We know, there’s no such thing as a stupid question. But there are some questions you might not want to ask your local shop or riding buddies. AASQ is our weekly series where we get to the bottom of your questions – serious or otherwise. This time it’s all about hydraulic disc brakes! Hit the link at the bottom of the post to submit your own question.
Have you ever considered increasing your brake rotor size to get more stopping power from your hydraulic disc brakes? How much extra power will it actually give you? 220mm rotors are becoming common place nowadays, especially on 29″ downhill bikes and e-bikes where riders need all the stopping power they can get.
The experts at Shimano, TRP Cycling, Hope and Magura are on hand to answer this very question. They also go into detail on actual clamping force at the rotor, discussing the various factors that influence the final force values. The final topic of this week’s Ask A Stupid Question is the issue of sticky pistons. Why does it happen, and how can we maintain our brake calipers to prevent this happening?
How much clamping force do standard hydraulic disc brakes put on the rotor? Obviously this changes with the type of disc brake and the size of rotor, etc., but around what order of magnitude? Like 1 to 3 kNs, or more like 6-8 kN, or something else entirely? I have tried searching for this information elsewhere but it doesn’t usually show up on a technical documents and reaching out to manufacturers has been fruitless. I might have to buy one and use a force gauge to find this value experimentally.
TRP Cycling: To determine the clamping force from lever to rotor, there is the leverage and torque equation. It comes from the length of the lever and the distance from the lever pivot to the piston actuation rod, the basic mechanical advantage for the lever (MA = Fr/Fe = de/dr), the leverage ratio of fluid movement between the master cylinder and caliper pistons, the diameter and stiffness of the hose, and then ultimately your finger strength; i.e., how hard you can pull that lever to give the mechanical advantage.
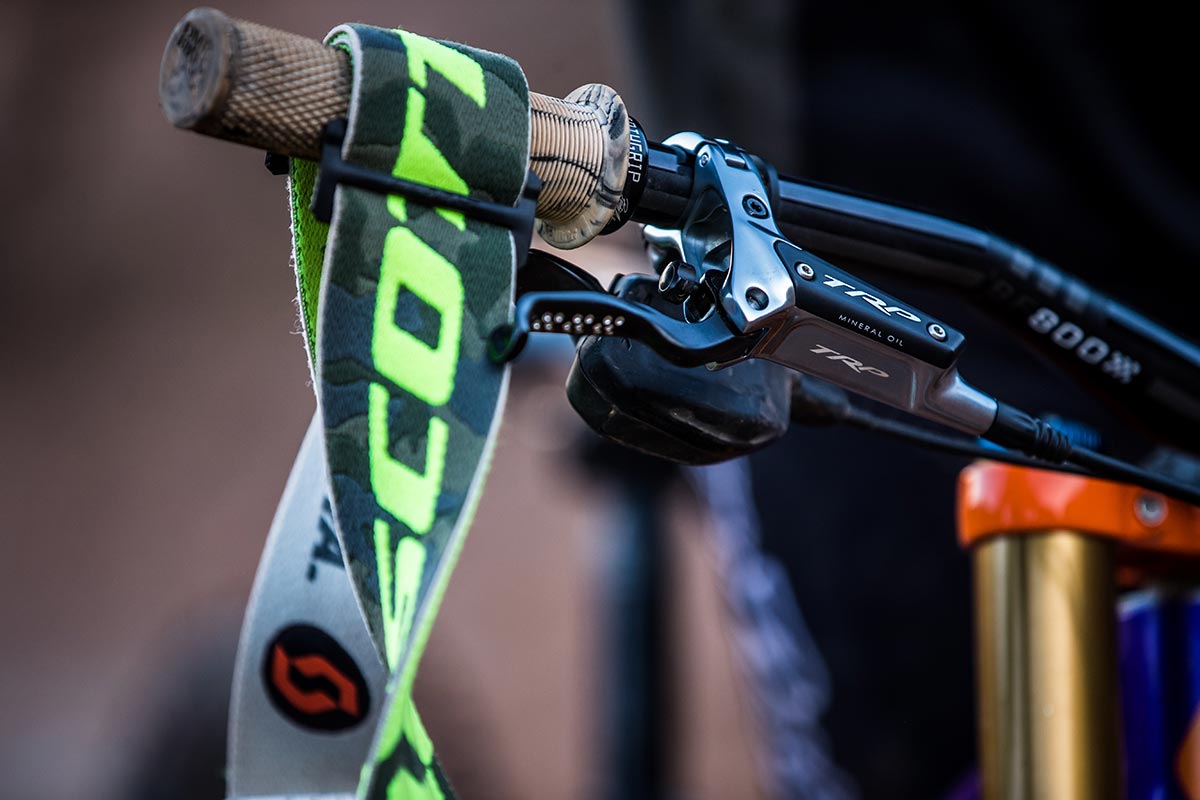
As you can see, there are many variables in determining actual clamping force making it different for every rider. So, it’s tough to calculate as an average. And this doesn’t include the most important part, the friction coefficient of the pads and rotors as all the force in the world will do nothing if the pads don’t bite. Meaning, a high force with a bad friction coefficient could produce lower braking power than a low force with a high friction coefficient.
