With Bespoked – the UK Handmade Bicycle Show – only weeks away now, we thought we would take the opportunity to cover a few UK-based builders who will appear in that show.
I met Tom Warmerdam, the builder and Star Wars aficionado behind Demon Frameworks, in the back of a cab going to a party at NAHBS this year. When he introduced himself, I had to shake off my fanboy response a little. Demon Frameworks has been a guilty pleasure for me and my friends for awhile now. Tom is ruthless in his pursuit of precision in his frames – to a point where he comfortably discards widely accepted methods where they don’t suit his preferred level of capabilities. The result is a process that is long, involved, highly technical, and gratifying in how hands-on it is and a product that, according to Tom, is “fucking, fucking straight.”
Though outside perception seems to be that Tom has hit his stride, the road has not been easy. In this interview, conducted in his booth at NAHBS (which featured a single bike and very little more) we discussed his challenges in getting into the craft, with early acclaim and recognition in the community, and how he’s arrived at his current level of process.
BIKERUMOR: How did you get into bikes?
TOM: Well, I’m Dutch. Cycling’s just in the blood, I suppose. Living in Switzerland, I got into mountain biking. That’s kind of where it started. The Alps? That’s what happens. In terms of making bikes, I went to university…
BIKERUMOR: Where? For what?
TOM: Southampton. Mechanical Engineering.
BIKERUMOR: So Engineering school wasn’t working out for you?
TOM: No. That was no good. The whole time I was there, I welded two small pieces of metal together. That was it. I got to a point about two and a half years in, I thought, “This is bullshit. I want to make shit. I don’t want to talk about making shit. I want to make shit.” I thought, “Okay. What do I like to make? Bikes? Bikes yeah.”
I shouldn’t have gone to university anyway. I should have gone into something…
BIKERUMOR: Like a trade school?
TOM: Something like that. I was never really good at school. It didn’t suit me.
Then, let me see, my grandfather was a cabinet maker. I actually wanted to follow that route but the parents didn’t like the idea. That’s how I ended up at university. That was a mistake. Well, it wasn’t a mistake in one sense, that I left university knowing how to use AutoCAD.
So I wanted to design bikes. I thought if I’m going to design bikes, I really ought to know how to fucking make them. So I phoned around…
BIKERUMOR: Which is a strangely sophisticated decision. Most bike designers have never built a bike.
TOM: I don’t know. I think it’s a good idea. I think it helps. The way I see it, if you don’t know how to make shit, you can’t really design shit. You can’t design shit you can’t fucking make. So what I ended up doing is I phoned a bunch of places. Bob Jackson, Dave Yates, and stuff like that. All the bike builders said “We just don’t have enough business to take someone on.” I was too old to be an apprentice. So I thought, “Right. Shit. What do I do?”
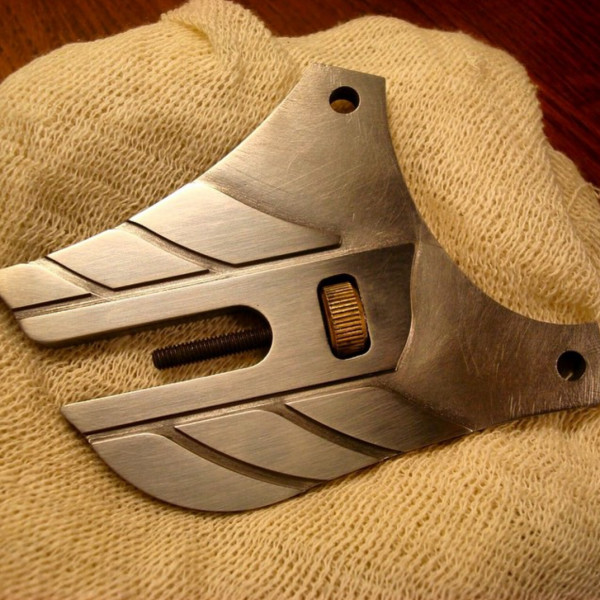
So I found a place in Southampton called The Southampton Engineering Training Association. They train apprentices for precision engineering firms in the whole Hampshire area. I phoned them up and said where I wanted to end up. They said, “Okay, come on in and we’ll talk about it, but we don’t know how to build bikes so we’re not going to be able to teach you that. But we’ll teach you everything you’re going to need to know.”
