How much do you really know about your bicycle helmet? Hopefully, you know that it fits well and looks good, and you may have an awareness of some of its fancier features, like its rotational impact protection technology, its dual- or single-density EPS, its retention system adjustability, and so on, but what do you really know about how it has been tested, and thus how it might behave when you take a knock?
All bike helmets need to be certified for sale in most parts of the world, and each region has different rules for that certification. A helmet goes through fairly rigorous testing to demonstrate its ability to dissipate impact energy away from the wearer’s skull, at least in the case of linear impacts. Every brand is subject to those tests without exception.
For MET, the standard safety test procedures simply aren’t rigorous enough. The Italian Helmet manufacturers therefore take matters into their own hands, at their own test laboratory, to ensure their helmets not only meet the requirements for certification, but go way above and beyond them.
To get an insiders look at helmet design and testing, we’ve teamed up with MET Helmets to lift the lid (excuse the pun) on the mysteries surrounding it all. We go into detail on the mandatory shock absorbing test procedures carried out for CE, CPSC/US, AS/NZ, NTA, and ASTM certification, explaining what each one is for, and we also take a closer look at the extra-curricular stuff MET is doing to ensure their helmets are offering top notch protection to the crashing rider.
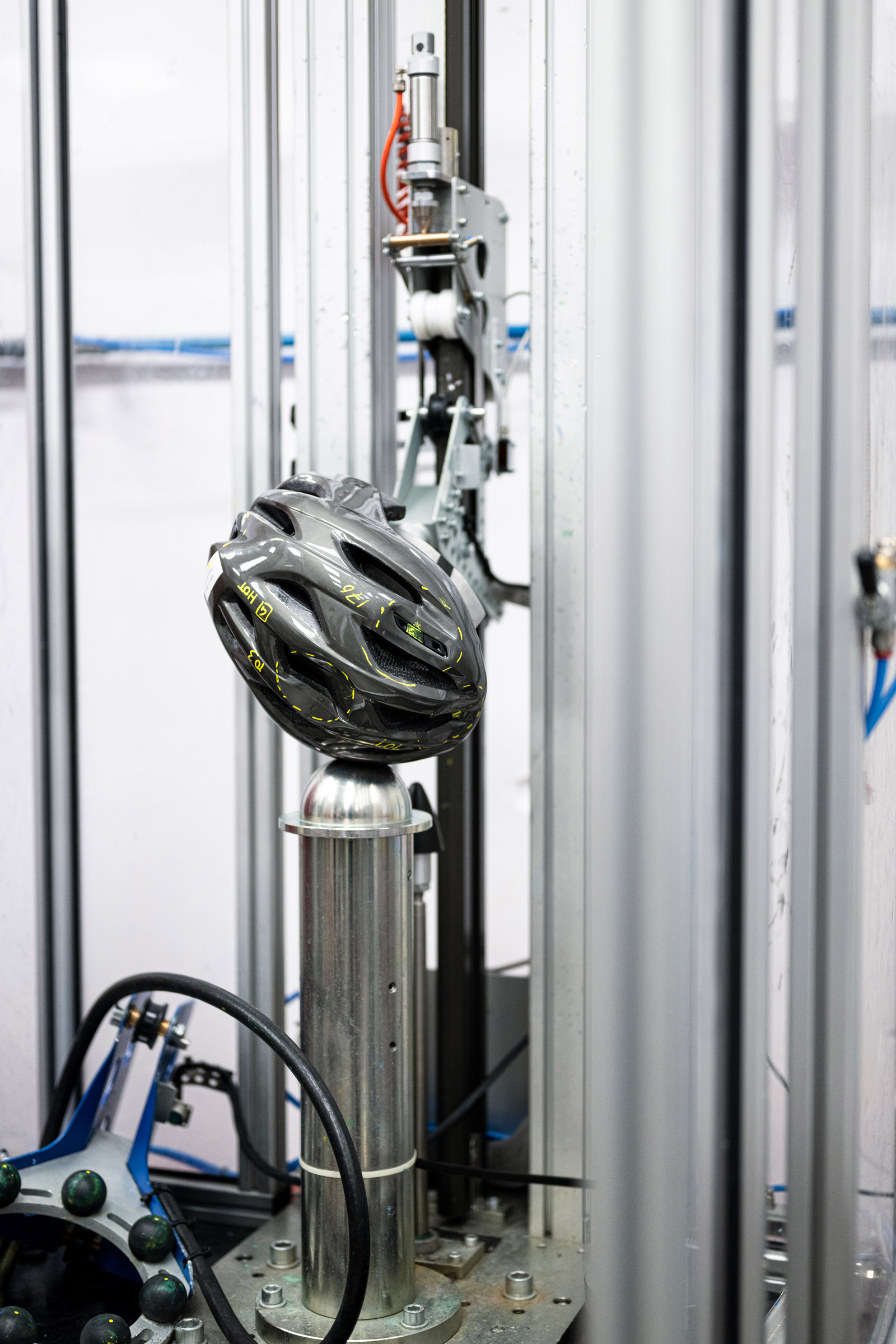
All photos are credited to @ulyssedaessle and @met-helmets, unless otherwise stated
What safety tests do bike helmets undergo?
The short answer is, it depends. Where you are in the world will determine the safety requirements that your helmet had to meet before it was certified for sale in that region.
It is interesting that the powers that be, those who govern what the specific helmet safety requirements are in the different regions, make no distinction between road, gravel and (open face) mountain biking helmets. Beyond passing the basic tests set out by the relevant certifications (EN, CPSC, AS/NZ, NTA, ASTM) the hones is upon the manufacturer to over-engineer their helmets to go above and beyond in the name of keeping riders as safe as possible in the event of a crash.
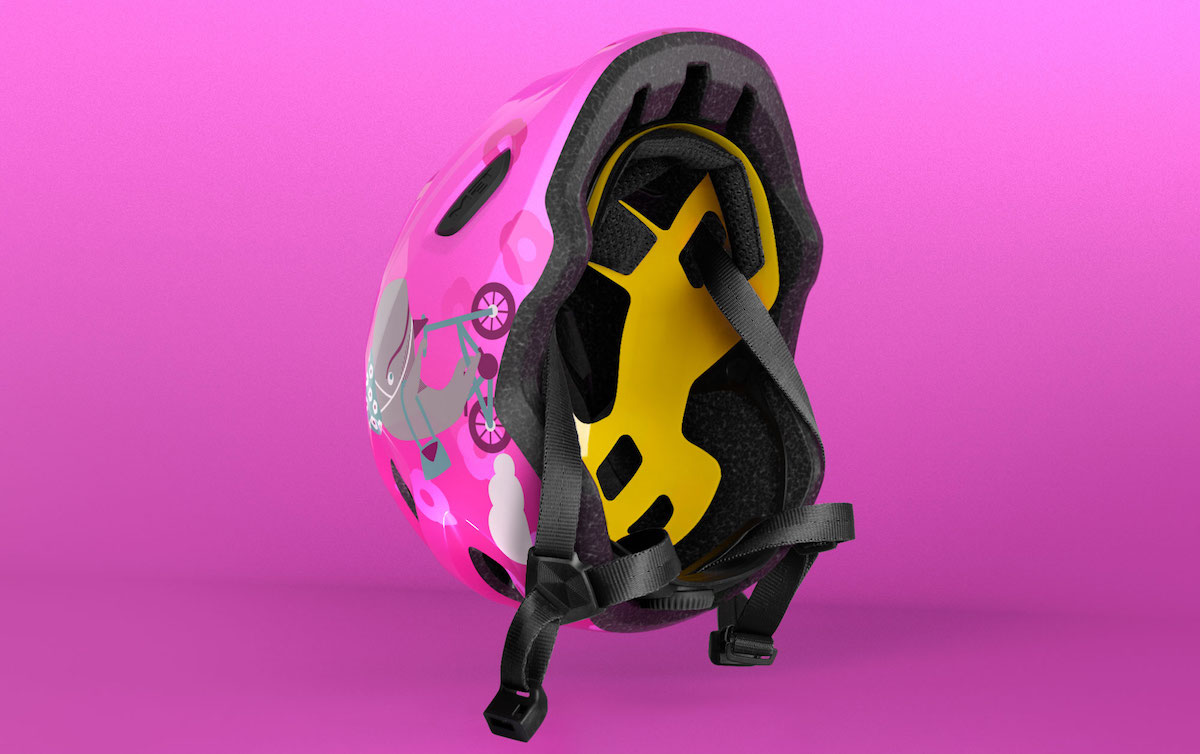
And most do, of course, often adding various rotational impact protection technologies, dual-density EPS, and adding extended coverage to the rear to confer more protection to the occipital portion of the head – a feature seen more commonly on mountain biking helmets.
Italian-brand, MET Helmets, is one of those manufacturers. The reason they are able to go the extra mile with helmet safety is because they have their own testing laboratory at their HQ in Talamona, near Lake Como. Before we get into that, let’s take a closer look at what the mandatory helmet safety tests look like, and what is required for official certification in different parts of the world.
