For sure, carbon fiber has been a huge boon for the development of lightweight, high performance bikes. But unlike the metal bikes before them, damage to a carbon component is not so easy to detect & their failure after being damaged is even harder to predict. So Belgian startup REIN4CED has developed a new type of carbon composite, reinforced with steel fibers. The new composite remains lightweight & flexible to build with, but results in a material with better impact resistance and improved integrity following local damage.
REIN4CED steel-fiber impact-resistant carbon composite
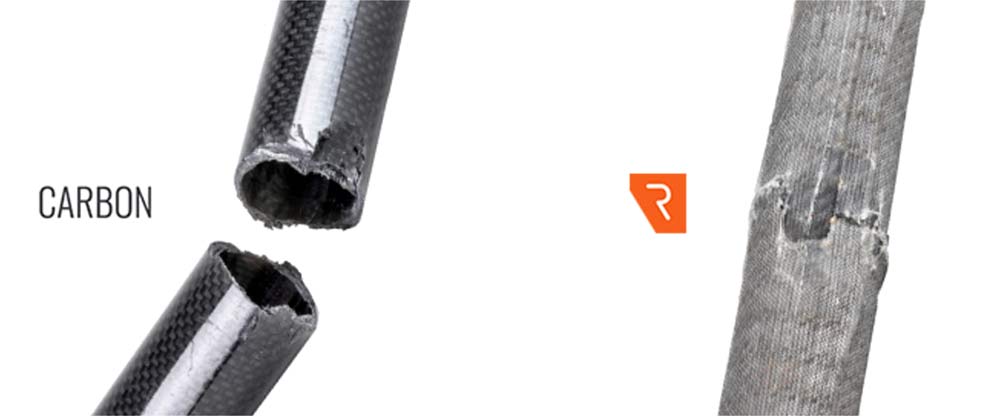
For many cyclists, perceived fragility and the often catastrophic failure mode of tradition carbon fiber remains off-putting. While carbon construction methods have improved by leaps and bounds over the last decade or so, we still occasionally see a carbon component explode or see one recalled due to increased risk of failure. Sure, for the most part failures result from specific crash damage. Or parts fail from stress beyond a component’s design intent, or sometimes just a manufacturing issue. But that fragility or ‘fear of failure’ has limited carbon application. And it has meant that carbon fiber seems less appropriate in the eyes of many cyclists for day-to-day commuting bikes or those expected to get more regular abuse.
So that’s where REIN4CED’s steel-reinforced carbon composite comes in. REIN4CED developed the material based on research into a more ductile and damage-resistant composite. The resulting steel-reinforced composite is much more durable than a typical carbon+resin composite. At the same time it retains light weight and similar structural characteristics. Put simply, REIN4CED inserts a small amount of “dedicatedly developed steel fibers applied on specific locations in the material”.
The result is that the new REIN4CED composite acts more like a metal following an impact than traditional carbon. Hit it with something and you get a local and visible dent that “barely reduces the frame strength”. With most of structural integrity intact, sudden frame failure instance should decrease. And damage becomes more easily detectable so a cyclist will know that a part needs to be repaired or replaced.
Building bikes from REIN4CED steel-carbon composite
The trick to it all seems to be the automated material production. Mixing the steel fibers into the matrix yields the added impact resistance benefit without significantly impacting weight or workability of something like a prepreg raw material. Conventional carbon production remains very separate of the actual product manufacturing. But, it seems that REIN4CED requires a more closely combined production process. So together with the material they have developed a fully automated manufacturing process that would start with the raw carbon, steel & resin materials and output the final frame or fork, for example. So they have already started to work with a few bike brands. And are now looking to ramp up some new European production soon.
The most recent news is that REIN4CED has just acquired a big influx of funding. They are now tasked with setting up their pilot production plant in Belgium in 2018, making what they are calling “unbreakable composite bicycle frames”