We mapped out a course for me. I used inheritance from my grandfather. They taught me every single metal joining process, bench fitting, sheet metal fabrication, milling, turning. We chucked some CNC stuff in there just for fun. Some of it was with other apprentices who were doing shit I needed to know. Some of it was on my own. Some of it was in a room full of 16 year olds, which was amusing.
BIKERUMOR: So they designed a course with you, for you. Was it a course that they determined based off of what they thought needed to happen?
TOM: Basically, yeah. They knew what it takes to make a bike. But they didn’t actually have jigs and shit.
BIKERUMOR: See, with UBI and you’ve got these people who have been making bikes forever. It’s interesting to have an education that isn’t that but instead, to have someone’s interpretation of what it needs to be. That’s interesting because it’s different.
TOM: I suppose because I didn’t learn from another frame builder it’s set me free to do things that may be a little bit different. So I did the course. I think it was about six months in total.
BIKERUMOR: You learned how to CNC too, huh?
TOM: Yeah. G-code and all that.
BIKERUMOR: How good at you at cold-coding G-code?
TOM: That’s I think how I learned how to do shit. I just plot coordinates.
BIKERUMOR: No shit.
TOM: I lift coordinates. I don’t even print shit out. I just hover my cursor over all the curves and the points.
BIKERUMOR: So you’re not even at CAM software. You’re completely two-dimensional.
TOM: I’m 2D, yeah. I’d like to step it up, but this is what I think is quite cool is because I’m restricted in my knowledge in how to do shit, that actually dictates what I make. So what happens is you end up making really quite simple stuff, but you need to try to get as much awesomeness into it.
BIKERUMOR: I think sometimes when you have a CAM program and you get so far into 3D, you can’t really focus on the things that would make 2D form work. It’s a different level of sophistication. It’s cluttered. Because you can’t be 3D, you can’t be cluttered like that.
TOM: Yeah, you come up with clean shit. But it’s mainly dropouts. I really want to do a flat top fork crown to Columbus Max. I need it 1-⅛ but it doesn’t exist. It doesn’t exist. Not a flat top one. So yeah, I need to figure that out.
BIKERUMOR: Bi-plane crowns, man.
TOM: I don’t know, I don’t know if I like bi-plane crowns.
BIKERUMOR: What about tri-plane?
TOM: No, no, I don’t know.
BIKERUMOR: Quad-plane?
TOM: Fucking hexa-plane? Denta-plane?
BIKERUMOR: It’s like razors. Just keep adding planes.
TOM: Yeah, yeah, yeah. What are we on now?
BIKERUMOR: Six.
TOM: The more the better. Exactly.
BIKERUMOR: Well, it’s a differentiator.
TOM: Yes. So then I took the inheritance money I got from my grandfather. I’d like to think he’d be pretty happy with what I did with it. I rented a workshop and I spent the next two years- I was a part time glazer.
BIKERUMOR: Oh cool!
TOM: Um, no. It was shit. They give you this fucking tongs to grab the plate. You dip it in, you shake it off, round and round, you load it in the kiln. It was kind of monotonous. I had already sort of fried my brain quite badly, so doing menial tasks was helpful for awhile.
BIKERUMOR: It helps to have time to be frustrated too so you can think.
TOM: I should have said, when I left university I had a little mental breakdown. I do that occasionally.
I go round and round. It happens, you know? I’m a long term depression suffering person. Anyway. Yeah, so I practiced for a couple of years. I did the glazing at the same time. I was just practicing. Just trying shit out. When I was looking on the internet for ideas and how to get started. I looked at frame forums and stuff like that.
Yeah, so about two years I did some friend and family shit. Then in 2009 we had the European Handbuilt Bicycle Expo in Germany. It seemed the cool thing to do.
BIKERUMOR: That’s when it kicked into full time?
TOM: Yeah. The mucking about started 2006-ish. Maybe 2005. It took time to find the workshop.
BIKERUMOR: That’s one of the things that I think is really interesting about England. Workshop space around anything urban is really tricky.
TOM: It is, and it’s fucking expensive, but I stumbled across this place. I’d been looking outside and around Southampton for fucking ages. It was all too expensive or it was just damp and shit, you know.
BIKERUMOR: Or you’re literally in a cave.
TOM: The workshop I then found was great because the location was just by the central train station, five minutes ride from my house. I stumbled across it while riding with my buddy, dropping down stairs on downhill bikes, urban freeriding. I thought, “Wow, I didn’t know this place was here.” I popped my head in one of the workshops. The guy was doing car body repair. I said, “You guys got any free workshops?”