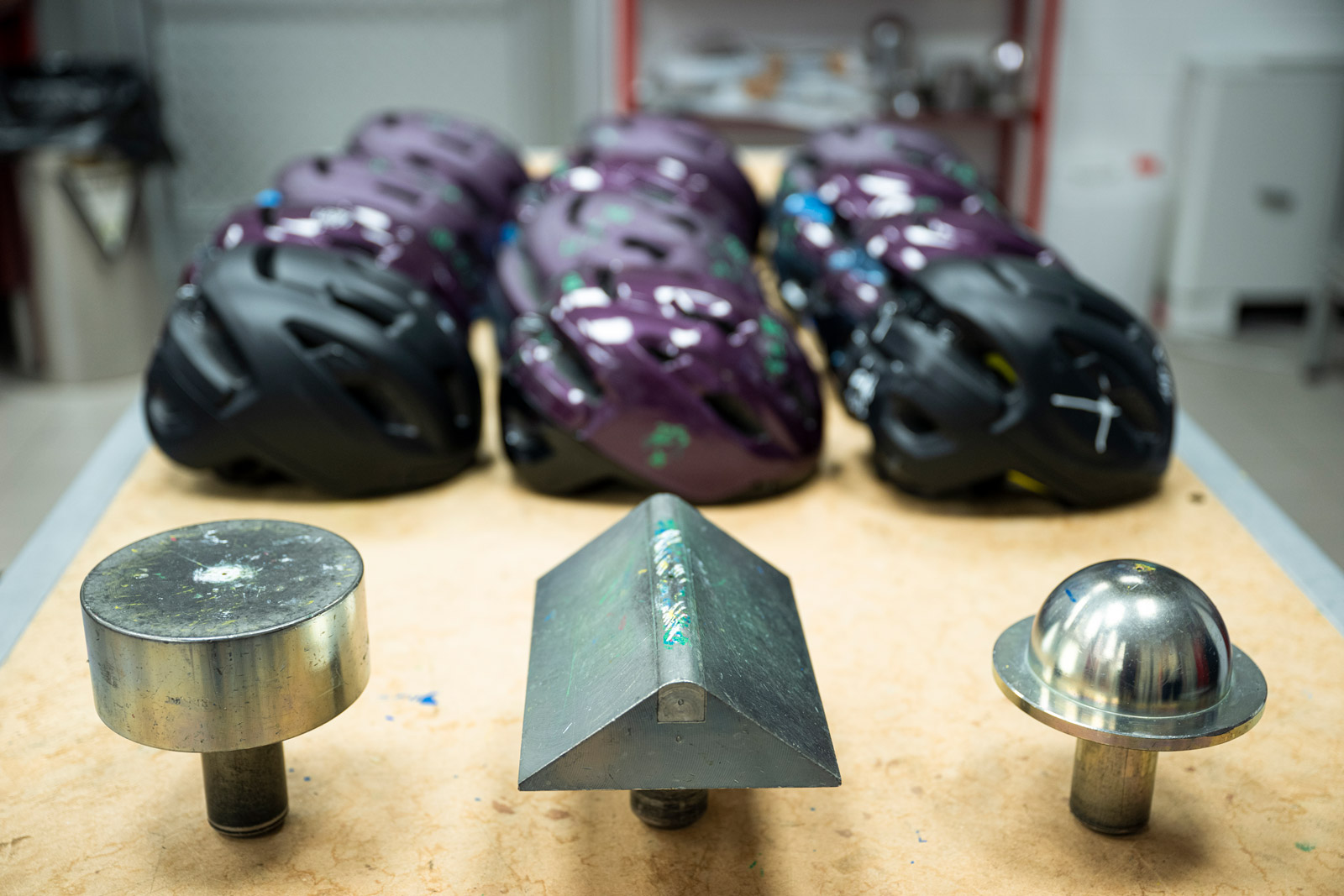
Helmet Safety Certifications & Test Result Minimum Requirements
EN 1078 / Europe (and most of the world)
In any test, the absolute limit for energy transmitted to the head during an impact is 250 g. That is measured using a tri-axis accelerometer, with each helmet receiving two impacts – gnarly crashes can easily involve more than one blow to the head. The tests make use of two types of anvil – the object the helmet is colliding with when dropped from a mono-rail drop tower. In one of the tests, the helmet is dropped onto a flat anvil from a height of 1.5 meters. In another, the helmet is dropped onto a Curb-shaped (pointy) anvil from a height of 1.07 meters.

These tests are carried out under a variety of conditions; cold, hot and ambient temperatures, after a period pf being sprayed with water, and after a period of UV exposure, all to simulate the conditions helmets might see out on the road or the trail. Moisture and UV radiation can expedite the degradation of EPS, hence the inclusion of those conditions in the test. The tests carried out for certification in other parts of the world are very similar, but they have slightly different requirements in terms of how much energy is permitted to be transmitted to the rider’s head during an impact.
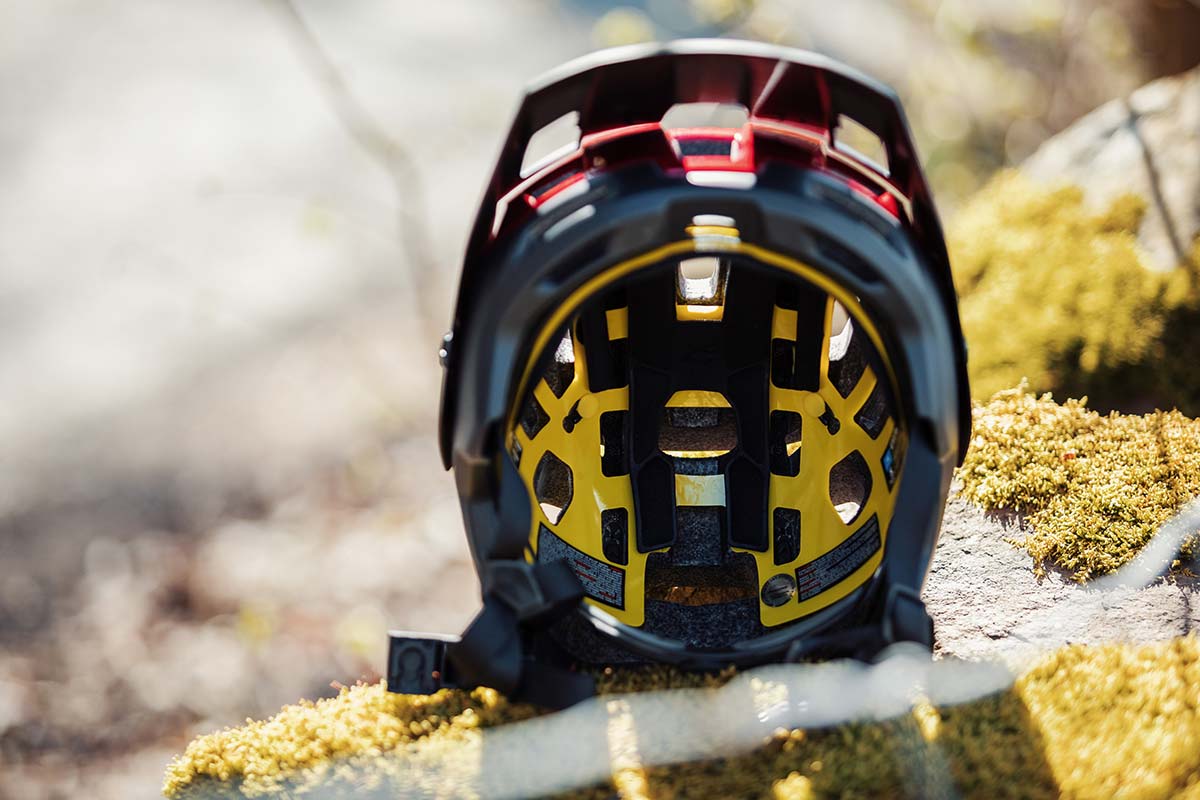
In addition to Linear Impact Testing, MET also carry out Rotational Impact Testing of their helmets at their in-house laboratory in Italy. This goes above and beyond what is required by the various safety certifications listed here. While MET test this aspect of their helmets’ protection properties in-house, they also submit many of their helmets to the independent helmet testing facility at Virginia Tech.