Magura: As I understand the clamping force, it is the force with which the pistons or pads press against the rotor. So, it is independent of the rotor size.

The clamping force depends on the applied hand force. The more hand force you apply, the higher the clamping force. It also depends on the total ratio of the brake, which is the mechanical ratio (leverage arm from finger contact point to pivot point of lever blade divided by leverage arm from piston contact point to pivot point of lever blade) multiplied by the hydraulical ratio (surface of caliper piston(s) divided by surface of master piston).
For example, for the Magura MT7 with the HC-lever blade: mechanical ratio 5.8; hydraulical ratio 5.8; total ratio 33.6.
Now comes the hand force. Typical hand forces for average decelerations vary between 30N to 70N (1 Newton corresponds a weight of 0.98kg or 2.16lbs). Normal hand force is 100N.
If you apply a hand force of 100N, with the total ratio of the MT7 with HC blade of 33.6, a clamp force on the rotor of 3360N/3.36kN is achieved.
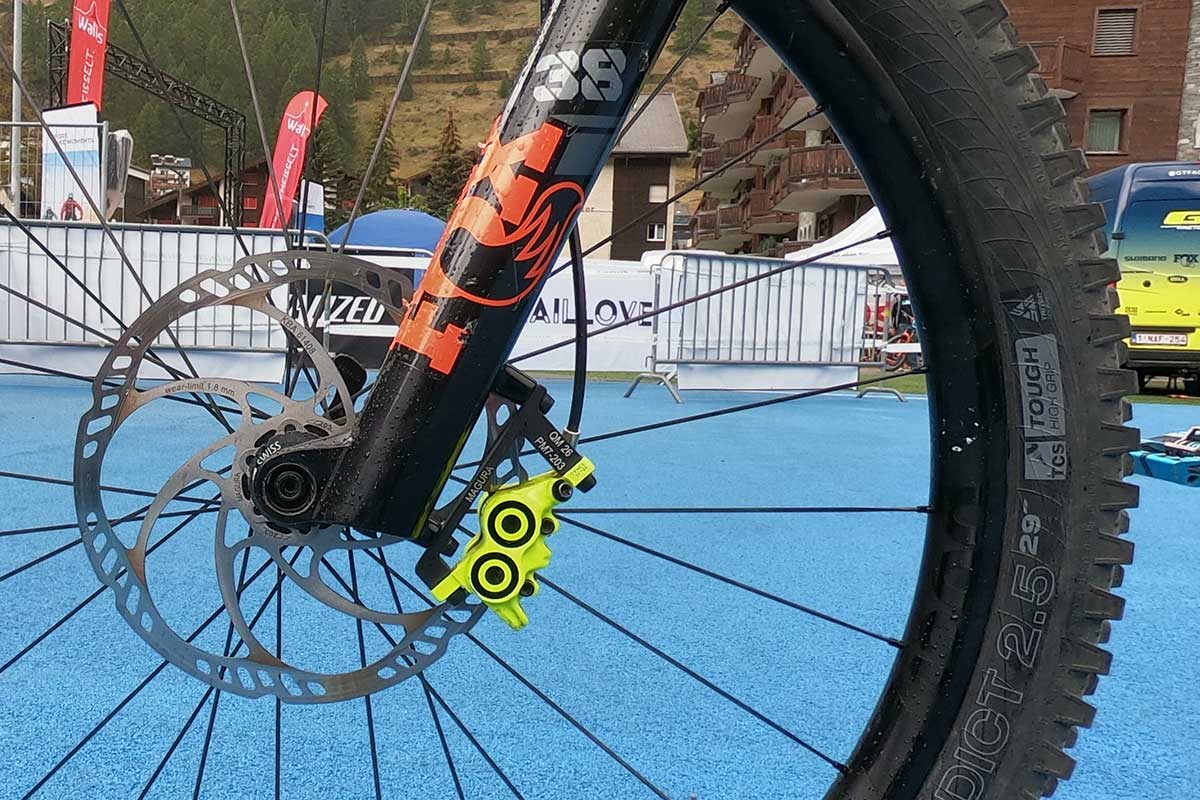
The resulting brake force, with which you can decelerate your bike, depends additionally on the friction coefficient of the brake pads and rotor, rotor size and wheel size, and on the mentioned total ratio of the brake and the hand force.
