If you’ve ever set your air fork or shock’s suspension pressure, checked sag and then put the pump back on to make an adjustment, you’ve probably noticed things weren’t where you left them just seconds ago.
We’ve all heard that psssssst of escaping air as we’ve disconnected the shock pump. And when we put the pump back on the fork or shock and notice it’s a few PSI lower than what we just left it with, it’s easy to assume we’re losing a bit of air by removing the pump. Common sense then dictates we should put a bit more than we need into the chamber, that there’s something wrong with our pump, or something else. Which can be frustrating.
But don’t worry. There’s probably nothing wrong with your equipment, and it’s working the way it should. Here to ease your concerns is Cane Creek’s Andrew Slowey to explain how it all works…
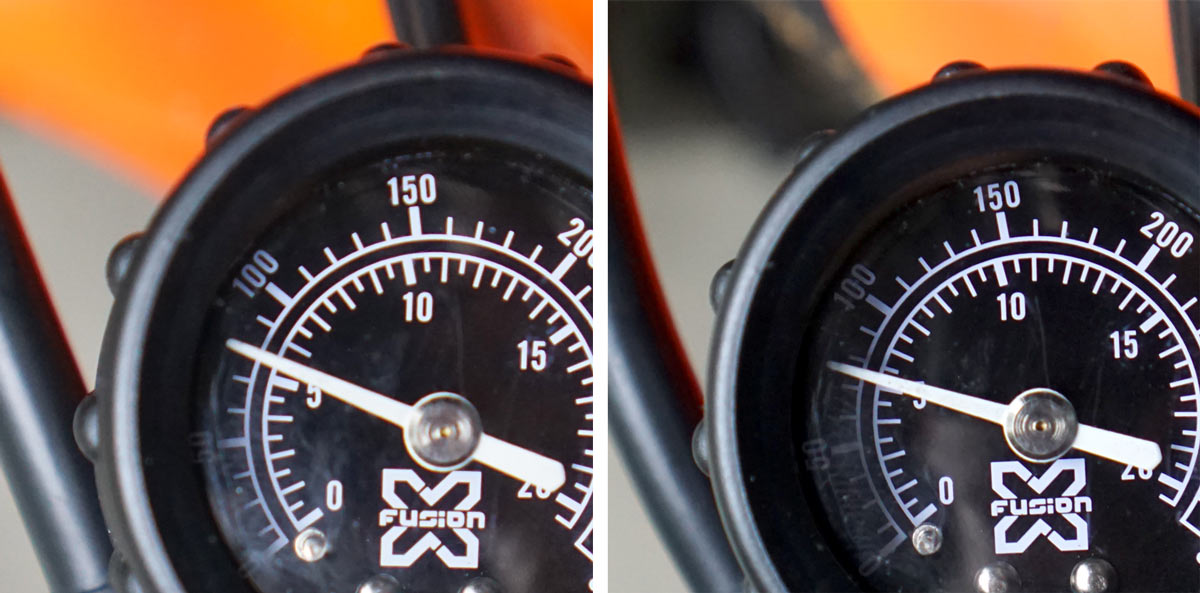
BIKERUMOR: How much air is actually lost when disconnecting a shock pump?
LUKE: If your air can’s valve is working properly, no PSI should be lost while disconnecting the shock pump.
The air you hear when disconnecting the pump is actually air from the pump’s hose. When you put a pump back on you lose some air pressure in the air can due to it charging the pump again. That’s why recording (i.e. writing down) your setup is important for riders looking to tune their suspension to suit their individual wants and needs.
BIKERUMOR: What’s the best way to remove a shock pump to minimize air pressure leakage when disconnecting the pump?
LUKE: Ensuring that your air valve on your air can and shock pump are clean and working properly. There is no special technique to minimize air leakage as this is a common misconception.
BIKERUMOR: So there’s no need to over inflate our suspension slightly to account for the air lost when disconnecting the pump?
LUKE: No, a properly working shock pump and air can valve will not allow air to escape the air can while disconnecting the pump. The air you hear when disconnecting the pump is actually air from the pump’s hose.
BIKERUMOR: Why don’t air forks and shocks have built in air pressure gauges?
LUKE: Building in a pressure gauge onto a suspension fork or shock would add extreme complexity to the overall design. The pressure gauge would have to be able to handle forces from 100psi to 1000psi due to the ramp of pressure during use and to get the precision as well as reliability needed would be very difficult.
How a Shock Pump Works
So, taking a look inside the valve, here’s why it won’t leak…assuming everything’s in good working order. For simplicity’s sake, we’ll refer to any air suspension as a “shock”, but you could replace it with “fork” and the effect is the same.
When the shock pump is threaded onto the valve, it creates a seal before the plunger is depressed to open the airway. Once the plunger is depressed, it lets air escape from the shock into the pump, filling its hose and gauge. Luke calls this “charging” the pump, and that’s what makes it seem like there’s less air in your shock than what you started with. We’re only talking a few PSI, but it’s enough to register.
When you’re done pumping up the shock and start to unthread the hose from the valve, the plunger moves back into the closed position (Fig. C) before the seal between the valve and pump’s head is broken, keeping all of the intended air inside the shock. As you unthread the pump’s hose further to remove it, that’s when the seal is broken and you hear the pressurized air escape from the pump’s hose and gauge.
The fun never ends. Stay tuned for a new post each week that explores one small suspension tech, tuning or product topic. Check out past posts here. Got a question you want answered? Email us. Want your brand or product featured? We can do that too.