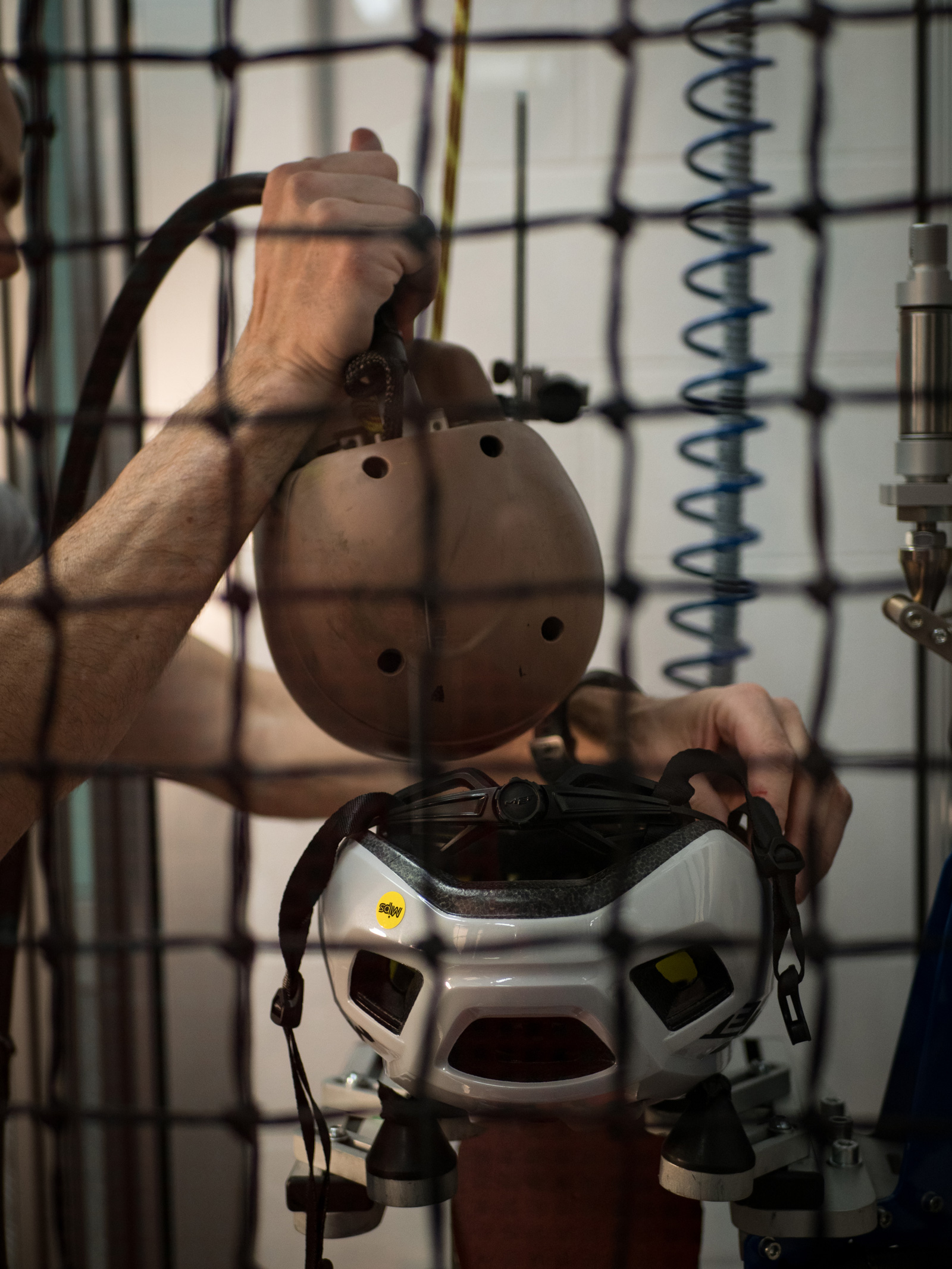
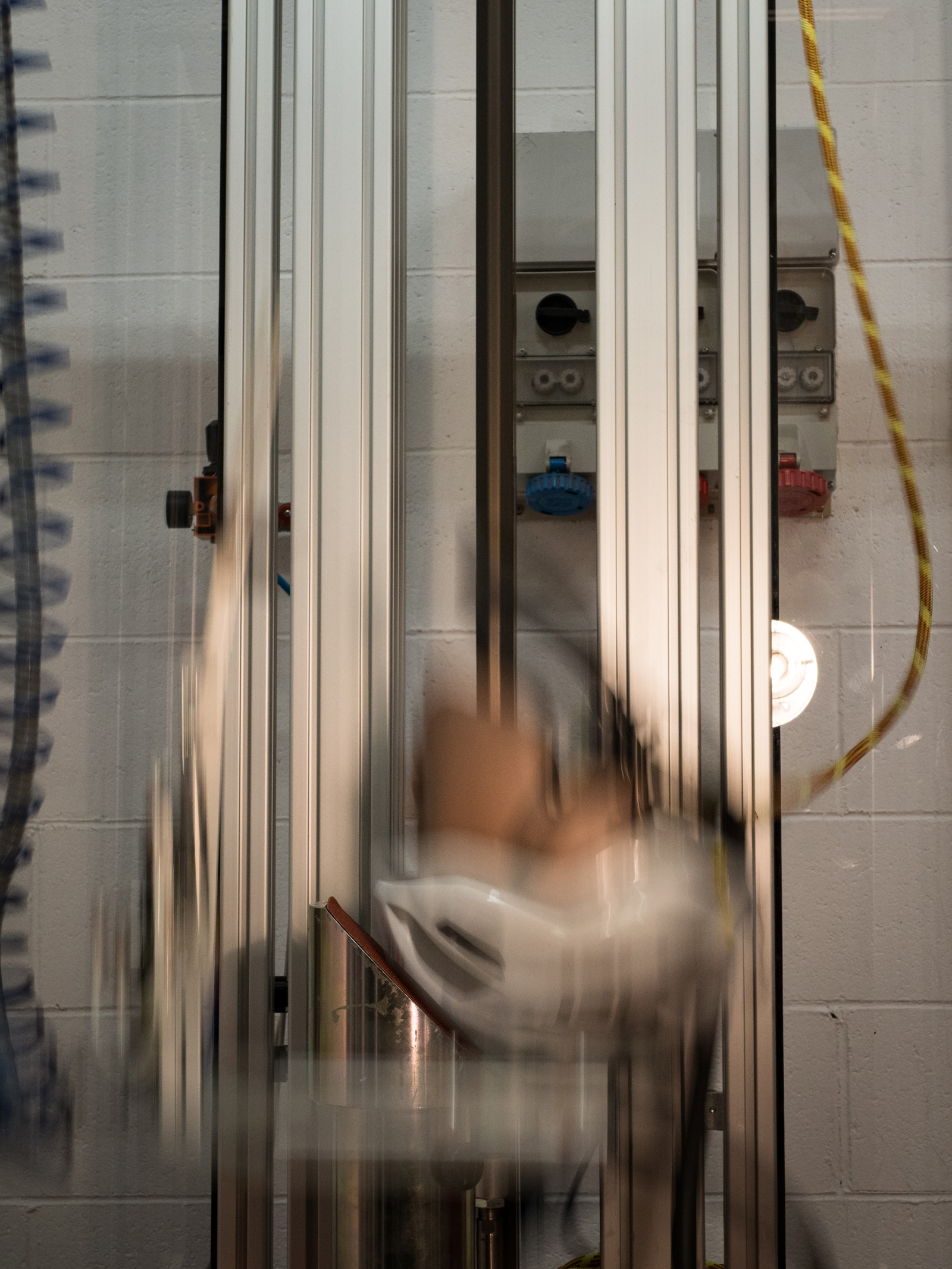
CPSC/USA
Tests carried out for CPSC / USA certification are as follows:
- Helmet dropped onto a flat anvil from a height of 2 meters (video below)
- Helmet dropped onto a curbstone and hemispherical anvil from a height of 1.2 meters
- 4 Impacts per Helmet Tested
- Energy limit transmitted to the head during any single impact is 300 g, as measured by a linear accelerometer
- Conditions tested include cold, hot, and ambient temperatures, as well as one wherein the helmet is tested after immersion in water for 4 to 24 hours
AS/NZ
Tests carried out for AS / NZ certification are as follows:
- Helmet dropped onto a flat anvil from a height of 1.5 meters
- Anvil dropped onto the helmet that is fixed on a force transducer – from a height of 1 meter
- 4 Impacts per Helmet Tested
- Energy limit transmitted to the head during any single impact is 250 g for flat impacts, 500 N for the force transfer test with a curbstone anvil
- Conditions tested include cold, hot, and ambient temperatures, as well as one wherein the test is carried out post immersion in water
ASTM Certification for Full Face Helmets (1952-15 for DH MTB and 2032-15 for BMX)
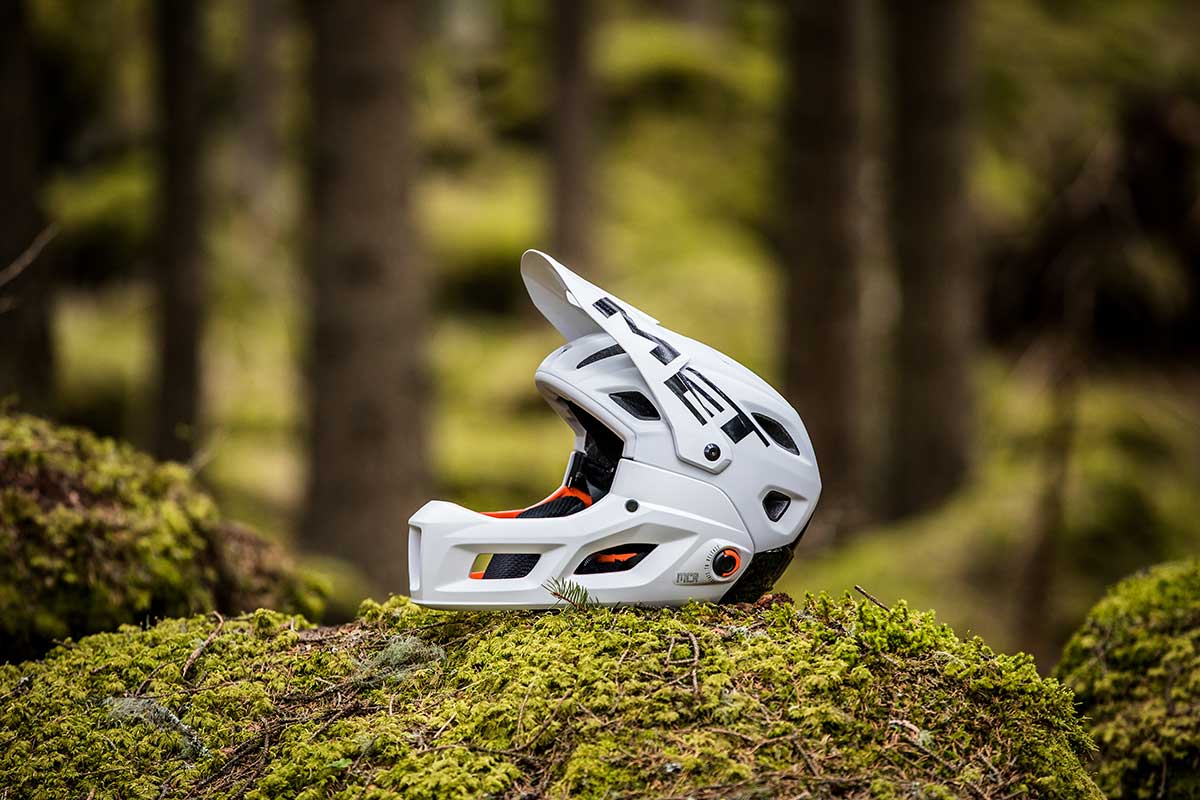
This US Certification is made specifically for assessing Full Face Helmets that are often required for Enduro or Downhill Mountain Bike Racing, or BMX Racing. The test assesses the safety of both the main body of the helmet and the chain bar, and is a little more comprehensive as such.
The tests for ASTM Certification are split into two categories; one for the main body (shell) of the helmet, and another for the chin bar.