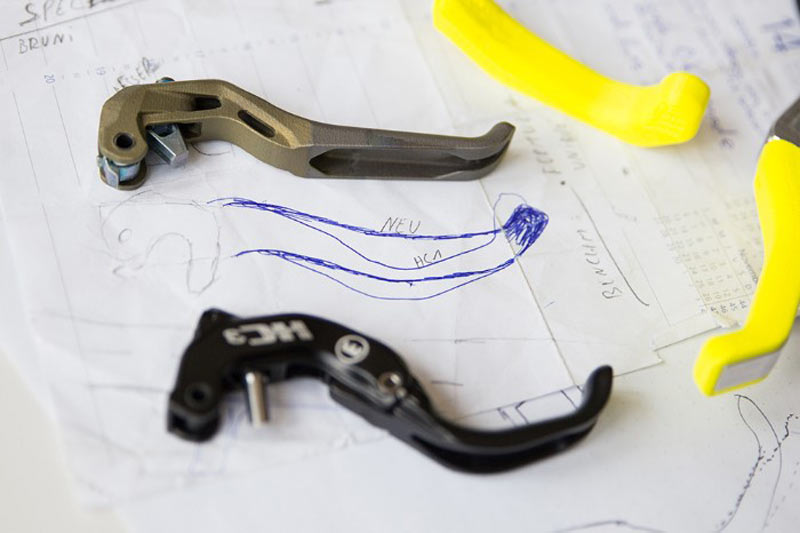
Clamping force on the Magura MT7 increases with the same hand force. If a longer lever blade is used, there is a greater mechanical ratio. Clamp force with for example, the older 2 finger blade with 100N hand force, increases to 3820N. But, the lever feel is different. It feels firmer on the HC blade and softer on the 2-finger blade with different feedback.
Hope: If we only consider the brake system without taking into account the disc, from a force applied on the lever we get a corresponding clamping force on the pads. For our current brakes, the ratio averages between 55:1 to 65:1. So, for example, a 50N force applied on the brake lever results in 2750N (50×55) on the pads.

I am thinking of upgrading my rotor size from 200mm to 220mm to get more powerful braking performance from my 4-piston hydraulic disc brakes. How much more power can I expect to get with the larger rotor? Is it simply a linear correlation or is it more complicated than that?
Shimano: The simple answer is that since 220 is 10% more than 200, you will get a 10% increase in power.
TRP Cycling: All things being equal, a larger rotor is basically a bigger lever to stop motion. The hub being the center of lever rotation, with a 220mm rotor over a 200mm rotor, you are grabbing the rotation with a 10mm longer lever (measuring the radius rather than diameter).
Therefore, a larger lever equals a larger mechanical advantage in stopping rotation. In theory this is a linear correlation, however, variables such as clamping force, coefficient of friction for the pads, and rider weight can all influence power output making it more complicated than that.
Magura: We calculate about another 10% more force added from the leverage advantage of a 220mm rotor vs a 203mm (20% from 180 to 203).
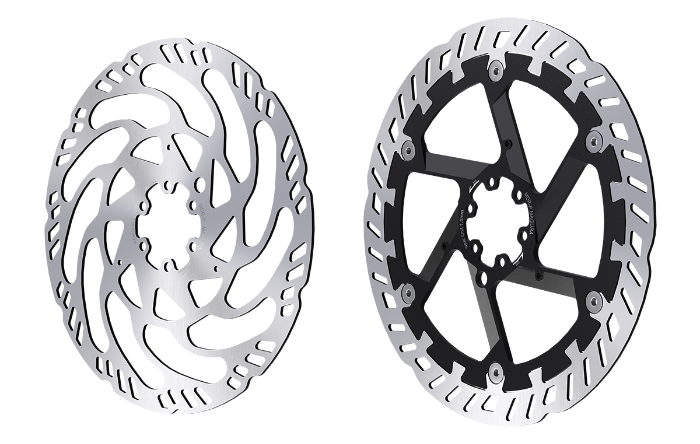
But, another thing to consider is the effect the faster moving rotor surface has passing by the pads versus the smaller rotor. Rotor speed makes a difference in initial feel when the pads contact the rotor because heat is built up quicker with a faster moving rotor. The downside is less modulation from a larger rotor!