An hour later I signed a lease and I had a fucking workshop. It was damp and needed work. I, you know, took care of it. I chiseled off all the shit off the walls and re-rendered it with waterproof stuff. It had a water feature running through it. Every time it rained it came pissing out the back wall because they built up against a bank. Above that bank used to be allotments where people would grow. In the city there used to be lots of growing. But the people who owned the workshop, they owned that as well. They sold it to the council. They put a giant fucking office building on it, a parking lot with a flood drain that went straight down, hit the clay, and the water would go straight through my workshop. That’s how I started.
I was just doing standard lugged bikes just like everybody else. The same Long Shen castings. Some Pacenti stuff. Some Richard Sachs stuff. But I got to a point where I thought, “Hang on a moment. I’m making the same bike as everybody else. The only difference is the way I do the seat stay caps, blah blah blah, and the name.” I just wanted a bit more than that.
BIKERUMOR: How is it getting frame parts in that part of the world?
TOM: We have Ceeway. Ceeway Framebuilding Supplies, they have everything. I could get pretty much anything I needed. I just had a hankering for something a bit more. So I stepped it up a notch.
I was doing a show in London, the second time I did this show in London, I had this idea of building a bike around Hermes, the messenger to the gods in Greek mythology. I started drawing some lug shapes. That’s how I came up with this. The stylized wing shape. That little piece of metal- this is the very first one ever.
BIKERUMOR: This is a tube. Is this CNC’ed?
TOM: No. This is all hand cut. So I start with…
BIKERUMOR: What is wrong with you? This is dumb… I mean, like, in a really cool way. It takes a lot of time.
TOM: That’s backhanded. “It’s dumb but in a cool way?” You’re a savage.
BIKERUMOR: We’ve established this. It’s a really nice feeling lug. Something that bothers me about castings is that they aren’t particularly precise.
TOM: The castings aren’t precise. That’s another thing that I hated about them. You spend half your fucking day grounding up the inside, making everything fit, closing the gaps, setting angles. What a pain in the ass. I thought, by the time I have these things looking good and fitting good, I might as well have made it. And the reason why I don’t machine it is because I’m not clever enough with work holding and all that sort of stuff, I didn’t have an indexer or anything like that. I don’t know how to use one. I don’t even know how to cut threads on my lathe. That’s how it came about.
That’s how the first one – it’s wrong.
BIKERUMOR: It says “wrong.”
TOM: It hangs in the window of my shop. So that’s how it came about. It was 2010 I made the first frame. I showed it to some other people on the forum, no, Velocipede. It got a very lukewarm response. People were just like, “Ah, if you left those funny key-way lollipop things out, it might be a nice lugset.”
I was like, “Oh. Fuck.”
BIKERUMOR: “Thanks, assholes.”
TOM: That was the last time I was on Velocipede [Salon]. Someone said, “Oh, it looks like someone is trying too hard.” And I was like, fuck, I don’t know to respond to that. First of all it’s not “they,” it’s “I.” And how the fuck can you try too hard? That didn’t compute. But Dave Bohm jumped in, he’s cool like that. Like, “Fuck you. If it wasn’t for people like the original poster, we’d still be making the same shit we were making fifty years ago.”
Far out. Cool. He believes in it. So I went with it. I thought, “Okay, he’s on my side. He’s a cool guy. I respect him as a craftsman.” I thought, “Fuck. Just carry on. Just do it.”
With the customers I had, I had to line up a standard, long point, simple stuff. For the same price, I said, “For the same price, I’d like to do this.” I showed them the stuff.
Some of them said, “Oh, I don’t like it.” Others went, “Hey, yeah, yes.”
Over the next couple of years I went through all the standard stuff and started building more and more of my own lug shit.
BIKERUMOR: Are you making all your own lugs at this point?
TOM: Yeah. What I do is I take CroMoly 4130. I buy it with the wall thickness that makes the ID just a little bit smaller than it needs to be. I bore them out. I turn them down to be the right inside and outside diameters for the actual fucking tube I’m using. Not just relative. I like to have a light interference fit.
BIKERUMOR: So a transitional fit, actually.
TOM: A transitional fit. Yes. And when you use silver you get a stronger joint.
