The exception to the rule at this year’s Press Camp was Koroyd who, unlike any other exhibitor, brought literally no products to sell. The aerospace material manufacturer doesn’t sell directly to consumers, after all, it supplies brands with their technology (such as Smith). Rather than a pitch a new product, Koroyd presented media with their new safety initiative: a call to action to industry to voluntarily raise the safety performance standards of helmets.
Their case? Unlike the automotive industry which has an evolving safety star rating year to year, the cycling industry has a pass/fail validation system, one that Koroyd believes sets an unacceptably high level of risk of injury for riders and which has not been updated in twenty years to reflect improving materials and technology.
In this interview taken on the last evening of Press Camp 2016, John Lloyd, owner of Koroyd, and Bas Jongsma, discuss the initiative, the urgency behind it, and the opportunity for safety within helmets and protective equipment in the industry. Basically, we can all be safer- and industry can and should voluntarily up their game to make that happen.
Koroyd Safety Initiative
BIKERUMOR: Firstly, how did you get your start?
JOHN: I was working in the motorcycle market and I was heading up a team that was developing motorcycle helmets and clothing and protective accessories. At the time, we had a pretty large share of the market so we were often approached by people with different ideas and technologies and materials.
The inventor of the material which came to be known as Koroyd approached that company to introduce it to the motorcycle helmets. We did the validation and yeah, the results looked pretty close to what the inventor had told us. From there, that’s where I spun out Koroyd and left that company I was working for. We started Koroyd and really started to research the material.
BIKERUMOR: Were you seeking out motorcycle helmets and bicycle helmets for application of the material initially?
JOHN: When we started the company- Bas joined almost immediately- Bas was in the motorcycle market already as well.
Right from the beginning, Bas and I put a plan together to try to introduce the material to the motorcycle market where we had the experience, we had the contacts. We knew how to build the helmets, we knew the material performance in the helmets- we imagined that would be the first market to enter. But, as we found, it was much more conservative and less receptive to new technologies than cycle and ski, which we were approaching at the same time.
BIKERUMOR: How were you approaching these companies with this crazy new material?
JOHN: Our material is more expensive than traditional energy absorbers. We had a clean sheet to build the company that we wanted. The idea there, and it’s true today, we were looking for premium partners in each market. In each market we were looking for two- three- four of these that we could really integrate with and become part of their proposition. When we say ‘premium partners’ we’re talking about companies that are in a perceived premium position in the market. With that, they’ve got the distribution channels and the volumes and the machines that can give us the financial reward as well for our equipment, got to be able to integrate the material as well, so you’ve got to have the good technological level. They’ve got to be able to communicate the technology correctly and effectively to the consumers.
BIKERUMOR: You’re talking about strategy. One of the negative aspects of the bike industry is that it can be very traditional. If it doesn’t look or feel or behave in the way it’s behaved in the past 50 years, then it can terrifying to consumers and a challenge to adopt. Nobody wants to touch it. I remember the first time I saw your material in a helmet. I was like, “What kind of novelty is that?” honestly. Either it’s done purely out of novelty and adopted out of novelty as a new product… or its just so weird that the industry doesn’t adopt it.
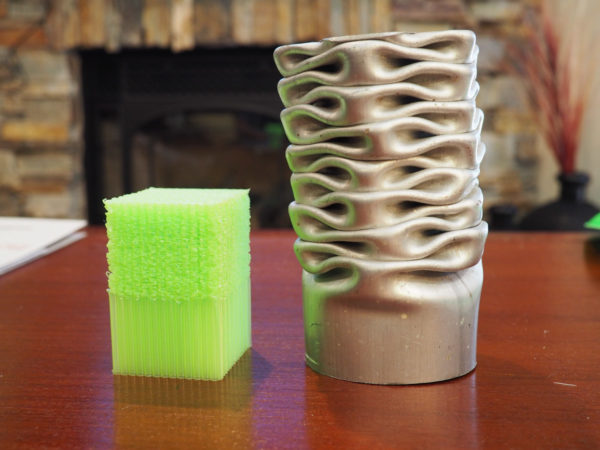
JOHN: I think there is a lot of skepticism, and it probably doesn’t help us that a lot of the other innovations in the marketplace aren’t innovations at all. There’s some sort of marketing connotation to it. But we’re talking about a wholesale change on how to manage energy. So EPS foams, viscoelastic foams, EPP- all these materials, they aren’t true energy absorbers. They hold the material like a spring and the material energy comes back out. Our material is sacrificial so when you have a higher velocity accident, the material is crushing, and the energy is being transferred into that crushing, and also the little bit of heat is being given off.
We had to overcome a lot of that skepticism because I guess there aren’t that many true, true innovations in energy absorption.We still do a lot to try to support and revalidate all of our thoughts and how our material works and find more data to support it. More processes.
