Are fully 3D-printed bike frames the next big thing in titanium? It’s quite possible based on what we saw today at the Pilot Cycles booth at Eurobike. The Eindhoven-based company has been creating custom titanium bikes for 10 years now, but the Seiren looks to take it to the next level (and then some).
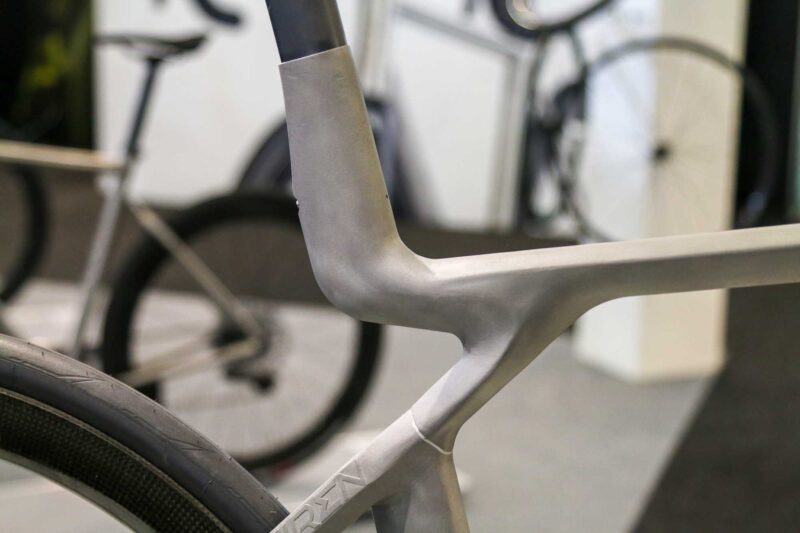
It was hard to avoid the Seiren’s call walking past, but it wasn’t the 3D-printed aspect that caught my eye. It was the relatively-unique seat mast. But looking closer, it was suddenly clear that this was no average titanium bike. Not even a slick titanium bike with 3D-printed lugs. This bike is 100% 3D-printed from powdered titanium.
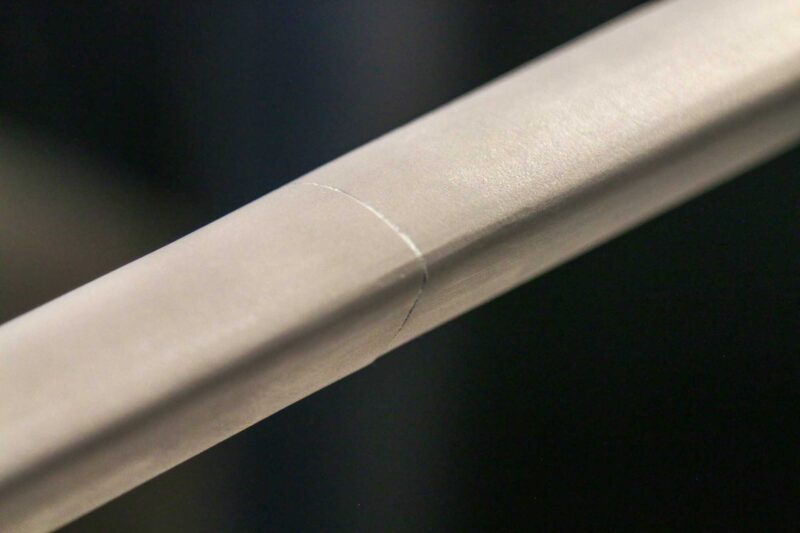
Now, it’s not printed all in one piece. Instead, it’s printed in three parts and then bonded together with a specially developed “metal glue for titanium.” We were told that the total printing time was just 8 hours on (what we assume is a very large) SLM (Selective Laser Melting) printer. That number is kind of staggering considering many 3D printers take just as long if not longer, just to create small parts out of plastic. Even if that number is 8 hours for each of the three frame parts, that’s still very quick to create a completely custom titanium bike.