Hope: If we consider that the braking force at the pads is the same, the generated braking torque with the larger rotor will be an increase dependent on the ratio between rotor sizes. Therefore, between a 200mm and 220mm rotor, the torque will be increased by a factor of 1.1.
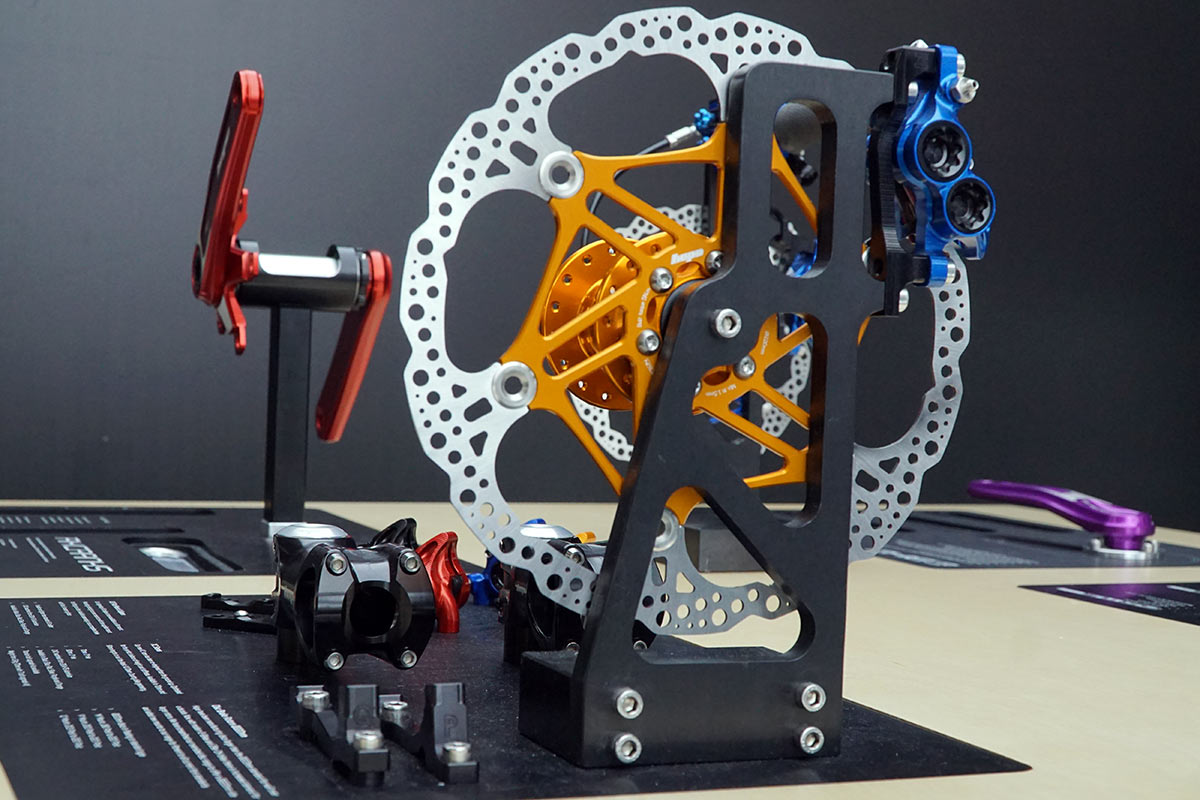
Please note that increasing the wheel size has the opposite effect because the leverage length between the tyre/ground contact to wheel axis gets longer. Therefore, on larger wheels, discs are getting larger too.
Why are sticky pistons in brakes such a prevalent issue? Specifically, I have struggled with pistons getting stuck in and out and the only effective way I have found to fix this is to rebuild the calipers and grease the seals/pistons with DOT grease. Then, of course, bleed the brakes. My brakes are SRAM Code Rs. I have a friend with less than a full season on Code RSCs with the same issue. Service intervals, in general, seem very short on hydraulic disc brakes. Why can my car go a few years without having to service/bleed brakes but mountain bike brakes seem like a yearly maintenance item?
Shimano: The service interval on car and bicycle brake fluid is similar when they are used in the same conditions. A typical service interval for a car is to check the brake fluid every two years or 30,000 miles with normal road driving conditions, but it drops to an annual check for off road use.
