To celebrate the SRAM RED eTAP wireless shifting launch, they brought us to their drivetrain development office in Schweinfurt, Germany, for technical presentations and the very first public test rides anywhere.
We’ve covered the product tech, weights & setup here, now we’ll cover the lengthy testing procedure they underwent to ensure that the most anticipated launch in the company’s history is bombproof. And we’ll share thoughts after riding 145 miles (233km) over three days through the rolling hills surrounding their office.
The testing process started in the lab, progressed to employee and “super testers”, then smaller and regional teams, then finally to AG2R in the Tour Down Under and Tour de France. Here’s how it went…
LAB TESTING
The eTAP project meant hiring a lot of new people, from electrical engineers to consultants, and borrowed concepts from others. For example, they used Nokia’s tumbler test, used to test cell phone durability. They borrowed vibration tests from the automotive industry to simulate 10 years of use. That made certain that the battery won’t pop off even under extreme conditions – once the battery snaps into place, it’s there to stay.
They also made sure it passed dust and water ingress, with the latter passing a 1m submersion test. It also stands up to a 30 minute power washing test with water hitting it at high speed from every direction.
Inside this climate chamber, shifters and derailleurs are subjected to extremely high and low temperatures and humidities. They cycled the system through hundreds of thousands of shifts over days in the machine as it swung from each extreme. The standard testing range is -10°C to 40°C (14ºF to 104ºF) testing, then they push it to -30° to 50° (-22ºF to 122ºF) to test it at the extremes.
On top of that, they tested it against thermal shock, which proved it would work if, for example, it sat inside your car and hit temps well over 130ºF and then you sprayed it with cold water to wash it.
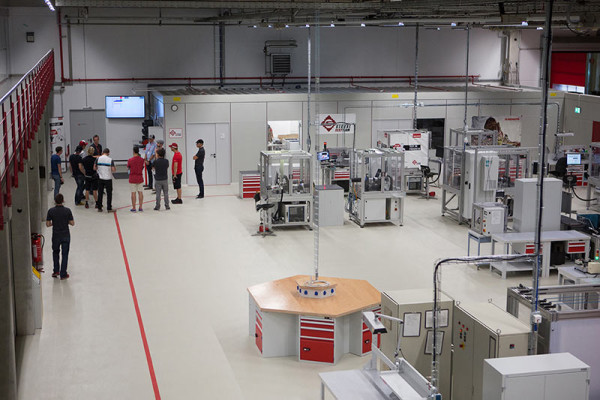
To make sure all of those tests and standards make it from development prototypes into full production models, the manufacturing process is completely controlled by SRAM. With many electronics being outsourced (in any industry, not just cycling), it’s important to make the distinction that they control both the electronic production and the finished assembly production. They created a clean room in Taiwan to create the prototypes over the five years this project has been in development. What they learned there led to a complete trashing of old production and assembly lines and diagnostic tools. All of that is completely new in order to make the parts to SRAM’s specifications.
So far, they’ve done 26 pilot production runs for each component, with another six planned before anything ships. Each run sees further refinements to the process to ensure that when it does ship, it’ll be right.
MORE TESTING
Both derailleurs are put on separate testing machines where they’re cycled through the range of the cassette or back and forth between chainrings. They test it to failure, keeping it running well past any 3rd party and internal standards. The last rear derailleur they tested went through more than 1.7 million cycles. They measure not just the overall accuracy of the parts, but also wear, to see how they tolerances start to vary over time.
Another device is used to test the shifters coming off the production line – each and every one of them is checked. For long term test samples, they’re checking not just the mechanical accuracy but also the firmware and other electrical parts over time. There’s a physical test machine that applies a high load to the setup buttons, which will typically see very few actual pushes. Another pulls the brake lever harder than you’re likely to ever pull it for 100k cycles to see how it holds up. They also perform drop and impact (crash) testing and submersion and salt spray testing. They even have a machine that does nothing by stretch and cycle the springs used inside mechanical rear derailleurs.
If you think you’ll encounter it, there’s a darn good chance they’ve tested for it.
FIELD TESTING

The first generation is what we spotted at some 2013/2014 cyclocross races and had fake external control boxes. These were the first stage of testing with their employees and in-house athletes.
The second generation had internal electronics and was wireless, but they mocked up fake cable housing to keep it somewhat incognito. These were pushed out to their “super testers”, who would take the system to a broader range of environments and expose it to new challenges and generate new questions. This included pro women like Kristin Armstrong and Alison Tetrick, and Axel Merckx’s Bontrager cycling team in spring 2014 at the Amgen Tour of California.
They also brought it to Redlands, which was pilot run six or seven, but had some pre-race water ingress issues that made them switch back to standard systems for the event. They fixed that and brought it back for the Gila, where Bissel’s Nicolai Broechner rode it to a stage win despite being in a massive pileup that gave it a few scratches. During these races, their neutral support cars and motorcycles were stealthily equipped with wireless monitoring systems to check for interference, but found none.