BIKERUMOR: You’re not relying on your filler…
TOM: -to take up the slack. Yeah. The closer the fit, the easier it is to get the silver in there. Total silver penetration is crucial. If you sweat the small stuff, you don’t have to sweat the big stuff. Someone said that, I don’t know who that is. Then I build up a small front triangle, I just shift the bottom bracket way up- but I build it up the same way I build the final frame. I go through the same process. I jig it up, tack it, check the alignment on the table, braze it up, check it again, then chop it into small pieces.
BIKERUMOR: So you build a baby frame with all the same angles and dimensions.
TOM: All the dimensions, all the angles. Then I chop it up.
BIKERUMOR: I’d imagine at that scale it’d have to be super precise because problems over small frames are harder to identify. Did you have to make a tiny frame fixture, a special one for this?
TOM: No, no, no. I build it as small as I can get with on an Anvil jig.
BIKERUMOR: Oh. That’s pretty big, though.
TOM: I waste a bit of tubing on every frame.
BIKERUMOR: You make windchimes with it?
TOM: I’ve thought about it. What I could do is take all of the scrap I make making a customer’s bike and make something like a shitty fucking statue. “This is what your anti-bike is.”
So that’s as precise as I can make it.
BIKERUMOR: You build two frames in the process of building one frame.
TOM: If you speak to anybody else who makes bikes, there’s different ways of doing it. I mean, you could put it on the ends then braze it on, then miter it. That’s not a real lug. That’s actually going to be a bi-lam. You don’t want your top tube touching the little piece that’s still inside the sleeve that you made that goes over the headtube. See what I’m saying? So I make proper lugs. That’s way more precise. Look at all it is. That’s way more precise than you can get in a casting.
BIKERUMOR: Oh absolutely. Because of how they are made, investment pieces are strong enough just because it’s that much extra material. I think the minimal thickness is a millimeter and a half.
TOM: That’s ‘cause the steel is shit.
BIKERUMOR: The steel is shit.
TOM: [The Hermes lug is] aerospace cromoly. That’s good quality shit.
BIKERUMOR: You can touch it and feel it being a better material.
TOM: And also it’s fucking round. Actually round.
BIKERUMOR: And these inner interfaces are perfect… they can just be shit on a cast lug.
TOM: Exactly. Building the right lugs, getting the miters dead on and everything, that’s the foundation of a strong and straight frame. That’s how that came about. And then I came to NAHBS, Austin. By then I had built slightly less than 40 frames, so I was at a new builder’s table.
I built a dirt jump frame with stainless steel lug set. I just build the whole thing in one piece. I’d sort of fallen out with my painter ‘cause it was always too heavy or orange peely. I just thought, I’m making a lot of effort to make my frames clean and I’m covering it up in shit paint. So I thought, I’ll just make it in stainless. That shows what I can do. So I did copper. I did a copper plated frame, and then I antiqued it.
BIKERUMOR: Your finish has to be so top notch for the copper to work.
TOM: This nickel as well, it shows up everything. Absolutely everything.
BIKERUMOR: You can see exactly how shitty tubing surface is… because you have to polish the shit out of it to make it work.
TOM: I know. Well, that’s why I didn’t bring this to a mirror finish because I refuse to polish out little scratches in the tubes. I refuse to do it. You don’t want to take that risk. And then I spoke to Reynolds, they said it was really hard to take off 0.05mm; 0.05mm all the way around is 0.1mm.
So yeah, I did the Austin thing and people really digged it. The whole design thing- they liked the finish. That spurred me on! So when I got back from NAHBS, I had this really cool idea. “I want to do another themey sort of thing!” So I did another themed bike. I liked the Manhattan skyline. I wanted something that would capture the Manhattan skyline. One of my favorite buildings in the Chrysler Building. That’s where my other lug design came from.
In about 2012, I came back to NAHBS and I thought, you know, I’m going to put this in the Best Road Category and see what happens. I got a prize for it, and that’s cool. I wasn’t ready for a prize. I told my wife on the way over, “You know, one day it’d be really fucking cool to win an award. It might be ten, fifteen years time, but that’d be really fucking cool.” NAHBS is like the Mecca for frame builders.
But after I won that award, I felt like an impostor. I felt like shit. I felt like I could have done much better. Then again, I feel that all the time. I feel that with every bike. I’m never 100% happy. Speaking to Bruce [Gordon], I asked if it ever goes away. It doesn’t. I’m always trying to improve the craftsmanship. All of it.
BIKERUMOR: For the good ones, it can’t go away.