BIKERUMOR: When we were talking earlier, you said you were cutting apart other people’s helmets and just sticking your material in there.
JOHN: Yes. What we were doing there was for our knowledge. Okay, if we really want to get into the ski market, let’s get some hardshell helmets, let’s get some in-mold helmets, let’s put our material in, let’s grow our knowledge base, and then we can approach different brands. But most brands that we approached, when we were telling them about the amazing performance of our material, want to validate it in their helmets. So they would send us their helmets and we would cut the cavities and put our material in and send it back to them for testing. They would validate it and see that the material does work in some way inside their products, in their test lab, and under their control.
BIKERUMOR: I have to ask as far as Koroyd- was it the safety applications of the material that made it attractive to you?
JOHN: I’ve always been a product guy. All my life, from a kid growing up, I’ve liked product and design and building good product with the right teams. I’ve always been hugely drawn to that. There is an urgency about the safety side. We’re not on a mission to save the world, and we’re not going too far with it, but I definitely have a huge interest in reducing the risk of injuries of people in activities.
BIKERUMOR: It’s interesting because this campaign seems to be exactly that. The campaign as I understand it is “we all need to be better.”
JOHN: Do you think that it’s particularly normal to inform consumers that actually, they should have an awareness of the stuff they’re buying, how it is performing? In any other industry, you’d be really quite acutely aware of the performance of a product you are buying and why you are buying it.
BAS: In this way, we ARE trying to change the behavior of consumers.
JOHN: I’m saying that that’s not particularly normal.
BIKERUMOR: Your Press Camp presentation compared bicycle and motorcycle compared very directly the automotive standards with the bike industry and motorcycle industry standards. That’s really interesting because with the automotive industry there are standards- but there is also a star rating. The tests are constantly validated and improved and your results fall somewhere on the spectrum. It’s an industry adjacent thing rather than a governing body thing. It’s not like the bike industry where it is black and white. You pass or you don’t. And the standards rarely change.
What I was taking away from the presentation was that it was you guys saying, “We need to have something like this. We need to move in this direction.”
BAS: That’s one possible solution to it. Acceptance criteria for helmets have been the same for about 20 years.
BIKERUMOR: What was the motivation behind this campaign?
BAS: With Koroyd you have a material that absorbs more energy in the same thickness, for instance, than traditional materials. So you can do two things with this. You can either make products smaller because you can meet the same criteria with smaller product, or you can use the additional performance to make a better performing helmet. We had a big preference to say, okay, this is an accepted helmet size, for instance, let’s make these products better.
We wanted to make sure that there was a necessity to make it better. If helmets that are out right now are protecting well enough, then we might as well make smaller helmets. So that’s when we dug into the automotive industry data.
As long as anyone trusts the risk curves that all these NCAP programs are using internationally, which are pretty much the best things we have to review the risk of severe head injuries, we’re using these same exact risk curves to see what the potential risk is of suffering these severe head injuries. And these risks are really high, as high as 40% risk of suffering a skull fracture at the maximum allowed limit of European helmets. The US standards allow an even higher tolerance of acceleration of 300g, which is correlated with a 79% chance of suffering a skull fracture. Those risks are so high that, definitely, it’s a good idea to make better helmets.
In the automotive industry, they are working towards these less than 5% limits. If you look at less than 5% limit for skull fracture, you’re talking about 183g of acceleration. If you have a helmet that voluntarily complies with the lower limit of 183g, then now you have a helmet that is protecting in a better way, at the very least at the reference impact velocity. That’s what we’re trying to do, offer more protection.
BIKERUMOR: When you approached this research, because you were doing it from scratch, what did that look like? You learned a lot about it. How did you approach that research as people coming at it from the outside? What did you discover that was most horrifying to you in the process?
BAS: We were pretty shocked by these really high risk tolerances that these helmet standards are allowing, basically. These risk curves have been around for a long time, since ‘85, so at the time that these helmets were set, which was in the mid ‘90s, the knowledge was available for how much risk we were accepting with these helmet standards. We asked why they were set at these high tolerance levels. The answer we believe is that at that time, technology didn’t allow for lower acceleration, for lower acceptance criteria.
It’s important that the industry is able to produce products that comply with limits. But it’s 20 years later now, and we’ve proven that with new technologies you can make much better helmets. That’s why a step is necessary to have better performing helmets. You could wish or hope that safety standards are catching up and improving their acceleration limits, for instance, their tolerance levels.
We’ve talked to several safety boards, okay, what can we expect for any updates on these standards. I’ll give you an example. The European motorcycle standard allows for a crazy number, which is correlated with a 97% risk of suffering a severe traumatic brain injury-
BIKERUMOR: – even if the helmet does everything it is supposed to do.
