thyssenkrupp’s Steelworks R&D team has won a Red Dot Award for a new automated technology shaping high-quality steel into complex shapes that are then machine welded to build premium lightweight bikes. Steelworks’ mission was to rethink how premium lightweight performance bikes are produced, and to develop a steel production process that could outperform both carbon & aluminum bikes.
Steelworks lightweight automated steel bike production
The German industrial Thyssenkrupp AG, who I know for making elevators, also happens to be one of the largest producers of premium steel sheet goods in the world as Thyssenkrupp Steel Europe. That explains why they are so heavily invested in developing new lightweight steel fabrication applications, and why the want to promote more EU manufacturing.
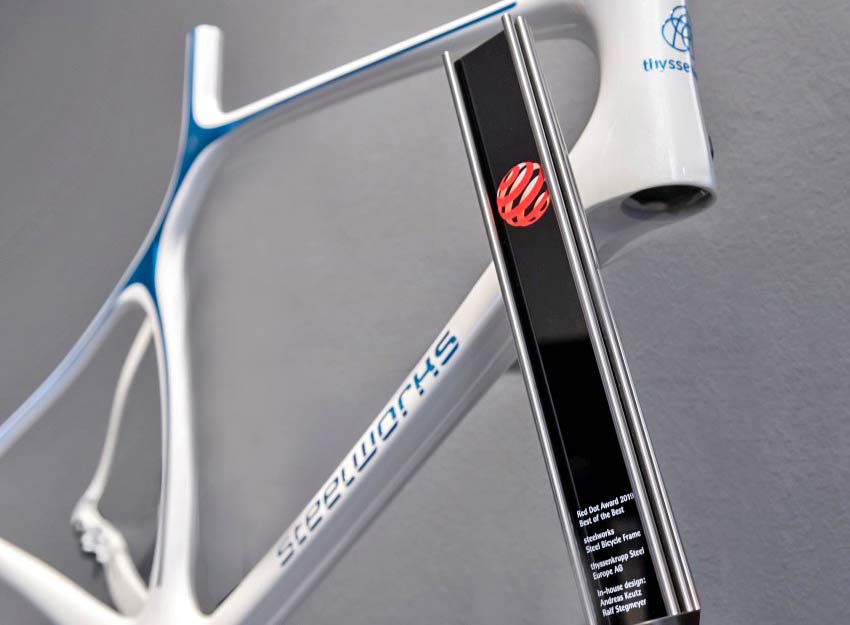
Setting out to revolutionize how bike frames are manufactured is a pretty lofty goal. But Thyssenkrupp Steelworks claim their new sheet steel process maximizes frame stiffness on par with carbon, while maintaining steel’s signature comfortable ride.
How will Steelworks innovation revolutionize bike production?
The new Steelworks bike starts with a technology similar to the stamping of steel used extensively in the automotive sector, crossed with the hydroforming that gives shape to aluminum tubing used in the cycling sector. With a single-sided mold, a sheet of high-quality, durable DP600 steel is placed over the mold and a pressure diaphragm deforms the sheet to match the shape of the mold. Excess material is cut away to create one half of the shell that will become the frame, then precise laser welding join the two halves together. I remember a number of monocoque-style alloy mountain bikes back in the 1990’s that did something similar, but never in steel of at the level of detail these images suggest.
By carefully designing the shape of the mold & its interaction with the diaphragm, Thyssenkrupp engineers are able to precisely control material placement, much like in a carbon layup apparently. Their thought is that they remove the impact of welds out of critical stress zones (like aluminum) and eliminate the occurrence of invisible impact damage (like carbon). The end result is that a machine manufactured steel bike can be built as light as aluminum, with the more beneficial properties of steel.
Tech details
Unsurprisingly, crafting a high-end steel bike is more complicated than simply welding together two halves. Not unlike what Pole is doing by bonding CNC-machined elements together to create a similar sandwich, it all comes down to how you solve the details. And Steelworks look to have those details dialed – dropped seatstays, semi-integrated seat mast, 12mm thru-axle, flat mount disc brakes, internal cable routing, tapered headtube with internal headset & a threaded bottom bracket…
As of now, Steelworks remain rather tight-lipped on the full details of their bike development, but they do promise availability later this summer 2019 which suggest they are quite far along. And test bikes are being road tested in the real world already now. Maybe we’ll find out more at Eurobike…