Tests for the shell:
- Helmet dropped onto a flat anvil from a height of 2 meters
- Helmet dropped onto a curbstone anvil from a height of 1.7 meters in ASTM 1952-15 for DH MTB Helmets; drop height is 1.3 meters in ASTM 2032-15 for BMX Racing)
- Helmet dropped onto a hemispherical anvil from a height of 1.7 meters in ASTM 1952-15 for DH MTB Helmets; drop height is 1.3 meters in ASTM 2032-15 for BMX Racing)
- Energy limit transmitted to the head is 300 g, as measured by a linear accelerometer
- 4 impacts on the shell, per helmet tested
Tests for the chin bar:
- Helmet dropped from a height of 40cm onto a flat anvil
- Limit of the deformation admitted on the chin bar is 60mm
- 1 impact per helmet on the chin bar
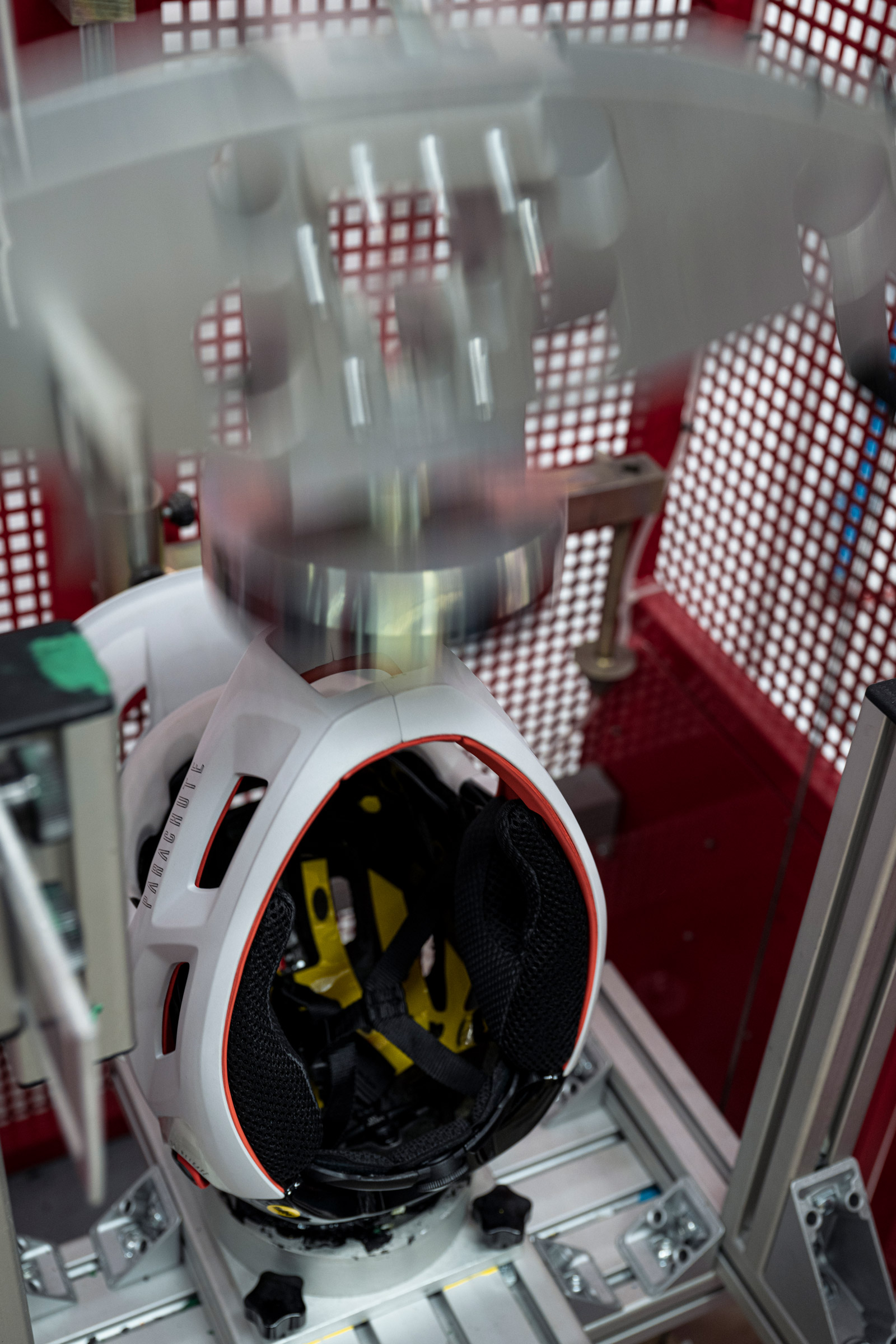
NTA 8776 (not mandatory): Certification with a higher impact speed
There is another CE Certification called the NTA 8776 standard. It is a relatively new Dutch standard created for helmets of speed pedelec riders, where the speed pedelec is capable of providing assistance up to speeds of 45 kph. In these tests, the impact speed is increased in line with the faster average speeds associated with riding those bikes.
- Helmet dropped from a height of 2.15 meters onto a flat anvil
- Helmet dropped from a height of 1.5 meters onto a curbstone anvil
- Energy limit transmitted to the head is 250 g, as measured with a tri-axis accelerometer
- 2 impacts per helmet tested
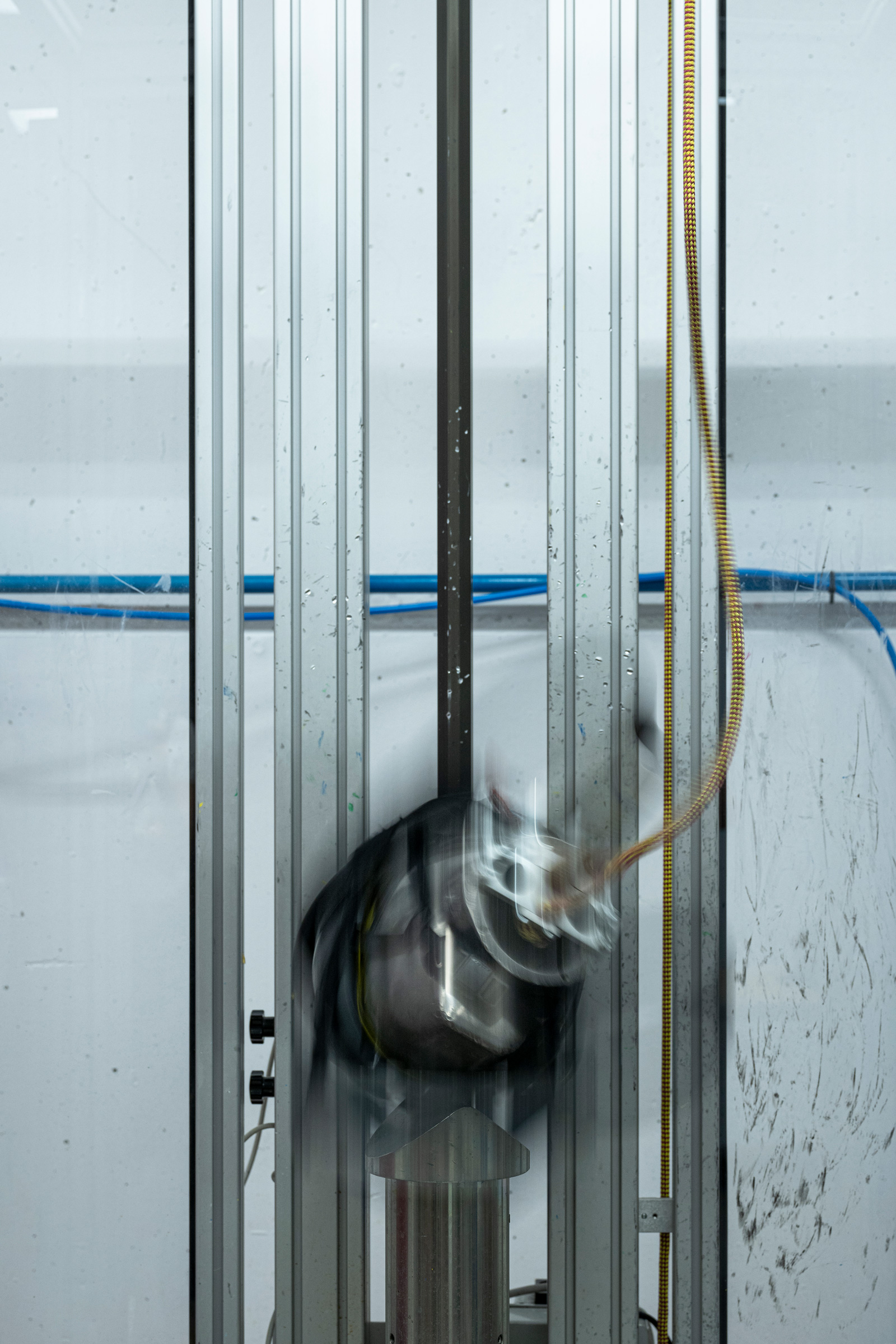
Helmets submitted for NTA Certification are tested under a variety of conditions; high temperature (+50° C 4-6 hours), low temperature (-20° C 4-6 hours), and artificial ageing (UV at 125 W for 48 hours plus water spraying for 4-6 hours).
So, how do manufacturers make sure their new helmet designs will pass the necessary tests?
Designing a Safe Bike Helmet
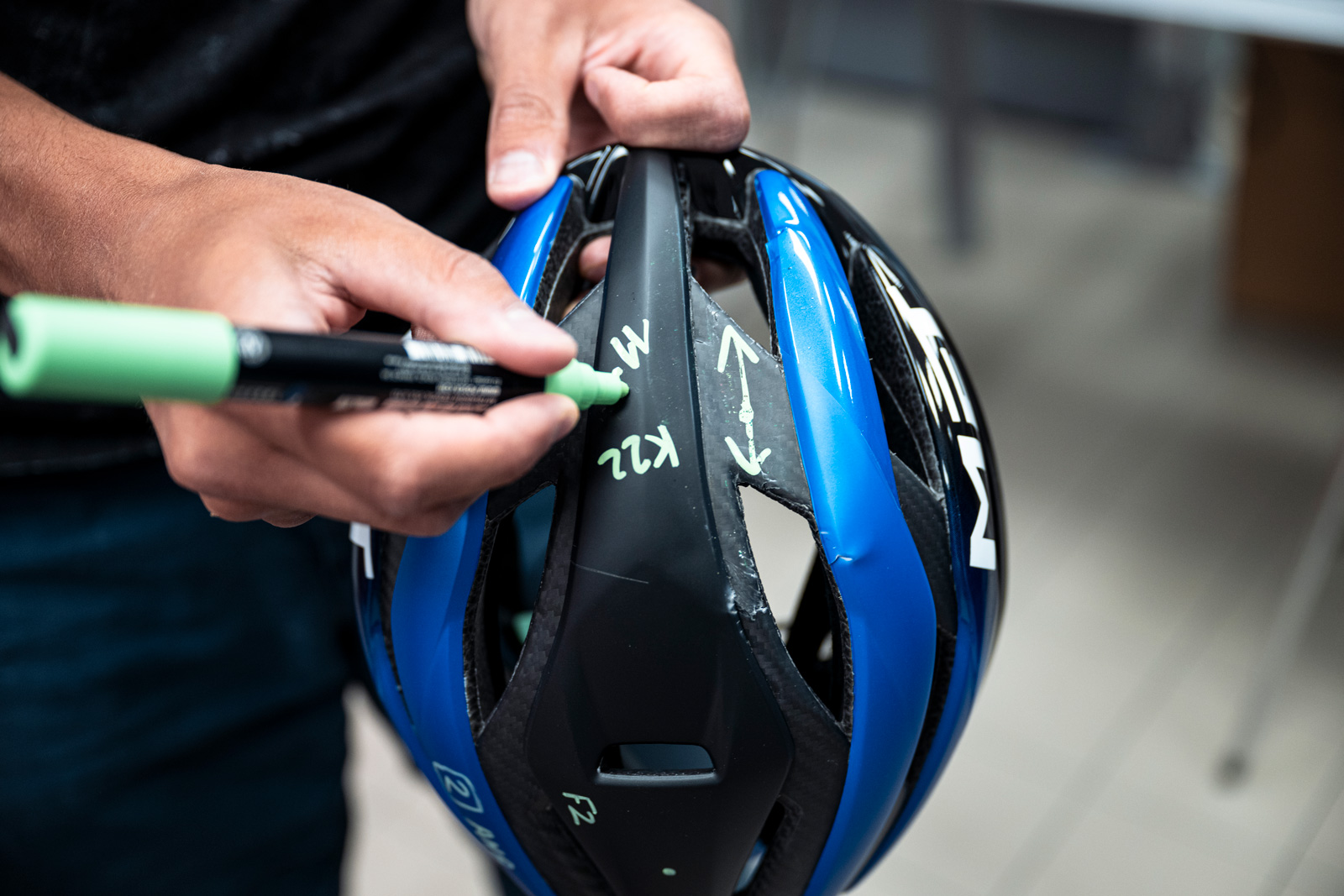
The process of designing a helmet varies between manufacturers. Some start with 2D drawings, and then create a 3D sculpture of the helmet to approve the design and validate its shape. The issue with that approach is that, sometimes, the structure of the final helmet fails laboratory testing, and the manufacturer must start the helmet design again from scratch. Ulysse of MET Helmets tells us they take a different approach that does, of course, involve 2D-drawings and 3D-sculptures, but also relies heavily upon computational modelling prior to the creation of any costly tooling or actual manufacture.