BAS: Exactly. Imagine a motorcycle helmet that is performing close to its limit- and this criterium they need to pass is actually the single most difficult part of the helmet standard to pass… so if you’re wearing one of these helmets and it’s performing close to the limit, and you have an impact at the velocity it is tested at, which is about 20mph, in the same conditions- according to these risk curves, you are exposed to a 97% chance of sustaining a severe traumatic brain injury.
BIKERUMOR: 20mph isn’t even that fast on a motorcycle.
BAS: Correct. That’s very shocking. I called the ECE, the Economic Commission for Europe that govern the European motorcycle helmet standard, to ask them: when is this going to change? And they said “we meet every year. We have a meeting in October to discuss the helmet standard and there is nothing on the agenda.”
Then I spoke to a person who is actually on the board when the helmet standard was test in ‘97. He said it took about five to ten years to set the helmet standard back in ‘97. He said “it’s probably going to take you another five to ten years before any change will happen.”
Right now, we can’t wait for these safety standards to catch up. So if manufacturers take the step to voluntarily comply with lower limits, then we are already offering much better helmets for consumers. That will lead to much lower risk of these severe head injuries. We reduce the risk of suffering skull fractures or a fatal traumatic brain injury.
BIKERUMOR: One of the things that was brought up was that it’s not just the levels of standards but the tests themselves that are outdated. They were updated at a point where most people didn’t even wear helmets.
BAS: I can give you an interesting fact. With the cars on the street, they use these advanced dummies. They have sort of skin-like cover so they can really simulate how a person works. A head will have a skin layer and another layer on it with different properties to them to simulate a human head. In helmet tests, they still use steel head forms, which do not have these properties. We spoke to the original creators of these risk curves that we’re referring to, Dr. Prasad, he was telling me that in the late 60’s he wrote and article and academic paper on how helmet tests should incorporate these advanced biofidelic head forms instead of steel headforms. That’s almost fifty years ago. Lot of people agree, but it probably won’t change anytime soon.
BIKERUMOR: John, what’s the most horrifying thing you’ve learned in this process?
JOHN: The acceptable risk of injury on fully homologated helmets, and that the consumers have no awareness of this. If the consumer wants to do a good job and buy what they consider to be a safe helmet they’ll take $250, go to a reputable dealer, they’ll pick a brand they perceive to be reputable, it’ll be one of the top eight brands that we all know, they’ll get their helmet fitted. It’ll look good, feel good, maybe it will have good ventilation.
They will probably do as good of a job as they can at that point. They’ll choose a brand that has been around for a long time that they perceive knows how to build safe helmets but really there is no metric or data to share with the consumer that that is one of the safer helmets in the shop or not.
I think that the manufacturers have had a challenge because the marketplaces demanded until recently smaller helmets or lighter helmets or more breathable helmets, and that’s dictated what the manufacturers have been building. That’s what the demand has been from the consumers in the store. Even if the manufacturer wanted to build a helmet that is perceived to be safer or have a better performance level, it’s been very hard to communicate that to consumers in a understandable way which also doesn’t enter into some huge legal situation where perhaps they expose themselves to litigation because they are trying to do the right thing and inform consumers the difference in their performance to other helmet performance.
I think with our initiative it’s the first time to correlate the metrics that we’re using for recording the values, the energies, the peak g’s from decelerations, and also the HIC levels, and correlate them with the body of work from the automotive industry that has been validated, has been published, has been critiqued, but eventually implemented and standards built around, and fully accepted- it’s the first time to have this correlation which is now linked to this risk of injury. We have them for risk of a skull fracture, have them for the risk of a fatal traumatic brain injury, have them for severe traumatic brain injury, and I think this is something that manufacturers can now use to communicate the reduced risk of injury with a helmet that complies with these lower limits. There hasn’t been this mechanism or this framework that has allowed them to do it even if they wanted to. And I think now as consumers are more attentive and inquisitive about the safety levels of their helmets, I think this is an opportunity to align the manufacturers and consumers, actually.
BIKERUMOR: Why isn’t this change happening on an industry level? Why aren’t these standards changing, in your perception of things?
JOHN: It’s hard for me to give an answer to that. All I can say is that whenever we talk to people about changing and implementing standards, that’s a very long road to go down. It’s a road we will continue to pursue, but in the meantime these voluntary lower standards are something we can initiate now.
BAS: Imagine you have a manufacturer dusting off an old mold from 1997, and starting to build helmets again from this mold. It is perfectly fine to sell helmets like this again because they comply with the same limits. In that sense, it’s like we’re stuck in the ‘90s. We think consumers are not fully aware when we say: guys, we need a better helmet. That’s what we’re trying to achieve.
BIKERUMOR: That’s scary to me. A lot of vintage technology is interesting because of just how inferior it is, because of how far we’ve come technologically since when it was made. That analogy is frightening. I wouldn’t wear a lot of protective gear from the 90’s.