Shimano similarly recommends an annual check of brake fluid but it may last longer if the bike is ridden in cleaner conditions. Bike brakes can sometimes be more fussy than car brakes because we are asking bicycle brakes to completely retract from the rotor surface so that there is no drag.
In order for that to work, we need our brake caliper seals to predictably flex the same amount at every piston and then break free at the same time and let the pistons auto-extract as the pads wear. If one seal lets its piston break free earlier than the others, you’ll end up with a piston migration issue.
The contributing factors are seal flexibility and stickiness, piston material and surface treatment, and piston scoring and contamination from them working in dirty conditions. That’s why many mechanics will say the first rule of working with disc brakes is to clean the pistons before pushing them back into the caliper.
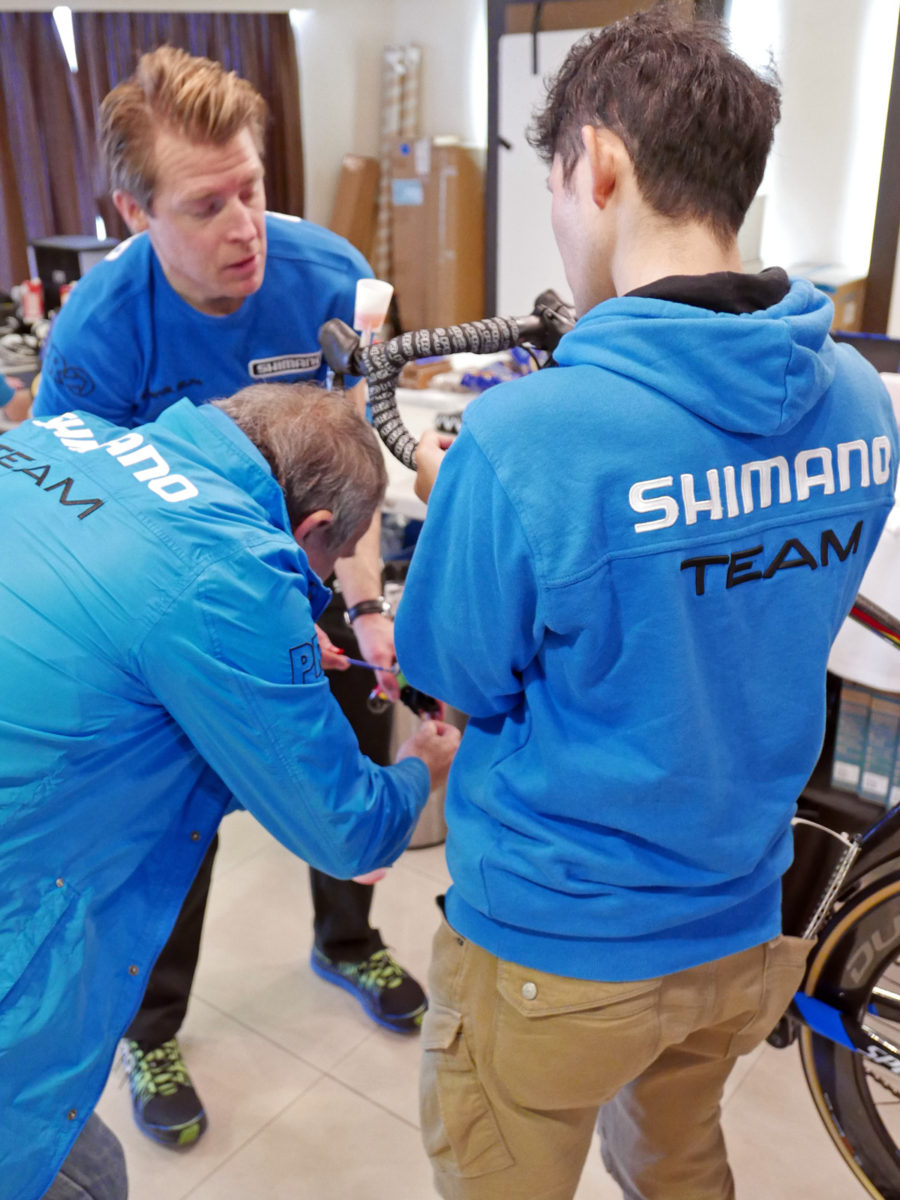
Any time you change pads, bleed the brakes, or simply re-center the caliper, the pistons should be cleaned. One of the benefits of a mineral oil brake system is that we have some freedom to play with the piston and seal materials.
In the past we’ve used different surface treatments on alloy pistons to match seals that can behave more predictably, but our biggest breakthrough was the shift to ceramic pistons on our current performance brakes.