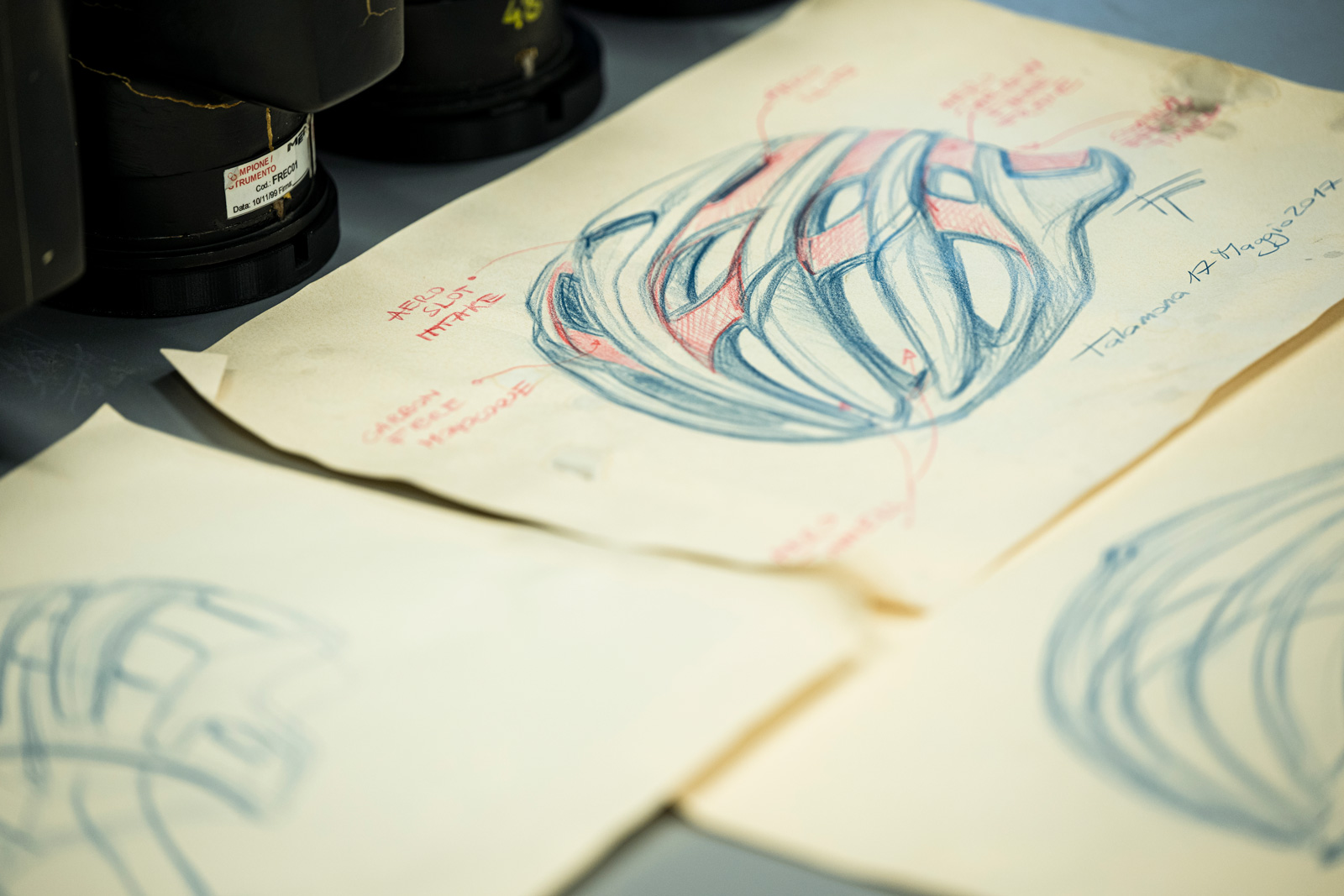
At their R&D facility in Talamona, the MET Helmet designers are able to go straight from the drawings and sculptures of the new helmet model, and plug them straight into modelling software that is able to simulate impacts with a high degree of accuracy. It can simulate a nigh-on infinite number of scenarios varying anvil shape, impact speed, impact force, temperature, humidity, all while tweaking the structure of the helmet to make it as robust as possible.
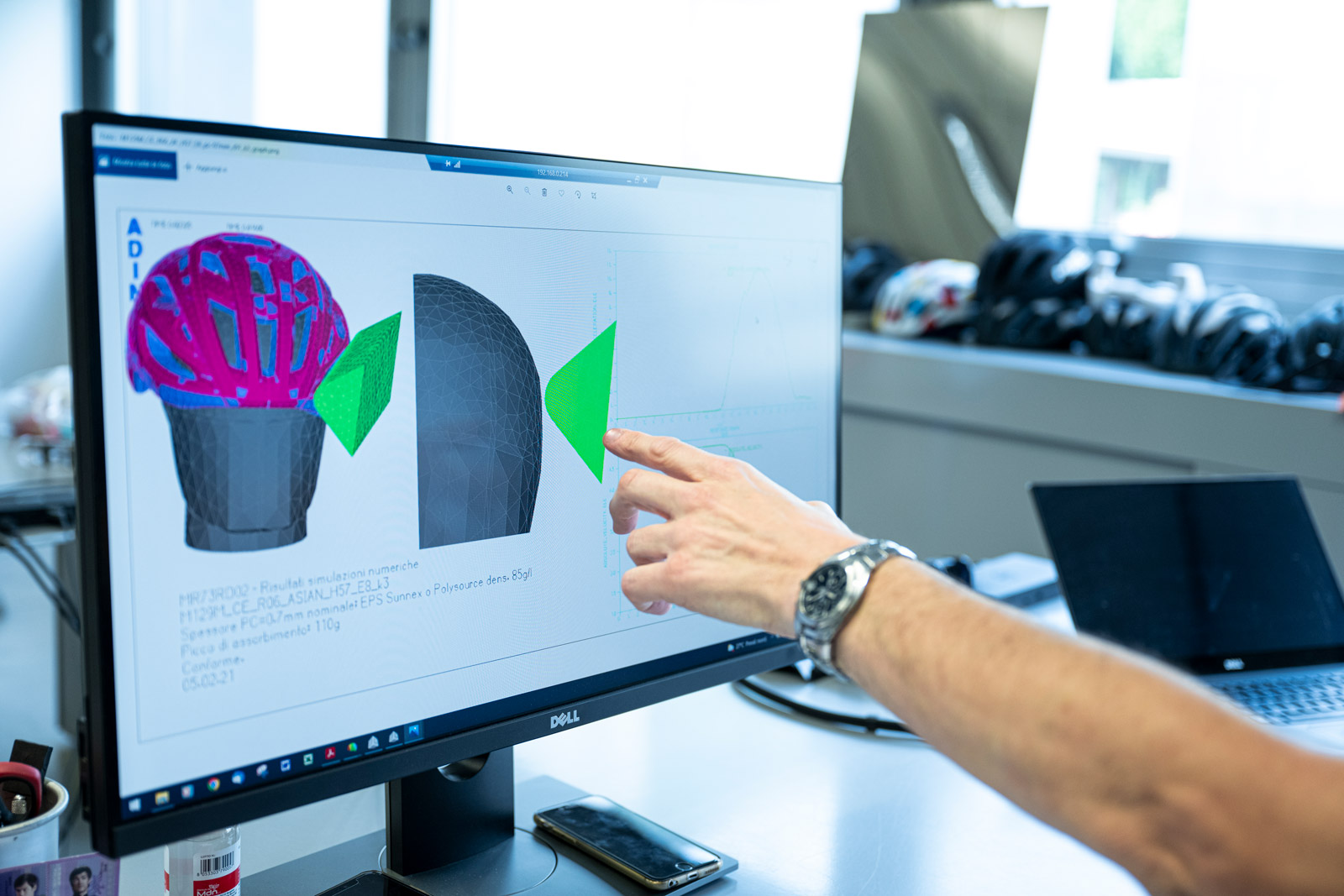
The computational algorithm used by the R&D team is based on millions of data points collected from thousands of real helmet safety tests carried out at the MET Testing Laboratory. Data collected from every test is used to improve the robustness of the computer modelling, making the process of designing each new model of helmet more and more streamlined.