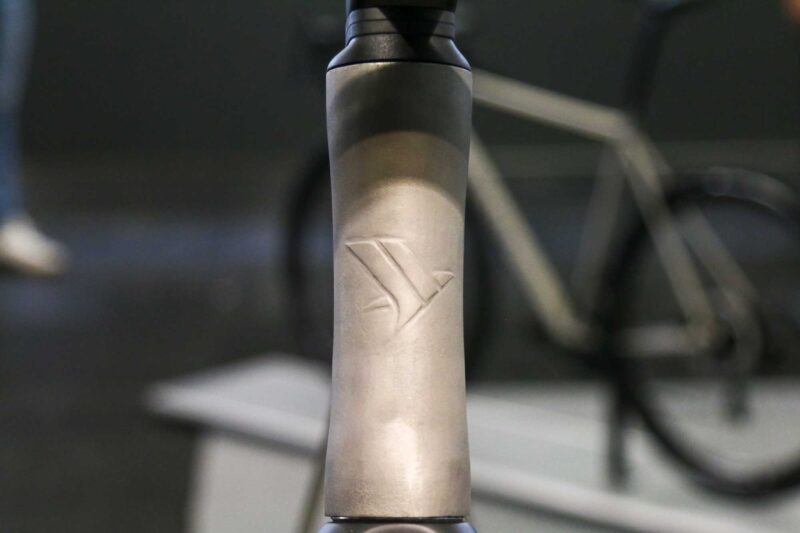
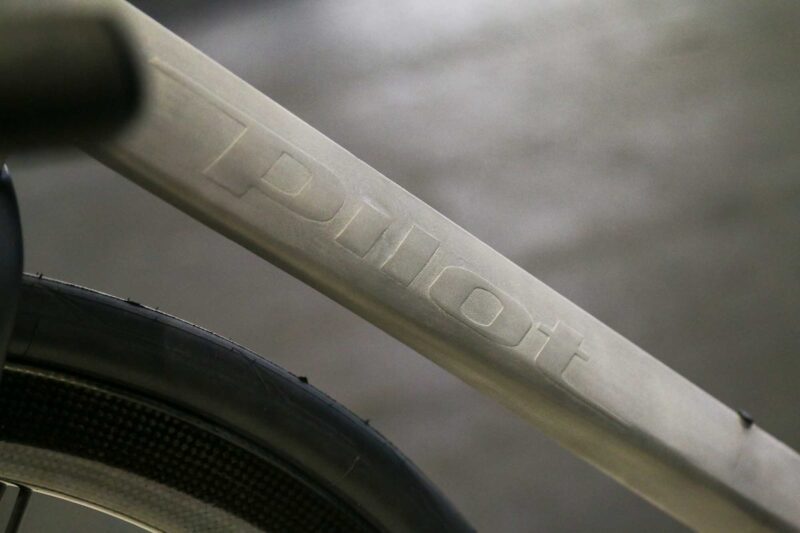
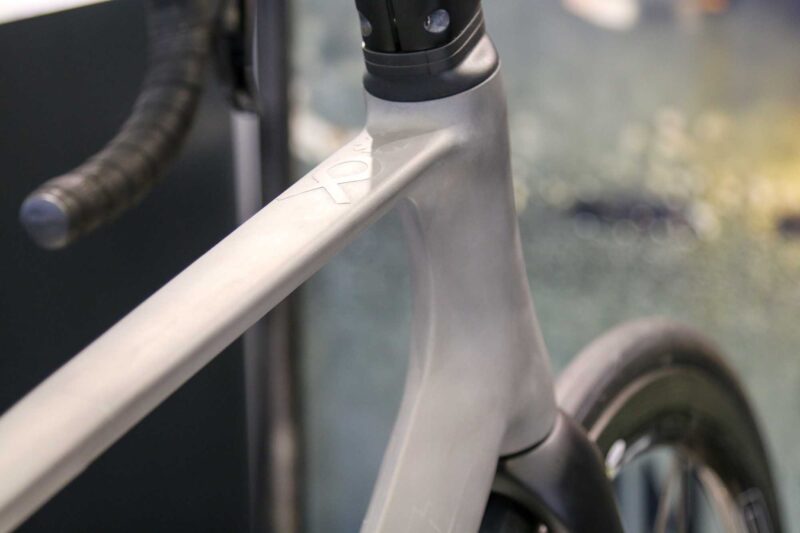
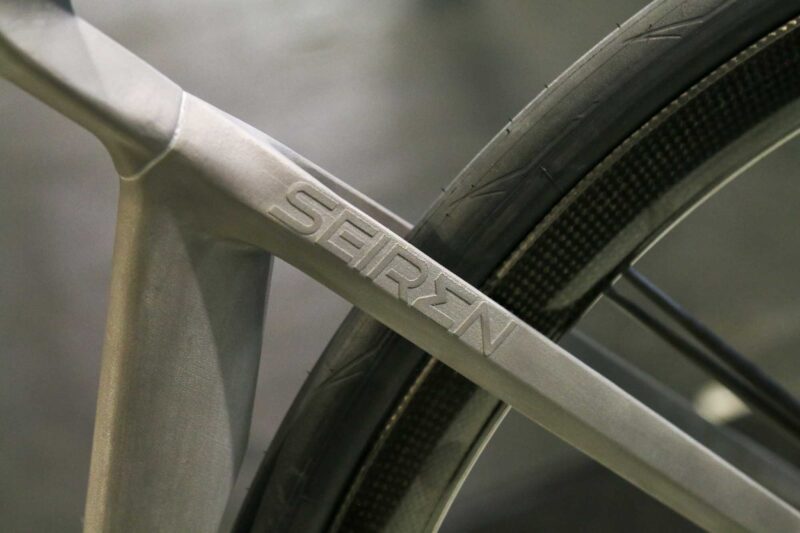
Not only is this a fast way to create a custom bike, but there is very little waste from production since the excess titanium powder