Since they are harder, resist scoring, and allow a better seal material, we saw a big drop off in the frequency of piston migration problems. Every part of the brake system has a give and take to it though and each brake manufacturer makes different decisions about what they think are the most important characteristics.
TRP Cycling: Sticky pistons are a natural result of usage over time. Their frequency can vary depending on the conditions you ride through and the construction materials of your caliper.
Ultimately, a sticky piston is caused from either the seal drying out or contamination blocking the smooth action of the piston. On the internal side of the seal you have oil and on the external side you have dirt, grime, and dust. Fixing a sticky piston is actually quite simple as all that is required is basic cleaning and lubrication of the pistons while still in the caliper housing. It is outlined in this TRP Service Video:
Your car gets sticky pistons as well, but there are much larger forces acting on your car compared to your bike, making contamination and the drying out of the caliper seals more difficult. With an engine, cars can rely on power to drive weight meaning their calipers can use a more robust build with heavier caliper halves, more oil, and heavy seals.
This, combined with all the mechanics that sit between a car caliper and your foot, like hose size, fluid volume, master cylinder size, power assist, and what shoe you decided to wear that day, means you just won’t notice the sticky pistons as much.
In relation, because human powered bicycles don’t rely on a 200+ hp engine to drive motion, higher tolerances and different materials are needed to create a lightweight system capable of single finger cylinder movement.
The use of light action seals naturally allow for easier contamination when riding primarily in dusty or muddy off-road conditions, and because all drag on a bicycle brake is felt through the sensitivity of a fingertip, you will feel it much more frequently compared to a car.
Magura: Sticky seals refer to the interface of the square sided caliper seals called quad rings and the caliper piston surfaces they interact with. The relationship requires proper lubrication for pad adjustments so when the brake pad thickness wears slightly, the caliper piston is able to “slip” toward the rotor in order to make up for the reduced pad thickness.
The benefits are many but the main benefit is that the lever blade engages in the same position every time.
When a brake sits unused (OEM bike in shipping, warehousing, sitting on the sales floor, hanging in the shop or even riding scenarios not requiring hard braking) the pad doesn’t wear so therefore the adjustment described above doesn’t happen in time enough to let the caliper pistons and seals “slip” and bring fresh fluid with it.
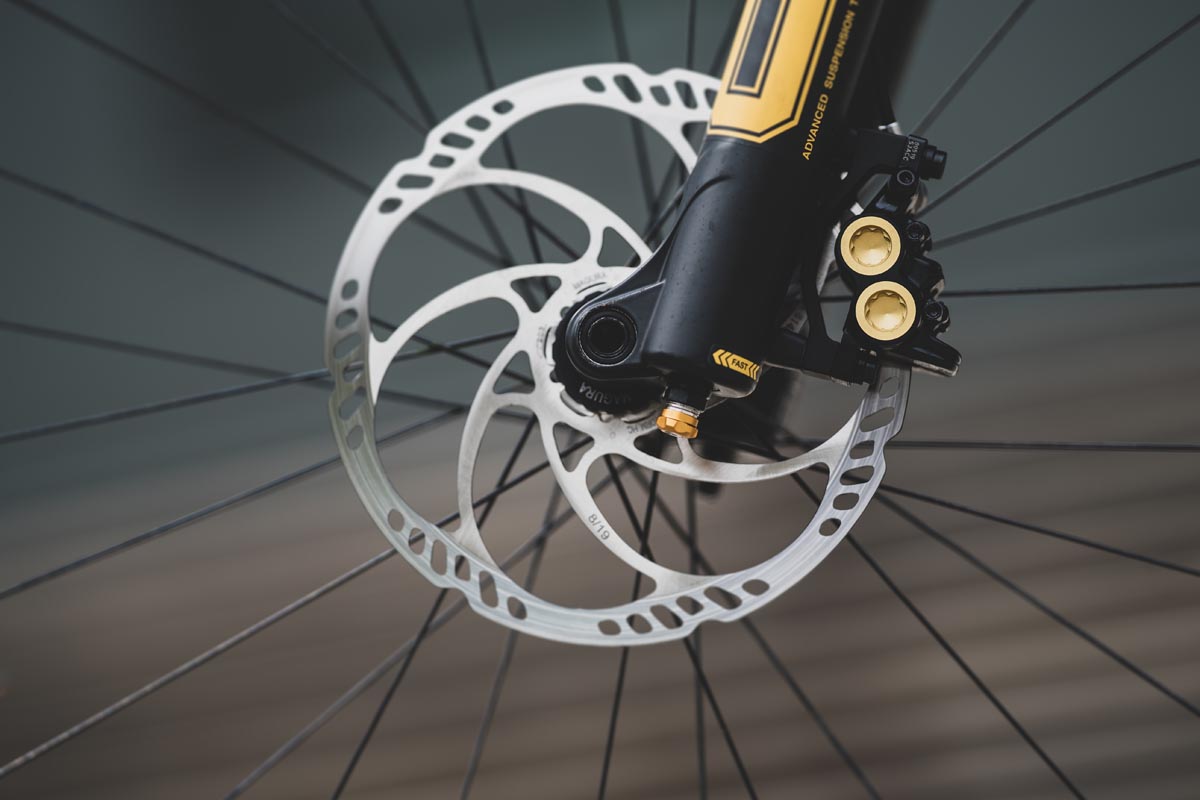
The seal/piston interface therefore continues to dry and not receive fresh internal fluid as the required lubricant. Then, as the pad wears and the slip doesn’t occur, then the quad ring has a firm grasp on the piston and contorts more and more to make up for the missing pad material. This exaggerates the lever’s travel and can be confused as requiring a bleed.