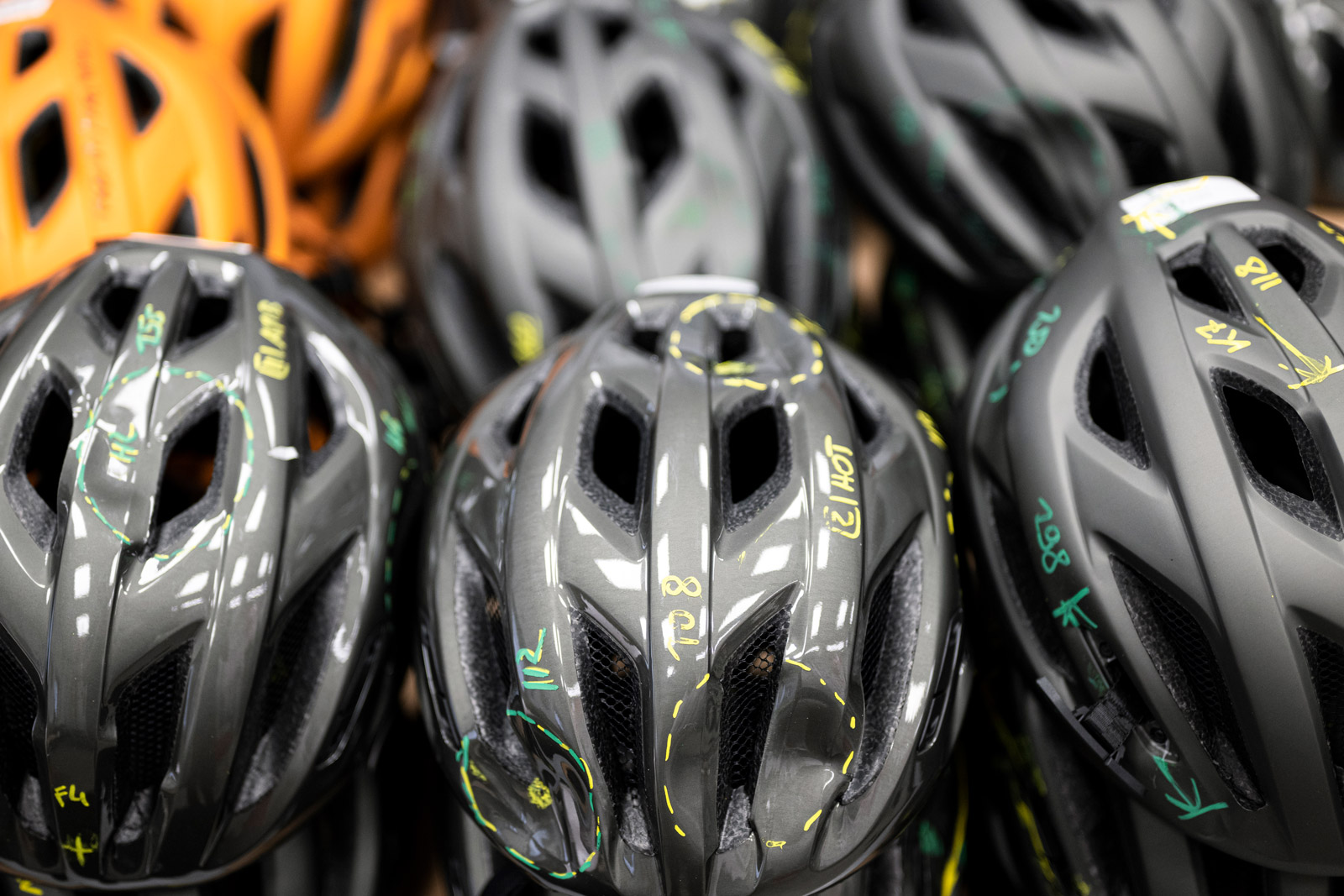
Through their own in-house testing, MET discovered that, while a helmet can pass the safety requirements set out by the Certifications mentioned above, that same helmet may also permit the anvil to come into contact with the wearer’s skull, or get very, very close to it. As far as they are concerned, such a helmet shouldn’t be let out the door. That’s why they design their helmets to confer protection that is way above and beyond the requirements of the standards listed.
Due to the robustness of their computational modeling, in recent times at least, MET has never had a new helmet model developed and manufactured that has then gone on to fail any of the standard test requirements. That highlights the efficiency of their approach, and is less wasteful than a more trial and error approach.
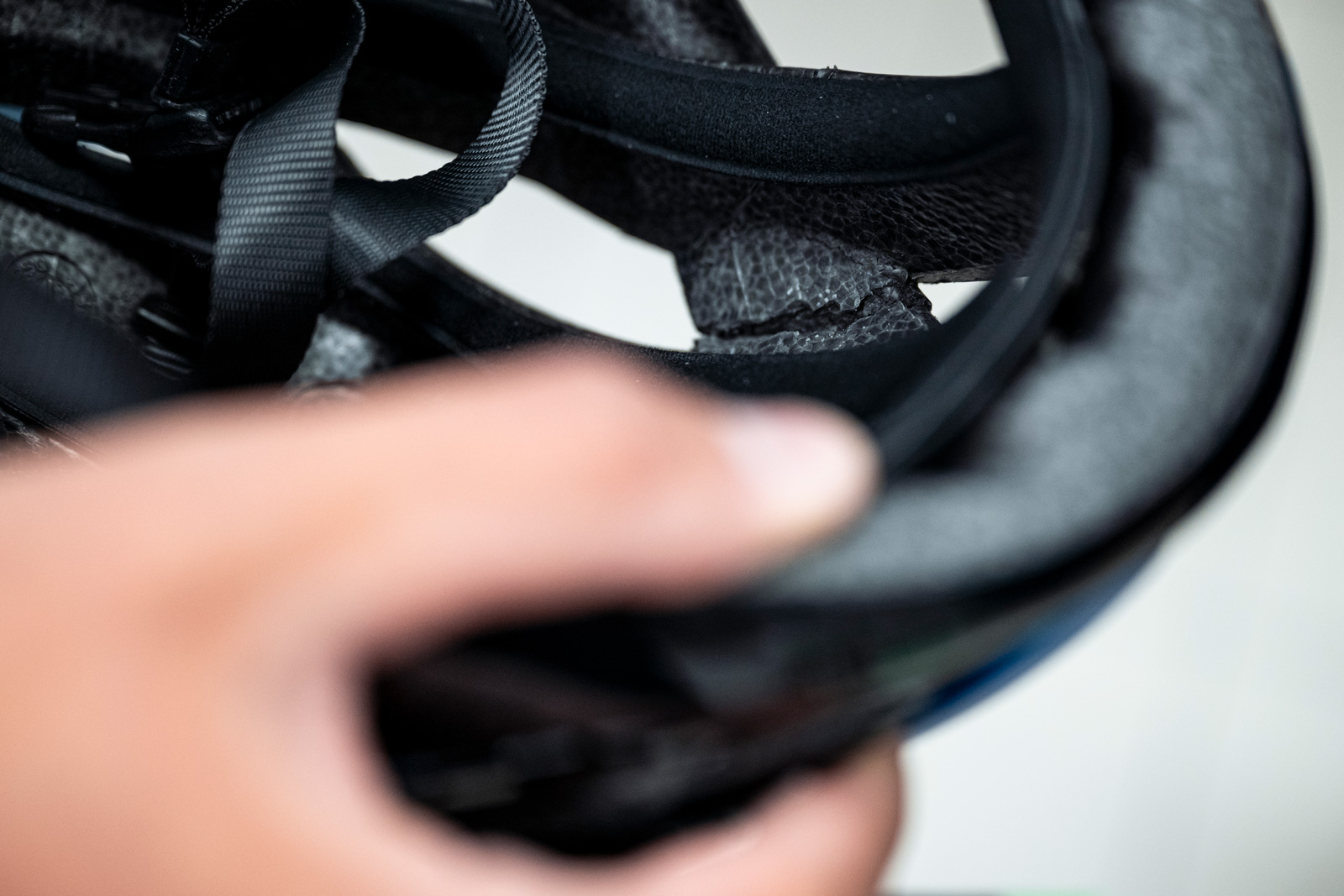
While many brands choose to use dual-density EPS foams within their helmets (Fox and Troy Lee Designs, for example), MET choose to use a single-density EPS on all of their helmets while optimizing the structure for its impact energy dissipation characteristics.
Not all helmets are made equal
The quality of a helmet, in terms of its ability to protect your head during an impact, will be determined by the safety technologies it packs in; its rotational impact protection technology, its construction, the structure and thickness of the EPS and so on, but it can also be affected by the humidity of the environment in which the in-molding process took place. A helmet made in summer can turn out quite different to a helmet made in winter, for example, and that shows in the impact test data.
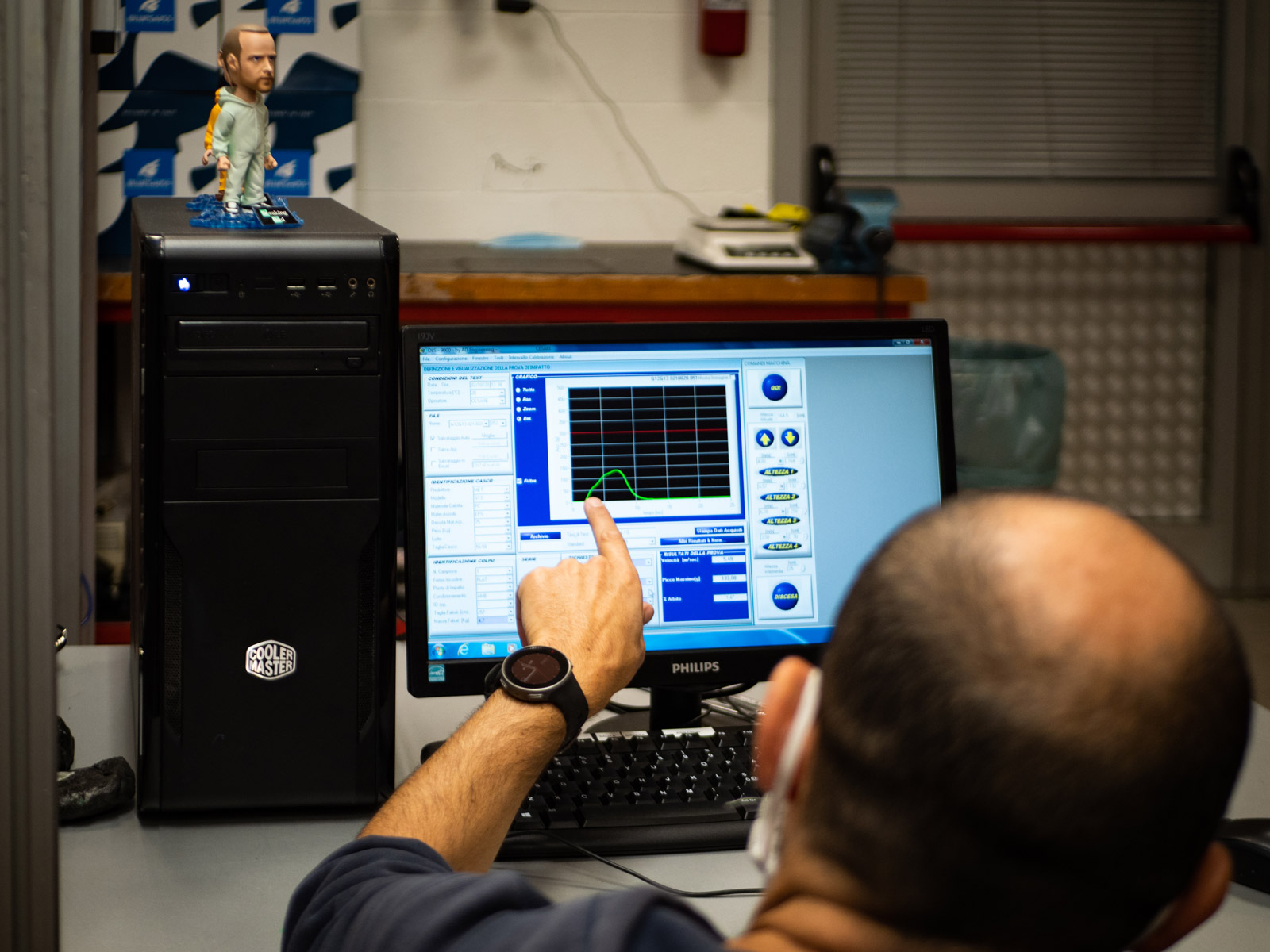
This is why MET take quality control very seriously. Batch testing of helmets is not mandatory, at least for helmets sold in Europe. But, due to the potential for seasonal variation in production quality and other factors that can influence the final product, MET take it upon themselves to go above and beyond the requirements of the CE Norm, testing a number of helmets from every single batch produced.
