest of the team helps craft the ads and other marketing materials.
Back at the main office building, other Niner paraphernalia and trinkets pop up everywhere…like this collection of IMBA frames from past years that appeared on the engineer’s conference table.
Behind George’s desk is this patent drawing for an old Schwinn boy’s frame.
Thanks for the tour and the burrito’s!