can be reused. Pilot also claims the frames are 100% recyclable.
On display at the show was one of the first prototypes, which is already being improved upon. The version on display is claimed to be about 1,150g for a 57cm frame, while the next version they’re working on is expected to be around 1050g for the same size.
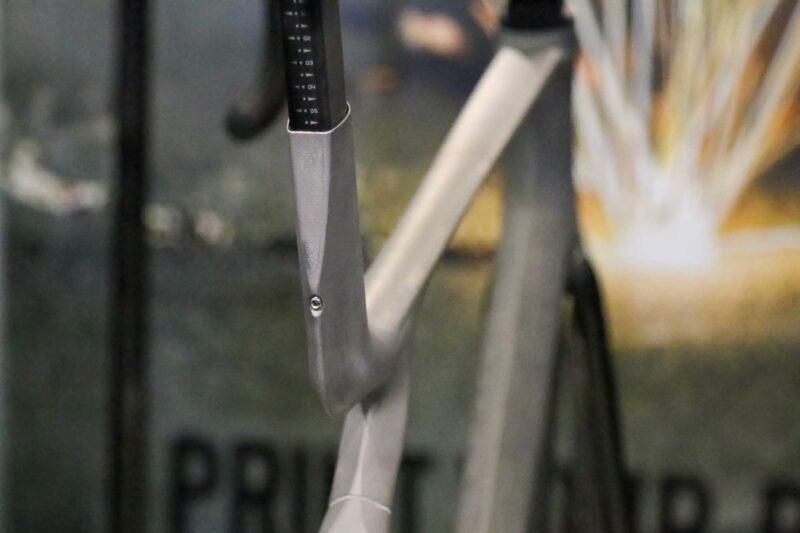
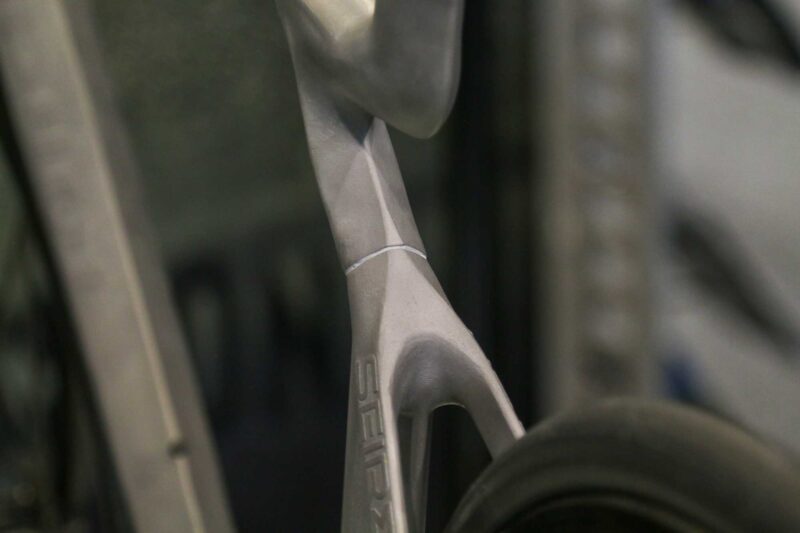
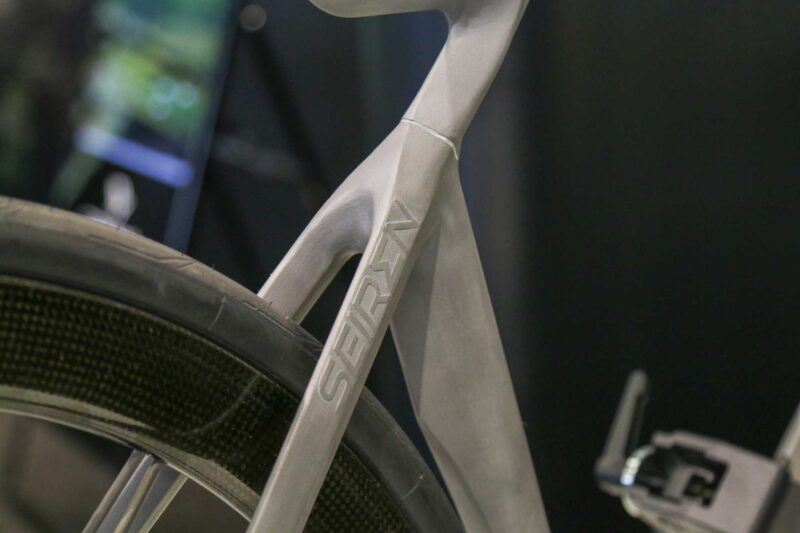
When asked about the seat mast design, the answer was surprising – the configuration was chosen to aid in frame alignment more than rider comfort.
