While we’re busy lining up a proper tour for this fall, HIA Velo sent over this video as a taste of things to come. If you read our Guru factory tour parts one and two a couple years ago, some of it will look familiar. And we’re very, very excited to see what else they’ll be bringing to the table. It starts off a little slow, but gets going and mentioned something we found very interesting: When you can send your bike in for warranty or repair to the same people that actually made it, that brings a whole new level to customer service. Of course, we all hope we’ll never have to send our bikes in, but should you need to, that’s a unique selling point in a day of overseas production that’s all but anonymous. Check out our initial story on HIA Velo to see what’s up down in Arkansas.
HIA Velo gives first look into their new Arkansas carbon bike factory
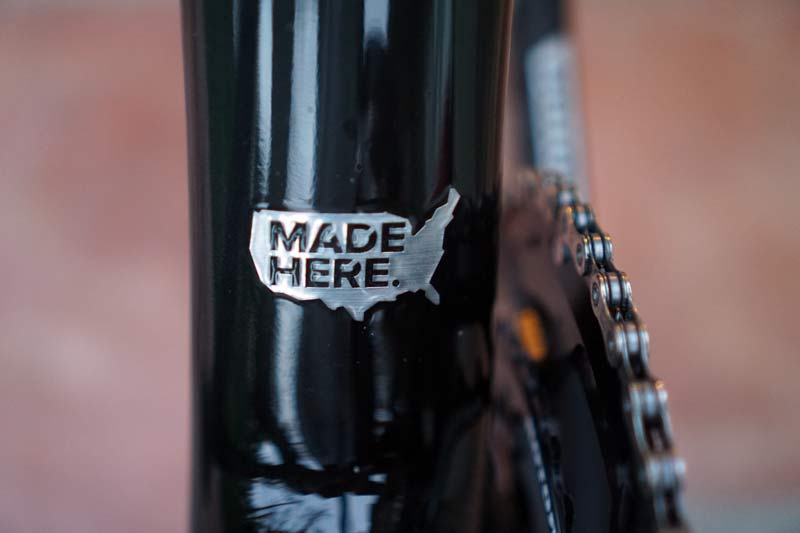