They put the TT parts on 2008 Olympic Gold Medalist triathlete Jan Fordeno’s bikes, who used it to win Oceanside this year, and Lisa Brennauer, current world ITT champion. What’s interesting about the TT parts is that, unlike mechanical or Di2/EPS buttons, they don’t lengthen the aero extensions or become part of the load bearing setup, which frees up the types of handlebars and extensions the athlete can use.
The final step was Version 3 (and 3.1, 3.2, etc…), which have been tested in the pro peloton by AG2R. As that testing progressed, and they refined the pilot run production process, they put up to 100 systems in the wild. Up until this year’s Tour Down Under, they continued to put fake control boxes and wires on the bike (including even wrapping a raisin box in electrical tape) to hide the fact that it was wireless.
That put the system through top level competitive tests, which meant crash testing and dealing with battery anxiety. After all, the bikes might be left in a freezing cold truck overnight, which is notorious for shortening Li-Ion battery life. And they’d be in a peloton with other bikes shifting amid wireless communications and broadcast signals bathing them in similar wavelengths.
Now, as we hopped on board our first ride of the system, there are close to 200 systems out there with an estimated one million kilometers of real world testing. And through all that, they say they could count on one hand the number of times anyone’s missed a shift. In other words, they say it’s flawless.
FIRST RIDES
…and it is. We put in 145 miles through the rolling hills around SRAM’s Schweinfurt, Germany, drivetrain development center and walked away extremely impressed.
The shifting is not blazingly fast, but it’s fast enough to work as well as you’d want it to. Which is good, because you can’t change it…much. Adjusting the B-screw to change the gap between the top pulley and the cassette within the 6-8mm recommended range can tweak it slightly. The closer it is, the faster your outboard (harder) shift will be. More space will make the inboard (easier) shifts quieter, but won’t really speed them up.
SRAM’s tech folks even admitted it’s not lightning fast, but that the overall time and energy the rider expends to make the shift, though, is much, much shorter. So the effect is quicker shifts than what you’re likely to get from a mechanical system, and it’s definitely waaaaaay easier.
All that said, it’ll still move up and down the entire cassette in under four seconds just by holding the button down. And faster if you repeatedly tap the shift button yourself. And that’s just the rear shifting. The front shifting is simply brilliant…and very fast. Check it out in this video:
Why not synchronized shifting that automatically shifts the front to maintain a certain gear ratio? Mainly because it can’t read your mind and you may want a different cadence at different points in a ride. The benefit of synchro shifts is that you no longer have to think about which button makes the correct front shift, and with eTAP, you really don’t – you just push both.
That simplicity is one of the our favorite aspects of the system. Push the left one and it shifts easier. Push the right one and it shifts harder. Push both and the front shifts. It couldn’t be easier, and it takes all of two minutes to get used to.
Just like with the mechanical system, the YAW front derailleur works great at eliminating chain rub. And the calculated front shifting movement with auto trim never missed a beat. Honestly, front shifting is flawless, quick and can be done back and forth in rapid succession.
Rear shifting is very smooth under power shifting to an easier gear. That made for incredibly easy downshifts while climbing, no matter whether I was seated or standing, pedaling fast or slow. Shifting to a harder gear under power (hard climbing or sprinting) can feel a bit chunky, so it’s best to ease off just slightly. In other words, shift before you need to sprint rather than during the sprint. That’s really the only criticism I can levy on it. At risk of sounding overly positive, the eTAP has changed the landscape of bicycle shifting for the better and everyone else must now catch up.
Basically, this is F1 shifting for your bike. Do we need it? No. Do I want it? Only on every bike I own.
PREDICTIONS
WiFli wider range double gearing will likely come soon. Could you hack it by putting a longer cage on it? Maybe, but there’s more of a difference between their derailleurs than just cage length – the upper jockey wheel is sometimes offset and the parallelogram arms are a bit longer.
Mountain bike versions are likely, but perhaps with initial development around an X-Horizon rear derailleur for cyclocross first. To go with those WiFli cassettes. With regards to MTB, one SRAM manager told us “We’re looking at it, and there’s been some work put behind it. A lot of the heavy lifting has been done already because we needed this system to be so robust.”
But Hydro versions are a bigger priority, opening up the group to widespread use with their disc brakes. There’s no set timeframe, but we’d be surprised if it’s not ready for the 2016/17 cyclocross season. That said, they continually reinforced their commitment to mechanical 1x groups with hydraulic brakes for ‘cross. So, expect those groups to continue even at the highest level, and RED mechanical will remain, too, with graphic updates to match the rest of the eTAP group.
Lastly, this is a halo product that, in our opinion, puts SRAM at the top of the electronic game. But to make the system more widely adopted, it’ll have to trickle down to Force level groups at a minimum. As they put it, “If you look at who we’ve hired over the past few years, we’re all in. There’s a lot of sunk cost there, and this first product alone won’t cover that. The technology is now developed, and it can be applied to anything that shifts and anything with a cable…now it’s just a matter of where we apply it next.”