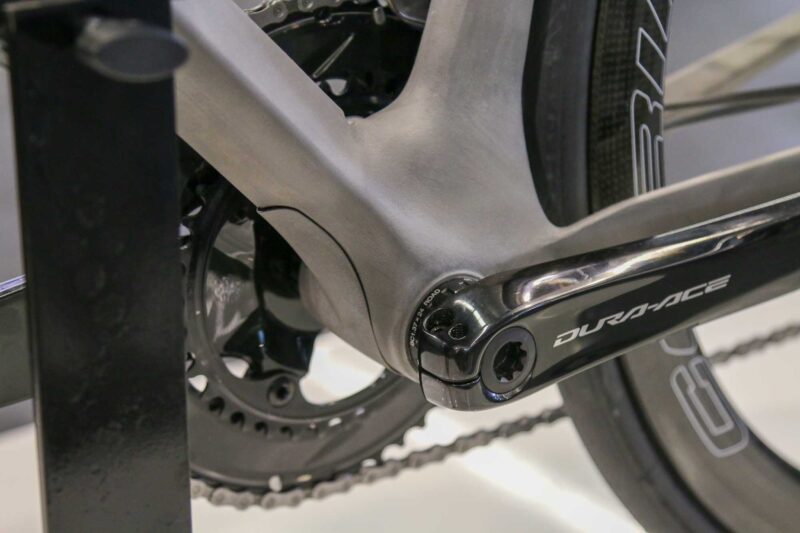
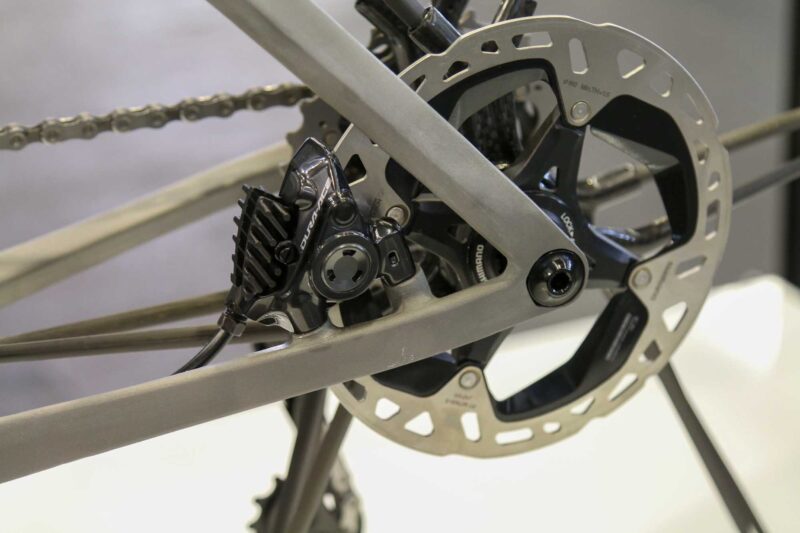
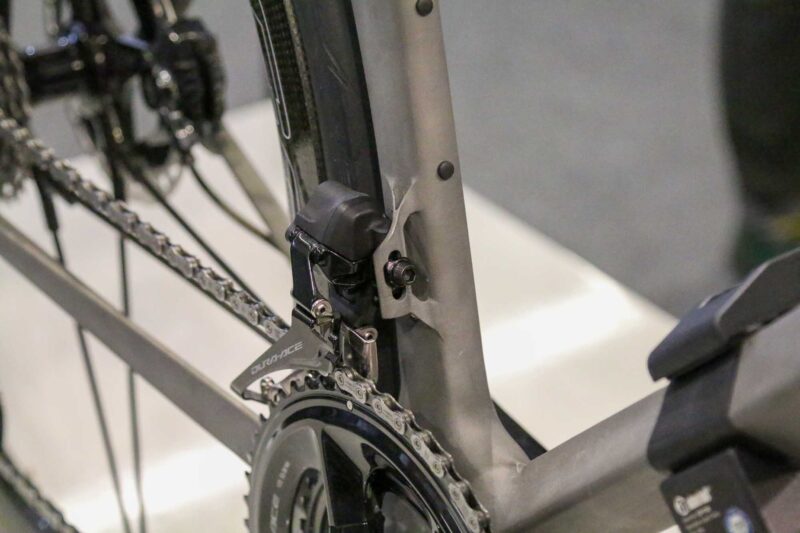
The frame uses a standard threaded bottom bracket with printed threads. Pilot notes that all of the threaded holes do have to be chased after printing. The frame itself was shown as a raw sandblasted titanium, though they’re looking into methods of polishing the titanium as well. Behind the door on the bottom bracket is another 3D-printed part inside to hold a Shimano Di2 battery.
The Seiren will first be completed as a stock design, but the goal is to offer complete customization from frame geometry to frame details. We’re hoping to get details on potential pricing and availability soon.