Passenger car components are massively overbuilt and very slightly stressed versus MTB hydraulic disc brakes which are on the highest end of the performance spectrum. They are minimally overbuilt saving valuable weight, yet they are massively over-stressed. Adding to the problem is the lack of engine braking.
Think of a Toyota SUV brake versus an Indy Car brake. One has the ability to add weight, passengers and pull a trailer up and down mountain passes and last 20 plus years whereas the Indy car has to deal with the heat, forces and duration for only a short period of race time and for a short life span (i.e. half the race season).
A more realistic comparison to an MTB brake system would be a “factory level” moto or car brake system which requires frequent bleeds, perfection with caliper alignment but have very short component lives.
Hope: Depending on the environment, the usage and piston material used, pistons can get “sticky”. The best way to maintain them is by lubricating them with silicon lubricant which is harmless to seal material (for both DOT and Mineral systems).
Gently pumping the pistons out and lubricating them should be sufficient without going to the trouble of rebuilding the brake, bleeding, etc. You can see how to lubricate pistons in this tech video.
On a car, everything is much larger and better protected, so it is less affected by heat and dust, mud. And, you normally love your MTB more than your car so it definitely requires more TLC!
Why does my rear brake need to be bled more frequently than the front brake?
Shimano: There’s nothing inherent to a rear brake that would require more frequent bleeding. However, rear brakes can be more difficult to bleed because of the caliper angle and house route. It could be that there is simply still air in there from the last brake bleed. You may also notice an increase in sponginess in a rear brake more easily because the longer hose also adds some sponginess to the lever feel.
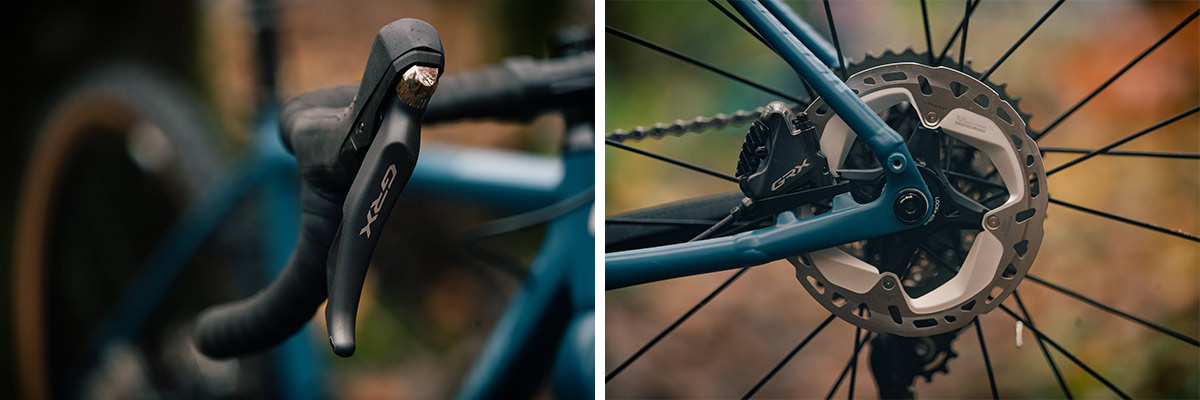
TRP Cycling: A rear brake shouldn’t need to be bled more frequently than the front in terms of reliability, but it will feel different from the front because of the larger length of hose. A longer hose has more fluid movement and introduces more hose flex naturally leading to a slightly more spongy feeling.