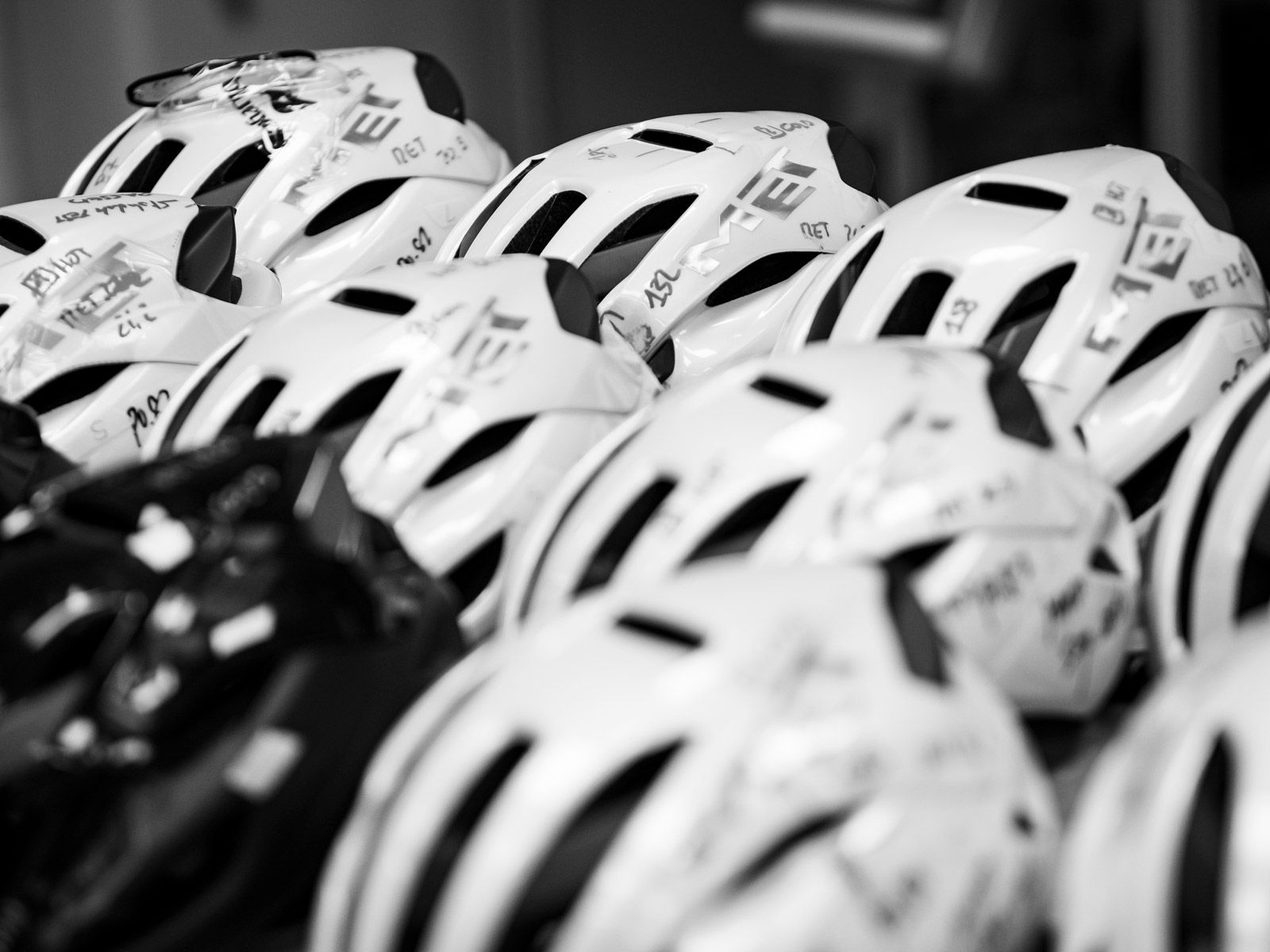
They have three employees in Asia who are working to QC the production process. They ship samples directly from the production line to the MET testing lab in Italy to ensure each batch meets the safety requirements.
Designing a helmet to fit everyone
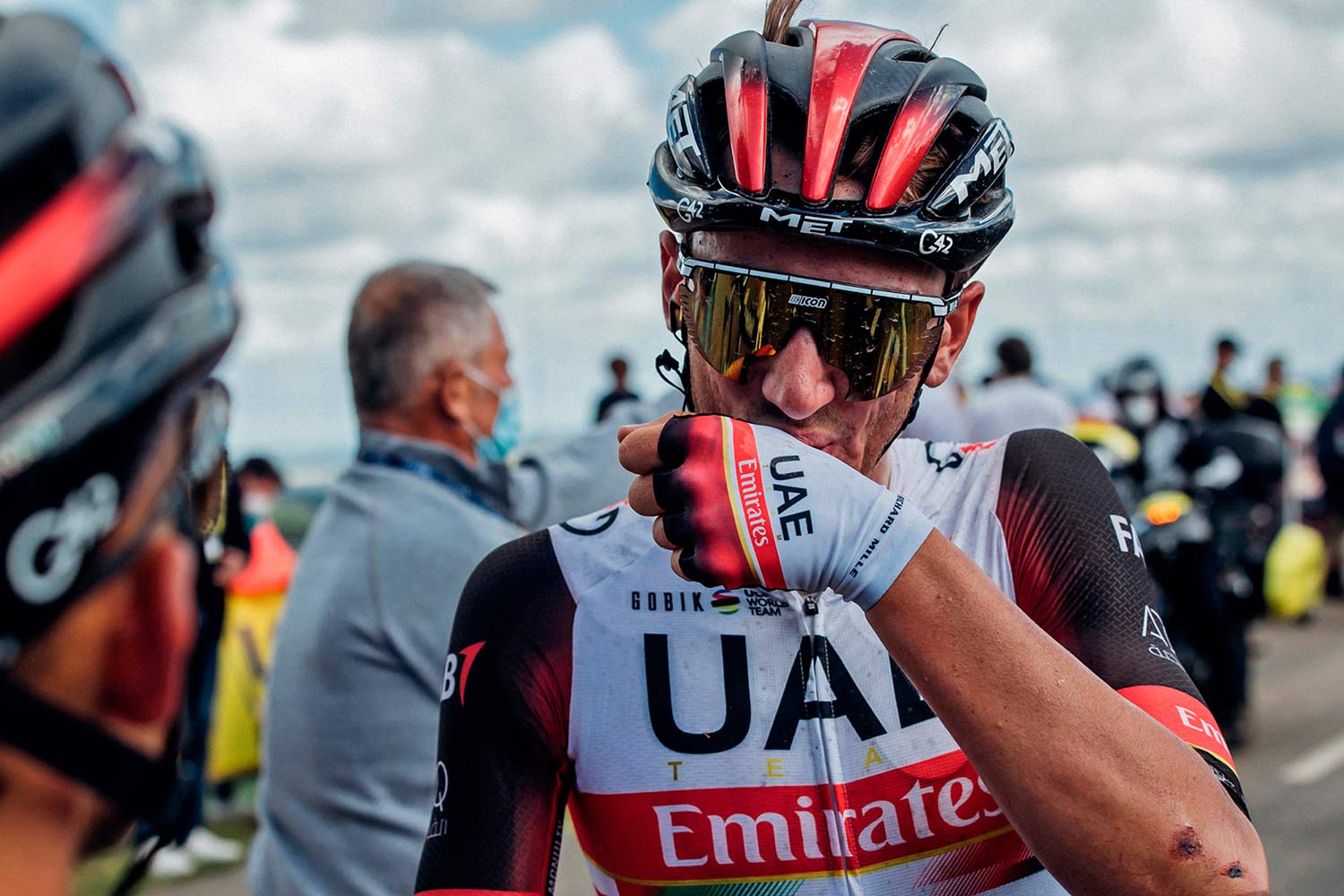
Of course, the relevance of rotational impact technology, EPS densities, and helmet construction is totally written-off if the helmet in question is a poor fit. Here, a major challenge is posed. The human head varies not only in size, but also in shape; even if you and I have the same head circumference, the chances of our heads being the same shape are negligible.
Now, certain brands will sell you a helmet that is custom-made specifically for your own head dimensions, usually at an eye-watering price. However, for most brands aiming for more reachable price points, a more universal approach is required, especially if they are looking to include expensive rotational impact protection technologies such as MIPS and the like.