TOM: That is what drive you on, to constantly improve. This bike right here is the best bike I’ve ever built.
BIKERUMOR: But three years from now, this will be a piece of shit. You’ll be an impostor again.
TOM: You’re only as good as your last bike. The whole of winning, it was a bit much. It was a bit much.
BIKERUMOR: When you get an award when you’re that new into something-
TOM: Yeah. It threw me into a turmoil. It really did. Then I had a shitty customer- a few shitty customers. And I’d completely fallen out of frame building for about a year.
BIKERUMOR: I’m sorry.
TOM: And I became very depressed.
BIKERUMOR: How did you fall back into it?
TOM: Well, I sort of picked up the pieces. I’d limped by for a while.
BIKERUMOR: Wow, so winning the award really ruined frame building for a minute?
TOM: Well, it wasn’t winning the award. It was a combination of that and having shitty customers and just feeling like an impostor. It sucked.
BIKERUMOR: I think that’s something that’s lacking in discussion. This is a very tough industry to be in.
TOM: First of all, it’s fucking isolating. I work on my own completely.
BIKERUMOR: I know there are frame building communities in the US where you’re isolated, but you’re not. The community here- everyone talks all the time.
TOM: Well, you are friendly people. Friendly and open. British people are reserved.
So picking up the pieces. Slowly but surely, I was picking up the pieces. I had good customers. They were nice and respectful! I had to manage a lot of expectations- that’s been a learning curve for me. Expectation management is a large part of running a business. I did that as good as I could. Then my wife became pregnant. That’s a game changer. It was time to step it up and be efficient, productive.
BIKERUMOR: You can’t live in a shop if you have a baby at home.
TOM: No, you have to work hard and fast and get home to your family. Right now, she’s fifteen months old. Since the NAHBS in Charlotte, which went hideously wrong for me- I was filing fillets in the hotel room and I wanted to commit suicide- since then, I’ve got my shit together. I’ve really got my shit together. I’m more productive. I’m a better frame builder and a better business-runny person. It’s all good. I’m surviving. I make just enough money with frame building to put a bit of food on the table and cover some bills. I put my prices up out of self-compassion. You can’t suffer for your art. It doesn’t work.
You know Van Gogh? I didn’t want to end up like him. I didn’t want to cut off my ear and drink absinthe and commit suicide. That seems like a shit way to go. No more suffering for me.
Since then I just really want to get further into the lugs. I used put a lug around the headtube and fillet braze the rest. I just thought, in terms of time and cost and aesthetic weight, I thought it was really only required. I liked it. It was quite cool. You could balance out the visual weight with doing awesome dropouts. But I have to say, more lugs is more awesome. So we’re lugging all over.
BIKERUMOR: Are you going to change your strategy for dropouts and do sockets?
TOM: I do. I machine the little plugs and slot them and put them back together again. I mean, I want to do castings, that would be cool, but we discussed the issues that.
BIKERUMOR: You’ve circumnavigated casting entirely, then, because you construct your dropouts as well. Wow.
TOM: Yes. My CNC machine occasionally breaks down… a few weeks before NAHBS and fucks me over. I spend two days fixing it.
BIKERUMOR: You were saying! It breaks down, wipes your memory, and speaks German to you.
TOM: Heidenhain is a German company, so that’s your default language.
BIKERUMOR: So does it seem that much more menacing a problem because it’s in German?
TOM: As a Dutch person, I do feel slightly invaded by it…
BIKERUMOR: That’s incredible.
TOM: So that’s how I do the dropouts. I want to shake things up. I want to do my own fork myself. My best friend who is an English teacher and a potter- he throws pots- he wanted to see this before I built it up, so I brought it home and we were looking at it. He says, “ Tom, there’s just one thing.” And there was a long pause and I was fucking nervous that he was going to point out some terrible mistake. He pointed at all the bits I didn’t actually fabricate. He said, “It’s working, but it needs to be all you. All you. All of it.” Like DiNucci. He makes all his own shit. Every single thing on that bike, except for the waterbottle bosses. I want that. I want my own seat clusters. I want my own fork crowns. I’ve got designs for several of those bits. I just need to get on it and get it made.
(Tom describes one of his proprietary process.)
And Presto! It’s design driven by ability.
BIKERUMOR: I don’t like the idea of using “ability” as the word. “Ability” implies a hierarchy. You have creatives who work in 2D. You have creatives who work in 3D. You have photographers. You have potters, like your friend. It doesn’t necessarily mean that one is less valuable in terms of capability.