Magura: It shouldn’t. However, typically, the rear brake receives much more usage, heat and abuse versus a front brake so therefore heat is the culprit.
Hope: Normally, the system should only be bled once a year, maximum. If this is required more frequently the problem usually comes from somewhere else. The quality of the brake fluid will deteriorate over time but taking into account the rear brake usually gets hotter, this repeated increase and decrease in temperature will make the fluid properties deteriorate faster than they would in the front brake.
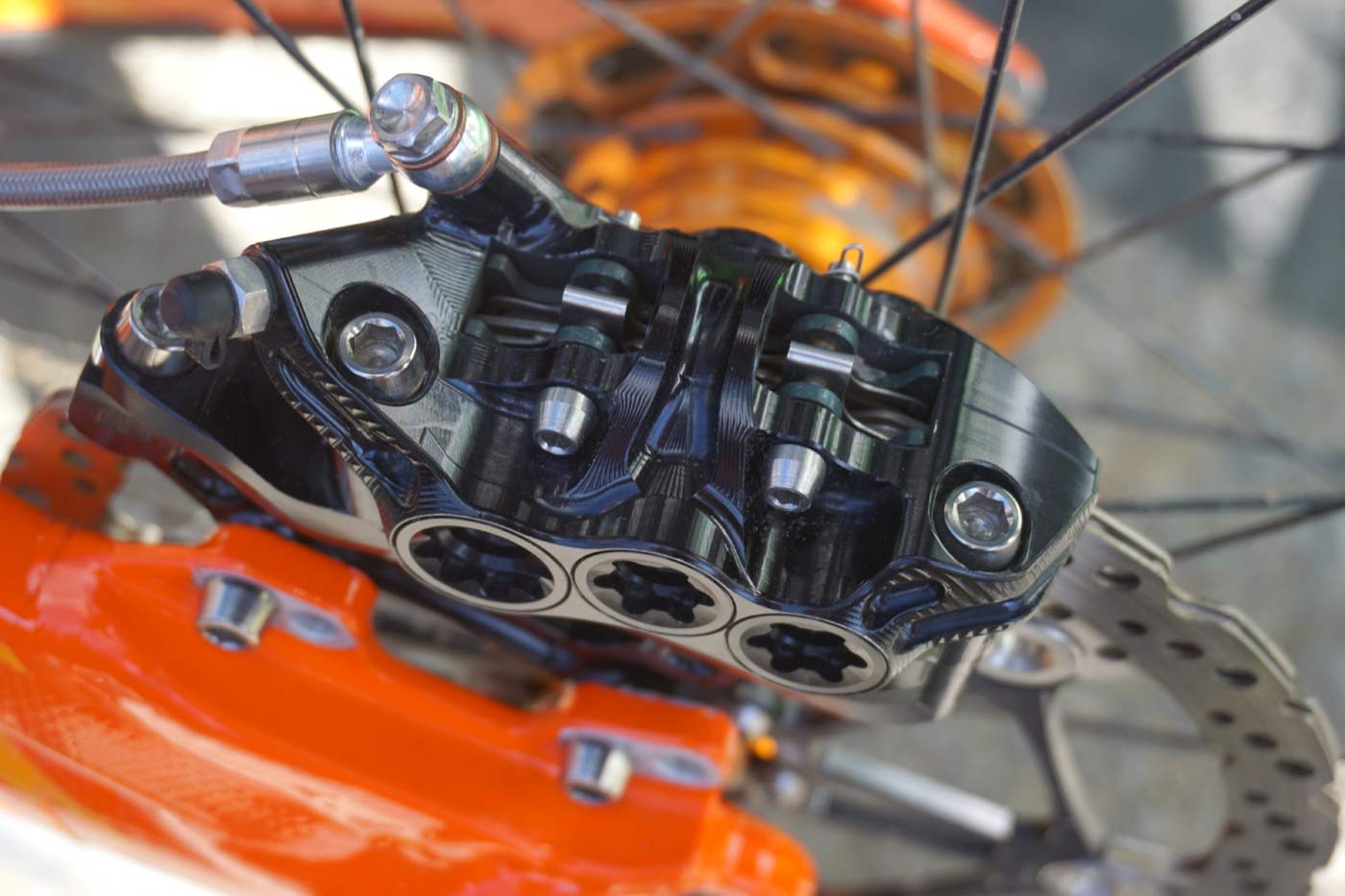