JOHN: How do you communicate this and bring people back to this European standard? I wonder whose idea was- we should put a brand new helmet next to a Sony Walkman. Yeah, this is when your helmet standard was defined, when we were walking around with Walkmans.
BIKERUMOR: I think of the early helmets I had, the early racing helmets…
JOHN: The fundamental construction is the same, isn’t it?
BIKERUMOR: The fundamental construction is the same.
JOHN: An in-mold helmet with EPS and a point whatever-it-is millimeter PC shell. The fundamentals of it are the same.
BIKERUMOR: The innovations have been in the structure- they’ve had the benefit of technology to simulate the structure of the foam. They can run analysis on it to meet the standards that are there with less material and better ventilation. Light straps. Better fitting. But you could wear a vintage helmet…
JOHN: If you remember back to the presentation- we can’t draw too too many parallels but the theme is correct- where you had the car from 1997 for the NCAP test and the modern car.
BIKERUMOR: That was bananas!

JOHN: It was very powerful because the car from 1997, the rear wheel is off the ground, the whole of the chassis is twisted, the front bonnet is compressed but it has also forced the wheels straight into the cabin, the occupant has gone straight through the window, the frame around the top of them is twisted. It’s not a pretty sight. And then the car from 2013, it still sat on the ground, the chassis isn’t twisted in any way at all, the bonnet is completely compressed so a lot of energy absorbed there, there is an air bag, and the occupant- you can see them not moved in such a dramatic way as the first car.
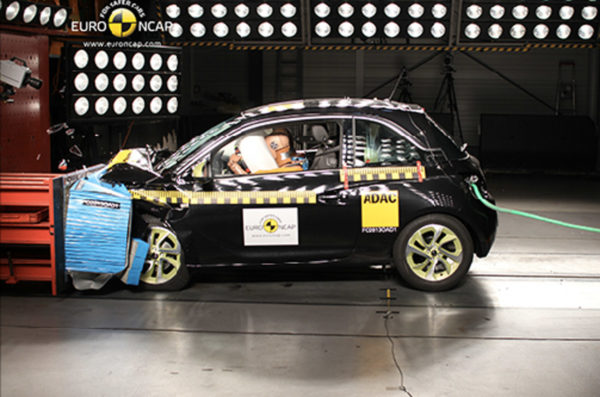
The automotive industry has progressed and has implemented on themselves lower acceptable limits because they are trying to reduce this risk of injury, and they’ve had a wholesale change in how they design the cars. We have not seen that in helmets.
BIKERUMOR: What has this whole process and exploration- what is your internal standard for your product when you integrate your technology into helmets.
JOHN: When we integrate Koroyd inside a helmet, we are always looking for a true innovative integration that enhances the experience for the rider. We’re not saying every helmet should always be the safest. They should always be safe. They should always perform well. But there are helmets where it is important to be the most aerodynamic, or where breathability is more important for some of these applications. We’re not saying that not every helmet should have the maximum maximum performance to reduce the risk of injury because that’s not what the market wants. What we are saying is that where we are majoring on the protective element, then we should make sure that we have lower levels of energy.
BIKERUMOR: It’s not like there is a rigid internal standard you’ve developed.
JOHN: And don’t forget that we’re always working in parallel with the brands, and we’re led by them and what their customers want as well. It is a true partnership in that way.
BIKERUMOR: Because you’re a material and a process but not the final product.
JOHN: Correct.
BIKERUMOR: What would you like the standard to look like, then? What would you like the world to look like from this exploration? Obviously, you could just sit back and go, our stuff is superior, but it sounds like you’re more alarmed enough that you’re talking about it on this level, talking about standards. You’re not just showing how far beyond your stuff is, you’re saying the standard is fucked.
JOHN: We definitely want to move away from some of the misinformation that consumers are facing and the more marketing-based claims that are made that for us raise more questions than answers, or are hard to justify or understand. What we are trying to do here is to have a completely transparent policy that consumers can be very well informed on, that manufacturers can support. Something which has the full transparency and gives the consumer more knowledge about the performance of their helmets.
BAS: What we are trying to achieve with this initiative, we’re not trying to set new standards. We’re saying why don’t manufacturers voluntarily comply with lower limits for acceleration? Why don’t they comply with 183g for maximum acceleration and 1666 for maximum HIC? From the risk curves developed by the automotive industry, that correlates with a less that 5% risk of suffering a skull fracture and a less that 5% chance of suffering a fatal traumatic brain injury. We’ve approached the original developers of these risk curves, to check that our initiative is indeed the correct way forward, and Dr. Prasad completely agrees and even voluntarily endorses our initiative has he believes it is the right way forward to start the process of continuous improvement within helmets, where it has been standing still for twenty years.
BIKERUMOR: You’re drawing a line in the sand.
BAS: Exactly. And hopefully in the future we’ll be able to continuously progress the safety level of helmets.