TOM: I realize because I did a wood carving course, I can’t draw for shit. I didn’t do art at school even when I was really young because I wanted to do biology and we get forced at a very young age to make choices. But when I did the wood carving course, I could feel it. I could feel the shape. I could feel things. Frame building is the same. I feel it. My hands are on it.
BIKERUMOR: What is your goal for your product? What is your product in an ideal case for you?
TOM: Well, I’m going through a bit of a moment right now where I want to do things. I want to continue to refine what I have right now. I want to make all my own shit, but I also have ideas for frames. I want to build bikes the way I want to build bikes. If that changes from year to year, so be it.
I want my bikes to be recognizable as my work without paint, without decals.
BIKERUMOR: So given your process, how do you get your lug points to match on the back of the headtube?
TOM: I think it’s about a quarter of a mill off.
BIKERUMOR: How are you living with yourself?
TOM: I know.
BIKERUMOR: So are you building exclusively in steel right now?
TOM: Yes. I quite like the idea of doing some other stuff, like a little bit of carbon stuff. I’ve been talking with Matt Appleman about doing a collaboration where I do the lugs and he does his carbon coolness. He’s Appleman Bicycles. I’m Demon Frameworks. We’re going to call it the “Forbidden Fruit Project.”
BIKERUMOR: Oh that’s great.
TOM: Yeah. So there’s that. I’d like to work on different materials in that way, but as collaborative stuff. It’s very interesting. I’d like to do a crazy monocoque thing as well, just unleash it. Go fucking nuts on it. But again, I don’t want to be seen as a form over function person. The forms that I come up with serve a function, not only structurally but visually.
BIKERUMOR: Where you put your keyholes, for example, you don’t see that really except for inch tube lugs, where structures were a lot more critical because of poor tubing or process, the really old stuff. I look at your lugs and I see that stuff. It’s very similar that way. I like it. Is it deliberate?
TOM: Well, I don’t know if it really was. It allows for movement in the joint and that’s fucking important. It just happened to work that way. I mean, the placement of everything on the lug had always been about visual flow. That’s how it starts. The fact that it’s also structurally a fucking good idea? Bonus.
Henry James remarked on it, Hank Folson remarked on it, “Actually, that’s really cool because it allows movement in the joint and it reduces stress risers. Go for it.”
BIKERUMOR: Yeah it does! But it wasn’t necessarily the goal.
TOM: No, the goal of the design of the lugs was purely aesthetically driven. And then the fact that I don’t have to change the angles of lugs and they are so precise. It’s a trifecta. I get pretty nutty about alignment as well. I like things to be fucking, fucking straight. I don’t really know what the industry standard-
BIKERUMOR: Is that metric? “Fucking, fucking straight?”
TOM: Yes. I have my minimum, minimum tolerance. I was talking to another builder in the UK, Bill Taylor. He organizes the Bristol show. He’s coming up and talking about alignment. Well, I want everything to be 0.2 of a mil. That’s really the minimum. If it is more than that, I deconstruct it and start it again.
BIKERUMOR: Over the whole frame 0.2mm?
TOM: So my head tube twists along the seat tube length and my maximum tolerance is within 0.2 mil. And consistently I hit it. The way I do that is refining the process, tweaking it and tweaking it, so that by the time you’re done, everything ends up where it wants to be. I need to witchwand the seat tube sometimes. You know witchwanding?
BIKERUMOR: Witchwanding? No.
TOM: Applying gentle heat to the right place, the metal cools down again and shrinks a tiny little bit. You can get it to move 0.1mm.
BIKERUMOR: I’ve never heard it called that! Is that what they call it there?
TOM: I’ve been doing it, but Don Ferris had the name for it. I don’t like [cold-set alignment]. You build a dynamically aligned frame that way and as soon as you have a jump or a drop down a curb, it settles back down to where it wants to be. Metal does it’s own shit. I don’t want to get all Richard Sachs and blog and get all philosophical about it, but metal moves. By the very nature of butted tubing, it goes, it moves. But you can control it. I have several levels of control. First, make your lugs as good as fucking possible. Then I pin my joints- I pin my joints in the jig, pull it out, check it on the table, tack the points with silver, take it out, check it again, braze it one joint at a time, checking every single time.
BIKERUMOR: You pin joints, do you have pins in the frame?