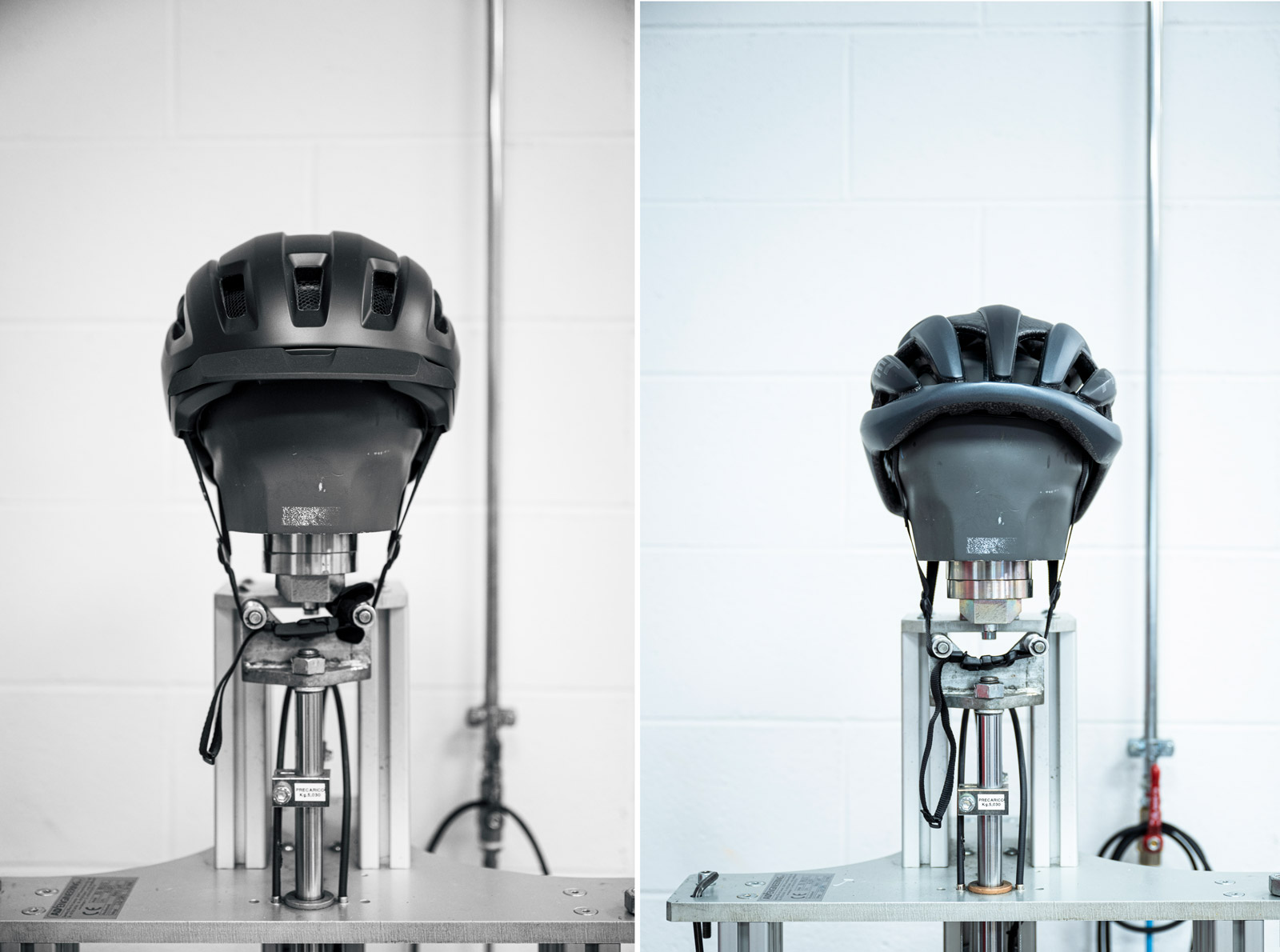
Having been in the business of designing and producing helmets for over 35 years, MET has a comprehensive bank of data and a wide breadth of knowledge and experience of helmet fit. Thus, the R&D team has a very good idea of how to design a helmet to fit well on, and be safe for, a variety of different head shapes. MET tells us their design team is constantly updating that bank of data measuring the head shape and circumference of MET’s sponsored riders, staff members, and members of the public to get data from a good cross-section of society.
Years ago, MET used to accommodate for different head shapes by adjusting the internal shape according to which market the helmet was to be sold in. They used to, for example, produce a helmet shape that was specific to the Asian market, as they figured that the shape of some of their models was too narrow for most riders in that part of the world. Nowadays, they are able to take a more universal approach thanks to advances in retention system design.
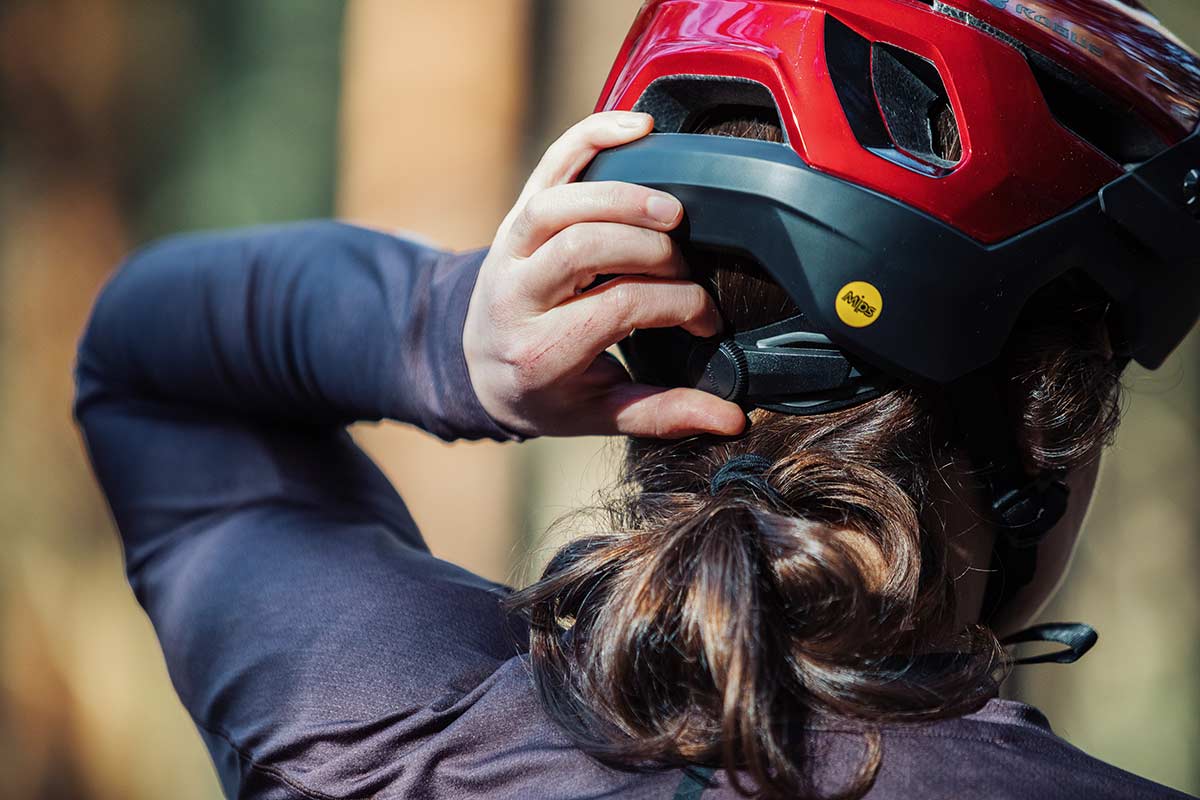
Their 360° head belt, part of the Safe-T retention system, is an innovation of theirs that gets around head-shape diversity. I’ve used the system on a number of MET Helmets, including the Parachute MCR; in my experience, the retention system does a good job of cinching down equally around the head, with no uncomfortable pressure points to speak of. It also allows for easy vertical adjustment of the cradle so most riders can get that in-the-helmet feeling, rather than feeling as though their helmet is simply perched atop their skull.
MET take a close look at their target market when designing the fit for any new model. For example, in the design of the MET Trenta 3K Carbon MIPS road helmet, weight was very high on the list of priorities. After all, it is the helmet worn by Tadej Pogačar and other members of the UAE Team Emirates. Aware of that, MET set about designing an ultra-compact helmet that would allow every member of the team to wear a small helmet, giving them a small weight advantage over having to wear the medium. It is the universal fit offered by the Safe-T Upsilon Retention System that allowed for that.
Of course, such universal approaches to helmet fit simply won’t cut the mustard for some people, and a custom-approach is sometimes the best and safest way forward. With this audience, I feel I don’t need to stress the importance of getting a good helmet fit. You guys don’t need to be taught how to suck eggs.
Who is MET Helmets?
Founded in 1987, MET Helmets was the first helmet brand in Europe. Created by Massimilliano Gaiatto and Luciana Sala, MET is still a family-owned company based in Talamona, close to Lake Como and surrounded by the trails of the Italian Alps.
The helmets evolved a lot since their first creations in the 80s.
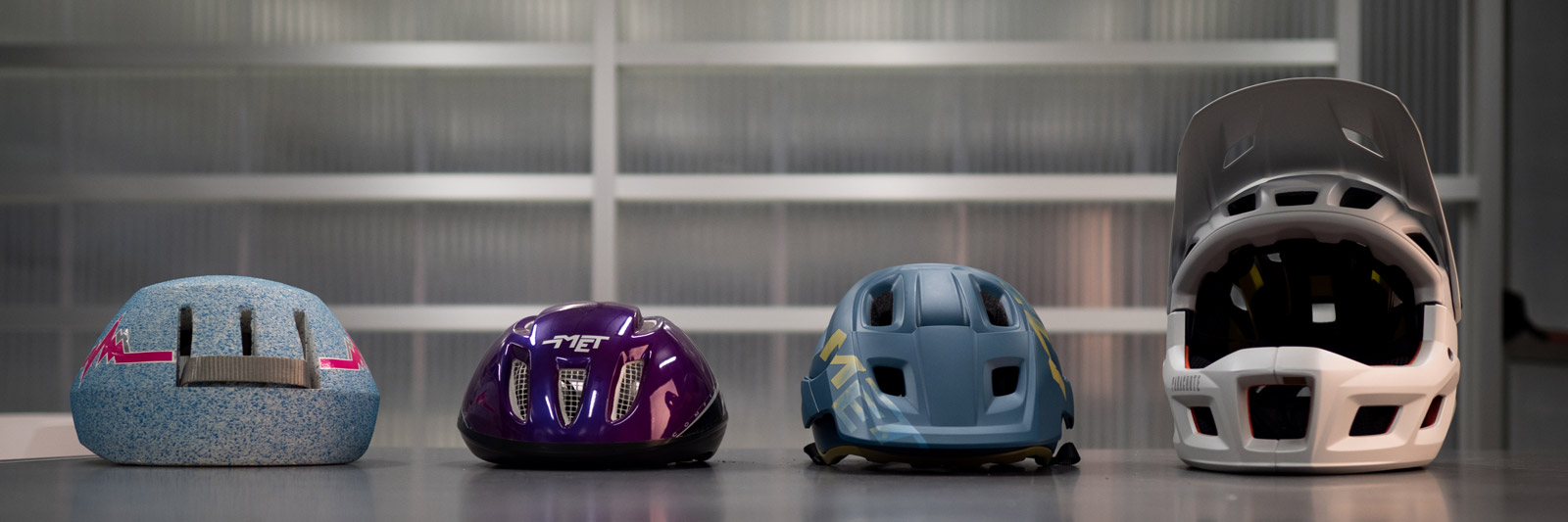
For 25 years, MET Helmets were entirely produced in Italy. Though MET are no longer producing in-house since 2012, they still have a huge influence over the processes as they custom-design their own tooling for the job thanks for the know how acquired.
MET are one of few European helmets brands to have an complete internal laboratory in Europe. They also are one of the few helmet specialists, offering only helmets and protective clothing for cyclists.
Discover more here:
This article was sponsored by MET Helmets