TOM: No, there are pins sticking through the frame. I put three to four pins in each joint. I use furniture tacks. They are square and tapered and they fill the holes nicely. But it’s belts and braces. You know when you’re wearing a belt but you’re also wearing braces?
BIKERUMOR: It’s overkill.
TOM: It’s being overly safe. The reason why I do that as well is because I can’t afford to fuck up. By the time I get to brazing the final frame up, I’m a week or two in.
BIKERUMOR: Do you build one frame at a time? So, you don’t batch.
TOM: The thing is that making lugs is hard on your hands.
BIKERUMOR: So you spread it out. I get that.
TOM: And also, mentally it’s taxing. The whole way the bike is made is taxing. I would like to take a long weekend after each bike. Drink some beer.
BIKERUMOR: So this guy, is this stainless?
TOM: Nickel plated. There’s not a single bit of stainless on this frame. Normally, all my contact surface shit is stainless unless a customer specified a particular dropout. I don’t let my customers specify much. I don’t give a lot of options. I build bikes the way I like to build bikes. I’m very selfish.
BIKERUMOR: How much does a frame and fork go retail for you?
TOM: 3,500£ for frame and steel fork [for the Hermes lugset]. I always do frame and fork together because I want to ensure the right handling. And I always build the fork first because it allows me to be half a mill off, a mill off with the axle to crown length and it doesn’t fuck it all up.
BIKERUMOR: Plus, with production carbon forks, where there isn’t nearly as much precision, you can ensure your frame works with exactly the fork you have.
So this frame is made for Don Walker.
TOM: It is indeed!
BIKERUMOR: Don Walker doesn’t often have other people have him make him bikes.
TOM: Not often, no.
BIKERUMOR: And he was so excited about this one when I interviewed him. So excited.
TOM: I didn’t think he was serious when he asked. He asked me how much. I told him. Then 500 pounds showed up in my PayPal account. He was serious. He said to me, “Tom, do what you want to do, just make it a fast road bike and make it to this geometry.”
The nickel plating was the thing that I really wanted to do, but I also wanted to do this tube format. Don’s a big dude. He’s powerful. He used to ride track and shit. So he needed big tubes.
BIKERUMOR: So your lugs are bigger for this then?
TOM: Oh yeah. As far as I know, I’m the first guy to make a proper lug around a 44mm headtube. I don’t know because I haven’t looked.
BIKERUMOR: You could be right! Especially as a real lug, not bi-lam. Why would you cast it? It would be a disaster to cast.
TOM: Yes, because you don’t have the freedom.
BIKERUMOR: Wow, it doesn’t look 44mm! I didn’t even notice!
TOM: That’s the greatest thing about it. The ratios of the tubes to each other are exactly the same as standards oversized with a 1-1/8th headtube.
BIKERUMOR: That’s a 1-¼ top tube? 1-½ downtube?
TOM: Top tube is 35mm. Downtube is 38.1mm. And the 19mm seat stays.
BIKERUMOR: I saw that. It’s totally scaled.
TOM: I know. You put it in a photocopier and hit enlarge 25%. The proportions are the same. It’s pretty cool how that came together.
BIKERUMOR: I feel like you’re doing something weird with your caps, too. Weird in the best way possible. What is going on with your caps?
TOM: I machine plugs so they sit in there.
BIKERUMOR: So it’s not a cap, it’s a plug. Wow.
TOM: It’s a “top eye.” We call them “top eyes” in England. There are “top eyes” and “bottom eyes.”
BIKERUMOR: See, I’ve never heard that. You could totally be making this up. Is this a big joke you’re playing on us?
TOM: No!
BIKERUMOR: So what else about this frame is great that I wouldn’t know or see? Because I wasn’t expecting that “top eye.” I wasn’t expecting a lot of what you told me.
TOM: As a designer- I’m not really a designer, I muddle through- as a person who muddles through and as a frame builder, out of self respect I think you need to progress. Not just with muscle memory and craft but also in terms of design.
BIKERUMOR: Given that you’ve completely attacked from an outsider position- you have! Over and over again. I don’t know a lot of people who do this the way you do. Clearly you think it’s valuable.
TOM: It’s dumb. I’m dumb for doing it in many ways.
BIKERUMOR: My last question for everyone is, what do you tell the kid that wants to grow up to be you, to be who you are, go at it the way you have? Hasn’t been trained, has no experienced, What do you tell him?
TOM: Practice. Be yourself. Make what you want to make.
That’s about it really.